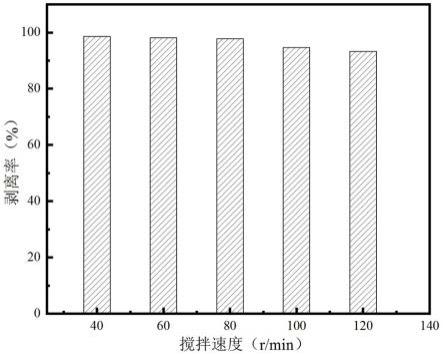
1.本技术涉及锂离子正极片回收技术领域,特别是涉及一种用于废旧锂离子电池正极片回收的低共熔溶剂及其应用。
背景技术:2.随着锂离子动力电池需求量和产量的增加,报废的锂离子电池将会呈井喷式增长。预计2025年,动力电池报废量将会达到110 gwh,市场规模将超过200亿元。废旧锂电池中的有价金属具有巨大的社会经济价值,废旧三元正极粉料中含li 5%~7%、ni 5%~12%、co 5%~20%、mn 7%~10%,这远远高于开采矿石中有价金属的品位。废旧锂电池处理不当,不仅会造成有机物、粉尘以及重金属污染,还会造成资源浪费。因此,建立有效的锂离子电池回收策略可以减小废旧电池的环境影响并降低电池供应链对原材料的依赖,同时最大限度地减少废旧电池对人类健康和自然环境的影响,促进锂离子电池产业的健康可持续发展。
3.目前,对于废旧锂离子电池正极材料,即铝箔、粘结剂和正极活性粉末组成的正极材料,或称锂离子正极片,其回收处理主要有两种工艺。第一种工艺是通过物理或化学方法剥离正极材料获取正极活性粉末,再通过高温火法工艺或强酸湿法工艺回收正极活性粉末得到镍、钴、锰的金属粉,或金属氧化物,或金属盐等产品;该工艺多为实验室工艺探究。第二种工艺是直接粉碎正极材料得到混合有铝箔的黑粉,再通过火法工艺或湿法工艺回收废电池中的金属元素得到铝粉,镍、钴、锰的金属粉,或金属氧化物,或金属盐等产品;该工艺中需要联用萃取剂的工艺方法,并结合各种沉淀剂对溶液的金属进行多次分离和纯化。显然,第一种工艺虽然能得到纯度较高的产品但是效率太低,物理方法剥离正极材料效率过低不适用于大规模工业化应用;化学方法剥离需要用到有机溶剂等额外的化学物质对环境有一定危害。第二种工艺复杂,流程冗长,成本高。
4.低共熔溶剂(des)是由氢键供体(hbd)和氢键受体(hba)构成的有机溶剂,具有还原能力和高溶解能力的绿色溶剂,可以应用于废旧电池中回收有价金属,同时,低共熔溶剂作为碳源对再生的正极材料进行包覆,改善材料电导率和锂离子扩散速率,提高正极材料的充放电容量。此外,使用低共熔溶剂可以有效规避传统火法工艺中的高耗能,高污染和传统湿法工艺存在腐蚀性酸/碱性溶液等有害化学物质的高消耗、昂贵的萃取剂、产生二次废酸和高浓度盐溶液等问题。
5.低共熔溶剂回收废旧锂电池正极材料的原理如下:组成低共熔溶剂的氢键供体和受体,两者以一定比例混合后,由于氢键供体和受体间体会形成大量氢键,分子间作用力变弱,形成了低共熔溶剂,这种液体溶剂更有利于固-液相发生传质,低共熔溶剂形成过程可以表示为:氢键受体+氢键供体
→
阳离子+阴离子+氢键供体。研究表明,低共熔溶剂具有金属的溶解能力,溶解后的金属元素与低共熔溶剂以配合物的形式存在。其与金属的反应过程可表示为:阳离子+阴离子+氢键供体+金属元素
↔
阳离子+金属配合物。
6.现有的低共熔溶剂普遍存在金属元素的浸取效率低,无法完全浸取废旧正极材料等缺陷。因此,如何提高低共熔溶剂的浸取效率低,是低共熔溶剂回收废旧锂离子正极片技
术领域的研究重点和难点。
技术实现要素:7.本技术的目的是提供一种改进的用于废旧锂离子电池正极片回收的低共熔溶剂及其应用。
8.本技术采用了以下技术方案:本技术的一方面公开了一种用于废旧锂离子电池正极片回收的低共熔溶剂,由氢键受体、氢键供体和助剂组成;其中,氢键受体为氯化胆碱,氢键供体为尿素、氨基磺酸、乙酰胺、聚乙二醇和甲基脲中的至少两种,助剂为抗坏血酸、乙醛和葡萄糖中的至少一种。
9.需要说明的是,本技术的低共熔溶剂包含氯化胆碱和至少两种氢键供体,由此构建的多元低共熔溶剂能够有效的降低溶剂熔点,本技术的一种实现方式中,只需要在80℃加热搅拌即可制备获得低共熔溶剂;并且,本技术的多元低共熔溶剂具有更好的传质效果。此外,在多元低共熔溶剂的基础上,本技术的低共熔溶剂中进一步添加了抗坏血酸等助剂,使得高价钴和镍更容易被浸取,从而进一步提高了金属元素的浸取效率,能够更有效的浸取废旧正极材料。
10.本技术的一种实现方式中,氢键供体为尿素、氨基磺酸、乙酰胺、聚乙二醇和甲基脲中的任意两种,分别作为第一氢键供体和第二氢键供体;并且,氯化胆碱:第一氢键供体:第二氢键供体的摩尔比为1:1:0.5~1:1:3。
11.需要说明的是,本技术的一种实现方式中具体采用的是三元低共熔溶剂,即包含氯化胆碱和两种氢键供体,三元低共熔溶剂即可有效的降低溶剂熔点,并具有良好的传质效果。其中,氢键供体和受体的比例影响溶剂的熔点,比例太高或太低均会导致低共熔溶剂在常温下熔点过高,即常温下呈现半固态,这种常温下熔点过高的物质浸取效率极低。本技术氯化胆碱:第一氢键供体:第二氢键供体的摩尔比为1:1:0.5~1:1:3的比例是实验探究过程中最适宜的比例。
12.本技术的一种实现方式中,第一氢键供体为氨基磺酸,所述第二氢键供体为尿素。
13.需要说明的是,氯化胆碱、氨基磺酸和尿素组成的三元低共熔溶剂,是本技术的一种实现方式中经过证实的熔点低、传质效果好的低共熔溶剂体系。可以理解,在此基础上,采用与氨基磺酸和尿素理化特性类似的共熔溶剂,如乙酰胺、聚乙二醇或甲基脲替换氨基磺酸和尿素中的一种或两种,同样可以达到氯化胆碱、氨基磺酸和尿素三元低共熔溶剂相同或类似的熔点低、传质效果好的效果。
14.同样的,抗坏血酸也是本技术的一种实现方式中经过证实的能够使高价钴和镍更容易被浸取的助剂,其原理是利用抗坏血酸的还原性能,使得废旧正极材料中高价态的钴和镍能够更容易的被浸取出来。可以理解,在此基础上,采用理化特性类似的还原剂,如乙醛或葡萄糖替换抗坏血酸,同样能够起到使高价钴和镍更容易被浸取的效果。
15.本技术的一种实现方式中,助剂占总重量的2%~20%。
16.需要说明的是,助剂含量过少,同一温度条件下高价态离子需要更长的时间才能还原,效率低,而且若还原助剂过少还不能完全转化高价态离子,导致后续转化率过低;助剂用量过多,第一是成本增多,第二是一定量的高价态离子转化成低价态离子所需还原剂是一定的,过多助剂对转化率无提升且增加成本。
17.本技术的另一方面公开了本技术的低共熔溶剂的制备方法,包括按配比称取氢键受体、氢键供体和助剂,置于容器中,在80℃下搅拌,直至固体完全溶解为粘稠状液体,即获得本技术的低共熔溶剂。
18.需要说明的是,本技术的低共熔溶剂制备方法,只需要在80℃下搅拌即可,制备方法简单、易操作,且能耗低。
19.本技术的再一方面公开了本技术的低共熔溶剂在废旧锂离子电池正极片回收中的应用。
20.本技术的一种实现方式中,本技术的废旧锂离子电池为镍钴锰三元电池、钴酸锂电池、锰酸锂电池中的一种或几种。
21.需要说明的是,本技术的低共熔溶剂具有熔点低、传质效果好的优点,能够用于各种废旧锂离子电池正极片回收。可以理解,本技术的低共熔溶剂,由于能够使高价钴和镍更容易被浸取;因此,尤其适用于镍钴锰三元电池、钴酸锂电池、锰酸锂电池等废旧锂离子电池的正极片回收。
22.本技术的再一方面公开了一种采用本技术的低共熔溶剂进行废旧锂离子电池正极片回收的方法。
23.需要说明的是,本技术的废旧锂离子电池正极片回收方法,由于采用本技术的低共熔溶剂,具有更高的浸取效率;本技术的一种实现方式中,对金属锂的浸取率可以达到100%,对金属镍、钴、锰的浸取率最高也可以达到99%以上;例如,镍的浸取率可以达到99.5%,钴和锰的浸取率也可以分别达到99.3%。
24.本技术的一种实现方式中,本技术的废旧锂离子电池正极片回收方法包括将低共熔溶剂与正极片按液固比10-200进行混合;然后在搅拌条件下加热反应,使箔片和正极活性粉末分离,取出铝箔回收利用;剩余的正极活性粉末继续在低共熔溶剂中反应,至完全溶解;完全溶解后,对其进行高温煅烧,高温煅烧过程中,利用低共熔溶剂作为碳源,对正极活性粉末进行包覆,实现正极材料的回收和再生。
25.需要说明的是,本技术的废旧锂离子电池正极片回收方法,进一步的还包括利用低共熔溶剂在高温煅烧时提供碳源,包覆正极活性材料,使其能够再生;使得回收的正极材料具有较高的充放电容量和良好的循环性能,可以直接作为新能源汽车、移动电子设备、储能设备等领域的电池原材料使用。
26.本技术的一种实现方式中,搅拌条件为60~180r/min。
27.本技术的一种实现方式中,加热反应的温度为60~180℃,反应时间为30~120min。
28.本技术的一种实现方式中,正极活性粉末继续在低共熔溶剂中反应的时间为6~12h。
29.本技术的一种实现方式中,高温煅烧的温度为700~850℃,煅烧时间为6~12h。
30.本技术的一种实现方式中,在将正极片与低共熔溶剂混合之前,还包括对正极片进行裁剪。
31.本技术的一种实现方式中,将正极片裁剪成2
×
1.5cm的块状,以便放入容器中进行后续剥离和正极材料回收。
32.本技术的有益效果在于:本技术用于废旧锂离子电池正极片回收的低共熔溶剂,熔点低、传质效果好,能够
使得高价钴和镍更容易被浸取,提高了金属元素的浸取效率,进而提高了废旧锂离子电池正极片的回收效率。并且,基于本技术低共熔溶剂进行的废旧锂离子电池正极片回收,还能够利用低共熔溶剂提供碳源进行再生,使得回收的正极材料具有较高的充放电容量和良好的循环性能,可以直接作为新能源汽车、移动电子设备、储能设备等领域的电池原材料使用,提高了回收正极材料的质量。
附图说明
33.图1是本技术实施例中不同搅拌速度下铝箔剥离率的测试结果;图2是本技术实施例中循环再生后正极材料的倍率性能测试结果;图3是本技术实施例中循环再生后正极材料的循环性能测试结果。
具体实施方式
34.现有的低共熔溶剂普遍存在金属元素浸取效率较低的问题。研究发现,氢键供体为羧酸类的低共熔溶剂有更好的金属溶解能力,这是因为羧酸不仅提供配位阴离子,还提供质子氢促进金属的回收的效率。因此,本技术创造性的选取氨基磺酸作为氢键供体;实验中发现,氨基磺酸和氯化胆碱组成的二元低共熔溶剂熔点高,金属元素的浸取效率低,加入尿素后构成的三元低低共熔溶有效的降低了溶剂熔点,且三元低共熔溶剂具有更好的传质效果。但是,更进一步研究试验显示,由氯化胆碱、尿素和氨基磺酸组成的三元低共熔溶剂无法完全浸取废旧正极材料。研究发现,这是因为废旧正极材料中高价态的钴和镍存在导致的;因此,本技术在低共熔溶剂中添加还原剂抗坏血酸,使得高价钴和镍更容易被浸取。最终获得以氯化胆碱、尿素和氨基磺酸组成的三元低共熔溶剂,并采用抗坏血酸作为助剂。
35.在以上研究的基础上,本技术进一步研究了氢键供体的替换方案,研究显示,乙酰胺、聚乙二醇或甲基脲替换氨基磺酸和尿素中的一种或两种,同样可以达到氯化胆碱、氨基磺酸和尿素三元低共熔溶剂相同或类似的熔点低、传质效果好的效果。至于助剂,乙醛或葡萄糖替换抗坏血酸,同样能够起到使高价钴和镍更容易被浸取的效果。
36.因此,本技术研发了一种用于废旧锂离子电池正极片回收的低共熔溶剂,由氢键受体、氢键供体和助剂组成;其中,氢键受体为氯化胆碱,氢键供体为尿素、氨基磺酸、乙酰胺、聚乙二醇和甲基脲中的至少两种,助剂为抗坏血酸、乙醛和葡萄糖中的至少一种。
37.在本技术的低共熔溶剂基础上,本技术进一步的研发了一种采用本技术的低共熔溶剂进行废旧锂离子电池正极片回收的方法。具体的,包括将低共熔溶剂与正极片按液固比10-200进行混合;然后在搅拌条件下加热反应,使箔片和正极活性粉末分离,取出铝箔回收利用;剩余的正极活性粉末继续在低共熔溶剂中反应,至完全溶解;完全溶解后,对其进行高温煅烧,高温煅烧过程中,利用低共熔溶剂作为碳源,对正极活性粉末进行包覆,实现正极材料的回收和再生。
38.本技术的低共熔溶剂和回收方法,可以一步直接实现废旧正极材料回收和再生,制备得到新的正极材料。本技术的回收方法,首先,将正极材料中的铝箔剥离,铝箔是惰性物质影响正极材料的电化学性能,正极活性材料和铝箔通过粘结剂涂敷在一起,通过控制搅拌速率,利用相似相溶原理,在本技术的低共熔溶剂中可以实现正极活性物质与铝箔的分离。粘结剂和低共熔溶剂都是有机物质,因此可以利用相似相容原理将正极活性物质从
铝箔上分离。由此分离出铝箔,废旧正极活性留在低共熔溶剂中。然后,对低共熔溶剂中的活性物质进行浸取反应溶解和活化;最后,采用溶胶凝胶法和煅烧得到再生的正极活性物质。
39.本技术的一种实现方式中,对回收再生的正极材料性能进行测试表征。结果显示,回收的正极材料具有较高的充放电容量和良好的循环性能。因此,常规的回收工艺只是通过低共熔溶剂把废旧正极材料溶解回收,而本技术的回收方法则是在溶解的基础上实现再生,得到可以直接使用的正极活性物质。并且,本技术的回收方法操作简单,流程简短。
40.本技术的多元低共熔溶剂能够在温和条件下,一步实现正极材料的高效剥离、正极活性粉末的高效浸取以及浸取液循环再生,从而制备可以直接使用的正极活性物质。具有操作简单、节能环保、易于产业化等优点。循环再生的正极材料具有较高的充放电容量和良好的循环性能,可以直接应用于新能源汽车、移动电子设备、储能设备等领域的电池原材料。
41.与现有工艺相比,本技术的回收方法具有以下优势:(1)本技术的低共熔溶剂是一种绿色的、温和的溶剂,其来源广泛,价格低廉。采用本技术的低共熔溶剂能够高效地实现正极材料中铝箔和正极活性组分的剥离,避免传统物理剥离工艺和化学剥离工艺中的低效率和化学污染。
42.(2)本技术的低共熔溶剂在使用过程中起到了浸出剂和螯合剂的双重作用,简化了回收和再生流程。可以避免传统火法工艺和湿法工艺中产生的高污染,降低能耗和强酸使用时的危险。同时,能够在温和条件下,一步实现正极材料的高效剥离、正极活性粉末的高效浸取以及浸取液的循环再生制备正极活性组分。具有操作简单,节能环保,易于产业化的优点。
43.(3)本技术的低共熔溶剂作为碳源对再生的正极材料进行包覆,改善材料电导率和锂离子扩散速率,使得循环再生正极材料具有较高的充放电容量和循环稳定性。
44.下面通过具体实施例和附图对本技术作进一步详细说明。以下实施例仅对本技术进行进一步说明,不应理解为对本技术的限制。
45.实施例一本例的低共熔溶剂由氢键受体、氢键供体和助剂组成;其中,氢键受体为氯化胆碱,氢键供体为尿素和氨基磺酸,助剂为抗坏血酸。氯化胆碱:尿素:氨基磺酸的摩尔比为1:1:1,抗坏血酸占低共熔溶剂总重量的5%。本例的废旧锂离子电池正极片回收方法具体步骤如下:(1)将废旧的三元电池进行机械拆解得到正极材料、负极及隔膜等材料;取正极材料剪成2
×
1.5cm的块状以便放入单口烧瓶进行后续剥离和回收。
46.(2)称取摩尔比氯化胆碱:尿素:氨基磺酸=1:1:1,及终浓度5%的抗坏血酸混合置于烧瓶中,在80℃的温度下搅拌30min,直至固体逐渐完全溶解,形成无色透明粘稠状的低共熔溶剂。
47.(3)称取步骤(1)中剪裁的块状正极材料加入到步骤(2)中制备的低共熔溶剂中,低共熔溶剂与正极材料的液固比为50,在60r/min的搅拌速度,90℃的油浴锅中反应60min后,剥离下来的块状铝箔取出回收利用,剩余的正极活性组分继续在低共熔溶剂中反应10h。
48.(4)将步骤(3)中含有正极活性元素的低共熔溶剂转移至瓷舟中,然后置于850℃的马弗炉中煅烧6h得到正极活性物质,取正极活性组装成扣式电池并进行电化学性能测试。
49.将回收的正极材料按照常规操作组装成纽扣电池,并测试其电化学性能。本例具体使用2025型硬币电池进行电化学测试,其中回收的正极材料作为阴极,celgard 2500膜作为隔膜,锂箔作为阳极。电解质是在碳酸乙酯和碳酸二甲酯(1:1体积比)的混合物中的1m lipf6。将ncm811粉末(80重量%)、pvdf(10重量%)和super-p(10重量%)放入n-甲基-2-吡咯烷酮(nmp)中并搅拌以制备浆料,该浆料涂覆在铝箔上,然后在真空烘箱中在120℃下干燥极片过夜。接下来,切割、压制和称重极片。最后,电池组装在手套箱中。锂片用作另一极。依次添加电解液隔膜电解液锂片垫片弹片负极外壳。样品中活性物质的质量负荷为6~8mg。
50.测试工步方法(包含循环):搁置12h-0.1c恒流恒压充电4.3v-20.1c恒流放电,截止电压3v-搁置5min-0.2c恒流恒压充电4.3v-0.2c恒流放电,截止电压3v(后面依次0.5c,1c,0.1c倍率充放电)-循环次数2000-结束。
51.对步骤(3)的反应产物,用icp(电感耦合等离子光谱发生仪)测量金属铝的剥离率,以及浸取液中金属锂、镍、钴及锰的浸取率。
52.结果显示,步骤(3)反应后金属铝的剥离率为98.11%,浸取液中金属锂、镍、钴及锰的浸取率分别为eli=100%、eni=99.5%、eco=98.7%、emn=99.3%。
53.电化学性能测试结果如图2和图3所示。图2的结果显示,本例回收的材料表现出良好的倍率性能。图2和图3的结果显示,采用本例回收材料制备的电池,其容量在190左右(0.1c倍率下),回收后的电池容量与高镍的实际容量200mah/g相媲美;而且,在循环过程中表现出良好的循环稳定性和良好的倍率性能。
54.实施例二本例的低共熔溶剂由氢键受体、氢键供体和助剂组成;其中,氢键受体为氯化胆碱,氢键供体为尿素和氨基磺酸,助剂为抗坏血酸。氯化胆碱:尿素:氨基磺酸的摩尔比为1:1:1,抗坏血酸占低共熔溶剂总重量的10%。本例的废旧锂离子电池正极片回收方法具体步骤如下:(1)将废旧的三元电池进行机械拆解得到正极材料,负极及隔膜等材料;取正极材料剪成2
×
1.5cm的块状以便放入单口烧瓶进行后续剥离和回收。
55.(2)称取摩尔比氯化胆碱:尿素:氨基磺酸=1:1:1,及终浓度10%的抗坏血酸混合置于烧瓶中,在80℃的温度下搅拌30min,直至固体逐渐完全溶解,形成无色透明粘稠状的低共熔溶剂。
56.(3)称取步骤(1)中2
×
1.5cm的块状正极材料加入到步骤(2)中制备的低共熔溶剂中,低共熔溶剂与正极材料的液固比为50,在60 r/min的搅拌速度,90℃的油浴锅中反应60min后,剥离下来的块状铝箔取出回收利用,剩余的正极活性组分继续在低共熔溶剂中反应8h。
57.(4)将步骤(3)中含有正极活性元素的低共熔溶剂转移至瓷舟中,然后置于850℃的马弗炉中煅烧6h得到正极活性物质。
58.对步骤(3)的反应产物,用icp测量金属铝的剥离率,以及浸取液中金属锂、镍、钴及锰的浸取率。
59.结果显示,步骤(3)反应后金属铝的剥离率为98.62%,浸取液中金属锂、镍、钴及锰的浸取率分别为eli=100%、eni=99.4%、eco=99.3%、emn=98.6%。
60.实施例三本例的低共熔溶剂由氢键受体、氢键供体和助剂组成;其中,氢键受体为氯化胆碱,氢键供体为尿素和氨基磺酸,助剂为抗坏血酸。氯化胆碱:尿素:氨基磺酸的摩尔比为1:1:1,抗坏血酸占低共熔溶剂总重量的10%。本例的废旧锂离子电池正极片回收方法具体步骤如下:(1)将废旧的三元电池进行机械拆解得到正极材料,负极及隔膜等材料;取正极材料剪成2
×
1.5cm的块状以便放入单口烧瓶进行后续剥离和回收。
61.(2)称取摩尔比氯化胆碱:尿素:氨基磺酸=1:1:1,及终浓度10%的抗坏血酸混合置于烧瓶中,在80℃的温度下搅拌30min,直至固体逐渐完全溶解,形成无色透明粘稠状的低共熔溶剂。
62.(3)称取步骤(1)中2
×
1.5cm的块状正极材料加入到步骤(2)中制备的低共熔溶剂中,低共熔溶剂与正极材料的液固比为50,在100 r/min的搅拌速度,90℃的油浴锅中反应40min后,剥离下来的块状铝箔取出回收利用,剩余的正极活性组分继续在低共熔溶剂中反应8h。
63.(4)将步骤(3)中含有正极活性元素的低共熔溶剂转移至瓷舟中,然后置于850℃的马弗炉中煅烧6h得到正极活性物质。
64.对步骤(3)的反应产物,用icp测量金属铝的剥离率,以及浸取液中金属锂、镍、钴及锰的浸取率。
65.结果显示,步骤(3)反应后金属铝的剥离率为93.29%,浸取液中金属锂、镍、钴及锰的浸取率分别为eli=99.8%、eni=98.7%、eco=99.2%、emn=97.9%。
66.实施例四本例的低共熔溶剂由氢键受体、氢键供体和助剂组成;其中,氢键受体为氯化胆碱,氢键供体为尿素和氨基磺酸,助剂为抗坏血酸。氯化胆碱:尿素:氨基磺酸的摩尔比为1:1:1,抗坏血酸占低共熔溶剂总重量的10%。本例的废旧锂离子电池正极片回收方法具体步骤如下:(1)将废旧的三元电池进行机械拆解得到正极材料,负极及隔膜等材料;取正极材料剪成2
×
1.5cm的块状以便放入单口烧瓶进行后续剥离和回收。
67.(2)称取摩尔比氯化胆碱:尿素:氨基磺酸=1:1:1,及终浓度10%的抗坏血酸混合置于烧瓶中,在80℃的温度下搅拌30min,直至固体逐渐完全溶解,形成无色透明粘稠状的低共熔溶剂。
68.(3)称取步骤(1)中2
×
1.5cm的块状正极材料加入到步骤(2)中制备的低共熔溶剂中,低共熔溶剂与正极材料的液固比为50,在60 r/min的搅拌速度,120℃的油浴锅中反应30min后,剥离下来的块状铝箔取出回收利用,剩余的正极活性组分继续在低共熔溶剂中反应6h。
69.(4)将步骤(3)中含有正极活性元素的低共熔溶剂转移至瓷舟中,然后置于850℃的马弗炉中煅烧6h得到正极活性物质。
70.对步骤(3)的反应产物,用icp测量金属铝的剥离率,以及浸取液中金属锂、镍、钴
及锰的浸取率。
71.结果显示,步骤(3)反应后金属铝的剥离率为94.72%,浸取液中金属锂、镍、钴及锰的浸取率分别为eli=100%、eni=99.4%、eco=98.2%、emn=98.1%。
72.实施例五本例的低共熔溶剂由氢键受体、氢键供体和助剂组成;其中,氢键受体为氯化胆碱,氢键供体为尿素和氨基磺酸,助剂为抗坏血酸。氯化胆碱:尿素:氨基磺酸的摩尔比为1:1:1,抗坏血酸占低共熔溶剂总重量的10%。本例的废旧锂离子电池正极片回收方法具体步骤如下:(1)将废旧的三元电池进行机械拆解得到正极材料,负极及隔膜等材料;取正极材料剪成2
×
1.5cm的块状以便放入单口烧瓶进行后续剥离和回收。
73.(2)称取摩尔比氯化胆碱:尿素:氨基磺酸=1:1:1,及终浓度10%的抗坏血酸混合置于烧瓶中,在80℃的温度下搅拌30min,直至固体逐渐完全溶解,形成无色透明粘稠状的低共熔溶剂。
74.(3)称取步骤(1)中2
×
1.5cm的块状正极材料加入到步骤(2)中制备的低共熔溶剂中,低共熔溶剂与正极材料的液固比为50,在100 r/min的搅拌速度,60℃的油浴锅中反应50min后,剥离下来的块状铝箔取出回收利用,剩余的正极活性组分继续在低共熔溶剂中反应12h。
75.(4)将步骤(3)中含有正极活性元素的低共熔溶剂转移至瓷舟中,然后置于850℃的马弗炉中煅烧6h得到正极活性物质。
76.对步骤(3)的反应产物,用icp测量金属铝的剥离率,以及浸取液中金属锂、镍、钴及锰的浸取率。
77.结果显示,步骤(3)反应后金属铝的剥离率为97.84%,浸取液中金属锂、镍、钴及锰的浸取率分别为eli=99.9%、eni=98.6%、eco=97.9%、emn=98.7%。
78.实施例六本例的低共熔溶剂由氢键受体、氢键供体和助剂组成;其中,氢键受体为氯化胆碱,氢键供体为尿素和氨基磺酸,助剂为抗坏血酸。氯化胆碱:尿素:氨基磺酸的摩尔比为1:1:1,抗坏血酸占低共熔溶剂总重量的10%。本例的废旧锂离子电池正极片回收方法具体步骤如下:(1)将废旧的三元电池进行机械拆解得到正极材料,负极及隔膜等材料;取正极材料剪成2
×
1.5cm的块状以便放入单口烧瓶进行后续剥离和回收。
79.(2)称取摩尔比氯化胆碱:尿素:氨基磺酸=1:1:1,及终浓度10%的抗坏血酸混合置于烧瓶中,在80℃的温度下搅拌30min,直至固体逐渐完全溶解,形成无色透明粘稠状的低共熔溶剂。
80.(3)称取步骤(1)中2
×
1.5cm的块状正极材料加入到步骤(2)中制备的低共熔溶剂中,低共熔溶剂与正极材料的液固比为50,在100 r/min的搅拌速度,90℃的油浴锅中反应40min后,剥离下来的块状铝箔取出回收利用,剩余的正极活性组分继续在低共熔溶剂中反应8h。
81.(4)将步骤(3)中含有正极活性元素的低共熔溶剂转移至瓷舟中,然后置于850℃的马弗炉中煅烧12h得到正极活性物质。
82.对步骤(3)的反应产物,用icp测量金属铝的剥离率,以及浸取液中金属锂、镍、钴及锰的浸取率。
83.结果显示,步骤(3)反应后金属铝的剥离率为93.29%,浸取液中金属锂、镍、钴及锰的浸取率分别为eli=99.8%、eni=98.7%、eco=99.2%、emn=97.9%。
84.实施例七本例在实施例一的基础上,调整步骤(3)中的搅拌速度,观察不同搅拌速度对铝箔的剥离率的影响。具体的,分别在40r/min、60r/min、80r/min、100r/min、120r/min的搅拌速度进行油浴锅反应,其余条件都与实施例一相同。
85.步骤(3)反应完成后,用icp测量金属铝的剥离率,以及浸取液中金属锂、镍、钴及锰的浸取率,测试结果如图1所示。
86.结果显示,搅拌速度为60 r/min时,铝箔的分离效果最佳,剥离率为98.11%,浸取液中金属锂、镍、钴及锰的浸取率分别为eli=100%、eni=99.5%、eco=98.7%、emn=99.3%。
87.实施例八本例在实施例一的基础上,调整步骤(2)中低共熔溶剂的抗坏血酸的用量,具体的,分别添加终浓度2%、5%、10%、15%、20%的抗坏血酸,其余条件都与实施例一相同。
88.同样的,在步骤(3)反应完成后,用icp测量金属铝的剥离率,以及浸取液中金属锂、镍、钴及锰的浸取率。
89.结果显示,抗坏血酸的用量为5%时效果最佳,剥离率为98.11%,浸取液中金属锂、镍、钴及锰的浸取率分别为eli=100%、eni=99.5%、eco=98.7%、emn=99.3%。
90.实施例九本例在实施例一的基础上,改变步骤(2)中低共熔溶剂的助剂,具体的,分别采用终浓度5%乙醛、终浓度5%的葡萄糖替换实施例一中的抗坏血酸,其余条件都与实施例一相同。
91.同样的,在步骤(3)反应完成后,用icp测量金属铝的剥离率,以及浸取液中金属锂、镍、钴及锰的浸取率。
92.结果显示,5%乙醛或5%葡萄糖,其效果与抗坏血酸相当,可以根据需求采用乙醛或葡萄糖替换抗坏血酸;具体相似的金属铝剥离率和金属浸取率。
93.实施例十本例在实施例一的基础上,改变步骤(2)中低共熔溶剂的氢键供体,即分别采用乙酰胺、聚乙二醇和甲基脲中的一种或两种替换尿素和氨基磺酸中的一种或两种,其余条件都与实施例一相同。
94.结果显示,尿素和氨基磺酸中一种可以被乙酰胺、聚乙二醇和甲基脲中的任意一种取代,或者,尿素和氨基磺酸中两者同时被乙酰胺、聚乙二醇和甲基脲中的任意两种取代,最终获得的金属铝剥离率和金属浸取率效果相当。
95.以上内容是结合具体的实施方式对本技术所作的进一步详细说明,不能认定本技术的具体实施只局限于这些说明。对于本技术所属技术领域的普通技术人员来说,在不脱离本技术构思的前提下,还可以做出若干简单推演或替换。