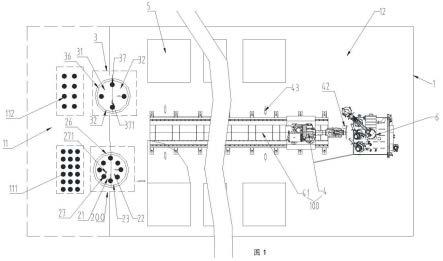
1.本发明的实施例涉及一种机械手自动搬运装置,特别涉及精密铸造炉模壳用机械手自动搬运装置及控制方法。
背景技术:2.真空精密铸造炉模壳搬用通常操作是采用人工搬运的方式来完成浇铸模壳从取壳区域搬运到预热炉焙烧炉中进行预热,按照对应的工艺加热到指定温度后,再进行人工的二次转移,此时模壳由冷态变为热态,通常表面温度会达到800℃
ꢀ‑
1000℃。精密铸造炉熔炼室内完成相应的浇铸动作后,在铸锭室内经过一段时间的凝固,打开铸锭室炉门,由现场工人手动搬运到成品区,不难看出此时搬运的模壳和钢液也是一个高温物体,需要工人在高温环境下完成整个模壳搬运环节。
3.从上不难看出在整个工序中,需要人工来完成工艺流程的衔接,相对于人来说就会带来几个问题。首先,高温环节的安全性,操作人员进行高温物品搬运会存在一系列的安全隐患,高温钢液和模壳所带来的损伤所产生的后果也是不容小觑的;其次,人工搬运效率和稳定性相对来说没有机械的重复性那么高,每次搬运模壳的时间都会有所差异,模壳在搬运过程中温度的变化也是不尽相同。
技术实现要素:4.本发明的实施方式的目的在于提供一种真空精密炉模壳机械手自动搬运装置,通过机械手或者机器人来完成精密铸造炉模壳搬运动作,通过控制系统统筹控制相关单元,完成整个过程的自动化,以解决精密铸造炉现有模壳搬运操作采用大量人工手动操作问题、安全问题以及重复性的重要技术问题。
5.为了实现上述目的,本发明的实施方式设计了一种精密铸造炉模壳用机械手自动搬运装置,包括:精密铸造炉;在所述的精密铸造炉模壳用机械手自动搬运装置的一端设置所述精密铸造炉;机械手搬运装置,在所述的精密铸造炉的预设轴线的一端设置所述的机械手搬运装置;焙烧炉,在所述的机械手搬运装置的两侧设置若干所述的焙烧炉;取料装置,在所述焙烧炉的一侧设置所述的取料装置;成品装置,在所述取料装置的一侧设置所述的成品装置;所述机械手搬运装置将在所述的取料装置上的模壳放入到所述焙烧炉,待所述的焙烧炉焙烧所述模壳完成后,所述的机械手搬运装置将焙烧后的所述模壳,放入所述精密铸造炉,进行铸造;待铸造完成后,所述的机械手搬运装置将所述的模壳运送至所述的成品装置。
6.进一步,在所述的成品装置和取料装置的中间位置设置安全围栏;所述的焙烧炉、
所述机械手搬运装置以及精密铸造炉均设置在所述的安全围栏内;在所述安全围栏一侧设置有所述取料装置,所述取料装置被安全围栏分割成两块,所述取料装置的一半在人工区域内设定为第一取料区,所述取料装置的一半在工作区域内设定为第二取料区;在所述安全围栏一侧相对取料装置纵轴方向平行设置有所述成品装置,所述成品装置被安全围栏分割成两块,所述成品装置的一半在人工区域内设定为第一成品区,所述成品装置的一半在工作区域设定为第二成品区;所述机械手搬运装置设置在工作区域内,并放置于所述取料装置和所述成品装置轴向中心线上,所述机械手搬运装置沿所述所述中心线的水平方向移动;若干个所述焙烧炉设置于工作区域内,在所述机械手搬运装置两侧相对分布排列;在所述安全围栏的另一侧设置有精密铸造炉的炉体。
7.所述人工区域,还包括新模壳堆放点和浇铸件堆放点;所述新模壳堆放点设置在第一取料区的水平方向,所述浇铸件堆放点设置在第一成品区的水平方向。
8.进一步,所述取料装置,还包括:取料托盘,在所述取料托盘上端设置若干个模壳放料位;取料转动轴,在所述的取料托盘的下方,所述取料转动轴与所述取料托盘通过齿盘连接转动;所述取料转动轴的下端活动连接在所述取料底座上;第一伺服电机,所述第一伺服电机设置于所述取料底座上并驱动所述的取料转动轴旋转;第一报警器,所述第一报警器设置于取料底座上方;所述成品装置,还包括:成品托盘,所述成品托盘上端设置若干个模壳成品位;成品转动轴,在所述的成品托盘的下方,在所述的成品转动轴与所述的成品托盘通过齿盘连接转动;所述的成品转动轴下端活动连接所述成品底座上;第二伺服驱动电机、所述第二伺服驱动电机设置于成品底座上并驱动成品转动轴旋转;第二报警器,所述第二报警器设置于成品底座上。
9.进一步,所述机械手搬运装置,还包括:移动轨道装置,在所述取料装置和所述成品装置的轴向中心线上设置所述的,移动轨道装置;工业机器人,在所述的移动轨道装置上活动连接所述的工业机器人;所述的工业机器人沿着所述的移动轨道装置从所述的精密铸造炉移动至所述焙烧炉、所述的工业机器人并在所述取料装置和所述成品装置之间进行移动;红外测温计,在所述的工业机器人上设置所述红外测温计;所述的工业机器人对应任何一个所述焙烧炉的位置设置、第三传感器,在所述的移动轨道装置的两侧对应每个焙烧炉位置设置有第三传感器;所述的工业机器人感应所述的第三传感器,对所述的工业机器人在所述移动轨道装置的位置进行定位。
10.进一步,每个所述模壳放料位设置对应的第一传感器,每次所述第一伺服电机转动所述取料托盘的旋转角度为360
°
/n度,n为6的倍数;工业机器人每次在取料托盘完成取料后,对应模壳放料位的第一传感器的信号输至人机界面并显示无,则信号传输至第一伺服电机并带动取料托盘旋转360
°
/n度,使下一个放置有模壳的模壳放料位旋转至取料点;每个所述第一传感器检测每个任意模壳放料位是否放置模壳,当所有第一传感器检测每个所述模壳放料位位置为空的时候,第一报警器响起,提醒工作人员从新模壳堆放点进行添加模壳操作,直至有新的模壳放入模壳放料位第一报警器报警消除。
11.进一步,每个所述模壳成品位设置对应的第二传感器,工业机器人每次在成品托盘完成放料后,每次第二伺服电机转动带动成品托盘旋转角度360
°
/m度,m为4的倍数,使下一个无模壳的模壳成品位旋转至成品点;每次所述第二传感器检测每个模壳成品位是否放置成品模壳,当所有第二传感器检测每个所述模壳成品位位置为满的时候,第二报警器响起,提醒工作人员在浇铸件堆放点进行模壳堆放操作,直至有空的模壳成品位,第二报警器报警消除。
12.进一步,所述工业机器人的运动控制由上位机程序控制,所述的上位机同时采集模壳加热系统、精密铸造炉生产时的反馈信号;所述工业机器人上的红外测温计温度信号,所述的上位机控制所述工业机器人,完成将模壳从取料装置进入焙烧炉的模壳加热系统、从焙烧炉的模壳加热系统进入精密铸造炉铸型室和从精密铸造炉铸型室取出模壳后进入成品装置的操作。
13.本发明还提供了一种精密铸造炉模壳用机械手自动搬运装置的控制方法,包括以下步骤:步骤s01:确认工艺路线,选定取模壳的位置和放入的焙烧炉的位置;步骤s02:确认模壳是否在模壳放料位:工业机器人放置所需模壳,若第一传感器检测模壳放料位位置为无的时候,现场第一报警器响起,提醒工作人员从新模壳堆放点进行添加模壳操作,直至有新的模壳放入模壳放料位,第一报警器报警消除;步骤s03:选择焙烧炉:选择取、放停机时长最久的焙烧炉位置,即当焙烧炉处于待机或停机状态时候开始计时,默认取计时时间最久的焙烧炉进行放置模壳,在直接满炉为止调至下一个,根据选择的焙烧炉,由工业机器人在移动轨道上完成移动至选择的焙烧炉;步骤s04:焙烧炉模壳加热:确定对应焙烧炉和工位,打开对应的焙烧炉炉门,待炉门开门限位触发后,点击执行,工业机器人完成从s02中确定的取料点取模壳,搬运至焙烧炉中的对应位置后放入模壳,工业机器人退回到原点;关闭焙烧炉炉门,待炉门关闭后点击开始加热按钮,加热开始;步骤s05:模壳加热工艺设定:若模壳加热未达到工艺设定温度,焙烧炉继续加热模壳,若达到模壳工艺要求温度并处于保温状态时,模壳加热流程结束,焙烧炉处于保温状态;步骤s06:选择保温模壳:当焙烧炉处于保温状态时开始计时,默认取计时时长最久的焙烧炉位置,确定待取的加热好的模壳,关闭焙烧炉的加热功能,由工业机器人抓取选择的模壳,自动完成;步骤s07:模壳装入铸锭室:当精密铸造炉熔炼室内熔炼坩埚内钢液温度达到浇铸要求时,精密铸造炉完成对应的浇铸准备操作,打开精密铸造炉铸锭室炉门与对应焙烧炉
的炉门,待到炉门开启后,点击执行,工业机器人完成模壳从焙烧炉搬运到精密铸造炉铸锭室炉模壳升降机构上,工业机器人回到原点,关闭铸锭室炉门与对应焙烧炉的炉门,精密铸造炉开始浇铸操作;步骤s08:模壳出炉:确定模壳放置成品装置位置,精密铸造炉完成浇铸等待操作,打开铸锭室炉门,待炉门反馈信号触发后,点击执行,工业机器人完成从精密铸造炉取走模壳到成品装置放料点放料的动作后回到原点。
14.本发明的实施方式同现有技术相比,在精密铸造炉模壳用机械手自动搬运装置的一端设置精密铸造炉;在精密铸造炉的预设轴线的一端设置机械手搬运装置;在机械手搬运装置的两侧设置若干焙烧炉;在精密铸造炉的另一端的一侧设置取料装置;在精密铸造炉的另一端的一侧设置成品装置;机械手搬运装置将在取料装置上的模壳放入到焙烧炉,待焙烧炉焙烧模壳完成后,机械手搬运装置将焙烧后的模壳,放入精密铸造炉,进行铸造;待铸造完成后,机械手搬运装置将模壳运送至成品装置;通过确认工艺路线,选定取模壳的位置和放入的焙烧炉的位置;从而实现了通过机械手或者机器人来完成精密铸造炉模壳搬运动作,通过控制系统统筹控制相关单元,完成整个过程的自动化,解决了精密铸造炉现有模壳搬运操作采用大量人工手动操作问题、安全问题以及重复性的重要技术问题。
附图说明
15.图1为本发明的结构示意图;图2:为本发明取料装置的主视图;图3:为本发明成品装置的主视图;图4:为本发明的控制方法流程图;图中:1-安全围栏,11-人工区域,111-新模壳堆放点,112-浇铸件堆放点,12-工作区域,21-第一取料区,22-第二取料区,23-取料托盘,24-取料转动轴,25-第一伺服电机,26-取料底座,27-模壳放料位,271-第一传感器,28-第一报警器,3-成品装置,31-第一成品区,32-第二成品区,33-成品托盘,34-成品转动轴,35-第二伺服电机,36-成品底座,37-模壳成品位,371-第二传感器,38-第二报警器,4-工业机器人,41-移动轨道装置,42-红外测温计,43-第三传感器,5-焙烧炉,6-精密铸造炉,100-机械手搬运装置, 200-取料装置。
具体实施方式
16.为使本发明的目的、技术方案和优点更加清楚,下面将结合附图对本发明的各实施方式进行详细的阐述。然而,本领域的普通技术人员可以理解,在本发明各实施方式中,为了使读者更好地理解本技术而提出了许多技术细节。但是,即使没有这些技术细节和基于以下各实施方式的种种变化和修改,也可以实现本技术各权利要求所要求保护的技术方案。
17.本发明的实施方式涉及一种精密铸造炉模壳用机械手自动搬运装置,如图1-图3所示,包括:在本实施例中的精密铸造炉模壳用机械手自动搬运装置的一端设置精密铸造炉6;精密铸造炉6用于精密铸造;
精密铸造炉6的预设轴线的一端设置机械手搬运装置100;在本实施例中的预设轴线为水平中心线,在精密铸造炉6的中心轴线的一端设置机械手搬运装置100。
18.在机械手搬运装置100的两侧设置若干焙烧炉5;焙烧炉5用于对模壳进行预加热;在焙烧炉5的一侧设置取料装置200;取料装置200用于对模壳在取料过程中进行定位;在取料装置200的一侧设置成品装置3;成品装置3用于对成品在放置过程中进行定位。
19.机械手搬运装置100将在取料装置200上的模壳放入到焙烧炉5,待焙烧炉5焙烧所述模壳完成后,机械手搬运装置100将焙烧后的模壳,放入精密铸造炉6,进行铸造;待铸造完成后,机械手搬运装置100将所述的模壳运送至成品装置3。
20.从而实现了通过机械手搬运装置100来完成精密铸造炉模壳搬运动作,完成整个过程的自动化,解决了精密铸造炉现有模壳搬运操作采用大量人工手动操作问题、安全问题以及重复性的重要技术问题。
21.为了实现上述的技术效果,本实施例中的精密铸造炉模壳用机械手自动搬运装置,如图1-图3所示,在成品装置3和取料装置200的中间位置设置安全围栏1;焙烧炉5、机械手搬运装置100以及精密铸造炉6均设置在安全围栏1内;在安全围栏1一侧设置有取料装置200,取料装置200被安全围栏1分割成两块,取料装置200的一半在人工区域11内设定为第一取料区21,取料装置200的一半在工作区域12内设定为第二取料区22;在安全围栏1一侧相对取料装置200纵轴方向平行设置有成品装置3,成品装置3被安全围栏1分割成两块,成品装置3的一半在人工区域11内设定为第一成品区31,成品装置3的一半在工作区域12设定为第二成品区32;机械手搬运装置100设置在工作区域12内,并放置于取料装置200和成品装置3轴向中心线上,机械手搬运装置100沿着中心线的水平方向移动;若干个焙烧炉5设置于工作区域12内,在机械手搬运装置100两侧相对分布排列;在安全围栏1的另一侧设置有精密铸造炉6的炉体。
22.人工区域12,还包括:新模壳堆放点111和浇铸件堆放点112;所述新模壳堆放点111设置在第一取料区21的水平方向,浇铸件堆放点112设置在第一成品区31的水平方向。
23.为了实现上述的技术效果,本实施例中的精密铸造炉模壳用机械手自动搬运装置,取料装置200,还包括:在取料托盘23上端设置若干个模壳放料位27;取料托盘23用于放置模壳放料位27;在取料托盘23的下方,取料转动轴24与取料托盘23通过齿盘连接转动;取料转动轴24的下端活动连接在取料底座26上;取料转动轴24用于将第一伺服电机25的动力传递到取料托盘23上。
24.第一伺服电机25设置于取料底座26上并驱动取料转动轴24旋转;第一报警器28设置于取料底座26上方;第一报警器28主要用于报警。
25.成品装置3,还包括:成品托盘33上端设置若干个模壳成品位37;成品托盘33用于放置模壳成品位37;
在成品托盘33的下方,在成品转动轴34与成品托盘33通过齿盘连接转动;成品转动轴34下端活动连接成品底座36上;第二伺服驱动电机35设置于成品底座36上并驱动成品转动轴34旋转;第二伺服驱动电机35主要起到驱动成品转动轴34旋转的作用。
26.第二报警器38设置于成品底座36上。第二报警器38同样起到报警的作用。
27.本发明的实施方式涉及一种精密铸造炉模壳用机械手自动搬运装置,如图1-图3所示,包括:机械手搬运装置100,还包括:移动轨道装置41,在取料装置200和成品装置3的轴向中心线上设置移动轨道装置41;工业机器人4,在移动轨道装置41上活动连接工业机器人4;工业机器人4沿着移动轨道装置41从精密铸造炉6移动至焙烧炉5、工业机器人4并在取料装置200和成品装置3之间进行移动;在工业机器人4上设置红外测温计42;工业机器人4对应任何一个焙烧炉5的位置设置;红外测温计42用于检测焙烧炉5的温度,进行检测。
28.在移动轨道装置41的两侧对应每个焙烧炉5位置设置有第三传感器43;工业机器人4感应第三传感器43,对工业机器人4在移动轨道装置41的位置进行定位。第三传感器43主要用于工业机器人4在移动轨道装置41上,进行定位。
29.本发明的实施方式涉及一种精密铸造炉模壳用机械手自动搬运装置,如图1-图3所示,每个模壳放料位27设置对应的第一传感器271,每次所述第一伺服电机25转动所述取料托盘23的旋转角度为360
°
/n度,n为6的倍数;工业机器人4每次在取料托盘23完成取料后,对应模壳放料位27的第一传感器271的信号输至人机界面并显示无,则信号传输至第一伺服电机25并带动取料托盘23旋转360
°
/n度,使下一个放置有模壳的模壳放料位27旋转至取料点;每个所述第一传感器271检测每个任意模壳放料位27是否放置模壳,当所有第一传感器271检测每个所述模壳放料位27位置为空的时候,第一报警器28响起,提醒工作人员从新模壳堆放点进行添加模壳操作,直至有新的模壳放入模壳放料位27,第一报警器28报警消除。
30.本发明的实施方式涉及一种精密铸造炉模壳用机械手自动搬运装置,如图1-图4所示,每个模壳成品位37设置对应的第二传感器371,工业机器人4每次在成品托盘33完成放料后,每次第二伺服电机35转动带动成品托盘33旋转角度360
°
/m度,m为4的倍数,使下一个无模壳的模壳成品位37旋转至成品点;每次所述第二传感器371检测每个模壳成品位37是否放置成品模壳,当所有第二传感器371检测每个所述模壳成品位37位置为满的时候,第二报警器38响起,提醒工作人员在浇铸件堆放点进行模壳堆放操作,直至有空的模壳成品位37,第二报警器38报警消除。
31.本发明的实施方式涉及一种精密铸造炉模壳用机械手自动搬运装置,如图1-图4所示,工业机器人4的运动控制由上位机程序控制,上位机同时采集模壳加热系统、精密铸造炉6生产时的反馈信号;所述工业机器人4上的红外测温计42测量温度信号,所述的上位机控制所述工业机器人4,完成将模壳从取料装置200进入焙烧炉5的模壳加热系统、从焙烧炉5的模壳加热系统进入精密铸造炉6铸型室和从精密铸造炉6铸型室取出模壳后进入成品
装置3的操作。
32.本发明的第二实施例中还提供了一种精密铸造炉模壳用机械手自动搬运装置的控制方法,如图4所示,包括以下步骤:步骤s01:确认工艺路线,选定取模壳的位置和放入的焙烧炉5的位置;步骤s02:确认模壳是否在模壳放料位27:工业机器人4放置所需模壳,若第一传感器271检测模壳放料位27位置为无的时候,现场第一报警器28响起,提醒工作人员从新模壳堆放点进行添加模壳操作,直至有新的模壳放入模壳放料位27,第一报警器报警28消除;步骤s03:选择焙烧炉5:选择取、放停机时长最久的焙烧炉5位置,即当焙烧炉5处于待机或停机状态时候开始计时,默认取计时时间最久的焙烧炉进行放置模壳,在直接满炉为止调至下一个,根据选择的焙烧炉5,由工业机器人4在移动轨道装置41上完成移动至选择的焙烧炉5;步骤s04:焙烧炉模壳加热:确定对应焙烧炉5和工位,打开对应的焙烧炉5炉门,待炉门开门限位触发后,点击执行,工业机器人4完成从s02中确定的取料点取模壳,搬运至焙烧炉中的对应位置后放入模壳,工业机器人4退回到原点;关闭焙烧炉5炉门,待炉门关闭后点击开始加热按钮,加热开始;步骤s05:模壳加热工艺设定:若模壳加热未达到工艺设定温度,焙烧炉5继续加热模壳,若达到模壳工艺要求温度并处于保温状态时,模壳加热流程结束,焙烧炉5处于保温状态;步骤s06:选择保温模壳:当焙烧炉5处于保温状态时开始计时,默认取计时时长最久的焙烧炉5位置,确定待取的加热好的模壳,关闭焙烧炉5的加热功能,由工业机器人4抓取选择的模壳,自动完成;步骤s07:模壳装入铸锭室:当精密铸造炉熔炼室内熔炼坩埚内钢液温度达到浇铸要求时,精密铸造炉6完成对应的浇铸准备操作,打开精密铸造炉铸锭室炉门与对应焙烧炉的炉门,待到炉门开启后,点击执行,工业机器人4完成模壳从焙烧炉5搬运到精密铸造炉铸锭室炉模壳升降机构上,工业机器人4回到原点,关闭铸锭室炉门与对应焙烧炉的炉门,精密铸造炉开始浇铸操作;步骤s08:模壳出炉:确定模壳放置成品装置位置,精密铸造炉完成浇铸等待操作,打开铸锭室炉门,待炉门反馈信号触发后,点击执行,工业机器人4完成从精密铸造炉6取走模壳到成品装置放料点放料的动作后回到原点。
33.本领域的普通技术人员可以理解,上述各实施方式是实现本发明的具体实施例,而在实际应用中,可以在形式上和细节上对其作各种改变,而不偏离本发明的精神和范围。