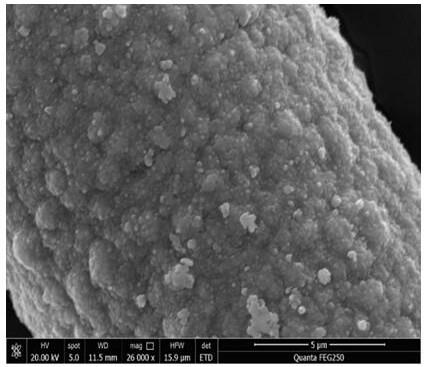
1.本发明属于特种纤维界面处理技术领域,涉及一种连续氧化铝纤维铜界面的制备方法。
背景技术:2.氧化铝纤维(al2o
3f
)增强金属基复合材料因具有高强度、高耐磨性等优异性能被广泛应用在航天航空、石油开采、电子封装及大型军事武器制品领域中,备受各国行内人士的重视,国外早在60年代就已开始研究,目前国外的技术相对成熟,且在美日都已大量投入应用。例如,美国已投入应用由al2o3增强铝基复合材料所制备的燃料注入零件,提高了零件的使用寿命,取得较好的经济效益;日本丰田投入应用由al2o3长纤维增强铝基复合材料的汽车连杆,极大提高了连杆的强度,提升了发动机性能,并有较好的减重效果。
3.我国金属基复合材料起步于上世纪八十年代,时至今日,和发达国家相比仍有很大差距。就目前研究而言,氧化铝纤维增强金属基复合材料制备过程中,制备过程温度高,且金属熔体表面能大,与al2o
3f
增强相间润湿性差,一直是制约金属基复合材料性能提高的关键问题。表面金属化已被证实可有效改善氧化铝与金属之间浸润性问题,其中al2o
3f
表面因过于光滑而不能有效施镀是目前金属化过程中存在的关键问题。
4.al2o
3f
因具有耐高温耐腐蚀变形低热导率小等优异性能,同时生产原料成本低、生产工艺相对简单,被广泛应用在金属基陶瓷基复合材料领域,纤维表面金属化能够有效改善与金属基体之间浸润性问题,其潜在金属为镍、铜、银。化学镀已被公认为有效处理技术之一,通过对纤维预处理,在经配置镀液使纤维表面覆有所需金属涂层,使纤维拥有电学、磁学和化学性能。就目前研究而言,国外不少学者对氧化铝颗粒表面金属化的报道较多,但前处理用时较长且对al2o
3f
表面金属化的报道几乎没有。
5.目前纤维表面处理工艺主要包括热还原法、传统预处理法以及钯盐敏化活化一体化法,其中采用热还原法主要应用于碳纤维表面镀铜工艺,虽减少了敏化活化步骤,但预处理时间长,且热还原过程所需工艺条件严格;传统预处理法耗时长,且施镀过程较为繁琐,不利工业化生产;钯盐敏化活化一体化,虽减少了操作步骤,但耗时依然过长且钯盐价格及其昂贵,也不利于工业大规模使用。
技术实现要素:6.本发明针对传统纤维铜界面制备中存在的问题提出一种新型的连续氧化铝纤维铜界面的制备方法。
7.为了达到上述目的,本发明是采用下述的技术方案实现的:本发明所提供的连续氧化铝纤维铜界面的制备方法,工艺流程分为两大步骤:纤维表面预处理和纤维表面金属化镀层。
8.具体操作步骤如下:s0:准备氧化铝纤维。
9.s1前处理:配制活化液,将浓度为5-20g/l的氯化亚锡溶液,浓度为2-10g/l的硝酸银溶液,以及37wt%的hcl溶液2-10ml混合均匀;然后将纤维浸泡于活化液中10-20min,浸泡完成后取出纤维,用去离子水充分冲洗。氯化亚锡溶液:硝酸银溶液:hcl溶液体积比为6:3:1,浸泡时间为10-20min,冲洗液为去离子水。
10.s2配制铜盐溶液:取硝酸铜、硫酸铜、氯化铜中的任意一种或几种溶于去离子水中,配成浓度为0.1mol/l的铜盐溶液,溶液澄清透明即可。
11.s3配制镀液:取s2所配制铜盐溶液试剂,依次加入络合剂、还原剂、氢氧化钾,所述络合剂为酒石酸或酒石酸钾钠、edta-2钠中的一种或两种,浓度为10-60g/l,还原剂为甲醛、蔗糖、葡萄糖中的一种或多种,其浓度为2-10wt%,去离子水若干,氢氧化钾若干,将镀液ph调整至11-13,铜盐溶液:络合剂:还原剂:去离子水份数比为10-30:5:0.2-0.6:20-50。
12.s4:将s1处理后的纤维置于s3所配制镀液中,水浴加热反应,水浴温度控制在50-70℃,反应过程中缓慢搅拌镀液,至镀液澄清,则反应停止,即可取出镀铜后的纤维,自然烘干即可。
13.本发明所采用的连续氧化铝纤维表面涂层附着机理较传统碳纤维有所区别,碳纤维是利用前处理使纤维表面变得更加粗糙,以便在后面敏化活化时,提供活化点的附着,达到金属沉积的效果。而氧化铝纤维因比表面积比较大,吸附性能极强,且拥有优异的耐腐蚀性能,即使表面光滑也依然能够吸附单质,故本发明针对其特性在前处理中省去除胶、除油、粗化三个阶段,将敏化和活化液组合一起,通过加入适当盐酸,稳定活化液,使银单质能够稳定的析出,并被纤维吸附在表面形成形核质点,达到后期还原金属沉积的目的。在本发明制备过程中,影响金属沉积质量的关键点,除了后期施镀的成分及浓度外,前期预处理步骤至关重要。本发明通过工艺改进,省略了除胶、除油、粗化三大步骤,并把敏化活化缩为一步,大大缩短预处理的时间,并在工艺大大简化的前提下,取得理想的效果。本发明所提供的方法中氯化亚锡与水反应,生产锡膜附着在氧化铝纤维表面,锡膜中的锡离子与银离子反应,将银离子还原成银单质沉积在纤维表面,形成形核质点。盐酸在其中起到防止氯化亚锡过快的水解导致失效的作用。
14.与现有技术相比,本发明的优点和积极效果在于:通过敏化活化一体化缩短了氧化铝纤维预处理时间,简化预处理步骤,随后采用化学镀对氧化铝纤维表面镀铜处理,可以在氧化铝纤维表面镀上一层均匀致密的铜界面,从而扩展氧化铝纤维的应用场景,整个工艺流程简单方便,耗时少,成本低,适合大规模工业推广。
附图说明
15.图1为实施例1氧化铝纤维铜界面的sem照片。
16.图2为实施例1氧化铝纤维铜界面的eds图谱。
17.图3为实施例1氧化铝纤维铜界面表面元素及其含量。
18.图4为实施例1氧化铝纤维铜界面xrd图谱。
19.图5为对比例1氧化铝纤维铜界面的sem照片.图6为对比例2氧化铝纤维铜界面的sem照片。
具体实施方式
20.为了能够更清楚地理解本发明的上述目的、特征和优点,下面结合具体实施例对本发明做进一步说明。需要说明的是,在不冲突的情况下,本技术的实施例及实施例中的特征可以相互组合。
21.在下面的描述中阐述了很多具体细节以便于充分理解本发明,但是,本发明还可以采用不同于在此描述的其他方式来实施,因此,本发明并不限于下面公开说明书的具体实施例的限制。
22.实施例1取长度8cm的氧化铝纤维若干,本实施例中氧化铝纤维来源如下:国产莫纶996(morlion 996,牌号:ml996,厂家:国装新材料技术(江苏)有限公司)连续氧化铝纤维。将7g/l的氯化亚锡溶液60ml,2g/l的硝酸银溶液30ml,以及37wt%的hcl溶液10ml混合均匀。然后将纤维加入混合溶液中浸泡15min。称取硫酸铜15g,加入去离子水,配制成0.1mol/l的溶液,并搅拌使得硫酸铜溶解,得到澄清透明的硫酸铜溶液。依次往硫酸铜溶液中加入浓度为10g/l的络合剂酒石酸钾钠、4wt%的还原剂甲醛,并加入氢氧化钾,将镀液ph调整至12;其中铜盐溶液:络合剂:还原剂:去离子水:体积比为20:5:0.2:30,得到镀液。将浸泡预处理后的氧化铝纤维加入到镀液中,水浴加热,温度控制在50℃进行反应,反应过程中缓慢搅拌镀液,至镀液澄清反应停止时,取出镀后纤维,自然晾干,即得到镀铜氧化铝纤维。
23.图1-4分别为本实施例所制备得到的镀铜氧化铝纤维铜界面的sem照片、eds图谱、表面元素及其含量以及xrd图谱。
24.从图1可以看出,镀铜氧化铝纤维铜界面均匀致密,从图2-4可以看出:镀层表面元素有c\o\cu,其中cu含量最多,质量分数占76.25wt%,其它为基本元素。进一步由图4 xrd图谱分析可知,铜物相特征衍射峰较明显,其2θ为43.1
°
、50.3
°
、73.9
°
会出现(111)(200)(220)晶面特征峰,且峰宽较窄,峰型较尖表明晶粒结晶较好,其中2θ在43.1
°
时强度最高。
25.实施例2取长度10cm的氧化铝纤维若干,将10g/l的氯化亚锡溶液60ml,5g/l的硝酸银溶液30ml,以及37wt%的hcl溶液10ml混合均匀。然后将纤维加入混合溶液中浸泡10min。称取适量硝酸铜,加入去离子水,配制成0.1mol/l的溶液,并搅拌使得硝酸铜溶解。依次往硝酸铜溶液中加入浓度为30g/l的络合剂酒石酸、7wt%的还原剂葡萄糖,并加入氢氧化钾,将镀液ph调整至11;其中铜盐溶液:络合剂:还原剂:去离子水:体积比为10:5:0.4:20,得到镀液。将浸泡预处理后的氧化铝纤维加入到镀液中,水浴加热,温度控制在60℃进行反应,反应过程中缓慢搅拌镀液,至镀液澄清反应停止时,取出镀后纤维,自然晾干,即得到镀铜氧化铝纤维。经检测,本实施纤维所镀效果同实施例1差别不大。
26.实施例3取长度12cm的氧化铝纤维若干,将20g/l的氯化亚锡溶液60ml,10g/l的硝酸银溶液30ml,以及37wt%的hcl溶液10ml混合均匀。然后将纤维加入混合溶液中浸泡20min。称取氯化铜若干,配制成0.1mol/l的溶液,并搅拌使得氯化铜溶解,依次往氯化铜溶液中加入浓度为60g/l的络合剂edta-2na、10wt%的还原剂葡萄糖,并加入氢氧化钾,将镀液ph调整至13;其中铜盐溶液:络合剂:还原剂:去离子水:体积比为30:5:0.6:50,得到镀液。将浸泡预处理后的氧化铝纤维加入到镀液中,水浴加热,温度控制在70℃进行反应,反应过程中缓慢
搅拌镀液,至镀液澄清反应停止时,取出镀后纤维,自然晾干,即得到镀铜氧化铝纤维。经检测,本实施纤维所镀效果同实施例1差别不大。
27.对比例1本对比例未特殊说明之处,与实施例1一致。
28.本对比例与实施例1相比,改变的条件是纤维前处理参数,具体来讲是将氯化亚锡和硝酸银浓度升高,以便检测活化液浓度对产品的影响。
29.取长度10cm的氧化铝纤维若干,将30g/l的氯化亚锡溶液60ml,15g/l的硝酸银溶液30ml,以及37wt%的hcl溶液10ml混合均匀。然后将纤维加入混合溶液中浸泡10min。称取硫酸铜15g,加入去离子水,配制成0.1mol/l的溶液,并搅拌使得硫酸铜溶解,得到澄清透明的硫酸铜溶液。依次往硫酸铜溶液中加入浓度为10g/l的络合剂酒石酸钾钠、4wt%的还原剂甲醛,并加入氢氧化钾,将镀液ph调整至12;其中铜盐溶液:络合剂:还原剂:去离子水的体积比为20:5:0.2:30,得到镀液。将浸泡预处理后的氧化铝纤维加入到镀液中,水浴加热,温度控制在50℃进行反应,反应过程中缓慢搅拌镀液,至镀液澄清反应停止时,取出镀后纤维,自然晾干,即得到镀铜氧化铝纤维。
30.图5为本对比例制备得到的氧化铝纤维铜界面的sem图,从图中可以看出铜颗粒沉积不均匀,且局部出现未施镀局域。与实施例1相比效果明显下降。说明了纤维前处理工艺参数严重影响镀层的好坏。
31.对比例2本对比例改变纤维施镀参数,将酒石酸钾钠浓度调整为70g/l,甲醛浓度调整为15wt%,ph调整到14,施镀温度调整到40℃。
32.取长度8cm的氧化铝纤维若干,将7g/l的氯化亚锡溶液60ml,2g/l的硝酸银溶液30ml,以及37wt%的hcl溶液10ml混合均匀。然后将纤维加入混合溶液中浸泡15min。称取硫酸铜加入去离子水搅拌,配成0.1mol/l的澄清透明溶液,依次加入络合剂、还原剂、氢氧化钾,络合剂为酒石酸钾钠溶液,浓度为70g/l,还原剂为浓度15wt%的甲醛溶液,加入去离子水和氢氧化钾,将镀液ph调整至14。其中铜盐溶液:络合剂:还原剂:去离子水的体积比为20:5:0.2:30。将预活化处理后的纤维置于镀液中,水浴加热,温度控制在40℃进行反应,反应中缓慢搅拌镀液,至镀液澄清反应停止时,取出镀铜后纤维,自然晾干,即得到镀铜氧化铝纤维。
33.图6为本实施例制备得到的氧化铝纤维铜界面的sem照片,从图中可以看出铜颗粒大小相对较均匀,但局部出现未施镀局域。与实施例1相比效果出现下降。说明了纤维施镀参数对镀层形貌也有较大影响。
34.对比例3取长度8cm的氧化铝纤维若干,将7g/l的氯化亚锡溶液60ml,2g/l的硝酸银溶液30ml,以及37wt%的hcl溶液10ml混合均匀。然后将纤维加入混合溶液中浸泡15min。称取硫酸铜15g,加入去离子水,配制成0.1mol/l的溶液,并搅拌使得硫酸铜溶解,得到澄清透明的硫酸铜溶液。依次往硫酸铜溶液中加入浓度为10g/l的络合剂酒石酸钾钠、4wt%的还原剂甲醛,并加入氢氧化钾,将镀液ph调整至12;其中铜盐溶液:络合剂:还原剂:去离子水:体积比为20:5:0.8:30,得到镀液。将浸泡预处理后的氧化铝纤维加入到镀液中,水浴加热,温度控制在50℃进行反应,反应过程中缓慢搅拌镀液,至镀液澄清反应停止时,取出镀后纤维,自
然晾干,即得到镀铜氧化铝纤维。
35.改变施镀组分的体积比发现,提升甲醛的体积比将会导致镀液快速发生反应,引起镀液失效,继而纤维表面无有效颗粒沉积。
36.以上所述,仅是本发明的较佳实施例而已,并非是对本发明作其它形式的限制,任何熟悉本专业的技术人员可能利用上述揭示的技术内容加以变更或改型为等同变化的等效实施例应用于其它领域,但是凡是未脱离本发明技术方案内容,依据本发明的技术实质对以上实施例所作的任何简单修改、等同变化与改型,仍属于本发明技术方案的保护范围。