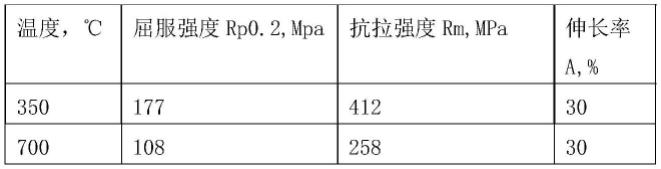
1.本发明涉不锈钢精密薄壁管材技术领域,具体涉及一种321型耐热不锈钢精密薄壁管及其制造方法。
背景技术:2.321型耐热不锈钢精密薄壁管是一种奥氏体型不锈钢管,在氧化介质中具有良好的耐腐蚀性能,广泛地运用于锅炉过热器、换热器、冷凝器、催化管、裂解管装置等钢管及管件。目前市面上难找到壁厚小于0.5mm的该类型管材,然而随着我国核电技术突飞猛进的发展,对耐腐蚀薄壁管的要求也越来越严苛。现有技术的不锈钢薄壁管的抗晶间腐蚀性能及高温力学性能往往不能满足要求。
技术实现要素:3.本发明的目的是提供一种321型耐热不锈钢精密薄壁管及其制造方法,以提升所述薄壁管的抗晶间腐蚀性能及高温力学性能,并符合实际需求。
4.为实现上述发明目的,本发明提供了一种321型耐热不锈钢精密薄壁管,其采用的合金的组分及重量百分数为:c:0.07-0.12;mn:≤2.0;si:≤0.8;p:≤0.020;s:≤0.005;cr:17.00~19.00;ni:9.00~11.00;co:<0.08;ti:5(c-0.02)~0.7;cu:≤0.25;al:<0.06;b:≤0.001;n:<0.012;sb:≤0.005;pb:≤0.005;sn:≤0.01;bi:≤0.005;as:≤0.01;se:≤0.002;fe:余量。
5.该薄壁管的室温力学性能抗拉强度≥530mpa,屈服强度≥205mpa,伸长率≥40%,布氏硬度≤220。
6.该薄壁管的高温力学性能符合表1的规定
7.表1精密管高温力学性能
[0008][0009]
该薄壁管的成品铁素体含量不大于5%;晶粒度等级为5~8级,8级晶粒度不大于30%;成品固溶管材无晶间腐蚀裂纹。
[0010]
该薄壁管的非金属夹杂物应满足表2要求
[0011]
表2非金属夹杂物要求
[0012]
类型a类b类c类d类b类tind类tin粗系<0.5<0.5<0.5<0.5≤0.5≤0.5细系<1.0≤1.0<1.0≤1.0≤1.5≤2.0
[0013]
本发明所使用的荒管是采用了冶炼技术,通过真空冶炼加真空电渣重熔后再进行
锻造,然后通过热穿孔制作而成,所以荒管具有成分均匀且夹杂少,各处性能均匀无裂纹等优点。
[0014]
本发明的管材截面圆的形状,名义壁厚为0.3mm主要步骤如下:荒管修磨后进行冷轧,采用两辊冷轧开坯,多辊冷轧多道次轧制成型,每次冷轧后需进行检验、脱脂清洗、固溶热处理、矫直、修磨等工序,保证管材的内外表面合格,最终通过冷轧道次完成薄壁管成品规格的轧制,轧管后进行成品热处理,随后进行探伤、表检、性能测试及包装入库。
[0015]
本发明的薄壁管的制造方法,具体工艺流程如下:荒管修磨
→
清洗
→
检验
→
轧制
→
切管
→
镗孔
→
去油
→
检验
→
热处理
→
矫直
→
磨抛
→
清洗
→
冷轧循环生产至成品规格
→
超声波无损探伤
→
切管
→
去油
→
成品固溶热处理
→
矫直
→
取样(理化检测)
→
精整
→
表面检验
→
复检
→
包装入库。
[0016]
本发明涉及的主要工艺介绍如下:
[0017]
1、修磨
[0018]
荒管修磨:荒管矫直外磨后先对荒管表面擦伤,以及局部麻坑等缺陷,用手提砂轮进行点磨,再用单头抛光机和内磨机对来料荒管内外表面进行整体内磨外抛。缺陷能够处理的用砂轮处理干净,无法处理干净的要切除。
[0019]
中间品修磨:中间品(中间生产道次的产品)在矫直、切管后进行内外表面检查,对发现的类似划伤、局部凹坑等缺陷进行点磨、内磨以及外抛处理。
[0020]
点磨:用抛光轮对外表面划伤、局部凹坑进行点磨处理。
[0021]
内磨:采用内磨机逐支进行内磨。
[0022]
外抛:逐支在带式抛光机上进行外抛;抛光后表面粗糙度ra≤0.8μm。
[0023]
内喷砂:采用内喷砂清理内壁附作物、以及浅表层痕迹等缺陷。
[0024]
修磨处理完毕后,在热水缸中进行清洗,并用压缩空气将内外表面吹扫干净。
[0025]
2、冷轧变形
[0026]
整个冷加工工艺按照两辊大变形量开坯,多辊冷轧机小变形量多道次精轧。这样既可保证产品的内在质量,还可获得极高的尺寸精度。
[0027]
使用设备:开坯一般选用两辊冷轧机,中间道次及成品道次选用多辊冷轧机,根据所轧规格选取轧辊、顶头和芯棒等。进行冷轧工装的设计优化和控制,以提高内外表面质量及尺寸的精准控制。针对管材尺寸精度高及薄壁的特点,研究轧机型号及控制参数、工模具、润滑油的选择等对成品管材性能的影响。
[0028]
1)成品轧制采用多辊30型号轧机生产,轧辊经过开口操作后满足轧制的要求,设备稳定性好,管材尺寸精度及内外表面质量控制得到保障。
[0029]
2)冷轧过程中的润滑控制研究,采用专用tdn81(两辊)及46#全损耗油(多辊)轧制该材料润滑与冷却效果较普通轧制油好,管材轧制不易轧毛。
[0030]
3)冷轧过程中的冷轧速度、送进量控制。研究不同轧制速度、送进量时,轧制力变化、制造过程平稳性、管材表面质量稳定性及一致性、尺寸精度趋势(外径公差、壁厚公差、椭圆度及偏心度)等等。
[0031]
针对该钢种加工尺寸精度要求高且壁厚薄的特点,优化设计了变形曲线,轧制过程更平稳,塑性变形顺利,无轧制缺陷产生。
[0032]
研究了孔型的最优化调整以及润滑冷却控制对成品管材残余应力分布特征的影
响及其对成品综合性能的影响。
[0033]
优化变形区分配,提高轧制精整次数,保障管材尺寸精度。轧制过程中,通过稳定车速及采用1.5-3mm送进量,在管材内部形成较均匀的应力及强化,提高批次稳定性。
[0034]
研究模具尺寸精度、粗糙度与管材尺寸精度、粗糙度的关系,提高轧制磨具的精度,一般需达到
±
0.01mm,选用表面粗糙度<0.3μm的工模具,控制管材轧制后的粗糙度<0.3μm(外表面)、<0.4μm(内表面)。
[0035]
冷轧表面质量控制:轧制前将整个沿线工装全部清理,上下料轻拿轻放,避免划伤管材表面,通过精心调整杜绝轧折、轧毛、竹节印等轧制缺陷。
[0036]
冷轧变形工艺见表3、表4、表5。
[0037]
表3φ24
×
0.3mm冷轧变形工艺及工模具
[0038][0039]
表4φ26
×
0.3mm冷轧变形工艺及工模具
[0040][0041]
表5φ29
×
0.3mm冷轧变形工艺及工模具
[0042][0043]
通过以上工艺管材的外径、壁厚可以控制到0.02mm的极差范围内。而现有技术的管材外径、壁厚的极差范围在0.06mm以上。
[0044]
3、去油清洗
[0045]
采用先进的超声波清洗工艺清洗管材,较现有技术中管材普通清洗更为干净,也不伤表面。
[0046]
去油工艺流程:超声波去油槽去油
→
清水槽清洗
→
热水槽清洗
→
[0047]
清理(人工擦洗)、检查。去油工艺参数见表6。
[0048]
表6去油工艺
[0049]
项目超声波去油槽超声波热水槽清水槽清洗时间≥90min2-15min2-15min温度(
±
10℃)60-7060-70室温
[0050]
清理与检查:在清洗槽内处理后要进行清理,先用压缩空气将内外表面水份吹干,然后用浸乙醇的布条擦拭外表面,用浸乙醇的布条吹打内壁三次。去油清理后,管材内外表面不得有油污、垃圾及其它附着物。去油质量检查采用布条擦拭外表面,以及用布条吹打内壁,均不得变色。如不合格,需再次进行清理,直至合格。
[0051]
4、热处理
[0052]
采用先进的辊底式氢气保护光亮热处理炉,确保管材内外表面光亮无氧化。热处理工艺参数见表7。
[0053]
表7热处理工艺参数
[0054][0055][0056]
5、精整
[0057]
镗孔:荒管冷轧到指定规格后在镗床上进行内壁镗孔,根据工艺要求镗掉内部缺陷部分。
[0058]
矫直:1)机矫前,均测量来料外径公差;
[0059]
2)矫直中心线调整正确,矫直辊的倾角和压下量要调整到与管材表面完全吻合,其接触长度大于辊身长的三分之二;在矫直过程中,随时检查质量情况以及外径公差,没有产生压伤、矫直印等缺陷;
[0060]
3)对于成品,矫后的管材必须轻拿轻放,避免了擦伤、碰伤;
[0061]
4)对于成品异型管亦可采取人工手动矫直,确保管材直线度。
[0062]
切管:在切管过程中,不允许拖、拽管材,避免管材表面划伤、擦伤;切管后,管材的两端平直、无毛刺。切后的管材端口需清理油污以及其它脏东西。
[0063]
表面抛光:采用带式抛光机或手提式沙带机对管材外表面进行整体抛光,抛光通过高速旋转的砂带接触管材而实现,抛光深度在0.01~0.03mm,抛光后表面粗糙度ra≤0.4
μm。
[0064]
6、检验
[0065]
尺寸测量:用壁厚千分尺针对每支管材两端壁厚实施垂直对称四点检测。用外径千分尺对每支管材两端和中间任意两截面实施对称三点检测;当对管材中部的外径偏差有疑问时应对其增加尺寸检验。尺寸检验记录中填写该批管材实际测得的最大、最小值。管材的外形和尺寸检查采用的工具为:0-25mm外径千分尺,25-50mm外径千分尺,0-25mm壁厚千分尺等。管材的外径壁厚允许偏差见表8。
[0066]
表8管材的外径允许偏差
[0067][0068]
平直度检验:用塞尺测量管材的平直度,将被测量管材放在大理石检验平台上,滚动后选取间隙最大的方向,并用1.0mm的塞尺片塞,无法塞进则平直度视为合格,如不合格允许重新矫直至到合格。
[0069]
表面检验:管材内、外表面应光滑,不允许有裂纹、折叠、轧折、结疤、离层、氧化皮、发纹和其它缺陷。内表面将逐支用36v低压行灯或对着充足光线进行内表面光照检验。检验内壁是否有凹坑、翘皮、竹节印等缺陷,用布条吹打内部,检验内壁清洁度。外表面在充足的光线下进行外表面全周滚动检验,检验表面是否有裂纹、擦伤、划伤等缺陷,用干净擦布擦拭管材外表面,检验外表面清洁度。在检查内外表面时,采用手提粗糙度检测仪器,对成品内外表面进行粗糙度检测。
[0070]
探伤检测:按gb/t5777的规定对管材进行超声波检测,探伤级别为l1级点聚焦,人工伤为纵横向u型槽,u型槽尺寸为0.05
±
0.002(深)
×
0.1
±
0.002(宽)
×5±
03(长)。
[0071]
成分检验:使用直读式光谱仪和手持式光谱仪对异型管化学成分进行检验,应满足本发明设计需求。
[0072]
力学性能检验:成品钢管的室温拉伸试验采用纵向短标准试样,在万能电子试验机上进行试验,应满足本发明设计要求。
[0073]
晶粒度检验:任意取两根钢管上各取一支试管,经磨制腐蚀后的试样在金相显微镜下,在放大100倍视场用比较法进行评级。
[0074]
本发明具有以下有益效果:(1)、本发明通过设备准备、原材料修磨、以及冷轧各工序的严格控制,使成品公差精度控制在较好的技术水平;(2)、本发明的薄壁管材与304不锈钢的性能相似,由于添加了适量的ti元素,有效抑制了碳化铬(cr
23
c6)的生成,故在高温环境下具有更好的抗晶间腐蚀性能及高温力学性能,高温力学性能对比见表9;(3)、本发明管材平直度在同规格薄壁管中占有优势;(4)、本发明较现有技术在成本和质量方面都有显著提高。
[0075]
表9高温管材力学性能对比
[0076]
具体实施方式
[0077]
下面对本发明实施例中的技术方案进行清楚、完整地描述,显然,所描述的实施例仅是本发明的一部分实施例,而不是全部的实施例。基于本发明中的实施例,本领域普通技术人员在没有做出创造性劳动前提下所获得的所有其它实施例,都属于本发明保护的范围。
[0078]
实施例1:
[0079]
一种规格为φ29
×
0.3mm的321型耐热不锈钢精密薄壁管的物、理化学检测结果如下:
[0080]
本发明使用直读光谱分析仪检测化学成分,其实测化学成分见表10。
[0081]
表10实测化学成分
[0082][0083][0084]
其尺寸规格为φ29
×
0.3mm。抽检实测尺寸规格见表11。
[0085]
表11实测尺寸规格
[0086][0087]
其室温力学性能见表12。
[0088]
表12室温力学性能
[0089][0090]
其高温力学性能见表13。
[0091]
表13高温力学性能
[0092] 温度,℃屈服强度rp0.2,mpa抗拉强度rm,mpa伸长率a,%要求35017742026实测值35018648542实测值35018952544.5要求70010825822实测值70012030570.5实测值70011529568.5
[0093]
其晶粒度等级及铁素体含量见表14。
[0094]
表14晶粒度及铁素体
[0095][0096][0097]
其非金属夹杂见表15。
[0098]
表15非金属夹杂物要求
[0099][0100]
实施例2:
[0101]
一种规格为φ26
×
0.3mm的321型耐热不锈钢精密薄壁管物理化学检测结果如下:
[0102]
本发明使用直读光谱分析仪检测化学成分,其实测化学成分见表16。
[0103]
表16实测化学成分
[0104][0105][0106]
其尺寸规格为φ26
×
0.3mm。抽检实测尺寸规格见表17。
[0107]
表17实测尺寸规格
[0108][0109]
其室温力学性能见表18。
[0110]
表18室温力学性能
[0111][0112]
其高温力学性能见表19。
[0113]
表19高温力学性能
[0114][0115][0116]
其晶粒度等级及铁素体含量见表20。
[0117]
表20晶粒度及铁素体
[0118][0119]
其非金属夹杂见表21。
[0120]
表21非金属夹杂物要求
[0121]
[0122]
实施例3:
[0123]
一种规格为φ24
×
0.3mm的321型耐热不锈钢精密薄壁管物理化学检测结果如下:
[0124]
本发明使用直读光谱分析仪检测化学成分,其实测化学成分见表22。
[0125]
表22实测化学成分
[0126][0127]
其尺寸规格为φ24
×
0.3mm。抽检实测尺寸规格见表23。
[0128]
表23实测尺寸规格
[0129][0130]
其室温力学性能见表24。
[0131]
表24室温力学性能
[0132][0133]
其高温力学性能见表25。
[0134]
表25高温力学性能
[0135] 温度,℃屈服强度rp0.2,mpa抗拉强度rm,mpa伸长率a,%要求35017742026实测值35018547036.5实测值35018647539.0要求70010825822实测值70012929067.5实测值70011627472.0
[0136]
其晶粒度等级及铁素体含量见表26。
[0137]
表26晶粒度及铁素体
[0138][0139]
其非金属夹杂见表27。
[0140]
表27非金属夹杂物要求
[0141][0142][0143]
该三例实例工序流程为:
[0144]
荒管修磨
→
清洗
→
检验
→
轧制
→
切管
→
镗孔
→
去油
→
检验
→
热处理
→
矫直
→
磨抛
→
清洗
→
冷轧循环生产至成品规格
→
超声波无损探伤
→
切管
→
去油
→
成品固溶热处理
→
矫直
→
取样(理化检测)
→
精整
→
表面检验
→
复检
→
包装入库。
[0145]
该实施例冷轧道次实际冷轧工艺如表3、4、5,其对应的成品道次加工率分别为38.1%、37.8%、36.3%。
[0146]
其热处理制度为1120℃,750mm/min,尤其值得提出的是,无缝薄壁管材成品首次使用了先进的热处理设备“辊底式氢气保护热处理炉”,而现有技术生产的该种薄壁管采用传统的“箱式热处理炉”,前者的优点如下:
[0147]
1、辊底炉有强还原性气体氢气作为保护气氛,杜绝了管材热处理过程中的氧化,而采用现有技术管材热处理后表面氧化,必须添加磨抛、酸洗等工序将表面氧化膜清除,从而加大了薄壁管材生产加工难度,降低了成材率。
[0148]
2、辊底炉炉膛小,炉内各区独立加热且温度均匀,而箱式炉炉膛大,炉内又无风机形成均匀的热对流,导致各区炉温不均匀,温差较大,固溶温度需较高才能达到所需力学性能,进而能耗也较辊底炉高。
[0149]
3、辊底炉“流水线”式生产,工作效率高于常规热处理炉。综上所述,从成本及表面质量方面本发明都是处于领先优势。其余工序参见上述发明内容。