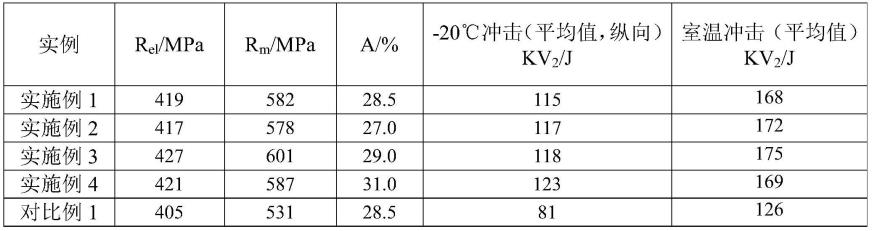
一种稀土微合金化355mpa级低成本热轧h型钢的冶炼连铸方法
技术领域
1.本发明属于冶炼连铸技术领域,具体涉及一种稀土微合金化355mpa级低成本热轧h型钢的冶炼连铸方法。
背景技术:2.包钢q355b h型钢的生产主要采用钒合金化来确保钢坯和钢材各项性能,目前生产情况比较稳定,力学性能富余量近50mpa。由于国内钢筋新标准的制定实施、环保对v提取工艺的高要求以及手机、新能源汽车等领域对v的需求,导致v供需不平衡,市场价格居高不下,并有持续上涨的趋势。为此寻找适宜的微合金元素及工艺,减小对钒氮合金的依赖,降低生产成本迫在眉睫。
3.专利文献cn110484825a(以下称文献1)公开一种低成本355mpa热轧h型钢及其制备方法,其通过采用铌钒复合微合金化成分设计,以降低钢中锰含量达到h型钢的综合性能,大幅度降低了冶炼成本,但得到的热轧h型钢中仍含有成本较高的v元素,并不利于该文献1生产成本的降低。
技术实现要素:4.针对现有技术中存在的问题,本发明一个方面提供一种稀土微合金化355mpa级低成本热轧h型钢的冶炼连铸方法,其化学成分按质量百分比计为:c 0.17%~0.24%、si 0.35%~0.55%、mn 1.30%~1.60%、p≤0.035%、s≤0.035%、re 0.002%~0.003%,其余为fe和不可避免的杂质;
5.所述冶炼连铸方法包括以下工序:转炉冶炼、lf精炼、异型坯连铸、铸坯堆垛缓冷,其中在所述异型坯连铸工序中,全程采用保护浇注,过热度≤30℃,采用弱冷制度,入拉矫机前,铸坯腹板目标温度控制为820-830℃,铸坯翼缘目标温度控制为785-795℃,r角温度控制为855-870℃,采用恒拉速操作,拉速控制在0.9m/min-1.2m/min。
6.在一些实施方式中,在所述转炉冶炼工序中,终渣碱度按3.0控制,终点控制目标c≥0.03%,t≥1610℃,采用simn、mnfe脱氧合金化,终脱氧采用有al脱氧,在出钢过程中加入白灰,出钢挡渣。
7.在一些实施方式中,在所述lf精炼工序中,全程进行吹ar操作,根据转炉钢水成份及温度进行脱硫、成份微调及升温操作,脱硫后s≤0.020%,成分含量为c 0.17%~0.24%、si 0.35%~0.55%、mn 1.30%~1.60%、p≤0.035%、s≤0.020%,升温后温度t≥1560℃;精炼后期加入稀土,加入后保证稀土含量为0.002~0.003%,保证软吹时间大于10min。
8.在一些实施方式中,在所述铸坯堆垛缓冷工序中,缓冷时间大于48小时。
9.本发明另一方面提供一种稀土微合金化355mpa级低成本热轧h型钢,其由上述的冶炼连铸方法得到的连铸坯经轧制获得。
10.在一些实施方式中,所述稀土微合金化355mpa级低成本热轧h型钢的力学性能满足:屈服强度≥415mpa,抗拉强度≥575mpa,延伸率a≥27.0%,-20℃纵向冲击功≥115j,室温冲击功≥165j。
11.基于以上技术方案提供的稀土微合金化355mpa级低成本热轧h型钢的冶炼连铸方法通过采用稀土元素,并在异型坯连铸工序中控制过热度≤30℃,采用弱冷制度,入拉矫机前,铸坯腹板目标温度控制为820-830℃,铸坯翼缘目标温度控制为785-795℃,r角温度控制为855-870℃,并采用恒拉速操作,拉速控制在0.9m/min-1.2m/min,得到的连铸坯经轧制后得到的热轧h型钢中不含有成本较高的v元素,但仍保持优良的综合力学性能,因此可明显降低热轧h型钢的生产成本。另外,相对于上述文献1生产的热轧h型钢,本发明提供的稀土微合金化355mpa级低成本热轧h型钢的韧性性能更加优良。
具体实施方式
12.本发明旨在提供一种稀土微合金化355mpa级低成本热轧h型钢的冶炼连铸方法,并提供由该冶炼连铸方法获得的稀土微合金化355mpa级低成本热轧h型钢。
13.本发明提供的稀土微合金化355mpa级低成本热轧h型钢的冶炼连铸方法包括以下工序:转炉冶炼、lf精炼、异型坯连铸、铸坯堆垛缓冷,其中:
14.在所述转炉冶炼工序中,终渣碱度按3.0控制,终点控制目标c≥0.03%,t≥1610℃,采用simn、mnfe脱氧合金化,终脱氧采用有al脱氧,在出钢过程中加入白灰,出钢挡渣;
15.在所述lf精炼工序中,全程进行吹ar操作,根据转炉钢水成份及温度进行脱硫、成份微调及升温操作,脱硫后s≤0.020%,成分含量为c 0.17%~0.24%、si 0.35%~0.55%、mn 1.30%~1.60%、p≤0.035%、s≤0.020%,升温后温度t≥1560℃;精炼后期加入稀土,加入后保证稀土含量为0.002~0.003%,保证软吹时间大于10min;
16.在所述异型坯连铸工序中,全程采用保护浇注,过热度≤30℃,采用弱冷制度,入拉矫机前,铸坯腹板目标温度控制为820-830℃,铸坯翼缘目标温度控制为785-795℃,r角温度控制为855-870℃,采用恒拉速操作,拉速控制在0.9m/min-1.2m/min,连铸坯断面尺寸可为h440mm
×
105mm
×
555mm;
17.在所述铸坯堆垛缓冷工序中,缓冷时间大于48小时。
18.经以上冶炼连铸方法获得的连铸坯可按照上述文献1中公开的轧制方法轧制得到稀土微合金化355mpa级低成本热轧h型钢。
19.在一些实施例中,所述稀土微合金化355mpa级低成本热轧h型钢的按质量百分比计为:c 0.17%~0.24%、si 0.35%~0.55%、mn 1.30%~1.60%、p≤0.035%、s≤0.035%、re(例如ce)0.002%~0.003%,其余为fe和不可避免的杂质;可选为:c 0.17%~0.19%、si 0.36%~0.41%、mn 1.30%~1.34%、p≤0.023%、s≤0.013%、re 0.0022%~0.0028%,其余为fe和不可避免的杂质。
20.在一些实施例中,所述稀土微合金化355mpa级低成本热轧h型钢的力学性能满足:屈服强度≥415mpa,抗拉强度≥575mpa,延伸率a≥27.0%,-20℃纵向冲击功≥115j,室温冲击功≥165j。
21.以下通过具体实施例详细说明本发明的内容,实施例旨在有助于理解本发明,而不在于限制本发明的内容。
22.实施例1:
23.该实施例旨在生产一种稀土微合金化355mpa级低成本热轧h型钢,其化学成分如下表1所示。具体生产方法包括以下工序:转炉冶炼、lf精炼、异型坯连铸、铸坯堆垛缓冷、异型坯加热、轧制、轧后冷却;其中异型坯加热、轧制、轧后冷却工序按照上述文献1的操作进行,异型坯连铸工序的控制参数如下表2所示,对连铸坯表面质量进行检查,同时对内部质量进行热酸低倍检验并跟踪检查h型钢的钢坯质量,未发现明显铸坯表面及内部质量缺陷,铸坯质量良好,铸坯表面裂纹率低于1%,轧制后的h型钢各项性能均满足标准要求,具体如下表3所示。
24.实施例2-4
25.实施例2-4按照实施例1的操作进行,不同之处仅在于生产的稀土微合金化355mpa级低成本热轧h型钢的化学成分,以及异型坯连铸工序中参数控制不同,具体如下表1和表2所示。对实施例2-4轧制后得到的稀土微合金化355mpa级低成本热轧h型钢的力学性能进行检验,检验结果如下表3所示。
26.对比例1
27.对比例1按照实施例1的操作进行,不同之处仅在于异型坯连铸工序中参数控制不同,具体如下表1和表2所示。对对比例1轧制后得到的热轧h型钢的力学性能进行检验,检验结果如下表3所示。
28.表1:各实例的热轧h型钢的化学成分(wt%)
29.实例csimnpsre实施例10.190.361.310.0160.0100.0025实施例20.170.391.300.0220.0060.0026实施例30.180.381.340.0230.0090.0028实施例40.190.411.330.0150.0130.0022对比例10.190.361.310.0160.0100.0025
30.表2:各实例的异型坯连铸工序参数
31.实例过热度(℃)拉速(m/min)翼缘板端部(℃)r角(℃)腹板(℃)实施例1271.11795855825实施例2281.10790860821实施例3271.14788867826实施例4261.19791861829对比例1271.11805890855
32.表3:各实例的热轧h型钢的力学性能
33.34.由上表1-表3所示,可知实施例1-4生产的稀土微合金化355mpa级低成本热轧h型钢均具有优良的综合力学性能,力学性能满足:屈服强度≥415mpa,抗拉强度≥575mpa,延伸率a≥27.0%,-20℃纵向冲击功≥115j,室温冲击功≥165j。相比之下,对比例1在异型坯连铸工序中控制相对较高的铸坯腹板目标温度、铸坯翼缘目标温度和r角温度,生产获得的热轧h型钢的强度和韧性性能均明显降低。并且相对于上述文献1,本发明采用稀土代替文献1生产的热轧h型钢中的v和nb元素,并调节其他元素的含量,且通过优化冶炼连铸方法中的异型坯连铸工序参数,能够在保证生产的热轧h型钢具有优良的综合力学性能(甚至优于上述文献1,例如耐低温韧性性能)的基础上,明显降低热轧h型钢的生产成本。
35.最后应说明的是:以上所述仅为本发明的优选实施例,并不用于限制本发明,尽管参照前述实施例对本发明进行了详细的说明,对于本领域的技术人员来说,其依然可以对前述各实施例所记载的技术方案进行修改,或者对其中部分技术特征进行等同替换。凡在本发明的精神和原则之内,所作的任何修改、等同替换、改进等,均应包含在本发明的保护范围之内。