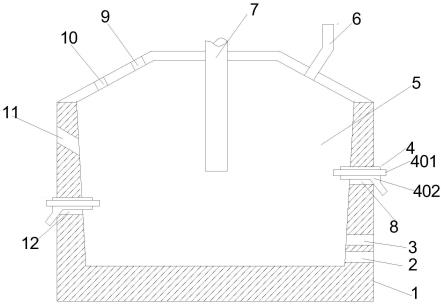
1.本发明涉及金属冶炼技术领域,具体涉及一种用氢还原铁的矿热炉设备和方法。
背景技术:2.在传统的方法生产生铁时,在矿热炉中以碳作为燃料产生热能,同时又作为还原剂,将铁矿石还原为铁的。这种传统方法存在诸多的缺陷,比如在生产过程产生了大量的一氧化碳。由于国际上对环保的要求不断提高,特别对碳的排放也不断提出更高的要求。因此,如何提升技术装备水平,优化生产工艺来减少一氧化碳的产生成了国内外冶金行业急需解决的问题。
3.目前,有在高炉冶炼铁的过程中加入一定量的氢气,从而减少一氧化碳的产生,减少碳排放的方法;也有用直接还原法生产纯铁,即在一定温度、压力下用氢作为还原剂生产纯铁。中国发明专利cn202011238747.2公开了一种利用可再生能源电的方法,利用可再生能源电进行电解水生产氢气和氧气,氢气进入气基竖炉作为还原剂生产海绵铁。但其设备复杂,生产难度大,产量小,生产成本高,对原料要求较高,且生产的还原铁呈粉状运输困难,钢铁企业也无法将这种粉状的还原铁产品直接作为炼钢原料来使用,需要在使用前先加工成压铁块。
技术实现要素:4.本发明的目的在于解决现有技术中存在的用氢作为还原剂生产纯铁的技术难度大,产量小,生产成本高,且产品不能直接作为炼钢材料被使用的问题,提供一种用氢还原铁的矿热炉设备和方法。
5.为解决上述技术问题,本发明采用的技术方案如下:一种用氢还原铁的矿热炉设备,所述矿热炉设备包括炉壳,所述炉壳内设置有炉腔,所述炉壳包括顶部、底部和侧壁,所述炉壳侧壁的下端部设置有排渣口和出铁口,所述出铁口靠近炉壳底部设置,所述排渣口设置在出铁口上方;所述炉壳侧壁上设置有多个侧吹风口,所述多个侧吹风口远离出铁口设置,所述每个侧吹风口内均设置有吹风套管;所述炉壳侧壁的上端设置有多个取样口,所述取样口设置在多个侧吹风口上方;所述炉壳顶部中心设置有电加热棒,所述电加热棒从上而下贯穿炉壳顶部向炉腔内延伸,所述炉壳顶部上设置有多个进料口、热风口和排烟口。
6.优选地,所述多个侧吹风口呈上、下两排设置,分别为上排侧吹风口和下排侧吹风口,所述上排侧吹风口设置在炉壳侧壁的中部,所述下排侧吹风口间隔设置在上排侧吹风口的下方。
7.优选地,所述吹风套管包括中心管和环缝管,所述环缝管空心套设在中心管外,所述中心管和环缝管之间设置有环形风道。
8.本发明同时提供了在上述矿热炉设备中用氢还原铁的方法,其特征在于,包括以下步骤:
9.s1、在矿热炉设备中加入生铁块和炉渣作为底料,通电熔化,形成初始熔池;加入
原料,并通过上、下两排侧吹风口的中心管和环缝管送入氮气,形成稳定熔池;
10.s2、待矿热炉中原料完全熔化,且炉渣温度≧1510℃,开始主还原阶段操作,时间为0.9~1.5小时,切换矿热炉上、下排侧吹风口的中心管气体为氢气和氮气的混合气体,上排侧吹风口的环缝管仍配氮气;切换下排侧吹风口的环缝管为氮气和细铁精粉的混合物,所述混合物中细铁精粉的含量为0.5~5kg/m3;当矿热炉渣层上方氢气含量≧28%,开始供应热风。
11.s3、停止热风供应,开始终还原阶段操作,时间为0.65~0.9小时,向矿热炉中加入预还原度大于63%直接还原铁,上、下两排侧吹风口的环缝管中气体及流量与s2保持一致;上、下两排侧吹风口的中心管通氢气加氮气的混合气体,氢气和氮气比例为1:3,流量为83~92m3/min,压力为0.6~0.81mpa,待炉渣温度降到1150~1200℃,增加侧风口中心管氢气比例,炉渣温度降至1100~1150℃时,中心管中全部为氢气;
12.优选地,所述s1中原料为经过干燥预还原的含铁原料和造渣材料,所述经过干燥预还原的含铁原料包括尾矿、矿粉矿、低品位矿石中的一种或几种。
13.优选地,所述s1中,中心管的氮气流量为25~29m3/min,环缝管的氮气流量为11~14m3/min。
14.优选地,所述s2中,所述上排侧吹风口的中心管混合气体的流量为109~125m3/min,压力0.6~0.82mpa,氢气和氮气的重量比为1:0.2~5,环缝管氮气流量为26~32m3/min,压力0.5~0.59mpa;所述下排侧吹风口的中心管混合气体的流量为117~132m3/min,压力0.6~0.72mpa,氢气和氮气的重量比为1:0.2~5,环缝管的混合物流量为29~37m3/min,压力为0.5~0.61mpa。
15.进一步优选,所述s2中,热风流量为15~20m3/min,热风温度为1150~1250℃。
16.进一步优选,所述s3中,预还原度大于63%直接还原铁的添加量为矿热炉中熔体重量的20~30%。
17.进一步优选,所述s3中,加入造渣剂调节炉渣ph值为1.2~1.4。
18.本发明优化了矿热炉的炉体设计,在炉壳上采用从侧风口喷吹氢气和炉顶热风口通入热空气的技术,达到较高的二次燃烧率和二次燃烧传热效率。矿热炉的炉壳上设置上、下两排侧吹风口,侧吹风口中均设置有吹风套管,该吹风套管为中心管和环缝管套设的双层套管。该侧吹结构设计中,侧吹风口在渣层位置附近分上下两层排布。还原过程中,保护气体n2和细粒度铁精粉从较低的下排侧风口喷入到熔融的渣层中,对渣层进行必要的搅拌,同时与渣层中大量金属铁进行反应,生成feo。还原氢气从较高的上排侧风口中从熔池表面喷入,将渣中feo还原成金属铁。同时溢出的未还原氢气在炉顶热风口吹入的热空气(不低于1150℃)下进行二次燃烧,来熔化炉顶加入的固体原料,大大提高能源利用效率。熔池上部反应强烈,二次燃烧传热速度快。侧边喷吹引起熔池强烈的搅拌和产生大量液滴,为在熔池上方形成一个理想的传热区提供了有利的条件。金属液滴就像喷泉形成的喷溅那样进入上部空间,将燃烧区的热量迅速带入熔池,使渣中金属铁与feo含量形成梯度分布,可获得最佳还原效果。调节喷吹气体中氮气和氢气比例,还可控制金属铁生成速度。
19.本发明采用大渣量操作,熔渣和炉料的体积比0.8~1.2。熔渣中的氢一部分直接将其中液态铁氧化物还原成铁滴,其他部分在渣中循环并与热风中的氧进行部分燃烧。大渣量操作可吸收二次燃烧热量,阻止铁液的喷溅,同时可有效地降低渣中含铁量,减少粉尘
逃逸,以及防止金属铁再氧化。
20.本发明所具有的有益效果:
21.一)本发明将氢用喷吹法加入到用电能熔化的矿料熔液中,通过氢的喷吹使矿料熔液形成一定流场,使氢与铁氧化物之间充分发生化学反应,从而实现生铁的高效冶炼;本发明在主还原阶段喷入氢气的同时喷入氮气和细铁精粉的混合物,使得熔池搅拌作用加强,并加速铁的高阶氧化物还原速度,从而进一步提高生铁的产出效率,显著提高生铁产量;
22.二)本发明仅需在现有矿热炉的炉壳上增加上、下两排侧吹风口,即完成对矿热炉的改造,该结构改造简单,不复杂,不改变矿热炉主体结构,改造成本低,适于在工业中广泛推广应用;
23.三)本发明中用氢代替碳作为还原剂,氢与氧结合生成的h2o,使生产铁的过程中没有了一氧化碳和二氧化碳的产生,彻底改变了传统工艺碳还原铁的方式,有效减少生产过程中的碳排放;
24.四)本发明中使用的原料为经过干燥预还原的含铁原料,主要含有粒度大于3mm,铁含量小于40%的尾矿、矿粉矿和低品位矿石,同时加入部分冶金含铁废料,进行混合配料,保证其中总铁含量tfe≥45%;含铁原料中的尾矿、矿粉矿和低品位矿石都属于采矿产生的废弃物,利用废弃物来实现生铁的高效冶炼,达到废物利用目的,减少环境污染,同时也显著降低生产成本;
25.五)本发明中熔炼的主要能源为电能,通入的氢气也可作为辅助燃料降低电耗能,同时在还原过程中通过吹入热空气,获得高的二次燃烧率,进一步提高能量利用率,从而进一步降低生产成本。
附图说明
26.图1为本发明中矿热炉设备的结构示意图。
27.图中:1-炉壳,2-出铁口,3-排渣口,4-吹风套管,401-中心管,402-环缝管,5-炉腔,6-排烟口,7-电加热棒,8-上排侧吹风口,9-热风口,10-进料口,11-取样口,12-下排侧吹风口。
具体实施方式
28.下面结合附图和具体实施例对本发明作进一步的说明。
29.实施例1一种用氢还原铁的矿热炉设备
30.一种用氢还原铁的矿热炉设备,矿热炉设备包括炉壳1,炉壳1内设置有炉腔5,炉壳包括顶部、底部和侧壁,炉壳5侧壁的下端部设置有排渣口3和出铁口2,出铁口靠近炉壳底部设置,排渣口3设置在出铁口2上方;炉壳5侧壁上设置有多个侧吹风口,多个侧吹风口远离出铁口设置,每个侧吹风口内均设置有吹风套管;多个侧吹风口呈上、下两排等数设置,分别为上排侧吹风口8和下排侧吹风口12,上排侧吹风口8设置在炉壳侧壁的中部,下排侧吹风口12间隔设置在上排侧吹风口8的下方。吹风套管包括中心管401和环缝管402,环缝管402空心套设在中心管401外,中心管401和环缝管402之间设置有环形风道,中心管401和环缝管402可分别通入不同的气体;炉壳5侧壁的上端设置有2个取样口11,取样口11设置在
侧吹风口上方;炉壳1顶部中心设置有电加热棒7,电加热棒7贯穿炉壳1顶部向炉腔5内延伸,炉壳1顶部上设置有进料口10、热风口9和排烟口6。
31.本实施例中,进料口10设置有进料系统,排烟口6设置有烟气排除系统,取样口11设置有取样系统;进料系统、烟气排除系统和取样系统均为现有技术。进料系统可实现自动上料、自动称重、自动下料。取样系统在炉腔5不同部位设置取样口11,采用小枪型取样机定期收集铁水和渣样,连续分析炉气成分以计算二次燃烧率,并调整热空气供给量;渣中的铁水用取样杯浸入渣中取得,并取废气中的灰尘样。烟气排出系统通过外接高温风机,将烟气抽出矿热炉外,经过沉积室,去除粗颗粒、烟尘等,再经过燃烧器,使可燃气体燃尽,然后通过热风口9重新进入炉腔5内用于物料的加热。
32.实施例2在矿热炉设备中用氢还原铁的工艺
33.矿热炉设备如实施例1所示,在矿热炉设备中用氢还原铁,具体步骤如下:
34.1.向矿热炉炉腔中先加入生铁块和炉渣作为底料,然后通电熔化,形成初始熔池。生铁块和炉渣为本技术领域的常用材料,生铁块加入重量为原料总重量的控制目标值是22%;炉渣加入重量为原料总重量的控制目标值是15.5%。
35.将经过干燥预还原的含铁原料和造渣材料输送到矿热炉中,装料及熔化过程中,分别向侧吹风口的中心管配氮气控制目标值为25m3/min、环缝管配氮气控制目标值为11m3/min。经过干燥预还原的含铁原料包括粒度大于3mm,铁含量小于40%的矿粉矿,同时加入部分冶金含铁废料,进行混合配料,使含铁原料的总铁含量tfe为48%;造渣材料包括石灰石、轻烧白云石和萤石,均参考现有技术制备。
36.2.主还原阶段操作。待炉中物料完全熔化,通过矿热炉的自动测温系统,观察炉内温度情况,当炉渣温度达到1510℃,开始主还原阶段操作。
37.根据在线成分分析系统确定炉渣、铁水成分,初步计算理论氢气消耗量,理论氢气消耗量的计算方程式如表1所示,生产1t铁水需要2.08t左右的经过干燥预还原的含铁原料。相应的,生产1t铁水消耗氢气量为900m3左右(氢气利用率67%)。开始配气操作。开始切换上排侧吹风口的中心管气体为氢气加氮气,流量控制目标值为125m3/min,压力0.6mpa,环缝管仍配氮气,流量控制目标值为32m3/min,压力0.5mpa;下排侧吹风口的中心管气体为氢气加氮气,流量控制目标值为128m3/min,压力0.6mpa,环缝管为氮气加细铁精粉(购买得到),流量控制目标值为29m3/min氮气,所述混合物中细铁精粉的含量控制目标值为1.5kg/m3,压力0.5mpa。上下两排侧吹风口的中心管具体氢气与氮气比例,根据化渣情况逐步增加,具体如表2所示。
38.表1理论计算氢气消耗量的反应方程式
39.反应方程式耗氢量/kgfe2o3+3h2==2fe+3h2o1000*55%*95%/55.85*2*1.5=28
ꢀꢀ
fe2o3+h2==2feo+h2o1000*55%*5%/55.85*2*0.5=0.49
40.在计算氢气的理论消耗量时,假设fe以fe2o3形态存在,不考虑其他氧化物的还原,其中fe2o3的95%还原为fe,5%还原为feo,通入的纯氢有100%用于还原氧化物,以1吨铁矿石为例,具体耗氢量如表1所示。
41.表2上下两排侧吹风口的中心管具体氢气与氮气比例
[0042][0043][0044]
根据在线分析仪显示熔渣上表面炉气成分,炉气中h2达到30%,打开热风管,控制热风流量目标值为15m3/min,热风温度目标值为1150℃,形成二次燃烧,加速还原。当初步达到理论计算氢气消耗量后,即降低风口中心管、环缝管流量,根据自动测温系统显示炉内炉渣温度,配电操作配合冶炼温度需要进行相应操作,控制炉内熔渣温度目标值为1560℃。主还原阶段时长为1.5小时。
[0045]
3.终还原操作。停止热风口的热空气供应。进料系统从进料口加入预还原度目标值为63%直接还原铁(现有方法制备),并加入造渣剂调整炉渣的碱度目标值为1.28。
[0046]
上下两排侧吹风口的环缝管中气体流量及气体类型均不变,中心管通氢气加氮气,控制比例目标值为1:3,流量控制目标值为83m3/min,压力0.6mpa。炉渣温度降到1200℃,增加中心管氢气比例,直至全部为氢气。
[0047]
结合在线成分分析系统得到的铁水成分与人工取样结果,铁含量及其他元素含量满足出炉要求,即可完成脱氧操作。终还原阶段时长为0.9小时。
[0048]
4.出铁操作。将合格铁水从出铁口流出并浇铸成铁块,渣从出渣口流出。本实施例中金属铁的回收率为88%。
[0049]
实施例3
[0050]
矿热炉设备如实施例1所示,在矿热炉设备中用氢还原铁,具体步骤如下:
[0051]
1.向矿热炉炉腔中先加入生铁块和炉渣作为底料,然后通电熔化,形成初始熔池。生铁块和炉渣为本技术领域的常用材料,生铁块加入重量为原料总重量的控制目标值是25%;炉渣加入重量为原料总重量的控制目标值是17%。
[0052]
将经过干燥预还原的含铁原料和造渣材料输送到矿热炉中,装料及熔化过程中,分别向侧吹风口的中心管配氮气控制目标值为27m3/min、环缝管配氮气控制目标值为14m3/min。经过干燥预还原的含铁原料包括粒度大于3mm,铁含量小于40%的尾矿、矿粉矿和低品位矿石,同时加入部分冶金含铁废料,进行混合配料,使含铁原料的总铁含量tfe为52%;造渣材料包括石灰石、轻烧白云石和萤石,均参考现有技术制备。
[0053]
2.主还原阶段操作。待炉中物料完全熔化,通过矿热炉的自动测温系统,观察炉内温度情况,当炉渣温度达到1520℃,开始主还原阶段操作。
[0054]
根据在线成分分析系统确定炉渣、铁水成分,初步计算理论氢气消耗量,理论氢气消耗量的计算方程式如实施例2中表1所示,生产1t铁水需要1.92t左右的经过干燥预还原的含铁原料。相应的,生产1t铁水消耗氢气量为833m3左右(氢气利用率72%)。开始配气操作。开始切换上排侧吹风口的中心管气体为氢气加氮气,流量控制目标值为118m3/min,压力0.75mpa,环缝管仍配氮气,流量控制目标值为29m3/min,压力0.55mpa;下排侧吹风口的中心管气体为氢气加氮气,流量控制目标值为132m3/min,压力0.65mpa,环缝管为氮气加细
铁精粉(购买得到),流量控制目标值为33m3/min,所述混合物中细铁精粉的含量控制目标值为2.4kg/m3,压力0.58mpa。上下两排侧吹风口的中心管具体氢气与氮气比例,根据化渣情况逐步增加,具体如实施例2中表2所示。
[0055]
根据在线分析仪显示熔渣上表面炉气成分,炉气中h2达到32%时,打开热风管,控制热风流量在17m3/min,控制热风温度目标值为1210℃,形成二次燃烧,加速还原。当初步达到理论计算氢气消耗量后,即降低风口主管、环缝流量,根据自动测温系统显示炉内炉渣温度,配电操作配合冶炼温度需要进行相应操作,控制炉内熔渣温度目标值为1530℃。主还原阶段时长为1.1小时。
[0056]
3.终还原操作。停止热风口的热空气供应。进料系统从进料口加入预还原度控制目标值为70%直接还原铁(现有方法制备),并加入造渣剂调整炉渣的碱度控制目标值为1.32。
[0057]
上下两排侧吹风口的环缝管中气体流量及气体类型均不变,中心管通氢气加氮气,控制比例目标值为1:3.2,流量目标控制值为89m3/min,压力0.75mpa。炉渣温度降到1150℃,增加中心管氢气比例,直至全部为氢气。
[0058]
结合在线成分分析系统得到的铁水成分与人工取样结果,铁含量及其他元素含量满足出炉要求,即可完成脱氧操作。终还原阶段时长为0.78小时。
[0059]
4.出铁操作。将合格铁水从出铁口流出并浇铸成铁块,渣从出渣口流出。本实施例中金属铁的回收率为92%。
[0060]
实施例4
[0061]
矿热炉设备如实施例1所示,在矿热炉设备中用氢还原铁,具体步骤如下:
[0062]
1.向矿热炉炉腔中先加入生铁块和炉渣作为底料,然后通电熔化,形成初始熔池。生铁块和炉渣为本技术领域的常用材料,生铁块加入重量为原料总重量的目标控制值是28%;炉渣加入重量为原料总重量的目标控制值是18.5%。
[0063]
将经过干燥预还原的含铁原料和造渣材料输送到矿热炉中,装料及熔化过程中,分别向侧吹风口的中心管配氮气目标控制值为29m3/min、环缝管配氮气目标控制值为13m3/min。经过干燥预还原的含铁原料包括粒度大于3mm,铁含量小于40%的尾矿、矿粉矿和低品位矿石,同时加入部分冶金含铁废料,进行混合配料,使含铁原料的总铁含量tfe为65%;造渣材料包括石灰石、轻烧白云石和萤石,均参考现有技术制备。
[0064]
2.主还原阶段操作。待炉中物料完全熔化,通过矿热炉的自动测温系统,观察炉内温度情况,炉渣温度达到1550℃,开始主还原阶段操作。
[0065]
根据在线成分分析系统确定炉渣、铁水成分,初步计算理论氢气消耗量,理论氢气消耗量的计算方程式如实施例2中表1所示,生产1t铁水需要1.54t左右的经过干燥预还原的含铁原料。相应的,生产1t铁水消耗氢气量为750m3左右(氢气利用率80%)。开始配气操作。开始切换上排侧吹风口的中心管气体为氢气加氮气,流量控制目标值为109m3/min,压力0.82mpa,环缝管仍配氮气,流量控制目标值为26m3/min,压力0.59mpa;下排侧吹风口的中心管气体为氢气加氮气,流量控制目标值为117m3/min,压力0.72mpa,环缝管为氮气加细铁精粉(购买得到),流量控制目标值为37m3/min,压力0.61mpa。上下两排侧吹风口的中心管具体氢气与氮气比例,根据化渣情况逐步增加,具体如实施例2中表2所示。
[0066]
根据在线分析仪显示熔渣上表面炉气成分,炉气中h2达到28%时,打开热风管,控
制热风流量目标值为20m3/min,控制热风温度目标值为1250℃,形成二次燃烧,加速还原。当初步达到理论计算氢气消耗量后,即降低风口主管、环缝流量,根据自动测温系统显示炉内炉渣温度,配电操作配合冶炼温度需要进行相应操作,控制炉内熔渣温度目标值为1518℃。主还原阶段时长为0.9小时。
[0067]
3.终还原操作。停止热风口的热空气供应。进料系统从进料口加入预还原度控制目标值为75%直接还原铁(现有方法制备),并加入造渣剂调整炉渣的ph值控制目标值为1.38。
[0068]
上下两排侧吹风口的环缝管中气体流量及气体类型均不变,中心管通氢气加氮气,控制比例目标值为1:2.9,流量控制在92m3/min,压力0.81mpa。炉渣温度降到1100℃,增加中心管氢气比例,直至全部为氢气。
[0069]
结合在线成分分析系统得到的铁水成分与人工取样结果,铁含量及其他元素含量满足出炉要求,即可完成脱氧操作。终还原阶段时长为0.65小时。
[0070]
4.出铁操作。将合格铁水从出铁口流出并浇铸成铁块,渣从出渣口流出。本实施例中金属铁的回收率为93.5%。
[0071]
综上所述,本发明对现有矿热炉进行简单的结构改造,增加上、下两排侧吹风口(实施例1),将氢用喷吹法加入到用电能融化的矿粉熔液中,同时喷入氮气和细铁精粉的混合物,使氢与铁氧化物之间充分发生化学反应,显著提高尾矿、矿粉和低品位矿石原料中生铁的产出效率,对总铁含量48%≦tfe≦65%的含铁原料中金属铁的回收率达到了88%以上(实施例2-实施例4数据),实现了生铁的高效冶炼和对矿石废物(铁含量小于40%的尾矿、矿粉和低品位矿石)的再利用,减少资源浪费。
[0072]
本发明的说明书和附图被认为是说明性的而非限制性的,在本发明基础上,本领域技术人员根据所公开的技术内容,不需要创造性的劳动就可以对其中一些技术特征做出一些替换和变形,均在本发明的保护范围内。