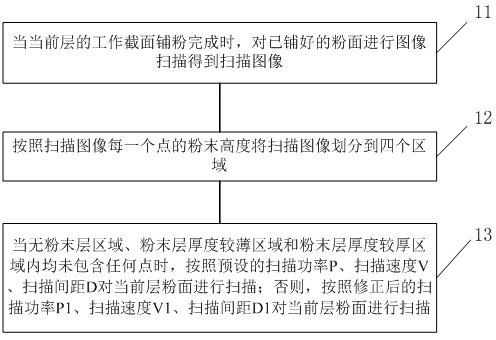
1.本技术涉及增材制造技术领域,特别是涉及一种用于粉床熔融激光烧结的控制方法、系统及增材制造设备。
背景技术:2.增材制造技术是一种通过控制激光逐层扫描,层层叠加形成三维工件的快速制造技术。其工艺流程如下:首先对工件的三维模型进行切片处理,得到工件每一层的轮廓信息;将粉末状材料均匀地铺洒在工作平台表面上,激光根据系统指令选择性地熔化粉末;一个截面完成后,再铺上一层新材料,继续有选择性地根据三维物体对应的截面信息进行扫描;按照此方法再对下一个截面进行铺粉扫描,最终得到三维工件。
3.在增材制造技术的成型过程中,铺粉的均匀性直接影响工件的打印质量,因为粉层过厚会出现粉末未完全熔化,形成夹杂等缺陷;而粉层过薄,则会出现过度烧结,产生气孔等缺陷,同时会产生较大残余应力,导致工件翘曲变形,严重的话导致打印工件的报废,给企业造成大量经济损失。
4.现有技术中,虽然出现了对粉末质量进行监控的技术,但其仅仅也是在监测到粉末质量出现异常时,采取暂停、报警等操作,或者重新铺上一层粉末,然而对于采取的暂停、报警方式,并没有从本质上解决粉末质量出现异常的弊端,而是通过放弃或暂停工作,这样导致了工作效率降低,以及粉末材料的浪费;而对于采取的重新铺上一层粉末方式,粉末的过厚影响了工件的打印质量,同样地,也带来了效率的降低。
技术实现要素:5.基于此,有必要针对上述技术问题,提供了一种用于粉床熔融激光烧结的控制方法、系统及增材制造设备,该方法可以有效地提升工件的表面质量和致密性,且抑制了工件在构建过程中产生的翘曲与变形。
6.为了实现上述目的,本发明提供了一种用于粉床熔融激光烧结的控制方法,包括:步骤一、当当前层的工作截面铺粉完成时,对已铺好的粉面进行图像扫描得到扫描图像;步骤二、按照扫描图像每一个点的粉末高度将扫描图像划分到四个区域,所述四个区域包括无粉末层区域、粉末层厚度较薄区域、粉末层厚度正常区域和粉末层厚度较厚区域;步骤三、当无粉末层区域、粉末层厚度较薄区域和粉末层厚度较厚区域内均未包含任何点时,按照预设的扫描功率p、扫描速度v、扫描间距d对当前层粉面进行扫描;否则,按照修正后的扫描功率p1、扫描速度v1、扫描间距d1对当前层粉面进行扫描;其中,p1=α
•
p,无粉末层区域α为0~0.5、粉末层厚度较薄区域α为0.2~1.0、粉末层厚度正常区域α为1.0、粉末层厚度较厚区域α为1.0~2.0;v1==β
•
v,无粉末层区域β为2.0~10.0、粉末层厚度较薄区域β为1.0~3.0、粉末层厚
度正常区域β为1.0、粉末层厚度较厚区域β为0.2~1.0;d1=γ
•
d,无粉末层区域γ为1.0~5.0、粉末层厚度较薄区域γ为0.5~2.0、粉末层厚度正常区域γ为1.0、粉末层厚度较厚区域γ为0.5~2.0。
7.作为本发明的进一步优选方案,按照扫描图像每一个点的粉末高度将扫描图像划分到四个区域具体包括:当该点粉末层厚度ti满足ti<0.2t0,则该点划分为无粉末层区域;当该点粉末层厚度ti满足0.2t0≤ti<0.8t0,则该点划分为粉末层厚度较薄区域;当该点粉末层厚度ti满足0.8t0≤ti≤1.8t0,则该点划分为粉末层厚度正常区域;当该点粉末层厚度ti满足ti>1.8t0,则该点划分为粉末层厚度较厚区域,其中,t0为一个层厚的高度。
8.作为本发明的进一步优选方案,在步骤二之后,以及步骤三之前还包括区域合并修正,所述区域合并修正具体包括:当粉末层厚度正常区域的外形长度小于或等于20mm,且其面积小于或等于2mm2,或者其外形长度大于20mm,且其区域面积小于或等于10mm2时,将其合并至相邻的粉末层厚度较厚区域或粉末层厚度较薄区域;若不存在相邻的粉末层厚度较厚区域或粉末层厚度较薄区域则不进行合并。
9.作为本发明的进一步优选方案,所述区域合并修正还包括:当粉末层厚度较薄区域的外形长度小于或等于20mm,且其区域面积小于或等于2mm2,或其外形的长度大于20mm区域,且其面积小于或等于10mm2时,将其合并至相邻的粉末层厚度正常区域或无粉末层区域,若不存在相邻的粉末层厚度正常区域或无粉末层区域,则不进行合并。
10.作为本发明的进一步优选方案,所述步骤三按照以下顺序扫描:支撑区域>填充区域>轮廓区域;且支撑区域、填充区域和轮廓区域中每一区域均按照以下顺序进行扫描:粉末层厚度较厚区域>粉末层厚度正常区域>粉末层厚度较薄区域>无粉末层区域。
11.作为本发明的进一步优选方案,所述控制方法还包括:当存在多个相同顺序的下一扫描区域时,按照就近原则与最短路线选择下一扫描区域。
12.本发明还提供了一种用于粉床熔融激光烧结的控制系统,所述控制系统执行所述计算机程序时实现上述任一项所述的用于粉床熔融激光烧结的控制方法的步骤。
13.本发明还提供了一种增材制造设备,包括上述所述的用于粉床熔融激光烧结的控制系统。
14.本发明还提供了一种增材制造设备的制造方法,包括以下步骤:步骤s1、对待打印工件的三维模型进行切片处理,得到每一层的工作截面信息;步骤s2、将粉末状材料均匀地铺洒在工作平台的表面或者已烧结的粉面上;步骤s3、当当前层的工作截面铺粉完成时,对已铺好的粉面进行图像扫描得到扫描图像;步骤s4、按照扫描图像每一个点的粉末高度将扫描图像划分到四个区域,所述四个区域包括无粉末层区域、粉末层厚度较薄区域、粉末层厚度正常区域和粉末层厚度较厚
区域;步骤s5、当无粉末层区域、粉末层厚度较薄区域和粉末层厚度较厚区域内均未包含任何点时,按照预设工作截面信息中的扫描功率p、扫描速度v、扫描间距d对当前层粉面进行扫描;否则,对工作截面信息中的扫描功率p、扫描速度v、扫描间距进行修正,并按照修正后的扫描功率p1、扫描速度v1、扫描间距d1对当前层粉面进行扫描;其中,p1=α
•
p,无粉末层区域α为0~0.5、粉末层厚度较薄区域α为0.2~1.0、粉末层厚度正常区域α为1.0、粉末层厚度较厚区域α为1.0~2.0;v1==β
•
v,无粉末层区域β为2.0~10.0、粉末层厚度较薄区域β为1.0~3.0、粉末层厚度正常区域β为1.0、粉末层厚度较厚区域β为0.2~1.0;d1=γ
•
d,无粉末层区域γ为1.0~5.0、粉末层厚度较薄区域γ为0.5~2.0、粉末层厚度正常区域γ为1.0、粉末层厚度较厚区域γ为0.5~2.0;步骤s6、加工平台下降一个层厚;步骤s7、重复步骤s2-s6,直至待打印工件打印完成。
15.本发明的用于粉床熔融激光烧结的控制方法、系统及增材制造设备,通过获取每一层的粉面并根据每一层的粉面的粉面分别进行区域划分;当无粉末层区域、粉末层厚度较薄区域和粉末层厚度较厚区域内均未包含任何点时(也就是粉面合格),按照预设的扫描功率p、扫描速度v、扫描间距d对当前层粉面进行扫描;否则,按照修正后的扫描功率p1、扫描速度v1、扫描间距d1对当前层粉面进行扫描;这样可以很好地抑制工件在构建过程中产生的翘曲与变形,从而有效地提升了待打印工件的表面质量和致密性。
附图说明
16.图1为本发明用于粉床熔融激光烧结的控制方法提供的一实施例的方法流程图;图2为本发明增材制造设备的制造方法提供的一实施例的方法流程图。
具体实施方式
17.为了使本技术的目的、技术方案及优点更加清楚明白,以下结合附图及实施例,对本技术进行进一步详细说明。应当理解,此处描述的具体实施例仅仅用以解释本技术,并不用于限定本技术。
18.如图1所示,本发明提供的一实施例的用于粉床熔融激光烧结的控制方法,包括:步骤11、当当前层的工作截面铺粉完成时,对已铺好的粉面进行图像扫描得到扫描图像;步骤12、按照扫描图像每一个点的粉末高度将扫描图像划分到四个区域,所述四个区域包括无粉末层区域、粉末层厚度较薄区域、粉末层厚度正常区域和粉末层厚度较厚区域;步骤13、当无粉末层区域、粉末层厚度较薄区域和粉末层厚度较厚区域内均未包含任何点时,按照预设的扫描功率p、扫描速度v、扫描间距d对当前层粉面进行扫描;否则,按照修正后的扫描功率p1、扫描速度v1、扫描间距d1对当前层粉面进行扫描;其中,p1=α
•
p,无粉末层区域α为0~0.5、粉末层厚度较薄区域α为0.2~1.0、粉末层厚度正常区域α为1.0、粉末层厚度较厚区域α为1.0~2.0;
v1==β
•
v,无粉末层区域β为2.0~10.0、粉末层厚度较薄区域β为1.0~3.0、粉末层厚度正常区域β为1.0、粉末层厚度较厚区域β为0.2~1.0;d1=γ
•
d,无粉末层区域γ为1.0~5.0、粉末层厚度较薄区域γ为0.5~2.0、粉末层厚度正常区域γ为1.0、粉末层厚度较厚区域γ为0.5~2.0。
19.上述步骤12中,按照扫描图像每一个点的粉末高度将扫描图像划分到四个区域具体包括:当该点粉末层厚度ti满足ti<0.2t0,则该点划分为无粉末层区域;当该点粉末层厚度ti满足0.2t0≤ti<0.8t0,则该点划分为粉末层厚度较薄区域;当该点粉末层厚度ti满足0.8t0≤ti≤1.8t0,则该点划分为粉末层厚度正常区域;当该点粉末层厚度ti满足ti>1.8t0,则该点划分为粉末层厚度较厚区域,其中,t0为一个层厚的高度。以上无粉末层区域、粉末层厚度较薄区域、粉末层厚度正常区域和粉末层厚度较厚区域四个区域可能不一定每个区域都会存在满足上述要求的点,在此需说明的是,如果某个区域包括的点的数量为0,则该区域为空区域,可以放弃该区域,即对该区域不进行任何操作。
20.在此需说明的是,上述无粉末层区域、粉末层厚度较薄区域、粉末层厚度正常区域和粉末层厚度较厚区域可能都不是一个连续的区域,而是由多个不连续的子区域构成。优选地,为了减少激光空扫时间,提高激光烧结效率,在上述步骤12之后,以及步骤13之前还包括区域合并修正,所述区域合并修正具体包括:当粉末层厚度正常区域的外形长度小于或等于20mm,且其面积小于或等于2mm2,或者其外形长度大于20mm,且其区域面积小于或等于10mm2时,将其合并至相邻的粉末层厚度较厚区域或粉末层厚度较薄区域;若不存在相邻的粉末层厚度较厚区域或粉末层厚度较薄区域则不进行合并。进一步优选地,若既与粉末层较厚区域相连又与粉末层较薄区域相连,则按照粉末层厚度较厚区域>粉末层厚度较薄区域的顺序进行合并,也就是优先合并到粉末层厚度较厚区域,这样可以提高工件致密性,防止缺陷的产生。
21.具体地,所述区域合并修正还包括:当粉末层厚度较薄区域的外形长度小于或等于20mm,且其区域面积小于或等于2mm2,或其外形的长度大于20mm区域,且其面积小于或等于10mm2时,将其合并至相邻的粉末层厚度正常区域或无粉末层区域,若不存在相邻的粉末层厚度正常区域或无粉末层区域,则不进行合并。进一步优选地,若既与粉末层厚度正常区域相连又与无粉末层区域相连,则按照优先级粉末层厚度正常区域>无粉末层区域进行合并,也就是优先合并到粉末层厚度正常区域,这样可以进一步提高工件致密性,防止缺陷的产生。
22.由于在激光烧结过程中会有飞溅产生,飞溅落到粉床上会包裹周围粉末形成大的粉末球,这些粉末球落在粉末层较厚区域更易形成缺陷,影响零件质量。因此,为了进一步提高待打印工件的质量,优选地,所述步骤13按照以下顺序扫描:支撑区域>填充区域>轮廓区域;且支撑区域、填充区域和轮廓区域中每一区域均按照以下顺序进行扫描:粉末层厚度较厚区域>粉末层厚度正常区域>粉末层厚度较薄区域>无粉末层区域。具体地,如支撑(粉末层厚度较厚区域)>支撑(粉末层厚度正常区域)>支撑(粉末层厚度较薄区域)>支撑(无粉末层区域)>填充(粉末层厚度较厚区域)>填充(粉末层厚度正常区域)>填充(粉末层厚度较薄区域)>填充(无粉末层区域)>轮廓(粉末层厚度较厚
区域)>轮廓(粉末层厚度正常区域)>轮廓(粉末层厚度较薄区域)>轮廓(无粉末层区域)。上述支撑区域、填充区域和轮廓区域统称为扫描图像,其可以根据工作截面信息区分。
23.进一步优选地,所述控制方法还包括:当存在多个相同顺序的下一扫描区域时,按照就近原则与最短路线选择下一扫描区域,这样可以进一步减少激光空扫时间。
24.本发明还提供了一种用于粉床熔融激光烧结的控制系统,所述控制系统执行所述计算机程序时实现上述任一实施例所述的用于粉床熔融激光烧结的控制方法的步骤。
25.本发明还提供了一种增材制造设备,包括上述任一实施例所述的用于粉床熔融激光烧结的控制系统。
26.基于与上述用于粉床熔融激光烧结的控制方法相同的发明构思,本发明还提供了一种增材制造设备的制造方法,如图2所示,该制造方法包括以下步骤:步骤21、对待打印工件的三维模型进行切片处理,得到每一层的工作截面信息;步骤22、将粉末状材料均匀地铺洒在工作平台的表面或者已烧结的粉面上;步骤23、当当前层的工作截面铺粉完成时,对已铺好的粉面进行图像扫描得到扫描图像;步骤24、按照扫描图像每一个点的粉末高度将扫描图像划分到四个区域,所述四个区域包括无粉末层区域、粉末层厚度较薄区域、粉末层厚度正常区域和粉末层厚度较厚区域;步骤25、当无粉末层区域、粉末层厚度较薄区域和粉末层厚度较厚区域内均未包含任何点时,按照预设工作截面信息中的扫描功率p、扫描速度v、扫描间距d对当前层粉面进行扫描;否则,对工作截面信息中的扫描功率p、扫描速度v、扫描间距进行修正,并按照修正后的扫描功率p1、扫描速度v1、扫描间距d1对当前层粉面进行扫描;其中,p1=α
•
p,无粉末层区域α为0~0.5、粉末层厚度较薄区域α为0.2~1.0、粉末层厚度正常区域α为1.0、粉末层厚度较厚区域α为1.0~2.0;v1==β
•
v,无粉末层区域β为2.0~10.0、粉末层厚度较薄区域β为1.0~3.0、粉末层厚度正常区域β为1.0、粉末层厚度较厚区域β为0.2~1.0;d1=γ
•
d,无粉末层区域γ为1.0~5.0、粉末层厚度较薄区域γ为0.5~2.0、粉末层厚度正常区域γ为1.0、粉末层厚度较厚区域γ为0.5~2.0。
27.步骤26、加工平台下降一个层厚;步骤27、重复步骤22-26,直至待打印工件打印完成。
28.在此需说明的是,上述无粉末层区域、粉末层厚度较薄区域、粉末层厚度正常区域和粉末层厚度较厚区域可能都不是一个连续的区域,而是由多个不连续的子区域构成。优选地,为了减少激光空扫时间,提高激光烧结效率,在上述步骤22之后,以及步骤23之前还包括区域合并修正,所述区域合并修正具体包括:当粉末层厚度正常区域的外形长度小于或等于20mm,且其面积小于或等于2mm2,或者其外形长度大于20mm,且其区域面积小于或等于10mm2时,将其合并至相邻的粉末层厚度较厚区域或粉末层厚度较薄区域;若不存在相邻的粉末层厚度较厚区域或粉末层厚度较薄区域则不进行合并。进一步优选地,若既与粉末层较厚区域相连又与粉末层较薄区域相连,则按照粉末层厚度较厚区域>粉末层厚度较薄区域的顺序进行合并,也就是优先合并
到粉末层厚度较厚区域,这样可以进一步提高工件致密性,防止缺陷的产生。
29.具体地,所述区域合并修正还包括:当粉末层厚度较薄区域的外形长度小于或等于20mm,且其区域面积小于或等于2mm2,或其外形的长度大于20mm区域,且其面积小于或等于10mm2时,将其合并至相邻的粉末层厚度正常区域或无粉末层区域,若不存在相邻的粉末层厚度正常区域或无粉末层区域,则不进行合并。进一步优选地,若既与粉末层厚度正常区域相连又与无粉末层区域相连,则按照优先级粉末层厚度正常区域>无粉末层区域进行合并,也就是优先合并到粉末层厚度正常区域,这样可以提高工件致密性,防止缺陷的产生。
30.由于在激光烧结过程中会有飞溅产生,飞溅落到粉床上会包裹周围粉末形成大的粉末球,这些粉末球落在粉末层较厚区域更易形成缺陷,影响零件质量。因此,为了进一步提高待打印工件的质量,优选地,所述步骤25按照以下顺序扫描:支撑区域>填充区域>轮廓区域;且支撑区域、填充区域和轮廓区域中每一区域均按照以下顺序进行扫描:粉末层厚度较厚区域>粉末层厚度正常区域>粉末层厚度较薄区域>无粉末层区域。具体地,如支撑(粉末层厚度较厚区域)>支撑(粉末层厚度正常区域)>支撑(粉末层厚度较薄区域)>支撑(无粉末层区域)>填充(粉末层厚度较厚区域)>填充(粉末层厚度正常区域)>填充(粉末层厚度较薄区域)>填充(无粉末层区域)>轮廓(粉末层厚度较厚区域)>轮廓(粉末层厚度正常区域)>轮廓(粉末层厚度较薄区域)>轮廓(无粉末层区域)。
31.进一步优选地, 当存在多个相同顺序的下一扫描区域时,按照就近原则与最短路线选择下一扫描区域,这样可以进一步减少激光空扫时间。
32.以上实施例的各技术特征可以进行任意的组合,为使描述简洁,未对上述实施例中的各个技术特征所有可能的组合都进行描述,然而,只要这些技术特征的组合不存在矛盾,都应当认为是本说明书记载的范围。以上所述实施例仅表达了本技术的几种实施方式,其描述较为具体和详细,但并不能因此而理解为对发明专利范围的限制。应当指出的是,对于本领域的普通技术人员来说,在不脱离本技术构思的前提下,还可以做出若干变形和改进,这些都属于本技术的保护范围。因此,本技术专利的保护范围应以所附权利要求为准。