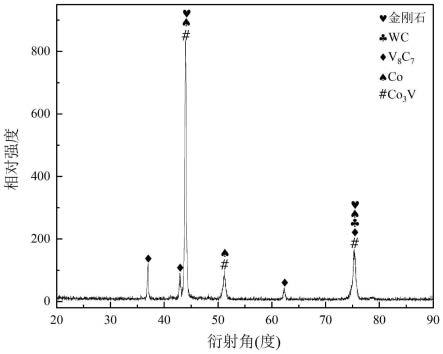
1.本发明属于材料科学领域,具体涉及一种钒增强聚晶金刚石复合片及其制备方法。
背景技术:2.聚晶金刚石复合片(polycrystalline diamond compact,简称pdc)是由金刚石微粉在高温高压下烧结在硬质合金衬底上而形成的一种兼具聚晶金刚石的高导热、高硬度,硬质合金的高韧性、易焊接的复合材料,被广泛应用于刀具、地质勘探钻头及油气井钻头等领域。虽然pdc在软到中硬的、比较均质的地层中具有钻速快、寿命长等明显的优势,但在坚硬、强研磨性和软硬交错等非均质地层中其钻进效果并不理想。
3.目前市面上流通的pdc多数是由高温高压烧结过程中硬质合金衬底中向金刚石层扫越的钴作为粘结剂的钴基聚晶金刚石复合片,但钴基聚晶金刚石容易在高温下石墨化或氧化,同时由于钴和金刚石的热膨胀系数差距较大,在高温下容易导致pdc失效。
技术实现要素:4.针对以上问题,本发明的目的是提供一种钒增强聚晶金刚石复合片及其制备方法,采用金刚石微粉为主材料,添加难熔金属钒粉,利用六面顶压机高温高压合成兼具耐热性、耐磨性、抗冲击韧性,用于油气钻井领域的聚晶金刚石复合片。
5.本发明为实现上述目的所采用的技术方案是:
6.本发明一方面提出了一种钒增强聚晶金刚石复合片,该钒增强聚晶金刚石复合片由聚晶金刚石层和硬质合金衬底烧结而成,所述聚晶金刚石层是由下述重量百分比的原料制备的:97wt%~99.7wt%的金刚石微粉和0.3wt%~3wt%的钒粉;所述硬质合金衬底采用wc-co硬质合金。
7.进一步,所述wc-co硬质合金衬底的钴含量为11%~16%,直径为8mm~19mm,厚度为8mm~16mm。
8.进一步,所述金刚石微粉由粒径为12μm~22μm和粒径为1μm~3μm两种粒径的金刚石颗粒组成,且粒径为12μm~22μm的金刚石颗粒和粒径为1μm~3μm的金刚石颗粒的重量百分比为9:1,以保证最密堆积密度。
9.进一步,所述钒粉的粒径小于5μm。
10.本发明另一方面提出了一种制备所述钒增强聚晶金刚石复合片的方法,包括以下步骤,且下述步骤顺序进行:
11.步骤1、原料准备:
12.对硬质合金衬底进行处理,去除硬质合金衬底表面杂质,备用;
13.按照重量百分比为金刚石微粉97wt%~99.7wt%和钒粉0.3wt%~3wt%,分别称量金刚石微粉和钒粉,放入行星式球磨机中,以10:1的球料比均匀混合后过200目筛,分离研磨球与混合粉末,将混合粉末装入内钽杯中,将所述硬质合金衬底放置在混合粉末上方,
并在硬质合金衬底上扣外钽杯,在液压机上以3mpa的压力预压后,置于真空炉内以700℃进行热处理2h,得到内组装块;
14.步骤2、将内组装块置于盐管中,利用氧化镁包裹盐管,然后再与石墨管、叶蜡石组装成块,得到外组装块,将外组装块置于六面顶压机中,经高温高压烧结,得到金刚石复合片毛坯;
15.其中,高温高压烧结时,以2gpa/min的速率升压至8gpa,以30℃/s的速率升温至1600℃~1800℃,保温240s,以30℃/s的速率降温至室温,然后以1gpa/min的速率卸压至常压:
16.步骤3、将步骤2中得到的金刚石复合片毛坯经过喷砂处理后,送入马弗炉中,然后在650℃退火1h,得到所述钒增强聚晶金刚石复合片。
17.进一步,所述步骤1中,对硬质合金衬底进行处理,去除硬质合金衬底表面杂质的过程如下:将硬质合金衬底加工到设计尺寸后,采用金刚砂进行喷砂处理,直至露出新鲜的表面后,置于无水乙醇中超声处理30min,去除表面残留的杂质。
18.进一步,所述步骤1中,所述wc-co硬质合金的钴含量为11%~16%,直径为8mm~19mm,厚度为8mm~16mm。
19.进一步,所述步骤1中,所述金刚石微粉由粒径为12μm~22μm和粒径为1μm~3μm两种粒径的金刚石颗粒组成,且粒径为12μm~22μm的金刚石颗粒和粒径为1μm~3μm的金刚石颗粒的重量百分比为9:1,以保证最密堆积密度。
20.进一步,所述步骤1中,所述钒粉的粒径小于5μm。
21.进一步,所述步骤1中,球磨时无液相,为干式球磨,采用直径为6mm和3mm的硬质合金球,按照1:1的重量比混合构成研磨球,球磨罐为硬质合金罐,球磨机转速为450rpm,球磨时间为正转20min,反转20min。
22.通过上述设计方案,本发明可以带来如下有益效果:
23.本发明提出的钒增强聚晶金刚石复合片,由金刚石微粉和钒粉构成的混合粉末为原料,利用传统的六面顶压机,在8gpa高压下,1600℃~1800℃温度下与wc-co硬质合金衬底烧结而成。本发明所选择的金刚石微粉的主粒径为12μm~22μm,副粒径为1μm~3μm。经本发明制得的油气钻井钻头用钒增强聚晶金刚石复合片,同时具有高耐磨性、高抗冲击韧性和高耐热性。
24.采用本发明的工艺,省去金刚石微粉净化处理步骤,节约时间与人工成本,同时避免净化处理用到的酸、碱造成的环境污染问题。
25.通过大量的实验证明,本发明提出的钒增强聚晶金刚石复合片,钒的加量小于0.3wt%时,耐磨性、抗冲击韧性有提升,但均小于10%,热膨胀临界温度提升小于5℃。钒的加量大于3wt%时,会极大的影响成片率。本发明对温度的要求也更加严格,低于1600℃时,钴在金刚石层中的扫越不充分,导致复合片不成形;高于1800℃时,钴扫越过多,在界面处堆积导致分层。为了避免金属钒过早的与金刚石微粉发生反应,本发明采用700℃温度对内组装块进行热处理,不同于常规使用的850℃,本工艺节约能量的同时,又可以获得性能更好的产品。
附图说明
26.此处所说明的附图用来提供对本发明的进一步理解,构成本技术的一部分,本发明示意性实施例及其说明用于理解本发明,并不构成本发明的不当限定,在附图中:
27.图1为本发明实施例1中pdc的聚晶金刚石层的x射线衍射图;
28.图2为本发明实施例2中钒增强聚晶金刚石复合片的聚晶金刚石层的x射线衍射图;
29.图3为本发明实施例3中钒增强聚晶金刚石复合片的聚晶金刚石层的x射线衍射图;
30.图4为本发明实施例4中钒增强聚晶金刚石复合片的聚晶金刚石层的x射线衍射图;
31.图5为本发明实施例5中钒增强聚晶金刚石复合片的聚晶金刚石层的x射线衍射图;
32.图6为本发明实施例6中钒增强聚晶金刚石复合片的聚晶金刚石层的x射线衍射图;
33.图7为本发明实施例7中钒增强聚晶金刚石复合片的聚晶金刚石层的x射线衍射图。
具体实施方式
34.为了更清楚地说明本发明,下面结合优选实施例和附图对本发明做进一步的说明。本领域技术人员应当理解,下面所具体描述的内容是说明性的而非限制性的,不应以此限制本发明的保护范围。除非另作定义,此处使用的技术术语或者科学术语应当为本发明所属领域内具有一般技能的人士所理解的通常意义。
35.为了避免混淆本发明的实质,公知的方法、过程、流程、元件和电路并没有详细叙述。
36.需要说明的是,实施例1-7中,所述硬质合金衬底采用wc-co硬质合金。进一步,所述wc-co硬质合金的钴含量为11%~16%,直径为8mm~19mm,厚度为8mm~16mm。
37.实施例1(对照组)
38.本实例中一种聚晶金刚石复合片的制备方法,具体步骤如下:
39.步骤1、原料准备:
40.①
将硬质合金衬底加工到18mm直径、15mm高的毛坯体后,采用金刚砂进行喷砂处理,直至露出新鲜的表面后,置于无水乙醇中超声处理30min,去除表面残留的杂质,备用;
41.②
按照90wt%粒径12μm~22μm的金刚石颗粒和10wt%粒径1μm~3μm的金刚石颗粒的重量百分比称量,在行星式球磨机中,采用干式球磨的方法,利用直径为6mm和3mm的硬质合金球,按照1:1的重量比混合构成研磨球,以10:1的球料比,在450rpm的转速下,正转20min,反转20min,均匀混合后过200目筛,分离研磨球与混合粉末,将混合粉末装入内钽杯中,将所述硬质合金衬底放置在混合粉末上方,并在硬质合金衬底上扣外钽杯,在液压机上以3mpa的压力预压后,置于真空炉内以700℃进行热处理2h,得到内组装块;
42.步骤2、将内组装块置于盐管中,利用氧化镁包裹盐管,然后再与石墨管、叶蜡石组装成块,得到外组装块,将外组装块置于六面顶压机中,以2gpa/min的速率升压至8gpa,以
30℃/s的速率升温至1800℃,保温240s,以30℃/s的速率降温至室温,然后以1gpa/min的速率卸压至常压,完成高温高压烧结,得到金刚石复合片毛坯;
43.步骤3、将步骤2中得到的金刚石复合片毛坯经过喷砂处理后,送入马弗炉中,然后于650℃退火1h,研磨聚晶金刚石层表面,加工外圆尺寸至16mm,聚晶金刚石层厚度研磨至2.2mm~2.4mm,硬质合金衬底底面机加工至金刚石复合片高度为13mm,机加工聚晶金刚石层倒角、硬质合金衬底倒角,其尺寸皆为0.38mm/45
°
,抛光pdc的外圆、底面,进行一系列上述流程后,得到聚晶金刚石复合片。
44.检测本实例中制备的所述聚晶金刚石复合片性能指标:立式车床磨耗比111万,抗冲击韧性1680j,聚晶金刚石层热膨胀临界温度842℃。图1示出了本实施例的pdc的聚晶金刚石层的x射线衍射图。
45.实施例2
46.本实例中一种钒增强聚晶金刚石复合片的制备方法,具体步骤如下:
47.步骤1、原料准备:
48.①
将硬质合金衬底加工到18mm直径、15mm高的毛坯体后,采用金刚砂进行喷砂处理,直至露出新鲜的表面后,置于无水乙醇中超声处理30min,去除表面残留的杂质,备用;
49.②
按照89.73wt%粒径12μm~22μm的金刚石颗粒、9.97wt%粒径1μm~3μm的金刚石颗粒和0.3wt%钒粉的重量百分比称量,在行星式球磨机中,采用干式球磨的方法,利用直径为6mm和3mm的硬质合金球,按照1:1的重量比混合构成研磨球,以10:1的球料比,在450rpm的转速下,正转20min,反转20min,均匀混合后过200目筛,分离研磨球与混合粉末,将混合粉末装入内钽杯中,将所述硬质合金衬底放置在混合粉末上方,并在硬质合金衬底上扣外钽杯,在液压机上以3mpa的压力预压后,置于真空炉内以700℃进行热处理2h,得到内组装块;
50.步骤2、将内组装块置于盐管中,利用氧化镁包裹盐管,然后再与石墨管、叶蜡石组装成块,得到外组装块,将外组装块置于六面顶压机中,以2gpa/min的速率升压至8gpa,以30℃/s的速率升温至1800℃,保温240s,以30℃/s的速率降温至室温,然后以1gpa/min的速率卸压至常压,完成高温高压烧结,得到金刚石复合片毛坯;
51.步骤3、将步骤2中得到的金刚石复合片毛坯经过喷砂处理后,送入马弗炉中,然后于650℃退火1h,研磨聚晶金刚石层表面,加工外圆尺寸至16mm,聚晶金刚石层厚度研磨至2.2mm~2.4mm,硬质合金衬底底面机加工至金刚石复合片高度为13mm,机加工聚晶金刚石层倒角、硬质合金衬底倒角,其尺寸皆为0.38mm/45
°
,抛光pdc的外圆、底面,进行一系列上述流程后,得到钒增强聚晶金刚石复合片。
52.检测本实例中制备的所述钒增强聚晶金刚石复合片性能指标:立式车床磨耗比159万、抗冲击韧性3420j、聚晶金刚石层热膨胀临界温度859℃,相比与对照组分别提升了43.2%、104%、17℃。
53.实施例3
54.本实例中一种钒增强聚晶金刚石复合片的制备方法,具体步骤如下:
55.步骤1、原料准备:
56.①
将硬质合金衬底加工到18mm直径、15mm高的毛坯体后,采用金刚砂进行喷砂处理,直至露出新鲜的表面后,置于无水乙醇中超声处理30min,去除表面残留的杂质,备用;
57.②
按照89.46wt%粒径12μm~22μm的金刚石颗粒、9.94wt%粒径1μm~3μm的金刚石颗粒和0.6wt%钒粉的重量百分比称量,在行星式球磨机中,采用干式球磨的方法,利用直径为6mm和3mm的硬质合金球,按照1:1的重量比混合构成研磨球,以10:1的球料比,在450rpm的转速下,正转20min,反转20min,均匀混合后过200目筛,分离研磨球与混合粉末,将混合粉末装入内钽杯中,将所述硬质合金衬底放置在混合粉末上方,并在硬质合金衬底上扣外钽杯,在液压机上以3mpa的压力预压后,置于真空炉内以700℃进行热处理2h,得到内组装块;
58.步骤2、将内组装块置于盐管中,利用氧化镁包裹盐管,然后再与石墨管、叶蜡石组装成块,得到外组装块,将外组装块置于六面顶压机中,以2gpa/min的速率升压至8gpa,以30℃/s的速率升温至1600℃,保温240s,以30℃/s的速率降温至室温,然后以1gpa/min的速率卸压至常压,完成高温高压烧结,得到金刚石复合片毛坯;
59.步骤3、将步骤2中得到的金刚石复合片毛坯经过喷砂处理后,送入马弗炉中,然后于650℃退火1h,研磨聚晶金刚石层表面,加工外圆尺寸至16mm,聚晶金刚石层厚度研磨至2.2mm~2.4mm,硬质合金衬底底面机加工至金刚石复合片高度为13mm,机加工聚晶金刚石层倒角、硬质合金衬底倒角,其尺寸皆为0.38mm/45
°
,抛光pdc的外圆、底面,进行一系列上述流程后,得到钒增强聚晶金刚石复合片。
60.检测本实例中制备的所述钒增强聚晶金刚石复合片性能指标:立式车床磨耗比175万、抗冲击韧性4570j、聚晶金刚石层热膨胀临界温度865℃,相比与对照组分别提升了57.7%、172%、23℃。
61.实施例4
62.本实例中一种钒增强聚晶金刚石复合片的制备方法,具体步骤如下:
63.步骤1、原料准备:
64.①
将硬质合金衬底加工到18mm直径、15mm高的毛坯体后,采用金刚砂进行喷砂处理,直至露出新鲜的表面后,置于无水乙醇中超声处理30min,去除表面残留的杂质,备用;
65.②
按照89.19wt%粒径12μm~22μm的金刚石颗粒、9.91wt%粒径1μm~3μm的金刚石颗粒和0.9wt%钒粉的重量百分比称量,在行星式球磨机中,采用干式球磨的方法,利用直径为6mm和3mm的硬质合金球,按照1:1的重量比混合构成研磨球,以10:1的球料比,分离研磨球与混合粉末,将混合粉末装入内钽杯中,将所述硬质合金衬底放置在混合粉末上方,并在硬质合金衬底上扣外钽杯,在液压机上以3mpa的压力预压后,置于真空炉内以700℃进行热处理2h,得到内组装块;
66.步骤2、将内组装块置于盐管中,利用氧化镁包裹盐管,然后再与石墨管、叶蜡石组装成块,得到外组装块,将外组装块置于六面顶压机中,以2gpa/min的速率升压至8gpa,以30℃/s的速率升温至1700℃,保温240s,以30℃/s的速率降温至室温,然后以1gpa/min的速率卸压至常压,完成高温高压烧结,得到金刚石复合片毛坯;
67.步骤3、将步骤2中得到的金刚石复合片毛坯经过喷砂处理后,送入马弗炉中,然后于650℃退火1h,研磨聚晶金刚石层表面,加工外圆尺寸至16mm,聚晶金刚石层厚度研磨至2.2mm~2.4mm,硬质合金衬底底面机加工至金刚石复合片高度为13mm,机加工聚晶金刚石层倒角、硬质合金衬底倒角,其尺寸皆为0.38mm/45
°
,抛光pdc的外圆、底面,进行一系列上述流程后,得到钒增强聚晶金刚石复合片。
68.检测本实例中制备的所述钒增强聚晶金刚石复合片性能指标:立式车床磨耗比186.6万、抗冲击韧性4990j、聚晶金刚石层热膨胀临界温度868℃,相比与对照组分别提升了68.1%、197%、26℃。
69.实施例5
70.本实例中一种钒增强聚晶金刚石复合片的制备方法,具体步骤如下:
71.步骤1、原料准备:
72.①
将硬质合金衬底加工到18mm直径、15mm高的毛坯体后,采用金刚砂进行喷砂处理,直至露出新鲜的表面后,置于无水乙醇中超声处理30min,去除表面残留的杂质,备用;
73.②
按照89.1wt%粒径12μm~22μm的金刚石颗粒、9.9wt%粒径1μm~3μm的金刚石颗粒和1wt%钒粉的重量百分比称量,在行星式球磨机中,采用干式球磨的方法,利用直径为6mm和3mm的硬质合金球,按照1:1的重量比混合构成研磨球,以10:1的球料比,分离研磨球与混合粉末,将混合粉末装入内钽杯中,将所述硬质合金衬底放置在混合粉末上方,并在硬质合金衬底上扣外钽杯,在液压机上以3mpa的压力预压后,置于真空炉内以700℃进行热处理2h,得到内组装块;
74.步骤2、将内组装块置于盐管中,利用氧化镁包裹盐管,然后再与石墨管、叶蜡石组装成块,得到外组装块,将外组装块置于六面顶压机中,以2gpa/min的速率升压至8gpa,以30℃/s的速率升温至1700℃,保温240s,以30℃/s的速率降温至室温,然后以1gpa/min的速率卸压至常压,完成高温高压烧结,得到金刚石复合片毛坯;
75.步骤3、将步骤2中得到的金刚石复合片毛坯经过喷砂处理后,送入马弗炉中,然后于650℃退火1h,研磨聚晶金刚石层表面,加工外圆尺寸至16mm,聚晶金刚石层厚度研磨至2.2mm~2.4mm,硬质合金衬底底面机加工至金刚石复合片高度为13mm,机加工聚晶金刚石层倒角、硬质合金衬底倒角,其尺寸皆为0.38mm/45
°
,抛光pdc的外圆、底面,进行一系列上述流程后,得到钒增强聚晶金刚石复合片。
76.检测本实例中制备的所述钒增强聚晶金刚石复合片性能指标:立式车床磨耗比187万、抗冲击韧性5270j、聚晶金刚石层热膨胀临界温度870℃,相比与对照组分别提升了68.5%、214%、28℃。
77.实施例6
78.本实例中一种钒增强聚晶金刚石复合片的制备方法,具体步骤如下:
79.步骤1、原料准备:
80.①
将硬质合金衬底加工到18mm直径、15mm高的毛坯体后,采用金刚砂进行喷砂处理,直至露出新鲜的表面后,置于无水乙醇中超声处理30min,去除表面残留的杂质,备用;
81.②
按照88.2wt%粒径12μm~22μm的金刚石颗粒、9.8wt%粒径1μm~3μm的金刚石颗粒和2wt%钒粉的重量百分比称量,在行星式球磨机中,采用干式球磨的方法,利用直径为6mm和3mm的硬质合金球,按照1:1的重量比混合构成研磨球,以10:1的球料比,分离研磨球与混合粉末,将混合粉末装入内钽杯中,将所述硬质合金衬底放置在混合粉末上方,并在硬质合金衬底上扣外钽杯,在液压机上以3mpa的压力预压后,置于真空炉内以700℃进行热处理2h,得到内组装块;
82.步骤2、将内组装块置于盐管中,利用氧化镁包裹盐管,然后再与石墨管、叶蜡石组装成块,得到外组装块,将外组装块置于六面顶压机中,以2gpa/min的速率升压至8gpa,以
30℃/s的速率升温至1700℃,保温240s,以30℃/s的速率降温至室温,然后以1gpa/min的速率卸压至常压,完成高温高压烧结,得到金刚石复合片毛坯;
83.步骤3、将步骤2中得到的金刚石复合片毛坯经过喷砂处理后,送入马弗炉中,然后于650℃退火1h,研磨聚晶金刚石层表面,加工外圆尺寸至16mm,聚晶金刚石层厚度研磨至2.2mm~2.4mm,硬质合金衬底底面机加工至金刚石复合片高度为13mm,机加工聚晶金刚石层倒角、硬质合金衬底倒角,其尺寸皆为0.38mm/45
°
,抛光pdc的外圆、底面,进行一系列上述流程后,得到钒增强聚晶金刚石复合片。
84.检测本实例中制备的所述钒增强聚晶金刚石复合片性能指标:立式车床磨耗比168万、抗冲击韧性4850j、聚晶金刚石层热膨胀临界温度876℃,相比与对照组分别提升了51.4%、189%、34℃。
85.实施例7
86.本实例中一种钒增强聚晶金刚石复合片的制备方法,具体步骤如下:
87.步骤1、原料准备:
88.①
将硬质合金衬底加工到18mm直径、15mm高的毛坯体后,采用金刚砂进行喷砂处理,直至露出新鲜的表面后,置于无水乙醇中超声处理30min,去除表面残留的杂质,备用;
89.②
按照87.3wt%粒径12μm~22μm的金刚石颗粒、9.7wt%粒径1μm~3μm的金刚石颗粒和3wt%钒粉的重量百分比称量,在行星式球磨机中,采用干式球磨的方法,利用直径为6mm和3mm的硬质合金球,按照1:1的重量比混合构成研磨球,以10:1的球料比,在450rpm的转速下,正转20min,反转20min,均匀混合后过200目筛,分离研磨球与混合粉末,将混合粉末装入内钽杯中,将所述硬质合金衬底放置在混合粉末上方,并在硬质合金衬底上扣外钽杯,在液压机上以3mpa的压力预压后,置于真空炉内以700℃进行热处理2h,得到内组装块;
90.步骤2、将内组装块置于盐管中,利用氧化镁包裹盐管,然后再与石墨管、叶蜡石组装成块,得到外组装块,将外组装块置于六面顶压机中,以2gpa/min的速率升压至8gpa,以30℃/s的速率升温至1800℃,保温240s,以30℃/s的速率降温至室温,然后以1gpa/min的速率卸压至常压,完成高温高压烧结,得到金刚石复合片毛坯;
91.步骤3、将步骤2中得到的金刚石复合片毛坯经过喷砂处理后,送入马弗炉中,然后于650℃退火1h,研磨聚晶金刚石层表面,加工外圆尺寸至16mm,聚晶金刚石层厚度研磨至2.2mm~2.4mm,硬质合金衬底底面机加工至金刚石复合片高度为13mm,机加工聚晶金刚石层倒角、硬质合金衬底倒角,其尺寸皆为0.38mm/45
°
,抛光pdc的外圆、底面,进行一系列上述流程后,得到钒增强聚晶金刚石复合片。
92.检测本实例中制备的所述钒粉增强聚晶金刚石复合片性能指标:立式车床磨耗比157万、抗冲击韧性2760j、聚晶金刚石层热膨胀临界温度887℃,相比与对照组分别提升了41.4%、64%、45℃。
93.上述实施例1制备的聚晶金刚石复合片以及实施例2-7所制备得到的钒增强聚晶金刚石复合片是在同等测试条件下进行的耐磨性、抗冲击韧性、热膨胀系数测定,测定方法均采用国内复合片厂家常规测试手段,采用立式花岗岩车床进行耐磨性测试,岩石吃入深度为0.25mm。采用落锤冲击装置进行抗冲击测试,测试角度与耐磨性测试相同均为15
°
,单次冲击功60j,直至试样破碎。采用热膨胀系数测试仪进行热膨胀系数测定,设定条件为空
气加热,起始温度为30℃,升温速率为5.4℃/min,升温至1000℃。
94.本发明提出的钒增强聚晶金刚石复合片的性能强化原理如下:
95.钒在高温高压下与金刚石原位生成v8c7并与wc-co基硬质合金衬底中扫越的co生成co3v两种增强相,见图2至图7中关于实施例2-7的钒增强聚晶金刚石复合片的聚晶金刚石层的x射线衍射图。v8c7是材料领域常用的增强相,但co3v在材料领域中对耐磨性、抗冲击韧性、耐热性的强化作用未见报道。本发明的实施例2-7表明,通过添加钒,复合片的耐磨性、抗冲击韧性、耐热性都会得到显著提升,见表1中示出的实施例1-7力学性能对比。
96.表1实施例1-7力学性能对比
[0097][0098]
以上所述,仅是本发明的较佳实施示例而已,并非对本发明作任何形式上的限制。任何熟悉本领域的技术人员,在不脱离本发明技术方案范围情况下,都可利用上述揭示的方法和技术内容对本发明技术方案做出许多可能的变动和修饰,或修改为等同变化的等效实施示例。因此,凡是未脱离本发明技术方案的内容,依据本发明的技术实质对以上实施示例所做的任何简单修改、等同变化及修饰,均仍属于本发明技术方案保护的范围内。