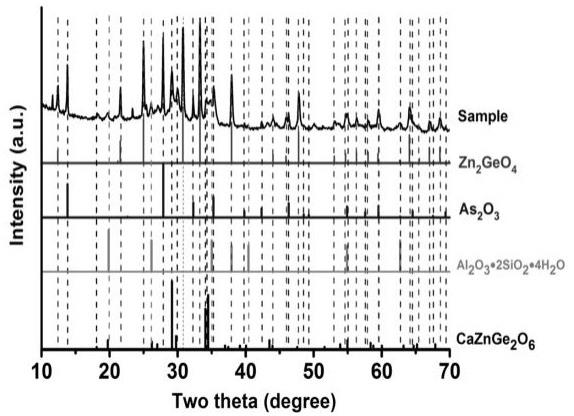
1.本发明属于冶金化工技术领域,具体的说,涉及一种含砷和锗的物料中砷锗的分离方法。
背景技术:2.锗是一种重要的稀有金属和战略资源,在地壳中的丰度为0.00016%,分布稀散且难于从矿石中提取。锗及其化合物具有许多特殊性质,常被应用于红外光学、太阳能电池、纤维光纤、聚合催化剂及医药等高新技术领域,是军工、国防、高新科技等领域的重要原材料。目前,全球原生锗主要来自锌冶炼的副产品回收、含锗褐煤的单独提取。然而,在原生锗的制备过程中,会产生大量含锗砷烟尘,这些含锗砷物料的常规处理方法为深埋处置。然而,这些锗烟尘中含砷量高,约为2%~15%,这些砷随着风化、雨水淋溶等作用会重新溶出,造成严重的砷污染。此外,经检测,这些锗烟尘中锗含量高达8%~25%,由于砷的存在导致无法二次利用这部分锗,导致锗资源浪费。因此预先进行较高砷含量的物料中砷锗分离是锗冶炼的重要环节。
3.目前对含锗砷物料的处理方法主要有火法焙烧脱砷、湿法浸出脱砷和火法-湿法联合工艺。火法焙烧脱砷主要是在高温下使含砷物料中的砷以三氧化二砷的形态挥发,使其与其他有价金属分离,再通过冷凝收尘得到粗制三氧化二砷产品。根据含砷物料中砷的赋存状态,处理方法可以分为直接焙烧挥发法、氧化焙烧法和还原焙烧法。焙烧脱砷存在脱砷率较低,投资大,原料适用范围小,作业环境较差及对大气污染严重等缺点,且得到的三氧化二砷产品纯度较低,还需要进一步处理,湿法浸出脱砷主要是指使用合适的浸出剂搅拌浸取含砷物料,使砷从固相转移进入浸出液中,按照浸出剂的种类一般可以分为水热浸出、酸浸脱砷和碱浸脱砷。与火法焙烧脱砷相比,湿法浸出脱砷具有脱砷率高、环境污染轻、适用范围广、能耗较低等优点,且在浸出液的后续处理过程中还可以直接制备不同的砷系列产品,火法
−
湿法联合工艺主要是指采用纯碱/烧碱焙烧然后水浸脱砷,该生产工艺生产能耗较高、纯碱/烧碱消耗量大、环境污染比较严重。本发明可进行有效的砷锗分离,并对浸出后含砷浸出液进行生产线初步除砷处理,达到厂域内集中处理的要求。
技术实现要素:4.为了克服背景技术中存在的问题,本发明提供了一种含砷和锗的物料中砷锗的分离方法,可进行有效的砷锗分离,并且砷去除率高,锗的损失率小,可充分利用含锗砷物料中的锗,减少锗资源的浪费。
5.为实现上述目的,本发明是通过如下技术方案实现的:所述的含砷和锗的物料中砷锗的分离方法包括以下步骤:1)粉碎:将干燥的含砷锗物料粉碎至50~400目;2)浸出:使用氢氧化钠溶液浸出步骤1)的含砷锗物料,浸出时间为2~18h,浸出固液比为1:2~1:15,浸出次数为1~3次。含锗砷物料中除了部分有机物物外,砷主要以as2o3形
态存在,少量以砷酸盐形态存在, 锗以geo2和锗配合物形态存在。含锗砷物料中典型的锗和砷含量分别为2%-15%和8%~25%。本发明为“湿法”除砷,以砷的浸出率为主,兼顾锗的损失率,其中砷去除率为90%以上,锗的损失率小于10%。
6.3)污水除砷:在步骤2)所得的浸出液中加入三氯化铁,搅拌反应1~6h,静置1~6h,然后分离固体沉淀与除砷污水。采用加入三氯化铁的方式,产生砷酸铁,沉淀污水中的砷,处理后的污水中砷含量为3~5mg/l ,固体沉淀按固废处理,除砷污水并入厂域内污水系统集中处理。
7.4)干燥:将步骤2)所得的浸出渣清洗,干燥,得到除砷高锗精矿,可用于锗的冶炼。
8.作为优选,步骤2)的浸出温度为18~90℃。
9.作为优选,步骤2)氢氧化钠溶液的初始浓度为0.5-10mol/l。
10.作为优选,步骤3)浸出污水沉砷的反应温度为10~40℃。
11.作为优选,步骤3)中三氯化铁与砷的摩尔比为:3:1~10:1。
12.作为优选,步骤3)除砷污水中含砷3~5mg/l。
13.作为优选,步骤4)浸出渣的干燥条件为80~120℃。
14.本发明的有益效果:1、本发明通过对锗烟尘采用单段或多段碱浸浸出砷,实现锌和锗的高效分离,尽量多的浸出砷,并对浸出后含砷的浸出液进行生产线初步除砷处理,达到厂域内集中处理的要求。
15.2、本发明可减少企业含砷废渣的外排,减少含锗砷物料处理过程中所带来的各种潜在污染,确保企业能够长期稳定生产,有利于真正意义上的环境保护,利国利民;并且利于充分利用含锗砷物料中的锗,不仅减少锗资源的浪费,还会产生良好的经济效益。
附图说明
16.图1是本发明锗砷物料的xrd分析结果图;图2是本发明锗砷物料的sem图。
具体实施方式
17.为了使本发明的目的、技术方案和有益效果更加清楚,下面将结合附图,对本发明的优选实施例进行详细的说明,以方便技术人员理解。
18.所述的含砷和锗的物料中砷锗的分离方法包括以下步骤:1)粉碎:将干燥的含砷锗物料粉碎至50~400目;2)浸出:使用初始浓度为0.5-10mol/l的氢氧化钠溶液浸出步骤1)的含砷锗物料,浸出温度为18~90℃,浸出时间为2~18h,浸出固液比为1:2~1:15,浸出次数为1~3次;3)污水除砷:在步骤2)所得的浸出液中加入三氯化铁,反应温度为10~40℃,三氯化铁与砷的摩尔比为:3:1~10:1,搅拌反应1~6h,静置1~6h,然后分离固体沉淀与除砷污水,除砷污水中含砷3~5mg/l;4)干燥:将步骤2)所得的浸出渣清洗,80~120℃干燥,得到除砷高锗精矿。
19.对含锗砷物料进行了x射线衍射分析,判断样品中可能存在的晶体结构。从图1可见,锗烟尘中主要的矿物为锗酸锌、三氧化二砷、埃洛石和氧化锗锌钙,说明在锗烟尘中锗
主要以锗酸锌和氧化锗为主,而砷以三氧化二砷的形式存在,这些氧化物通过碱浸出的方式可以将其转化为相应的离子形式,进而浸出。从图2可以看出,原料主要以小颗粒形式存在并且相互团聚结合为大颗粒的物料颗粒,直径约100~500 nm。
20.实施例1某含锗砷物料的化学成分见表1,对该含锗砷物料进行砷、锗分离。
21.表1 含锗砷物料及除砷高锗精矿的化学组分含锗砷物料组分geo2znoas2o3sb2o3fe2o3mgocaosio2tio2含量%24.719.714.56.015.74.03.92.31.7除砷高锗精矿组分geo2znoas2o3sb2o3fe2o3mgocaosio2tio2含量%34.127.11.40.612.32.13.75.82.9对该含锗砷物料进行分离,具体包括以下步骤:1)粉碎:将干燥的含砷锗物料粉碎至200目;2)浸出:使用初始浓度为3mol/l的氢氧化钠溶液浸出步骤1)的含砷锗物料,浸出温度为80℃,浸出时间为6h,浸出固液比为1:12,浸出次数为2次;3)污水除砷:在步骤2)所得的浸出液中加入三氯化铁,反应温度为25℃,三氯化铁与砷的摩尔比为5:1,搅拌反应2h,静置6h,然后采用板框压滤机分离固体沉淀与除砷污水,除砷污水中含砷量4.1mg/l;4)干燥:将步骤2)所得的浸出渣用清水清洗1次,然后在80℃条件下干燥,得到除砷高锗精矿,其化学组成见表1。
22.由表1中高锗精矿的化学组分可见,精矿中砷的含量由14.5%降低至1.4%,去除物料质量变化的因素,物料中砷的含量降低了90个百分点以上,精矿中锗的含量由24.7%提高到34.1%,结果表明本发明达到了除砷富锗的目标。
23.实施例2某含锗砷物料的主要化学成分见表2,对该含锗砷物料进行砷、锗分离。
24.表2 含锗砷物料及除砷高锗精矿的主要化学组分含锗砷物料组分geo2as2o3含量%24.714.5除砷高锗精矿组分geo2as2o3含量%32.11.5对该含锗砷物料进行分离,具体包括以下步骤:1)粉碎:将干燥的含砷锗物料粉碎至50目;2)浸出:使用初始浓度为10mol/l的氢氧化钠溶液浸出步骤1)的含砷锗物料,浸出温度为90℃,浸出时间为2h,浸出固液比为1:15,浸出次数为1次;3)污水除砷:在步骤2)所得的浸出液中加入三氯化铁,反应温度为10℃,三氯化铁与砷的摩尔比为:3:1,搅拌反应6h,静置6h,然后采用离心机分离固体沉淀与除砷污水,除砷污水中含砷量5.0mg/l;4)干燥:将步骤2)所得的浸出渣用清水清洗1次,然后在120℃条件下干燥,得到除砷高锗精矿,其主要化学组成见表2。
25.由表2中高锗精矿的主要化学组分可见,精矿中砷的含量由14.5%降低至1.5%,去
除物料质量变化的因素,物料中砷的含量降低了90个百分点以上,精矿中锗的含量由24.7%提高到32.1%,结果表明本发明达到了除砷富锗的目标。
26.实施例3某含锗砷物料的主要化学成分见表3,对该含锗砷物料进行砷、锗分离。
27.表3 含锗砷物料及除砷高锗精矿的主要化学组分含锗砷物料组分geo2as2o3含量%24.714.5除砷高锗精矿组分geo2as2o3含量%32.61.4对该含锗砷物料进行分离,具体包括以下步骤:1)粉碎:将干燥的含砷锗物料粉碎至400目;2)浸出:使用初始浓度为0.5mol/l的氢氧化钠溶液浸出步骤1)的含砷锗物料,浸出温度为18℃,浸出时间为18h,浸出固液比为1:2,浸出次数为3次;3)污水除砷:在步骤2)所得的浸出液中加入三氯化铁,反应温度为40℃,三氯化铁与砷的摩尔比为:6:1,搅拌反应6h,静置3h,然后采用离心机分离固体沉淀与除砷污水,除砷污水中含砷量3.8mg/l;4)干燥:将步骤2)所得的浸出渣用清水清洗1次,然后在100℃条件下干燥,得到除砷高锗精矿,其主要化学组成见表3。
28.由表3中高锗精矿的主要化学组分可见,精矿中砷的含量由14.5%降低至1.4%,去除物料质量变化的因素,物料中砷的含量降低了90个百分点以上,精矿中锗的含量由24.7%提高到32.6%,结果表明本发明达到了除砷富锗的目标。
29.实施例4某含锗砷物料的主要化学成分见表4,对该含锗砷物料进行砷、锗分离。
30.表4 含锗砷物料及除砷高锗精矿的主要化学组分含锗砷物料组分geo2as2o3含量%24.714.5除砷高锗精矿组分geo2as2o3含量%33.61.3对该含锗砷物料进行分离,具体包括以下步骤:1)粉碎:将干燥的含砷锗物料粉碎至200目;2)浸出:使用初始浓度为5mol/l的氢氧化钠溶液浸出步骤1)的含砷锗物料,浸出温度为25℃,浸出时间为3h,浸出固液比为1:6,浸出次数为1次;3)污水除砷:在步骤2)所得的浸出液中加入三氯化铁,反应温度为30℃,三氯化铁与砷的摩尔比为10:1,搅拌反应4h,静置1h,然后采用离心机分离固体沉淀与除砷污水,除砷污水中含砷量4.0mg/l;4)干燥:将步骤2)所得的浸出渣用清水清洗1次,然后在80℃条件下干燥,得到除砷高锗精矿,其主要化学组成见表4。
31.由表4中高锗精矿的主要化学组分可见,精矿中砷的含量由14.5%降低至1.3%,去除物料质量变化的因素,物料中砷的含量降低了90个百分点以上,精矿中锗的含量由24.7%
提高到33.6%,结果表明本发明达到了除砷富锗的目标。
32.最后说明的是,以上优选实施例仅用于说明本发明的技术方案而非限制,尽管通过上述优选实施例已经对本发明进行了详细的描述,但本领域技术人员应当理解,可以在形式上和细节上对其作出各种各样的改变,而不偏离本发明权利要求书所限定的范围。