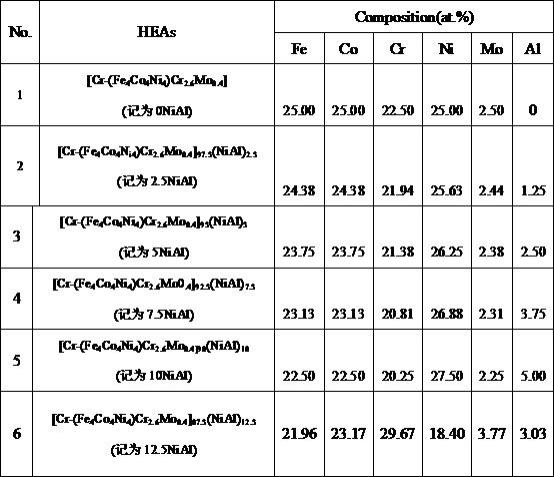
1.本发明涉及一种耐强酸冲蚀的高熵合金涂层成分设计及制备方法,采用激光熔覆方法制备,属于新材料研发及涂层技术领域。
背景技术:2.贵州磷矿资源丰富,瓮福集团作为贵州磷矿支柱产业之一,其磷酸生产能力已达到1000吨有效p2o5/天,产品主要为浓度48~52%的磷酸,副产品为18~20%的氟硅酸(h2sif6) 1.1万吨/年,排放废渣二水石膏(caso4·
2h2o) 145万吨/年。目前瓮福集团生产磷酸以湿法为主,湿法磷酸生产装置由于其生产工艺的特殊性,在生产过程中,各种工况介质均涉及硫酸、磷酸、氢氟酸及氯离子等多种腐蚀性组分,且温度较高,酸度大,故对材料的腐蚀很强。设备在承受腐蚀作用的同时,还要承受腐蚀介质中大量固相颗粒(二氧化硅、磷石膏等)的磨损作用。腐蚀与磨损的迭加和相互作用,造成材料快速破坏失效。由于服役条件苛刻,磷化工设备的许多零部件使用寿命较短,尤其是搅拌桨叶片、石膏再浆泵、料浆过流部件、料浆泵等。
3.在磷酸反应制备过程中,904l不锈钢搅拌桨被用来对反应槽内部进行搅拌,加速槽内液体流动及反应的快速进行。在此种强酸环境下,搅拌桨叶片与磷矿石之间发生强烈碰撞。然而,904l不锈钢为单一的立方结构,硬度较低(~190hv),不能满足强酸冲蚀的服役要求。仅我省瓮福磷矿一家企业在正常情况下每根搅拌桨轴的使用寿命为7-9个月,此外,开磷集团、湖北宜化、兴发集团等企业的叶片腐蚀、磨损严重,缩短了搅拌叶片和轴的使用寿命,造成每年修复成本费用极高,在1亿元以上,这已成为广大磷化工企业面临的共性问题。
4.高熵合金因其独特的成分及组织结构而具有优异的性能,与传统合金设计理念不同,高熵合金通过合理地成分设计,加上适当的制备手段,达到兼具耐磨性和耐蚀性,因此在搅拌浆叶片表面制备一层专用的耐磨耐蚀的高熵合金材料,有望延长搅拌浆叶片的服役寿命,降低生产成本。但是高熵合金成分复杂、组织多变,需要在理论指导下实施精确的成分设计。近年来大连理工大学董闯教授提出利用团簇加连接原子模型来设计合金成分。该模型是将理想结构单元分为团簇和连接原子两个部分。其中,团簇是由中心原子及其最近邻壳层原子组成,而连接原子则是处于中心原子的次近邻位置。溶剂与溶质原子在模型中的占位由各元素之间的混合焓δh
mix
决定。通常,溶剂原子占据团簇的壳层位置,溶质与溶剂原子之间δh
mix
越负,则溶质原子占据团簇中心位置。反之,溶质原子占据连接原子位置。如图一所示,fcc结构固溶体的团簇加连接原子模型中,中心原子周围最近邻原子的配位数是12,连接原子个数一般为1-6,因此可表示为[a-b
12
]c
1-6
,其中a为中心原子,b为壳层原子,c为连接原子。该模型的特点是从短程序的角度解释了理想固溶体模型,准确描述合金固溶体的理想结构单元以及溶剂与溶质原子的点阵占位情况,进而对固溶体成分进行优化,可有效取代传统“炒菜式”的合金成分设计,大大节约时间和人力成本。他们的研究工作给我们的启发是如果利用团簇加连接原子模型对cocrfeni-m合金体系成分进行优化设计,则可
能设计出满足极端条件下服役的高耐磨耐蚀的高熵合金材料。但由于宽带激光熔覆具有超快速加热和超快速冷却的特点,如果涂层与基材的适配性差,将会导致熔覆过程中裂纹产生。
技术实现要素:[0005]
本发明要解决的技术问题是采用团簇加连接原子模型解析904l不锈钢牌号,基于cocrfeni设计一种有序相析出强化的高熵合金成分,并采用激光熔覆技术在904l不锈钢表面制备,获得一种高硬度且耐强酸冲刷腐蚀的高熵合金涂层材料。
[0006]
本发明的技术方案:其特征包括如下步骤:一种耐强酸冲蚀的高熵合金涂层材料的制备方法,包括如下步骤:(a)粉末配制:选用高纯度fe、co、ni、cr、al、mo金属粉末,按照fe:25.00~21.88 at.%,co:25.00~21.88 at.%,cr:22.50~19.69 at.%,ni:25.00~28.13 at.%,mo:2.50~2.19 at.%,al:0~6.25 at.%,进行粉末配制,采用精度为0.1mg的mettler toledo电子天平进行称量;(b)粉末球磨:将称量好的混合粉末置于不锈钢球磨罐中进行球磨,使粉末混合均匀;球磨后的粉末经过120目不锈钢分样筛过筛后,将样品放置于真空干燥箱中保存。
[0007]
(c)基材使用:904l不锈钢常作用为磷酸生产过程中磷酸搅拌器的叶片材料,选用尺寸为50mm(长)*30mm(宽)*10mm(厚)的904l不锈钢作为基材,其成分列于表一;表一 904l不锈钢化学成分(wt%)fecrnimocmnsip scubal19~2323~284~5≤0.02≤2≤2≤0.045 ≤0.0351~2(d)激光熔覆涂层制备:实验中采用预铺粉末法,激光熔覆前先在基材表面预铺一层厚1.5mm的粉末,并用不锈钢片压实。激光熔覆过程中通过氩气保护,氩气纯度为99.99%,气流密度为25 l
·
min-1
。
[0008]
步骤(a)中,各纯金属粉末均购于长沙天久公司,纯度皆在99.6%以上、尺寸45~105μm。
[0009]
步骤(b)中,使用qm-3sp2行星式球磨机,球磨参数为:球料比:5:1,球磨转速200rmp/min,球磨时间2h,期间每球磨30min停转15min再球磨,不断循环。
[0010]
步骤(c)中,先用砂轮机清除基材熔覆面的氧化皮,利用酒精清洗表面油污,并用吹风机吹干,干燥保存。
[0011]
步骤(d)中,熔覆所使用的激光器型号为6kw rc-lms-6000-r光纤激光器,工艺参数为:激光功率p = 2500 w,扫描速率v = 5 mm/s,矩形光斑尺寸20mm*2mmmm。
[0012]
本发明的原理:本发明是在解析904l不锈钢牌号的基础上,设计出与之成分性质相近的高熵合金涂层成分,使涂层与基材的热物性参数接近,可以降低涂层开裂敏感性。由3d过渡族元素构成的cocrfeni-m系高熵合金是目前研究最多的合金体系。在通过溶入足够cr含量以保证耐蚀性的前提下,为了提升耐磨性,需要加入能够析出有序相的元素。该体系有序相类型分为以c14-laves、mc为代表的非共格析出相和以b2-(nial)和l1
2-(ni3al)为代表的共格析出相。一般认为,c14、mc等非共格析出相虽具有明显的强度增益效果,但高的界面能容易诱发微电偶腐蚀。而共格析出相在提高强度的同时,不明显降低塑性,且低的共格
界面能不易诱发微电偶腐蚀。因此,共格析出强化是在不降低耐蚀性能的前提下,提高合金硬度和韧性的可行办法。本发明采用团簇加连接原子模型,设计适用于强酸腐蚀和矿石粉强烈冲刷环境条件下(以下简称极端条件下)的高熵合金成分,并运用激光熔覆技术,在904l不锈钢表面制备既耐强酸冲刷腐蚀的高熵合金涂层,为我国磷化工产业提供耐强酸冲刷腐蚀的表面涂层配方及涂层制备技术。
[0013]
本发明的成分设计:根据904l不锈钢牌号(00cr20ni25mo4.5cu),化为相应的原子比:fe-24.2ni-22.9cr-2.6mo-1.5mn-1.3cu,根据团簇加连接原子模型,其团簇式可描述为[cr-fe
7.6
ni
3.9
mn
0.3
cu
0.2
]cr
2.6
mo
0.4
。在不考虑mn和cu的情况下,引入“平均原子”概念,将原子性质相近、相互作用力较弱的第
ⅷ
族fe、co、ni看作平均原子m,并选用m为溶剂原子,取代壳层原子位置的fe和ni,由此构建的团簇模型式为[cr-fe4co4ni4]cr
2.6
mo
0.4
(co25cr22.5fe25ni25mo2.5, at.%)。在此基础上,在连接原子位置添加有序相b2(nial)进行成分设计和优化,进一步构建有序相共格析出的[cr-(fe4co4ni4)cr
2.6
mo
0.4
]
100-x
(nial)
x
高熵合金体系,以期提高合金硬度,其中x=0, 2.5, 5, 7.5, 10, 12.5 at.%。
[0014]
本发明的有益效果:引入团簇加连接原子模型设计理论,通过解析904不锈钢化学成分,构建与其成分相似的团簇式[cr-fe4co4ni4]cr
2.6
mo
0.4
高熵合金成分,并在连接原子位置添加nial原子进一步构建有序相共格析出的[cr-(fe4co4ni4)cr
2.6
mo
0.4
]
100-x
(nial)
x
高熵合金,通过宽带激光熔覆技术制备高熵合金涂层,以提高合金的硬度和耐冲刷腐蚀性能。通过团簇加连接原子模型理论解析传统904l不锈钢牌号,设计出与之成分相近的合金成分,并通过激光熔覆技术进行涂层制备。本发明取代了传统“炒菜式”和“试错式”的设计模式,并且建立起了传统合金材料与高熵合金之间的桥梁,极大地拓宽了高熵合金的设计和应用范围,大大地节约时间和成本。
附图说明
[0015]
图1是本发明的fcc型固溶体团簇加连接原子模型示意图;图2是本发明的实施例1的[cr-(fe4co4ni4)cr
2.6
mo
0.4
]
100-x
(nial)
x
高熵合金涂层xrd图谱;图3是本发明的实施例1的[cr-(fe4co4ni4)cr
2.6
mo
0.4
]100-x(nial)x高熵合金涂层sem显微组织;图4是本发明的实施例1的[cr-fe4co4ni4)cr
2.6
mo
0.4
]100-x(nial)x高熵合金涂层tem显微组织;其中(a)7.5nial涂层明场相(b)7.5nial涂层衍射斑点(c)12.5nial涂层明场相(d)12.5nial涂层衍射斑点(e)12.5nial涂层高分辨图像和傅立叶转变斑点;图5是本发明的实施例1的[cr-(fe4co4ni4)cr
2.6
mo
0.4
]
100-x
(nial)
x
高熵合金涂层硬度分布曲线图;图6是本发明的实施例1的[cr-(fe4co4ni4)cr
2.6
mo
0.4
100-x
(nial)
x
高熵合金涂层室温磨损质量损失(磨损参数:加载载荷20n,时间15min,往复长度5mm);图7是本发明的实施例1的[cr-(fe4co4ni4)cr
2.6
mo
0.4
]
100-x
(nial)
x
高熵合金涂层室温磨损曲线变化(磨损参数:加载载苛20n,时间15min,往复长度5mm)图8是本发明的实施例1的[cr-(fe4co4ni4)cr
2.6
mo
0.4
]
100-x
(nial)
x
高熵合金涂层室温磨痕形貌(磨损参数:加载载苛20n,时间15min,往复长度5mm);其中,(a)904l基材(b)
0nial涂层 (c)2.5nial涂层 (d)5nial(e)7.5nial涂层(f)10nial涂层(g)12.5nial涂层;图9是本发明的实施例1的[cr-(fe4co4ni4)cr
2.6
mo
0.4
]
100-x
(nial)
x
高熵合金涂层在0.5mol/l h2so4溶液中的电化学极曲线;图10是本发明的实施例1的[cr-(fe4co4ni4)cr
2.6
mo
0.4
]
100-x
(nial)
x
高熵合金涂层在0.5mol/l h2so4溶液中的电化学阻抗图;图11是本发明的实施例1的[cr-(fe4co4ni4)cr
2.6
mo
0.4
]
100-x
(nial)
x
高熵合金涂层冲蚀腐蚀质量曲线图(冲刷腐蚀条件:50%硫酸溶液,30%不规则玻璃颗粒,实验温度80
±
2℃);图12是本发明的实施例1的[cr-(fe4co4ni4)cr
2.6
mo
0.4
]100-x(nial)x高熵合金涂层冲蚀腐蚀sem形貌(冲刷腐蚀条件:50%硫酸溶液,30%不规则玻璃颗粒,实验温度80
±
2℃);其中:(a)904l基材(b)0nial涂层(c)2.5nial涂层 (d)5nial(e)7.5nial涂层(f)10nial涂层(g)12.5nial涂层。
具体实施方式
[0016]
实施例1第一步:将粉末粒度200目以上的fe、co、ni、cr、al、mo合金粉末按表二成分进行配制,每个成分称量粉末50g。
[0017]
第二步:将称量好的合金粉末放置于不锈钢球磨罐中,球磨机转速为200转/min,球磨时间为2h。经120目不锈钢标准筛过筛后,将粉末存放于真空干燥箱中保存待用。
[0018]
第三步:利用手持式打磨机去除基材表面氧化皮,直到表面出现金属光泽,并用酒精去除表面污渍,吹风机吹干,置于真空干燥箱中保存。
[0019]
第四步:将球磨后的合金粉末预置在基材表面,预涂合金粉末厚度1.5mm,利用不锈钢模具在基材表面预置一层1.5 mm厚的粉末,并用不锈钢刀压实。利用宽带激光熔覆设备进行涂层制备。
[0020]
表二 高熵合金涂层化学成分
图2中[cr-fe4co4ni4]cr
2.6-x
al
x
mo
0.4
高熵合金涂层xrd图谱表明nial涂层由单一fcc固溶体组成。随着nial含量添加,涂层中图中(111)峰出现逐渐减弱然后增强,而(200)峰的变化趋势刚好相反,先增强再减弱,具有明显的择优取向和各向异性。衍射峰的强度反映了晶体中原子的排列,是判断晶体结构的基础。衍射峰强度逐渐减弱,表明不同半径原子排列更加均匀,晶格畸变变大,扩散效应增强。
[0021]
图3nial涂层显微组织为典型的胞状晶结构,包括胞状晶和晶间区域,这主要是由于激光熔覆过程快速冷却,导致温度梯度及一定程度的成分过冷。此外,随着nial添加,涂层组织逐渐变细。
[0022]
图4(a)为7.5nial涂层的明场相,图中黑色的析出相与fcc基底呈良好冶金结合,析出相尺寸大约200nm,图四(b)为(a)中黑色析出相的衍射斑点,可以看出高熵合金具有fcc结构沿[011]方向生长,析出相具有明显的超晶格点阵结构,推测其为l1
2-ni3al共格析出相。图四(c)为12.5nial涂层明场相显微组织,可以看出有大量fcc结构纳米晶析出。图四(e)为12.5nial涂层的高分辨形貌及相应的快速傅立叶转变斑点。析出相与fcc基底呈完全共格关系。基底尺寸约为0.2272nm,析出相尺寸约为0.2195nm。
[0023]
图5为[cr-(fe4co4ni4)cr
2.6
mo
0.4
]
100-x
(nial)
x
高熵合金涂层硬度分布曲线图,涂层硬度基本保持稳定,在热影响区开始下降。0-12.5nial涂层平均硬度为207.1hv
0.2
, 227.4hv
0.2
,258.6hv
0.2
, 299.3hv
0.2
, 275.3hv
0.2
, 239.6hv
0.2
,均高于904l基材(~190hv),且呈现先增加再下降的趋势。
[0024]
图6为[cr-(fe4co4ni4)cr
2.6
mo
0.4
]
100-x
(nial)
x
高熵合金涂层室温磨损质量损失,磨
损质量变化与涂层硬度变化呈反比,呈现先下降后升高的趋势,7.5nial涂层质量损失最少为7.9mg,904l基材质量损失最大为12.5mg。
[0025]
图7为[cr-(fe4co4ni4)cr
2.6
mo
0.4
]
100-x
(nial)
x
高熵合金涂层室温磨损曲线变化,磨损初期,曲线急剧上升,主要原因是涂层表面较粗糙,磨损副与涂层相互作用明显,之后磨损曲线趋于稳定。涂层平均摩擦系数变化也呈现先下降再上升的趋势。7.5nial涂层摩擦平均摩擦系数值最低f
ave
=0.6737,代表其耐磨性最好。
[0026]
图8为[cr-(fe4co4ni4)cr
2.6
mo
0.4
]
100-x
(nial)
x
高熵合金涂层室温磨痕形貌,904l基材由于硬度低,磨损后表面出现明显的塑性变形和剥落现象。nial涂层表面出现明显的犁沟和剥落,典型的粘着磨损机制。
[0027]
图9为[cr-(fe4co4ni4)cr
2.6
mo
0.4
]
100-x
(nial)
x
高熵合金涂层电化学极曲线,904l基材及nial涂层出现明显的钝化区,说明在电化学腐蚀过程中有钝化膜自发形成。
[0028]
图10为[cr-(fe4co4ni4)cr
2.6
mo
0.4
]
100-x
(nial)
x
高熵合金涂层在0.5mol/l h2so4溶液中的电化学阻抗图,阻抗谱越大,涂层耐蚀性越好,从图中可以看出来0nial,2.5nial涂层阻抗半径小于904l基材,说明0nial,2.5nial涂层电化学耐蚀性较基材稍差。7.5nial涂层具有最大的阻抗半径,说明其电化学耐蚀性最好。
[0029]
图11为涂层在强酸冲蚀条件下出现质量损失,在0-10h涂层质量损失增加迅速,10-24h涂层质量损失变化缓慢增加。904l基材,0nial,2.5nial,5nial,7.5nial,10nial,12.5nial涂层冲蚀质量损失分别为7.1mg,6.6mg,6.2mg,5.4mg,5.0mg,5.9mg,8.5mg在所有试样中,12.5nial涂层质量损失多于904基材,表现出较差的冲蚀性能。其他涂层冲蚀质量损失均低于基材,7.5nial涂层质量损失最少(5.0 mg),表明耐冲刷腐蚀性能较好。
[0030]
图12(a)中904l冲蚀后表面出现明显的切削和犁沟形貌。nial涂层冲蚀后主要沿晶界发生腐蚀,此外还存在少量冲蚀坑。0nial涂层(图(b))晶界腐蚀最明显。2.5-12.5nial涂(图(c~f))层冲蚀后,沿晶界出现大量的犁沟、切削和冲蚀孔洞。12.5nial涂层(图(g))发生最严重的晶界腐蚀弄丢,冲蚀过程中,流动的溶液和冲蚀颗粒在晶界或孔处形貌涡流加速腐蚀。