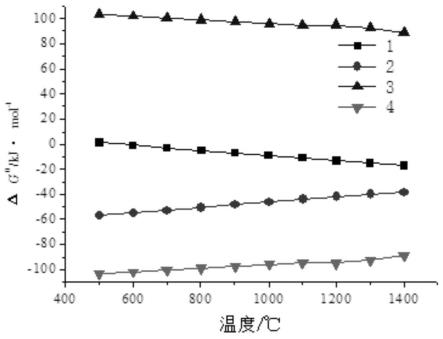
1.本发明涉及有色金属冶炼技术领域,具体而言,涉及一种阳极炉精炼阳极铜的方法。
背景技术:2.近年来,气候逐渐变暖,其主要原因是空气中温室气体——co2浓度越来越高,化石燃料的使用是co2排放的主要来源,且80%左右的能源供应来自于化石燃料。有色金属冶炼过程中使用一定量煤等化石燃料,会产生一定的co2,利用co2弱氧化性、搅拌性等功能在冶金方面进行重复应用可降低其排放量,提高其价值。
3.作为有色金属铜冶炼过程主要工序之一的铜阳极炉精炼,阳极炉铜精炼分氧化、还原两个阶段,氧化阶段主要将锌、铁、铅、铋、砷、硫、锑等杂质氧化进入渣中,在此过程中喷吹天然气和氧气,氧气部分用于粗铜中杂质氧化,部分用于与天然气燃烧供热,在氧化过程中部分铜进入精炼渣,精炼渣含铜达到40%,导致铜直收率低。氧化完成后,将氧化渣扒出,进入还原阶段,还原段依然喷吹天然气和富氧空气,通过调整氧气和天然气比例,使得天然气不完全燃烧,产生co和氢气,将粗铜中氧脱除。
技术实现要素:4.本发明的主要目的在于提供一种阳极炉精炼阳极铜的方法,以解决现有技术中铜直收率低、阳极铜中杂质含量高的问题。
5.为了实现上述目的,根据本发明的一个方面,提供了一种阳极炉精炼阳极铜的方法,该方法包括:将粗铜在阳极炉中进行氧化反应,氧化反应的过程中通入第一喷吹气体,得到铜液和精炼渣;将精炼渣进行还原反应,还原反应的过程中通入第二喷吹气体,得到阳极铜;其中,第一喷吹气体包括第一氧气、第一二氧化碳和第一天然气;第二喷吹气体包括第二氧气、第二二氧化碳和第二天然气。
6.进一步地,第一氧气和第一二氧化碳的总量与第一天然气的体积比为2.2~2.5:1;优选地,按体积份数计,以第一氧气和第一二氧化碳的总量为100份,其中,第一二氧化碳为5~12份,第一氧气为88~95份。
7.进一步地,第二氧气和第二二氧化碳的总量与第二天然气的体积比为1.6~1.8:1。
8.进一步地,按体积份数计,第二氧气和第二二氧化碳的总量为100份,其中,第二二氧化碳为5~12份,第二氧气为88~95份。
9.进一步地,第一二氧化碳和第二二氧化碳各自独立地选自烟气和/或石灰窑烟气。
10.进一步地,第一氧气和第二氧气各自独立地选自空气、富氧空气、工业氧气中的一种或多种。
11.进一步地,铜液中的氧质量含量为0.2%~0.5%。
12.进一步地,精炼渣含铜的质量含量为25%~40%。
13.进一步地,第一二氧化碳氧势低,以实现脱除杂质并避免铜进入精炼渣中。
14.进一步地,第二二氧化碳与第二天然气反应产生一氧化碳,一氧化碳和第二天然气同时作为还原剂,一氧化碳还用于提高铜液中氧的脱除效率。
15.应用本发明的技术方案,本技术在氧化和还原反应阶段采用co2代替部分氧气,利用co2的弱氧化性(氧势低)和对于铜的惰性(可以氧化金属铁、锌等,但无法氧化金属铜),可以降低精炼渣中的含铜量,保护喷枪,并增强熔池搅拌性能,同时实现co2的有效利用,提高co2的利用率,从而减少co2排放。
附图说明
16.构成本技术的一部分的说明书附图用来提供对本发明的进一步理解,本发明的示意性实施例及其说明用于解释本发明,并不构成对本发明的不当限定。在附图中:
17.图1示出了本发明一个实施例中co2发生的各反应的吉布斯自由能示意图。
具体实施方式
18.需要说明的是,在不冲突的情况下,本技术中的实施例及实施例中的特征可以相互组合。下面将参考附图并结合实施例来详细说明本发明。
19.如背景技术所分析的,现有技术中铜阳极炉精炼均采用氧气和天然气喷吹供热及氧化、还原。阳极炉铜精炼过程一般由透气砖喷吹氮气用于熔体搅拌,从而提高动力学条件;由喷枪喷吹富氧空气和天然气,从而用于氧化和还原。现有技术所采用的这种方法存在铜直收率低、阳极铜中杂质含量高问题。为了解决这一问题,本技术提供了一种阳极炉精炼阳极铜的方法。
20.在本技术一种典型的实施方式中,提供了一种阳极炉精炼阳极铜的方法,该方法包括:将粗铜在阳极炉中进行氧化反应,氧化反应的过程中通入第一喷吹气体,得到铜液和精炼渣;将精炼渣进行还原反应,还原反应的过程中通入第二喷吹气体,得到阳极铜;其中,第一喷吹气体包括第一氧气、第一二氧化碳和第一天然气;第二喷吹气体包括第二氧气、第二二氧化碳和第二天然气。
21.本技术在氧化和还原反应阶段采用co2代替部分氧气,利用co2的弱氧化性(氧势低)和对于铜的惰性(可以氧化金属铁、锌等,但无法氧化金属铜),可以降低精炼渣中的含铜量,保护喷枪,并增强熔池搅拌性能,同时实现co2的有效利用,提高co2的利用率,从而减少co2排放。
22.本技术co2代替部分氧气在熔池中发生反应主要如下:
23.co2+fe=co+feo(1)
24.co2+zn=co+zno(2)
25.co2+cu=co+cu2o(3)
26.co+cu2o=co2+2cu(4)
27.上述反应的吉布斯自由能示意图如图1所示。根据图1所示吉布斯自由能计算可知,在氧化反应中,第一co2通入粗铜中可氧化铁、锌等杂质,但不能氧化铜,因此在氧化阶段可利用部分第一co2代替氧气通入粗铜中,由于第一co2较氧气氧势低,在实现铁、锌等杂质脱除的同时,减少铜进入精炼渣中,降低精炼渣含铜量,从而提高铜直收率;同时较低氧
化阶段完成后,铜液中氧含量少,降低还原操作周期。
28.由上述反应式可以看出,在氧化阶段,利用第一co2代替部分氧气,具有以下优势:co2属于弱氧化性气体,可氧化粗铜中铁、锌,但无法氧化主元素——铜,减少铜进入精炼渣中,提高铜直收率。
29.在还原阶段,利用第二co2代替部分氧气,降低熔体氧势,有利于提高铜中氧的脱除率,同时第二co2与第二天然气反应产生co和氢气,具有以下优势:
①
属于吸热反应,可保护喷枪及周围耐材,减少喷枪烧损和耐材熔损;
②
第二co2反应产生co,co也可以用于还原反应,提高co2利用率、减少碳排放;
③
第二co2与天然气反应可较氧气直接反应多产生一倍的co,提高熔池搅拌性能;
④
提高铜液中氧的脱除效率。在还原段利用部分第二co2代替氧气,与第二天然气反应产生co和氢气,气量较大,在完成还原的同时,提高熔池搅拌效率。
30.本技术在阳极炉的液面以上设置烧嘴,烧嘴部分在氧化阶段喷吹第一氧气、第一天然气、第二氧气和第二天然气。在阳极炉液面以下的底部或侧部设置数根喷枪或透气砖,在氧化段的喷枪从阳极炉底部或侧部喷吹第一氧气(可以是空气、富氧空气等)和第一二氧化碳,在还原段的喷枪从阳极炉底部或侧部喷吹第二二氧化碳和第二天然气。优选地,第一喷吹气体和第二喷吹气体通过喷枪和/或透气砖进行喷吹。co2代替现有技术中常用的氧气从阳极炉炉体底部喷吹,可以增强熔体搅动,进一步改善动力学条件。
31.在氧化阶段,为了使co2与粗铜中的杂质充分反应进而脱除铁锌等杂质,在一些实施例中,优选第一氧气和第一二氧化碳的总量与第一天然气的体积比为2.2~2.5:1;例如一氧气和第一二氧化碳的总量与第一天然气的体积比为2.2:1、2.25:1、2.3:1、2.35:1、2.4:1、2.45:1、2.5:1。优选地,按体积份数计,以第一氧气和第一二氧化碳的总量为100份,其中,第一二氧化碳为5~12份,第一氧气为88~95份。由于co2本身不可燃,若co2含量过多,在氧化阶段难以燃烧,从而影响氧化反应的进行。氧化阶段中所用的第一氧气较第一天然气过量,可以在熔体中形成氧化性气氛,从而氧化粗铜中的铁、锌、铅、锑、铋、硫等杂质。
32.在还原阶段,为了降低粗铜中的氧含量并使铜氧化物充分还原,优选第二氧气和第二二氧化碳的总量与第二天然气的体积比为1.6~1.8:1;例如第二氧气和第二二氧化碳的总量与第二天然气的体积比为1.6:1、1.65:1、1.7:1、1.75:1、1.8:1。按体积份数计,第二氧气和第二二氧化碳的总量为100份,其中,第二二氧化碳为5~12份,第二氧气为88~95份。
33.在还原阶段,第二氧气与天然气体积比较氧化阶段减少,在熔体中形成还原性气氛,与熔体中氧反应,脱除熔体中氧,并形成阳极铜。第二co2与第二天然气反应为吸热反应,可以避免局部热量高从而保护喷枪和枪砖,同时,在还原反应阶段,利用第二co2与第二天然气反应产生更多的co和氢气,在脱除熔体中氧的同时,可以提高冶炼效率,还可以降低天然气使用量。
34.为了防止铜直收率低、阳极铜中杂质含量高等问题并避免co2含量过多影响氧化和还原工艺。本技术中第一天然气和第二天然气总喷吹量为15~30nm3/t.铜,其中第二天然气喷吹量为5~10nm3/t.铜;第一天然气喷吹量为10~20nm3/t.铜;第一氧气喷吹量为20~40nm3/t.铜。
35.本技术对喷吹气体中二氧化碳的来源没有特别的限制,阳极炉中的烟气可以直接利用,其他工业产生的co2,或者经过提纯处理获得的co2也可以用于本技术中。在一些实施
例中,第一二氧化碳和第二二氧化碳各自独立地来自烟气和/或石灰窑烟气。
36.本技术对喷吹气体中氧气的来源也没有特别的限制。在一些实施例中,第一氧气和第二氧气各自独立地来自空气、富氧空气(氧气体积含量为50~99%)、工业氧气中的一种或多种。本领域技术人员应当知晓,由于第一氧气和第二氧气来源于上述气体,因此在上述氧化反应和还原反应中不可避免还含有氮气,氮气不参与反应,可以起到保护透气砖的作用,从而提高透气砖的使用寿命。
37.在一些实施例中,本技术利用co2代替氧化反应和还原反应阶段的部分氧气,可以在氧化完成后降低铜液中的氧含量并降低精炼渣中的含铜量,铜液中的氧含量为0.2%~0.5%,精炼渣含铜的质量为25%~40%。
38.在一些实施例中,第一二氧化碳氧势低,以实现脱除杂质并避免铜进入精炼渣中。
39.在一些实施例中,第二二氧化碳与第二天然气反应产生一氧化碳,一氧化碳和第二天然气同时作为还原剂,一氧化碳还用于提高铜液中氧的脱除效率。
40.以下结合具体实施例对本技术作进一步详细描述,这些实施例不能理解为限制本技术所要求保护的范围。
41.对比例1
42.将粗铜在阳极炉中进行氧化反应,通过透气砖从阳极炉底部喷吹第一喷吹气体(第一工业氧气和第一天然气),第一工业氧气和第一天然气的体积比为2.3:1,得到铜液和精炼渣;将上述精炼渣进行还原反应,利用喷枪从阳极炉底部喷吹第二喷吹气体(第二工业氧气和第二天然气和氮气),第二工业氧气和第二天然气的体积比为1.7:1,得到阳极铜。第一天然气和第二天然气总喷吹量为20nm3/t.铜。上述精炼渣含铜量为40wt%,氧化阶段完成后铜液含氧量1.1wt%。
43.实施例1
44.与对比例1不同的是,第一喷吹气体中利用co2代替5wt%工业氧气,第二喷吹气体中利用co2代替5wt%o2,co2的使用可以代替透气砖喷吹用氮气,可减少氮气使用量,精炼渣含铜由仅使用工业氧气作为第一喷吹气体时(对比例1)的40wt%降至32wt%,氧化阶段完成后铜液含氧量0.4wt%;在还原段第二喷吹气体中利用co2代替,减少2wt%天然气使用,同时精炼时间缩短30min,且阳极铜质量良好,喷枪周围枪砖和喷枪寿命是原来的1.1倍。
45.实施例2
46.与对比例1不同的是,第一喷吹气体中利用co2代替8wt%工业氧气,第二喷吹气体中利用co2代替8wt%o2,co2的使用可以代替透气砖喷吹用氮气,可减少氮气使用量,氧化段渣含铜由仅使用工业氧气作为第一喷吹气体时的40wt%降至30wt%,氧化阶段完成后粗铜含氧量0.32wt%,如表1所示;在还原段第二喷吹气体中利用co2代替8wt%o2,减少3wt%天然气使用,同时精炼时间缩短31min,且阳极铜质量良好,喷枪周围枪砖和喷枪寿命是原来的1.15倍。
47.实施例3
48.与对比例1不同的是,第一喷吹气体中利用co2代替12wt%工业氧气,第二喷吹气体中利用co2代替12wt%o2,co2的使用可以代替透气砖喷吹用氮气,可减少氮气使用量,氧化段渣含铜由仅使用工业氧气作为第一喷吹气体时的40wt%降至29wt%,氧化阶段完成后铜液含氧量0.3wt%;在还原段第二喷吹气体利用co2代替12wt%o2,减少5wt%天然气使用,
同时精炼时间缩短35min,且阳极铜质量良好,喷枪周围枪砖和喷枪寿命是原来的1.25倍。
49.实施例4
50.与对比例1不同的是,第一喷吹气体采用3wt%co2代替o2。氧化段渣含铜量为39wt%,氧化阶段完成后铜液含氧量0.77wt%;还原阶段减少1wt%天然气使用,同时精炼时间缩短15min,且阳极铜质量良好,喷枪周围枪砖和喷枪寿命是原来的1.05倍。
51.实施例5
52.与实施例1不同的是,第一喷吹气体采用15wt%co2代替o2。氧化段渣含铜为28wt%,氧化阶段完成后铜液含氧量0.15wt%;在还原段减少1wt%天然气使用,同时精炼时间缩短20min,且阳极铜质量良好,喷枪周围枪砖和喷枪寿命是原来的1.3倍。
53.实施例6
54.与实施例1不同的是,第二喷吹气体采用3wt%co2代替o2。氧化段渣含铜为36wt%,氧化阶段完成后铜液含氧量0.58wt%;在还原段减少0.5wt%天然气使用,同时精炼时间缩短15min,且阳极铜质量良好,喷枪周围枪砖和喷枪寿命是原来的1.25倍。
55.实施例7
56.与实施例1不同的是,第二喷吹气体采用15wt%co2代替o2。氧化段渣含铜为36wt%,氧化阶段完成后铜液含氧量0.55wt%;在还原段减少1.5wt%天然气使用,同时精炼时间缩短15min,且阳极铜质量良好,喷枪周围枪砖和喷枪寿命是原来的1.25倍。
57.上述各实施例和对比例中的数据如表1所示。
58.表1
[0059][0060]
从以上的描述中,可以看出,本发明上述的实施例实现了如下技术效果:本技术在氧化和还原反应阶段采用co2代替部分氧气,利用co2的弱氧化性(氧势低)和对于铜的惰性(可以氧化金属铁、锌等,但无法氧化金属铜),可以降低精炼渣中的含铜量,保护喷枪,并增强熔池搅拌性能,同时实现co2的有效利用,提高co2的利用率,从而减少co2排放。
[0061]
以上所述仅为本发明的优选实施例而已,并不用于限制本发明,对于本领域的技术人员来说,本发明可以有各种更改和变化。凡在本发明的精神和原则之内,所作的任何修改、等同替换、改进等,均应包含在本发明的保护范围之内。