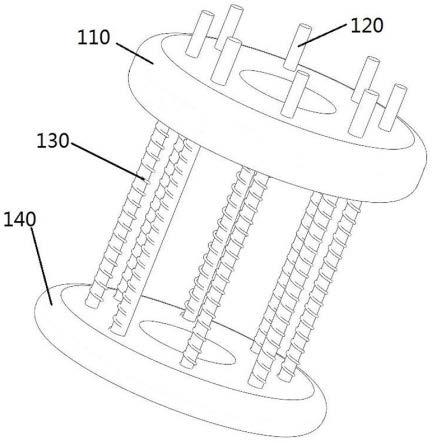
1.本发明属于铝合金低压铸造领域,具体涉及一种铝合金轮毂低压铸造模具的顶出机构。
背景技术:2.低压铸造:低压铸造是指铸型一般安置在密封的坩埚上方,坩埚中通入压缩空气,在熔融金属的表面上造成低压力(0.06~0.15mpa),使金属液由升液管上升填充铸型和控制凝固的铸造方法,这种铸造方法补缩好,铸件组织致密,容易铸造出大型薄壁复杂的铸件,无需冒口,金属收得率达95%,无污染,易实现自动化,但设备费用较高,生产效率较低,一般用于铸造有色合金。
3.铝合金材料因其密度小、比强度高、耐蚀性好等一系列优势,在航空航天、轨道交通、汽车工业等领域具有广泛的应用,随着我国社会的不断发展进步,节能减排这一理念已经被各行各业重视起来,而轻量化铝合金构件的应用范围逐渐扩大,汽车零部件的制造工艺中,压力铸造工艺凭借其生产效率高、零件尺寸精度高、综合性能好等特点,在汽车轮毂、转向节、控制臂、副车架等零部件的制造中得到广泛应用,压力铸造过程涉及的工序步骤、影响因素众多,造成其产品质量和生产效率有待进一步提高,如何快速高效、保质保量的对铸造零件进行生产已经成为相关领域追求的首要目标。
4.以铝合金轮毂低压铸造为例,铝液经过充型、加压补缩、保压凝固及泄压后需要将轮毂顶出脱模以便进行下一轮的铸造过程,目前铝合金轮毂的顶出机构多采用多根刚性顶杆,呈圆环分布;在脱模时,给多根顶杆同时施加载荷,使轮毂与凸模分离,然而,目前的顶出机构存在缺点,即刚性顶杆在承受较大载荷时容易发生弯曲变形,此时再进行轮毂脱模容易发生轴心偏载,即造成铸件表面划伤、变形甚至导致卡死无法脱模等问题,在发生上述问题时,会显著降低轮毂的表面质量和成品率,还有可能因为无法脱模引发异常停机,降低生产效率,因此,如何提供一种铝合金轮毂低压铸造模具的顶出机构是本领域技术人员亟需解决的问题。
技术实现要素:5.本发明的主要目的是提供一种铝合金轮毂低压铸造模具的顶出机构,以解决上述技术问题。该装置采用顶出块与轮毂接触,其作用面积增加,载荷分布也更加均匀,在保证其顶出效率的同时也可有效避免伤害轮毂表面质量;本发明通过压块作用碟簧,可将压力均匀的传递至顶出块,避免偏心加载的工况;并可实现载荷的线型加载控制,提升脱模效率。
6.为了达到上述目的,本发明采用下述技术方案:一种铝合金轮毂低压铸造模具的顶出机构,包括顶杆,压块,碟簧以及顶出块,所述顶出块顶端设置有顶杆,所述压块位于所述顶出块上方,所述顶杆顶端贯穿所述压块,所述顶杆位于所述顶出块与所述压块之间的部分套设有所述碟簧。
7.进一步的,所述顶出块的底端均匀分布有四个压力传感器。
8.进一步的,所述压块为中空的环状块。
9.进一步的,所述顶出块为中空的环状块。
10.与现有技术相比,本发明具有以下有益效果:本发明采用顶出块与轮毂接触,其作用面积增加,载荷分布也更加均匀,在保证其顶出效率的同时也可有效避免伤害轮毂表面质量;本发明通过压块作用碟簧,可将压力均匀的传递至顶出块,避免偏心加载的工况;并可实现载荷的线型加载控制,提升脱模效率;顶出块底部的压力传感器可以实时反馈顶出块与轮毂的接触载荷,当压力传感器之间的压力值相差较大时,则出现偏心加载工况,此时压块会退回至初始位置,重新进行加载,可保证轮毂的正常脱模。
附图说明
11.为了更清楚地说明本发明实施例或现有技术中的技术方案,下面将对实施例或现有技术描述中所需要使用的附图作简单地介绍,显而易见地,下面描述中的附图仅仅是本发明的实施例,对于本领域普通技术人员来讲,在不付出创造性劳动的前提下,还可以根据提供的附图获得其他的附图。
12.图1为本发明的结构示意图。
13.图2为本发明的底部结构示意图。
14.其中,110-压块,120-顶杆,130-碟簧,140-顶出块,150-压力传感器。
具体实施方式
15.下面将结合本发明实施例中的附图,对本发明实施例中的技术方案进行清楚、完整地描述,显然,所描述的实施例仅仅是本发明一部分实施例,而不是全部的实施例。基于本发明中的实施例,本领域普通技术人员在没有做出创造性劳动前提下所获得的所有其他实施例,都属于本发明保护的范围。
16.实施例1:如图1~2所示,本发明提供一种铝合金轮毂低压铸造模具的顶出机构,包括顶杆120,压块110,碟簧130以及顶出块140,所述顶出块140顶端设置有顶杆120,所述压块110位于所述顶出块140上方,所述顶杆120顶端贯穿所述压块110,所述顶杆120位于所述顶出块140与所述压块110之间的部分套设有所述碟簧130;通过压块110作用碟簧130,能够将压力均匀的传递至顶出块140,避免偏心加载,并且能够实现载荷的线型加载控制,提升脱模效率。
17.本实施例中,所述顶出块140的底端均匀分布有四个压力传感器150;压力传感器150可以实时反馈顶出块140与轮毂之间的接触载荷。
18.本实施例中,所述压块110为中空的环状块。
19.本实施例中,所述顶出块140为中空的环状块。
20.采用铝合金轮毂低压铸造模具的顶出机构实施轮毂脱模的步骤如下:当铝液晶粒充型、增压补缩、保压凝固和泄压处理后,模具开模,顶模带着轮毂与边模和底模分开,此时开始运行模具顶出机构使轮毂与凸模分离。
21.步骤一:开始对压块110施加载荷,使碟簧130受压力收缩;步骤二:继续稳步推进增大对压块110的载荷,顶出块140受压力作用开始与轮毂接触并将压力传递至轮毂上表面;步骤三:当压力超过轮毂脱模力时,轮毂开始松动,脱模开始;步骤四:轮毂完全与凸模分离,脱模完成,卸载,顶出机构复位。
22.实施例2:a356铝合金轮毂低压铸造脱模步骤一:当a356铝合金轮毂泄压结束后,开始对压块110施加载荷,使碟簧130受压力收缩,通过压力传感器150控制其进给位移;步骤二:继续稳步推进增大对压块110的载荷,顶出块140与轮毂接触后,其底部的压力传感器150开始记录载荷;步骤三:当顶出块140载荷达到最大值后开始减小,此时轮毂开始与凸模分离,压力进给量开始减小;步骤四:当顶出块140载荷减小至100n以下时,此时认为轮毂完全脱模,减小压块110载荷,使压块机顶出块140返回至顶杆120恢复正常长度时的最底端。
23.表1不同顶出机构脱模效率对比机构顶出时间表面划伤概率停机概率传统顶出机构15s23%7%本发明中的顶出块机构6s4%0%如表1不同顶出机构脱模效率对比中所示,传统顶出机构的顶出时间为15s,本发明中的顶出块机构顶出时间为6s,本发明中的顶出块机构要比传统顶出机构的顶出时间快9秒,本发明中的顶出块机构的顶出效率要更高;传统顶出机构对铸件表面划伤的概率为23%,本发明中的顶出块机构对铸件表面划伤的概率为4%,本发明中的顶出块机构对铸件表面划伤的概率更小,更不容易划伤铸件,能够显著的提升铸件的表面质量;传统顶出机构的停机概率为7%,本发明中的顶出块机构的停机概率为0%,本发明中的顶出块机构不可能停机,因此本发明中的顶出块机构相对于传统顶出机构能够更好的保证铸件的产出效率,并保证铸件的表面质量。
24.本说明书中各个实施例采用递进的方式描述,每个实施例重点说明的都是与其他实施例的不同之处,各个实施例之间相同相似部分互相参见即可。对于实施例公开的装置而言,由于其与实施例公开的方法相对应,所以描述的比较简单,相关之处参见方法部分说明即可。
25.对所公开的实施例的上述说明,使本领域专业技术人员能够实现或使用本发明。对这些实施例的多种修改对本领域的专业技术人员来说将是显而易见的,本文中所定义的一般原理可以在不脱离本发明的精神或范围的情况下,在其它实施例中实现。因此,本发明将不会被限制于本文所示的这些实施例,而是要符合与本文所公开的原理和新颖特点相一致的最宽的范围。