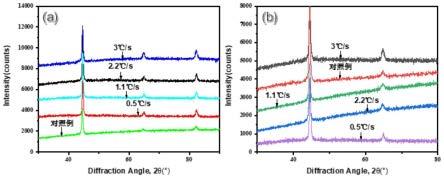
1.本发明涉及一种热轧方法,尤其是一种调控马氏体钢热轧组织的方法。
背景技术:2.相关资料表明,汽车保有量的增多,燃油消耗增多必然造成排放物的增多,每燃烧1l汽油,排放二氧化碳2.2~2.5kg,因此,汽车轻量化必将成为汽车发展的一个趋势。新一代轻量化汽车对其使用的超高强度钢材料提出了更高的要求,需要兼顾轻量化和更好的安全使用性能,材料的强韧性匹配是实现这一目标的重要途径。通常,钢铁材料的强度越高,越容易发生脆性断裂,尤其对于马氏体钢,由于较高的强度,材料面临延伸率不足的问题,因此在进行超高强度马氏体汽车用钢的研究和开发时,对热轧显微组织的调控是有效提高材料的强韧性必要手段。通过对马氏体钢高强度钢热轧组织的调控,有利于汽车轻量化用钢开发研究、选材优化和提高车身安全性。
3.第三代先进高强度钢听过细晶强化、弥散强化等强化机制来获取高强塑积、高硬度、低成本等优异性能的钢种,因此在汽车车身上的应用前景广阔。如马氏体钢为马氏体和残余奥氏体的混合组织,其中较硬的马氏体基体具有较高的强度,而残余奥氏体属于较软相,对材料的韧性贡献巨大。因此,为保证材料能够获得良好的力学性能,显微组织进行调控极其重要。
4.显微组织的差异决定高强度钢的性能差异,是权衡材料强度和韧性的重要手段。传统显微组织调控的方法是通过退火工艺,按照不同的奥氏体化温度、加热速率、保温时间、冷却速率等参数,研究不同参数下显微组织的变化情况。由于通过退火工艺只能对热轧后的组织进行调控,对于如何对热轧组织进行调控,传统调控方法往往忽略这个问题。但是热轧组织对钢后续的退火组织影响较大,从而影响材料的强韧性,传统的调控方法无法满足,因此必须考虑材料热轧组织的调控,必须探索出一种新的对热轧组织的调控方法。
技术实现要素:5.本发明要解决的技术问题是提供一种调控马氏体钢热轧组织的方法,以提升提升钢的力学性能。
6.为解决上述技术问题,本发明所采取的技术方案是:其包括轧制、层流冷却和卷取步骤;所述轧制步骤:一火开轧温度1100~1200℃,终轧温度940~1000℃;二火开轧温度960~1160℃,终轧温度为860~940℃;
7.所述层流冷却步骤:轧后进行层流冷却,在冷却速率0.5~3℃/s的范围内调控热轧组织;
8.所述卷取步骤:层流冷却至600~750℃进行卷取。
9.本发明所述层流冷却步骤中,冷却水的喷水量0.1~0.16m3/h、水压0.03~0.07mpa、水温10~25℃。所述层流冷却步骤中,钢带运行速度2~3mm/min。
10.本发明所述马氏体钢合金成分的质量百分含量为:c 0.3%~0.32%,si 0.2%~
0.3%,mn 0.42%~1.0%,p≤0.01%,s≤0.005%,al 0.04%~0.05%,cr≤0.45%,ni≤0.04%,v 0.011%~0.04%,ti 0.02%~0.04%,nb≤0.06%,cu≤0.2%,b 0.0018~0.002%,余量为fe和不可避免的杂质。
11.采用上述技术方案所产生的有益效果在于:由于超高强度钢的热轧组织对其淬火后钢的组织影响较大,因此材料的性能也会发生变化。本发明通过层流冷却速率来调控马氏体钢热轧组织,更好的实现对热轧组织的调控,可显著提升钢的力学性能,为超高强度钢的研究及开发提供有益指导。本发明通过对热轧钢板组织的调控,使热轧板中存在大量尺寸在50~120nm的fe3c纳米颗粒,位错密度控制在在1.2
×
105~5.4
×
107,硬度控制在220~300hv,退火后可使钢的强度控制在1500~2200mp,原始奥氏体晶粒尺寸控制在8.5~13.5μm。
附图说明
12.下面结合附图和具体实施方式对本发明作进一步详细的说明。
13.图1为本发明试样例及对照组热轧淬火板的拉伸应力变化曲线,图中横坐标代表拉伸时间进程;
14.图2为本发明试样例所得铸锭试样;
15.图3为本发明试样例不同层流冷却速率下的热轧板样品照片;
16.图4为本发明试样例及对照组的热轧板及热轧淬火板x射线衍射(xrd)分析图;
17.图5为本发明试样例不同层流冷却速率下的热轧板扫描电子显微镜(sem)照片;
18.图6为本发明试样例不同层流冷却速率下的热轧板透射电子显微镜(tem)照片;
19.图7为本发明试样例不同层流冷却速率下的热轧板中析出相尺寸统计结果图;
20.图8为本发明试样例及对照组的热轧板硬度测试结果图;
21.图9为本发明试样例及对照组的热轧板位错密度测试结果图;
22.图10为本发明试样例热轧淬火板在苦味酸腐蚀后的扫描电子显微镜(sem)照片;
23.图11为本发明试样例不同层流冷却速率下的热轧淬火板透射电子显微镜(tem)照片。
具体实施方式
24.实施例1-7:本调控马氏体钢热轧组织的方法采用下述工艺。
25.(1)本方法适用于下述合金成分的马氏体钢(wt):c 0.3%~0.32%,si 0.2%~0.3%,mn 0.42%~1.0%,p≤0.01%,s≤0.005%,al 0.04%~0.05%,cr≤0.45%,ni≤0.04%,v 0.011%~0.04%,ti 0.02%~0.04%,nb≤0.06%,cu≤0.2%,b 0.0018~0.002%,余量为fe和不可避免的杂质。各实施例以及对照例的合金成分见表1。
26.表1:各实施例以及对照例的合金成分
[0027][0028]
(2)本方法包括轧制、层流冷却和卷取步骤,各步骤工艺如下所述。
[0029]
①
轧制步骤:铸锭采用粗轧-精轧两火轧制,一火开轧温度1100~1200℃、终轧温度940~1000℃;二火开轧温度960~1160℃、终轧温度为860~940℃;一火轧制道次见表2,二火轧制道次见表3;精轧后最终成品厚度为3~4.5mm。
[0030]
表2:一火轧制道次
[0031]
道次设定辊缝/mm实际辊缝/mm压下率/%轧制力/kn1145.00145.016.455882135.00135.006.905153125.00125.007.405004115.00114.998.015375100.00100.0113.03698690.0090.0010.01562780.0079.9911.12601870.0070.0212.47649960.0060.0014.318011050.0050.0116.659741140.0040.0020.0111081230.0030.0124.9714161320.0019.9933.392024
[0032]
表3:二火轧制道次
[0033]
道次设定辊缝/mm实际辊缝/mm压下率/%轧制力/kn110.009.9950.04238525.005.0249.75330833.503.4930.493145
[0034]
②
层流冷却步骤:轧后进行层流冷却;冷却水的喷水量0.1~0.16m3/h、水压0.03
~0.07mpa、温度10~25℃,钢带运行速度2~3mm/min,从而控制在冷却速率0.5~3℃/s的范围内通过控制喷水量调控热轧组织。
[0035]
③
卷取步骤:层流冷却至600~750℃进行卷取,卷取后的热轧板即可进行后续的淬火或退火等处理。所得热轧板热轧组织中位错密度高,无fe3c颗粒存在;热轧板中渗碳体析出相平均颗粒尺寸为50~120nm、硬度为240~365hv、位错密度为1.2
×
105~5.4
×
107;热轧板经退火后,所得超高强度钢的抗拉强度可达1500~2200mpa、原始奥氏体晶粒尺寸为8.5~13.5μm,根据所需,可生产热冲压成形钢、延性淬火钢、马氏体钢;热轧板淬火后,基体为马氏体,马氏体板条宽度为80~200nm,板条束直径为2~4μm,抗拉强度高达1500~2200mpa,析出相为含有vc、cu、fe3c的纳米颗粒。各实施例的工艺参数见表4,各实施例所得热轧板的力学性能见表5。
[0036]
表4:各实施例的工艺参数
[0037][0038]
表5:各实施例所得热轧板的力学性能
[0039][0040][0041]
表5中,所述对照例采用常规工艺生产。
[0042]
材料力学性能试验:
[0043]
(1)拉伸性能测试:
[0044]
上述实施例6铸坯采用轧制、层流冷却和卷取步骤进行生产,其中,层流冷却步骤分别以冷却速率0.5℃/s、1.1℃/s、2.2℃/s、3℃/s进行控制,其它工艺同上述实施例6,制得4组试样例、每组4个;取上述试样例进行淬火后的钢钢板进行测试,根据gb/t228.1-2010标准,沿淬火板轧制方向取样,试样标距80mm、平行段宽度20mm。每组取四个淬火板试样,测试过程按测试标准规定进行,获得的拉伸性能为轧制方向的纵向性能;其中,1~4#为0.5℃/s样品的淬火板,5~8#为1.1℃/s样品的淬火板,9~12#为2.2℃/s样品的淬火板,13~16#为3.0℃/s样品的淬火板;采用常规方法生产的17~20#为对照组样品的淬火板;表6为试样和对照组试样的抗拉性能。图1为4组试样例及对照组热轧淬火板的拉伸应力变化曲线,图中横坐标代表拉伸时间进程。
[0045]
表6:测试试样和对照组试样的抗拉性能
[0046][0047][0048]
由表6可见,采用本方法所得淬火板的抗拉强度最高可以达到2200mpa、最低可以达到1500mpa,对照组的抗拉强度最高为1490mpa。可见,层流冷却速率不同,热轧板淬火后的力学性能不同,而本方法在层流冷却速率在0.5~3℃/s之间,可大幅度改善钢的力学性能;抗拉性能的差异是钢材的层流冷却速率导致的结果;传统钢中当前尚无对热轧组织调控的研究,本方法通过对层流冷却速率的控制,实现对热轧组织的调控,获得不同的机械性能。
[0049]
(2)材料的显微组织分析:
[0050]
上述4组试样例铸坯进行取样,样品如图2所示;在上述4组试样例中取样,所取热轧板样品如图3所示,其中,(a)为0.5℃/s样品的热轧板样,(b)为1.1℃/s样品的热轧板样,(c)为2.2℃/s样品的热轧板样,(d)为3℃/s样品的热轧板样,(e)为对照组样品的热轧板
样。
[0051]
上述4组试样例和对照组样中所取热轧板样和淬火板均采用x射线晶体衍射(xrd)法分析材料晶体结构,其中(a)为热轧板样、(b)为淬火板样;如图4所示,热轧板和热轧淬火板均为bcc晶体结构,采用扫描电子显微镜(sem)观察材料基体金相组织,采用透射电子显微镜(tem)分析热轧组织,上述分析均依照常规方法进行。
[0052]
上述4组试样例和对照组样中所取热轧板样进行sem分析,如图5所示;其中,(a)为0.5℃/s样品的热轧板样,(b)为1.1℃/s样品的热轧板样,(c)为2.2℃/s样品的热轧板样,(d)为3℃/s样品的热轧板样,(e)为对照组样品的热轧板样;由图5可见,在0.5℃/s冷速下,热轧在铁素体基体上分布着大量的析出相,随着冷速的增加,析出相数量减少;当增加至3℃/s时,组织中无析出相颗粒存在(图5(d)),对照组中析出相数量最多(图5(e))。
[0053]
上述4组试样例和对照组样中所述热轧板样进行tem分析,如图6所示;其中,(a)(b)为3℃/s样品的热轧板样,(c)(d)为0.5℃/s样品的热轧板样,(e)(f)为1.1℃/s样品的热轧板样,(g)(h)为2.2℃/s样品的热轧板样,(i)(j)为对照组样品的热轧板样;由图6可见,图6(a)热轧组织中的析出相为fe3c颗粒,且fe3c尺寸较图6(b)中的大,数量多。图7进一步对析出相尺寸进行统计,其中(a)为3℃/s样品的热轧板样,(b)为0.5℃/s样品的热轧板样,(c)为1.1℃/s样品的热轧板样,(d)为2.2℃/s样品的热轧板样;结果显示图6(a)中的fe3c尺寸在80~160nm,图6(b)中的在20~100nm,图6(c)中的在20~100nm;图6(d)中的在160~280nm。
[0054]
上述4组试样例和对照组样中所述热轧板样的硬度测试结果见图8;上述4组试样例和对照组样中所述热轧板样的位错密度计算结果见图9。
[0055]
图10为上述4组试样例和对照组样中所述热轧淬火板在苦味酸腐蚀后的sem照片;其中,(a)为3℃/s样品的淬火板样,(b)为0.5℃/s样品的淬火板样,(c)为1.1℃/s样品的淬火板样,(d)为2.2℃/s样品的淬火板样,(e)为对照组样品的淬火板样;经统计图10(a)的原始奥氏体晶粒尺寸为13.5μm,图9(b)为12μm;图9(c)为10.5μm;图9(d)为8.5μm;图9(e)为14μm。
[0056]
上述4组试样例和对照组样中所述热轧淬火板进行tem分析,结果见图11;其中,(a)(b)为3℃/s样品的淬火板样,(c)(d)为0.5℃/s样品的淬火板样,(e)(f)为1.1℃/s样品的淬火板样,(g)(h)为2.2℃/s样品的淬火板样,(i)(j)为对照组样品的淬火板样;经统计,图11(a)马氏体板条厚度为200nm;图11(c)马氏体板条厚度为146nm;图11(e)马氏体板条厚度为112nm;图11(h)马氏体板条厚度为80nm;图11(g)为225nm。