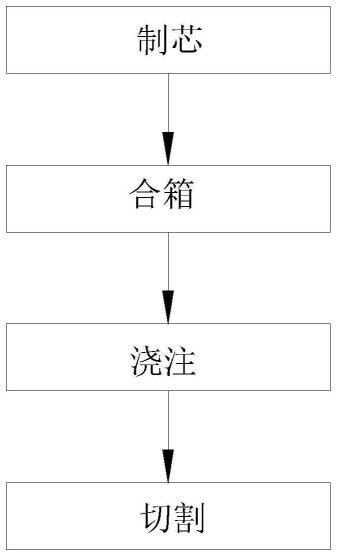
1.本发明涉及铸造技术领域,尤其是指一种涡轮壳体的冷芯壳型铸造工艺。
背景技术:2.随着国家对环保的日益重视,从2014年开始对小型汽车逐步采用国
ⅴ
排放标准,对汽车发动机的性能要求也越来越高,以达到提高动力、减少有害气体排放的目的。汽车燃油燃烧越充分,尾气的排放温度就会越高,对涡轮增压器壳体的耐高温性能也就提出了更高的要求。目前欧洲实施的欧
ⅴ
排放标准及国内实施的国
ⅴ
排放标准的发动机尾气排放温度已经到了950℃到1050℃。
3.随着尾气排放温度的提高,为了适应950℃-1100℃的尾气排放温度,增压器涡轮壳体的材质普遍采用的都是1.4848 、1.4837和1.4826耐热不锈钢材料。为了获得外形完整内部组织致密的铸件,这些材质的涡轮壳体的浇铸温度一般要达到1550℃以上,特殊情况下可以达到1600℃以上。
4.耐热不锈钢材质涡轮壳体目前大多采用冷芯壳型铸造工艺,采用冷芯壳型工艺具有生产效率高、能耗低、劳动条件好等优点,冷芯壳型生产可以和辊道运输设备、机械手转运设备、浇铸设备等组线生产,大大降低对生产面积的要求。冷芯壳型使用的原砂大多采用铸造业广泛采用的石英砂(sio2),铸造用石英砂的耐火温度普遍大约在1500℃,低于耐热不锈钢的浇铸温度1550℃以上。在生产中钢液和砂模中的石英砂、树脂、固化剂会发生物理及化学反应,在砂型内部产生很强的气压,钢水会借助这股压力从砂模之间的间隙中钻出。从而形成铸件批缝,甚至跑火。业界通常的解决办法在壳型砂模防火墙上抹上耐火粘接剂,但粘接剂富有黏性、砂模之间存在摩擦力,机械手在合模过程中并不能很好的将粘接剂压平,且不能确保砂模上下模之间的间隙达到不大于0.5mm的要求。
技术实现要素:5.为此,本发明所要解决的技术问题在于克服现有技术中涡轮壳体的冷芯壳型铸造过程中利用机械手合模不严导致的浇注跑火、铸件批缝过大的问题。
6.为解决上述技术问题,本发明提供一种涡轮壳体的冷芯壳型铸造工艺,所使用的铸造砂型结构包括上砂型以及与上砂型配合的下砂型,所述上砂型设有出气孔以及用于注入铁水的直浇道;所述工艺包括如下步骤:s1:制芯:制作第一砂芯:用覆膜砂作为制芯材料,采用热芯盒制芯,将热芯盒温度加热到220-240℃,并将热芯盒安装于射芯机上,通过射芯机的射砂口向芯盒内射砂7-8秒,结壳固化后倒去热芯盒的砂芯内腔没有固化的覆膜砂,得到第一砂芯;制作第二砂芯:将芯盒安装于射芯机上,喷涂脱模剂,将烘干砂和树脂a、b进行加热混合搅拌,温度为30-60℃,催化下成型,得到第二砂芯;s2:合箱:将下砂箱放置于托盘上,将第一砂芯和第二砂芯放置于下砂箱的下砂型
位置,通过机器人将铸件上砂箱合到下砂箱上,得到完整的砂型,托盘将砂型周转至压紧气缸正下方,到位后光电传感器给压紧气缸信号,压紧气缸开始工作,压紧气缸驱动压板垂直下压作用于上砂箱上,使得上砂箱和下砂箱之间的间隙小于等于0.5mm;s3:浇注:浇注钢水温度控制在1450-1500℃之间,同时抽负压-0.03至-0.02mpa,浇注的钢水冷却≥75min后,进行开箱、清理并取出铸件;s4:切割:切割铸件的浇注系统和冒口,对铸件进行抛瓦及打磨处理。
7.在本发明的一种实施方式中,步骤s1中,覆膜砂中掺杂有铬铁矿砂。
8.在本发明的一种实施方式中,步骤s1中,树脂a为液态酚醛树脂,树脂b为液态聚异氰酸酯树脂。
9.在本发明的一种实施方式中,步骤s1中,制作第一砂芯时,射砂压力为6-7.5bar,固化时间为190-200s。
10.在本发明的一种实施方式中,步骤s1中,制作第二砂芯时,吹入三乙胺气体30-40ml,三乙胺气体温度为110-130℃。
11.在本发明的一种实施方式中,步骤s2中,所述托盘放置于输送线上,所述压紧气缸设于输送线正上方,所述压板连接于压紧气缸的驱动端,所述压紧气缸正下方的输送线上设有光电传感器。
12.在本发明的一种实施方式中,步骤s2中,所述光电传感器检测到托盘时,所述输送线停止运行。
13.在本发明的一种实施方式中,步骤s2中,合箱完成后,所述托盘经过所述烘箱对砂型进行加热。
14.在本发明的一种实施方式中,所述对砂型进行加热的温度为110-130℃。
15.在本发明的一种实施方式中,步骤s3中,所述浇注时间为3-4s。
16.本发明的上述技术方案相比现有技术具有以下优点:本发明所述的一种涡轮壳体的冷芯壳型铸造工艺,解决了现有技术中涡轮壳体的冷芯壳型铸造过程中利用机械手合模不严导致的浇注跑火、铸件批缝过大的问题,将现有生产线增加一个断点,加入自动压紧气缸,利托盘将砂型周转至压紧装置正下方,到位后光电传感器给压紧气缸一个信号,压紧气缸开始工作。压板垂直下压作用于上砂箱上,使其砂模上下模之间的间隙≤0.5mm,压紧气缸的作用力大小由气压表控制,保证压紧气缸在工作时达到砂型间隙≤0.5mm的同时不压坏砂型。
附图说明
17.为了使本发明的内容更容易被清楚的理解,下面根据本发明的具体实施例并结合附图,对本发明作进一步详细的说明,其中图1是本发明的涡轮壳体的冷芯壳型铸造工艺流程图。
18.图2是本发明的合箱时的布置示意图。
19.说明书附图标记说明:1、压紧气缸;2、烘箱;3、压紧板;4、砂模;5、托盘。
具体实施方式
20.下面结合附图和具体实施例对本发明作进一步说明,以使本领域的技术人员可以
更好地理解本发明并能予以实施,但所举实施例不作为对本发明的限定。
21.参照图1所示,本发明的一种涡轮壳体的冷芯壳型铸造工艺,所使用的铸造砂型结构包括上砂型以及与上砂型配合的下砂型,所述上砂型设有出气孔以及用于注入铁水的直浇道;所述工艺包括如下步骤:s1:制芯:制作第一砂芯:用覆膜砂作为制芯材料,其中覆膜砂中掺杂有铬铁矿砂,采用热芯盒制芯,将热芯盒温度加热到220-240℃,并将热芯盒安装于射芯机上,通过射芯机的射砂口向芯盒内射砂7-8秒,射砂压力为6-7.5bar,固化时间为190-200s,结壳固化后倒去热芯盒的砂芯内腔没有固化的覆膜砂,得到第一砂芯;制作第二砂芯:将芯盒安装于射芯机上,喷涂脱模剂,将烘干砂和树脂a、b进行加热混合搅拌,温度为30-60℃,催化下成型,得到第二砂芯;其中,树脂a为液态酚醛树脂,树脂b为液态聚异氰酸酯树脂。
22.s2:合箱:如图2所示,将下砂箱放置于托盘5上,将第一砂芯和第二砂芯放置于下砂箱的下砂型位置,通过机器人将铸件上砂箱合到下砂箱上,得到完整的砂型(砂模4),托盘5将砂型周转至压紧气缸1正下方,到位后光电传感器给压紧气缸1信号,压紧气缸1开始工作,压紧气缸1驱动压板垂直下压作用于上砂箱上,使得上砂箱和下砂箱之间的间隙小于等于0.5mm;s3:浇注:浇注钢水温度控制在1450-1500℃之间,同时抽负压-0.03至-0.02mpa,浇注时间为3-4s,浇注的钢水冷却≥75min后,进行开箱、清理并取出铸件;s4:切割:切割铸件的浇注系统和冒口,对铸件进行抛瓦及打磨处理。
23.具体地,步骤s1中,制作第二砂芯时,吹入三乙胺气体30-40ml,三乙胺气体温度为110-130℃。
24.具体地,步骤s2中,所述托盘5放置于输送线上,所述压紧气缸1设于输送线正上方,所述压板连接于压紧气缸1的驱动端,所述压紧气缸1正下方的输送线上设有光电传感器。
25.具体地,步骤s2中,所述光电传感器检测到托盘5时,所述输送线停止运行。
26.本发明通过将现有生产线增加一个断点,加入自动压紧气缸1,利托盘5将砂型周转至压紧装置正下方,到位后光电传感器给压紧气缸1一个信号,压紧气缸1开始工作。压板垂直下压作用于上砂箱上,使其砂模4上下模之间的间隙≤0.5mm。压紧气缸1的作用力大小由气压表控制,保证压紧气缸1在工作时达到砂型间隙≤0.5mm的同时不压坏砂型,压紧气缸1结束工作后,托盘5继续往烘箱2内周转,采用气缸压紧的方式适配任意厚度的砂模4,无需产品切换时调整压紧行程。在其他实施例中,为了将自动压紧气缸1加入到现有生产线中,首先需要将现有生产线的烘箱2区加热区位置加热组件拆除,以便安装自动压紧气缸1。
27.具体地,步骤s2中,合箱完成后,所述托盘5经过所述烘箱2对砂型进行加热,所述对砂型进行加热的温度为110-130℃。
28.最后所应说明的是,以上具体实施方式仅用以说明本发明的技术方案而非限制,尽管参照实例对本发明进行了详细说明,本领域的普通技术人员应当理解,可以对本发明的技术方案进行修改或者等同替换,而不脱离本发明技术方案的精神和范围,其均应涵盖在本发明的权利要求范围当中。