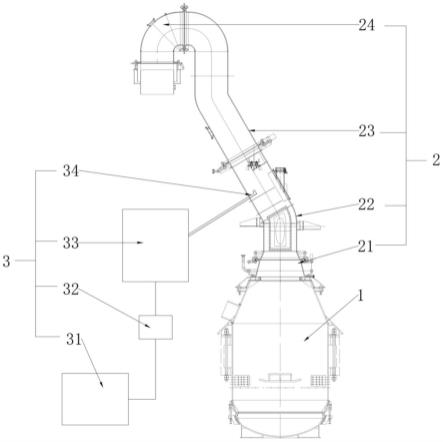
1.本技术涉及转炉煤气回收技术领域,尤其涉及一种可提升转炉煤气回收量与热值的转炉汽化冷却烟道、转炉煤气回收前处理系统与方法,以及一种能够提升转炉煤气回收量与热值的转炉。
背景技术:2.转炉“负能炼钢”是炼钢生产过程中节能技术的综合体现,它不仅体现了节约能源、减少环境污染,还体现了一个厂的能源管理水平。“负能炼钢”的含义是指炼钢过程中回收的煤气和蒸汽能量大于实际炼钢过程中消耗的水、电、风、气等能量总和,而转炉煤气回收就占整个转炉工序能源回收部分的80%~90%,是降低工序能耗、实现负能炼钢的关键环节。因此,为实现节能减排,转炉煤气回收系统已成为当前冶金行业中广泛采用的能量回收的工艺环节之一。
3.转炉煤气是转炉炼钢过程中的副产品,它是转炉炼钢过程中,铁水中的碳在高温下和吹入的氧生成一氧化碳和少量二氧化碳的混合气体。炉口烟气温度可达1450℃~1600℃,是一种无色、无味的有毒气体,发热量约为6800kj/m3~10000kj/m3,燃点约为600℃~700℃,密度为1.25kg/n
·
m3~1.29kg/n
·
m3。转炉煤气的成分随冶炼过程而不断变化,其主要成分按比重递减规则排序为:co、co2、n2、h2、o2。在转炉煤气中主要烟气成分为co,为了达到转炉煤气回收的安全指标,必须保证转炉煤气温度和浓度不在着火点与爆炸极限浓度范围内。
4.在转炉吹炼过程中,产生约1600℃~1800℃的高温废气,主要成分是co、o2、co2、n2和so2,co含量可高达80%以上,含有大量的工业粉尘,含尘浓度可达80~150g/nm3,吨钢可产生10kg~30kg工业粉尘。因此,转炉烟气具有高温、有毒、易燃易爆、含尘量高等特点,可以被回收使用,实现节能减排。
5.转炉煤气回收系统的主要工艺系统包括烟道换热装置、冷却装置、粗除尘装置、精除尘装置、引风机、切换站、管网的设置以及控制系统的配备等。转炉烟气净化回收系统主要包括烟气的收集、输导、降温、净化、抽引与放散等过程,但无论是采用og法(转炉烟气湿法除尘)还是lt法(转炉烟气静电除尘)都离不开汽化冷却烟道。转炉汽化冷却烟道作为炼钢工艺的关键设备之一,其作用在于降低排烟温度、回收高温烟气中的余热,同时收集烟气中的部分烟尘,保证炼钢过程的顺利进行。og法和lt法主要区别在于汽化烟道后面的除尘方式不一样,但是在汽化烟道部分结构大致相同,主要包括:活动烟罩、炉口固定段烟道、中间段烟道和末段烟道等。
6.转炉煤气回收量的影响因素包括转炉设备条件、原料条件、钢水碳含量、空气吸入量、煤气回收条件、供氧强度等,其中空气吸入量、煤气回收条件、供氧强度等对其影响尤为显著。
7.现有转炉煤气回收系统在应用实践中还存在如下不足:在转炉烟气高温(1600℃~1800℃)、高粉尘(80-150g/nm3)、co含量高(0-80%)、周期性冶炼等极端条件下,转炉煤
气回收量低且煤气热值较低,造成了转炉煤气的极大浪费;进一步的,转炉煤气在冶炼中期co2含量和冶炼前后期的o2含量还有进一步降低的需求,转炉煤气中o2含量的比重大于2%,则会有爆炸风险。
8.因此,基于对安全的考虑,以及提升转炉煤气的回收品质,现阶段应当提出新的技术方案以提高转炉煤气回收量和热值,并降低转炉烟气二氧化碳排放量。
技术实现要素:9.本技术提供一种转炉及其汽化冷却烟道、转炉煤气回收前处理系统与方法,用以解决现有转炉煤气回收量不足且煤气热值低的问题。
10.为了实现上述目的,本技术提供如下技术方案:
11.第一个方面,本技术提供一种可提升转炉煤气回收量的转炉汽化冷却烟道,包括活动烟罩、炉口固定段烟道、中间段烟道和末端烟道;所述活动烟罩位于转炉炉口上方,所述活动烟罩的上部与所述炉口固定段烟道的下部相连,所述炉口固定段烟道的上部与所述中间段烟道的下部通过密封伸缩连接装置相连,所述中间段烟道的上部与所述末端烟道相连;
12.所述炉口固定段烟道、中间段烟道和末端烟道中,至少有一段烟道与碳输送系统相连,所述碳输送系统向与其相连的烟道内喷射干熄焦除尘灰,进入转炉汽化冷却烟道的转炉煤气中的二氧化碳和氧气分别与所述干熄焦除尘灰反应生成一氧化碳,所述干熄焦除尘灰的粒径范围为200目~300目;所述碳输送系统将干熄焦除尘灰喷射在温度范围为900℃~1600℃的烟道内。
13.上述技术方案进一步的,所述干熄焦除尘灰与所述转炉煤气中的二氧化碳及氧气的反应温度范围为900℃~1600℃。
14.进一步的,所述碳输送系统包括储碳仓、气力输灰装置、智能定碳撬装设备、高速喷枪和控制装置;所述储碳仓用以储存干熄焦除尘灰,所述气力输灰装置用以实现将储碳仓内的干熄焦除尘灰输送至所述智能定碳撬装设备中。
15.进一步的,所述智能定碳撬装设备包括定量粉末输送装置、气流输送装置、粉末分配装置、测温防堵装置以及检测装置;所述定量粉末输送装置自所述气力输灰装置接收干熄焦除尘灰,且将干熄焦除尘灰定量输送至所述粉末分配装置;所述粉末分配装置内设置有多个粉末输送通道,每个所述粉末输送通道的出口端与转炉汽化冷却烟道相连通;所述气流输送装置与所述粉末分配装置相适配,用以将各个粉末输送通道内的干熄焦除尘灰朝转炉汽化冷却烟道吹送。
16.进一步的,所述测温防堵装置用以对粉末输送通道内的温度进行实时测量以获得粉末输送通道的管道通畅状态。
17.进一步的,所述检测装置用以实现对转炉内的烟气流量、烟气成分及烟气温度的检测。
18.进一步的,所述控制装置用以接收所述检测装置测得的各项数据,且根据接收的数据调整所述定量粉末输送装置、气流输送装置、粉末分配装置的运行状态。
19.进一步的,所述粉末分配装置内的每个粉末输送通道的出口端设置有一个所述高速喷枪,所述高速喷枪将粉末输送通道内的干熄焦除尘灰喷射至转炉汽化冷却烟道中。
20.第二个方面,本技术提供一种安装在转炉汽化冷却烟道上的转炉煤气回收前处理系统,所述转炉煤气回收前处理系统包括转炉汽化冷却烟道,以及安装在所述转炉汽化冷却烟道上的碳输送系统;所述碳输送系统将干熄焦除尘灰吹送至转炉汽化冷却烟道内,使得转炉煤气中的二氧化碳和氧气分别与所述干熄焦除尘灰在温度范围为900℃~1600℃的烟道内反应生成一氧化碳。
21.上述技术方案中进一步的,所述碳输送系统包括储碳仓、气力输灰装置、智能定碳撬装设备、高速喷枪和控制装置;所述储碳仓用以储存干熄焦除尘灰,所述气力输灰装置用以实现将储碳仓内的干熄焦除尘灰输送至所述智能定碳撬装设备中。
22.进一步的,所述智能定碳撬装设备包括定量粉末输送装置、气流输送装置、粉末分配装置、测温防堵装置以及检测装置;所述气力输灰装置将干熄焦除尘灰输送至所述定量粉末输送装置,所述定量粉末输送装置将干熄焦除尘灰定量输送至所述粉末分配装置;所述粉末分配装置内设置有多个粉末输送通道,每个所述粉末输送通道的出口端与转炉汽化冷却烟道相连通;所述气流输送装置与所述粉末分配装置相适配,用以将各个粉末输送通道内的干熄焦除尘灰朝转炉汽化冷却烟道吹送。
23.进一步的,所述测温防堵装置用以对粉末输送通道内的温度进行实时测量以获得粉末输送通道的管道通畅状态;所述检测装置用以实现对转炉内的烟气流量、烟气成分及烟气温度的检测。
24.进一步的,所述控制装置用以接收所述检测装置测得的各项数据,且根据接收的数据调整所述定量粉末输送装置、气流输送装置、粉末分配装置的运行状态。
25.进一步的,所述粉末分配装置内的每个粉末输送通道的出口端设置有一个所述高速喷枪,所述高速喷枪将粉末输送通道内的干熄焦除尘灰喷射至转炉汽化冷却烟道中。
26.第三个方面,本技术提供一种可提升转炉煤气回收量的方法,包括:将碳输送系统与转炉汽化冷却烟道相连,所述碳输送系统向所述转炉汽化冷却烟道内喷射干熄焦除尘灰;转炉煤气中的二氧化碳和氧气分别与所述干熄焦除尘灰在温度范围为900℃~1600℃的烟道内反应生成一氧化碳。
27.上述技术方案中进一步的,所述碳输送系统的出口端设置高速喷枪,通过所述高速喷枪将所述干熄焦除尘灰喷射至转炉汽化冷却烟道内。
28.进一步的,所述干熄焦除尘灰的粒径范围为200目~300目。
29.第四个方面,本技术提供一种可提升转炉煤气回收量的转炉,所述转炉的炉口上方设置有上述的转炉汽化冷却烟道,所述转炉汽化冷却烟道与碳输送系统相连,所述碳输送系统向所述转炉汽化冷却烟道内喷射粒径范围为200目~300目的干熄焦除尘灰,所述碳输送系统将干熄焦除尘灰喷射在温度范围为900℃~1600℃的烟道内,转炉煤气中的二氧化碳和氧气分别与所述干熄焦除尘灰反应生成一氧化碳。
30.相比现有技术,本技术具有以下有益效果:
31.1、本技术提供一种可提升转炉煤气回收量的转炉汽化冷却烟道,该转炉汽化冷却烟道与碳输送系统相连,碳输送系统向与其相连的烟道内喷射干熄焦除尘灰,进入转炉汽化冷却烟道的转炉煤气中的二氧化碳和氧气分别与所述干熄焦除尘灰反应生成一氧化碳。现有技术中,转炉汽化冷却烟道将转炉煤气输送回收,转炉煤气中的二氧化碳和氧气含量较高,而氧气含量较高则导致了转炉煤气直接排放,浪费了能源,也增加了企业的碳排放,
加剧温室效应。而本技术提供的转炉汽化冷却烟道与碳输送系统相连,使得转炉汽化冷却烟道内的转炉煤气与干熄焦除尘灰在烟道高温环境下发生反应,利用干熄焦除尘灰将转炉煤气中的二氧化碳和氧气反应为可回收利用的一氧化碳,提升了转炉煤气热值,同时降低了二氧化碳和氧气的含量,提升了转炉煤气对一氧化碳的回收量,即提升了转炉煤气的回收品质。再者,降低了氧气含量也降低了爆炸风险,且干熄焦除尘灰利用烟道高温环境完成反应,实现了对转炉煤气中热量的利用。
32.2、本技术提供的可提升转炉煤气回收量的转炉汽化冷却烟道内,与转炉煤气中的二氧化碳和氧气分别发生反应的是干熄焦除尘灰,干熄焦除尘灰是焦化厂产生的焦化除尘废物,本技术使用干熄焦除尘灰作为反应碳源实现了废物的二次利用,变废为宝,降低了生产成本,实现了节能减排。
33.3、本技术还提供一种安装在转炉汽化冷却烟道上的转炉煤气回收前处理系统,现有的转炉煤气回收系统是将自转炉汽化冷却烟道内排出的转炉煤气依次送入一次除尘系统以及煤气柜中,一次除尘系统及煤气柜形成对转炉煤气的后处理回收系统,而转炉汽化冷却烟道内的转炉煤气中含有含量相对较高的二氧化碳和氧气,导致转炉煤气回收品质不高,二氧化碳排放量高,且氧气含量较高则存在一定的爆炸风险,导致转炉煤气后处理回收系统将该部分煤气放散,增加了炼钢工序的碳排放量。本技术提供的安装在转炉汽化冷却烟道上的转炉煤气回收前处理系统可在转炉煤气进入后处理回收系统前,先一步对转炉煤气进行处理,以提升转炉煤气的回收品质及回收量。具体的,本技术通过向转炉汽化冷却烟道内通入干熄焦除尘灰,同时利用烟道高温,实现转炉煤气中二氧化碳和氧气分别与干熄焦除尘灰反应,生成目标回收的一氧化碳,提升了一氧化碳的含量,同时降低了二氧化碳和氧气的含量,即提升了转炉煤气的回收品质,提升了转炉煤气的回收量,同时降低了烟囱放散煤气量,降低了爆炸风险,减少了炼钢工序的碳排放量。
34.4、本技术提供一种可提升转炉煤气回收量的方法,该方法主要通过向转炉汽化冷却烟道内通入干熄焦除尘灰,同时利用烟道高温,实现转炉煤气中二氧化碳和氧气分别与干熄焦除尘灰反应,生成目标回收的一氧化碳,实现了转炉煤气回收量的提升,同时提升了转炉煤气的热值,提高了转炉煤气的回收品质。
35.5、基于上述的可提升转炉煤气回收量的转炉汽化冷却烟道,本技术提供了一种可提升转炉煤气回收量的转炉,该转炉的转炉汽化冷却烟道与碳输送系统相连,碳输送系统向转炉汽化冷却烟道内喷射干熄焦除尘灰,转炉煤气中的二氧化碳和氧气分别与干熄焦除尘灰反应生成一氧化碳,该转炉的应用可提升转炉煤气回收量,提升转炉煤气的回收品质。
附图说明
36.为了更清楚地说明本技术实施例中的技术方案,下面将对实施例中所需要使用的附图作简单地介绍,显而易见地,下面描述中的附图仅仅是本技术的一些实施例,对于本领域普通技术人员来讲,在不付出创造性劳动的前提下,还可以根据这些附图获得其它附图。应当理解,附图中所示的具体形状、构造,通常不应视为实现本技术时的限定条件;例如,本领域技术人员基于本技术揭示的技术构思和示例性的附图,有能力对某些单元(部件)的增/减/归属划分、具体形状、位置关系、连接方式、尺寸比例关系等容易作出常规的调整或进一步的优化。
37.图1为不同温度下,干熄焦除尘灰与转炉煤气在烟道中发生的各个反应的自由能生成趋势图;
38.图2为100目、200目和300目的三种碳在1000℃与转炉烟气反应后烟气中co2含量和co含量的变化曲线图;
39.图3为100目、200目和300目的三种碳在1100℃与转炉烟气反应后烟气中co2含量和co含量的变化曲线图;
40.图4为100目、200目和300目的三种碳在1200℃与转炉烟气反应后烟气中co2含量和co含量的变化曲线图;
41.图5为100目、200目和300目的三种碳在1250℃与转炉烟气反应后烟气中co2含量和co含量的变化曲线图;
42.图6为一种实施例中本技术提供的可提升转炉煤气回收量的转炉汽化冷却烟道的结构示意简图,图中对转炉、转炉汽化冷却烟道、碳输送系统进行了示意,可用以体现提升转炉煤气回收量的过程原理。
43.附图标记说明:
44.1、转炉;2、转炉汽化冷却烟道;21、活动烟罩;22、炉口固定段烟道;23、中间段烟道;24、末端烟道;3、碳输送系统;31、储碳仓;32、气力输灰装置;33、智能定碳撬装设备;34、高速喷枪。
具体实施方式
45.以下结合附图,通过具体实施例对本技术作进一步详述。
46.在本技术的描述中:除非另有说明,“多个”的含义是两个或两个以上。本技术中的术语“第一”、“第二”、“第三”等旨在区别指代的对象,而不具有技术内涵方面的特别意义(例如,不应理解为对重要程度或次序等的强调)。“包括”、“包含”、“具有”等表述方式,同时还意味着“不限于”(某些单元、部件、材料、步骤等)。
47.本技术中所引用的如“上”、“下”、“左”、“右”、“中间”等的用语,通常是为了便于对照附图直观理解,而并非对实际产品中位置关系的绝对限定。在未脱离本技术揭示的技术构思的情况下,这些相对位置关系的改变,当亦视为本技术表述的范畴。
48.随着钢铁工业对节能与环保需求的日益加剧,“转炉煤气回收量”成为衡量一个冶金企业节能环保水平的重要指标。如何进行转炉煤气的极限回收和有效利用,对企业节能降耗、提高效益至关重要。吨钢回收量低、放散量大,既浪费了能源,又严重污染了环境。如何提高转炉煤气吨钢回收量,稳定地保持高水平的回收状态,解决供需不平衡等一系列矛盾,已成为需要迫切解决的难题。
49.为解决煤气回收量低和煤气回收品质不高、放散量大的问题。本技术从降低转炉烟气o2含量、降低co2含量、提高co含量方面着手,通过在转炉烟气中加入干熄焦除尘灰,以碳降碳,实现了增效、减排、利废的目的。
50.从工业分析的角度对比,干熄焦除尘灰的组成性质与无烟煤非常相似,都具有固定碳含量高、挥发分低及含硫量低等特点,用干熄焦除尘灰作为碳源即保证了转炉煤气回收量的提升,也降低了碳供给成本。
51.转炉煤气是转炉炼钢过程中的副产品,它是转炉炼钢过程中,铁水中的碳在高温
下和吹入的氧生成一氧化碳和少量二氧化碳的混合气体。转炉煤气的成分随冶炼过程而不断变化,其主要成分可见下表1:
52.表1转炉煤气主要成分及其含量占比
[0053][0054]
在转炉煤气中主要烟气成分为一氧化碳,为了达到转炉煤气回收的安全指标,必须保证转炉煤气温度和浓度不在着火点与爆炸极限浓度范围内,即需要降低转炉煤气中o2和co2的含量。
[0055]
实施例一
[0056]
在转炉烟气高温(1600℃~1800℃)、高粉尘(80~150g/nm3)、co含量高(0~80%)、周期性冶炼等极端条件下,为实现节能减排、提高煤气回收量和回收品质,本技术提出了一种全新的以碳降碳技术,即在转炉煤气回收前,利用烟道高温,通过干熄焦除尘灰反应掉转炉煤气中的o2和co2,快速降低转炉煤气中o2和co2的含量,保证转炉煤气温度和浓度不在着火点与爆炸极限浓度范围内;同时,反应生成的co也提高了煤气回收量。
[0057]
这种可提高转炉煤气回收量和热值,并降低转炉烟气二氧化碳排放量的方法,主要是向转炉汽化冷却烟道内通入干熄焦除尘灰,同时利用烟道高温,实现转炉煤气中二氧化碳和氧气分别与干熄焦除尘灰反应。这种方法在不改变转炉冶炼工艺的情况下,只对汽化冷却烟道稍作改动,即实现增加煤气回收量、提升煤气回收品质、降低碳排放的目标。转炉煤气中二氧化碳和氧气分别与干熄焦除尘灰反应后,生成目标回收的一氧化碳,提升了一氧化碳的含量,同时降低了二氧化碳和氧气的含量,即提升了转炉煤气的回收品质,提升了转炉煤气的回收量,同时降低了烟囱放散煤气量,降低了爆炸风险,减少了炼钢工序的碳排放量。
[0058]
烟道中干熄焦除尘灰与转炉煤气发生如下反应:
[0059]c(s)
+co
2(g)
=2co
(g)
ꢀꢀꢀꢀ
δ
r1gθ
=166550-171.00t
ꢀꢀꢀj·
mol-1
[0060]
2c
(s)
+o
2(g)
=2co
(g)
ꢀꢀꢀꢀ
δ
r2gθ
=-228800-171.54t
ꢀꢀj·
mol-1
[0061]c(s)
+o
2(g)
=co
2(g)
ꢀꢀꢀꢀꢀ
δ
r3gθ
=-395350-0.54t
ꢀꢀꢀꢀj·
mol-1
[0062]
2co
(g)
+o
2(g)
=2co
2(g)
ꢀꢀ
δ
r4gθ
=-561900-170.46t
ꢀꢀj·
mol-1
[0063]
由于干熄焦除尘灰与转炉煤气的反应是在转炉汽化冷却烟道内进行的,温度和气体成分都不是在标准状态下。因此,应该用实际条件下反应的吉布斯自由能变化(δg)来判断它们反应的情况,所依据的化学反应等温方程式如下:
[0064][0065]
由于反应在汽化烟道内进行,总压强可以近似为一个标准大气压,根据转炉烟气的成分,分别计算得到相应的吉布斯自由能变如下表2:
[0066]
表2干熄焦除尘灰与转炉煤气在烟道内进行的各个反应的反应吉布斯自由能变
[0067][0068]
各个反应在不同温度下对应的反应吉布斯自由能变的函数图像见图1,图1反映了不同温度下各个反应的自由能生成趋势,由图1可知,在转炉汽化烟道内900℃~1600℃的烟道内,c与co2的反应更加容易进行。
[0069]
发明人通过实验对碳源的粒径进行选择,具体过程如下:
[0070]
通过对100目(149μm)、200目(74μm)和300目(48μm)的三种碳为原料,在相同的条件下(等温1000℃、1100℃、1200℃和1250℃)与转炉烟气反应后烟气中co2含量和co含量的变化曲线见图2、3、4、5。
[0071]
由图2至图5可知,在转炉高温烟气中增加碳颗粒的粒径在200~300目之间时,反应效率较高。
[0072]
下面表3展示了多个企业在生产过程中排出的干熄焦除尘灰的组分:
[0073]
表3多个企业在生产过程中排出的干熄焦除尘灰的组分表
[0074][0075]
下面表4展示了除尘灰粒度分布比例情况:
[0076]
表4除尘灰粒度分布比例表
[0077][0078]
发明人在200~300目的粒径范围之间选择碳源时,发现干熄焦除尘灰的粒径恰好在该范围内,可利用干熄焦除尘灰作为碳源,完成对转炉煤气中的二氧化碳和氧气的反应,也实现了废物的二次利用,降低了碳成本。
[0079]
本实施例提供的方法主要通过向转炉汽化冷却烟道内通入干熄焦除尘灰,同时利
用烟道高温,实现转炉煤气中二氧化碳和氧气分别与干熄焦除尘灰反应,生成目标回收的一氧化碳,实现了对转炉煤气回收量和热值的提升,提高了转炉煤气的回收品质。
[0080]
实施例二
[0081]
基于上述实施例一提供的可提升转炉煤气回收量的方法,本技术实施例提供一种可提升转炉煤气回收量的转炉汽化冷却烟道。参见图6,图6转炉汽化冷却烟道进行了简单示意,对该转炉汽化冷却烟道2包括活动烟罩21、炉口固定段烟道22、中间段烟道23和末端烟道24;活动烟罩21位于转炉炉口上方,活动烟罩21的上部与炉口固定段烟道22的下部相连,炉口固定段烟道22的上部与中间段烟道23的下部通过密封伸缩连接装置相连,中间段烟道23的上部与末端烟道24相连。炉口固定段烟道、中间段烟道和末端烟道中,至少有一段烟道与碳输送系统3相连。碳输送系统向与其相连的烟道内喷射干熄焦除尘灰,进入转炉汽化冷却烟道的转炉煤气中的二氧化碳和氧气分别与干熄焦除尘灰反应生成一氧化碳。优选的,为了促进反应充分发生,碳输送系统将干熄焦除尘灰喷射在温度范围为900℃~1600℃的烟道内,使得干熄焦除尘灰与转炉煤气中的二氧化碳及氧气的反应温度在900℃~1600℃范围内。干熄焦除尘灰的喷射方向与转炉煤气在烟道内的流动方向一致,若干熄焦除尘灰的喷射方向与转炉煤气在烟道内的流动方向相反,则会影响转炉汽化冷却烟道内转炉烟气的冶炼排出。
[0082]
在一种实施例中,干熄焦除尘灰的粒径范围为100目~300目。优选的,干熄焦除尘灰的粒径范围为200目~300目,比如250目、270目等。本技术选用干熄焦除尘灰作为碳源既减少了碳成本,又处理了固废,实现了节能减排。
[0083]
在一种实施例中,与烟道相连的碳输送系统3可包括储碳仓31、气力输灰装置32、智能定碳撬装设备33、高速喷枪34和控制装置。其中:储碳仓31用以储存干熄焦除尘灰,气力输灰装置32用以实现将储碳仓31内的干熄焦除尘灰输送至智能定碳撬装设备33中。智能定碳撬装设备(规格型号可为bf-t120)包括定量粉末输送装置、气流输送装置、粉末分配装置、测温防堵装置以及检测装置;定量粉末输送装置自气力输灰装置接收干熄焦除尘灰,且将干熄焦除尘灰定量输送至粉末分配装置;粉末分配装置内设置有多个粉末输送通道,每个粉末输送通道的出口端与转炉汽化冷却烟道相连通;气流输送装置与粉末分配装置相适配,用以将各个粉末输送通道内的干熄焦除尘灰朝转炉汽化冷却烟道吹送。测温防堵装置用以对粉末输送通道内的温度进行实时测量以获得粉末输送通道的管道通畅状态,当粉末输送通道的有堵塞迹象时可利用管道吹灰装置进行清理。检测装置用以实现对转炉内的烟气流量、烟气成分及烟气温度的检测。控制装置用以接收检测装置测得的各项数据,且根据接收的数据调整定量粉末输送装置、气流输送装置、粉末分配装置的运行状态。粉末分配装置内的每个粉末输送通道的出口端设置有一个高速喷枪,高速喷枪将粉末输送通道内的干熄焦除尘灰喷射至转炉汽化冷却烟道中。
[0084]
本技术提供的可提升转炉煤气回收量的转炉汽化冷却烟道与碳输送系统相连,碳输送系统向与其相连的烟道内喷射干熄焦除尘灰,进入转炉汽化冷却烟道的转炉煤气中的二氧化碳和氧气分别与所述干熄焦除尘灰反应生成一氧化碳。
[0085]
现有技术中,转炉汽化冷却烟道将转炉煤气输送回收,转炉煤气中的二氧化碳和氧气含量较高,而氧气含量较高则导致了转炉煤气直接排放,浪费了能源,也增加了企业的碳排放,加剧温室效应。而本技术提供的转炉汽化冷却烟道与碳输送系统相连,使得转炉汽
化冷却烟道内的转炉煤气与干熄焦除尘灰在烟道高温环境下发生吸热反应,利用干熄焦除尘灰将转炉煤气中的二氧化碳和氧气反应为可回收利用的一氧化碳,同时降低了二氧化碳和氧气的含量,提升了转炉煤气对一氧化碳的回收量,即提升了转炉煤气的回收品质。再者,降低了氧气含量也降低了爆炸风险,且干熄焦除尘灰利用烟道高温环境完成反应,实现了对转炉煤气中热量的利用。
[0086]
本技术提供的可提升转炉煤气回收量的转炉汽化冷却烟道内,与转炉煤气中的二氧化碳和氧气分别发生反应的是干熄焦除尘灰,干熄焦除尘灰是焦化厂产生的焦化除尘废物,本技术使用干熄焦除尘灰作为碳源实现了废物的二次利用,降低了生产成本,实现了节能减排。
[0087]
实施例三
[0088]
基于实施例一提供的可提升转炉煤气回收量的方法,本技术实施例提供一种安装在转炉汽化冷却烟道上的转炉煤气回收前处理系统。转炉煤气回收前处理系统包括转炉汽化冷却烟道,以及安装在转炉汽化冷却烟道上的碳输送系统。碳输送系统将干熄焦除尘灰吹送至转炉汽化冷却烟道内,使得转炉煤气中的二氧化碳和氧气分别与干熄焦除尘灰在温度范围为900℃~1600℃的烟道内反应生成一氧化碳。
[0089]
在一种实施例中,碳输送系统包括储碳仓、气力输灰装置、智能定碳撬装设备、高速喷枪和控制装置。储碳仓用以储存干熄焦除尘灰,气力输灰装置用以实现将储碳仓内的干熄焦除尘灰输送至智能定碳撬装设备中。本实施例提供的碳输送系统与实施例二中记载的碳输送系统相同。
[0090]
本技术提供的转炉煤气回收前处理系统在投入使用时,可采用罐车将干熄焦除尘灰运送至储碳仓储存下来,通过气力输灰装置将灰粉输送至智能定碳撬装设备中,在智能定碳撬装设备内设置定量粉末输送装置、气流输送装置、粉末分配装置、测温防堵装置、检测仪器仪表等,通过与转炉冶炼状况、烟气流量、烟气成分、烟气温度等参数的连锁控制,使得干熄焦除尘灰高速喷入转炉汽化烟道,以提高转炉煤气的回收量和回收品质。
[0091]
现有的转炉煤气回收系统是将自转炉汽化冷却烟道内排出的转炉煤气依次送入一次除尘系统以及煤气柜中,一次除尘系统及煤气柜形成对转炉煤气的后处理回收系统,而转炉汽化冷却烟道内的转炉煤气中含有含量相对较高的二氧化碳和氧气,导致转炉煤气回收品质不高,二氧化碳排放量高,且氧气含量较高则存在一定的爆炸风险,导致将该部分煤气放散,增加了炼钢工序的碳排放量。而本技术提供的安装在转炉汽化冷却烟道上的转炉煤气回收前处理系统可在转炉煤气进入后处理回收系统前,先一步对转炉煤气进行处理,以提升转炉煤气的回收品质及回收量。具体的,本技术通过向转炉汽化冷却烟道内通入干熄焦除尘灰,同时利用烟道高温,实现转炉煤气中二氧化碳和氧气分别与干熄焦除尘灰反应,生成目标回收的一氧化碳,提升了一氧化碳的含量,同时降低了二氧化碳和氧气的含量,即提升了转炉煤气的回收品质,提升了转炉煤气的回收量,同时降低了烟囱放散煤气量,降低了爆炸风险,减少了炼钢工序的碳排放量。
[0092]
实施例四
[0093]
基于上述的可提升转炉煤气回收量的转炉汽化冷却烟道,本技术实施例提供一种可提升转炉煤气回收量的转炉,转炉的炉口上方设置有上述的转炉汽化冷却烟道,转炉汽化冷却烟道与碳输送系统相连,碳输送系统向转炉汽化冷却烟道内喷射干熄焦除尘灰,转
炉煤气中的二氧化碳和氧气分别与干熄焦除尘灰反应生成一氧化碳。该转炉的应用可提升转炉煤气回收量,提升转炉煤气的回收品质。
[0094]
本实施例提供的转炉可通过简单改造制得,改造过程不改变转炉冶炼工艺,只对汽化冷却烟道稍作改动,即在汽化冷却烟道上连接碳输送系统,通过碳输送系统向汽化冷却烟道喷射干熄焦除尘灰,如此便可实现增加煤气回收量、提升煤气回收品质、降低碳排放的目标。
[0095]
发明人通过计算得出,转炉煤气回收前在转炉汽化冷却烟道内施行以碳降碳技术,标况下,转炉煤气回收量可增加10%,煤气回收时间增加60s,煤气热值增加10%以上,每年减少碳排放10kg/吨钢,年处理固废(干熄焦除尘灰)2.5kg/吨钢,年效益5~8元/吨钢。
[0096]
本技术提供的可提升转炉煤气回收量的方法,以原有转炉为基础,不影响原转炉冶炼生产系统的正常运行,通过对原转炉的转炉汽化冷却烟道的改造实现了转炉煤气回收量的提升,降低工程造价和运行成本。
[0097]
以上实施例的各技术特征可以进行任意的组合(只要这些技术特征的组合不存在矛盾),为使描述简洁,未对上述实施例中的各个技术特征所有可能的组合都进行描述;这些未明确写出的实施例,也都应当认为是本说明书记载的范围。
[0098]
上文中通过一般性说明及具体实施例对本技术作了较为具体和详细的描述。应当理解,基于本技术的技术构思,还可以对这些具体实施例作出若干常规的调整或进一步的创新;但只要未脱离本技术的技术构思,这些常规的调整或进一步的创新得到的技术方案也同样落入本技术的权利要求保护范围。