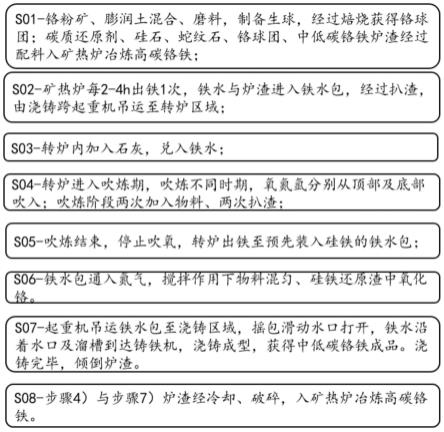
1.本发明涉及中低碳铬铁生产技术领域,尤其是一种高碳铬铁、中低碳铬铁联合生产方法。
背景技术:2.国内生产中低碳铬铁的工艺有三步法(或叫硅热法)和氩氧精炼法(aod法)。三步法工艺是在三台电炉上实现的。第一台电炉生产高碳铬铁,第二台电炉以高碳铬铁为原料生产硅铬合金,第三台电炉以硅铬合金为原料生产中低碳铬铁。三步法工艺冗长,能耗较高。aod炉冶炼中低碳铬铁虽然直接利用了高温铬铁铁水,但是aod炉布置于浇铸跨的偏跨,aod炉需要另外起高层厂房,高度大概40m,投资成本较高。并且aod炉冶炼中低碳铬铁顶枪喷入氧气,底枪为氩气氧气混合气体,底枪氧气比氩气从6:1到达3:1,然后从2:1到达1:1,然后从1:3到达1:6,最后顶枪停止吹氧底枪吹入纯氩,加入硅铁还原。现有的aod炉生产中低碳铬铁,吨合金消耗氩气达到83nm3,而氩气的制备成本极高。
3.由于aod炉底部同时喷入大量氧气和氩气,熔池反应激烈,熔池对炉衬的冲刷十分剧烈,导致aod炉炉衬仅仅40炉次(5天)就要更换一次;频繁更换导致成本增加,并且冶炼中低碳铬铁中断频率较高。即使采用大量氮气代替大量氩气(降低用氩成本)然后与氧气同时从底部喷入,同样会面临熔池反应激烈的问题,熔池冲刷炉衬侧壁,导致炉衬频繁更换。大量氮气从熔池底部吹入也面临产品氮含量较高,不利于下游厂家使用的问题。
技术实现要素:4.针对现有技术存在的不足,本发明的目的是提供一种高碳铬铁、中低碳铬铁联合生产方法,节约了大量的氩气消耗,中低碳铬铁成品被浇铸到合适粒度小于25cm,能够满足下游厂商需求。
5.为了实现上述目的,本发明是通过如下的技术方案来实现:
6.一种高碳铬铁、中低碳铬铁联合生产方法,包括:
7.在冶炼跨利用矿热炉冶炼高碳铬铁,矿热炉出铁时,铁水与炉渣沿着溜槽落入铁水包,铁水包从冶炼跨转运至浇铸跨,经过扒渣,由浇铸跨起重机转运并倾倒至预先加入石灰、铬球团的顶底复出转炉,倾倒时转炉底枪吹入氮气、氩气;
8.顶底复出转炉顶枪吹入氧气,底枪吹入氮气和氩气以进行吹炼,第一阶段吹炼结束进行出渣并加入石灰和铬球团,第二阶段吹炼结束进行出渣并加入铬球团,第三阶段吹炼结束后停止吹氧;
9.倾动顶底复出转炉倒出铁水至预先装入硅铁的铁水包,倾倒过程中,保持转炉氩气、氮气吹入,铁水包底部通入氮气以混匀硅铁及铁水、炉渣,硅铁还原炉渣中氧化铬;
10.浇铸跨起重机吊运铁水包至浇铸区域,铁水包下方滑动水口打开,铁水沿着滑动水口以及溜槽到达铸铁机浇铸成型得到中低碳铬铁成品。
11.作为进一步的实现方式,先采用铬粉矿与膨润土按设定配比混合、磨料,制备生
球,经过焙烧获得铬球团;之后碳质还原剂、硅石、蛇纹石、铬球团、冶炼中低碳铬铁产生的炉渣通过设定配比入矿热炉冶炼高碳铬铁。
12.作为进一步的实现方式,所述铬粉矿粒度小于1mm,碳质还原剂粒度为8~40mm,碳含量大于82%。
13.作为进一步的实现方式,所述顶底复出转炉预先加入石灰、铬球团的吨合金需要量分别为40~90kg、20~30kg,所述顶底复出转炉兑入铁水时间3~6min。
14.作为进一步的实现方式,所述第一阶段吹炼结束后,石灰和铬球团的吨合金需要量分别为0~30kg、20~50kg;第二阶段吹炼结束后,铬球团的吨合金需要量为10~50kg,三个吹炼阶段时间为19min~22min。
15.作为进一步的实现方式,顶底复出转炉倒出铁水铁水包前停止吹氧,倒铁水时间为3min~5min。
16.作为进一步的实现方式,铁水浇铸完毕,关闭滑动水口,起重机吊运铁水包至扒渣区,倾倒炉渣,扒渣区与吹炼阶段的炉渣经冷却、破碎后,用于矿热炉冶炼高碳铬铁。
17.作为进一步的实现方式,所述铁水包与铸铁机接触位置上方设置吸尘罩,以处理浇铸产生的烟尘。
18.作为进一步的实现方式,所吹的气体压力为1.6~2.0mpa。
19.作为进一步的实现方式,所述第一阶段吹炼结束加入的石灰粒度为10~70mm,硅铁的粒度为10~50mm。
20.上述本发明的有益效果如下:
21.1.本发明的铁水包倾倒至预先加入石灰、铬球团的顶底复出转炉,倾倒时转炉底枪吹入氮气、氩气,顶底复出转炉顶枪吹入氧气,底枪吹入氮气和氩气,之后分为三个阶段吹炼,每一阶段结束后进行扒渣;顶底复出转炉节约了大量的氩气消耗,降低氩气成本以及提高了炉衬使用周期;底枪吹入少量氩气和少量氮气,对于炉衬的冲刷较少。减少了转炉换衬成本,保障了转炉最大限度生产;铁水包下方滑动水口定点浇铸系统,仅在滑动水口打开一瞬间产生少量烟尘。浇铸过程中,几乎无烟尘。设置收尘罩便于实现粉尘收集。浇铸铁水可以通过铸铁机上的喷淋系统降温冷却,热量由水吸收,减少热量对空气的辐射。
22.2.本发明在转炉吹炼体系中加入了铬粉矿,一方面减缓铁水内铬的过度氧化,另一方面合理造渣,无需使用氟化钙作为造渣熔剂;另一方面铬粉矿平衡炉内铁水温度,避免炉温过高,以及减少了炉内喷溅事故发生。
23.3.本发明采用铸铁机直接将中低碳铬铁成品浇铸到合适粒度小于25cm,相对于常规浇铸的中低碳铬铁成品,需要经过人工破碎到合格粒度,人力成本较高,人员作业环境和安全无法保障,采用铸铁机能够满足下游厂商需求。
24.4.本发明采用铁水包加入硅铁、兑入铁水,硅铁在转炉外还原氧化铬、铁水包内精炼提高铬收得率,避免了硅与氧化铬反应生成的sio2对转炉碱性炉衬的侵蚀。
附图说明
25.构成本发明的一部分的说明书附图用来提供对本发明的进一步理解,本发明的示意性实施例及其说明用于解释本发明,并不构成对本发明的不当限定。
26.图1是本发明实施例中一种高碳铬铁、中低碳铬铁联合生产方法的流程图。
27.图2是本发明实施例中生产中低碳铬铁的阶段示意图。
28.图3是本发明实施例中高碳铬铁、中低碳铬铁联合生产的系统平面布置图。
29.图中:为显示各部位位置而夸大了互相间间距或尺寸,示意图仅作示意。
具体实施方式
30.应该指出,以下详细说明都是例示性的,旨在对本发明提供进一步的说明。除非另有指明,本发明使用的所有技术和科学术语具有与本发明所属技术领域的普通技术人员通常理解的相同含义。
31.本发明的一种典型的实施方式中,一种高碳铬铁、中低碳铬铁联合生产方法,其生产系统布置如图3所示,包括依次设置的冶炼跨、浇筑跨和成品跨。矿热炉设置在冶炼跨,用于冶炼高碳铬铁,浇铸跨设有铸造起重机,用于转运铁水包,将铁水包从冶炼跨转运至浇铸跨的顶底复出转炉,转炉位于浇铸跨,用于生产中低碳铬铁,转炉与矿热炉距离小于100m。顶底复出转炉一侧设置铸铁机,用于浇铸成型中低碳铬铁成品。成型后的成品被转运至成品跨。
32.具体生产步骤如下:
33.1)铬粉矿与膨润土按照一定配比混合、磨料,制备生球,经过焙烧获得铬球团;碳质还原剂、硅石、蛇纹石、铬球团、冶炼中低碳铬铁产生的炉渣通过合理配比入矿热炉冶炼高碳铬铁;
34.2)矿热炉每2~4个小时出铁1次,出铁时间15~25min;出铁时,矿热炉铁水与炉渣沿着溜槽落入铁水包。铁水包从冶炼跨转运至浇铸跨,经过扒渣,由浇铸跨起重机转运至顶底复出转炉区域;
35.3)顶底复出转炉预先加入石灰、铬球团,吨合金需要量分别为40~90kg、20~30kg,然后起重机吊运铁水包倾倒至转炉内,兑入高碳铬铁铁水;兑入铁水时间3~6min,兑入过程转炉底枪吹入氮气、氩气;
36.4)兑入结束,转炉进入吹炼阶段,顶枪吹入氧气、底枪吹入氮气和氩气,吹炼分为3个阶段,每个阶段时间为19min~22min;
37.吹炼1期末尾,进行出渣、然后加入石灰和铬球团,吨合金需要量分别为0~30kg、20~50kg;吹炼2期末尾,进行出渣,然后加入铬球团,吨合金需要量为10~50kg;
38.5)吹炼结束,停止吹氧,倾动转炉倒出铁水至预先装入硅铁的铁水包,倒铁水时间为3min~5min。倾倒过程中,保持转炉氩气、氮气吹入。
39.6)铁水包底部通入氮气,保内物料上下翻腾,在氮气搅拌下混匀硅铁及铁水、炉渣,硅铁还原炉渣中氧化铬。
40.7)浇铸跨起重机吊运铁水包至浇铸区域,铁水包下方滑动水口打开,铁水沿着水口以及溜槽到达铸铁机、浇铸成型,中低碳铬铁成品粒度小于25cm。铁水浇铸完毕,关闭滑动水口。起重机吊运铁水包至扒渣区,倾倒炉渣。
41.8)步骤4)与步骤7)所获得炉渣经冷却、破碎后,用于步骤1)矿热炉冶炼高碳铬铁。
42.其中步骤3)吨合金耗氮量0.5~1nm3,耗氩气量为0.3~0.7nm3。
43.其中步骤3)~5)过程,各类气体压力为1.6~2.0mpa
44.其中,步骤4)吹炼1期,吨合金耗氧量为23~38nm3,耗氮量为5~7nm3,耗氩气量为
2.6~4.0nm3;吹炼2期,吨合金耗氧量为45~67nm3,耗氮量为2.6~4.0nm3,耗氩气量为2.6~4.0nm3;吹炼3期,吨合金耗氧量为23~38nm3,耗氮量为2.6~4.0nm3,耗氩气量为2.6~4.0nm3;
45.其中步骤1)高碳铬铁碳含量为6~10%,硅含量为3~5%;
46.其中步骤7)中低碳铬铁碳含量小于2%,硅含量小于2%;
47.其中步骤5)铁水包内硅铁量为吨合金消耗10~50kg。
48.其中步骤5)吨合金耗氮气量0.6~1.2nm3,耗氩气量为0.4~0.9nm3。
49.其中步骤6)氮气用量为吨合金消耗1~2nm3。
50.其中步骤7)铁水包与铸铁机接触位置上方,设置吸尘罩,处理浇铸产生的烟尘。
51.其中步骤1)铬粉矿粒度小于1mm,氧化铬含量大于40%,cr/fe大于1.5;碳质还原剂,粒度为8~40mm,碳含量大于82%;铬球团粒度为
52.其中步骤4)石灰粒度为10~70mm;
53.其中步骤5)硅铁粒度为10~50mm;
54.实施例1
55.本实施例的转炉与矿热炉距离50m,矿热炉为全密闭36000kva高碳铬铁矿热炉,转炉为25吨转炉。
56.该系统生产步骤如下:
57.1)铬粉矿与膨润土按照一定配比混合、磨料,制备生球,经过焙烧获得铬球团;碳质还原剂、硅石、蛇纹石、铬球团、冶炼中低碳铬铁产生的炉渣通过合理配比入矿热炉冶炼高碳铬铁;
58.2)矿热炉每3个小时出铁1次,出铁时间20min;出铁时,矿热炉铁水与炉渣沿着溜槽落入铁水包。铁水包从冶炼跨转运至浇铸跨,经过扒渣,由浇铸跨起重机转运至顶底复出转炉区域;
59.3)顶底复出转炉预先加入石灰、铬球团,吨合金需要量分别为55kg、25kg,然后起重机吊运铁水包倾倒至转炉内,兑入高碳铬铁铁水;兑入铁水时间4min,兑入过程转炉底枪吹入氮气、氩气;
60.4)兑入结束,转炉进入吹炼阶段,顶枪吹入氧气、底枪吹入氮气和氩气,吹炼分为3个阶段,3阶段时间分别为19min、20min、20min;
61.吹炼1期末尾,进行出渣、然后加入石灰和铬球团,吨合金需要量分别为25kg、35kg;吹炼2期末尾,进行出渣,然后加入铬球团,吨合金需要量为40kg;
62.5)吹炼结束,停止吹氧,倾动转炉倒出铁水至预先装入硅铁的铁水包,倒铁水时间为4min。倾倒过程中,保持转炉氩气、氮气吹入。
63.6)铁水包底部通入氮气,包内物料上下翻腾,在氮气搅拌下混匀硅铁及铁水、炉渣,硅铁还原炉渣中氧化铬。
64.7)浇铸跨起重机吊运铁水包至浇铸区域,铁水包下方滑动水口打开,铁水沿着水口以及溜槽到达铸铁机、浇铸成型,中低碳铬铁成品粒度小于25cm。铁水浇铸完毕,关闭滑动水口。起重机吊运铁水包至扒渣区,倾倒炉渣。
65.8)步骤4)与步骤7)所获得炉渣经冷却、破碎后,用于步骤1)矿热炉冶炼高碳铬铁。
66.其中步骤3)吨合金耗氮量0.8nm3,耗氩气量为0.4nm3。
67.其中步骤3)~5)过程,各类气体压力为1.8mpa
68.其中,步骤4)吹炼1期,吨合金耗氧量为33nm3,耗氮量为6nm3,耗氩气量为3nm3;吹炼2期,吨合金耗氧量为50nm3,耗氮量为3nm3,耗氩气量为2.9nm3;吹炼3期,吨合金耗氧量为29nm3,耗氮量为3.2nm3,耗氩气量为3.0nm3;
69.其中步骤1)高碳铬铁碳含量为7%,硅含量为4%;
70.其中步骤7)中低碳铬铁碳含量小于2%,硅含量小于2%;
71.其中步骤5)铁水包内硅铁量为吨合金消耗12kg。
72.其中步骤5)吨合金耗氮气量0.8nm3,耗氩气量为0.6nm3。
73.其中步骤6)氮气用量为吨合金消耗1nm3。
74.其中步骤7)铁水包与铸铁机接触位置上方,设置吸尘罩,处理浇铸产生的烟尘。
75.其中步骤1)铬粉矿粒度小于1mm,氧化铬含量大于40%,cr/fe大于1.5;碳质还原剂,粒度为8~40mm,碳含量大于82%;铬球团粒度为
76.其中步骤4)石灰粒度为10~70mm;
77.其中步骤5)硅铁粒度为10~50mm。
78.传统中低碳铬铁浇铸采用起重机吊运铁水包,移动倾倒、浇铸到不同锭模上,客观导致了浇铸除尘困难。因为起重机吊运倾倒过程为动态,无法设置收尘罩。导致浇铸区域热量增加、粉尘大量产生影响健康。
79.本实施例的铁水包下方滑动水口定点浇铸系统,仅在滑动水口打开一瞬间产生少量烟尘。浇铸过程中,几乎无烟尘。可以在浇铸区域上方设置收尘罩,实现粉尘收集。浇铸铁水可以通过铸铁机上的喷淋系统降温冷却,热量由水吸收,减少热量对空气的辐射。
80.实施例2
81.本实施例的矿热炉与顶底复出转炉距离为55m,矿热炉为39000kva全密闭高碳铬铁矿热炉,转炉为30t转炉。
82.具体的生产步骤如下:
83.1)铬粉矿与膨润土按照一定配比混合、磨料,制备生球,经过焙烧获得铬球团;碳质还原剂、硅石、蛇纹石、铬球团、冶炼中低碳铬铁产生的炉渣通过合理配比入矿热炉冶炼高碳铬铁;
84.2)矿热炉每2.6个小时出铁1次,出铁时间22min;出铁时,矿热炉铁水与炉渣沿着溜槽落入铁水包。铁水包从冶炼跨转运至浇铸跨,经过扒渣,由浇铸跨起重机转运至顶底复出转炉区域;
85.3)顶底复出转炉预先加入石灰、铬球团,吨合金需要量分别为80kg、28kg,然后起重机吊运铁水包倾倒至转炉内,兑入高碳铬铁铁水;兑入铁水时间5min,兑入过程转炉底枪吹入氮气、氩气;
86.4)兑入结束,转炉进入吹炼阶段,顶枪吹入氧气、底枪吹入氮气和氩气,吹炼分为3个阶段,每个阶段时间均为22min;
87.吹炼1期末尾,进行出渣、然后加入石灰和铬球团,吨合金需要量分别为30kg、40kg;吹炼2期末尾,进行出渣,然后加入铬球团,吨合金需要量为45kg;
88.5)吹炼结束,停止吹氧,倾动转炉倒出铁水至预先装入硅铁的铁水包,倒铁水时间为5min。倾倒过程中,保持转炉氩气、氮气吹入。
89.6)铁水包底部通入氮气,包内物料上下翻腾,在氮气搅拌下混匀硅铁及铁水、炉渣,硅铁还原炉渣中氧化铬。
90.7)浇铸跨起重机吊运铁水包至浇铸区域,铁水包下方滑动水口打开,铁水沿着水口以及溜槽到达铸铁机、浇铸成型,中低碳铬铁成品粒度小于25cm。铁水浇铸完毕,关闭滑动水口。起重机吊运铁水包至扒渣区,倾倒炉渣。
91.8)步骤4)与步骤7)所获得炉渣经冷却、破碎后,用于步骤1)矿热炉冶炼高碳铬铁。
92.其中步骤3)吨合金耗氮量0.52nm3,耗氩气量为0.35nm3。
93.其中步骤3)~5)过程,各类气体压力为1.7mpa
94.其中,步骤4)吹炼1期,吨合金耗氧量为29nm3,耗氮量为6.8nm3,耗氩气量为3.7nm3;吹炼2期,吨合金耗氧量为66nm3,耗氮量为3.6nm3,耗氩气量为3.9nm3;吹炼3期,吨合金耗氧量为36nm3,耗氮量为2.9nm3,耗氩气量为3.9nm3;
95.其中步骤1)高碳铬铁碳含量为9.9%,硅含量为5%;
96.其中步骤7)中低碳铬铁碳含量小于2%,硅含量小于2%;
97.其中步骤5)铁水包内硅铁量为吨合金消耗45kg。
98.其中步骤5)吨合金耗氮气量1.2nm3,耗氩气量为0.8nm3。
99.其中步骤6)氮气用量为吨合金消耗1.2nm3。
100.其中步骤7)铁水包与铸铁机接触位置上方,设置吸尘罩,处理浇铸产生的烟尘。
101.其中步骤1)铬粉矿粒度小于1mm,氧化铬含量大于40%,cr/fe大于1.5;碳质还原剂,粒度为8~40mm,碳含量大于82%;铬球团粒度为
102.其中步骤4)石灰粒度为10~70mm;
103.其中步骤5)硅铁粒度为10~50mm。
104.本实施例的吹炼时间约57min~66min,相对常规aod工艺节约吹炼时间,更利于保护炉衬。并且吨合金消耗硅铁较少,更加降低成本;甚至可以不用硅铁去提升氧化铬收得率。对于中低碳铬铁生产过程中产生的炉渣,冷却、破碎重新返回至矿热炉冶炼高碳铬铁;矿热炉内电弧高温下碳热还原反应将中低碳铬铁冶炼过程产生的炉渣中氧化铬还原。
105.实施例3
106.本实施例的矿热炉与顶底复出转炉距离为80m,矿热炉为48000kva全密闭高碳铬铁矿热炉,转炉为50t转炉。
107.该系统生产步骤如下:
108.1)铬粉矿与膨润土按照一定配比混合、磨料,制备生球,经过焙烧获得铬球团;碳质还原剂、硅石、蛇纹石、铬球团、冶炼中低碳铬铁产生的炉渣通过合理配比入矿热炉冶炼高碳铬铁;
109.2)矿热炉每4个小时出铁1次,出铁时间25min;出铁时,矿热炉铁水与炉渣沿着溜槽落入铁水包。铁水包从冶炼跨转运至浇铸跨,经过扒渣,由浇铸跨起重机转运至顶底复出转炉区域;
110.3)顶底复出转炉预先加入石灰、铬球团,吨合金需要量分别为45kg、30kg,然后起重机吊运铁水包倾倒至转炉内,兑入高碳铬铁铁水;兑入铁水时间3~6min,兑入过程转炉底枪吹入氮气、氩气;
111.4)兑入结束,转炉进入吹炼阶段,顶枪吹入氧气、底枪吹入氮气和氩气,吹炼分为3
个阶段,每个阶段时间分别为20min、22min、19min;
112.吹炼1期末尾,进行出渣、然后加入石灰和铬球团,吨合金需要量分别为30kg、20kg;吹炼2期末尾,进行出渣,然后加入铬球团,吨合金需要量为49kg;
113.5)吹炼结束,停止吹氧,倾动转炉倒出铁水至预先装入硅铁的铁水包,倒铁水时间为5min。倾倒过程中,保持转炉氩气、氮气吹入。
114.6)铁水包底部通入氮气,包内物料上下翻腾,在氮气搅拌下混匀硅铁及铁水、炉渣,硅铁还原炉渣中氧化铬。
115.7)浇铸跨起重机吊运铁水包至浇铸区域,铁水包下方滑动水口打开,铁水沿着水口以及溜槽到达铸铁机、浇铸成型,中低碳铬铁成品粒度小于25cm。铁水浇铸完毕,关闭滑动水口。起重机吊运铁水包至扒渣区,倾倒炉渣。
116.8)步骤4)与步骤7)所获得炉渣经冷却、破碎后,用于步骤1)矿热炉冶炼高碳铬铁。
117.其中步骤3)吨合金耗氮量0.5nm3,耗氩气量为0.7nm3。
118.其中步骤3)~5)过程,各类气体压力为1.9mpa。
119.其中,步骤4)吹炼1期,吨合金耗氧量为25nm3,耗氮量为7nm3,耗氩气量为2.6nm3;吹炼2期,吨合金耗氧量为49nm3,耗氮量为4.0nm3,耗氩气量为4.0nm3;吹炼3期,吨合金耗氧量为25nm3,耗氮量为2.7nm3,耗氩气量为2.7nm3;
120.其中步骤1)高碳铬铁碳含量为6%,硅含量为3.2%;
121.其中步骤7)中低碳铬铁碳含量小于2%,硅含量小于2%;
122.其中步骤5)铁水包内硅铁量为吨合金消耗48kg。
123.其中步骤5)吨合金耗氮气量1.0nm3,耗氩气量为0.9nm3。
124.其中步骤6)氮气用量为吨合金消耗1.2nm3。
125.其中步骤7)铁水包与铸铁机接触位置上方,设置吸尘罩,处理浇铸产生的烟尘。
126.其中步骤1)铬粉矿粒度小于1mm,氧化铬含量大于40%,cr/fe大于1.5;碳质还原剂,粒度为8~40mm,碳含量大于82%;铬球团粒度为
127.其中步骤4)石灰粒度为10~70mm;
128.其中步骤5)硅铁粒度为10~50mm。
129.以上所述仅为本发明的优选实施例而已,并不用于限制本发明,对于本领域的技术人员来说,本发明可以有各种更改和变化。凡在本发明的精神和原则之内,所作的任何修改、等同替换、改进等,均应包含在本发明的保护范围之内。