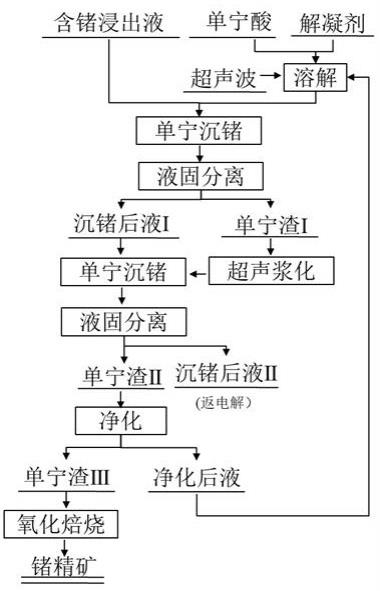
1.本发明涉及一种超声协同单宁酸改性强化单宁沉锗的方法,属于稀散金属富集提取技术领域。
背景技术:2.锗是一种稀缺的、有限的重要战略资源。锗及其化合物因具有较高的红外折射系数、较高的光电转化效率和较低的传输损耗等优点,在国防工业、航空航天和现代通信领域等的价值无可取代。我国主要从含锗氧化锌烟尘中提取锗,主要采用单宁沉锗工艺,由于单宁溶液具有半胶体溶液性质,且单宁溶液中单宁分子间存在氢键或偶极作用,这使单宁半胶体溶液具有缔合作用,影响单宁酸的沉锗作用,单宁酸用量高达锗含量的30倍以上,生产成本高,单宁酸用量高时,会吸附大量杂质,造成制备锗精矿品位低,仅为25%左右。
3.为了降低单宁酸用量,在梯级超声强化单宁络合沉锗的方法中,通过加入掩蔽剂来降低单宁与杂质离子的反应,通过引入晶种及梯级超声来强化单宁沉锗;单宁酸循环沉锗的方法中,将已沉淀的单宁锗返回用作沉锗晶核,利用两段沉锗实现单宁锗晶核形成及颗粒长大,实现单宁酸高效沉锗。
4.目前降低单宁酸主要通过加入晶种方式,对单宁酸胶体性质及改性尚无研究。
技术实现要素:5.本发明针对现有技术中存在的单宁酸用量高、沉锗效率低等问题,提出了一种超声协同单宁酸改性强化单宁沉锗的方法,利用超声与解凝剂协同强化大幅度降低单宁酸用量,声化学产生的剪切力足够强,能破坏氢键或偶极作用,降低单宁酸溶解时的胶体吸附作用,同时解凝剂能使单宁酸胶束分散,此外超声波空化气泡破裂后产生的液体微射流,足以使分散胶束发生键断裂,产生活性化学物质,强化单宁沉锗效率。
6.一种超声协同单宁酸改性强化单宁沉锗的方法,具体步骤如下:(1)超声条件下,将单宁酸和解凝剂加入到水中溶解形成单宁酸液;(2)将单宁酸液加入含锗浸出液中进行单宁沉锗,液固分离得到沉锗后液i和单宁渣i;(3)单宁渣i加入到工业水进行超声浆化得到混合浆,混合浆与沉锗后液i混合后进行单宁沉锗,液固分离得到沉锗后液ii和单宁渣ii;(4)沉锗后液ii直接中和后进行净化电积,单宁渣ii经工业水净化,液固分离得到单宁渣iii和净化后液;单宁渣iii氧化焙烧得到锗精矿,净化后液返回步骤(1)溶解单宁酸和解凝剂。
7.所述步骤(1)溶解温度为50~70℃,溶解ph为1~3,超声波强度为0.3~0.6w/cm2,超声频率为16-20khz,单宁酸浓度为10~20wt.%,解凝剂浓度为0~5wt.%,解凝剂为乙醇、乙酸、甘油或葡萄糖。
8.所述步骤(2)含锗浸出液中锗含量为50~200mg/l,fe
3+
含量为10~50mg/l,锌含量为
100~150g/l。
9.进一步的,所述步骤(2)含锗浸出液的ph为1~3,单宁酸液中单宁酸为含锗浸出液中锗质量的10~15倍,单宁沉锗的温度为60~70℃,沉锗时间为10~30min。
10.更进一步的,所述沉锗后液i的ph值为1~2,温度为60~65℃,沉锗后液i中锗含量为20~80mg/l,fe
3+
含量为5~30mg/l,锌含量为99.4~148.4g/l;单宁锗渣i中锌含量为4.53~12.52%,fe含量为0.60~0.77%,ge含量为3.63~4.66%。
11.所述步骤(3)工业水的ph为4~5,浆化液固质量比为1:1,超声浆化频率为16-20khz,超声波强度为0.4~0.7w/cm2,浆化温度为50~70℃,浆化ph为1~3。
12.所述步骤(3)单宁沉锗温度为60~65℃,沉锗时间为20~40min。
13.进一步的,所述沉锗后液ii的ph值为2~3,温度为55~60℃,沉锗后液ii中锗含量为0.01~0.1mg/l,fe
3+
含量为1~5mg/l,锌含量为99~148g/l;单宁锗渣ii锌含量为14.62~34.82%,fe含量0.62~1.26%,ge含量为3.45~5.62%。
14.所述步骤(4)净化用工业水与单宁渣ii的液固质量比为2~4:1,净化ph值为1~2,净化温度为40~60℃,单宁渣iii中锌含量为0.8~1.5%,fe
3+
含量0.4~0.8%,ge含量为5.2~19.4%。
15.所述步骤(4)净化后液中有效单宁含量为0.5~1%,zn含量为70.46~86.38g/l,fe
3+
含量为0.66~2.80mg/l,ge含量为0.12~5.44mg/l。
16.本发明的有益效果是:(1)针对单宁酸耗量高本质性问题-单宁溶液具有半胶体溶液性质,且单宁溶液中单宁分子间存在氢键或偶极作用,使单宁半胶体溶液具有缔合作用,极大降低单宁酸沉锗效率,本发明提出超声与解凝剂协同强化手段,声化学产生的剪切力足够强,能破坏氢键或偶极作用,降低单宁酸溶解时的胶体吸附作用,同时解凝剂能使单宁酸胶束分散;超声波空化气泡破裂后产生的液体微射流,足以使分散胶束发生键断裂,产生活性化学物质,三重作用下能强化单宁酸的沉锗作用,大幅度降低单宁酸用量;(2)本发明方法能将单宁酸用量降低50%~66.67%,以单宁酸4.2万/吨计算,每吨锗沉锗成本降低63~84万,同时单宁用量降低,吸附杂质降低,锗精矿品位由现有水平的25%左右提高至47~59%。
附图说明
17.图1为本发明工艺流程图。
18.图2为不加超声和解凝剂条件下所获得单宁锗渣的gpc图;图3为实施例1所获得单宁锗渣iii的gpc图。
具体实施方式
19.下面结合具体实施方式对本发明作进一步详细说明,但本发明的保护范围并不限于所述内容。
20.实施例1:一种超声协同单宁酸改性强化单宁沉锗的方法,具体步骤如下:(1)单宁溶解:在温度50℃、超声条件下,将单宁酸和解凝剂(甘油)加入到ph值为1的工业水中溶解5min形成单宁酸液;其中单宁酸液的单宁酸为含锗浸出液中锗质量的10
倍,超声功率密度0.3w/cm2,超声频率为16khz,单宁酸液中单宁酸浓度为10wt.%,解凝剂(甘油)浓度为5wt.%;(2)单宁沉锗:将单宁酸液加入含锗浸出液中进行单宁沉锗10min,液固分离得到沉锗后液i和单宁渣i;其中含锗浸出液中锗含量为50mg/l,fe
3+
含量为10mg/l,锌含量为100g/l,ph为1,温度为60℃;沉锗后液i中锗含量为20mg/l,fe
3+
含量为5mg/l,锌含量为99.4g/l,ph为1,温度为60℃;单宁锗渣i中锌含量为12.52%,fe含量为0.60%,ge含量为3.63%;(3)单宁渣浆化沉锗:单宁渣i加入到ph值为4的工业水中,在温度60℃下进行超声浆化20min得到混合浆,其中单宁渣i与工业水的固液质量比为1:1,浆化超声频率为16khz,超声波强度为0.4w/cm2;混合浆与沉锗后液i混合后,在温度60℃下进行单宁沉锗20min,液固分离得到沉锗后液ii和单宁渣ii;沉锗后液ii中锗含量为0.01mg/l,fe
3+
含量为1mg/l,锌含量为99g/l,ph为2,温度为55℃;单宁锗渣ii中锌含量为34.82%,fe含量0.62%,ge含量为3.45%;(4)单宁渣净化焙烧:沉锗后液ii直接中和后进行净化电积,单宁渣ii经工业水净化,液固分离得到单宁渣iii和净化后液,其中净化用工业水与单宁渣ii的液固质量比为2:1,净化ph为1,净化温度为40℃,单宁渣iii中锌含量为0.8%,fe
3+
含量0.4%,ge含量为5.2%;单宁渣iii氧化焙烧得到锗精矿,净化后液返回步骤(1)溶解单宁酸和解凝剂;净化后液中有效单宁含量为0.5%,zn含量为70.46g/l,fe
3+
含量为1.78mg/l,ge含量为0.12mg/l;不加超声和解凝剂(其他条件不变化)条件下,所获得单宁锗渣的gpc图见图2,本实施例所获得单宁锗渣iii的gpc图见图3,从图2可知,不加超声和解凝剂条件下获得单宁锗渣iii的数均分子量mn为3197,分布系数pdi为1.45;本实施例超声和解凝剂(甘油)共同作用下,获得单宁锗渣iii的数均分子量mn为532,分布系数pdi为1.36,证明超声和解凝剂共同作用可降低单宁胶体的缔合作用,形成的单宁锗渣分子量更小,分子量分布更均匀;本实施例所制备锗精矿品位为47.02%。
21.实施例2:一种超声协同单宁酸改性强化单宁沉锗的方法,具体步骤如下:(1)单宁溶解:在温度60℃、超声条件下,将单宁酸和解凝剂(乙酸)加入到ph值为2的工业水中溶解10min形成单宁酸液;其中超声功率密度0.5w/cm2,超声频率为18khz,单宁酸液中单宁酸浓度为15wt.%,解凝剂(乙酸)浓度为0.5wt.%;(2)单宁沉锗:将单宁酸液加入含锗浸出液中进行单宁沉锗20min,液固分离得到沉锗后液i和单宁渣i;其中单宁酸液的单宁酸为含锗浸出液中锗质量的12倍,含锗浸出液中锗含量为100mg/l,fe
3+
含量为15mg/l,锌含量为120g/l,ph为2,温度为65℃;沉锗后液i中锗含量为30mg/l,fe
3+
含量为8mg/l,锌含量为118.9g/l,ph为1.5,温度为62℃;单宁锗渣i中锌含量为8.70%,fe含量为0.40%,ge含量为4.08%;(3)单宁渣浆化沉锗:单宁渣i加入到ph值为4.5的工业水中,在温度60℃下进行超声浆化20min得到混合浆,其中单宁渣i与工业水的固液质量比为1:1,浆化超声频率为18khz,超声波强度为0.6 w/cm2;混合浆与沉锗后液i混合后,在温度62℃下进行单宁沉锗30min,液固分离得到沉锗后液ii和单宁渣ii;沉锗后液ii中锗含量为0.05mg/l,fe
3+
含量为2mg/l,锌含量为118.5g/l,ph为2.5,温度为58℃;单宁锗渣ii中锌含量为21.09%,fe含量0.50%,ge含量为
3.82%;(4)单宁渣净化焙烧:沉锗后液ii直接中和后进行净化电积,单宁渣ii经工业水净化,液固分离得到单宁渣iii和净化后液,其中净化用工业水与单宁渣ii的液固质量比为3:1,净化ph为1.5,净化温度为50℃,单宁渣iii中锌含量为1%,fe
3+
含量0.6%,ge含量为7.5%;单宁渣iii氧化焙烧得到锗精矿,净化后液返回步骤(1)溶解单宁酸和解凝剂;净化后液中有效单宁含量为0.75%,zn含量为68.62g/l,fe
3+
含量为0.66mg/l,ge含量为0.13mg/l;本实施例所制备锗精矿品位为50.31%。
22.实施例3:一种超声协同单宁酸改性强化单宁沉锗的方法,具体步骤如下:(1)单宁溶解:在温度70℃、超声条件下,将单宁酸加入到ph值为3的工业水中溶解20min形成单宁酸液;其中超声功率密度0.6w/cm2,超声频率为20khz,单宁酸液中单宁酸浓度为20wt.%;(2)单宁沉锗:将单宁酸液加入含锗浸出液中进行单宁沉锗30min,液固分离得到沉锗后液i和单宁渣i;其中单宁酸液的单宁酸为含锗浸出液中锗质量的15倍,含锗浸出液中锗含量为200mg/l,fe
3+
含量为50mg/l,锌含量为150g/l,ph为3,温度为70℃;沉锗后液i中锗含量为80mg/l,fe
3+
含量为30mg/l,锌含量为148.4g/l,ph为2,温度为65℃;单宁锗渣i中锌含量为12.52%,fe含量为0.77%,ge含量为4.66%;(3)单宁渣浆化沉锗:单宁渣i加入到ph值为5的工业水中,在温度70℃下进行超声浆化15min得到混合浆,其中单宁渣i与工业水的固液质量比为1:1,浆化超声频率为20khz,超声波强度为0.7w/cm2;混合浆与沉锗后液i混合后,在温度65℃下进行单宁沉锗40min,液固分离得到沉锗后液ii和单宁渣ii;沉锗后液ii中锗含量为0.1mg/l,fe
3+
含量为5mg/l,锌含量为148g/l,ph为3,温度为60℃;单宁锗渣ii中锌含量为14.62%,fe含量1.26%,ge含量为5.62%;(4)单宁渣净化焙烧:沉锗后液ii直接中和后进行净化电积,单宁渣ii经工业水净化,液固分离得到单宁渣iii和净化后液,其中净化用工业水与单宁渣ii的液固质量比为4:1,净化ph为2,净化温度为60℃,单宁渣iii中锌含量为1.5%,fe
3+
含量0.8%,ge含量为19.4%;单宁渣iii氧化焙烧得到锗精矿,净化后液返回步骤(1)溶解单宁酸;净化后液中有效单宁含量为1%,zn含量为86.38g/l,fe
3+
含量为2.80mg/l,ge含量为5.44mg/l;本实施例所制备锗精矿品位为58.86%。
23.以上对本发明的具体实施方式作了详细说明,但是本发明并不限于上述实施方式,在本领域普通技术人员所具备的知识范围内,还可以在不脱离本发明宗旨的前提下作出各种变化。