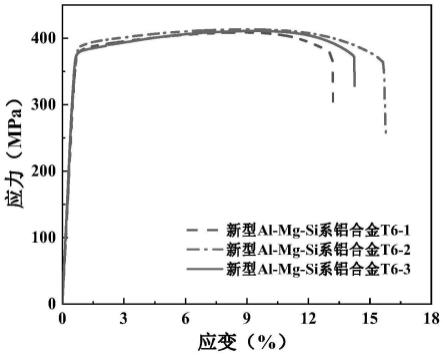
一种高强高耐蚀al-mg-si合金及其制备方法
技术领域
1.本发明涉及新材料技术领域,尤其涉及一种高强高耐蚀al-mg-si合金及其制备方法。
背景技术:2.al-mg-si系(aa 6000系)合金广泛用于建筑、船舶制造、新能源汽车、轨道交通等领域。其中,aa6005、aa6061、aa6082等是目前常用的al-mg-si系工业铝合金,经铸造、均匀化、变形和固溶时效热处理(t6)后的屈服强度约为240~260mpa,抗拉强度约为260~310mpa。相比于al-cu-mg系(aa 2000系)和al-zn-mg-cu系(aa 7000系)高强铝合金,al-mg-si系铝合金具有优秀的成形性、耐腐蚀性和可焊接性,以及较低原材料成本,其主要不足之处是强度较低。
3.针对强度较低的缺陷,aa6013将cu含量提高至0.8~1.2%,实现强度较大幅度提高,t6态的屈服强度约为290mpa、抗拉强度约为350mpa,是目前国内外实现工程应用、强度最高的al-mg-si系铝合金之一,但较高的cu含量导致aa6013合金的耐蚀性和焊接性显著下降。
4.若能在不降低耐蚀性和焊接性的前提下大幅提高al-mg-si系合金的强度,将大大提高该系合金的应用范围,甚至有望代替全铝汽车中的部分al-cu-mg系和al-zn-mg-cu系高强铝合金,从而实现整车材料“素化”,大幅降低后续回收难度和回收成本。
5.al-mg-si系合金的强化机制主要是高密度纳米相的析出强化,mg、si作为主要强化元素,其含量直接决定强化效果。有研究表明,每增加0.1% mg2si,强度可以提高5mpa,但共晶温度下mg2si在al中的溶解度为1.85%,加入过多的mg和si元素不仅无法提供强化效果,还会以微米级初生mg2si的形式存在,降低材料力学性能和耐蚀性能。因此,仅依靠mg、si两种元素的强化作用难以大幅提高合金的强度。
6.进一步提高al-mg-si系合金强度的有效手段之一是添加cu、cr、mn、zr、ti、fe、sc、er、y等微合金化元素,其中sc、er、y元素虽然强化效果明显,但价格昂贵、不适合大规模工业化生产。添加cu可以增强时效硬化响应,但含cu析出物在晶界的偏聚,增大晶界与基体的电位差,使合金晶间腐蚀倾向增大;mn、cr、zr、ti等元素形成的多尺度弥散相可以起到细晶强化和弥散强化效果,但如果含量过高,则会形成大尺寸难溶相,恶化材料性能;mn含量过高还会在挤压时产生粗晶环降低材料性能,并且容易挤裂,因此需要控制在较低范围;fe可以与过剩si形成alfesi三元化合物,有助于细化晶粒,但过量的fe在晶界处形成粗大针状结晶相对合金性能产生有害影响。并且,如果采用传统的实验试错法在al-mg-si系合金中添加强化元素实现综合性能提升,元素的种类和含量的选择难度大,开发效率低、成本高,而数据驱动的机器学习方法可以优化相互冲突的性能,用来辅助新材料的研发。
7.因此,有必要研究一种高强高耐蚀al-mg-si合金及其制备方法来应对现有技术的不足,以解决或减轻上述一个或多个问题。
技术实现要素:8.有鉴于此,本发明提供了一种高强高耐蚀al-mg-si合金及其制备方法,能够获得高强高耐蚀的al-mg-si合金,相较于目前的aa6013合金,其能够在屈服强度、抗拉强度和耐蚀性能上均得到显著提高。
9.一方面,本发明提供一种高强高耐蚀al-mg-si合金的制备方法,所述方法的步骤包括:
10.s1、确定成分数据:获取由机器学习方法给出的成分-性能预测结果,并根据强塑性和耐蚀性选择出满足要求的成分数据;
11.s2、铸造:根据s1得到的成分数据进行熔炼和铸造,得到al-mg-si合金锭;
12.s3、均匀化处理:采用两步均匀化工艺对s2得到的al-mg-si合金锭进行处理,以提高初生mg2si溶解度,改善材料塑性;
13.s4、热挤压:对均匀化处理后的al-mg-si合金锭进行热挤压;
14.s5、固溶处理:将热挤压后合金制品在固溶温度下进行固溶处理,随后水淬至室温;
15.s6、时效处理:将s5处理后的合金制品在时效温度下进行时效处理,随后空冷至室温。
16.如上所述的方面和任一可能的实现方式,进一步提供一种实现方式,步骤s3中两步均匀化工艺的内容包括:
17.s3.1、将s2得到的al-mg-si合金锭置于电阻炉中并升温至460~480℃,保温4~8h,以消除局部偏析,防止局部过烧;
18.s3.2、再以0.5~1℃/min的速率升温至530~550℃,保温20~30h后,以充分消除成分偏析,最大限度溶解微米相;
19.s3.3、从电阻炉中取出al-mg-si合金锭并空冷至室温。
20.如上所述的方面和任一可能的实现方式,进一步提供一种实现方式,步骤s4中热挤压的内容包括:将al-mg-si合金锭置于420~460℃温度下保温2~3h后进行挤压;挤压器件,包括挤压筒、模具和挤压垫,的温度均为420~480℃,即保证挤压过程中的温度能满足要求。
21.如上所述的方面和任一可能的实现方式,进一步提供一种实现方式,步骤s4中热挤压的挤压比为5~50。
22.如上所述的方面和任一可能的实现方式,进一步提供一种实现方式,步骤s5中固溶处理的内容包括:在540~560℃温度下保温10~120分钟。
23.如上所述的方面和任一可能的实现方式,进一步提供一种实现方式,步骤s6中时效处理的内容包括:在160~200℃温度下保温2~50h。
24.如上所述的方面和任一可能的实现方式,进一步提供一种实现方式,步骤s2的内容包括:根据s1得到的成分数据,采用纯度在99.99%以上的al金属和mg金属,以及al-20si、al-50cu、al-mn、al-fe和al-10zr中间合金作为原料,进行熔炼和铸造;熔炼温度为700~750℃,然后浇注成锭,脱模空冷,得到al-mg-si合金锭。
25.另一方面,本发明提供一种高强高耐蚀al-mg-si合金,所述al-mg-si合金采用如上任一所述的高强高耐蚀al-mg-si合金的制备方法制备得到;
26.所述al-mg-si合金的组分包括:mg含量为0.65~0.95wt.%,si含量为0.7~0.9wt.%,cu含量为0.1~0.35wt.%,mn含量为0.1~0.3wt.%,cr含量为0.1~0.5wt.%,fe含量为0.1~0.5wt.%,zr含量为0.05~0.3wt.%,ti含量为0.05~0.3wt.%,杂质元素总和<0.2%,余量为al。
27.如上所述的方面和任一可能的实现方式,进一步提供一种实现方式,所述al-mg-si合金的基体中具有均匀分布的尺寸在50~200nm的α-al(mnfecr)si和尺寸在10~40nm的(al,si)3zr弥散相,用于在热变形过程中提供钉扎晶界,阻碍位错运动,从而实现细晶强化和弥散强化。
28.如上所述的方面和任一可能的实现方式,进一步提供一种实现方式,所述al-mg-si合金的性能同时满足:屈服强度≥370mpa,抗拉强度≥400mpa,断后伸长率≥13%,astm g31-2012a标准下的腐蚀速率≤0.04565mm
·
a-1
。
29.与现有技术相比,上述技术方案中的一个技术方案具有如下优点或有益效果:本发明的新型高强高耐蚀al-mg-si系铝合金屈服强度≥370mpa,抗拉强度≥400mpa,断后伸长率≥13%,与目前较高强度的aa6013合金相比,新型合金t6态的屈服强度提高25%以上,抗拉强度提高15%以上,耐蚀性能显著提高;和目前常用的aa6005、aa6061、aa6082等al-mg-si系合金相比,屈服强度提高40%以上,抗拉强度提高30%以上,且耐蚀性能相当;对比例1显示了aa6013含cu 0.8%,强度350mpa,本发明较其降低了50%cu,并加入cr、zr等元素,耐蚀性改善的同时,强度得到大幅提高;
30.上述技术方案中的另一个技术方案具有如下优点或有益效果:本发明的新型高强高耐蚀al-mg-si系铝合金在成分设计中采用低mg、si含量设计,使基体中微米级难溶相体积分数大大减少,在腐蚀溶液中局部点蚀倾向小;cu含量较低,相较于对比例1的cu含量降低了50%,并加入cr、zr等元素,合金的耐晶间腐蚀能力突出,在耐蚀性改善的同时,强度得到大幅提高;同时,将mn含量从一般的0.3~1.0wt.%(al-mg-si合金分很多种,该一般范围指cu、mn、cr、zr元素均存在的al-mg-si合金)降低到0.1~0.3wt.%,避免了mn含量过高导致的在挤压时产生粗晶环从而降低材料性能的情况,辅助提高合金的性能,使之能同时满足前面记载的高强和高耐蚀性,也不易挤裂,保证合金制品的制备成功率;
31.上述技术方案中的另一个技术方案具有如下优点或有益效果:本发明高强高耐蚀al-mg-si系铝合金加入适量的mn、cr、zr、ti微合金元素,使基体中均匀形成尺寸50~200nm的α-al(mnfecr)si和尺寸10~40nm的(al,si)3zr弥散相,在热变形过程中钉扎晶界,阻碍位错运动,提供细晶强化和弥散强化效果;并且不含昂贵的稀土元素,且制备工艺流程均采用常规方法,成本低,适合大规模工业化生产应用。
32.当然,实施本发明的任一产品并不一定需要同时达到以上所述的所有技术效果。
附图说明
33.为了更清楚地说明本发明实施例的技术方案,下面将对实施例中所需要使用的附图作简单地介绍,显而易见地,下面描述中的附图仅仅是本发明的一些实施例,对于本领域普通技术人员来讲,在不付出创造性劳动的前提下,还可以根据这些附图获得其它的附图。
34.图1是本发明实施例1提供的al-mg-si系铝合金t6拉伸应力-应变曲线图;图中所示是三组平行样的平均结果;
35.图2是本发明实施例1提供的al-mg-si系铝合金固溶时效显微组织形貌图;
36.图3是本发明实施例1提供的al-mg-si系铝合金固溶时效弥散相形貌图;
37.图4是本发明实施例1提供的al-mg-si系铝合金峰值时效析出相形貌图;
38.图5是本发明实施例1提供的al-mg-si系铝合金(a)与对比文件1提供的aa6013合金(b)晶间腐蚀形貌对比图。
具体实施方式
39.为了更好的理解本发明的技术方案,下面结合附图对本发明实施例进行详细描述。
40.应当明确,所描述的实施例仅仅是本发明一部分实施例,而不是全部的实施例。基于本发明中的实施例,本领域普通技术人员在没有做出创造性劳动前提下所获得的所有其它实施例,都属于本发明保护的范围。
41.本发明针对目前al-mg-si系工业铝合金强度不足的问题,开发出一种高强、高耐蚀性新型al-mg-si系合金及其制备方法,与目前较高强度的aa6013合金相比,新型铝合金t6态的屈服强度提高25%以上,抗拉强度提高15%以上,耐蚀性能显著提高;和目前常用的aa6005、aa6061、aa6082合金相比,屈服强度提高40%以上,抗拉强度提高30%以上,且耐蚀性能相当。
42.机器学习方法可以给出成分-性能的预测结果,可以节省成分设计前期的大量试错时间和成本。但机器学习给出的成分设计往往是能够取得较好效果的成分组成,但并非最好,还有待优化。本发明采用数据驱动的机器学习方法优化的合金元素种类和含量,从中挑选出强塑性好,耐蚀性好的成分再进行工艺优化和实验验证,得到最优设计结果。
43.通常情况下,加入大量的mg(1.0%以上),si(1.2%以上),cu(1.0%以上),可以使强度达到400mpa,但耐蚀性往往较差;本发明采用低mg、si、cu含量,以及本发明独特的制备方法,使得al-mg-si合金耐蚀性好、强度低,设计出同时满足400mpa以上,且耐蚀性好的al-mg-si合金。对比例1显示了aa6013含cu 0.8%,强度350mpa,本发明较其降低了50%cu,加入cr、zr等元素,耐蚀性改善,强度大幅提高。
44.本发明的新型高强、高耐蚀性al-mg-si系铝合金特征如下:mg含量为0.65~0.95wt.%,si含量为0.7~0.9wt.%,cu含量为0.1~0.35wt.%,mn含量为0.1~0.3wt.%,cr含量为0.1~0.5wt.%,fe含量为0.1~0.5wt.%,zr含量为0.05~0.3wt.%,ti含量为0.05~0.3wt.%,其余杂质元素总和<0.2%,余量为al。
45.上述高强高耐蚀al-mg-si铝合金的制备方法步骤如下:
46.(1)铸造:采用纯度99.99%的al、mg等纯金属和al-20si、al-50cu、al-mn、al-fe、al-10zr中间合金作为原料,熔炼和铸造高强高耐蚀al-mg-si合金,熔炼温度为700~750℃,浇注成锭,脱模空冷;
47.(2)均匀化:采用两步均匀化工艺,提高初生mg2si溶解度,有利于改善材料塑性;将(1)中铸造的锭子在电阻炉中升温至460~480℃,保温4~8h,消除局部偏析,防止局部过烧;再以0.5~1℃/min的速度缓慢升温至530~550℃,充分消除成分偏析,极大限度溶解微米相,保温20~30h后,取出空冷至室温;
48.该步骤是区别于一般制备方法的,采用两步均匀化工艺制备的合金基体中只含有
极少量的微米相,反应到最终结果就是大尺寸微米相的体积分数减少,从而提高强塑性,耐蚀性。如果直接升温到530~550℃均匀化,将出现局部过烧。
49.(3)热挤压:将(2)步骤的铸锭在炉中420~460℃保温2~3h后,取出进行挤压,挤压筒、模具、挤压垫的温度为420~480℃,挤压比为5~50;挤压比是指挤压筒腔的横断面面积同挤压制品总横断面面积之比;高mn含量的al-mg-si合金往往需要更高的挤压温度,一般要求540℃以上,本发明420~460℃的热挤压温度是本发明低mn含量的另一个优势,即节能环保,且低温容易保持合金成分的稳定,避免热活泼成分发生不可预测的反应;
50.(4)固溶:将热挤压后制品在540~560℃的电阻炉中进行10~120分钟固溶处理,随后水淬至室温;
51.(5)时效:将(4)步骤后的制品在160~200℃下,保温2~50h,随后空冷至室温。
52.实施例1:
53.新型高强高耐蚀al-mg-si系铝合金特征如下,mg含量为0.78wt.%,si含量为0.85wt.%,cu含量为0.30wt.%,mn含量为0.29wt.%,cr含量为0.19wt.%,fe含量为0.2wt.%,zr含量为0.13wt.%,ti含量为0.11wt.%,余量为al。
54.上述合金的制备方法步骤如下:
55.(1)铸造:采用纯度99.99%的al、mg等纯金属和al-20si、al-50cu、al-mn、al-fe、al-10zr中间合金作为原料,熔铸高强高耐蚀al-mg-si合金,熔炼温度为750℃,浇注成锭,脱模空冷;
56.(2)均匀化:将(1)中铸造的锭子在电阻炉中升温至480℃,保温4h,再以0.5℃/min的速度缓慢升温至540℃,保温24h,取出空冷至室温;
57.(3)挤压:将(2)步骤的铸锭在450℃保温2h后进行挤压,挤压筒、模具、挤压垫的温度为480℃,挤压比为25;
58.(4)固溶:将线切割后的制品在550℃的电阻炉中进行30分钟固溶处理,随后水淬至室温;
59.(5)时效:将(4)步骤后的制品在180℃下,保温10h,随后空冷至室温。
60.采用上述制备工艺流程制备三根标准拉伸试样,测试得到合金的力学性能为屈服强度378
±
5mpa,抗拉强度412
±
2mpa,延伸率14.5
±
1%。测试得到的三组应力-应变曲线如图1所示。
61.实施例1峰值时效的sem照片如图2所示,基体中只存在少量的微米相,黑色相为mg2si,白色相为al
15
(mnfecr)3si2;图3显示了基体中亚微米级弥散相,尺寸较大的椭球形相为α-al(mnfecr)si,尺寸较小的球形相为(al,si)3zr;图4显示了新型合金峰值时效的典型析出相,短棒状β
″
相和更窄更长的板条状q
′
相协同强化作用显著。
62.浸渍腐蚀实验按照astm g31-2012a标准进行。
63.取时效后的样品10mm
×
10mm
×
10mm,将其表面从200#砂纸打磨至2000#砂纸,丙酮洗去表面油污,测量实际尺寸并进行称重,之后放入3.5%nacl溶液中浸泡168小时,用70% hno3中酸洗表面腐蚀产物,对浸渍后的样品进行称重,并按公式(1)计算得到的腐蚀速率为0.04544
±
0.00021mm
·
a-1
,属于高耐腐蚀材料。
64.65.其中,r为腐蚀速率,m为腐蚀前的质量,m1是腐蚀后的质量,s是样品的总面积,t是腐蚀时间,d是合金的密度。为每组合金制备三个样品,并取三个样品的平均值作为最终结果。
66.实施例2:
67.新型高强高耐蚀al-mg-si系铝合金特征如下,mg含量为0.93wt.%,si含量为0.82wt.%,cu含量为0.35wt.%,mn含量为0.30wt.%,cr含量为0.18wt.%,fe含量为0.28wt.%,zr含量为0.14wt.%,ti含量为0.15wt.%,余量为al。
68.上述合金的制备方法步骤如下:
69.(1)铸造:采用纯度99.99%的al、mg等纯金属和al-20si、al-50cu、al-mn、al-fe、al-10zr中间合金作为原料,熔铸高强高耐蚀al-mg-si合金,熔炼温度为750℃,浇注成锭,脱模空冷;
70.(2)均匀化:将(1)中铸造的锭子在电阻炉中升温至480℃,保温6h,再以1℃/min的速度缓慢升温至540℃,保温24h,取出空冷至室温;
71.(3)挤压:将(2)步骤的铸锭在460℃保温2h后进行挤压,挤压筒、模具、挤压垫的温度为480℃,挤压比为16;
72.(4)固溶:将线切割的制品在560℃的电阻炉中进行30分钟固溶处理,随后水淬至室温;
73.(5)时效:将(4)步骤后的制品在170℃下,保温14h,随后空冷至室温。
74.采用上述制备工艺流程制备三根标准拉伸试样,测试得到合金的力学性能为屈服强度387
±
3mpa,抗拉强度416
±
2mpa,延伸率13.8
±
0.7%。
75.根据astm g31-2012a标准进行浸渍腐蚀实验,按公式(1)计算得到的腐蚀速率为0.04115
±
0.00034mm
·
a-1
,属于高耐腐蚀材料。
76.实施例3:
77.新型高强高耐蚀al-mg-si系铝合金特征如下,mg含量为0.69wt.%,si含量为0.90wt.%,cu含量为0.28wt.%,mn含量为0.20wt.%,cr含量为0.15wt.%,fe含量为0.22wt.%,zr含量为0.13wt.%,ti含量为0.08wt.%,余量为al。
78.上述合金的制备方法步骤如下:
79.(1)铸造:采用纯度99.99%的al、mg等纯金属和al-20si、al-50cu、al-mn、al-fe、al-10zr中间合金作为原料,熔铸高强高耐蚀al-mg-si合金,熔炼温度为750℃,浇注成锭,脱模空冷;
80.(2)均匀化:将(1)中铸造的锭子在电阻炉中升温至470℃,保温6h,再以0.8℃/min的速度缓慢升温至550℃,保温18h,取出空冷至室温;
81.(3)挤压:将(2)步骤的铸锭在460℃保温2h后进行挤压,挤压筒、模具、挤压垫的温度为480℃,挤压比为25;
82.(4)固溶:将线切割的制品在550℃的电阻炉中进行30分钟固溶处理,随后水淬至室温;
83.(5)时效:将(4)步骤后的制品在190℃下,保温6h,随后空冷至室温。
84.采用上述制备工艺流程制备三根标准拉伸试样,测试得到合金的力学性能为屈服强度375
±
2mpa,抗拉强度413
±
2mpa,延伸率15
±
0.5%。
85.根据astm g31-2012a标准进行浸渍腐蚀实验,按公式(1)计算得到的腐蚀速率为0.04342
±
0.00015mm
·
a-1
,属于高耐腐蚀材料。
86.对比例1:
87.制备aa6013合金,mg含量为0.82wt.%,si含量为0.90wt.%,cu含量为0.80wt.%,mn含量为0.21wt.%,fe含量为0.18wt.%,zn含量为0.10wt.%,余量为al,其他步骤同实施例1。
88.测试得到合金的力学性能为屈服强度286
±
5mpa,抗拉强度347
±
3mpa,延伸率16
±
1%。
89.将对比例1和实施例1按照astm g110标准进行晶间腐蚀测试。
90.表面从200#砂纸打磨至2000#砂纸,在90℃刻蚀液(945ml去离子水+5ml 48% hf+50ml 70% hno3)中刻蚀60s,再在70% hno3中酸洗1min,最后浸泡在腐蚀液(57g nacl+10ml h2o2,用去离子水稀释至1l)中,实验温度为30℃,浸泡时间24h。
91.对比结果如表1所示,晶间腐蚀形貌如图5所示。对比例1的最大腐蚀深度为220μm,平均腐蚀深度为189μm,实施例1的最大腐蚀深度为97μm,平均腐蚀深度为81μm。新型al-mg-si系合金耐晶间腐蚀能力较aa6013具有显著的提升。
92.表1al-mg-si系铝合金与aa6013力学性能和耐蚀性能对比表
[0093][0094]
以上对本技术实施例所提供的一种高强高耐蚀al-mg-si合金及其制备方法,进行了详细介绍。以上实施例的说明只是用于帮助理解本技术的方法及其核心思想;同时,对于本领域的一般技术人员,依据本技术的思想,在具体实施方式及应用范围上均会有改变之处,综上所述,本说明书内容不应理解为对本技术的限制。