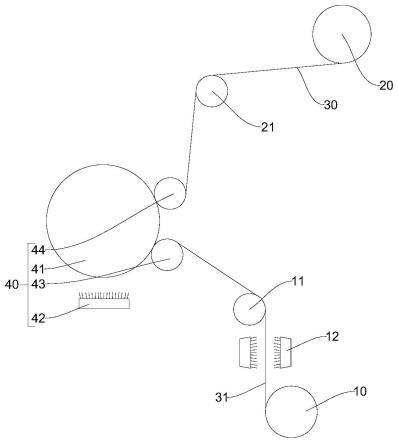
1.本发明涉及镀膜技术领域,具体的说,是涉及一种高分子基膜表面处理方法、设备及镀膜产品。
背景技术:2.目前,为了进一步提升高分子基膜的功能化及应用领域,其中应用最为广泛的方式是进行高分子基膜的功能膜层复合,即高分子基膜表面进行薄膜的沉积以形成具有阻隔、导电等功能的复合材料。镀膜产品的重要特性之一是镀制的膜层具有良好的附着性能,通常采用物理法(等离子体、电晕等)及化学法(如表面接枝改性等)进行基膜表面的改性以增强涂层附着。
3.然而现有的改性方式中,在真空环境进行等离子体轰击的改性方式,其设备结构相对复杂,并且因等离子体设备的运行维护的问题难以保障长时间的生产运行,镀膜前电晕处理需要多增加一道工序,如表面接枝改性的方法则新增工序且可能造成基膜表面的污染,并且设备系统相对更加复杂。
4.上述缺陷,值得解决。
技术实现要素:5.为了克服现有技术中高分子基膜的表面处理不便捷、系统结构复杂的缺陷,本发明提供一种高分子基膜表面处理方法、设备及镀膜产品。
6.本发明技术方案如下所述:本发明提供了一种高分子基膜表面处理方法,其特征在于,在高分子基膜镀膜前的出料端设置基膜表面改性装置,使得高分子基膜表面形成与镀膜材料产生化学键合反应的活性界面。
7.根据上述方案的本发明,其特征在于,在高分子基膜的出料端设置紫外辐射装置,使得所述高分子基膜表面辐照后诱导引入含氧基团。
8.根据上述方案的本发明,其特征在于,在高分子基膜镀膜前的出料端还设有微量气体布气管道,用于向高分子基膜表面输送含氧气氛。
9.另一方面,本发明提供一种高分子基膜表面处理设备,包括放卷辊、收卷辊、以及位于所述放卷辊与所述收卷辊之间的膜层沉积区域,由所述放卷辊放卷的高分子基膜经由所述膜层沉积区域后收卷于所述收卷辊上,其特征在于,所述膜层沉积区域与所述放卷辊之间设有紫外辐射装置,所述紫外辐射装置用于辐照所述高分子基膜的单侧或双侧,使其表面形成活性界面。
10.根据上述方案的本发明,其特征在于,所述紫外辐射装置的辐射强度与所述高分子基膜的走速呈正相关。
11.根据上述方案的本发明,其特征在于,所述紫外辐射装置相对于所述高分子基膜的距离与所述高分子基膜的走速呈反相关。
12.根据上述方案的本发明,其特征在于,所述紫外辐射装置与所述放卷辊之间还设有微量气体布气管道,所述微量气体布气管道置于所述高分子基膜的单侧或双侧,其用于向高分子基膜表面输送含氧气氛。
13.根据上述方案的本发明,其特征在于,膜层沉积区域包括功能镀层镀膜组件,功能镀层镀膜组件位于高分子基膜的单侧或双侧。
14.本发明还提供一种镀膜产品,包括高分子基膜、位于所述高分子基膜表面的功能镀层,其特征在于,所述高分子基膜与所述功能镀层之间设有用于增强所述功能镀层与所述高分子基膜之间粘附力的增强层,所述增强层由镀层材料与所述高分子基膜表面的活性界面化学键合形成。
15.根据上述方案的本发明,其特征在于,所述高分子基膜与所述功能镀层之间还设有缓冲层,所述增强层位于所述缓冲层与所述高分子基膜之间,且所述增强层由所述缓冲层的原材料与所述高分子基膜表面的活性界面化学键合形成。
16.根据上述方案的本发明,其有益效果在于,本发明在镀膜的真空腔体内引入紫外辐射装置,通过紫外辐射装置对高分子基膜表面进行辐照,使其形成活性界面,可以形成在后续基膜表面的沉积过程中与镀层化学键合的条件,进而增加镀膜与高分子基膜之间的粘附力;整个镀膜系统无需增设庞大的改性设备,可以更加方便的实现高分子基膜的表面处理,表面处理过程无污染、高效率。
附图说明
17.图1为本发明实施例一的结构示意图;图2为本发明实施例二的结构示意图;图3为本发明实施例三的结构示意图;图4为本发明实施例四的结构示意图;图5为本发明实施例五的结构示意图;图6为本发明实施例六的结构示意图;图7为本发明实施例七的结构示意图;图8为本发明实施例八的结构示意图;图9为本发明实施例九的结构示意图;图10为本发明一具体实施例中镀膜产品的结构示意图;图11为本发明另一具体实施例中镀膜产品的结构示意图。
18.在图中,各个附图标号为:10、放卷辊;11、放卷过辊;12、紫外辐射装置;13、微量气体布气管道;20、收卷辊;21、收卷展平辊;30、镀膜产品;31、高分子基膜;32、氧化铝层;33、铝层;34、钛氧化物层;35、钛层;40、第一镀膜组件;41、第一镀膜冷辊;42、第一蒸发机构;43、第一镀膜展平辊;44、第一镀膜过辊;45、第一靶材;50、第二镀膜组件;51、第二镀膜冷辊;52、第二蒸发机构;53、第二镀膜展平辊;54、第二镀膜过辊;55、第二靶材;60、第三镀膜组件;61、第三镀膜冷辊;62、第三蒸发机构;63、第三靶材;
70、第四镀膜组件;71、第四镀膜冷辊;72、第四蒸发机构;73、第四靶材。
具体实施方式
19.下面结合附图以及实施方式对本发明进行进一步的描述:为了能在真空镀膜的环境中,采用更加简便的方式对高分子基膜进行表面处理,使得镀膜表面形成能与镀层形成化学键合的结构,并提升镀层的附着能力,本发明提供了一种高分子基膜表面处理方法,在高分子基膜镀膜前的出料端设置基膜表面改性装置,使得高分子基膜表面形成与镀膜材料产生化学键合反应的活性界面,实现了高分子基膜表面改性的目的。
20.该基膜表面改性装置为紫外辐射装置,即在高分子基膜的出料端设置紫外辐射装置,使得高分子基膜表面的水分子、氧分子等物质辐照后,于高分子基膜表面诱导引入含氧基团。具体的,在真空卷绕镀膜设备的真空腔体内,通过紫外辐射装置对高分子基膜的表面进行辐照,可以诱导引入含氧基团。其中,含氧基团为包括单键氧(c-o-c,c-oh)、羰基(c=o)、羧基(cooh)等含氧基团,并且上述含氧基团能够为高分子基膜在后续过程中的镀层沉积提供了活性界面,且形成镀膜材料(如金属)与含氧基团的化学键合反应,在界面构建化学健价结构,最终达到增强镀膜膜层与高分子基膜界面粘附力的效果。
21.在后续镀膜过程中,带有活性界面的高分子基膜进入膜层沉积区域,膜层沉积区域的镀料与活性界面化学键合并形成增强层,用以增强镀层与高分子基膜表面的附着能力。具体的,膜层沉积区域沉积的镀层材料可以选择金属材料,膜层沉积区域的金属与活性界面化学键合并形成金属氧化物用以增强镀层与高分子基膜表面的附着能力。
22.金属材料可以选用具有良好缓冲粘附性能的ti及ti合金材料、al及其al合金材料、cr及cr合金材料,即通过蒸发、磁控溅射等方式沉积上述金属材料,处于活性非常高的原子级或离子级的材料附着于上述基膜表面时,更容易与高分子基膜表面的活性界面形成如tiox、crox、氧化铝等类似的化学健合的成分,从而增强镀层与基膜表面的附着性能。
23.高分子基膜的选材可以选择pet(聚对苯二甲酸乙二醇酯)、pi(聚酰亚胺)、pps(聚苯基硫醚)、pp(聚丙烯)、pe(聚乙烯)、pc(聚碳酸酯)、pen(聚萘二甲酸乙二醇酯)、ps(聚苯乙烯)、pa(聚酰胺)、ptfe(聚四氟乙烯)、pes(乙烯-醋酸乙烯共聚物)、pei(聚醚酰亚胺)、peek(聚醚醚酮)等。本发明的上述方法对于非极性特点的高分子基膜具有更显著的特点。
24.紫外辐射装置可以选用紫外辐射灯管,其中紫外辐照灯管可以采用市面上现成的uva波段(波长320~420nm,又称为长波黑斑效应紫外线)、uvb波段(波长275~320nm,又称为中波红斑效应紫外线)、uvc波段(波长200~275nm,又称为短波灭菌紫外线)、uvd波段(波长100~200nm,又称为真空紫外线)的产品。紫外辐射装置产生的紫外射线被高分子基膜的高分子基团吸收,其基团健断裂,并且因为基团表面吸附的水分子、氧分子等物质形成新的单键氧、双键氧的基团。选择合适的紫外光可以激发断裂氧分子健,从而形成原子氧,最终形成更多具有高活性基团或界面的改性的基膜表面。
25.进一步地,为了能够在基膜表面形成更多的含氧基团,在高分子基膜镀膜前的出料端还设有微量气体布气管道,用于向高分子基膜表面输送含氧气氛。微量气体布气关断与流量控制器连接,通过精密的流量控制器具实现布气管道含氧气氛的输送,其含氧气氛的引入也不影响后续薄膜的沉积。在具体实现过程中,含氧气氛采用微量掺杂的方式,如气
体浓度为99.5%ar+气体浓度0.5%o2的混合气氛,其中也可以采用臭氧源代替氧气。
26.如图1至图9所示,本发明提供了一种高分子基膜表面处理设备,在真空腔体内待镀膜材料原膜放卷端基膜拉出位置双面设置紫外灯辐照装置,以提供基膜表面处理的必要硬件条件。
27.该高分子基膜表面处理设备包括放卷辊10、收卷辊20、以及位于放卷辊10与收卷辊20之间的膜层沉积区域,由放卷辊放卷的高分子基膜31经由膜层沉积区域后收卷于收卷辊20上,其中放卷辊10用于实现高分子基膜31的放卷、镀层沉积区域用于实现高分子基膜31的表面镀膜,收卷辊20用于实现镀膜后的镀膜产品30的收卷。
28.为了保证整个镀膜设备内部走膜的平滑性,并且节省镀膜设备内部的空间,放卷辊10与膜层沉积区域之间设有放卷过辊11,高分子基膜31放卷后绕过放卷过辊11后进入膜层沉积区域;对应的,为了保证收卷后镀膜产品30的平整性,膜层沉积区域的末端与收卷辊20之间设有收卷展平辊21,镀膜完成后的镀膜产品30绕过收卷展平辊21后收卷于收卷辊20上。
29.为了增加镀膜与高分子基膜之间的附着力,本发明中的膜层沉积区域与放卷辊之间设有紫外辐射装置,紫外辐射装置用于辐照高分子基膜的单侧或双侧,当高分子基膜开始放卷时紫外辐射装置开始工作,使高分子基膜表面形成活性界面。
30.紫外辐射装置安装于位置调节装置上,通过位置调节装置调节紫外辐射装置与高分子基膜之间的间距,进而可以根据高分子基膜的走速来调节辐照距离。具体的,紫外辐射装置相对于高分子基膜的距离与高分子基膜的走速呈反相关。另外,紫外辐射装置的辐照强度也可以调节,根据高分子基膜的走速调节辐照强度。具体的,紫外辐射装置的辐射强度与高分子基膜的走速呈正相关。
31.通常情况下高分子基膜走速范围都非常大,一般为高分子基膜的走速为2m/min~400m/min。在此情况下,选择紫外辐射装置的辐射强度为0.5mw/cm2~500mw/cm2,紫外辐射装置相对于高分子基膜的距离为1cm~10cm。
32.膜层沉积区域用于实现高分子基膜表面的镀膜,其包括功能镀层镀膜组件,功能镀层镀膜组件位于高分子基膜的单侧或双侧,单侧的功能镀层镀膜组件实现高分子基膜单侧的镀膜,双侧的功能镀层镀膜组件实现高分子基膜双侧的镀膜。其中的功能镀层镀膜组件、缓冲层镀膜组件均包括镀膜冷辊、镀层蒸发源、展平辊以及过辊,高分子基膜依次绕过展平辊、镀膜冷辊以及过辊,且镀层蒸发源位于镀膜冷辊的走膜外侧。
33.根据需要,膜层沉积区域还包括缓冲层镀膜组件,沿着高分子基膜的走膜方向,缓冲层镀膜组件位于功能镀层镀膜组件的前侧,通过缓冲层镀膜组件对高分子基膜的表面镀缓冲层,再经过后续的功能镀层镀膜组件形成功能镀层,实现了功能镀层与高分子基膜表面的缓冲与进一步增强。
34.实施例1如图1所示,本实施例中,紫外辐射装置的紫外辐射灯管置于高分子基膜的两侧,紫外辐射灯管的辐照强度、其距离高分子基膜的距离根据高分子基膜的走速进行调节。
35.具体的,本实施例采用pi基膜作为镀膜材料的衬底,形成的镀膜产品的结构可以理解为pi/增强层/功能层的形式。并且本实施例的高分子基膜走速为2m/min,紫外辐射灯管采用的辐射强度为5mw/cm2,辐射距离4cm。
36.并且,本实施例采用单侧蒸镀方式进行镀膜,即功能镀层镀膜组件包括第一镀膜组件40,第一镀膜组件40包括第一镀膜冷辊41、第一蒸发机构42、第一镀膜展平辊43、第一镀膜过辊44,第一蒸发机构42位于第一镀膜冷辊41的下侧。高分子基膜依次绕过第一镀膜展平辊43、第一镀膜冷辊41、第一镀膜过辊44,并通过第一蒸发机构42完成单侧的蒸镀。
37.上述的功能镀层可以为金属膜层、金属化合物膜层等。
38.实施例2如图2所示,与实施例1不同的是,本实施例采用双侧蒸镀方式进行镀膜,即功能镀层镀膜组件包括第一镀膜组件40、第二镀膜组件50。具体的,第一镀膜组件40包括第一镀膜冷辊41、第一蒸发机构42、第一镀膜展平辊43、第一镀膜过辊44,第一蒸发机构42位于第一镀膜冷辊41的下侧;第二镀膜组件50包括第二镀膜冷辊51、第二蒸发机构52、第二镀膜展平辊53、第二镀膜过辊54,第二蒸发机构52位于第二镀膜冷辊51的下侧。
39.高分子基膜依次绕过第一镀膜展平辊43、第一镀膜冷辊41、第一镀膜过辊44,并通过第一蒸发机构42完成单侧的蒸镀;而后高分子基膜依次绕过第二镀膜展平辊53、第二镀膜冷辊51、第二镀膜过辊54,并通过第二蒸发机构52完成另一侧的蒸镀。
40.实施例3如图3所示,与实施例2不同的是,本实施例在完成功能层镀膜前,先通过缓冲层镀膜组件完成双侧的缓冲层蒸镀。
41.缓冲层镀膜组件包括第一镀膜组件40和第二镀膜组件50,第一镀膜组件40包括第一镀膜冷辊41、第一蒸发机构42、以及与第一镀膜冷辊41对应的第一镀膜展平辊、第一镀膜过辊;第二镀膜组件50包括第二镀膜冷辊51、第二蒸发机构52、以及与第二镀膜冷辊51对应的第二镀膜展平辊、第二镀膜过辊。高分子基膜依次绕过第一镀膜展平辊、第一镀膜冷辊41、第一镀膜过辊,并通过第一蒸发机构42完成单侧的缓冲层的蒸镀;而后高分子基膜依次绕过第二镀膜展平辊、第二镀膜冷辊51、第二镀膜过辊,并通过第二蒸发机构52完成另一侧的缓冲层的蒸镀。
42.功能镀层镀膜组件包括第三镀膜组件60和第四镀膜组件70,第三镀膜组件60包括第三镀膜冷辊41、第三蒸发机构62、以及与第三镀膜冷辊61对应的第三镀膜展平辊、第三镀膜过辊;第四镀膜组件70包括第四镀膜冷辊71、第四蒸发机构72、以及与第四镀膜冷辊71对应的第四镀膜展平辊、第四镀膜过辊。高分子基膜依次绕过第三镀膜展平辊、第三镀膜冷辊61、第三镀膜过辊,并通过第三蒸发机构62完成单侧的功能镀层的蒸镀;而后高分子基膜依次绕过第四镀膜展平辊、第四镀膜冷辊71、第四镀膜过辊,并通过第四蒸发机构72完成另一侧的功能镀层的蒸镀。
43.在具体实现过程中,缓冲层可以为ti及ti合金、cr及cr合金,功能镀层多采用金属膜层、金属化合物膜层等,本实施例可以采用金属ti为缓冲层,金属al为功能镀层,镀膜后的涂层(包括缓冲层、功能镀层)总厚度为150nm。
44.实施例4如图4所示,与实施例1不同的是,本实施例在进行紫外辐射装置辐照前先通入微量含氧气氛,即在紫外辐射装置12与放卷辊10之间还设有微量气体布气管道13,微量气体布气管道13置于高分子基膜31的单侧或双侧,其用于向高分子基膜31表面输送含氧气氛。
45.本实施例采用蒸镀方式进行镀膜,采用微量气体布气管道13通入微量含氧气氛,
用于生成增强层(例如氧化铝)。由于只是通入了微量含氧气氛,并且含氧气氛已经形成了单键氧、双键氧的基团,加之微量气体布气管道13与蒸发镀膜处有一定的距离,因此,通入的含氧气氛几乎不会对蒸发镀膜产生影响;并且,含氧气氛形成的含氧基团,在与金属化学键合形成作为增强层的氧化层时,已经被消耗完,因此不会对后续形成功能镀层造成影响。
46.实施例5如图5所示,与实施例2不同的是,本实施例在紫外辐射装置12与放卷辊10之间还设有微量气体布气管道13。
47.实施例6如图6所示,与实施例3不同的是,本实施例在紫外辐射装置12与放卷辊10之间还设有微量气体布气管道13。
48.实施例7如图7所示,与实施例4不同的是,本实施例采用溅射镀膜方式进行功能镀层的镀膜,即在第一镀膜冷辊41的外围设置多个第一靶材45,通过第一靶材45进行溅射镀膜。
49.本实施例采用溅射镀膜方式进行镀膜,溅射镀膜过程中需要通入用于溅射的气体。二本实施例在放卷辊10出膜端采用微量气体布气管道13通入含氧气氛,溅射气体的浓度的量远大于含氧气氛,并且由于大量溅射气体的扩散,含氧气氛不会扩散至溅射镀膜处,加之微量气体布气管道13与溅射镀膜处有一定的距离,因此,通入的含氧气氛,不会对溅射镀膜产生影响。
50.实施例8如图8所示,与实施例5不同的是,本实施例采用溅射镀膜方式进行功能镀层的镀膜,即在第一镀膜冷辊41的外围设置多个第一靶材45,通过第一靶材45进行溅射镀膜;在第二镀膜冷辊51的外围设置多个第二靶材55,通过第二靶材55对高分子基膜的另一侧进行溅射镀膜。
51.实施例9如图9所示,如实施例6不同的是,本实施例采用溅射镀膜方式进行缓冲层和功能镀层的镀膜,即在第一镀膜冷辊41的外围设置多个第一靶材45,通过第一靶材45对高分子基膜31的一侧溅射镀膜形成缓冲层;在第二镀膜冷辊51的外围设置多个第二靶材55,通过第二靶材55对高分子基膜的另一侧溅射镀膜形成缓冲层;在第三镀膜冷辊61的外围设置多个第三靶材63,通过第三靶材63对高分子基膜31的一侧溅射镀膜形成功能镀层;在第四镀膜冷辊71的外围设置多个第四靶材73,通过第四靶材73对高分子基膜的另一侧溅射镀膜形成功能镀层。
52.在上述实施例中,蒸发镀膜得具有蒸发机构;溅射镀膜得具有靶材,并通入气体,比如氩气。并且,在一个真空腔室内,当需要对高分子基膜两侧进行镀膜时采用两个镀膜冷辊,并且两个镀膜冷辊的位置采用相同的镀膜方式,例如两个都是蒸发镀膜,或两个都是溅射镀膜。
53.需要指出的是,上述镀膜过程均在真空环境中进行;当溅射镀膜时,需要通入用于溅射的气体。当加入微量气体布气管道时,由于通入含氧气氛的浓度远小于溅射气体的浓度,并且大量溅射气体的扩散,使得含氧气氛不会扩散至溅射镀膜处;加之,微量气体布气管道与溅射镀膜处有一定的距离,因此,通入的含氧气氛不会对溅射镀膜产生影响。
54.如图10、图11所示本发明还提供了一种镀膜产品,该镀膜产品的粘附力相比于改善前提升100%以上,其附着力达到600n/m。该镀膜产品包括高分子基膜、位于高分子基膜表面的功能镀层,高分子基膜与功能镀层之间设有用于增强功能镀层与高分子基膜之间粘附力的增强层,增强层由镀层材料与高分子基膜表面的活性界面化学键合形成。
55.具体的,在图10中,该镀膜产品30包括高分子基膜31、作为功能镀层的铝层33、高分子基膜31与铝层33之间的氧化铝层32,氧化铝层32作为增强层,其由铝层33的原料铝金属与高分基膜31表面的活性界面化学键合形成。该镀膜产品直接镀铝形成,金属铝的材料接触高分子基膜31表面时,先形成氧化铝层32,再形成铝层33。功能镀层(铝层33)的厚度按照产品需要控制在200nm~1500nm之间,增强层(氧化铝层33)的厚度为10nm以内;当加入图4或图7所示的微量气体布气管道并通入含氧气氛时,氧化铝层会更厚(大于10nm,且不大于25nm),粘附力更强。
56.如图11所示的优选的实施例中,高分子基膜与功能镀层之间还设有缓冲层,增强层位于缓冲层与高分子基膜之间,且增强层由缓冲层的原材料与高分子基膜表面的活性界面化学键合形成。
57.具体的,在图11中,该镀膜产品30包括高分子基膜31、作为功能镀层的铝层33,高分子基膜31与铝层33之间设有作为增强层的钛氧化物层34(tiox层)、作为缓冲层的钛层35,其中增强层由缓冲层的原材料-钛与高分子基膜31表面的活性几面化学键合形成。
58.在形成功能镀层(铝层33)之前,先形成钛氧化物层34,再形成钛层35,最后形成铝层33。当加入微量气体布气管道并通入含氧气氛时钛氧化物层34更厚,粘附力更强。在一个实例中,通入含氧气氛时的钛氧化物层35厚度在25nm以内(没有微量含氧气氛的输入时则一般在10nm以内),钛层35的厚度为200 nm~800nm,铝层33为200nm~800nm。
59.上述具体实施例中,采用铝层为功能镀层,其可以采用蒸发镀膜和溅射镀膜的方式;功能镀层还可以为铜层,其也可以采用蒸发镀膜和溅射镀膜的方式。
60.本发明还提供对比实验。
61.以基础实施例
‑‑‑
实施例1为例进行说明。首先不开启紫外辐射装置情况下,得到镀膜样品aa1,在开启紫外辐射装置情况下得到带有增强层的镀膜样品aa2。
62.1、对比镀膜样品aa1与镀膜样品aa2的粘附力性能。
63.分采用1000n/m的剥离力的20mm宽的胶带贴敷在镀膜样品aa1与镀膜样品aa2的表面,然后采用拉力机进行180
°
方式、50mm/min的速度进行拉伸测试涂层粘附力的大小。结果不开启紫外辐照的镀膜样品aa1的粘附力达到287n/m,而镀膜样品aa2达到了749n/m的粘附力。
64.通过本发明方式进行增强后,镀膜样品粘附性能得到显著的提升。
65.2、对比镀膜样品aa1与镀膜样品aa2的粘附性能。
66.本发明还模拟锂离子电池用的电解环境,分别将镀膜样品aa1与镀膜样品aa2在化学药剂中浸泡后测试其粘附性能。
67.采用常规的锂离子电池用电解液浸泡封装后,在85℃温度下烘烤72小时,镀膜样品aa1和镀膜样品aa2还保持良好的粘附性能,粘附力分别为镀膜样品aa1:213n/m、镀膜样品aa2:688n/m。两者分别为原始状态的74%和92%。
68.因此,通过本发明的方式进行增强后,镀膜样品aa2样品保持了良好的粘附性能优
势。
69.3、对比镀膜样品aa1与镀膜样品aa2的力学强度。
70.以10mm宽度的样品为例,50mm/min的拉伸速度测试样品的拉伸强度,其中镀膜样品aa1的拉伸强度可以达到195mpa,而镀膜样品aa2的强度可以达到231mpa。
71.本发明通过上述高分子基膜表面处理方法和设备,可以实现高分子基膜的无污染表面处理,其相对于传统的无表面处理而直接沉积镀层的薄膜相比,粘附性能提升了一倍以上,并且由于本发明采用化学键合的方式形成增强层,使得作为增强层的金属氧化物成分可以起到界面钝化的作用,所沉积的薄膜材料具有更为优异的耐化学药剂的效果,并且其力学强度(拉伸强度)得到了明显提升。
72.应当理解的是,对本领域普通技术人员来说,可以根据上述说明加以改进或变换,而所有这些改进和变换都应属于本发明所附权利要求的保护范围。
73.上面结合附图对本发明专利进行了示例性的描述,显然本发明专利的实现并不受上述方式的限制,只要采用了本发明专利的方法构思和技术方案进行的各种改进,或未经改进将本发明专利的构思和技术方案直接应用于其它场合的,均在本发明的保护范围内。