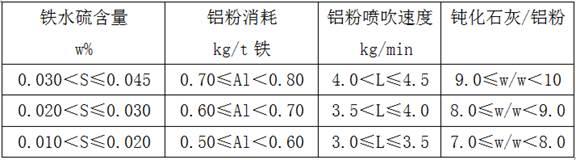
1.本发明涉及铁水预处理技术领域,尤其是一种钙铝基脱硫剂复合喷吹脱硫的方法。
背景技术:2.在高炉出铁过程中,铁水中难免会带入0.02%~0.04%的硫(甚至更高),这些硫对大多数钢材而言是非常有害的。硫含量过高不仅会影响钢的塑性、加工性能、焊接性能等,甚至还会导致钢的“热脆”。因此,脱除钢液中过多含量的硫是钢铁冶炼的主要任务之一。而进行铁水预处理脱硫是减轻高炉、转炉生产负荷,提高经济技术指标的主要方法之一,也是目前国内外钢铁企业生产低硫钢常用的技术手段。
3.目前国内外钢铁企业常用的铁水脱硫方式主要有kr(搅拌)脱硫和喷吹脱硫两种方法。kr(搅拌)脱硫主要是在铁水包内转动用耐火材料制的搅拌叶轮,将脱硫剂与铁水充分搅拌混合进行脱硫的方法,该方法由于借助了外力搅拌,脱硫反应动力学条件较好。该方法主要采用石灰做脱硫剂,虽然可以显著减少处理成本,但存在处理时间长,过程温降大的技术难题。另外,kr法还必须将铁水包中的前渣扒干净,否则会导致脱硫后渣子过多,难以扒净,在炼钢时发生回硫的问题,严重影响企业经济效益。
4.喷吹脱硫主要是通过借助浸入铁水中的喷枪,向铁水中喷吹脱硫剂的脱硫方法。根据喷吹料混合方式的不同,喷吹脱硫又可分为混合喷吹法和复合喷吹法。混合喷吹主要是两种或两种以上脱硫粉剂按照一定比例混合,然后用同一个喷粉罐经喷枪喷入铁包进行脱硫;复合喷吹主要是将脱硫粉剂单独储存在各自的喷粉罐内,在使用过程中,在喷吹管道内进行混合喷吹脱硫的方式。喷吹脱硫方法具有投资少、操作简单、事故率低等特点,是国内主要的铁水预处理脱硫方式。
5.喷吹脱硫常用的脱硫粉剂主要为石灰粉、镁粉、电石粉、苏打粉等。但由于电石粉在使用和储存过程中的安全性难以保证,苏打粉生产成本高、且污染环境均已被限制使用。目前主要采用石灰粉、镁粉为主,当仅采用石灰粉喷吹时,铁水中的硫含量很难降低至0.005%以下,要实现极低硫钢的冶炼,必须采用镁粉或镁粉、石灰粉进行复合喷吹。但镁基脱硫剂在使用过程中,由于镁的汽化温度低,在喷吹过程中镁蒸汽会瞬间排出,影响工艺控制稳定性,并会产生铁水喷溅,导致铁损增加。
6.申请号为200510030708.2(铁水预处理用镁粉脱硫剂)和200610119243.2(含稀土氧化物的钝化镁脱硫剂及其制备方法)的发明专利申请均是以镁基脱硫剂为主,通过在镁粉表面形成钝化膜,以防止镁粉过早汽化;但均没有解决铁水脱硫过程中镁粉消耗高、生产成本高,铁水喷溅严重的问题。
7.申请号为201610204836.2的发明专利申请公开了“一种铁水喷吹脱硫用复合脱硫剂及其制备方法”,该方法通过制备钝化镁粉80~90%、金属铝1~8%、三氧化二铝2~10%混合喷吹剂,有效提升了铁水喷吹脱硫用镁粉脱硫剂利用率,降低了喷吹脱硫成本;但该方法对于脱硫喷溅问题仍未完全解决。
8.申请号为202210872079.1的发明专利申请公开了“一种用于复杂钒钛高硫铁水喷吹氧化钙基脱硫剂及其应用”,该方法通过配制石灰粉cao、电石cac2、萤石caf2、以及ad粉的复合喷吹剂,其中:cao:68wt%~75wt%,cac2:7wt%~8wt%,caf2:5wt%~6wt%,al:0.5wt%~1.0wt%,al2o3:2wt%~3wt%;并根据铁水原始硫含量、铁水温度,确定脱硫剂加入量;将混合好的氧化钙基脱硫剂用氮气作为载气通过喷枪喷入铁水中进行脱硫;该方法很好的解决了复杂钒钛高硫铁水脱硫率低、预处理时间偏长影响生产组织的问题;但该方法中含有一定的cac2和caf2,不利于安全生产和环境保护。
9.论文《铝渣复合脱硫剂在kr铁水脱硫过程中的应用》介绍了采用部分铝渣与石灰粉混合在kr脱硫中提高脱硫效率的实践,但对于喷吹脱硫而言,由于反应动力学条件较差,且铝渣中含有近50%的al2o3、甚至更高,影响脱硫反应速率,不利于快速脱硫。
技术实现要素:10.本发明要解决的技术问题是提供一种有效解决脱硫喷溅的钙铝基脱硫剂复合喷吹脱硫的方法。
11.为解决上述技术问题,本发明所采取的技术方案是:铁水预处理时采用钝化石灰粉、铝粉复合喷吹进行脱硫;所述铁水初始硫含量0.030wt%<s≤0.045wt%时,喷吹质量配比为9.0≤钝化石灰粉/铝粉<10、0.70kg/t铁水≤铝粉消耗量<0.80kg/t铁水、4.0kg/min<铝粉喷吹速度≤4.5kg/min;所述铁水初始硫含量0.020wt%<s≤0.030wt%时,喷吹质量配比为8.0≤钝化石灰粉/铝粉<9.0、0.60kg/t铁水≤铝粉消耗量<0.70kg/t铁水、3.5kg/min<铝粉喷吹速度≤4.0kg/min;所述铁水初始硫含量0.010wt%<s≤0.020wt%时,喷吹质量配比为7.0≤钝化石灰粉/铝粉<8.0、0.50kg/t铁水≤铝粉消耗量<0.60kg/t铁水、3.0kg/min≤铝粉喷吹速度≤3.5kg/min。
12.进一步的,所述复合喷吹时,顶枪头部距包底200~500mm。
13.进一步的,所述复合喷吹时的粉气比控制在90~100kg/m3。
14.进一步的,复合喷吹开始时铁水温度在1250℃及以上。
15.进一步的,所述铝粉的金属铝含量≥95wt%,铝粉粒度为0.1~1.0mm。
16.进一步的,所述钝化石灰粉中有效cao含量≥90wt%,钝化石灰粉粒度≤250目。
17.采用上述技术方案所产生的有益效果在于:本发明根据铁水初始硫含量的不同合理搭配铝粉、钝化石灰粉的配比、消耗量和喷吹速度,提高了脱硫剂的脱硫效率、降低了脱硫成本。采用本发明后,铁水中的硫含量可降至0.005wt%以下,与镁基脱硫剂相比,吨铁脱硫成本降低6~7元;喷吹脱硫过程中的铁水喷溅、冒烟现象明显改善;铁水脱硫后脱硫渣的粘度,较镁基脱硫剂明显提高,渣铁分离更加容易,扒渣铁损减少5~6kg/t铁。本发明对于提高我国钢铁工业资源、能源利用率,最大限度降低产品的能源消耗量也具有重要战略意义。
具体实施方式
18.下面结合具体实施方式对本发明作进一步详细的说明。
19.本钙铝基脱硫剂复合喷吹脱硫的方法采用金属铝粉和钝化石灰粉进行复合喷吹。当采用石灰粉脱硫时,可以得到下述反应(1):(cao)+[s]=(cas)+[o]、δg0=115430-38.18t
ꢀꢀ
(1);根据反应式(1)可以看出:提高cao活度、降低氧势、提高温度、反应界面生成液相渣均可促进脱硫反应进行。
[0020]
当钝化石灰粉中混入一定的铝粉时,会有下述反应(2):3[s]+3cao+2[al]=3cas+al2o3ꢀꢀ
(2);而反应式(2)由以下基本反应(3)-(7)组成:ca+1/2o2=cao、δg0=-900300+275.1t
ꢀꢀ
(3)ca+1/2s2=cas、δg0=
ꢀ‑
548100+103.8t
ꢀꢀ
(4)2al+3/2o2=al2o3、δg0=-1683200+325.6t
ꢀꢀ
(5)al=[al]、δg0=-63178-27.91t
ꢀꢀ
(6)1/2s2=[s]、δg0=-135060+23.43t
ꢀꢀ
(7)。
[0021]
根据基本反应公式(3)-(7)及其各自δg0的计算公式可以得到反应(2)的δg0的计算公式(8):δg0=
ꢀ‑
95064
ꢀ‑ꢀ
202.77t
ꢀꢀ
(8);而镁基脱硫剂的基本反应为:[s]+[mg]=mgs、δg0=-325950+98.77t
ꢀꢀ
(9)。
[0022]
由公式(1)、(8)、(9)可以知,cao+al脱硫反应的标准吉布斯自由能明显低于镁粉脱硫及纯石灰粉脱硫的标准吉布斯自由能,这在热力学方面证实了cao+al脱硫的可行性。另外,cao+al脱硫反应生成的al2o3会使cao的溶解率提高,这进一步促进了脱硫反应的进行。并且,由于al的气化产生的蒸汽压明显低于mg气化产生的蒸气压,这使得脱硫反应变得更加柔和,减少了脱硫过程的喷溅和冒烟现象。
[0023]
基于上述原理,本钙铝基脱硫剂复合喷吹脱硫的方法采用下述工艺:所适用铁水的初始成分范围为(wt):c:3.5%~5.5%,si:0.15%~055%,mn:0.15%~1.5%;s:0.010%~0.045%,p≤0.15%;喷吹步骤为:(1)将铝粉和钝化石灰粉分别储存在密封料仓和各自的喷吹罐内;所述铝粉中,金属铝含量≥95wt%、al2o3含量≤5wt%,粒度为0.1~1.0mm;所述钝化石灰粉中,有效cao含量在90wt%及以上、s含量≤0.05wt%、活性度≥320ml,粒度≤250目。
[0024]
(2)当铁水包进站后,根据铁水初始硫含量,确定铝粉加入量、钝化石灰粉、铝粉配比以及钝化石灰粉加入量;所述铝粉、钝化石灰粉加入量与铁水初始硫含量的对应关系如下述表1所示。
[0025]
表1:铝粉、钝化石灰粉加入量与铁水初始硫含量的对应关系
(3)当铁包到达喷吹位后,开启喷吹氮气阀,将顶枪头部降至距包底200~500mm;开始复合喷吹时铁水温度在1250℃及以上;开启钝化石灰粉喷吹阀门,喷入石灰粉;然后打开铝粉喷吹阀门,通过调整铝粉、钝化石灰粉流态化气源控制阀的开口度和调整铝粉、钝化石灰粉的喷速度和喷吹比例,具体见上述表1。
[0026]
(4)喷吹过程中,喷吹粉气比控制在90~100kg/m3;喷吹结束后,先关闭铝粉喷吹阀门,再关闭钝化石灰粉喷吹阀门,提枪,关闭氮气;将铁水包车开至扒渣位,进行铁水包扒渣操作,将顶渣扒至“0”点以下。
[0027]
实施例1-3:采用的铝粉的金属铝含量95wt%、al2o3含量5wt%,粒度为0.1~0.5mm;钝化石灰粉的有效cao含量92wt%、s含量0.03wt%、活性度320ml,粒度≤250目。
[0028]
实施例1:本钙铝基脱硫剂复合喷吹脱硫的方法采用下述具体工艺。
[0029]
铁水包内的铁水重量为140吨,铁水温度1406℃,初始铁水硫含量0.045%。铁水包到喷吹位后,开启载气氮气阀门,将顶枪头部降至距包底500mm处,开启钝化石灰粉喷吹阀门,喷入钝化石灰粉,然后打开铝粉喷吹阀门,通过调整流态化气源控制阀的开口度和调整铝粉、钝化石灰粉的喷速度和喷吹比例;铝粉喷吹速度为4.5kg/min、总喷吹量为110.6kg(折合吨铁0.79kg),钝化石灰粉与铝粉的配比为9.9:1,石灰喷吹速度为44.5kg/min、喷吹总量为1094.9kg,喷吹过程中喷吹粉气比按100kg/m3控制。喷吹24.6min后喷吹结束,先关闭铝粉喷吹阀门,再关闭钝化石灰粉喷吹阀门,提枪、关闭氮气,将铁水包车开至扒渣位,进行铁水包扒渣操作,将顶渣扒至“0”点以下。取样检测,铁水中的硫含量为0.004w%,铁水温度1379℃,扒渣铁损18kg/t。
[0030]
实施例2:本实施例除下述工艺外,其他与实施例1采用相同或相同配比的参数:铁水硫含量0.031w%,铝粉喷吹速度为4.1kg/min、总喷吹量为98kg(折合吨铁0.70kg),钝化石灰粉与铝粉的配比为9:1,石灰喷吹速度为36.9kg/min、喷吹总量为882kg,23.9min后喷吹结束。取样检测,铁水中硫含量0.0027w%,铁水温度1381℃,扒渣铁损15kg/t。
[0031]
实施例3:本实施例除下述工艺外,其他与实施例1采用相同或相同配比的参数。实施例3铁水硫含量0.035w%,铝粉喷吹速度为4.3kg/min、总喷吹量为105kg(折合吨铁0.75kg),钝化石灰粉与铝粉的配比为9.5:1,石灰喷吹速度为40.9kg/min、喷吹总量为997.5kg,24.4min后喷吹结束。取样检测,铁水中硫含量0.0029w%,铁水温度1380℃,扒渣铁损16kg/t。
[0032]
实施例4-6:采用的铝粉的金属铝含量98wt%、al2o3含量2wt%,粒度为0.5~1.0mm;钝化石灰粉的有效cao含量90wt%、s含量0.04wt%、活性度350ml,粒度≤150目。
[0033]
实施例4:本钙铝基脱硫剂复合喷吹脱硫的方法采用下述具体工艺。
[0034]
铁水包内的铁水重量为138吨,铁水温度1350℃,初始铁水硫含量0.030%。铁水包到喷吹位后,开启载气氮气阀门,将顶枪头部降至距包底300mm处,开启钝化石灰粉喷吹阀门,喷入钝化石灰粉,然后打开铝粉喷吹阀门,通过调整流态化气源控制阀的开口度和调整铝粉、钝化石灰粉的喷速度和喷吹比例,铝粉喷吹速度为4.0kg/min、总喷吹量为95.2kg(折合吨铁0.69kg),钝化石灰粉与铝粉的配比为8.9:1,石灰喷吹速度为35.6kg/min、喷吹总量为847.5kg,喷吹过程中喷吹粉气比按95kg/m3控制。23.8min后喷吹结束,先关闭铝粉喷吹阀门,再关闭钝化石灰粉喷吹阀门,提枪,关闭氮气,将铁水包车开至扒渣位,进行铁水包扒渣操作,将顶渣扒至“0”点以下。取样检测后铁水中的硫含量为0.0038w%,铁水温度1321℃,扒渣铁损16kg/t。
[0035]
实施例5:本实施例除下述工艺外,其他与实施例4采用相同或相同配比的参数:实施例5铁水硫含量0.021w%,铝粉喷吹速度为3.6kg/min、总喷吹量为82.8kg(折合吨铁0.60kg),钝化石灰粉与铝粉的配比为8:1,石灰喷吹速度为28.8kg/min、喷吹总量为662.4kg,23.0min后喷吹结束。取样检测,铁水中硫含量0.0027w%,铁水温度1320℃,扒渣铁损14kg/t。
[0036]
实施例6:本实施例除下述工艺外,其他与实施例4采用相同或相同配比的参数:实施例6铁水硫含量0.026w%,铝粉喷吹速度为3.7kg/min、总喷吹量为89.7kg(折合吨铁0.65kg),钝化石灰粉与铝粉的配比为8.5:1,石灰喷吹速度为31.5kg/min、喷吹总量为762.5kg,24.2min后喷吹结束。取样检测,铁水中硫含量0.0029w%,铁水温度1320℃,扒渣铁损14kg/t。
[0037]
实施例7-9:采用的铝粉的金属铝含量96wt%、al2o3含量4wt%,粒度为0.1~1.0mm;钝化石灰粉的有效cao含量93wt%、s含量0.05wt%、活性度380ml,粒度≤200目。
[0038]
实施例7:本钙铝基脱硫剂复合喷吹脱硫的方法采用下述具体工艺。
[0039]
铁水包内的铁水重量为142吨,铁水温度1250℃,初始铁水硫含量0.020%。铁水包到喷吹位后,开启载气氮气阀门,将顶枪头部降至距包底200mm处,开启钝化石灰粉喷吹阀门,喷入钝化石灰粉,然后打开铝粉喷吹阀门,通过调整流态化气源控制阀的开口度和调整铝粉、钝化石灰粉的喷速度和喷吹比例,铝粉喷吹速度为3.5kg/min、总喷吹量为83.8kg(折合吨铁0.59kg),钝化石灰粉与铝粉的配比为7.9:1,石灰喷吹速度为27.65kg/min、喷吹总量为661.8kg,喷吹过程中喷吹粉气比按90kg/m3控制。23.9min后喷吹结束,先关闭铝粉喷吹阀门,再关闭钝化石灰粉喷吹阀门,提枪,关闭氮气,将铁水包车开至扒渣位,进行铁水包扒渣操作,将顶渣扒至“0”点以下。取样检测后铁水中的硫含量为0.0028w%,铁水温度1221℃,扒渣铁损14kg/t。
[0040]
实施例8:本实施例除下述工艺外,其他与实施例7采用相同或相同配比的参数:实施例8铁水硫含量0.011w%,铝粉喷吹速度为3.0kg/min、总喷吹量为71kg(折合吨铁0.50kg),钝化石灰粉与铝粉的配比为7:1,石灰喷吹速度为21kg/min、喷吹总量为497kg,23.7min后喷吹结束,结束后取样检测,铁水中硫含量0.0039w%,铁水温度1224℃,扒渣铁损13kg/t。
[0041]
实施例9:本实施例除下述工艺外,其他与实施例7采用相同或相同配比的参数:实施例9铁水硫含量0.015w%,铝粉喷吹速度为3.3kg/min、总喷吹量为78.1kg(折合吨铁0.55kg),钝化
石灰粉与铝粉的配比为7.5:1,石灰喷吹速度为24.8kg/min、喷吹总量为585.7kg,23.7min后喷吹结束,结束后取样检测,铁水中硫含量0.0035w%,铁水温度1228℃,扒渣铁损14kg/t。
[0042]
对比统计:采用本方法前,采用镁基脱硫剂和常规工艺进行预处理脱硫,统计某车间120炉次,其中,铁水脱硫后的硫含量在0.002~0.005wt%范围,25炉次出现铁水喷溅、110炉次出现冒烟现象、平均扒渣铁损22kg/t铁。采用本方法后,统计该车间127炉次,其中,铁水脱硫后的硫含量在0.002~0.005wt%范围,0炉次出现铁水喷溅、11炉次出现冒烟现象、平均扒渣铁损14.5kg/t铁。