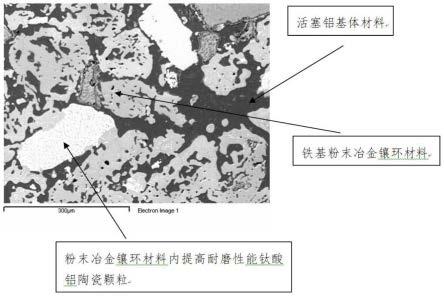
1.本发明涉及材料学技术领域,具体涉及一种铝活塞镶环用多孔铁基粉末冶金新材料。
背景技术:2.高功率发动机活塞主要采用铝合金材料制造,但是由于铝合金在高温下强度和耐磨性能严重下降,所以为了解决铝材料强度降低和耐磨性降低的问题,在铝活塞的头部环槽部位嵌入铸铁材料镶环,对第一、第二环槽进行强化。用于环槽强化的铸铁材料主要为高镍奥氏体材料,由于这种铸铁材料在高温下具有好的耐磨性能和抗拉强度,同时具有与铝活塞的铝合金基体相类似的膨胀系数,并在铸造过程中经铝硅合金浸渗处理后,可以与活塞铝合金基体进行有效的冶金结合,目前高镍奥氏体铸铁材料广泛应用于高功率铝活塞的强化。
3.目前用于铝合金活塞第一、第二环槽强化的材料主要为高镍奥氏体铸铁,这种铸造材料的主要优点是,膨胀系数接近活塞铝合金基体,可以与铝合金基体实现冶金结合,但是同样存在很多缺点,第一,高镍奥氏体铸铁镶环材料含有14%以上的金属镍,由于镍属于贵重金属,镶环材料价格较昂贵;第二、镶环材料采用的铸造方式为金属型离心铸造,虽然工艺简单,但是加工余量大,收成率仅为40%左右,能源消耗过高,成本高;第三,由于奥氏体铸铁材料的导热系数只有活塞基体铝合金的1/4,这就造成了发动机活塞在运行过程中第一环槽温度过高,环槽出现积碳,从而导致环槽过早磨损,发动机尾气排放超标,第四、现有铝活塞铸造工艺虽然可以实现奥氏体铸铁材料与活塞基体材料的冶金结合,但是在铸铁与铝基体之间存在结合层,结合层中含有大量脆性、低强度的铝铁化合物,结合层强度远低于铸铁材料和活塞铝基体,活塞在使用过程中经常铸造镶环脱落失效导致的发动机损坏失效,造成经济损失,所以需要对这些缺点进行改进。
技术实现要素:4.本发明旨在针对现有技术的技术缺陷,提供一种铝活塞镶环用多孔铁基粉末冶金新材料,以解决高镍奥氏体铸铁作物铝合金活塞第一、第二环槽强化材料,其性能有待改善的技术问题。
5.为实现以上技术目的,本发明采用以下技术方案:
6.一种铝活塞镶环用多孔铁基粉末冶金新材料,其特征在于:该材料包括以下重量百分比的成分:mn:3%-5%,cr:3%-5%,c:1.5%-2.5%,al2tio5陶瓷颗粒:2%-6%,余量为fe;该材料的空隙体积分数为vf:20%-30%;所述al2tio5陶瓷颗粒的粒度为5-10μm。
7.作为优选,该材料包括以下重量百分比的成分:mn:3%,cr:3%,c:
8.1.5%,al2tio5陶瓷颗粒:2%,余量为fe;该材料的空隙体积分数为vf:20%。
9.作为优选,该材料包括以下重量百分比的成分:mn:4%,cr:4%,c:2%,al2tio5陶瓷颗粒:4%,余量为fe;该材料的空隙体积分数为vf:25%。
10.作为优选,该材料包括以下重量百分比的成分:mn:5%,cr:5%,c:
11.2.5%,al2tio5陶瓷颗粒:6%,余量为fe;该材料的空隙体积分数为vf:30%。
12.本发明提供了一种铝活塞镶环用多孔铁基粉末冶金新材料。可用于铝活塞第一、第二环槽的强化,并用于替代目前的铝合金活塞广泛使用高镍奥氏体镶环材料。
13.本发明的粉末冶金烧结镶环材料具有多孔结构,密度只有原奥氏体铸铁材料的70%,采用了粉末冶金工艺,材料收成率达到100%,所以综合成本低于目前的奥氏体铸铁材料;同时本粉末冶金多孔镶环材料采用了压力铸造技术铸入铝活塞后,形成了铝基复合材料,由于多孔材料与活塞铝基体形成了铝基复合材料,并且与铝基体不存在明显的过度层(见图1),并且形成的铝基复合材料的导热性能优异,所以在相同工作条件下,与铸铁材料镶环相比,多孔镶环与活塞铝合金基体的结合强度提高2倍,导热性能提高1.5倍;由于多孔材料与活塞铝基体形的铝基复合材料,具有较高结合强度,并且组织致密,并且含有耐磨性能很好的陶瓷颗粒(见图2),所以与普遍使用的奥氏体铸铁材料镶环材料相比,复合材料镶环本体抗拉强度提高50%,耐磨性能提高一倍;使用粉末冶金多孔材料与活塞铝基体形成了铝基复合材料活塞环槽机构,可以在活塞设计时实现第一环槽高置,降低环槽温度,减少积碳,减少活塞环槽在使用过程中受到活塞环的磨损,提高活塞镶环的强度,在发动机全寿命内,活塞环槽不会出现磨损,脱落,可以实现发动机的整体性能提高。
附图说明
14.图1奥氏体铸铁镶环、粉末冶金复合材料镶环与活塞铝基体界面图片。
15.图2是活塞铝基体与粉末冶金镶环材料复合后sem图片。
具体实施方式
16.以下将对本发明的具体实施方式进行详细描述。为了避免过多不必要的细节,在以下实施例中对属于公知的结构或功能将不进行详细描述。以下实施例中所使用的近似性语言可用于定量表述,表明在不改变基本功能的情况下可允许数量有一定的变动。除有定义外,以下实施例中所用的技术和科学术语具有与本发明所属领域技术人员普遍理解的相同含义。
17.本发明中铝活塞用镶环材料为铁基多孔材料,制造工艺采用粉末冶金工艺,本发明中铁基镶环材料主要组成元素为:mn:3%-5%,cr:3%-5%,c:1.5%-2.5%,al2tio5陶瓷颗粒含量:2%-6%,余量为fe;多孔粉末冶金镶环的气孔体积分数vf:20%-30%,其中al2tio5陶瓷颗粒粒度为5-10μm。
18.实施例1
19.1、制备粉末冶金镶环材料;其中mn:3%,cr:3%,c:1.5%,al2tio5陶瓷颗粒:2%,余量为fe,空隙体积分数为vf:20%,
20.2、把镶环材料铸入铝活塞中,并进行t6热处理,
21.3、自活塞本体取样与奥氏体铸铁材料进行导热系数、抗拉强度,镶环与铝基体界面强度进行对比(结果见下表)。
22.物理及机械性能测试:
[0023][0024]
粉末冶金镶环材料在铸入活塞形成复合材料后,同试验条件下,复合材料导热系数、与铝基体的界面强度、复合材料本体强度均,优于奥氏体铸铁材料。
[0025]
4、自活塞本体取复合材料样与奥氏体铸铁材料进行摩擦磨损性能对比摩擦磨损试验条件:
[0026][0027][0028][0029]
粉末冶金镶环材料在铸入活塞形成复合材料后,同试验条件下,摩擦系数低于奥氏体铸铁材料,耐磨性能优于奥氏体铸铁材料。
[0030]
实施例2
[0031]
1、制备粉末冶金镶环材料;其中mn:4%,cr:4%,c:2%,al2tio5陶瓷颗粒:4%,余量为fe,空隙体积分数为vf:25%;
[0032]
2、把镶环材料铸入铝活塞中,并进行t6处理;
[0033]
3、取样与奥氏体铸铁材料进行摩擦性能,导热系数、抗拉强度,镶环与铝基体界面强度进行对比(结果见下表)。
[0034][0035]
4、自活塞本体取复合材料样与奥氏体铸铁材料进行摩擦磨损性能对比
[0036][0037][0038][0039]
粉末冶金镶环材料在铸入活塞形成复合材料后,同试验条件下,摩擦系数低于奥氏体铸铁材料,耐磨性能优于奥氏体铸铁材料。
[0040]
实施例3
[0041]
1、制备粉末冶金镶环材料;其中mn:5%,cr:5%,c:2.5%,al2tio5陶瓷颗粒:6%,余量为fe,空隙体积分数为vf:30%
[0042]
2、把镶环材料铸入铝活塞中,并进行t6处理,取样与奥氏体铸铁材料进行摩擦性能,导热系数、抗拉强度,镶环与铝基体界面强度进行对比(结果见下表)。
[0043][0044]
粉末冶金镶环材料在铸入活塞形成复合材料后,同试验条件下,复合材料导热系数、与铝基体的界面强度、复合材料本体强度均优于奥氏体铸铁材料。
[0045][0046][0047][0048]
粉末冶金镶环材料在铸入活塞形成复合材料后,同试验条件下,摩擦系数低于奥氏体铸铁材料,耐磨性能优于奥氏体铸铁材料。
[0049]
以上对本发明的实施例进行了详细说明,但所述内容仅为本发明的较佳实施例,并不用以限制本发明。凡在本发明的申请范围内所做的任何修改、等同替换和改进等,均应包含在本发明的保护范围之内。