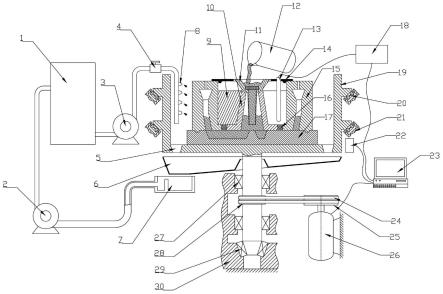
1.本发明属于航空材料铸造领域,涉及一种航空薄壁耐热铝合金机匣铸造的方法。
背景技术:2.外涵机匣是航空发动机的重要部件之一,该类铸件壁厚一般在3mm以下,且整体结构呈锥台型,除安装边可以加工,其他铸件处的结构都不允许加工,且表面精度要求不低于ra6.3,铸件整体尺寸不小于300mm
×
300mm
×
500mm,且内表面不允许加工,该类铸件对耐热及强度要求较高,只能够选用铸造用高强耐热铝合金。耐热铝合金是铝铜基合金,但高强耐热铝合金具有结晶温度范围广,呈糊状凝固,铸造流动性差,补缩难度大等问题。由于铸件薄壁面积过大,熔模铸造用蜡模强度不足,会发生变形;砂型重力铸造过程中,合金液流动性差,薄壁位置出现浇不足缺陷;反重力铸造过程中,在铸件表皮凝固后,难以将补缩压力传递到铸件内部,导致内部产生缩松缺陷。
技术实现要素:3.发明目的
4.为解决上述现有技术薄壁耐热铝合金机匣铸件铸造的难点问题,本发明提供一种航空薄壁耐热铝合金机匣铸造的方法。
5.技术方案
6.一种航空薄壁耐热铝合金机匣铸造系统,包括模具组、水箱、转动平台和电机,水箱能够给模具组提供冷却水,电机能够带动转动平台水平旋转,模具组包括模具和模具底座,模具固定连接于模具底座的上端,转动平台的上部是开放的,模具底座固定于转动平台内侧的底部上端。
7.进一步的,所述模具包括连接在一起的中央模具和外周模具,中央模具设有浇口杯,浇口杯的下部设置有合金液存储区外罩,合金液存储区外罩的内部为合金液存储区,模具底座设置有多个浇道,合金液存储区与浇道是连通的,外周模具内设置有铸件腔,铸件腔与浇道也是连通的,铸件腔的上端设有冒口,冒口设有排气孔,模具设置有加热装置。
8.进一步的,所述加热装置包括模具加热棒、加热棒支板和加热棒电源,模具加热棒通过加热棒支板固定在中央模具和外周模具之间,加热棒支板连接加热棒电源。
9.进一步的,所述中央模具的外周均布固定有多个支撑立板,支撑立板与外周模具相接触,中央模具与外周模具的底部隔有石墨环。
10.进一步的,所述转动平台的外周设置有滚动轴承,滚动轴承位于上部设备基座内,转动平台的一侧设置有转速传感器。
11.进一步的,所述电机的转动轴上固定有主动皮带轮,转动平台的下部固定有从动皮带轮,主动皮带轮和从动皮带轮通过传动皮带连接,转动平台的下部外周设置有转动轴承和圆锥滚子轴承,转动轴承和圆锥滚子轴承位于下部设备基座内侧。
12.进一步的,所述加热棒电源、转速传感器和电机电性连接有工控机。
13.进一步的,所述水箱通过管道连接有能够将水箱内的水向外抽取的上水水泵,上水水泵的出水口连接的管道设置有阀门,上水水泵的出水口连接的管道还设有冷却水喷口,冷却水喷口位于转动平台和模具之间并朝向模具,转动平台位于冷却水喷口的下侧设置有排水口,排水口的下侧设置有集水槽,集水槽的底面为斜坡状,斜坡的底端设有出水口,斜坡的出水口下侧设置有积渣槽,水箱还通过管道连接有能够将积渣槽内的水向水箱内抽取的抽水水泵,积渣槽内设有一个用于隔离水和废渣的隔板。
14.进一步的,所述合金液存储区外罩为倒锥型,锥度为1:0.8~1:1.2,浇道为内侧宽外侧窄的扇形,扇形角度22
°
~28
°
。
15.一种使用如所述的系统铸造航空薄壁耐热铝合金机匣的方法,在浇注前对模具进行装配和加热,加热至液相线温度以上9~11℃,浇包内的合金液往浇口杯浇注,浇注在10s内完成,浇注结束立即控制电机启动进而带动转动平台转动,转动平台的转速为40~60r/min,浇注结束2分钟后,提高转动平台的转速,将转动平台的转速提升至180~220r/min,此时合金液在离心力的作用下,由合金液存储区沿着浇道向铸件腔的方向流动,接下来开始启动上水水泵和抽水水泵,进行冷却水循环,通过冷却水喷口朝向模具喷水,待铸件凝固后,停止喷水和转动,拆卸模具即可取出铸件。
16.优点及效果
17.本发明通过研发一种航空薄壁耐热铝合金机匣铸造系统及方法,实现复杂薄壁耐热铝合金铸件的成型及补缩,通过内部加热和外部冷却的方式产生温度梯度,同时通过旋转使晶粒发生破碎,避免糊状凝固导致补缩通道堵塞,模具芯部的合金液在离心力的作用下向外侧流动补缩,对铸件部分合金液产生补缩压力,提高铸件内部组织致密度,消除缩孔及缩松缺陷。
附图说明
18.下面结合附图和具体实施方式对本发明作进一步说明。本发明的保护范围不仅局限于下列内容的表述。
19.图1为一种航空薄壁耐热铝合金机匣铸造系统整体结构示意图;
20.图2为模具和模具底座的结构示意图;
21.图3为模具底座俯视结构示意图;
22.图4为石墨环处结构示意图;
23.图5为一种铸造航空薄壁耐热铝合金机匣的方法流程图示意图。
24.附图标记说明:1.水箱、2.抽水水泵、3.上水水泵、4.阀门、5.排水口、6.集水槽、7.积渣槽、8.冷却水喷口、9.支撑立板、10.合金液存储区外罩、11.浇口杯、12.浇包、13.模具加热棒、14.加热棒支板、15.模具、16.石墨环、17.模具底座、18.加热棒电源、19.转动平台、20.滚动轴承、21.上部设备基座、22.转速传感器、23.工控机、24.传动皮带、25.主动皮带轮、26.电机、27.转动轴承、28.从动皮带轮、29.圆锥滚子轴承、30.下部设备基座、31.浇道、32.冒口、33.合金液存储区、34.铸件腔、35.定位槽。
具体实施方式
25.如图1、图2、图3和图4所示,一种航空薄壁耐热铝合金机匣铸造系统,其特征在于:
包括模具组、水箱1、转动平台19和电机26,水箱1能够给模具组提供冷却水,电机26能够带动转动平台19水平旋转,模具组包括模具15和模具底座17,模具15固定连接于模具底座17的上端,转动平台19的上部是开放的,模具底座17固定于转动平台19内侧的底部上端。
26.模具15包括连接在一起的中央模具和外周模具,中央模具设有浇口杯11,浇口杯11内何有陶瓷过滤片,陶瓷过滤片的下端为直角道,浇口杯11的下部设置有合金液存储区外罩10,合金液存储区外罩10的内部为合金液存储区33,模具底座17设置有多个浇道31,合金液存储区33与浇道31是连通的,合金液存储区外罩10为倒锥型,锥度为1:0.8~1:1.2,浇道31为内侧宽外侧窄的扇形,扇形角度22
°
~28
°
,可保证旋转所产生的压力传递至铸件内。外周模具内设置有铸件腔34,铸件腔34与浇道31也是连通的,铸件腔34的上端设有冒口32,冒口32设有排气孔,中央模具的外周均布固定有多个支撑立板9,支撑立板9与外周模具相接触,中央模具与外周模具的底部卡接隔有石墨环16,由于石墨环16内外的模具膨胀不同,石墨环16能够起到缓冲作用,减少对铸件的应力,进而能够有效减少铸件的开裂缺陷。模具15设置有加热装置,加热装置包括模具加热棒13、加热棒支板14和加热棒电源18,模具加热棒13通过加热棒支板14固定在中央模具和外周模具之间,加热棒支板14连接加热棒电源18。
27.转动平台19的外周设置有滚动轴承20,滚动轴承20位于上部设备基座21内,上部设备基座21用于使用时固定在其他固定装置上,转动平台19的一侧设置有转速传感器22。电机26的转动轴上固定有主动皮带轮25,转动平台19的下部固定有从动皮带轮28,主动皮带轮25和从动皮带轮28通过传动皮带24连接,转动平台19的下部外周设置有转动轴承27和圆锥滚子轴承29,转动轴承27和圆锥滚子轴承29位于下部设备基座30内侧。加热棒电源18、转速传感器22和电机26电性连接有工控机23。
28.水箱1通过管道连接有能够将水箱1内的水向外抽取的上水水泵3,上水水泵3的出水口连接的管道设置有阀门4,上水水泵3的出水口连接的管道还设有冷却水喷口8,冷却水喷口8位于转动平台19和模具15之间并朝向模具15,转动平台19位于冷却水喷口8的下侧设置有排水口5,排水口5的下侧设置有集水槽6,集水槽6的底面为斜坡状,斜坡的底端设有出水口,斜坡的出水口下侧设置有积渣槽7,水箱1还通过管道连接有能够将积渣槽7内的水向水箱1内抽取的抽水水泵2,积渣槽7内设有一个用于隔离水和废渣的隔板。
29.如图5所示,一种使用上述系统铸造航空薄壁耐热铝合金机匣的方法,在浇注前对模具进行装配和加热,加热至液相线温度以上9~11℃,为产生足够的离心力,使合金液存储区33内的合金液向铸件方向进行补缩,浇包12内的合金液往浇口杯11浇注,浇注在10s内完成,浇注结束立即控制电机26启动进而带动转动平台19转动,转动平台19的转速为40~60r/min,浇注结束2分钟后,提高转动平台19的转速,将转动平台19的转速提升至180~220r/min,此时合金液在离心力的作用下,由合金液存储区33沿着浇道31向铸件腔34的方向流动,并产生补缩压力,同时随着旋转作用,已经凝固的晶粒会发生扭转破碎,进而形成更多的晶粒,能够有效起到细化晶粒的作用,达到细化晶粒,提高铸件机械性能的目的,接下来开始启动上水水泵3和抽水水泵2,进行冷却水循环,通过冷却水喷口8朝向模具喷水,待铸件凝固后,停止喷水和转动,拆卸模具即可取出铸件
30.浇注系统的机匣结构型芯设计是为保证外涵机匣的完整充型及冷却控制,选取金属型作为模具,并针对该类铸件针对性设计一套浇注系统,该浇注系统区别于现有铝合金
砂型重力及反重力铸造的浇注系统。原理是通过对铸件冷却和加热形成利于该类铸件补缩的凝固温度梯度,同时通过外力(离心力)作用,使晶粒发生破碎,以细化晶粒和微观组织,畅通补缩通道,同时增加合金液的补缩压力,进而获得形状完整、组织致密的耐热铝合金薄壁机匣铸件。
31.显然,本发明的上述实施方式仅仅是为清楚地说明本发明所作的举例,而并非是对本发明的实施方式的限定,对于所属领域的普通技术人员来说,在上述说明的基础上还可以做出其他不同形式的变化或变动,这里无法对所有的实施方式予以穷举,凡是属于本发明的技术方案所引伸的显而易见的变化或变动仍处于本发明的保护范围之列。