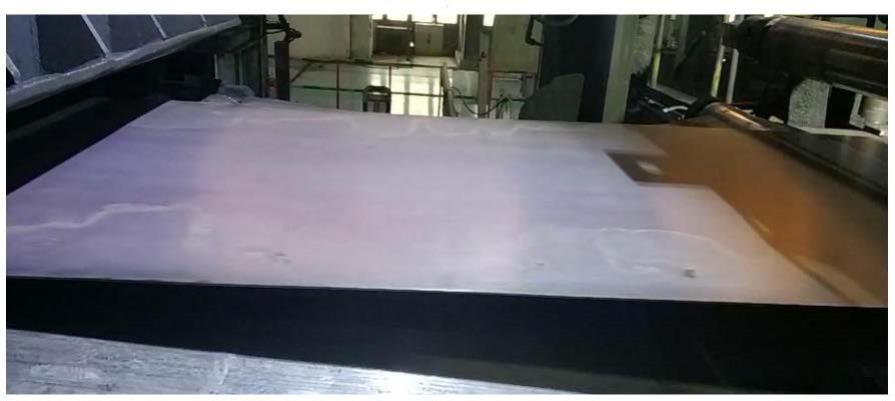
1.本发明涉及热轧双相钢技术领域,具体涉及一种表面无麻点及麻坑的低温卷取型热轧双相钢酸洗及生产方法。
背景技术:2.双相钢自20世纪60年代问世以来,由于良好的强韧性配比、较低的屈强比(rp0.2/rm)、较高的延伸率、很高的加工硬化率、钢种无屈服现象、良好的成形性能且成形后回弹小等优点,被广泛应用于汽车车轮的生产。高等级汽车用热轧酸洗双相钢,不但对冲压性能有严格要求,而且对表面质量的要求也非常苛刻。车轮作为外观件,要求涂装后表面零缺陷,然而涂装对酸洗表面的缺陷具有放大作用,热轧双相钢经过酸洗后,表面应无氧化铁皮残留、麻坑、麻点、锈蚀等缺陷,这对热轧双相钢的酸洗及生产工艺提出了更高的要求。
3.目前,热轧双相钢的生产制造主要包括两条技术路线,低温卷取和中高温卷取。其中中高温卷取型热轧双相钢主要依靠稳定奥氏体元素(如cr、mo等)提高淬透性,将钢卷控制在奥氏体亚稳态无相变转变区进行卷取,这种工艺虽然表面质量良好但是合金成本较高。低温卷取型热轧双相钢采用c-si-mn-cr的成分设计,卷取温度≤150℃,带钢在终轧后和卷取前完成铁素体和马氏体组织的转变。低温卷取型双相钢具有合金设计含量低、成本经济等优点,是目前钢厂的主流生产方式。对于低温卷取型双相钢来说,由于带钢需要冷却到低温,使得带钢表面存在莱顿弗罗斯特效应,这对带钢表面的温度影响极大,无法做到精准控制,实际生产过程中卷取温度一般都在100℃以下。然而卷取温度较低时,带钢表面的冷却水无法蒸干容易发生锈蚀,铁皮结构主要为feo及表层的feo
·
(h2o),此类铁皮疏松多孔容易脱落,如果酸洗工艺不当容易在带钢表面产生麻点、麻坑等缺陷,从而降低产品的竞争力。因此,针对低温卷取型的低成本酸洗双相钢表面质量要求高难题,亟需开发一种全新的表面无麻坑、麻点缺陷的双相钢生产工艺及方法。
4.中国发明专利cn105256323b提供了一种多种化学成分的热轧双相钢的连续酸洗方法,依次包括热轧原料开卷、激光焊接、拉矫机组破磷、紊流酸洗、漂洗和在线平整。在拉矫机组破磷工序,将拉矫机组拉矫延伸率控制在1.0%-1.6%。在紊流酸洗工序采用单酸环境进行酸洗,酸洗温度为55-85℃,并且至少分三段进行酸洗,控制各段酸洗条件为:第一段酸洗过程中,酸洗槽中fe
2+
浓度≤150g/l,所述单酸的浓度为50-120g/l;第二段酸洗过程中,酸洗槽中fe
2+
浓度≤120g/l,所述单酸的浓度60-160g/l;第三段酸洗过程中,酸洗槽中fe
2+
浓度≤80g/l,所述单酸的浓度80-200g/l。紊流酸洗工序中,酸洗速度为40-90m/min。漂洗工序分至少三级进行,最后一级漂洗槽内温度40-50℃,ph值≥6.0。漂洗结束后控制漂洗槽内溶液的电导率≤2.0us/cm。在线平整工序中,平整机组轧制力控制在150-450吨。
5.中国发明专利cn109112433b公开了一种无表面条纹缺陷590mpa级冷轧双相钢及生产方法,该钢板的成分按重量百分比计如下:c:0.050%-0.100%、si:≤0.25%、mn:1.20%-2.00%、p:≤0.012%、s:≤0.008%、al:0.05%-0.10%、sb:0.015%-0.050%,余
120m/s,缓蚀剂浓度控制在10%-20%,酸洗后烘干段长度控制在2-4米,烘干温度≥100℃。平整压下率控制在0.3%-2%,根据产品的不同厚度规格选在不同的平整压下率。
8.中国发明专利cn102337547b公开了一种热轧双相不锈钢板的酸洗方法,该方法采用双混酸酸洗,首先将钢板表面进行抛丸处理,然后将钢板经辊道送入预水冲洗段,钢板水冲洗后进入预酸洗段进行预酸洗,在预酸洗和最终酸洗段均采用hno3+hf混合溶液进行酸洗,其中在预酸洗阶段预酸洗液:hno3,140-180g/l;hf,80-100g/l;酸中金属离子含量:5-40g/l;在最终酸洗阶段,最终酸洗液:hno3,200-280g/l;hf,55-75g/l;酸中金属离子含量:5-40g/l;钢板的运行速度保持在1-3m/min,酸液温度控制在45
±
5℃,出预酸洗段后钢板直接进入水冲洗段,出水冲洗段后钢板进入最终酸洗段进行酸洗,钢板的运行速度保持在1-3m/min,酸液温度控制在45
±
5℃,钢板经过预酸洗和最终酸洗工艺段的时间为11.3-34分钟。钢板出最终酸洗段后进行最终水清洗,然后风幕吹扫、烘干,完成酸洗。
9.仔细分析对比可知,上述专利技术存在以下问题和不足:(1)这些方案主要从钢种开发的角度考虑,所提出的热轧、酸洗、冷轧工艺要求并未提及酸洗过程中带钢的麻点、麻坑缺陷,因此无法保证双相钢酸洗后表面不会出现麻点、麻坑等缺陷;(2)由于低温卷取经济型双相钢工艺特殊,使得带钢表面氧化铁皮结构与其他钢种存在明显差异,因而不能简单的参照其他钢种的酸洗工艺参数,现有的这些专利技术也并未涉及铁皮结构与酸洗工艺参数的对应性问题。
10.因此对双相钢进行在线酸洗时需要结合其特殊性,制定针对性的酸洗工艺。本发明主要针对低温卷取经济型双相钢,分析酸洗前矫直、升弯辊、拉矫等酸洗工艺参数对表面麻点、麻坑的影响,提供一种表面无麻点、麻坑缺陷的高表面质量酸洗双相钢的生产方法。
技术实现要素:11.本发明的目的在于克服现有技术存在的上述问题,根据低温卷取经济型双相钢的生产特点,结合热轧基料表面氧化铁皮结构主要为内层feo+外层fe2o3且铁皮疏松易脱落等实际情况,通过控制矫直、升弯辊、拉矫、酸洗速度等工艺参数,最大程度降低了钢板表面铁皮的脱落情况,同时还确立了辊道上铁皮脱落量与麻点、麻坑缺陷的对应关系,确定低温卷取经济型双相钢的最优酸洗生产工艺,最终批量化获得了表面无麻点、麻坑缺陷的酸洗双相钢产品。
12.一种表面无麻点及麻坑的热轧双相钢酸洗及生产方法,该方法包括以下步骤:热轧钢板经低温卷取得到钢卷,将钢卷开卷后依次经过矫直机、升弯辊、拉矫机组破鳞、酸洗、漂洗后再次卷取,最终得到表面无麻点及麻坑的热轧双相钢。
13.进一步的,热轧钢板低温卷取温度≤150℃,优选为50-100℃。
14.进一步的,低温卷取所得钢卷无需平整,直接在24h之内进入酸洗工序。
15.进一步的,钢卷开卷前需清扫酸洗工序中的矫直辊、升弯辊以及拉矫辊,确保各个辊面的清洁度≤ii级,即辊面铁皮脱落量≤3mg/cm2。对酸洗工序中的各个辊进行清扫,能够有效降低由于辊面铁皮聚积导致在带钢表面形成的物理压坑。
16.进一步的,钢卷开卷后矫直机组不投入使用,并且将上矫直辊抬起到高位,保证带钢表面不与上矫直辊辊面接触。矫直力的大小是参照公式(1)进行优化设定。
17.更进一步的,上矫直辊抬起后与带钢表面的距离≥8mm。
18.进一步的,钢卷开卷后升弯辊也不投入使用,带钢通过时不施加压力,减小因施加压力而使铁皮进一步脱落。
19.进一步的,带钢进入拉矫机组破鳞时,拉矫率≤0.2%,带钢张力100-150kn(参照公式(2)进行优化设定)。拉矫参数的优化和设定是关键,合理的工艺参数能够防止带钢表面的氧化铁皮发生大面积脱落,避免表面出现麻点、麻坑等缺陷。
20.进一步的,所述酸洗在三段式紊流酸洗槽中进行。
21.更进一步的,第一段酸洗温度为70-80℃,fe离子浓度为60-100g/l,酸浓度为100-120g/l;第二段酸洗温度为70-80℃,fe离子浓度为40-80g/l,酸浓度为100-140g/l;第三段酸洗温度为70-80℃,fe离子浓度20-60g/l,酸浓度为120-180g/l;酸洗速度为110-160m/min。
22.进一步的,酸洗后进行三级漂洗,漂洗段采用去离子水,电导率≤10um/cm;漂洗完对带钢进行表面烘干处理,烘干温度为105-130℃。
23.进一步的,整个酸洗过程中需对带钢表面质量进行在线监测,当其表面出现深度≥10um的麻点、麻坑时,再次对酸洗工序的矫直机组辊面、升弯辊辊面、拉矫破鳞机组辊面积聚的脱落铁皮进行清理,清理后的各个辊面清洁度≤ii级。辊面清理完成后,参照前述工艺流程继续完成带钢的酸洗。
24.本发明主要解决了现有热轧双相钢面临的两大难题:一是低温卷取(卷取温度≤150℃)经济型双相钢层流阶段冷速快、取温度低,高温氧化铁皮结构未及时发生相转变而保留到室温,双相钢室温下的铁皮结构主要为内层feo+外层fe2o3,这种铁皮疏松、易脱落,由于工艺特殊性决定了无法从调整工艺角度改善铁皮结构;二是由于双相钢铁皮结构的不同,不能参照其他钢种的酸洗工艺,如果采用不恰当的矫直、升弯辊及拉矫等酸洗工艺参数,会进一步加剧带钢表面铁皮脱落并且在辊道上聚积,从而形成物理压入的麻点、麻坑缺陷。本发明的难点在于如何控制矫直、升弯辊及拉矫等酸洗工艺参数,建立氧化铁皮脱落量、酸洗工艺、麻点及麻坑三者之间的对应关系,确定低温卷取经济型双相钢最优的酸洗生产工艺,从而获得表面无麻点、麻坑缺陷的酸洗双相钢产品。
25.进一步研究发现,低温卷取经济型双相钢表面的内层feo+外层fe2o3铁皮厚度约在10-15um,内层feo在室温下的抗拉强度≤10mpa且硬度为300hv,外层fe2o3基本无塑性且硬度达到1000hv。该双相钢的组织为软相组织f+硬相组织m,其中软相组织表面硬度hbf(铁素体的表面硬度)相对较低,因此要想双相钢在酸洗过程中不产生麻点、麻坑,必须满足以下条件:带钢表面单位面积上的压力p
表面单位面积
<铁素体的表面硬度hbf,根据以下公式可计算带钢表面单位面积上的压力p
表面单位面积
:
26.p
表面单位面积
=f2/m
ꢀꢀꢀ
(1)
27.其中:f2为酸洗过程的矫直力,单位kn;m为带钢表面铁皮脱落量,单位kg。
28.带钢表面铁皮脱落量m又与带钢截面受到的拉伸强度p
截
相关,p
截
的计算公式如下:
29.p
截
=f1/(b*t)
ꢀꢀꢀ
(2)
30.其中,f1为酸洗过程中拉矫带钢的张力,单位kn;t为带钢的厚度,单位mm;b为带钢的宽度,单位mm。
31.当带钢截面受到的拉伸强度p
截
≥内层feo的抗拉强度(最大为10mpa)时,铁皮将会发生破碎并脱落。根据公式(1)-(2),可以准确获知带钢在酸洗过程中的矫直、升弯辊及拉
矫等最佳酸洗工艺参数,并建立了氧化铁皮脱落量、酸洗工艺、麻点及麻坑三者之间的对应关系。据此设定的最佳酸洗工艺参数,能够确保双相钢表面无麻点、麻坑缺陷。
32.相对于现有同类技术,本发明工艺具有以下显著优势:
33.(1)解决了低温卷取经济型双相钢酸洗工艺中的各种难题,成功批量化制得了表面无麻点、麻坑缺陷的酸洗双相钢产品,满足了汽车客户的高品质要求;
34.(2)根据低温卷取经济型双相钢的生产特点和热轧基料表面氧化铁皮内层feo+外层fe2o3的结构特点,首次提出并建立了辊道上铁皮脱落量与麻点、麻坑缺陷的对应关系,并利用其优化和调控矫直、升弯辊、拉矫、酸洗速度等核心、关键工艺参数,最大限度的降低了带钢表面铁皮的脱落情况,确定了低温卷取经济型双相钢的最优酸洗生产工艺;
35.(3)本发明方法操作简单、灵活、成本低、易推广,可根据表面铁皮脱落情况设置不同的工艺参数,在保证酸洗表面无麻点、麻坑缺陷的同时没有降低酸洗的生产效率。
附图说明
36.图1为低温卷取热轧双相钢产品的表面质量照片;
37.图2为低温卷取热轧双相钢表面的铁皮结构与厚度照片;
38.图3为原工艺生产的热轧双相钢酸洗后带钢表面凹坑实物及截面微观形貌照片;
39.图4为原工艺生产的热轧双相钢酸洗后带钢表面凹坑的3d轮廓;
40.图5为本发明新工艺生产的热轧双相钢酸洗后表面质量实物及截面微观形貌照片。
具体实施方式
41.为使本领域普通技术人员充分理解本发明的技术方案和有益效果,以下结合具体实施例及附图进行进一步说明。
42.实施例1
43.一种表面无麻点、麻坑缺陷的双相钢酸洗工艺及生产方法,具体步骤如下:酸洗工序依次包括热轧原料开卷、矫直机、升弯辊、拉矫机组破鳞、三段式紊流酸洗、漂洗、卷取。
44.1、热轧生产完的低温卷取经济型双相钢(卷取温度设定为100℃),无需经过平整。由于卷取温度低,带钢表面会带有残水,需要在24h内准备进行酸洗,降低表面发生电化学腐蚀的概率。
45.2、热轧卷开卷前,首先清扫酸洗工序中的矫直辊、升弯辊及拉矫辊,保证各个辊面的清洁度为ii级。
46.3、钢卷开卷后,矫直机组不投入使用,将上矫直辊抬起到高位,使其与带钢表面的距离为8mm,保证带钢表面不与上矫直辊面接触。
47.4、与此同时升弯辊也不投入使用,带钢通过时不施加压力,避免铁皮在该工序脱落。
48.5、带钢进入拉矫机组破鳞时,拉矫参数的设定是关键。为防止带钢表面氧化铁皮发生大面积脱落,拉矫率要求0.2%,带钢张力100kn。
49.6、带钢进入三段式紊流酸洗槽中进行酸洗。第一段酸洗温度为70℃,fe离子浓度70g/l,酸浓度为100g/l;第二段酸洗温度为75℃,fe离子浓度60g/l,酸浓度为100g/l,第三
段酸洗温度为75℃,fe离子浓度40g/l,酸浓度为150g/l。酸洗速度控制在120m/min,酸洗完的带钢进行三级漂洗。漂洗段采用去离子水,电导率10um/cm。漂洗后进行表面烘干,烘干温度在110℃。
50.7、在生产过程中根据酸洗表面在线检测结果,当双相钢表面出现深度10um的麻点或麻坑时,需对酸洗工序的矫直机组辊面、升弯辊辊面、拉矫破鳞机组辊面上积聚的脱落铁皮进行清理,清理后各个辊面清洁度为ii级。辊面清理完成后,继续按照步骤3及其后续步骤进行带钢的酸洗。
51.实施例2
52.一种表面无麻点、麻坑缺陷的双相钢酸洗工艺及生产方法,具体步骤如下:酸洗工序依次包括热轧原料开卷、矫直机、升弯辊、拉矫机组破鳞、三段式紊流酸洗、漂洗、卷取。
53.1、热轧生产完的低温卷取经济型双相钢(卷取温度设定为80℃),无需经过平整,18h内准备进行酸洗。
54.2、热轧卷开卷前,首先清扫酸洗工序中的矫直辊、升弯辊及拉矫辊,保证各个辊面的清洁度为ii级。
55.3、钢卷开卷后,矫直机组不投入使用,将上矫直辊抬起到高位,使其与带钢表面的距离为10mm,保证带钢表面不与上矫直辊面接触。
56.4、与此同时升弯辊也不投入使用,带钢通过时不施加压力,避免铁皮在该工序脱落。
57.5、带钢进入拉矫机组破鳞时,拉矫率要求0.1%,带钢张力120kn。
58.6、带钢进入三段式紊流酸洗槽中进行酸洗。第一段酸洗温度为75℃,fe离子浓度80g/l,酸浓度为120g/l;第二段酸洗温度为75℃,fe离子浓度80g/l,酸浓度为110g/l;第三段酸洗温度为75℃,fe离子浓度60g/l,酸浓度为150g/l。酸洗速度控制在140m/min,酸洗完的带钢进行三级漂洗。漂洗段采用去离子水,电导率8um/cm。漂洗后进行表面烘干,烘干温度在120℃。
59.7、在生产过程中根据酸洗表面在线检测结果,当双相钢表面出现深度12um的麻点或麻坑时,需对酸洗工序的矫直机组辊面、升弯辊辊面、拉矫破鳞机组辊面上积聚的脱落铁皮进行清理,清理后各个辊面清洁度为i级。辊面清理完成后,继续按照步骤3及其后续步骤进行带钢的酸洗。
60.实施例3
61.一种表面无麻点、麻坑缺陷的双相钢酸洗工艺及生产方法,具体步骤如下:酸洗工序依次包括热轧原料开卷、矫直机、升弯辊、拉矫机组破鳞、三段式紊流酸洗、漂洗、卷取。
62.1、热轧生产完的低温卷取经济型双相钢(卷取温度设定为50℃),无需经过平整,12h内准备进行酸洗。
63.2、热轧卷开卷前,首先清扫酸洗工序中的矫直辊、升弯辊及拉矫辊,保证各个辊面的清洁度为i级。
64.3、钢卷开卷后,矫直机组不投入使用,将上矫直辊抬起到高位,使其与带钢表面的距离为10mm,保证带钢表面不与上矫直辊面接触。
65.4、与此同时升弯辊也不投入使用,带钢通过时不施加压力,避免铁皮在该工序脱落。
66.5、带钢进入拉矫机组破鳞时,拉矫率要求0.2%,带钢张力120kn。
67.6、带钢进入三段式紊流酸洗槽中进行酸洗。第一段酸洗温度为75℃,fe离子浓度80g/l,酸浓度为100g/l;第二段酸洗温度为75℃,fe离子浓度60g/l,酸浓度为110g/l;第三段酸洗温度为80℃,fe离子浓度40g/l,酸浓度为160g/l。酸洗速度控制在150m/min,酸洗完的带钢进行三级漂洗。漂洗段采用去离子水,电导率要求6um/cm。漂洗后进行表面烘干,烘干温度在125℃。
68.7、在生产过程中根据酸洗表面在线检测结果,当双相钢表面出现深度15um的麻点或麻坑时,需对酸洗工序的矫直机组辊面、升弯辊辊面、拉矫破鳞机组辊面上积聚的脱落铁皮进行清理,清理后各个辊面清洁度为ii级。辊面清理完成后,继续按照步骤3及其后续步骤进行带钢的酸洗。
69.对比例1(原工艺)
70.同样组成的热轧双相钢采取低温卷取(ct:180
±
20℃),在此温度范围内带钢表面的冷却存在莱顿弗罗斯特效应,无法实现精准控制,温度波动较大使得带钢存在一定浪型。据此完整的酸洗及生产步骤如下:开卷、平整、重卷、开卷、矫直机、升弯辊、拉矫机组破鳞、三段式紊流酸洗、漂洗、卷取。
71.热轧生产完的低温卷取双相钢,为消除板形、改善表面质量,根据平整计划(一般在轧制5天后)上平整机。平整机轧制力200-300吨,才能有效改善板形,然而过大的轧制力,会造成带钢表面形成物理凹坑。
72.钢卷平整后,根据运输计划(一般2天)送至酸洗线进行酸洗。钢卷酸洗时为保证板形质量,矫直机、升弯辊、拉矫机组全部投入使用。矫直机在100-200t,拉矫率≥0.5%,进一步加大了带钢表面铁皮压入基体形成凹坑的发生率。带钢进入三段式紊流酸洗槽中进行酸洗时。对各段的酸洗温度、fe离子浓度、酸液浓度、酸洗速度无特殊要求。
73.酸洗完成后,根据酸洗表检的检测结果,对钢卷进行封锁与放行。同时如果表面麻点、麻坑严重,后续将不安排钢卷进行酸洗,严重影响了热轧双相钢的生产效率及质量。
74.图1-2为低温卷取热轧双相钢酸洗前所观察到的,是来料的情况说明。其中图1表明采用低温卷取工艺后,热轧钢卷开卷表面存在水印;图2表明采用低温卷取工艺后,带钢表面的氧化铁皮结果主要以feo为主,厚度在7-10um。
75.图3-4为采用原工艺生产的热轧双相钢酸洗后的实物质量及凹坑的深度,从图中可以看出,原工艺生产的产品表面明显存在多个大小不一的麻点和麻坑,不满足客户质量要求。
76.图5为本发明新工艺生产的热轧双相钢酸洗后的实物质量及截面形貌。从图中可以看出,新工艺制得的产品表面未发现麻点或麻坑,相对于原工艺,新工艺的产品表面质量提升效果十分明显。