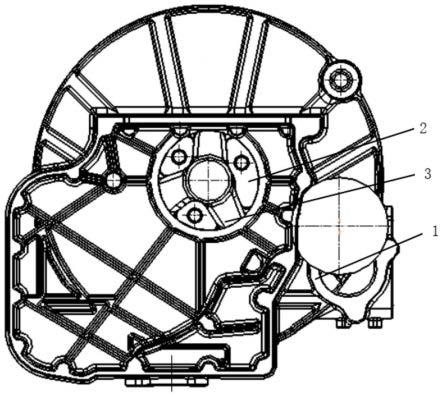
1.本发明属于低压铸造工艺技术领域,具体涉及一种飞轮壳体的低压铸造模具及工艺方法。
背景技术:2.现有一种某飞轮壳体铸件的外观尺寸为553mm
×
549mm
×
203mm,零件壁厚不均匀,如图1—图2所示,上法兰壁厚20-25mm,中间壁厚7-8mm,齿轮室安装孔厚度60-70mm,内腔为上小下大“内扣”结构,其中,φ2>φ1,低压铸造时难以形成至上而下顺序凝固的温度场。目前,飞轮壳体低压铸造模具设计多采用多内浇口及多冒口的模具方法,存在产品毛坯的材料利用率低的缺陷,材料利用率仅约70-75%。
技术实现要素:3.本发明的目的就是为了解决上述背景技术存在的不足,提供一种飞轮壳体的低压铸造模具及工艺方法。提升飞轮壳体材料利用率,减少生产节拍。
4.本发明采用的技术方案是:一种飞轮壳体的低压铸造模具,包括设于模具的上模和下模内的飞轮壳内腔砂芯,所述飞轮壳内腔砂芯的浇口为三叉圆锥形内浇道。
5.进一步优选的结构,所述三叉圆锥形内浇道分别对着飞轮壳铸件的三个不同方向。保证铸造充型时铝水平稳,铝水能够顺利的将模具充满,实际生产时压力参数为升液压力250mbar/15s,充型1段压力260mbar/4s,充型2段压力300mbar/2s,增压压力550mbar/2s。
6.进一步优选的结构,所述飞轮壳内腔砂芯设有多处芯头定位结构,所述飞轮壳内腔砂芯的砂芯芯头放置在下模对应位置,放置后使飞轮壳内腔砂芯与芯头的配合间隙为0.1-0.2mm。
7.本发明的模具在飞轮壳铸件的内腔的上小下大“内扣”结构特征无法通过金属模直接脱模形成,为解决内腔结构特征设计了飞轮壳内腔砂芯,飞轮壳内腔砂芯设计了多处芯头定位结构,铸造时将砂芯芯头放置在下模对应位置,放置后使砂芯与芯头的配合间隙为0.1-0.2mm。
8.上述方案中,采用单升液道由零件大圆处进料分成三个内浇口,在其它部位不使用冒口;通过设计砂芯的结构及砂芯与模具间隙,排出铸造过程的气体解决铸件憋气缺陷;通过使用多处模具冷却来调节模具温度,进而影响低压铸造时金属液在模具中的凝固顺序,减少或取消浇口、冒口的结构设计,使材料利用率大幅提升至90%以上。
9.进一步优选的结构,在所述飞轮壳内腔砂芯与上模接触的部位设有排气间隙用于将充型过程的气体排入飞轮壳内腔砂芯与上模构成的空腔内,并通过上模上的排气孔排出模具。
10.进一步优选的结构,所述排气间隙为0.1-0.2mm。
11.进一步优选的结构,在所述下模对应的飞轮壳体下齿轮室安装孔区域设有多处水冷却预铸销。
12.在不采用冒口结构的条件下通过快速冷却给模具降温解决螺栓孔的内部缩松缺陷,零件螺栓安装孔处漏气、漏油问题。下齿轮室安装孔区域的水冷却预铸销,在低压铸造开始后20s对模具通水冷却,作用时间120s后停止冷却。
13.进一步优选的结构,所述模具在所述飞轮壳体油泵孔区域设有第一冷却结构。
14.在飞轮壳体油泵孔区域设有第一冷却结构,在低压铸造开始后25s对模具通水冷却,作用时间200s后停止冷却。
15.进一步优选的结构,所述模具在所述飞轮壳体油封孔浇口区域设有环形的第二冷却结构。
16.在飞轮壳体油封孔浇口区域设有环形的第二冷却结构,解决油封孔浇口区域凝固缓慢铸造生产效率低问题,油封孔浇口区域风冷在低压铸造开始后100s对模具通风冷却,作用时间200s后停止冷却。
17.进一步优选的结构,所述模具在所述飞轮壳体下齿轮室安装孔区域设有多处水冷镶块。
18.上述方案,给飞轮壳体铸件局部厚大的区域降温,解决齿轮室区域局部温度高铸件容易变形的问答题。水冷镶块冷却在低压铸造开始后30s对模具通水冷却,作用时间180s后停止冷却。
19.本发明设计多处冷却结构,加快模具散热降温。
20.所述模具的内腔采用树脂砂芯结构成型。
21.一种飞轮壳体的低压铸造模具的工艺方法,包括利用飞轮壳体的低压铸造模具将飞轮壳体进行低压铸造成型。
22.本发明飞轮壳体低压铸造模具浇注系统只采用单升液道分出三叉形内浇口,其它部位不使用冒口进行模具温度调节控制凝固顺序,通过使用多处模具冷却来调节模具温度,进而影响低压铸造时金属液在模具中的凝固顺序,加快模具冷却提升产品生产节拍。
附图说明
23.图1是现有的飞轮壳体结构示意图;
24.图2是现有的飞轮壳体结构特征示意图;
25.图3是本发明飞轮壳内腔砂芯结构示意图;
26.图4是本发明三叉圆锥形内浇道结构示意图;
27.图5是本发明飞轮壳内腔砂芯特征示意图;
28.图6是本发明三叉圆锥形内浇道局部示意图;
29.图7是本发明排气孔位置示意图;
30.图8是本发明飞轮壳体下齿轮室安装孔区域水冷却结构示意图;
31.图9是本发明飞轮壳体油泵孔区域冷却结构示意图;
32.图10是本发明飞轮壳体油封孔浇口区域冷却结构示意图;
33.图11是本发明飞轮壳体下齿轮室安装孔区域水冷镶块结构示意图。
34.图中,1-飞轮壳铸件、2-飞轮壳内腔砂芯、3-三叉圆锥形内浇道、4-砂芯定位芯头、5-上模、6-空腔、7-排气孔、8-下模、9-下齿轮室安装孔、10-水冷却预铸销、11-第一冷却结构、12-第二冷却结构、13-水冷镶块、14-侧抽水冷镶块、15-侧抽风冷镶块。
具体实施方式
35.下面结合附图和具体实施例对本发明作进一步的详细说明,便于清楚地了解本发明,但它们不对本发明构成限定。
36.如图3-4、图6所示,本发明一种飞轮壳体的低压铸造模具,包括设于模具的上模5和下模8内的飞轮壳内腔砂芯2,飞轮壳内腔砂芯2的浇口为三叉圆锥形内浇道3。
37.三叉圆锥形内浇道3分别对着飞轮壳铸件1的三个不同方向。
38.如图5所示,飞轮壳内腔砂芯2设有5处芯头定位结构4,飞轮壳内腔砂芯2的砂芯芯头放置在下模8对应位置,放置后使飞轮壳内腔砂芯2与芯头的配合间隙为0.1-0.2mm。
39.如图7所示,在飞轮壳内腔砂芯2与上模5接触的部位设有排气间隙用于将充型过程的气体排入飞轮壳内腔砂芯2与上模5构成的空腔6内,并通过上模3上的排气孔7排出模具。
40.排气间隙为0.1-0.2mm。
41.如图8所示,在下模8对应的飞轮壳体下齿轮室安装孔9区域设有5处水冷却预铸销10。
42.如图9所示,模具在飞轮壳体油泵孔区域设有第一冷却结构11。
43.如图10所示,模具在飞轮壳体油封孔浇口区域设有环形的第二冷却结构12。
44.如图11所示,模具在飞轮壳体下齿轮室安装孔9区域设有多处水冷镶块,包括6处水冷镶块13、2处侧抽水冷镶块14、1处侧抽风冷镶块15。
45.本发明模具的内腔采用树脂砂芯结构成型。
46.本发明的飞轮壳体低压铸造生产模具,浇道为三叉形内浇道,其它部位无浇注系统及冒口,保证产品的出品率高>90%。本发明在上模与砂芯之间设有可收纳及带有排气孔的空腔,将充型过程的气体顺畅排出;本发明在下模样和上模样分别设计了多处强制冷却结构,冷却结构为模具内浇口区域及模具局部散热慢的部位进行冷却降低模具温度,缩短生产节拍<350s。
47.本说明书中未作详细描述的内容属于本领域专业技术人员公知的现有技术。