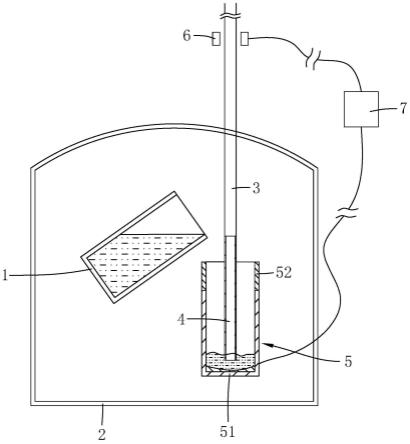
1.本技术涉及铸锭技术领域,尤其是涉及一种高熔点金属的低偏析细晶锭的铸造方法。
背景技术:2.目前针对特种合金和稀贵金属等材料,不少铸锭仍采用浇铸法生产;铸锭是将熔化的金属倒入永久的或可以重复使用的模具中制造出来的;铸锭可以进一步机械加工成多种新的形状;铸锭是铸态组织,传统铸造在稳定状态下金属是以枝晶方式长大,在凝固过程中容易出现成分偏析和粗大的柱状晶。
3.偏析主要是由于合金在凝固过程中溶质再分配而引起的,柱状晶凝固偏析明显,细等轴晶凝固能改善偏析。使未凝固的熔体保持在较低并且在可控的状态下迅速凝固,并且辅以机械搅拌,就可以使凝固组织中的偏析极低。
4.申请号为201711302710.x的专利文件公开了一种熔体电磁搅拌式低压铸造装置及铸造方法,其包括熔化炉、坩埚、密封圈、进排气及压力信号接口、盖板、真空气源和电控气动截止阀;还包括侧强磁体、底部强磁体和变频电源;侧强磁体位于熔化炉的四周,底部强磁体为熔化炉的底部,两个强磁体与变频电源实现电连接;所述侧强磁体和底部强磁体采用线圈结构。
5.针对上述中的相关技术,发明人认为设计的熔体电磁搅拌式低压铸造装置及铸造方法,采用电磁搅拌的方式驱使熔化炉内的金属液体运动,但是受感应电流的集肤效应限制,电磁搅拌的透入深度有限,对熔化炉中间区域的金属液体作用极小,导致熔化炉中间区域的金属液体的均温效果较差,影响铸锭的成型质量。
技术实现要素:6.为了提高铸锭的成型质量,本技术提供一种高熔点金属的低偏析细晶锭的铸造方法,采用如下的技术方案:一种高熔点金属的低偏析细晶锭的铸造方法,包括s1:熔融、保温:将固态金属加热至全部熔化形成金属熔体,并保持金属熔体温度始终在熔点以上;s2:调高、启转:采用金属杆同轴置于模具的成型腔底壁上方5-20mm,驱动金属杆旋转;其中金属杆材质与金属熔体材质相同,且金属杆与模具同轴;s3:引流、旋布均温:将s1步骤中制得的金属熔体沿金属杆流入模具的成型腔中,直至金属杆下端没入模具中的金属熔体中5-15mm,并通过旋转方式带动模具内的金属熔体流动;s4:提杆、连续浇铸:设定提杆力矩f并持续测量金属杆的旋转力矩m,若m<f,使金属杆以1-3mm/s的基本速度上升的同时持续旋转;若m≥f,则提升金属杆5-10mm,过程中控制s1步骤中制得的金属熔体以匹配速度持续沿金属杆流入模具中以使模具内的金属熔体
数量始终保持一致,金属杆始终伸入金属熔体中,直至铸锭成型完毕。
7.通过采用上述技术方案,先将固态金属加热,直至固定金属全部熔化后形成金属熔体,然后保持金属熔体的温度始终在熔点以上使金属熔体保持液态;采用金属杆同轴设置于模具底壁上方5-20毫米,驱动金属杆旋转;将s1步骤中制得的金属熔体沿着金属杆流入模具的成型腔中;金属熔体沿金属杆流入模具的过程中部分热量通过金属杆传递至外界,旋转的金属杆通过强力搅拌的方式将模具内的金属熔体内的初生枝晶打碎,并通过搅拌提供大量形核以生成细小的等轴晶,并且通过强力搅拌可以使金属熔体中合金成分均匀化,减轻偏析;同时,金属杆旋转时,温度较高的金属熔体由于粘度较小被甩到接近模具内腔壁的位置,而靠近模具内腔壁的位置冷却能力强,温度较低的金属熔体由于粘度较大,落在接近模具中心的位置,而靠近模具中心的位置冷却能力弱,在金属杆的旋布下,中心区域和边缘区域在水平方向上的冷却能力差异减小;同时,金属杆承担一部分模具中间区域金属熔体的散热作用,进一步减小了中间区域和边缘区域的金属熔体冷却速度差异;设定提杆力矩f,并在金属杆的旋转过程中持续测量金属杆的旋转力矩m,当模具中心区域凝固组织接近金属杆的端部时,金属杆的旋转力矩m明显上升,若金属杆的旋转力矩m<提升设定提杆力矩f,使金属杆以较低的基本速度上升并维持旋转,若金属杆的旋转力矩m≥提升设定提杆力矩f,控制金属杆提升模具5-10毫米,同时,控制s1步骤中制得的金属熔体以匹配的速度持续沿着金属杆流入模具中,并使得模具内的金属熔体数量始终保持一致,直至整个铸锭成型完毕;全浇铸过程中金属杆以较低的上升并且浇铸不断流,以避免浇铸凝固时可能的分层,获得连续完整的铸锭。
8.设计的高熔点金属的低偏析细晶锭的铸造方法,第一点:通过金属杆的旋转使模具内金属熔体在凝固在时间和空间上均匀可控;第二点:通过测量金属杆旋转力矩大小可以直接感知模具内金属熔体的凝固情况,并依此控制浇铸速度;第三点:通过金属杆的强力搅拌破碎初生枝晶,并细化晶粒,改善偏析;第四点:通过金属杆的引流作用可以在浇铸时减少金属熔体的迸溅现象;第五点:通过控制流量连续浇铸的方式,有利于金属熔体快速凝固以获得细晶组织;第六点:通过金属杆导热和旋转,进一步的减小中间区域和边缘区域金属熔体的冷却速度差异,提高铸锭质量;第七点:结构简单,成本低。
9.可选的,还包括s5:起弧补温:金属熔体全部浇入模具后,控制金属杆提升至金属熔体液面上方5-10mm并停转,向金属杆供电使得金属杆下端与金属熔体液面之间形成电弧,以延迟液面凝壳。
10.通过采用上述技术方案,s1步骤中制得的金属熔体全部浇铸入模具的成型腔中后,铸锭的铸造成型进入收尾阶段,此时模具中的金属熔体液面顶部散热速度较快,为避免铸锭顶部区域过早凝固形成凝壳,此时将金属杆提升至金属熔体液面上方5-10mm,向金属杆供电使得金属杆下端与金属熔体之间形成电弧,电弧放电为金属熔体液面顶部补温以延迟液面凝壳;设计的s5步骤,可以避免浇铸收尾阶段因金属熔体顶部过快凝壳导致内部出现缩孔。
11.可选的,所述金属杆设置为空心管。
12.通过采用上述技术方案,设计为空心管的金属杆,可以控制金属杆自身的散热效果以及旋布金属熔体的能力,避免因金属杆散热冷却能力过强导致模具中心区域的金属熔
体过早凝固。
13.可选的,所述模具包括水冷金属模具段和陶瓷模具段,所述水冷金属模具段和所述陶瓷模具段同轴设置,且所述水冷金属模具段位于所述陶瓷模具段下方。
14.通过采用上述技术方案,设计的模具,通过分段设置,以降低浇注后期顶部的散热速度,使金属熔体凝固的最后阶段液相线平坦化。
15.可选的,所述s1-s4步骤均在40-60pa的气压条件下进行。
16.通过采用上述技术方案,设计的在40-60pa的气压条件下进行的s1-s4步骤,可以在减少浇铸时金属熔体迸溅的同时还可以减少对流。
17.可选的,所述金属杆的转速为2-5转/秒。
18.通过采用上述技术方案,设计的转速为2-5转/秒的金属杆,可以在对模具内金属熔体起到搅拌作用的同时,减少因金属杆转速过快导致的金属熔体飞溅的现象。
19.可选的,所述s5中电弧的持续时长为5-8秒。
20.通过采用上述技术方案,设计的持续时长为5-8秒的电弧,可以在延迟模具中金属熔体液面顶部凝壳情况下减少补温对铸锭金相组织的干扰。
21.可选的,所述金属杆的外径d、所述金属杆的管厚h以及所述模具内腔直径r之间的关系为:d=0.25r=10h。
22.通过采用上述技术方案,可以在金属杆引流能力、导热能力以及搅拌能力和金属锭的外径之间形成一个平衡。
23.综上所述,本技术包括以下至少一种有益技术效果:1.设计的高熔点金属的低偏析细晶锭的铸造方法,第一点:通过金属杆的旋转使模具内金属熔体在凝固在时间和空间上均匀可控;第二点:通过观测金属杆旋转力矩大小可以直接感知模具内金属熔体的凝固情况,并依此控制浇铸速度;第三点:通过金属杆的强力搅拌破碎初生枝晶,并细化晶粒;第四点:通过金属杆的引流作用可以在浇铸时减少金属熔体的迸溅现象;第五点:通过控制流速连续浇铸的方式,最大程度避免柱状晶的形成,有利于金属熔体快速凝固以获得细晶组织;第六点:通过金属杆导热和旋转,进一步的减小中间区域和边缘区域金属熔体的冷却速度差异,提高铸锭质量;第七点:结构简单,成本低。
24.2.设计的高熔点金属的低偏析细晶锭的铸造方法,电弧放电为金属熔体液面顶部补温以延迟液面凝壳,可以避免浇铸收尾阶段因金属熔体液面顶部过快凝壳而导致内部缩孔。
25.3.设计的高熔点金属的低偏析细晶锭的铸造方法,可以控制金属杆自身的散热效果以及旋布金属熔体的能力,避免因金属杆散热冷却能力过强导致模具中心区域过早凝固。
附图说明
26.图1是本技术初始浇铸阶段的状态示意图;图2是本技术电弧放电补温阶段的状态示意图;图3是本技术制备例1制得的铸锭切面图;图4是本技术对比例1制得的铸锭切面图。
27.附图标记:1、熔埚;2、真空炉;3、升降杆;4、金属杆;5、模具;51、水冷金属模具段;
52、陶瓷模具段;6、电接触器;7、电弧电源。
具体实施方式
28.以下结合附图1-2对本技术作进一步详细说明。
29.本技术实施例公开一种高熔点金属的低偏析细晶锭的铸造方法。
30.参照图1和图2,一种高熔点金属的低偏析细晶锭成型装置至少包括真空炉、真空感应炉、plc控制器、倾炉电机、旋转电机、熔埚、模具、电弧电源、电接触器、升降杆以及金属杆;熔埚、模具以及金属杆均位于真空炉的内腔中,真空感应炉通过电磁感应的方式加热熔埚中的固态金属;升降杆和金属杆同轴焊接,升降杆穿过并与真空炉转动连接,旋转电机位于真空炉外并与升降杆连接,用于驱动升降杆转动。
31.参照图1和图2,为了在金属杆4的引流能力、导热能力以及搅拌能力和铸锭的尺寸之间形成一个平衡,金属杆4设置为空心管;且金属杆4的外径d、金属杆4的管厚h以及模具5内腔直径r之间的关系式为:d=0.25r=10h。
32.参照图1和图2,在铸锭浇铸后期,为了避免模具5成型腔中金属熔体温度散失过快,模具5包括水冷金属模具段51和陶瓷模具段52,水冷金属模具段51和陶瓷模具段52同轴设置,且水冷金属模具段51位于陶瓷模具段52的下方;本实施例中水冷金属模具段51设置为铜材质,陶瓷模具段52的材质设置为氧化镁材质。
33.参照图1和图2,电弧电源7一端与水冷金属模具段51电连接,另一端通过电接触器6与升降杆3电连接,在金属杆4提升至金属熔体液面顶部上方5mm并停转时,电接触器6与升降杆3自动闭合与水冷金属模具段51形成闭合回路。
34.一种高熔点金属的低偏析细晶锭的铸造方法包括s1:熔融、调压及保温;s11:熔融、保温:通过熔埚1来容纳固态金属,并通过真空感应炉加热熔埚1内的固态金属,直至熔埚1内的固态金属全部熔化形成金属熔体,维持真空感应炉的功率使得熔埚1内的金属熔体的温度始终高于自身熔点100-150摄氏度;本实施例中金属熔体的温度高于自身熔点120摄氏度。
35.s12:调压:为了减少浇铸时因气压过低带来的迸溅和因气压过高带来的明显对流影响铸锭的散热速度,通过真空炉2为低偏析细晶锭的铸造全过程提供一个40-60pa的低压环境,优选气压为50pa;s2:调高、启转;s21:调高:通过金属杆4同轴设置于模具5成型腔底壁上方5-20mm,优选为10mm,其中金属杆4的材质与金属熔体的材质相同;s22:启转:驱动金属杆4开始旋转,金属杆4的转速为2-5转/秒,优选为3转/秒;s3:引流、旋布:采用plc控制器和倾炉电机配合控制熔埚1倾转,使得熔埚1内的金属熔体沿金属杆4流入模具5的成型腔中;直至金属杆4下端没入模具5成型腔中的金属熔体中5-15mm,并通过旋转方式带动模具5成型腔内的金属熔体流动;s4:提杆、连续浇铸;s41:提杆:开始浇铸后,提杆以1-2mm/s的基本速度上升并维持旋转。设定提杆力矩f,采用旋转电机和升降杆3配合驱动金属杆4,升降杆3与金属杆4同轴焊接,且升降杆3可
导电,当旋转电机接近堵转电流时,升降杆3的旋转力矩达到f,并通过持续测量旋转电机电流的方式间接测量得到金属杆4的旋转力矩m,并将金属杆4的旋转力矩m和提杆力矩f作比较,若m≥f,则使金属杆4以3-4mm/s的速度上升5-8mm,提杆过程中金属杆4始终伸入模具中的金属熔体中;s42:连续浇铸:根据提升杆的位置,通过倾炉电机控制熔埚1缓慢持续倾转,使得熔埚1内的金属熔体连续沿金属杆4流入模具5的成型腔中,模具5成型腔内金属熔体数量始终保持一致;s5:起弧补温:待熔埚1内的金属熔体全部浇入模具5的成型腔中后,控制金属杆4提升,直至金属杆4下端高于模具5中的金属熔体液面顶部上方5-10mm并停转,优选为5mm;采用电接触器6与升降杆3接触,升降杆3、金属杆4、电弧电源7以及模具5之间形成闭合回路,使得金属杆4下端与金属熔体液面之间形成电弧并持续5-8秒,以延迟液面凝壳;本实施例中电弧持续时长优选为6秒。
36.本技术实施例一种高熔点金属的低偏析细晶锭的铸造方法的实施原理为:先借助真空感应炉隔空感应加热的方式对熔埚1内的固态金属加热,直至将固定金属加热至熔化,然后保持真空感应炉感应功率不变使熔埚1内的金属熔体保持液态,然后调节真空炉2内气压至50pa,以减少浇铸时因气压过低带来的迸溅和因气压过高带来的明显对流影响铸锭的散热速度。
37.然后通过升降杆3控制金属杆4下降,直至金属杆4下端与模具5成型腔底壁之间的间距介于5-20mm之间,同时驱动金属杆4开始旋转;然后控制熔埚1倾转,将熔埚1内的金属熔体倒出并沿着金属杆4流入模具5成型腔中,金属熔体沿金属杆4流入模具5成型腔的过程中部分热量通过金属杆4传递至外界,旋转的金属杆4通过强力搅拌的方式将模具5成型腔内的金属熔体内的初生枝晶打碎,并通过搅拌提供大量形核以生成细小的等轴晶,并且通过强力搅拌可以使金属熔体中的合金成分均匀化,避免成分偏析。
38.同时,金属杆4旋转时,温度较高的金属熔体由于粘度较小被甩到接近模具5成型腔周侧的位置,靠近模具5成型腔周侧的位置冷却能力强;接近熔点的金属熔体由于粘度较大,落在接近模具5中心的位置,而接近模具5中心的位置冷却能力弱,在金属杆4的旋布下,使得中心区域和边缘区域在水平方向上的冷却能力差异减小,同时,金属杆4承担一部分模具5中间区域金属熔体的散热作用,进一步减小了中间区域和边缘区域的金属熔体冷却速度差异。
39.在金属杆4的旋转过程中,始终通过测量数控电机电流大小的方式间接得出金属杆4的旋转力矩,当模具5中心区域凝固组织接近金属杆4端部时,金属杆4的旋转力矩明显上升,设定提杆力矩f,若金属杆4的旋转力矩m<提升设定提杆力矩f,金属杆4以1-2mm/s的基础速度上升并持续旋转,若金属杆4的旋转力矩m≥提升设定提杆力矩f,通过升降杆3带动金属杆4提升。熔埚1的倾转始终与提杆上升相关联。熔埚1内的金属熔体沿着金属杆4流入模具5成型腔中,模具5成型腔内的金属熔体数量保持一致,直至整个铸锭成型完毕。
40.在熔埚1内的金属熔体全部浇铸入模具5成型腔中后,铸锭铸造成型进入收尾阶段,此时金属熔体液面顶部散热速度较快,为避免铸锭顶部区域过早凝固形成凝壳,此时将金属杆4提升至金属熔体液面上方5-10mm,打开电弧电源7,金属杆4与模具5成型腔中的金属熔体之间起弧,并持续5-8秒,电弧放电为金属熔体液面顶部补温以延迟液面凝壳,然后
自然冷却凝固得到铸锭。
41.制备例1s1:熔融、保温:将20千克铂铑合金(ptrh20)加热至全部熔化形成铂铑合金熔体,并保持铂铑合金熔体温度高于熔点120℃;s2:调高、启转:采用金属杆4同轴置于模具5的成型腔底壁上方10mm,驱动金属杆4旋转;其中金属杆4材质与金属熔体材质相同,且金属杆4与模具5同轴,金属杆4的外径为25mm,管厚为2.5mm,水冷铜模具段内腔尺寸长*宽*高为75*100*130mm,氧化镁模具段内腔尺寸长*宽*高为75*100*70mm;s3:引流、旋布均温:将s1步骤中制得的铂铑合金熔体沿金属杆4流入模具5的成型腔中,直至金属杆4下端没入模具5中的铂铑合金熔体中10mm,并通过旋转方式带动模具5内的铂铑合金熔体流动;s4:提杆、浇铸:提杆基本上升速度为2mm/秒;设定提杆力矩f并持续测量金属杆4的旋转力矩m,若m<f,金属杆4按基本上升速度上升并维持旋转;若m≥f,则将金属杆4提升6mm;s1步骤中制得的铂铑合金熔体持续沿金属杆4流入模具5中,控制其浇铸速度与金属杆4提升速度相匹配,使模具5内的铂铑合金熔体数量始终保持一致,直至铸锭成型完毕。
42.s5:起弧补温:铂铑合金熔体全部浇入模具5后,控制金属杆4提升至铂铑合金熔体液面上方5mm并停转,向金属杆4供电使得金属杆4下端与铂铑合金熔体液面之间形成电弧并持续6秒,放电电流在900a,以延迟液面凝壳。
43.对比例1s1:将20千克铂铑合金加热至全部融化,并使铂铑合金熔体温度高于自身熔点75℃,将铂铑合金熔体逐步缓慢浇铸入立式水冷铜模中,浇铸总时间为50秒。
44.对比例2s1:将20千克铂铑合金加热至全部融化,并使铂铑合金熔体温度高于自身熔点75℃,将铂铑合金熔体逐步缓慢浇铸入立式水冷铜模中,并同时通过电磁搅拌的方式使得立式水冷铜模中的铂铑合金熔体流动。
45.性能检测数据表1.检测数据对比表标准试样宏观密度(g/cm3)相对密度缩孔和疏松制备例118.397.6%无对比例116.286.2%有对比例217.492.7%有结合制备例1、对比例1以及对比例2并结合表1可以看出,采用本技术实施例加工的铸锭,其宏观密度和相对密度均明显高于对比例1和对比例2制备的铸锭,说明采用本技术加工方法制得的铸锭中缩孔和疏松少。
46.以上均为本技术的较佳实施例,并非依此限制本技术的保护范围,故:凡依本技术的结构、形状、原理所做的等效变化,均应涵盖于本技术的保护范围之内。