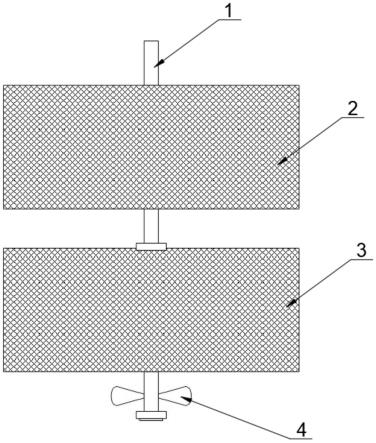
1.本发明涉及金属熔炼领域,尤其是一种锂镁硅合金熔炼方法。
背景技术:2.直接使用锂合金代替金属锂作为阳极在无锂合金阳极中,如sn-sb,sn-co,ni-sn合金等,没有预存储锂,整体能量密度受到低容量的金属锂氧化物阴极的限制,而纯金属锂阳极面临着高反应性和不可控的枝晶生长含锂合金阳极既继承了合金阳极的优良性能,又继承了纯锂金属阳极的优良性能。在过去的40年里,有大量的文献报道了用含锂合金作为锂离子电池的负极材料。从已报道的文献中,我们可以得出结论,合成这些锂合金的方法有几种,包括;熔炼反应、电化学锂化/沉积、磁控溅射和球磨。每种方法各有优缺点,如熔炼反应法和球磨法操作方便,设备价格不贵。电化学锂化法操作更复杂,但适用于几乎所有的锂合金。使用磁控溅射法,合金的成分和厚度很容易调整,但不能普遍地对每一种合金和设备昂贵。
3.在合金材料领域,熔炼法依然是最容易实现,相对工艺最简易、更易大规模工业化生产的方法,但是其合金化过程中的投料均匀性问题随着合金体系的繁多而更加复杂。相对于机械合金化等微观、介观尺度的合金化反应,熔炼法更易造成局部的不均匀,或有生成焓更低的金属间化合物优先生成形成杂相。而为了解决这些问题,使用者们不得不增加额外工艺削弱其影响,例如更高的合金化温度,更加剧烈的搅拌及更长的制备周期。造成极大的成本及不必要的资源浪费,因此,更加科学合理的分析其中各个组元在不同温度下的工艺条件是非常有必要的。
4.在现有的文献介绍中,锂镁硅三元合金li2mgsi被提出具有优良的电化学性能,有望成为下一代锂离子电池负极材料。但是通过传统的合金熔炼的方法容易形成锂硅二元合金li5si2和li7si3,通过美国西北大学chris wolverton团队创建的材料dft计算热力学和结构性质的数据库查阅发现,目标合金li2mgsi生成焓为-0.254ev/atom,大于li5si2的-0.273ev/atom及li7si3的-0.268ev/atom,这表明当在熔融的金属锂中同时投入硅和镁原料,生成li5si2、li7si3更加稳定,因而在最终产物中会夹杂li5si2、li7si3,li5si2、li7si3的熔点温度为750℃左右。因此采用传统的熔炼釜制备该材料需要至少耐熔融金属锂液800℃的腐蚀,对材质考验极大,较难实现。
5.因此,在li2mgsi制备过程中因避免锂硅金属间化合物的形成,有文献采用第一性原理计算通过优先生成mg2si再与金属锂通过固相反应法生成li2mgsi,描述了在外界电压下可将锂原子嵌入mg2si中,反应方程式为mg8si4+8li
→
mg4si4li8+4mg。但是,固相反应法无疑是效率较低的,不适用于工业生产。除此之外,通过对现有合金制备产线分析及相关专利检索,尚无锂镁硅三元合金的制备工艺。
技术实现要素:6.本发明所要解决的技术问题是提供一种可以稳定批量生产的锂镁硅合金熔炼方
法。
7.本发明公开的锂镁硅合金熔炼方法,包括如下步骤:
8.锂镁反应:按照锂镁硅合金li2mgsi中各元素的总体原子比例,向熔炼釜中加入单质锂和单质镁,控制温度至锂镁反应温度,生成锂镁金属间化合物limg2;
9.锂镁硅反应:按照锂镁硅合金中各元素的总体原子比例,再加入单质硅,控制温度至锂镁硅反应温度,生成锂镁硅合金li2mgsi。
10.优选地,在锂镁反应步骤中,先向熔炼釜中加入单质锂,并将单质锂熔化为金属锂液,再升温至锂镁反应温度,向金属锂液中加入单质镁进行反应。
11.优选地,在锂镁硅反应步骤中,先升温至锂镁硅反应温度,再加入单质硅进行反应。
12.优选地,采用的熔炼釜中设置有搅拌装置,所述搅拌装置包含搅拌杆以及滤网投料器,所述滤网投料器均连接于搅拌杆上,所述滤网投料器包含上滤网层和下滤网层,所述搅拌杆连接有升降机构;
13.在实施锂镁硅合金熔炼方法时,将单质锂加入熔炼釜中,将单质镁放入下滤网层,将单质硅放入上滤网层;
14.在锂镁反应步骤中,将单质锂熔化为金属锂液后,通过升降机构控制搅拌杆下降,使所述滤网投料器的下滤网层没入金属锂液中,启动搅拌装置进行搅拌,使下滤网层中的单质镁与金属锂液反应;
15.在锂镁硅反应步骤中,再通过升降机构控制搅拌杆下降,使所述滤网投料器的上滤网层没入金属熔融液中,继续开启搅拌装置进行搅拌,使上滤网层中的单质硅与金属熔融液反应。
16.优选地,所述滤网投料器的目数为50-200目。
17.优选地,所述滤网投料器加入的单质镁和单质硅的粒径为2~4mm。
18.优选地,所述锂镁反应温度为500℃-700℃,所述锂镁硅反应为700℃-800℃。
19.优选地,在锂镁反应步骤中,加入的单质镁质量比生成的锂镁硅合金li2mgsi中的镁质量多1%-5%;在锂镁硅反应中,加入的单质硅质量比生成的锂镁硅合金li2mgsi中的硅质量多1%-8%。
20.优选地,在锂镁硅反应步骤之后还包括:
21.浇铸:打开熔炼釜的浇铸阀门,将熔融状态的锂镁硅合金li2mgsi通入模具中,控制模具的温度,使锂镁硅合金li2mgsi在模具中凝固为固态并冷却。
22.优选地,在浇铸步骤之后还包括:
23.退火:将冷却的锂镁硅合金li2mgsi升温至400℃-500℃进行退火,升温速度为50℃-200℃/h,退火时间2-5h,然后进行冷却,冷却速度20℃-50℃/h。
24.本发明的有益效果是:本技术的锂镁硅合金熔炼方法相较于现有的熔炼方法,可以防止生成锂硅二元合金,保证锂镁硅合金的质量,且反应温度更低,安全性更好;相较于固相反应法工艺简单,生产效率更高,可实现批量稳定制备。
附图说明
25.图1是本技术的搅拌装置示意图;
26.图2是本技术制备出的锂镁硅合金li2mgsi与标准图谱的对比图。
27.附图标记:搅拌杆1,上滤网层2,下滤网层3,搅拌桨4。
具体实施方式
28.下面对本发明进一步说明。
29.本发明公开的锂镁硅合金熔炼方法,包括如下步骤:
30.锂镁反应:按照锂镁硅合金li2mgsi中各元素的总体原子比例,向熔炼釜中加入单质锂和单质镁,控制温度至锂镁反应温度,生成锂镁金属间化合物limg2;
31.锂镁硅反应:按照锂镁硅合金中各元素的总体原子比例,再加入单质硅,控制温度至锂镁硅反应温度,生成锂镁硅合金li2mgsi。
32.本技术将锂、镁、硅进行分批次投入,先进行锂镁反应,优先生成锂镁金属间化合物limg2(生成焓-0.060ev/atom),因为锂镁硅合金li2mgsi中锂镁硅三种元素总体原子比例为4:2:2(质量比为20.9:36.7:42.4)。因此在锂镁反应阶段,锂、镁按照约4:2投入,第一阶段反应式为4li+2mg
→
limg2+3li,控制温度使得镁完全熔于锂金属液中,获得含有锂镁金属间化合物limg2的锂金属液,然后按照上述比例加入单质硅,单质硅加入后会发生反应:3li+2si
→
2lisi+li,同时会发生的总反应:2lisi+limg2+li
→
2li2mgsi,最终获得锂镁硅合金li2mgsi。
33.由于金属锂熔点(180.5℃)远小于镁(650.0℃)和硅(1414.9℃),因而,作为本技术的优选实施方式,在锂镁反应步骤中,先向熔炼釜中加入单质锂,并将单质锂熔化为金属锂液,再升温至锂镁反应温度,向金属锂液中加入单质镁进行反应。如此,可以使单质镁充分与金属锂液接触,提高反应速率。类似地,在锂镁硅反应步骤中,先升温至锂镁硅反应温度,再加入单质硅进行反应。保证单质硅在加入熔炼釜时,釜具有合适比例并呈液态的limg2和li。
34.在熔炼过程中通常需要设置搅拌装置进行搅拌,使物料充分混合,加快反应进程,为了更好地实施本专利的分批投入原料的方法,在本技术的优选实施方式中,采用的熔炼釜中设置有搅拌装置,如图1所示,所述搅拌装置包含搅拌杆1以及滤网投料器,所述滤网投料器均连接于搅拌杆1上,所述滤网投料器包含上滤网层2和下滤网层3,所述搅拌杆1连接有升降机构;
35.在实施锂镁硅合金熔炼方法时,将单质锂加入熔炼釜中,将单质镁放入下滤网层3,将单质硅放入上滤网层2;
36.在锂镁反应步骤中,将单质锂熔化为金属锂液后,通过升降机构控制搅拌杆1下降,使所述滤网投料器的下滤网层3没入金属锂液中,启动搅拌装置进行搅拌,使下滤网层3中的单质镁与金属锂液反应;
37.在锂镁硅反应步骤中,再通过升降机构控制搅拌杆1下降,使所述滤网投料器的上滤网层2没入金属熔融液中,继续开启搅拌装置进行搅拌,使上滤网层2中的单质硅与金属熔融液反应。
38.采用该搅拌装置兼具分批次投料及搅拌的功能,控制升降搅拌杆1的高度使得掺杂元素镁和硅完全浸没入合金液中,实现分批次投料加料。滤网投料器本身可以作为搅拌桨4,也可以在其下再设置搅拌桨4,便于在锂熔化过程进行搅拌。升降机构可以采用现有的
搅拌将的升降装置,如气缸、油缸、电动伸缩杆等。
39.滤网投料器可在制备之初上下层分别内置适当比例的纯硅和纯镁,当锂金属熔融液达到目标温度后,下降该装置直至没入熔融液面一下适当位置,此时熔融金属液可浸没并浸入滤网投料器内与掺杂料接触并进行固液合金化。开启搅拌桨4,合金化后的熔融合金液由于离心力从侧边滤网溢出,而投料由于其粒径较大难以从滤网溢出,其余相对浓度较低的金属液进入搅拌桨4内部持续进行合金化。此装置可对熔融金属液起到一定的导流作用,当投料还未熔化时无法从滤网中溢出,离心力及搅拌桨4外部形状对金属液的扰动,使得投料周围保持的金属液具有较强的流动性,使得熔点较高的金属间化合物难以形成。同时,该装置也可有效阻碍基底金属锂液表面的氧化氮化杂质进入滤网与投料反应,而金属液合金化后以熔化或微细颗粒的形式从搅拌桨4内部离心至熔炼釜内,在搅拌桨4外部形状的扰动下更易彻底合金化。
40.该方法中所述装置材质需在目标环境中具有稳固结构及耐腐蚀;所述装置材质可选用316不锈钢;更优的,材质可选用耐腐蚀或耐高温不锈钢;更优的,材质可选用特种耐高温耐腐蚀钛合金、哈氏合金网;更优的,其过滤网内部设有加强钢筋以维持其在高温下的形状稳定。
41.该方法中所述滤网投料器目数为50-200目,更优的100目,这是由于熔融金属锂具有较高的表面张力,滤网目数过大会导致金属锂无法浸没入滤网内,目数过小会造成过滤效果不佳。所述滤网投料器加入的单质镁和单质硅的粒径优选为2~4mm,更优的粒径尺寸约为3mm。
42.在各反应步骤中,控制温度是很重要的操作,虽然本领域的技术人员可以根据现有技术找出大致的温度控制范围,但是,在本技术的优选实施方式中,首先将熔炼釜加热温度设置为250℃-400℃,待金属锂完全熔化且升至目标温度后,保温5-30min。更优的,加热温度设置为300℃-350℃,保温时间为10min。
43.进一步,升高温度至锂镁反应阶段,温度范围为500℃-700℃,更优的温度范围为500℃-600℃;控制搅拌杆1升降,将内置纯镁的下层投料滤网浸没入熔融金属锂液面下,开启搅拌桨4转速设置为50-200r/min,更优的50-100r/min,更优的搅拌桨4可设置这个反转以确保充分熔融合金化;保温时间设置为10min-60min,更优的30min-40min,使得镁与锂充分的结合。
44.进一步,升高温度至锂镁硅反应阶段,温度范围提升至700℃-800℃,更优的温度范围设置为700℃-750℃;保温5min,控制搅拌杆1升降,将内置纯硅的上层投料滤网浸没入熔融合金液面下,开启搅拌桨4转速设置为50-200r/min,更优的50-100r/min,更优的搅拌桨4可设置这个反转以确保充分熔融合金化;保温时间设置为10min-60min,更优的30min-40min,使得硅与锂镁合金充分的结合。
45.前面提到加入的单质锂镁硅按照锂镁硅合金li2mgsi中各元素的总体原子比例确定,但是并非是指加入的单质锂镁硅的比例等于li2mgsi中各元素的总体原子比例,锂镁硅的投入比例为原子比例,换算为质量比为20.9:36.7:42.4,实际投料应当考虑物料损耗,且不同的熔炼设备稍有差异,在本技术的优选实施方式中,加入的单质镁质量比生成的锂镁硅合金li2mgsi中的镁质量多1%-5%,更优为2%-3%;在锂镁硅反应中,加入的单质硅质量比生成的锂镁硅合金li2mgsi中的硅质量多1%-8%,更优为4%-5%。
46.在生成锂镁硅合金li2mgsi,还需要将其浇铸成锭以便于后续加工,因此,在本技术的优选实施方式中,在锂镁硅反应步骤之后还包括浇铸步骤:打开熔炼釜的浇铸阀门,将熔融状态的锂镁硅合金li2mgsi通入模具中,控制模具的温度,使锂镁硅合金li2mgsi在模具中凝固为固态并冷却。模具的温度优选控制在0℃-10℃。
47.在浇铸步骤之后还包括退火步骤:将冷却的锂镁硅合金li2mgsi升温至400℃-500℃进行退火,升温速度为50℃-200℃/h,退火时间2-5h,然后进行冷却,冷却速度20℃-50℃/h。更优的设置升温速度100℃/h,退火温度450℃,退火时间3h,冷却速度30℃/h。通过退火可以降低残余应力,稳定尺寸,减少变形与裂纹倾向,有利于后续加工。
48.下面是本技术的一个具体的实施例。
49.制备锂硅镁三元合金li2mgsi共2kg。
50.分别称量锂镁硅质量分别为418.9g、748.2g(补充损耗2%)、881.5g(补充损耗4%)。将纯镁置于下部投料滤网中,将纯硅置于上部滤网中,将纯锂置于熔炼釜底部。
51.①
首先将熔炼釜加热温度设置为300℃,待金属锂完全熔化且升至300℃后,保温10min。
52.②
升高温度至锂镁反应阶段,温度设置为550℃,控制搅拌杆1升降,将内置纯镁的下层投料滤网浸没入熔融金属锂液面下,开启搅拌桨4转速设置为100r/min,每5分钟改变一次方向,持续30min,使得镁与锂充分的结合。
53.③
升高温度至锂镁硅反应阶段,温度设置为750℃,保温5min,控制搅拌杆1升降,将内置纯硅的上层投料滤网浸没入熔融合金液面下,开启搅拌桨4转速设置为100r/min,每5分钟改变一次方向,持续60min,使得硅与锂镁合金充分的结合。
54.④
控制模具温度为6℃,关闭搅拌桨4,将搅拌桨4抬升至熔融合金液面以上,开阀,浇铸。控制模具温度低于10℃直至合金锭完全冷却。
55.⑤
对合金锭进行退火处理,设置升温速度100℃/h,退火温度450℃,退火时间3h,冷却速度30℃/h。
56.取锭,对其进行xrd成分结构分析,与标准图谱的对比如图2所示,可以看出制备的锂硅镁三元合金li2mgsi标准图谱十分吻合,纯度达到符合要求。