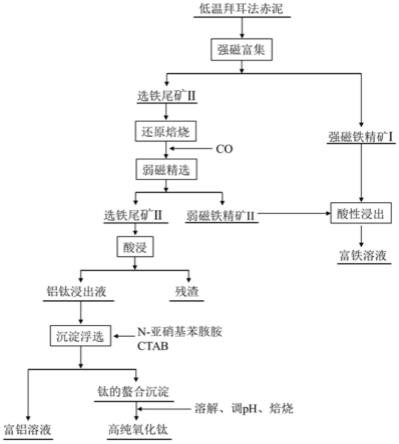
1.本发明涉及一种赤泥的资源化利用的方法,具体涉及一种进口铝土矿低温拜耳法赤泥梯级资源化利用的方法,属于固废资源化技术领域。
背景技术:2.赤泥是氧化铝的工业生产过程中同步产生的废渣,因其中含有大量的氧化铁而呈现红色。
3.赤泥中含有大量可再生利用的氧化物和多种有用金属元素,成为赤泥再生利用的基础。赤泥的成分、性质的差异,决定了不同赤泥的利用方法。国内针对赤泥的资源化利用等问题非常重视,诸多学者对赤泥中有价金属元素的资源化利用进行了大量的研究。中国专利cn109943706a公开了一种回收低铁拜耳法赤泥中铁的方法,通过脱碱、高温还原和磁选工艺从赤泥中回收铁,得到品位和回收率均超过80%的铁精矿;中国专利cn104195341a公开了一种赤泥提钛工艺,通过两次酸浸,水解煅烧得到高纯二氧化钛;中国专利cn111333091a公开了一种利用赤泥烧结法生产氧化铝的方法及生产系统,采用烧结、溶出步骤从赤泥中回收氧化铝;中国专利cn111573696a公开了赤泥碱直接回收利用的方法及系统,采用淋洗、蒸发浓缩等步骤从拜耳赤泥中回收碱。这些方法虽然各有所长,但均存在回收金属单一、收益少、赤泥回收利用率低的缺点。除此之外,中国专利 cn108754134a公开了一种赤泥综合利用工艺,提出通过高温电炉反应将赤泥直接还原成铁水,熔融炉渣制成矿棉,铁的回收率达到了90%,但该工艺忽略了其他有价金属的综合利用。中国专利cn102757078a公开了一种从拜耳法赤泥中分离有用组分的方法,通过沉降分离,料浆焙烧,水浸,循环酸浸,陈化提硅,铝铁分离等步骤来获取氢氧化铝、微细硅酸、铁粉、石膏等产品,但该方法铝铁分离效率较低。中国专利cn114772619a公开了一种将拜尔法赤泥资源化的方法,通过采用铝粉、赤泥粉、硅石粉按一定质量比混合,采用shs的方式让铝还原赤泥里的金属氧化物,来获得fe-si-m合金,该工艺操作较为复杂,难以实现大规模应用。中国专利cn113846227a公开了一种赤泥浸出液中多种金属组分的分离回收方法,该专利通过沉淀浮选法实现了铝和铁钛的分离,但在该过程中铁与钛的分离较为困难。
4.低温拜耳法赤泥是以三水铝矿石为原料生产氧化铝过程中产生的固体废弃物,铁也在生产过程中得以富集。低温拜耳法赤泥中fe2o3含量通常在35%~40%之间。由于反应温度较低,该赤泥中铁、硅的物相仍保持原矿中物相,利于采用物理法富集分离。本研究在中国专利(cn113846227a)公开的铁钛铝浸出液的沉浮分离工艺的基础上,引入磁选工艺来改善沉淀浮选过程中钛铁难以分离的不足。因此,该研究对赤泥浸出液中多种金属组分分离回收的研究具有重要意义。
技术实现要素:5.针对现有沉淀浮选工艺中钛和铁难以分离的问题,以及低温拜耳法赤泥中含铁物质大多以延伸矿物的形式存在的特点,本发明的目的是在于提供一种低温拜耳法赤泥梯级
资源化利用的方法,该方法采用两步磁选工艺分离富集赤泥中的铁,并结合酸浸-沉淀浮选工艺实现了铝、钛的分离回收,且该方法兼具工艺流程简单、成本低、回收效率高等优点,显著提高了赤泥综合利用价值。
6.为了实现上述技术目的,本发明提供了一种低温拜耳法赤泥梯级资源化利用的方法,该方法包括以下步骤:
7.1)将低温拜耳法赤泥进行磨矿后,采用强磁精选,得到磁性铁精矿i和选铁尾矿i;
8.2)将所述选铁尾矿i进行还原焙烧,所得还原焙烧产物进行磨矿后,采用弱磁精选,得到磁性铁精矿ii和选铁尾矿ii;
9.3)将所述磁性铁精矿i和磁性铁精矿ii通过酸浸回收铁;
10.4)将所述选铁尾矿ii通过酸性浸出,得到钛铝浸出液,所述钛铝浸出液通过沉淀浮选工艺分离铝和钛。
11.在现有的沉淀浮回收赤泥浸出液中钛、铁和铝等有价金属工艺过程中,钛、铁是一起分离的,后续钛、铁进一步分离的工艺相对较为复杂,针对该问题,本发明先采用两步磁选(强磁-还原焙烧-弱磁)工艺优先实现赤泥中铁的高效分离富集,进一步采用沉淀浮选工艺分离回收钛和铝,避免了后续的钛铁分离过程,从而实现铁、钛和铝的高效分离回收。本发明技术方案的关键在于预先采用强磁分离将大部分弱磁性铁矿从赤泥中分离回收,该过程显著提高了后续还原焙烧的效率,缩短还原焙烧过程,减少还原剂用量。而余下部分铁矿(如铁橄榄石、铁铝尖晶石和余下赤铁矿等)经过还原焙烧实现物相转化形成强磁性铁矿,进一步采用弱磁选即可实现与非磁性的钛铝等矿物的高效分离,进而实现铁的高效率分离。而且两种不同价态的铁精矿搭配实现氧化还原酸性浸出,可以提高铁矿的浸出效率。将低温拜耳法赤泥中铁元素通过两步磁选高效回收后,余下的钛铝元素主要分布于选铁尾矿ii中,采用酸性浸出可以将选铁尾矿ii中的铝和钛同时浸出,而溶液体系中的铝离子和钛离子易于通过沉淀浮选工艺进行分离。因此,通过本发明技术方案可以实现低温拜耳法赤泥中铁、铝和钛的高效分离。
12.作为一个优选的方案,所述低温拜耳法赤泥优选为进口铝土矿低温拜耳法赤泥,其包含的主要成分及各主要成分的质量百分比含量为:氧化铝10~20%,氧化铁20~40%,氧化钛1~10%。对于进口铝土矿低温拜耳法工艺的生产温度一般低于100℃,其中含铁物质大多以延伸矿物的形式存在,更适合于本发明的工艺。
13.作为一个优选的方案,所述低温拜耳法赤泥磨矿至粒度满足-400目粒级所占质量百分比含量不低于80%。将低温拜耳法赤泥原料磨矿至适当的粒度,有利于湿式强磁场对弱磁性铁矿的高效富集。
14.作为一个优选的方案,所述强磁精选的条件为:采用湿式磁选方式,液固比为2~10ml:1g,磁场强度为1400~1600ka/m。采用强磁选将大部分弱磁性铁矿从赤泥中分离回收,该过程显著提高了后续还原焙烧的效率,缩短还原焙烧过程,减少还原剂用量。
15.作为一个优选的方案,所述选铁尾矿i细磨至-200目粒级占比100%,且-400 目粒级所占比例为60%以上。所述细磨后的选铁尾矿i制成5~8mm粒径大小的球料。
16.作为一个优选的方案,所述还原焙烧的条件为:温度为500~700℃,时间为 30~60min,co气体提供还原气氛,co气体流速为400~700ml/min。在还原焙烧过程中,如果温度过低或时间过短,则容易导致还原反应不完全,影响后续的磁选效果,如果温度过高或时间
过长,易生成浮氏体,也是不利于后续磁选分离的。
17.作为一个优选的方案,所述还原焙烧产物磨矿至-200目。将还原焙烧原料磨矿至适当的粒度,有利于弱磁场对强磁性铁矿的高效富集。
18.作为一个优选的方案,所述弱磁精选的条件:磁场强度为60~90ka/m。余下部分铁矿经过还原焙烧实现物相转化形成强磁性铁矿,进一步采用弱磁选即可实现与非磁性的钛铝等矿物的高效分离。
19.作为一个优选的方案,所述酸性浸出的条件为:采用浓度为2~4mol/l的硫酸作为浸出剂,当硫酸浸出剂的浓度达到一定时,低温拜耳法赤泥中的钙盐会迅速与硫酸结合,形成不溶性硫酸钙固体,覆盖在颗粒表面,从而阻止了颗粒内部的金属的溶出,因此需要控制好硫酸浸出液的浓度。酸性浸出的条件进一步优选为:液固比为6~12ml/g,时间为100~150min,温度为70~90℃,在该酸性浸出条件下兼具了高浸出效率与低能源消耗。
20.作为一个优选的方案,所述沉淀浮选工艺过程为:在钛铝浸出液中加入n
‑ꢀ
亚硝基苯胲胺和ctab(十六烷基三甲基溴化铵)搅拌后,鼓泡浮选,泡沫为富钛产品。由于n-亚硝基苯胲胺可以和钛离子选择性螯合并生成颗粒较大的沉淀物,因此,在表面活性剂的作用下通入一定速率的气泡。可以有效的实现浸出液中铝离子和钛离子的选择性分离。
21.作为一个优选的方案,所述钛铝浸出液中n-亚硝基苯胲胺浓度为0.5~2g/l, ctab用量为0.5~2g/l,ph控制在0.8~1.5。在优选的条件下有利于钛铝浸出液中铝和钛的沉淀浮选分离。
22.相对现有技术,本发明的技术方案带来的有益技术效果:
23.1)本发明技术方案将赤泥采用分步磁选进行优选回收铁,具体分步磁选回收铁的过程为先采用强磁选富集铁矿,再通过还原焙烧来增强铁矿磁性实现弱磁选进一步回收铁矿,从而实现铁矿的高效富集,有利于后续钛铝等有价金属元素的分离回收。
24.2)本发明技术方案在分离回收铁的基础上,易于利用沉淀浮选工艺来实现钛铝浸出液中钛离子和铝离子的高效分离,避免了沉淀浮选工艺过程由于钛铁一起沉淀,而铁钛沉淀物分离困难等技术问题。
25.3)本发明技术方案操作简单、成本低,有利于工业化生产。
附图说明
26.图1为进口铝土矿低温拜耳法赤泥梯级资源化利用的工艺流程图。
具体实施方式
27.以下实施例旨在进一步详细说明本发明内容,而不是限制本发明权利要求的保护范围。
28.实施例1
29.以进口铝土矿低温拜耳法赤泥为原料,低温拜耳法赤泥(干基)粒度≤400 目,化学组成如表1所示。
30.表1.赤泥(干基)的化学组成(wt%)
31.tio2fe2o3al2o3其它9.32%33.23%15.27%42.11%
32.具体步骤如下:
33.将赤泥进行球磨筛分(-400目)后,按液固比为6:1(ml/g)将赤泥分散在水中,液固比不能太高以免后序混合液铝钠浓度被过多稀释。随后立刻进行磁选,磁选时磁场强度控制在1440ka/m磁选得到选铁尾矿i和磁性铁精矿i。将选铁尾矿i细磨至-200目粒级占比100%,-400目粒级所占比例为80%;进一步的将选铁尾矿i进行造球,制成5~8mm的球团,其中混合料水分为8%,将球团置于 120℃干燥箱中进行干燥得干球团;将干球团置于管式炉中,通过co气基还原焙烧,流量为500ml/min,焙烧温度为650℃,时间为30min,冷却后,将焙烧团块磨细至-200目粒级所占质量百分比为100%,在80ka/m的磁场强度下进行磁选,得到钛铝渣和磁性铁精矿ii。将两次磁性铁精矿混合干燥后,经2mol/l 硫酸浸出后,得到富铁溶液;将选铁尾矿ii与3mol/l的硫酸按液固比10:1(ml/g) 配制成混合浆,80℃下反应120min,过滤得到钛铝浸出液,浸出液中钛、铁和铝的浓度分别为500mg/l、80mg/l和1500mg/l。采用1mol/l的naoh溶液将 1l赤泥酸浸液ph调整至0.8,向浸出液中分别加入螯合剂(n-亚硝基苯胲胺)、表面活性剂(ctab)使其在浸出液中的浓度分别为1g/l和1.5g/l,搅拌6min 后刮泡浮选;浮选残余溶液即为富铝溶液,泡沫产品经焙烧、硫酸溶解后得到富钛溶液,调节溶液ph至3,离心分离所得固体经600℃焙烧后得到高纯度氧化钛产品。
34.实验结果:富铁溶液中fe
2+
的浓度为2170mg/l,铁的回收率为88.13%;富铝溶液产品中al
3+
的浓度为1373mg/l,铝的回收率为94.83%;氧化钛产品质量为765mg,钛的回收率为92.17%,钛产品中铁的含量低于1.2%。
35.实施例2
36.以进口铝土矿低温拜耳法赤泥为原料,低温拜耳法赤泥(干基)粒度≤400 目,化学组成如表2所示。
37.表2.赤泥(干基)的化学组成(wt%)
38.tio2fe2o3al2o3其它8.92%32.24%15.46%43.38%
39.具体步骤如下:
40.将赤泥进行球磨筛分(-400目)后,按液固比为8:1(ml/g)将赤泥分散在水中,随后立刻进行磁选,磁选时磁场强度控制在1500ka/m磁选得到选铁尾矿i和磁性铁精矿i。将选铁尾矿i细磨至-200目粒级占比100%,-400目粒级所占比例为60%;进一步的将选铁尾矿i进行造球,制成5~8mm的球团,其中混合料水分为8%,将球团置于100℃干燥箱中进行干燥得干球团;将干球团置于管式炉中,通过co气基还原焙烧,流量为600ml/min,焙烧温度为700℃,时间为40min,冷却后,将焙烧团块磨细至-200目粒级所占质量百分比为100%,在 60ka/m的磁场强度下进行磁选,得到钛铝渣和磁性铁精矿ii。将两次磁性铁精矿混合干燥后,经2mol/l硫酸浸出后,得到富铁溶液;将选铁尾矿ii与3mol/l 的硫酸按液固比10:1(ml/g)配制成混合浆,90℃下反应100min,过滤得到钛铝浸出液,浸出液中钛、铁和铝的浓度分别为250mg/l、50mg/l、和1500mg/l。采用1mol/l的naoh溶液将1l赤泥酸浸液ph调整至0.8,向浸出液中分别加入螯合剂(n-亚硝基苯胲胺)、表面活性剂(ctab)使其在浸出液中的浓度分别为1g/l和1g/l,搅拌8min后刮泡浮选;浮选残余溶液即为富铝溶液,泡沫产品经焙烧、硫酸溶解后得到富钛溶液,调节溶液ph至3,离心分离所得固体经 600℃焙烧后得到高纯度氧化钛产品。
41.实验结果:富铁溶液中fe
2+
的浓度为2238mg/l,铁的回收率为89.67%;富铝溶液产品中al
3+
的浓度为1611mg/l,铝的回收率为97.52%;氧化钛产品质量为398mg,钛的回收率为93.48%,钛产品中铁的含量低于1%。
42.实施例3
43.以进口铝土矿低温拜耳法赤泥为原料,低温拜耳法赤泥(干基)粒度≤400 目,化学组成如表3所示。
44.表3.赤泥(干基)的化学组成(wt%)
45.tio2fe2o3al2o3其它8.74%33.28%16.13%41.85%
46.具体步骤如下:
47.将赤泥进行球磨筛分(-400目)后,按液固比为10:1(ml/g)将赤泥分散在水中,随后立刻进行磁选,磁选时磁场强度控制在1600ka/m磁选得到选铁尾矿i和磁性铁精矿i。将选铁尾矿i细磨至-200目粒级占比100%,-400目粒级所占比例为80%;进一步的将选铁尾矿i进行造球,制成5~8mm的球团,其中混合料水分为8%,将球团置于140℃干燥箱中进行干燥得干球团;将干球团置于管式炉中,通过co气基还原焙烧,流量为700ml/min,焙烧温度为600℃,时间为50min,冷却后,将焙烧团块磨细至-200目粒级所占质量百分比为100%,在60ka/m的磁场强度下进行磁选,得到钛铝渣和磁性铁精矿ii。将两次磁性铁精矿混合干燥后,经2mol/l硫酸浸出后,得到富铁溶液;将选铁尾矿ii与2mol/l 的硫酸按液固比10:1(ml/g)配制成混合浆,70℃下反应150min,过滤得到钛铝浸出液,浸出液中钛、铁和铝的浓度分别为400mg/l、40mg/l、和1350mg/l。采用1mol/l的naoh溶液将1l赤泥酸浸液ph调整至1.5,向浸出液中分别加入螯合剂(n-亚硝基苯胲胺)、表面活性剂(ctab)使其在浸出液中的浓度分别为1g/l和0.5g/l,搅拌5min后刮泡浮选;浮选残余溶液即为富铝溶液,泡沫产品经焙烧、硫酸溶解后得到富钛溶液,调节溶液ph至3,离心分离所得固体经600℃焙烧后得到高纯度氧化钛产品。
48.实验结果:富铁溶液中fe
2+
的浓度为2039mg/l,铁的回收率为86.73%;富铝溶液产品中al
3+
的浓度为1432mg/l,铝的回收率为96.87%;氧化钛产品质量为648mg,钛的回收率为95.42%,钛产品中铁的含量低于0.8%。
49.对比例1
50.该对比实施例与实施例3相比,唯一区别点在于实验所采用赤泥为高温拜耳法赤泥,化学组成如表4所示。
51.表4.赤泥(干基)的化学组成(wt%)
52.tio2fe2o3al2o3其它4.14%11.77%25.48%58.61%
53.实验结果表明:富铁溶液中fe
2+
的浓度为562mg/l,铁的回收率为53.18%;氧化钛产品质量为326mg,钛的回收率为90.38%,钛产品中铁的含量达到27.38%。铁的回收率低,钛铁分离效果差。
54.对比例2
55.该对比实施例与实施例3相比,唯一区别点在于强磁富集的磁场强度为 800ka/m。
56.实验结果表明:富铁溶液中fe
2+
的浓度为1285mg/l,铁的回收率为68.13%;氧化钛
产品质量为782mg,钛的回收率为94.42%,钛产品中铁的含量达到42.86%。铁的回收率低,钛铁分离效果差。
57.对比例3
58.该对比实施例与实施例3相比,唯一区别点在于沉淀剂n-亚硝基苯胲胺的加入量为0.2g/l。
59.实验结果表明:富铝溶液产品中al
3+
的浓度为1340mg/l,铝的回收率为91.39%;氧化钛产品质量为204mg,钛的回收率为58.42%;铝、钛的分离和回收效果差。
60.综上所述,通过对比实施例分析,对于低温拜耳法赤泥,分步磁选与酸浸
‑ꢀ
沉淀浮选法相结合的技术可以显著提高赤泥浸出液中钛、铁、铝的分离回收效率。且该技术药剂消耗少,操作简单,对设备要求较低,适合工业化放大生产。