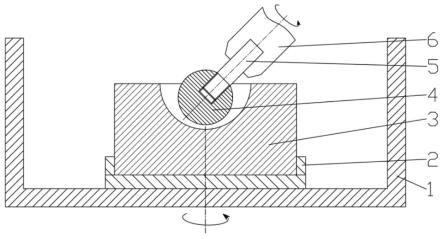
1.本发明主要涉及超精密修形加工技术领域,尤其涉及基于磁场增强力流变的微槽网络结构球头修形装置及方法。
背景技术:2.具有超光滑表面、高面型精度和低/无亚表面损伤的小口径非球面零件对光电通讯、国防、生物医用和航空航天等产业的高速发展起着至关重要的作用。小口径非球面零件需要经过超精密抛光加工过程,才能满足行业对其亚微米级的形状精度、纳米级的表面粗糙度和极小的亚表面损伤精度的加工要求。现有较为成熟的超精密确定性抛光技术包括单点金刚石车削、砂轮超精密磨削、气囊抛光、磁流变抛光、气囊-剪切增稠协同抛光以及化学-剪切增稠协同抛光等。单点金刚石车削和砂轮超精密磨削虽然可以实现曲面工件的高面型精度和高加工效率等要求,但工件表面不仅会残留有规则的磨痕,而且不可避免地产生晶格错位、裂纹、残余应力、加工硬化以及崩边等各种加工缺陷;气囊抛光具有高抛光效率、曲面形状自适应性等优点,同时也产生抛光形貌难以预测、抛光工具易损坏、亚表面损伤以及设备精度要求高等问题;磁流变抛光虽然具有去除函数稳定、无亚表面损伤以及无磨头损坏等优势,但现有的抛光液成本高昂、沉降性差,抛光系统复杂且制造成本过高,无法加工小口径凹面工件,上述问题成为了限制其实际工业应用的关键因素;气囊-剪切增稠抛光利用非牛顿流体抛光液使抛光工具在加工过程中产生动态变形,实现材料去除深度的自我调节,抛光液具有环境友好性,同时也存在抛光形貌难以预测、对陶瓷材料的加工效率低等技术难点;化学-剪切增稠协同抛光可以实现曲面工件的确定性抛光,具有抛光形状可控性、高表面精度等优点,但存在抛光液具有环境污染性、加工效率低等问题。可见,现有技术均具有较大的局限性,因此,亟需一种能够实现小口径非球面零件的高效、高精度、低损伤和低成本的修形装置及方法。
技术实现要素:3.本发明要解决的技术问题是克服现有技术的不足,提供基于磁场增强力流变的微槽网络结构球头修形装置及方法。
4.为解决上述技术问题,本发明采用以下技术方案:
5.基于磁场增强力流变的微槽网络结构球头修形装置,包括盛装有抛光液的抛光槽,所述抛光槽内设有治具,工件经所述治具固定在抛光槽内并被抛光液浸没;所述修形装置还包括位于抛光槽内、工件上方的磁性抛光球头,所述球头经杆件与驱动装置相连;所述球头为永磁铁材质,所述抛光槽、治具和杆件均由非导磁材料制成。
6.所述抛光液设置成掺有质量分数为3%-12%的羰基铁粉颗粒、10%-28%的磨粒和0.5%-5%的聚乙二醇的淀粉溶液;所述淀粉溶液由淀粉颗粒和去离子水按照1:1的质量分数混合并经机械搅拌制成。
7.所述球头表面成型有网格槽,所述网格槽的宽度与深度比为1:2。
8.所述球头表面镀膜。
9.所述球头表面磁场强度为50-250mt、工件表面磁感应强度为10-150mt。
10.然后,本发明公开了基于磁场增强力流变的微槽网络结构球头修形方法,所述修形方法应用于上述的修形装置,并包括以下步骤:
11.步骤s1,利用治具固定工件;
12.步骤s2,将球头的球心设置于工件的回转中心线上,并调整杆件相对于工件凹面的切平面倾斜,且球头与工件间在凹面不同位置上形成相同间隙;
13.步骤s3,制备抛光液,并将抛光液倾倒入抛光槽至浸没工件;
14.步骤s4,驱动装置根据驻留时间参数和抛光路径参数经杆件驱动球头进给加工。
15.所述步骤s3包括:
16.步骤s31,在常温条件下,将淀粉颗粒与去离子水按照质量分数1:1混合,并进行机械搅拌,得到剪切增稠液;
17.步骤s32,在剪切增稠液中掺入质量分数为3%-12%的羰基铁粉颗粒、10%-28%的磨粒和0.5%-5%的聚乙二醇,并对混合液进行搅拌和超声分散,直至均匀。
18.所述步骤s4包括:
19.步骤s41,利用pgi轮廓仪测量工件的面形误差,并据此计算获得驻留时间参数;
20.步骤s42,根据工件的凹面几何模型生成螺旋线抛光路径参数;
21.步骤s43,将驻留时间参数和抛光路径参数导入驱动装置。
22.球头沿回转工件曲面的子午线向边缘位置进给加工。
23.球头与工件间的间隙为0.1-0.8mm、球头转速范围为100-5000rpm。
24.与现有技术相比,本发明的优点在于:
25.通过安装的抛光槽,能够用于盛装抛光液,抛光液中含有羟基铁粉的磨粒,当球头开始旋转时,促使抛光间隙中的抛光介质产生局部增稠及固化等流变效应,在流动压效应作用下,含有磨粒的“粒子簇”微切削工件表面,造成工件表面材料去除,进而实现修形。
附图说明
26.图1是修形装置的结构示意图;
27.图2是球头和杆件的结构示意图;
28.图3是球头的磁场分布示意图;
29.图4是工件抛光前后对比示意图;
30.图5是修形方法的流程示意图。
31.图中各标号表示:1、抛光槽;2、治具;3、工件;4、球头;41、网格槽;5、杆件;6、驱动装置。
具体实施方式
32.以下将结合说明书附图和具体实施例对本发明做进一步详细说明。
33.如图1至图4所示,本实施例中,基于磁场增强力流变的微槽网络结构球头修形装置包括盛装有抛光液的抛光槽1,抛光槽1内设有治具2,工件3经治具2固定在抛光槽1内并被抛光液浸没;修形装置还包括位于抛光槽1内、工件3上方的磁性抛光球头4,球头4经杆件
5与驱动装置6相连;球头4为永磁铁材质,抛光槽1、治具2和杆件5均由非导磁材料不锈钢制成。基于磁场力和高剪切应力的耦合作用,促使抛光间隙中的抛光介质产生局部增稠及固化等流变效应,其中磁场增强了增稠效应,同时在楔形区域流体的流动压效应作用下,含有磨粒的“粒子簇”划擦及微切削工件3表面,造成工件3表面材料去除、实现修形。通过安装的抛光槽1,盛装抛光液含有羟基铁粉和磨粒,抛光过程中球头4发生旋转,在磁场力和高剪切应力作用下,促使工件3表面与球头4之间的抛光液产生局部增稠、固化等流变效应,并在楔形区域产生流动压效应,抛光液中的“粒子簇”划擦及微切削工件3表面,造成工件3表面材料去除,从而能够实现修形。工件3为小口径回转非球面硬脆陶瓷模具,其属于光学元件模具中的一种,是非导磁难加工材料,不会因磁场影响而被磁化,故其表面不会因磁场作用而吸附抛光液中的羰基铁粉颗粒。球头4为永磁铁材质,抛光槽1、治具2和杆件5可由不锈钢制成,非导磁材料能够避免对抛光区域的磁场大小和均匀性产生影响,从而使得抛光液中的各组分均匀分布,确保流变性能稳定。其中,球头4为钕铁硼永磁铁而非电磁铁,从而不会因产生大热量而使抛光液的流变特性发生改变,保证了材料去除的稳定性,且无安全隐患。相对于现有技术,本发明公开的修形装置结构简单、使用寿命长、定位精度高,且安装拆卸方便,结合修形需求,可以改变加工参数,实现可控性与自适应性。同时,由于采用柔性方式对小口径回转非球面工件的面型修正,实现对其表面的无/低损伤和高精度的抛光。在修形过程中也不会因产生大热量而使抛光液的流变特性发生改变,保证了材料去除的稳定性,且无安全隐患。
34.本实施例中,抛光液设置成掺有质量分数为3%-12%的羰基铁粉颗粒、10%-28%的磨粒和0.5%-5%的聚乙二醇的淀粉溶液;淀粉溶液由淀粉颗粒和去离子水按照1:1的质量分数混合并经机械搅拌制成。聚乙二醇具有水溶性和分散性,不但可以抑制颗粒过度团聚,还能与磨粒等粒子形成微米级的水团簇,使得磨粒更加均匀地分布在抛光液中。
35.本实施例中,球头4表面成型有网格槽41,网格槽41的宽度与深度比为1:2。通过在球头4表面设置网格槽41,不仅可以产生“尖峰效应”从而增强球头4表面的磁感应强度、促使抛光液在网格槽41上形成一系列柔性小磨头,在高速抛光下几乎不会产生离心和滑水效应,从而能够大幅提升材料去除能力;同时,还能增强抛光液与球头4表面的摩擦力,从而降低了球头4高速旋转时的离心作用,进一步提升了材料去除率。具体地,网格槽41布置在球头4跟工件3曲面相切的周边外侧,由于尖峰效应导致外侧磁场强度增加,这样可补偿外侧因流动压力低导致的材料去除力小,使材料去除轮廓由水滴形变为椭圆,减少了工件3表面抛光后的残余高度,使得工件3表面材料均匀化去除,同时可提高抛光质量和抛光效率。
36.本实施例中,球头4表面镀膜。球头4表面磁场强度为50-250mt、工件3表面磁感应强度为10-150mt。通过在球头4表面进行镀膜处理,可以保证球头4不被氧化,从而延长了使用寿命。沿杆件5长度方向对球头4充磁,使得其表面磁场强度为50-250mt,在球头4的磁场范围内,工件3表面磁感应强度为10-150mt。工件3表面一直处于弱磁感应强度条件下,在该磁场环境下,抛光液不仅具有较强的剪切应力,且保持有良好的流动特性进行流动循环。具体地,球头直径为φ5mm,工件选用口径φ10mm的碳化硅模具。网格槽41由激光扫描烧蚀形成,呈迷宫纹理,且槽深由外到内依次增大。
37.具体地,球头直径为φ5mm,工件选用口径φ10mm的碳化硅模具。网格槽41由激光扫描烧蚀形成,呈迷宫纹理,且槽深由外到内依次增大。
38.如图5所示,本发明还公开了基于磁场增强力流变的微槽网络结构球头修形方法,在其一实施例中,修形方法应用于上述的修形装置,并包括以下步骤:
39.步骤s1,利用治具2固定工件3;
40.步骤s2,将球头4的球心设置于工件3的回转中心线上,并调整杆件5相对于工件3凹面的切平面倾斜,且球头4与工件3间在凹面不同位置上形成相同间隙;
41.步骤s3,制备抛光液,并将抛光液倾倒入抛光槽1至浸没工件3;
42.步骤s4,驱动装置6根据驻留时间参数和抛光路径参数经杆件5驱动球头进给加工。
43.其中,使用ccd工业相机观察并且定位球头4的球心位置,使其处于工件3的回转中心线上。
44.步骤s3具体包括:
45.步骤s31,在常温条件下,将淀粉颗粒与去离子水按照质量分数1:1混合,并进行机械搅拌,得到剪切增稠液;
46.步骤s32,在剪切增稠液中掺入质量分数为5%的羰基铁粉颗粒、12%的磨粒和2%的聚乙二醇,并对混合液进行搅拌和超声分散,直至均匀。
47.步骤s4具体包括:
48.步骤s41,利用pgi轮廓仪测量工件3的面形误差,并据此计算获得驻留时间参数;
49.步骤s42,根据工件3的凹面几何模型生成螺旋线抛光路径参数;
50.步骤s43,将驻留时间参数和抛光路径参数导入驱动装置6。
51.本实施例中,球头4沿回转工件3曲面的子午线向边缘位置进给加工。
52.本实施例中,球头4与工件3间的间隙为0.1mm、球头4转速设置成3000rpm。
53.虽然本发明已以较佳实施例揭示如上,然而并非用以限定本发明。任何熟悉本领域的技术人员,在不脱离本发明技术方案范围的情况下,都可利用上述揭示的技术内容对本发明技术方案做出许多可能的变动和修饰,或修改为等同变化的等效实施例。因此,凡是未脱离本发明技术方案的内容,依据本发明技术实质对以上实施例所做的任何简单修改、等同变化及修饰,均应落在本发明技术方案保护的范围内。