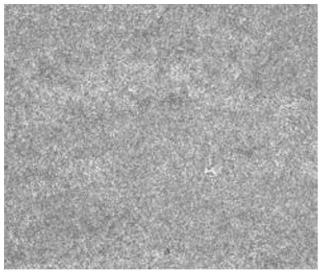
1.本发明涉及钢材热加工领域,特别涉及一种模具钢热处理过程中的冷却方法,同时本发明还涉及一种模具钢的热处理方法及采用上述模具钢的热处理方法制得的模具钢。
背景技术:2.模具是制造业不可缺少的基础工装,素有“工业之母”之称。我国是世界模具制造与消费第一大国,产值占全球三分之一,随着新能源汽车、5g通信、it电子、3c家电等领域的快速发展,对高品质模具钢材料的需求更加突出。据不完全统计,我国模具钢总产量约为150万吨,其中,塑料模具钢占60-70%,热作模具钢占20-25%,冷作模具钢约占15%。
3.目前,我国模具钢制备方式主要为冶炼+锻造,锻材占60%以上,剩余为轧材。我国每年的净进口总量约10万吨。进口来源主要有日本大同、日立金属、德国葛利兹,瑞典assab、美国芬可乐。进口模具钢的牌号包括日本skd61、dc53、skd11等,瑞典8407、dievar等,德国1.2344、1.2379,美国牌号h13、d2等。进口模具钢的规格主要是大尺寸的锻制模块及大尺寸的模具扁钢。从下游行业情况来看,汽车行业消费模具钢约占市场总量的35%,电脑、手机、电子设备等电子通讯行业用模具钢约占市场的20%。
4.随着未来模具应用领域的不断扩大以及向高端发展,面对我国模具钢质量、性能稳定性差,品种、规格不全的现状,模具钢必然朝着多品种规格、高纯净度、高等向性、超细化组织、长寿命方向发展。
技术实现要素:5.有鉴于此,本发明提出了一种模具钢热处理过程中的冷却方法,包括:该方法采用对钢锭入水冷却和空气冷却交替进行;第一次水冷时间为钢锭最大有效厚度*(2.0~2.2)s/mm;第一次空冷时间为钢锭最大有效厚度*(0.60~0.8)s/mm;第二次水冷时间为钢锭最大有效厚度*(1.3~1.5)s/mm;第二次空冷时间为钢锭最大有效厚度*(0.60~0.80)s/mm;第三次水冷时间为钢锭最大有效厚度*(0.28~0.48)s/mm;第三次空冷时间为30~40min。
6.采用本发明的模具钢热处理过程中的冷却方法,采用水和空气为介质,利用水的冷却能力强和空气冷却能力弱的特点,通过水与空气的多次强弱交替冷却,精确优化冷却控制时间,使钢锭的合金组织更细化,提高钢结构材料的强韧性。
7.本发明还提出了一种模具钢的热处理方法,该方法包括:对钢锭按如下步骤依次进行处理:热锻轧,吹风冷却,加热,水空交替冷却,球化退火;其中,水空交替冷却采用上述的模具钢热处理过程中的冷却方法。
8.本发明的模具钢的热处理方法对钢锭进行热锻轧,使钢锭粗加工成型,然后吹风冷却,加快热锻轧加工后的快速冷却,细化晶粒,进而加热使钢锭奥氏体化,继续水空交替冷却,使钢锭的合金组织更细化,进而球化退火消除工件在水空交替冷却过程中的应力,重结晶细化组织晶粒。
9.进一步的,所述钢锭的热锻轧的最终温度为cct曲线中二次碳化物析出温度以上。
10.进一步的,所述钢锭的吹风冷却后的温度为230-250℃。
11.进一步的,所述加热的方法包括:将所述钢锭以90-100℃/h的速率升温至600-680℃,保温2-3h;然后将所述钢锭以90-100℃/h的速率升温至1030-1050℃,保温2-3h。
12.进一步的,所述球化退火的方法包括:将所述钢锭以90-100℃/h的速率升温至600-680℃,保温3.5-4.5h;将所述钢锭以90-100℃/h的速率升温至800-900℃,保温8.5-9.5h;将所述钢锭以≤30℃/h的速率降温至600-680℃;将所述钢锭以90-100℃/h的速率升温到700-720℃,保温11-13小时;将所述钢锭以≤20℃/h的速率降温到400℃以下,出炉。
13.本发明进一步提出了一种模具钢,所述模具钢由钢锭通过上述的模具钢的热处理方法制得。
14.本发明的模具钢通过采用上述热处理方法,可以使钢组织细化,提高钢结构材料的强韧性。
附图说明
15.构成本发明的一部分的附图用来提供对本发明的进一步理解,本发明的示意性实施例及其说明用于解释本发明,并不构成对本发明的不当限定。在附图中:
16.图1为采用本发明实施例一的模具钢的热处理方法制备的模具钢的1/2d处放大500倍的金相图;
17.图2为采用本发明实施例二的模具钢的热处理方法制备的模具钢的1/2d处放大500倍的金相图;
18.图3为采用对比例一的模具钢的热处理方法制备的模具钢的1/2d处放大500倍的金相图。
具体实施方式
19.需要说明的是,在不冲突的情况下,本发明中的实施例及实施例中的特征可以相互组合。
20.下述实施例中的实验方法,如无特殊说明,均为常规方法。下述实施例中所用的试验材料,如无特殊说明,均为自常规购买得到的。另外,除本实施例特别说明之外,本实施例中所涉及的各术语及工艺依照现有技术中的一般认知及常规方法进行理解即可。
21.一种模具钢热处理过程中的冷却方法,该方法采用对钢锭入水冷却和空气冷却交替进行;第一次水冷时间为钢锭最大有效厚度*(2.0~2.2)s/mm;第一次空冷时间为钢锭最大有效厚度*(0.60~0.8)s/mm;第二次水冷时间为钢锭最大有效厚度*(1.3~1.5)s/mm;第二次空冷时间为钢锭最大有效厚度*(0.60~0.80)s/mm;第三次水冷时间为钢锭最大有效厚度*(0.28~0.48)s/mm;第三次空冷时间为30~40min。
22.采用本发明的模具钢热处理过程中的冷却方法,采用水和空气为介质,利用水的冷却能力强和空气冷却能力弱的特点,通过水与空气的多次强弱交替冷却,精确优化冷却控制时间,使组织转变过程中金相不在cct曲线中的珠光体区域和贝氏体区域停留,不产生珠光体和贝氏体,使钢锭的组织更细化,提高钢结构材料的强韧性。在计算冷却时间时,最大有效厚度的选取根据钢锭形状而定,圆钢钢锭则可以采用圆钢的直径,扁钢钢锭则采用
扁钢的高度,单位为毫米。
23.本发明还提出了一种模具钢的热处理方法,该方法包括:对钢锭按如下步骤依次进行处理:热锻轧,吹风冷却,加热,水空交替冷却,球化退火;其中,水空交替冷却采用上述的模具钢热处理过程中的冷却方法。
24.本发明的模具钢的热处理方法对钢锭进行热锻轧,使钢锭粗加工成型,然后吹风冷却,使热锻轧加工后的钢锭快速冷却,细化晶粒,进而加热使钢锭奥氏体化,继续水空交替冷却,使钢锭的合金组织更细化,进而球化退火消除工件在水空交替冷却过程中的应力,重结晶细化组织晶粒。
25.本发明对钢锭的热锻轧的最终温度可优选为cct曲线中二次碳化物析出温度以上,以防止二次碳化物的产生,具体的温度范围可以根据不同钢材牌号选取,若是h11钢,则热锻轧终温控制在805℃以上;若是h12钢,则热锻轧终温控制在810℃以上;若是5h12钢,则热锻轧终温控制在815℃;若是h13钢,则热锻轧终温控制在820℃以上。
26.然后将上述钢锭的吹风冷却后的温度为230-250℃,具体方法可以将钢锭放置在10-15mm高的钢轨上,在钢锭周围东西南北各方向放置一台轴流风机,东西位的风机出风方向平行间距10-20mm,南北位的风机亦如是,开启风机,使钢锭周围空气流动形成螺旋状,以将钢锭在短时间强冷至230-250℃,吹风冷却可以细化晶粒,减少热锻轧加工过程中动态再结晶产生的混晶现象。
27.进而对钢锭进行加热,加热的方法优选具体包括:将加热炉预先加热至300-400℃,防止钢锭入炉开裂,然后将钢锭放入加热炉中,入炉后保温1.5小时,进而将钢锭以90-100℃/h的速率升温至600-680℃,保温2-3h;继续将所述钢锭以90-100℃/h的速率升温至1030-1050℃,使钢锭奥氏体化,保温2-3h。加热后进行水空交替冷却,使钢锭组织细化。
28.然后对钢锭进行球化退火,球化退火的方法具体可以包括:将钢锭以90-100℃/h的速率升温至600-680℃,保温3.5-4.5h;将钢锭以90-100℃/h的速率升温至800-900℃,保温8.5-9.5h;将钢锭以≤30℃/h的速率降温至600-680℃;将钢锭以90-100℃/h的速率升温到700-720℃,保温11-13小时;将钢锭以≤20℃/h的速率降温到400℃以下,出炉。球化退火可以细化晶粒,调整组织,消除组织缺陷。
29.本发明进一步提出了一种模具钢,本发明的模具钢由钢锭通过上述的模具钢的热处理方法制得。本发明的模具钢通过采用上述热处理方法,可以使钢组织细化,提高钢结构材料的强韧性。
30.下面对本发明的具体实现方案做详细的描述。
31.实施例一
32.本实施例采用的钢锭为材质h13、规格φ254、长度5000mm的棒材。对钢锭采用以下热处理方法。
33.对钢锭加热至1150℃而后径向锻造,终锻度温度控制在820℃。
34.将钢锭热锻后放置在10-15mm高的钢轨上,在钢锭周围东西南北各放置一台轴流风机,风机不相对,错开10-20mm,将钢锭强冷至250℃。
35.将吹风冷却的钢锭放入已预热350℃的加热炉中,入炉后保温1.5小时,以90-100℃/h的速率升温至650℃,保温2.5h;继续将钢锭以90-100℃/h的速率升温至1050℃,保温2.5h。
36.然后进行水空交替冷却,第一次入水停留9min,出水空中停留3min,第二次入水停留6min,出水空中停留3min,第三次入水停留1.5min,出水空中停留30min。一次出水棒材表面温度为320℃,二次出水棒材表面温度为230℃,三次出水棒材表温度为110℃。
37.将钢锭放入加热炉中,以90-100℃/h的速率升温至650℃,保温4h;继续将钢锭以90-100℃/h的速率升温至900℃,保温9h;然后将钢锭以≤30℃/h的速率快速降温至650℃;将钢锭以90-100℃/h的速率从650℃升温到700℃,保温时间为12小时;将钢锭≤20℃/h的从700℃缓降到400℃出炉。
38.对上述钢锭进行矫直和车皮。检测钢锭1/4d和1/2d处的退火组织,取10-15mm的试样,1/2d处的组织金相如图1所示,根据sep1614-1996标准进行评定,本实施例退火组织为ga2级。
39.实施例二
40.本实施例采用的钢锭为材质h12、规格110x250、长度3000mm的扁钢。对钢锭采用以下热处理方法。
41.对钢锭加热至1120℃而后径向锻造,终锻度控制在810℃。
42.将钢锭热锻后放置在10-15mm高的钢轨上,在钢锭周围东西南北各放置一台轴流风机,风机不相对,错开10-20mm,将钢锭强冷至230℃。
43.将吹风冷却的钢锭放入已预热350℃的加热炉中,入炉后保温1.5小时,以90-100℃/h的速率升温至650℃,保温2.5h;继续将钢锭以90-100℃/h的速率升温至1050℃,保温2.5h。
44.然后进行水空交替冷却,第一次入水停留4min,出水空中停留1min第二次入水停留2.5min,出水空中停留1min第三次入水停留1.5min,出水空中停留30min。一次出水扁钢表面温度为270℃,二次出水棒材表面温度为210℃,三次出水棒材表温度为100℃。
45.将钢锭放入加热炉中,以90-100℃/h的速率升温至650℃,保温4h;继续将钢锭以90-100℃/h的速率升温至900℃,保温9h;然后将钢锭以≤30℃/h的速率快速降温至650℃;将钢锭以90-100℃/h的速率从650℃升温到700℃,保温时间为12小时;将钢锭≤20℃/h的从700℃缓降到400℃出炉。
46.对上述钢锭进行矫直和车皮。检测钢锭1/4d和1/2d的退火组织,取10-15mm的试样,1/2d处的组织金相如图1所示,根据sep1614-1996标准进行评定,本实施例退火组织为ga2级。
47.对比例一
48.本对比例采用的钢锭为材质h13、规格φ254、长度5000mm的棒材。对钢锭采用以下热处理方法。
49.对钢锭加热至1150℃而径向锻造,终锻温度控制在820℃。
50.将钢锭热锻后放置在10-15mm高的钢轨上,在钢锭周围东西南北各放置一台轴流风机,风机不相对,错开10-20mm,将钢锭强冷至250℃。
51.将吹风冷却的钢锭放入已预热350℃的加热炉中,入炉后保温1.5小时,以90-100℃/h的速率升温至650℃,保温2.5h;继续将钢锭以90-100℃/h的速率升温至1050℃,保温2.5h。
52.然后进行水空交替冷却,第一次入水停留4min,空中停留1min第二次入水停留
1.5min,空中停留1min第三次入水停留1min,空中停留30min。一次出水棒材表面温度为480℃,二次出水棒材表面温度为360℃,三次出水棒材表温度为230℃。
53.将钢锭放入加热炉中,以90-100℃/h的速率升温至650℃,保温4h;继续将钢锭以90-100℃/h的速率升温至900℃,保温9h;然后将钢锭以≤30℃/h的速率快速降温至650℃;将钢锭以90-100℃/h的速率从650℃升温到700℃,保温时间为12小时;将钢锭≤20℃/h的从700℃缓降到400℃出炉。
54.对上述钢锭进行进行矫直和车皮。检测1/4d和1/2d的退火组织,取10-15mm的试样,1/2d处的组织金相如图3所示。本对比例与实施例一的热处理方法基本相同,不同之处在于水空交替冷却的时间。水空交替冷却时间变更后,组织出现了大量贝氏体,不符合sep1614-1996的标准规定,钢锭使用寿命会大大降低。
55.以上详细描述了本发明的优选实施方式,但是,本发明并不限于上述实施方式中的具体细节,在本发明的技术构思范围内,可以对本发明的技术方案进行多种简单变型,这些简单变型均属于本发明的保护范围。
56.另外需要说明的是,在上述具体实施方式中所描述的各个具体技术特征,在不矛盾的情况下,可以通过任何合适的方式进行组合,为了避免不必要的重复,本发明对各种可能的组合方式不再另行说明。