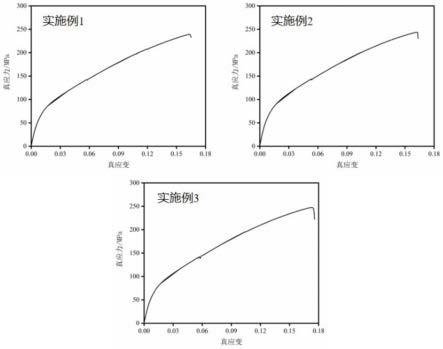
一种低铝含量az系高性能铸造镁合金及其制备方法
技术领域
1.本发明属于铸造镁合金制备技术领域,涉及一种低铝含量az系高性能铸造镁合金及其制备方法。
背景技术:2.镁合金作为最轻的金属结构材料,在实现轻量化的同时,还具有比强度高、比刚度高、导热性能好、屏蔽电磁辐射、减震和环境友好等特点,因此其在交通运输、航空航天、电子通讯、生物医疗等方面展现了良好而广阔的应用前景。然而受限于镁合金塑性加工难度及其成本问题,铸件是目前镁合金最主要的应用形式,可同时兼顾零部件的一体化设计需求和低的量产成本,其中,mg-al-zn(az)系镁合金的室温强度、塑性和耐腐蚀性匹配较好,而且价格较低,是目前牌号最多、应用最广的镁合金系列。
3.基于铝元素的加入,在提高合金强度和硬度的同时拓宽合金凝固区间、改善合金铸造性能,主要形成了以az31、az61、az80为代表的变形镁合金和以az91为代表的铸造镁合金。然而,随着凝固区间的扩大,较大的凝固区间和较多低熔点共晶相引起的较高线膨胀系数,使得合金极易产生铸造缺陷,如热裂、疏松、缩孔等问题,这将严重影响铸件的成品率,使材料的量产成本提高,进而阻碍镁合金在铸件一体化设计上的应用推进。
4.因此,需要在控制合金中铝元素含量的前提下,进一步研究高铸造性能镁合金的成分设计及其制备方法,以便在改善镁合金的铸造性能的同时降低镁合金的生产成本。
技术实现要素:5.有鉴于此,本发明的目的之一在于提供一种低铝含量az系高性能铸造镁合金;本发明的目的之二在于提供一种低铝含量az系高性能铸造镁合金的制备方法。
6.为达到上述目的,本发明提供如下技术方案:
7.1.一种低铝含量az系高性能铸造镁合金,按照质量百分数计,所述铸造镁合金由以下成分组成:al 2.52~2.85%、zn 0.87~1.18%、mn 0.15~0.25%、ca 0.02~0.18%、sr 0.18~0.22%、ce 0.001~0.01%、fe≤0.001%、si≤0.004%,其余为镁。
8.2.上述铸造镁合金的制备方法,所述制备方法具体如下所示:
9.(1)将经过预热处理的纯镁锭放入在500℃预热后的坩埚炉中,升温至560~600℃后通入由二氧化碳和六氟化硫组成的混合气体作为保护气体,继续升温至700℃,待95%以上的镁锭熔化后,然后再升温至720~730℃,保温至纯镁锭全部熔化;
10.(2)保温状态下继续加入经过预热处理的无氧化的纯铝,至纯铝熔化后通过加料勺加入经过预热处理的无氧化的mg-30ce中间合金、mg-30ca中间合金、mg-10mn中间合金、al-25sr中间合金和纯锌粒;
11.(3)继续保温至体系中的固态合金全部熔化,打渣后加入预热至100~150℃的六氯乙烷,精炼2~5min,搅拌使其混合均匀得到混合熔体;
12.(4)继续升温至735~745℃后保温10~20min使熔体与夹渣分离,打渣后降温至
720~730℃后进行浇铸,冷却即可得到低铝含量az系高性能铸造镁合金。
13.优选的,所述预热处理为在250~300℃下预热1h以上。
14.优选的,所述混合气体中二氧化碳和六氟化硫的体积比为100:0.3~0.6。
15.优选的,所述混合气体的通入过程中二氧化碳的流量为12~18l/min、六氟化硫的流量为0.03~0.12l/min。
16.优选的,所述加料勺包括顶盖1、带2mm微孔的圆柱形壳体2、底盖3、顶杆4和侧杆5;
17.所述顶盖为带2mm微孔的圆板,所述底盖为与顶盖直径相等的无孔的圆板,所述圆柱形壳体的底部直径与顶盖直径相等;
18.所述顶盖和底盖通过铰链连接在带2mm微孔的圆柱形壳体上,所述顶杆贯穿顶盖,并通过壳体后与底盖用铰链连接,所述顶盖上的微孔以圆板的中心为起点向外延伸呈阵列分布;
19.所述侧杆与壳体固定连接。
20.优选的,所述加料勺添加的方法为:将所述加料勺沉入熔体中,推动顶杆打开底盖,让加料勺中的材料滑入熔体中即可。
21.优选的,所述六氯乙烷的添加量为步骤(3)中打渣后熔体质量的0.2%~0.6%。
22.优选的,所述六氯乙烷的添加方法为:首先将大于0.5倍添加量的六氯乙烷加入,待其混合均匀后再加入剩下的六氯乙烷。
23.本发明的有益效果在于:本发明公开了一种低铝含量az系高性能铸造镁合金,该铸造镁合金中al的质量百分数为2.52~2.85%,突破了传统高铝含量铸造合金的设计思路,在低铝含量的基础上通过阻燃与细化晶粒元素的微量引入(如zn、mn、ca、sr、ce),得到具有抗拉强度、延伸率和流动性综合性能较好的铸造镁合金,且本发明的铸造镁合金制备方法较为简单,生产成本较低。
24.本发明的其他优点、目标和特征在某种程度上将在随后的说明书中进行阐述,并且在某种程度上,基于对下文的考察研究对本领域技术人员而言将是显而易见的,或者可以从本发明的实践中得到教导。本发明的目标和其他优点可以通过下面的说明书来实现和获得。
附图说明
25.为了使本发明的目的、技术方案和优点更加清楚,下面将结合附图对本发明作优选的详细描述,其中:
26.图1为加料勺的结构图,其中a为主视图,b为俯视图;
27.图2为实施例1~3中制备的低铝含量az系高性能铸造镁合金的om图,其中a为实施例1、b为实施例2、c为实施例3;
28.图3为实施例1~3中制备的低铝含量az系高性能铸造镁合金的粒径测试结果,其中a为实施例1、b为实施例2、c为实施例3;
29.图4为实施例1~3中制备的低铝含量az系高性能铸造镁合金的sem图,其中a为实施例1、b为实施例2、c为实施例3;
30.图5为实施例1~3中制备的低铝含量az系高性能铸造镁合金的xrd图;
31.图6为实施例1~3中制备的低铝含量az系高性能铸造镁合金的力学性能测试结
果;
32.图7为实施例1~3中制备的低铝含量az系高性能铸造镁合金拉伸断口的形貌图;
33.图8为实施例1~3中制备的低铝含量az系高性能铸造镁合金的流动性测试结果。
34.其中,1为顶盖、2为壳体、3为底盖、4为顶杆、5为侧杆。
具体实施方式
35.以下通过特定的具体实例说明本发明的实施方式,本领域技术人员可由本说明书所揭露的内容轻易地了解本发明的其他优点与功效。本发明还可以通过另外不同的具体实施方式加以实施或应用,本说明书中的各项细节也可以基于不同观点与应用,在没有背离本发明的精神下进行各种修饰或改变。需要说明的是,以下实施例中所提供的图示仅以示意方式说明本发明的基本构想,在不冲突的情况下,以下实施例及实施例中的特征可以相互组合。
36.下列实施例过程中由于在添加过程中mg-30ce中间合金、mg-30ca中间合金、mg-10mn中间合金、al-25sr中间合金的添加质量较小,因此采用加料勺进行操作。
37.加料勺的结如图1所示,其中a为主视图,b为俯视图。加料勺包括顶盖1、带2mm微孔的圆柱形壳体2、底盖3、顶杆4和侧杆5;顶盖为带2mm微孔的圆板,底盖为与顶盖直径相等的无孔的圆板,圆柱形壳体的底部直径与顶盖直径相等。顶盖和底盖通过铰链连接在带2mm微孔的圆柱形壳体上,顶杆贯穿顶盖,并通过壳体后与底盖用铰链连接;顶盖上的微孔以圆板的中心为起点向外延伸呈阵列分布;侧杆与壳体固定连接。
38.实施例1
39.一种低铝含量az系高性能铸造镁合金,由以下成分组成:al 2%、zn 1%、mn 0.2%、ca 0.1%、sr 0.2%、ce 0.005%、fe≤0.001%、si≤0.004%,其余为镁。
40.上述铸造镁合金的具体制备方法为:
41.(1)按照铸造镁合金的组成准备原材料(包括纯镁锭、纯铝、mg-30ce中间合金、mg-30ca中间合金、mg-10mn中间合金、al-25sr中间合金和纯锌粒),将其在250℃下预热1h以上得到经过预处理的原材料。
42.(2)将经过预热处理的纯镁锭放入在500℃预热后的坩埚炉中,升温至580℃后通入混合气体(由体积比为100:0.5的二氧化碳和六氟化硫组成,其中二氧化碳的流量为12l/min,六氟化硫的流量为0.04l/min)作为保护气体,继续升温至700℃,然后再升温至725℃,保温至纯镁锭全部熔化。
43.(3)保温状态下继续加入经过预热处理的无氧化的纯铝,至纯铝熔化后通过加料勺加入经过预热处理的无氧化的mg-30ce中间合金、mg-30ca中间合金、mg-10mn中间合金、al-25sr中间合金(上述各种合金通过加料勺添加,具体方法为:将待添加的合金材料放入加料勺中,沉入熔体中,推动顶杆打开底盖,让加料勺中的材料滑入熔体中即可,在添加过程中待添加的合金材料在重力和顶盖与壳体微孔熔体的挤压下进入熔体中下部,从而最大限度的保证微量合金元素的有效添加,降低常规添加方法下合金元素添加过程中在熔体表面的烧损)和纯锌粒。
44.(4)继续保温至体系中的固体全部熔化,打渣后加入预热至100℃的六氯乙烷(其中六氯乙烷的添加量为打渣后熔体质量的0.5%,其添加方法为:首先将0.6倍添加量的六
氯乙烷加入,待其混合均匀后再加入剩下的六氯乙烷),精炼4min,搅拌使其混合均匀得到混合熔体。
45.(5)继续升温至740℃后保温15min使熔体与夹渣分离,打渣后降温至725℃后进行浇铸,冷却即可得到低铝含量az系高性能铸造镁合金。
46.实施例2
47.一种低铝含量az系高性能铸造镁合金,由以下成分组成:al 2.52%、zn 0.87%、mn 0.15%、ca 0.02%、sr 0.18%、ce 0.001%、fe≤0.001%、si≤0.004%,其余为镁。
48.上述铸造镁合金的具体制备方法为:
49.(1)按照铸造镁合金的组成准备原材料(包括纯镁锭、纯铝、mg-30ce中间合金、mg-30ca中间合金、mg-10mn中间合金、al-25sr中间合金和纯锌粒),将其在250℃下预热1h以上得到经过预处理的原材料。
50.(2)将经过预热处理的纯镁锭放入在500℃预热后的坩埚炉中,升温至560℃后通入混合气体(由体积比为100:0.3的二氧化碳和六氟化硫组成,其中二氧化碳的流量为15l/min,六氟化硫的流量为0.07l/min)作为保护气体,继续升温至700℃,然后再升温至720℃,保温至纯镁锭全部熔化。
51.(3)保温状态下继续加入经过预热处理的无氧化的纯铝,至纯铝熔化后通过加料勺加入经过预热处理的无氧化的mg-30ce中间合金、mg-30ca中间合金、mg-10mn中间合金、al-25sr中间合金(上述各种合金通过加料勺添加,具体方法为:将待添加的合金材料放入加料勺中,沉入熔体中,推动顶杆打开底盖,让加料勺中的材料滑入熔体中即可,在添加过程中待添加的合金材料在重力和顶盖与壳体微孔熔体的挤压下进入熔体中下部,从而最大限度的保证微量合金元素的有效添加,降低常规添加方法下合金元素添加过程中在熔体表面的烧损)和纯锌粒。
52.(4)继续保温至体系中的固体全部熔化,打渣后加入预热至120℃的六氯乙烷(其中六氯乙烷的添加量为打渣后熔体质量的0.2%,其添加方法为:首先将大于0.51倍添加量的六氯乙烷加入,待其混合均匀后再加入剩下的六氯乙烷),精炼2min,搅拌使其混合均匀得到混合熔体。
53.(5)继续升温至735℃后保温20min使熔体与夹渣分离,打渣后降温至720℃后进行浇铸,冷却即可得到低铝含量az系高性能铸造镁合金。
54.实施例3
55.一种低铝含量az系高性能铸造镁合金,由以下成分组成:al 2.85%、zn 1.18%、mn 0.25%、ca 0.18%、sr 0.22%、ce 0.01%、fe≤0.001%、si≤0.004%,其余为镁。
56.上述铸造镁合金的具体制备方法为:
57.(1)按照铸造镁合金的组成准备原材料(包括纯镁锭、纯铝、mg-30ce中间合金、mg-30ca中间合金、mg-10mn中间合金、al-25sr中间合金和纯锌粒),将其在300℃下预热1h以上得到经过预处理的原材料。
58.(2)将经过预热处理的纯镁锭放入在500℃预热后的坩埚炉中,升温至600℃后通入混合气体(由体积比为0.6的二氧化碳和六氟化硫组成,其中二氧化碳的流量为18l/min,六氟化硫的流量为0.11l/min)作为保护气体,继续升温至700℃,然后再升温至730℃,保温至纯镁锭全部熔化。
59.(3)保温状态下继续加入经过预热处理的无氧化的纯铝,至纯铝熔化后通过加料勺加入经过预热处理的无氧化的mg-30ce中间合金、mg-30ca中间合金、mg-10mn中间合金、al-25sr中间合金(上述各种合金通过加料勺添加,具体方法为:将待添加的合金材料放入加料勺中,沉入熔体中,推动顶杆打开底盖,让加料勺中的材料滑入熔体中即可,在添加过程中待添加的合金材料在重力和顶盖与壳体微孔熔体的挤压下进入熔体中下部,从而最大限度的保证微量合金元素的有效添加,降低常规添加方法下合金元素添加过程中在熔体表面的烧损)和纯锌粒。
60.(4)继续保温至体系中的固体全部熔化,打渣后加入预热至150℃的六氯乙烷(其中六氯乙烷的添加量为打渣后熔体质量的0.6%,其添加方法为:首先将大于0.8倍添加量的六氯乙烷加入,待其混合均匀后再加入剩下的六氯乙烷),精炼5min,搅拌使其混合均匀得到混合熔体。
61.(5)继续升温至745℃后保温10min使熔体与夹渣分离,打渣后降温至730℃后进行浇铸,冷却即可得到低铝含量az系高性能铸造镁合金。
62.性能测试
63.对实施例1~3中制备的低铝含量az系高性能铸造镁合金进行om检测,其结果如图2所示,其中a为实施例1、b为实施例2、c为实施例3。从图2可以看出,实施例1~3中制备的低铝含量az系高性能铸造镁合金由灰白色基体和非连续分布黑色第二相组成,同时晶内和晶界上均有大量颗粒状第二相,说明实施例1~3中制备的低铝含量az系高性能铸造镁合金的组织中除含有少量的mg
17
al
12
低熔点相之外,还可能出现了alxca、mgxca、alxsr等高熔点第二相,从而导致其有利于提高铸造镁合金的强度。
64.对实施例1~3中制备的低铝含量az系高性能铸造镁合金进行粒径检测,其结果如图3所示,其中a为实施例1、b为实施例2、c为实施例3。从图3可以看出,实施例1~3中制备的低铝含量az系高性能铸造镁合金的晶粒尺寸主要分布在200μm附近,也有较多分布与100μm以上,还有极少量分布在400μm以上,说明实施例1~3中制备的低铝含量az系高性能铸造镁合金的组织细化较好,有利于合金强度与塑性的同时提高。
65.对实施例1~3中制备的低铝含量az系高性能铸造镁合金进行扫描电镜检测,其结果如图4所示,其中a为实施例1、b为实施例2、c为实施例3。对对实施例1~3中制备的低铝含量az系高性能铸造镁合金进行能谱分析,其结果如表1所示。从图4和表1可以看出,实施例1~3中制备的低铝含量az系高性能铸造镁合金由暗黑色α-mg基体和少量灰白色第二相组成。第二相中除少量的mg
17
al
12
相外,还有少量含ca、sr的白色块状和针状相,第二相整体分布较为弥散。
66.表1实施例1~3中制备的低铝含量az系高性能铸造镁合金的点能谱分析结果(at.%)
[0067][0068]
对实施例1~3中制备的低铝含量az系高性能铸造镁合金进行xrd检测,其结果如图5所示。从图5可以看出,实施例1~3中制备的低铝含量az系高性能铸造镁合金衍射峰主要由α-mg、mg
17
al
12
、al2ca组成。虽然相关研究显示此类合金还可能出现al4mn、(mg,al)4sr、(mg,al)
17
sr2和al4sr相,但考虑本合金中的sr、ce含量较低和固溶度的影响,未出现相关的相的衍射峰也是合理的。
[0069]
对实施例1~3中制备的低铝含量az系高性能铸造镁合金进行力学性能测试,其结果如图6所示。从图6可以看出,实施例1~3中制备的低铝含量az系高性能铸造镁合金拉伸曲线基本重合,数据偏差不大,其屈服强度约为65mpa,抗拉强度约为242mpa,变形延伸率约为15.8%,其中实施例3的抗拉强度和延伸率最高。
[0070]
对实施例1~3中制备的低铝含量az系高性能铸造镁合金进行拉伸至断裂,其断裂面的形貌如图7所示。从图7可以看出,实施例1~3中制备的低铝含量az系高性能铸造镁合金的断口形貌基本一致,断口表面由明显的河流花样、少量解理面和二次裂纹组成,部分区域存在少量很浅的韧窝。
[0071]
对实施例1~3中制备的低铝含量az系高性能铸造镁合金进行流动性测试,其结果如图8所示。从图8可以看出,实施例1~3中制备的低铝含量az系高性能铸造镁合金流动性能数值分别为229mm、222mm、213mm,较之常规的al含量较高的az91镁合金的流动性数据有轻微提高,约10%左右。
[0072]
综上所述,本发明公开了一种低铝含量az系高性能铸造镁合金,该铸造镁合金中al的质量百分数为2.52~2.85%,突破了传统高铝含量铸造合金的设计思路,在低铝含量的基础上通过阻燃与细化晶粒元素的微量引入(如zn、mn、ca、sr、ce),得到具有抗拉强度、延伸率和流动性综合性能较好的铸造镁合金,且本发明的铸造镁合金制备方法较为简单,生产成本较低;另外由于在制备过程中直接升温太高很容易导致镁合金的烧损增加,因此选择在700℃之前完成大部分镁锭的熔化,在720~730℃进行纯铝和中间合金以及小部分镁锭的熔化,特别是纯铝的熔化后发生氧化形成的氧化铝膜层致密度较大,可对熔体起保护作用。
[0073]
最后说明的是,以上实施例仅用以说明本发明的技术方案而非限制,尽管参照较佳实施例对本发明进行了详细说明,本领域的普通技术人员应当理解,可以对本发明的技术方案进行修改或者等同替换,而不脱离本技术方案的宗旨和范围,其均应涵盖在本发明的权利要求范围当中。