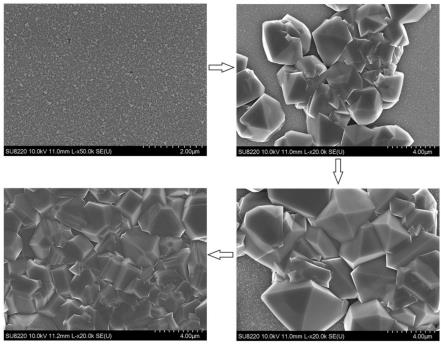
1.本技术涉及光电领域,主要涉及一种复合金刚石保护膜及其制备方法和芯片基材。
背景技术:2.随着激光能量及应用发展扩大,激光对电子元器件损伤的影响越来越大。电子元件感光芯片通常需要接收外界光线才能成像工作,这使得这类感光芯片对激光非常敏感,极易导致传感器破坏,如果感光芯片为电荷耦合器件(ccd)工作模式,则只需要小光斑的强激光就会导致感光芯片损伤,并显著影响成像效果或导致不能成像。即便是感光芯片为互补金属氧化物半导体(cmos)工作模式,也同样会因为强激光导致感光芯片发生损伤,导致成像出现故障。感光芯片通常是无人飞机、航天器、无人汽车等设备的“视网膜”,一旦发生损伤危害性大,且维修更换难度高。感光元件通常在激光能量达到0.1j/cm2(1064nm,8ns)量级便会出现成像异常,激光能量达到0.5j/cm2(1064nm,8ns)就会发生不可逆的硬损伤。
3.通常保护硅基芯片免受激光损伤的方法为添加中灰度(nd)滤镜、偏振滤镜或采用特殊波段截止滤镜,但是这些方法都存在抗激光损伤阈值低、较大局限性或对成像存在较大影响等问题。
4.因此,现有技术还有待于改进和发展。
技术实现要素:5.鉴于上述现有技术的不足,本技术的目的在于提供一种复合金刚石保护膜及其制备方法和芯片基材,所述复合金刚石保护膜为具有高激光损伤阈值的保护膜,可以提升芯片基材及其芯片元件的抗激光损伤阈值,旨在解决现有感光芯片的抗激光损伤阈值低的问题。
6.本技术的技术方案如下:一种复合金刚石保护膜的制备方法,其中,包括以下步骤:(1)将基材放置于金刚石纳米粉的无水乙醇悬浊液中进行超声处理,再用无水乙醇超声清洗;(2)将处理后的所述基材放置在微波等离子体化学气相沉积系统的样品台上,通入氢气和氩气,对所述基材表面进行等离子体清洗;(3)停止通入氩气,通入甲烷气体,在所述基材表面生长金刚石过渡层;(4)降低甲烷气体流量,生长高致密度的纳米晶金刚石层;(5)升高甲烷气体流量,生长高取向(100)微米晶金刚石层;(6)停止通入甲烷,通入氩气,对所述基材表面进行等离子体清洗;(7)停止通入氩气,降低氢气流量、气压、微波功率,降温速率低于每秒钟1℃,破真空后取出具有所述复合金刚石保护膜的所述基材。
7.本技术所提供的复合金刚石保护膜的制备方法,所述复合金刚石保护膜为具有高
激光损伤阈值的保护膜,可以提升芯片基材及其芯片元件的抗激光损伤阈值。
8.所述的复合金刚石保护膜的制备方法,其中,步骤(1)中,所述金刚石纳米粉选用粒径20~100nm金刚石粉;所述金刚石纳米粉的无水乙醇悬浊液中,所述金刚石纳米粉的浓度为5g/l~20g/l。
9.将基材浸泡此金刚石纳米粉的无水乙醇悬浊液的作用是利用液体在超声下的空化效应,在超声作用下,空蚀产生微小气泡,金刚石纳米粉可对基材进行空蚀作用,使得基材表面可以附着金刚石纳米粉,为后续形核生长提供形核位点,提高生长速度和生长质量。
10.所述的复合金刚石保护膜的制备方法,其中,步骤(1)中,所述超声处理和所述超声清洗的过程中,超声频率为35~60khz,超声时间10~20分钟。
11.所述的复合金刚石保护膜的制备方法,其中,步骤(2)中,所述通入氢气和氩气,对所述基材表面进行等离子体清洗包括以下步骤:通入氢气,氢气流量为30~120sccm,气压为2~6torr,起辉;增加氢气流量至80~500sccm,气压为10~100torr,微波功率为1~10kw,升温至750~900℃;通入占氢气流量3~10%的氩气,对所述基材表面进行等离子体清洗 15~30分钟;所述氢气和所述氩气的纯度不低于7n。
12.所述的复合金刚石保护膜的制备方法,其中,步骤(3)中,所述甲烷气体的通入比例为占所述氢气流量的6%~10%,气压为70~120 torr,所述基材表面温度为750~850℃,所述生长的时间为10~30分钟;所述甲烷气体的纯度不低于6n。
13.所述的复合金刚石保护膜的制备方法,其中,步骤(4)中,所述降低甲烷气体流量,生长高致密度的纳米晶金刚石层包括以下步骤:保持所述氢气流量不变,所述甲烷气体占比从6%~10%随时间线性降低到0.5%~1%,变化时间为5~15分钟;维持所述甲烷气体占比在0.5%~1%,生长所述高致密度的纳米晶金刚石层,生长时间为30~60分钟。
14.所述的复合金刚石保护膜的制备方法,其中,步骤(5)中,所述升高甲烷气体流量,生长高取向(100)微米晶金刚石层包括以下步骤:保持氢气流量不变,所述甲烷气体占比从0.5%~1%随时间线性升高到3%~5%,变化时间为5~15分钟;维持所述甲烷气体占比在3%~5%,生长所述高取向(100)微米晶金刚石层,生长时间为4~10小时。
15.所述的复合金刚石保护膜的制备方法,其中,步骤(6)中,所述氩气的通入量为占所述氢气流量的3~10%,所述等离子体清洗时间为30~60分钟;步骤(7)之后,还包括以下步骤:在高倍率显微镜下观察所述复合金刚石保护膜是否均匀且完全覆盖在所述基材上,若未达到100%覆盖,则重新进行步骤(2)~(7)。
16.一种复合金刚石保护膜,其中,采用如上任一项所述的复合金刚石保护膜的制备方法制备得到。
17.一种芯片基材,其中,所述芯片基材为采用如上任一项所述的复合金刚石保护膜的制备方法制备得到的具有所述复合金刚石保护膜的芯片基材。
18.有益效果:本技术所提供的复合金刚石保护膜及其制备方法和芯片基材,所述复
合金刚石保护膜为具有高激光损伤阈值的保护膜,可以提升芯片基材及其芯片元件的抗激光损伤阈值,所述复合金刚石保护膜适用于对硅等基材进行抗激光防护,提升硅等基材的抗激光损伤阈值。采用微波等离子体化学气相沉积法,在真空环境下生长低缺陷密度的纳米晶、微米晶复合金刚石,可以完全覆盖在基材表面同时提供高激光防护性能,同时可提升硅材料的抗强酸、强碱及力学、散热等特性。复合金刚石保护膜生长速率快,成本低,所用原材料对大气无污染,尾气易处理。本技术不仅适用于硅材料的激光防护,也可用于金属、陶瓷、玻璃、晶体等材料的激光防护。
附图说明
19.图1为本技术实施例1中复合金刚石保护膜的制备过程中不同生长阶段高分辨形貌图。
20.图2为本技术实施例1中复合金刚石保护膜的拉曼测试光谱图。
21.图3为本技术中所采用的激光光斑的三维图。
22.图4为本技术中所采用的激光光斑的二维图。
23.图5为本技术实施例1和对照例各样品的激光损伤形貌图。
具体实施方式
24.本技术提供一种复合金刚石保护膜及其制备方法和芯片基材,为使本技术的目的、技术方案及效果更加清楚、明确,以下对本技术进一步详细说明。应当理解,此处所描述的具体实施例仅用以解释本技术,并不用于限定本技术。
25.金刚石薄膜作为保护膜从uv-c(225nm)波段到远红外到微波波段均具有良好的透过率,同时导热系数高,电绝缘性好。在硅基材料上可通过多种方法沉积金刚石薄膜,经过实验对比不同沉积方法和效果,发现微波等离子体化学气相沉积方法制备的金刚石薄膜对硅基材料的保护性最好,可应用到感光芯片保护、显示元件保护等,提升芯片和元件的激光损伤阈值,避免被激光损伤破坏。
26.综上,使用微波等离子体化学气相沉积法制备金刚石保护膜,方法简单可靠,使用的原材料为甲烷和氢气等对环境没有污染,尾气易处理,生长速度快,最大可制备直径3英寸以上的金刚石保护膜,金刚石质量高,非金刚石相含量低,制备的金刚石保护膜对硅基材料的损伤阈值有较大的提升,可应用于硅基感光芯片(ccd、cmos)及显示器等,在军事、工业、消费等有较大的应用前景。
27.具体地,本技术提供一种复合金刚石保护膜的制备方法,适用于光电领域,包括以下步骤:(1)将基材放置于金刚石纳米粉的无水乙醇悬浊液中进行超声处理,再用无水乙醇进行超声清洗。
28.在本技术实施例方案中,基材为硅片。当保护对象为金属、陶瓷、玻璃、晶体等材料时,基材也可以为金属、陶瓷、玻璃、晶体。
29.在此步骤(1)中,金刚石纳米粉选用粒径为20~100nm的金刚石粉,若金刚石粉粒径过大会导致分布不均匀,同时增加硅片表面的粗糙度。金刚石纳米粉的无水乙醇悬浊液中,金刚石纳米粉的浓度为5g/l~20 g/l,采用此浓度可保证金刚石纳米粉的无水乙醇悬浊液
不会因为金刚石纳米粉含量太低而导致与基材作用不够,也可以避免浓度太高导致金刚石纳米粉团聚沉降,导致作用效果下降。将基材浸泡此金刚石纳米粉的无水乙醇悬浊液的作用是利用液体在超声下的空化效应,在超声作用下,空蚀产生微小气泡,金刚石纳米粉可对基材进行空蚀作用,使得基材表面可以附着金刚石纳米粉,为后续形核生长提供形核位点,提高生长速度和生长质量。
30.在此步骤(1)中,超声处理和超声清洗的过程中,超声频率可以为35~60khz,超声时间可以10~20分钟,超声频率不宜过低或过高,过低会导致作用力度大从而增加硅片表面粗糙度,频率过高会导致作用力度太低,导致金刚石纳米粉无法与硅片充分作用。
31.(2)将处理后的基材放置在微波等离子体化学气相沉积系统的样品台上,通入氢气用于起辉和升温,然后通入占氢气流量3~10%的氩气,对基材表面进行等离子体清洗。
32.在此步骤(2)中,样品台表面需要保证均匀无大尺寸颗粒物、无翘曲,避免与硅片接触不均匀导致升温中硅片发生翘曲或炸裂。通入的氢气、氩气的纯度不低于7n。
33.在此步骤(2)中,等离子体清洗的过程可以为15~30分钟。等离子体清洗可以对基材表面进行刻蚀,尤其是缺陷,可以降低基材表面附着的颗粒物污染等。
34.在此步骤(2)中,起辉时,氢气流量为30~120sccm,气压为2~6torr;升温时,氢气流量为80~500sccm,气压为10~100torr,微波功率为1~10kw,升温至750~900℃。
35.(3)保持氢气流量不变,停止通入氩气,通入占氢气流量6~10%的甲烷气体,气压为70~120 torr,基材表面温度为750~850℃,在基材表面生长金刚石过渡层,生长时间为10~30分钟。
36.在此步骤(3)中,甲烷气体的纯度不低于6n。
37.在此步骤(3)中,金刚石过渡层为晶粒较小(晶粒尺寸为10~80nm)的纳米晶金刚石薄膜,作用为形核层,覆盖基材表面,实现全表面覆盖,厚度一般为10~80nm。
38.(4)保持氢气流量不变,甲烷气体占比从6%~10%随时间线性降低到0.5%~1%,变化时间为5~15分钟,维持甲烷气体占比在0.5%~1%(占氢气流量0.5%~1%),生长高致密度的纳米晶金刚石层,生长时间为30~60分钟。
39.在此步骤(4)中,高致密度的纳米晶金刚石层,从表面形貌看没有明显空隙(50000倍),从截面形貌看无明显缝隙(50000倍)。高致密度的纳米晶金刚石层可以实现致密均匀的覆盖基材,形成致密覆盖,对光的散射作用小,其中,高致密度的纳米晶金刚石层的厚度为0.5~5微米,金刚石的粒径范围为50~300nm。在本技术实施例方案中,高致密度的纳米晶金刚石层的生长形貌,可参考图1的第一幅图。
40.(5)保持氢气流量不变,甲烷气体占比从0.5%~1%随时间线性升高至3%~5%,变化时间为5~15分钟;维持甲烷气体占比在3%~5%,生长高取向(100)微米晶金刚石层,生长时间为4~10小时。
41.在此步骤(5)中,高取向(100)微米晶金刚石层,微米晶晶粒表面平整,晶粒完整,棱角分明;在拉曼测试中,1332.8cm-1
附近有尖锐的金刚石膜特征峰,可参考图2所示。高取向(100)微米晶金刚石层的作用是具有更低的缺陷密度和应力,表面光滑,具有较高的热导率,其中,高取向(100)微米晶金刚石层的厚度为1~10微米,金刚石的粒径范围为2~50微米。在本技术实施例方案中,高取向(100)微米晶金刚石层的生长形貌,可参考图1的第二幅图和第三幅图,甲烷气体线性升高时的生长形貌对应图1中的第二幅图,在高致密度的纳米晶
金刚石层上生长微米晶金刚石形核;维持甲烷气体占比在3~5%时的生长形貌对应图1中的第三幅图,微米晶金刚石生长的同时取向转变;第四幅图为高取向(100)微米晶金刚石层完全覆盖高致密度的纳米晶金刚石层时的生长形貌。
42.(6)停止通入甲烷,通入占氢气流量3~10%的氩气,对基材表面的进行等离子体清洗,用于清除非金刚石相,时间为30~60分钟。
43.在此步骤(6)中,利用氢气、氩气(也可通入氧气等)产生的等离子体对表面进行刻蚀,非金刚石相更容易被刻蚀,可以清除非金刚石相,提高金刚石质量,降低表面缺陷密度。
44.(7)停止通入氩气,缓慢降低氢气流量、气压、微波功率,降温速率低于每秒钟1℃,降温至室温,破真空后取出具有复合金刚石保护膜的基材。
45.在此步骤(7)中,通过控制氢气流量、气压、微波功率的降低速率,可以达到控制温度的降低速率的目的,降温速率控制在低于每秒钟1℃,可以防止热失配引起的金刚石保护膜与基材表面的应力破坏。
46.(8)在高倍率(≥1000倍)显微镜下观察复合金刚石保护膜是否均匀且完全覆盖在基材上,若未达到100%覆盖,则需要重新进行步骤(2)~(7),直至复合金刚石保护膜100%覆盖在基材上。
47.本技术中还提供一种复合金刚石保护膜,采用上述复合金刚石保护膜的制备方法制备得到。
48.本技术中还提供一种芯片基材,采用上述复合金刚石保护膜的制备方法制备得到具有复合金刚石保护膜的芯片基材。
49.本技术所提供的复合金刚石保护膜及其制备方法和芯片基材,具有以下特点:(1)本技术所提供的复合金刚石保护膜的制备方法适用于制造抗激光辐照的金刚石保护膜,采用高致密度的纳米晶金刚石和高取向微米晶金刚石复合材料,可以提升被保护材料表面的抗纳米激光损伤特性;(2)本技术的复合金刚石保护膜致密度高,可增加被保护材料表面的导热性能,提升其耐划伤等力学性能,具有耐强酸、强碱的特性,并且不会对透光度产生明显影响;(3)采用本技术方法制备得到的复合金刚石保护膜,发生损伤后通常仅为电子元器件表面的复合金刚石保护膜的损伤,可依据本技术的制备方法的步骤进行修复,重新生长复合金刚石保护膜,本技术的复合金刚石保护膜,除了适用于硅材料的抗激光损伤保护外,也可适用于其他材料的抗激光损伤保护,如金属、陶瓷、玻璃、晶体等材料。
50.(4)在本技术技术方案中,采用甲烷、氢气、氩气为原料制备金刚石,原料及尾气均无毒无害,易于处理,环境友好度高,获得原材料容易。
51.以下通过具体实施例对本技术作进一步说明。
52.实施例1首先,将硅片放置于粒径约为50nm的金刚石纳米粉的无水乙醇悬浊液(金刚石纳米粉的浓度为10g/l)中进行超声处理,超声处理频率40khz,超声时间15分钟,之后用无水乙醇超声清洗3次,超声处理频率40khz,超声时间15分钟。
53.将处理后的硅片放置在微波等离子体化学气相沉积系统的样品台上,通入氢气(纯度7n)用于起辉和升温,缓慢增加氢气流量到40sccm、气压到5torr起辉,升温时增加氢气流量到400sccm、气压到95torr、微波功率到5600w,温度达到约780℃。然后通入占氢气流
量8%的氩气(纯度7n),对硅片表面进行25分钟的等离子体清洗。
54.保持氢气流量不变,停止通入氩气后,通入占氢气流量7%的甲烷气体(纯度为6n),气压95 torr,硅片表面温度约800℃,在硅片表面生长金刚石过渡层,厚度为50nm,生长金刚石过渡层的时间为15分钟。
55.保持氢气流量不变,甲烷气体占比从7%随时间线性降低到0.7%,变化时间为7分钟。维持甲烷气体占比在0.7%,生长高致密度的纳米晶金刚石层,厚度为3微米,生长时间为35分钟。
56.保持氢气流量不变,甲烷气体占比从0.7%随时间线性升高到4%,变化时间为7分钟。维持甲烷气体占比在4%,生长高取向(100)微米晶金刚石层,厚度为3微米,生长时间为7小时。
57.停止通入甲烷,通入占氢气流量8%的氩气,对硅片表面非金刚石相进行等离子体清洗,时间为35分钟。
58.停止通入氩气,缓慢降低氢气流量、气压、微波功率,保持降温速率为每秒钟低于0.8℃,降温至室温,破真空后取出具有复合金刚石保护膜的硅片。在高倍率(1000倍)显微镜下观察,硅片表面的复合金刚石保护膜均匀且覆盖完全。
59.在高倍率(1000倍)显微镜下观察,本实施例中复合金刚石保护膜在不同阶段的生长形貌,如图1所示,在硅片表面生长高致密度的粒径约100nm的纳米晶金刚石层,然后再在纳米晶金刚石层表面形成微米晶金刚石层,最终形成粒径2~6微米的高取向(100)微米晶金刚石层。对本实施例中复合金刚石保护膜表面进行拉曼测试,结果如图2所示,1332.8cm-1
附近有尖锐的金刚石膜特征峰。
60.对照例以未经处理的硅片为对照样品1,以未完全覆盖复合金刚石保护膜的硅片为对照样品2,以采用热丝化学气相沉积法在硅片表面沉积金刚石薄膜作为对照样品3。对照样品2采用与实施例1同样的步骤和参数,区别仅在于,生长高取向(100)微米晶金刚石层时的生长时间仅为2小时,从1000倍及以下观察硅片表面有覆盖不均匀的空隙,有纳米晶金刚石裸露。对照样品3采用与实施例1同样的步骤和参数,区别仅在于沉积方式的不同。
61.使用1064nm波长、8ns脉冲激光,光斑面积1.26*10-3
cm2,激光光斑的三维图和二维图如图3和图4所示,采用1-on-1测试方法,对实施例1制备得到的完全覆盖有复合金刚石保护膜的硅片、对照样品1-3进行激光损伤测试,实施例1和对照样品1-3的测试结果图5所示:硅近阈值损伤形貌为对照样品1的测试结果,硅片的损伤阈值为6.01j/cm2;热丝cvd金刚石膜近阈值损伤形貌为对照样品3的测试结果,损伤阈值为6.87j/cm2;未完全覆盖的复合金刚石膜近阈值损伤形貌为对照样品2的测试结果,损伤阈值为11.7j/cm2;高取向复合金刚石近阈值损伤形貌为实施例1的测试结果,损伤阈值为24.50j/cm2。同时,从损伤形貌可以看出,对照样品1和对照样品3发生损伤的位置均在硅片处,对比样品2发生损伤的位置在纳米晶金刚石层处,而完全覆盖有复合金刚石保护膜的硅片发生损伤的位置在复合金刚石保护膜表面高取向(100)微米晶金刚石层处,说明复合金刚石保护膜对硅片有较好的保护作用。
62.应当理解的是,本技术的应用不限于上述的举例,对本领域普通技术人员来说,可以根据上述说明加以改进或变换,所有这些改进和变换都应属于本技术的保护范围。