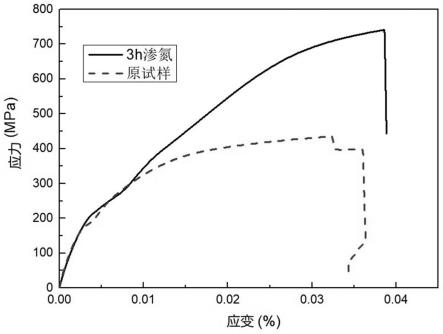
1.本发明涉及金属材料技术领域,尤其涉及一种金属材料及其制备和应用,具体涉及一种近铁素体不锈钢板件材料及其制备和在电机转子叠片中的应用。
背景技术:2.长期以来,对高功率密度和高效率电机的需求一直普遍存在于各种应用中,特别是在混合动力和电动汽车牵引应用中。目前混合动力和电动汽车牵引电机应用的发展趋势是通过提高转速来提高电机的功率密度,从而降低电机的质量和成本。然而,人们认识到,当电机用于混合动力和电动汽车的牵引应用时,功率密度、效率和机器的恒功率转速范围之间存在着明显的权衡,这种权衡带来了许多设计上的挑战。
3.电机的功率密度可以通过增加机器尺寸、改进热管理、提高转子速度或通过提高磁场利用率来提高。传统的电机转子是由硅钢片叠压而成的,这些叠片外圆轮廓为齿形,在工作过程中,转子和定子之间的间隙有空气或流体,由于转子和定子之间的气隙内的气体或流体搅动会产生大量的机械损失,特别是在一些高速工作的电机中损耗更加明显。为了减少这类原因造成的机械损失,通常采用磁桥结构来减少气息搅动,但是磁桥结构会漏磁,造成磁通量的损失。
4.具有磁桥结构的电机作为一种新型的电机,提高其性能的技术关键就是在于减小磁漏,提高叠片的凸极比。目前解决磁漏问题的方案包括采用多层结构的转子和减薄转子的磁桥,而这两种办法都会在追求高的凸极比,减小磁漏的同时带来机械强度的问题。
5.鉴于此,提出本发明。
技术实现要素:6.本发明提供一种局部固溶渗氮的金属材料及其制备和应用,具体涉及一种近铁素体不锈钢板件材料及其制备和在电机转子叠片中的应用,用以解决现有技术中电机转子叠片的磁桥在凸极比、磁漏和力学强度上不能同时满足高功率密度电机、高转速电机中叠片的要求的缺陷,通过从电机转子叠片的组织成分和磁性要求出发,结合schaeffer不锈钢组织相图建立了适用于电机转子叠片的选材依据,采取局部固溶渗氮工艺将目标区域奥氏体化,而其他区域保留软磁性,将这类材料应用于电机转子叠片,使磁桥不导磁而显著提高电机的磁利用率,提高电机的功率密度,并且提高磁桥的宽度从而叠片强度增加的同时也不会造成磁漏,而传统的电机转子叠片磁桥位置强度不够,在高速旋转中容易断裂,并且磁桥为铁素体会产生漏磁使磁阻转矩减小,降低了电机的功率密度。
7.本发明提供一种金属材料,包括:铁素体区域和非铁素体区域;
8.所述的铁素体区域中铁素体的含量为90%以上,其中,铁素体的主要元素组成为fe、cr、mn和mo,其中,cr的含量为20~26wt.%,mn的含量为2~8wt.%,mo的含量为0.5~2wt.%,其他元素为:0.001~0.04wt.%的c、0.1~0.5wt.%的al、0.5~1wt.%的si,余量为fe;所述的铁素体区域中的其余相为少量奥氏体或马氏体。
9.本发明的原料中,cr为与氮亲和力强的元素,能促进渗氮过程的发生,提高渗氮效率;同时cr属于cr当量定义的元素,cr当量定义的元素为铁素体生成元素,cr含量能保证渗氮前的基体材料为铁素体组织。
10.mn为与氮亲和力较强的元素,能促进渗氮过程的发生,提高渗氮效率;mn属于ni当量定义的元素,ni当量定义的元素为奥氏体体生成元素,合理控制mn含量的范围能保证渗氮前的基体材料为铁素体组织,同时提高固溶渗氮效率。
11.mo为与氮亲和力强的元素,能促进渗氮过程的发生,提高渗氮效率,加入mo元素为了进一步调节原材料的微观组织的磁畴性质,提高原材料的磁导率和磁感应强度。
12.合金元素cr,mn和mo能降低合金的马氏体转变线,使固溶渗氮的无防渗氮涂层区域立即淬火得到的组织保留为奥氏体,不会转变为马氏体。
13.所述的非铁素体区域中奥氏体的含量为70%以上,且根据渗氮时间的不同,所述的非铁素体区域的含氮量为0.4wt.%~1.2wt.%;本发明控制非铁素体区域的含氮量,这是局部固溶渗氮得到奥氏体的基本条件,渗入基体组织的含氮量低于此值原组织将无法充分由铁素体转化为奥氏体,高于此值将导致基体组织内的含氮量过饱和,氮元素将和合金元素cr等进一步得到氮化铬、氮化铁等氮化物。进一步地,所述的局部奥氏体区域也是提高电机转子叠片力学性能和磁性性能的关键因素,因此须控制含氮量来保证得到的高氮奥氏体。
14.所述的铁素体区域和非铁素体区域的交界处是晶粒尺寸上相变的牢固结合。
15.根据本发明提供的金属材料,所述的铁素体区域为schaeffer不锈钢组织相图中特定区域描述的基体组织,所述的特定区域是指所述的铁素体区域的各元素所占据的当量比满足如下式子:cr
当量
=cr%+mo%+1.5
×
(si%+v%)+0.8w%+0.5nb%+4ti%+3.5al%;
16.ni
当量
=ni%+co%+30
×
(c%+n%)+0.5mn%+0.33cu%。
17.本发明从电机转子叠片的组织成分和磁性要求出发,结合schaeffer不锈钢组织相图建立了适用于电机转子叠片的选材依据,根据schaeffer不锈钢组织相图,cr
当量
和ni
当量
会影响材料室温下的组织结构,因此,本发明设定铁素体中各元素所占据的当量比满足如下公式:
18.cr
当量
=cr%+mo%+1.5
×
(si%+v%)+0.8w%+0.5nb%+4ti%+3.5al%;
19.ni
当量
=ni%+co%+30
×
(c%+n%)+0.5mn%+0.33cu%。
20.根据本发明提供的金属材料,所述的铁素体区域中cr
当量
大于20wt.%且小于30wt.%,ni
当量
大于1wt.%且小于8wt.%。
21.本发明中设置cr
当量
和ni
当量
在上述范围内,这使得本发明的铁素体区域的软磁性能更优,其中当有较高的cr当量、较低的ni当量时,组织仅为铁素体,此时软磁性能较好,而控制高的cr当量和适当的ni当量来调节基体材料获得高的氮溶解度,较高的cr和适当的mn、mo含量有利于渗氮效率,并避免了板材高温时间过长引起的氧化等,此处为基于材料组分、固溶处理工艺和材料性能的总体优化。
22.根据本发明提供的金属材料,所述非铁素体区域是由所述的铁素体区域通过局部固溶渗氮的方式得到,且所述的非铁素体区域中除氮以外的其余元素的量在渗氮前后不产生变化。
23.根据本发明提供的金属材料,所述的金属材料为板材,且所述的铁素体区域和非
铁素体区域的界面处贯穿所述的板材的厚度方向。
24.根据本发明提供的金属材料,所述的铁素体区域和非铁素体区域的交界处是由所述的局部固溶渗氮工艺形成。
25.本发明还提供如上所述的金属材料的制备方法,在仅含有铁素体区域的板材表面上选择局部区域进行固溶渗氮得到所述的金属材料;
26.所述的局部区域在固溶渗氮后形成非铁素体区域。
27.固溶渗氮是一种将氮元素加入钢基体中的方法,当氮达到一定含量时钢基体可以在室温下得到奥氏体,奥氏体是一种非磁性相。将电机转子叠片采用局部固溶渗氮,对磁桥进行奥氏体化后得到非磁性的磁桥,并且氮的加入能使晶界结合力增强,阻碍晶粒长大,达到固溶强化的作用,从而提高了磁桥的强度和韧性,避免磁桥在高速转动中发生断裂和破坏。但是纯铁和硅钢对氮的溶解度很低,因此研究合金元素、组织和材料磁性的关系并确定适合进行固溶渗氮的材料依据尤为重要。本发明优化仅含有铁素体区域的板材的材料组分,通过局部区域的固溶渗氮可以得到具有导磁和不导磁的双相区域的材料。
28.根据本发明提供的金属材料的制备方法,具体步骤为:先在仅含有铁素体区域的板材表面上选择一部分区域涂敷防渗氮涂层或者镀铜,然后将涂覆后的板材整体置于充满氮气的高温高压环境中固溶渗氮后取出并立刻淬火;
29.所述的高温高压环境一般为高温高压炉;
30.所述的固溶渗氮过程中持续通入纯度为99.99%以上的氮气。
31.所述的局部区域和所述的一部分区域构成所述的块体的整个表面。
32.所述的氮气为经过干燥的氮气,纯度为99.99%,在固溶渗氮过程氮气一直处于流动状态,氮气压力为0.25mpa,本发明是高压气体流通的快速固溶渗氮技术。
33.为了使磁桥得到室温下稳定的奥氏体组织,避免产生有害的氮化物析出相,在固溶渗氮之后立即快速冷却,其中快速冷却可采用空淬、水淬和油淬,本发明根据板材的厚度来挑选合适的冷却方法,例如0.1mm~0.8mm的薄板可采用空淬或者高压气体淬火,而厚度0.8mm~1.5mm的板料宜采用水淬或者油淬。
34.根据本发明提供的金属材料的制备方法,所述的高温高压环境中的温度范围为1000℃~1200℃,压力范围为0.1mpa~0.5mpa;所述的固溶渗氮的时间范围为0.3h~4h。
35.采用上述工艺可以实现0.1mm~1.5mm的不同渗氮层深度。
36.板材越厚则选取的固溶渗氮保温时间越长,渗氮后的区域至少70%的组织发生奥氏体转变,最大磁导率约等于1,磁感应强度约为0。
37.根据本发明提供的金属材料的制备方法,所述的板材为0.1~1.5mm厚的轧制板材。轧制的热处理工艺可以采用退火处理,退火温度550-650℃,保温时间1-2h。
38.这与传统的电机转子叠片厚度是一致的,在0.3h~4h的固溶渗氮过程中得到整个厚度方向的渗氮层深度。
39.根据本发明提供的金属材料的制备方法,固溶渗氮之前采用抛光机或者喷砂的方式对轧制板材的表面进行抛磨,去除表层氧化层,然后用无水乙醇进行清洗并吹干。
40.根据本发明提供的金属材料的制备方法,在固溶渗氮结束之后立即进行淬火,再对板材进行退火处理,然后对板材表面残留的防渗氮涂层进行刷洗或浸泡在酸性溶液中可去除,另外也可以采用喷砂除去,对于镀铜的情况下不影响板材使用时可以不用除去。
41.退火处理消除内应力并改善磁性,提高最大磁导率与磁感应强度,再除去板材表面残留的防渗氮涂层,并清除表面的氧化物。
42.根据本发明提供的金属材料的制备方法,所述的镀铜是指在板材除非局部区域的位置表面镀上厚度范围为0.035mm~0.06mm的铜,避免非渗氮区域的渗氮。
43.根据本发明提供的金属材料的制备方法,涂敷防渗氮涂层是指先在板材除非局部区域的位置采用喷涂、浸涂或者刷涂防渗氮涂料,然后放入烘箱在100℃~150℃下保温0.5~1h,待涂层干燥后对局部区域进行固溶渗氮;
44.本发明所用的涂层材料为高温防渗氮涂料,该涂层具备耐1100
±
100℃的高温,能够阻止氮原子与涂覆涂层的区域的金属发生反应。
45.本发明还提供如上所述的金属材料的应用,将所述的金属材料应用于电机转子叠片;
46.所述的非铁素体区域作为电机转子叠片的磁桥;
47.所述的磁桥为不导磁且力学强度高的高氮奥氏体,使电机转子叠片在工作过程中不漏磁,无磁通量损失;所述的磁桥的拉伸强度提高50%以上,并且耐腐蚀和耐高温,在高速转动时不发生断裂失效。
48.本发明提供的一种金属材料及其制备和应用,通过优化金属材料的组分,采取局部固溶渗氮工艺将目标区域奥氏体化,而其他区域保留软磁性,将本发明的材料应用于电机转子叠片,可以显著提高电机转子叠片的磁性性能、力学强度,为高功率密度电机、高转速电机的电机提供了一种材料方案及其热处理工艺。
49.与普通的硅钢相比,本发明的金属材料板材含有更多的合金元素,机械性能好且耐腐蚀。
50.将本发明的金属材料板材制成的电机转子叠片,奥氏体的磁桥与叠片的铁素体是晶粒尺寸相变的结合而不是传统方式的焊接胶结,磁桥的强度进一步得到了提高,避免了磁桥在高转速下发生断裂失效。
51.与具有磁桥结构的传统硅钢叠片相比,传统硅钢叠片存在漏磁,本发明选择近铁素体(schaeffer图中铁素体区域及其附近的组织),是为了利用铁素体的软磁性,但是,传统的纯铁和低合金铁素体材料渗氮效率极低,难以经过固溶渗氮后奥氏体化,此处选取具有高铬锰钼的合金材料,这类材料组分的氮的饱和溶解度高,因此,可以在局部区域进行固溶渗氮,而且渗氮能够使电机转子叠片的磁桥区域增氮发生晶格重组,得到室温下为稳定奥氏体结构的无磁性的磁桥,从而解决了电机转子叠片结构磁通量损失。
52.本发明的金属材料板材制成的电机转子叠片在完全退火后的磁性性能较佳,尤其是磁桥区域为不漏磁的高氮奥氏体,这使得其磁通量无损失,磁阻转矩、功率密度更大,并且具有较强的力学强度,弥补了初始材料磁导率不如硅钢的不足,最后使电机叠片整体的磁性性能优于传统硅钢叠片,为高功率密度电机、高转速电机和耐腐蚀环境的电机提供了一种选材方案及其热处理工艺。
附图说明
53.为了更清楚地说明本发明或现有技术中的技术方案,下面将对实施例或现有技术描述中所需要使用的附图作一简单地介绍,显而易见地,下面描述中的附图是本发明的一
些实施例,对于本领域普通技术人员来讲,在不付出创造性劳动的前提下,还可以根据这些附图获得其他的附图。
54.图1为本发明的板材中各区域在schaeffer不锈钢组织相图的分布示意图;
55.图2为本发明的电机转子叠片的结构示意图;
56.图3为本发明的金属材料的横截面的sem图;
57.图4为本发明的板材在固溶渗氮前后的xrd图;
58.图5本发明的板材在固溶渗氮前后的拉伸强度曲线;
59.图6为本发明的板材在固溶渗氮前的硬度;
60.图7为本发明的板材在固溶渗氮3h后的硬度;
61.图8为本发明的板材在固溶渗氮前的磁极观察片结果;
62.图9为本发明的板材在固溶渗氮3h后的磁极观察片结果;
63.图10为本发明的板材在固溶渗氮前的磁滞回线;
64.图11为本发明的板材在固溶渗氮3h后的磁滞回线;
65.附图标记:
66.1:磁桥,2:导磁结构,3:气隙。
具体实施方式
67.为使本发明的目的、技术方案和优点更加清楚,下面将结合本发明中的附图,对本发明中的技术方案进行清楚、完整地描述,显然,所描述的实施例是本发明一部分实施例,而不是全部的实施例。基于本发明中的实施例,本领域普通技术人员在没有作出创造性劳动前提下所获得的所有其他实施例,都属于本发明保护的范围。
68.下面结合图1-图11描述本发明的一种金属材料及其制备和应用。
69.本发明的测试方法如下:
70.板材的非铁素体区域的相组成通过x射线衍射分析(xrd);
71.板材渗氮后的氮含量通过氮元素化学测试法进行测试,相比较传统的能谱测试元素(eds)的方法更为准确;
72.板材的的表面硬度通过维氏硬度仪进行测试;
73.通过拉伸实验对材料固溶渗氮前后的板材的拉伸强度进行测试;
74.渗氮前后的板材的组织结构通过扫描电镜(sem)进行观察;
75.渗氮前后的板材的导磁性能通过磁极观察片进行观察;
76.通过软磁直流b-h仪测试板材在渗氮前后的磁导率、矫顽力等磁性性能。
77.实施例1
78.一种金属材料的制备方法,具体步骤为:
79.(1)选取材料轧制成厚度为0.5mm的轧制板材;其中,轧制板材的结构示意图如图2所示,和电机转子叠片的构造相同,由磁桥1(渗氮区域)、气隙3和导磁结构2(非渗氮区域)组成,轧制的热处理工艺为退火处理,退火温度600℃,保温时间1.5h。
80.所选取的材料的元素组成为:fe、cr、mn、mo和其他元素,且cr的取值范围为22wt.%,mn的取值范围为4wt.%,mo的取值范围为0.75wt.%,其他元素为:0.001wt.%的c、0.1wt.%的al、0.5wt.%的si,余量为fe;如图1所示,实施例1的材料结合schaeffer不锈
钢组织相图的描述,制得的板材的组织为含量为99%以上的铁素体,其余相为少量奥氏体或马氏体。
81.测试轧制板材的磁性,结果为:最大磁导率为1000,磁感应强度为1t。
82.(2)采用喷砂的方式对轧制板材的表面进行抛磨,去除表层氧化层,然后用无水乙醇进行清洗并吹干。
83.(3)先在轧制板材上的非渗氮区域涂敷防渗氮涂层,然后将板材整体置于充满氮气的高温高压炉中固溶渗氮后取出并立刻淬火;
84.其中,防渗氮涂料为市售的高温防渗氮涂料;涂敷防渗氮涂层是指先在板材除非局部区域的位置采用喷涂、浸涂或者刷涂防渗氮涂料,然后放入烘箱在100℃下保温0.5h,待涂层干燥后对局部区域进行固溶渗氮;
85.固溶渗氮过程中持续通入流量纯度为99.99%的氮气;高温高压环境中的温度为1100
±
100℃,压力为0.2mpa;固溶渗氮的时间为3h;
86.淬火的方式为将固溶渗氮结束后的板材立刻放入水中进行水淬,待完全冷却至室温后再取出。
87.(4)对板材进行退火处理,再对板材表面残留的防渗氮涂层进行刷洗,得到金属材料。
88.对该金属材料进行测试:
89.根据xrd的物相分析方法,测试结果为:如图4所示,非渗氮区域中只有铁素体的衍射峰,和步骤(1)中的板材的xrd的物相分析结果一致,区域仍然为步骤(1)中的板材的材料和组织(即铁素体区域);渗氮区域中有奥氏体的衍射峰,通过xrd衍射峰的强度使用xrd分析软件mdi jade 6计算得出该区域中奥氏体的含量为70%以上(即非铁素体区域);铁素体区域和非铁素体区域的交界处是由所述的固溶渗氮工艺形成,且铁素体区域和非铁素体区域的界面处贯穿所述的板材的厚度方向。
90.根据氮元素化学测试的方法,测试结果为:铁素体区域不含氮,而渗氮后的非铁素体区域含氮量为0.6wt.%。
91.根据软磁b-h测量仪测试,测试结果为:铁素体区域的磁性为:最大磁导率为1000,磁感应强度为1.3t,这说明基体材料退火后的软磁性能较好。非铁素体区域的磁性为:最大磁导率为1,磁感应强度为0,这说明经过局部固溶渗氮,非铁素体区为不导磁的奥氏体组织。
92.根据sem的微观组织观察,如图3所示,测试结果为:在500倍的电子显微镜观察下可以清楚的看到铁素体和奥氏体的晶粒,并且还观察到铁素体区域和非铁素体区域的交界处是晶粒尺寸上相变的牢固结合。
93.通过维氏硬度仪进行测试,如图6、7所示,进行硬度测试时,在板材上随机取点,测试结果表明:板材渗氮前的平均硬度为287hv0.5,板材渗氮后的平均硬度为417hv0.5,固溶渗氮处理能够显著提高材料的硬度。
94.(5)将制得的金属材料作为电机转子叠片进行应用;其中,非铁素体区域作为电机转子叠片的磁桥;该磁桥不漏磁且无磁通量损失;所述的磁桥耐腐蚀和耐高温。
95.实施例2
96.一种金属材料的制备方法,具体步骤为:
97.(1)选取材料轧制成厚度为0.5mm的轧制板材,其中,轧制的热处理工艺为退火处理,退火温度600℃,保温时间1.5h,切取40mm
×
100mm的板材进行固溶渗氮实验。
98.所选取的材料的元素组成为:fe、cr、mn、mo,且cr的取值范围为21wt.%,mn的取值范围为6.5wt.%,mo的取值范围为1wt.%,其他元素为:0.001wt.%的c、1wt.%的si,余量为fe;实施例2的材料结合schaeffer不锈钢组织相图的描述,制得的板材的组织为99%以上的铁素体,其余相为少量奥氏体或马氏体。
99.(2)采用抛光机的方式对轧制板材的表面进行抛磨,去除表层氧化层,然后用无水乙醇进行清洗并吹干。
100.(3)先在轧制板材上的非渗氮区域镀铜,然后将板材整体置于充满氮气的高温高压炉中固溶渗氮后取出并立刻水淬;
101.其中,镀铜是指在板材除非局部区域的位置表面镀上厚度为0.06mm(固溶渗氮时间越长则越厚)的铜。
102.固溶渗氮过程中持续通入纯度为99.99%的氮气;高温高压环境中的温度为1150
±
50℃,压力为0.25mpa;固溶渗氮的时间为3h。
103.(4)对板材进行退火处理,表面残余的铜镀层在不影响使用的情况下不用除去,再对板材表面残留的氧化物和油污进行清洗,得到金属材料。
104.对该金属材料进行测试:
105.根据xrd的物相分析测试方法,同实施例1,测试结果为:非渗氮区域仍然为99%以上的铁素体(即铁素体区域);渗氮区域中奥氏体的含量为70%以上(即非铁素体区域);铁素体区域和非铁素体区域的交界处是由所述的固溶渗氮工艺形成,且铁素体区域和非铁素体区域的界面处贯穿所述的板材的厚度方向。
106.根据氮元素化学测试的方法,测试结果为:原铁素体不含氮,而渗氮后的非铁素体区域含氮量为0.8wt.%。
107.根据sem的微观组织测试方法,同实施例1,测试结果为:在500倍的电子显微镜观察下可以清楚的看到铁素体和奥氏体的晶粒,并且还观察到铁素体区域和非铁素体区域的交界处是晶粒尺寸上相变的牢固结合。
108.根据拉伸实验,对原试样和切取渗氮区域的试样进行单向拉伸,如图5所示,测试结果为:所述的金属材料的铁素体区域的拉伸强度为435mpa(原试样对应的虚线),奥氏体区域的拉伸强度为741mpa(3g渗氮对应的实线),强度提高了1.7倍。
109.采用磁极观察片观察材料的磁性性能,结果为在磁极观察片下,导磁位置为灰白色显影,而不导磁位置不显影,由图8、9可知,固溶渗氮后的组织(非铁素体区域)不显影,即不导磁;防渗氮区域下的组织(铁素体区域)为灰白色显影,即导磁性良好;
110.更进一步的根据软磁b-h测量仪测试,如图10、11所示,测试结果为:在渗氮前,材料的磁极化强度为1.002t,最大磁导率为208.4;渗氮后材料的磁极化强度为0.004253t,最大磁导率为1.167;发现磁感应强度渗氮前是渗氮后的236倍,磁导率渗氮前是渗氮后的178倍。
111.(5)将制得的金属材料作为电机转子叠片进行应用;其中,非铁素体区域作为电机转子叠片的磁桥;该磁桥不漏磁且无磁通量损失;所述的磁桥耐腐蚀和耐高温。
112.最后应说明的是:以上实施例仅用以说明本发明的技术方案,而非对其限制;尽管
参照前述实施例对本发明进行了详细的说明,本领域的普通技术人员应当理解:其依然可以对前述各实施例所记载的技术方案进行修改,或者对其中部分技术特征进行等同替换;而这些修改或者替换,并不使相应技术方案的本质脱离本发明各实施例技术方案的精神和范围。