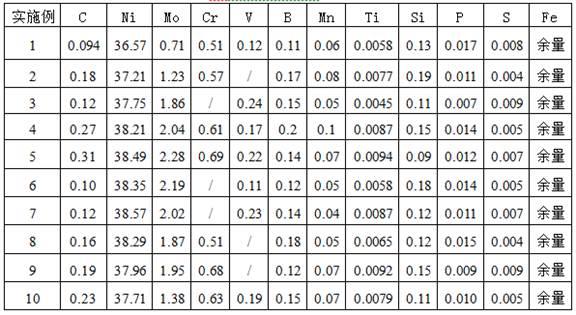
1.本发明属于低膨胀合金技术领域,具体涉及一种高强高导电率低膨胀铁镍钼合金丝材及其生产方法。
背景技术:2.传统的低膨胀铁镍、铁镍钴合金,具有较低的线膨胀系数,广泛应用于电器仪表、能源运输、通讯装备等领域。近年来,高强低膨胀铁镍、铁镍钴合金在电力运输、航空工业领域展现出极大的应用潜力,特别在电力传输领域,是制备倍容量导线无可替代的关键核心材料。目前铁镍、铁镍钴合金的强化方式有固溶强化、加工硬化、时效强化等。但上述强化方式为提高合金强度,通常会添加大量合金元素,抑或在基体中生成大量析出相,影响低膨胀合金的膨胀系数及导电率。
技术实现要素:3.为解决上述技术问题,本发明提供一种高强高导电率低膨胀铁镍钼合金丝材及其生产方法。本发明采取的技术方案是:一种高强高导电率低膨胀铁镍钼合金丝材,其化学成分组成及质量百分含量为:c:0.09~0.32%,ni:36.5~38.7%,mo:0.7~2.3%,b:0.1~0.2%,mn≤0.1%,ti≤0.01%,si≤0.2%,p≤0.02%,s≤0.01%,以及v:0.1~0.25%和cr:0.5~0.7%中的至少一种元素,余量为铁和不可避免的杂质。
4.所述c、mo、v、cr四种元素的质量百分含量满足关系式:c=0.6~1.1(0.045mo +0.2 v+0.2 cr)。
5.所述铁镍钼合金丝材φ2~6mm,抗拉强度≥1150mpa,20℃导电率≥2%iacs,室温~230℃热膨胀系数≤2.4
×
10-6
/℃。
6.上述高强高导电率低膨胀铁镍钼合金丝材的生产方法,包括真空熔炼、保护气氛电渣重熔二次精炼、锻造、轧制、固溶处理、冷拔、时效热处理工序;(1)真空熔炼工序:出钢浇铸温度控制在1460~1480℃;(2)保护气氛电渣重熔二次精炼工序:电渣精炼前20~30min向电渣炉内通入高纯氩气作为保护气;补缩期分两段补缩,电压在45~40v、电流在6k~4ka内递减,每段时间控制在2~4min;(3)锻造工序:包括加热、锻造、冷却步骤;所述加热步骤,采用三段式加热,第一段为升温至800~900℃,保温2~3h;第二段为升温至1180~1220℃,保温4~6h;第三段为随炉冷却至1150~1170℃,保温0.5~1h;所述锻造步骤,采用单向拔长的方式,锻造温度900~1100℃,锻造过程的送进量l=0.5~0.8h,单次压下量δh<18%h,端部锻造送进量a>0.4h;其中,h为锻件厚度,mm;δh为单次压下量,mm;a为端部锻造送进量,即开锻时端部的送进量,mm;锻造得到截面尺寸为135mm
×
135mm~150mm
×
150mm的方坯;
所述冷却步骤,冷却至方坯表面温度≤300℃;(4)轧制工序:方坯在1130~1180℃保温2~3h,之后进行粗轧,出钢温度≥900℃;中间补温至950℃后进行精轧,轧制为φ8~12mm的盘条,吐丝温度800~850℃;(5)固溶处理工序:在加热炉内通入氮气进行保护;盘条装炉前,加热炉先进行预热,升温至800~850℃保温1h以上,在盘条完全冷却前装炉;装炉后,采用两段式加热,第一段为升温至1050~1110℃,保温0.5h;第二段为升温至1190~1220℃进行保温,保温时间t1=1.5+0.1 d1,之后出炉水冷;t1为保温时间,h;d1为轧制后盘条的直径,mm;(6)冷拔工序:包括剥皮、拉拔步骤;剥皮前先进行喷丸处理,之后采用车刀剥皮+双砂带打磨方式进行剥皮;拉拔过程,除最后一道次拉拔无减面率要求外,其他道次的减面率按如下控制:当d2>6mm时,单道次减面率为25~30%;当d2≤6mm时,单道次减面率为20~25%;d2为拉拔过程中丝材的直径,mm;(7)时效热处理工序:在氢气气氛保护下,在550~630℃进行热处理,热处理时间t2=0.25d,t2为热处理时间,h;d为铁镍钼合金丝材的直径,mm。
7.所述保护气氛电渣重熔二次精炼工序,电渣精炼过程中控制熔速在4.3
±
0.3kg/min。
8.所述锻造工序,加热步骤,第一段的升温速率为100~150℃/h,第二段的升温速率为150~180℃/h;冷却步骤,采用缓冷坑缓冷或砂冷的方式。
9.所述固溶处理工序,采用井式加热炉进行,根据加热炉的容量,每立方米氮气的通气量为4~6.5l/min。
10.所述固溶处理工序,两段式加热,第一段的升温速率为150~180℃/h;第二段的升温速率为100~120℃/h。
11.所述冷拔工序,剥皮前,先使用1~1.5mm沙粒进行喷丸处理,去除表面松散氧化皮;车刀剥皮总去除量≤0.4mm;双砂带打磨过程中,单边打磨去除总量h与砂带机前、后砂带的规格满足:当h<0.1mm时,前、后砂带分别为240目、320目;当0.1≤h≤0.2mm时,前、后砂带分别为180目、320目;当h>0.20mm时,前、后砂带分别为80目、240目。
12.所述冷拔工序,拉拔过程总减面率≥70%,拉拔为φ2~6mm丝材。
13.本发明成分及工艺设计思路为:1、本发明在传统的低膨胀铁镍、铁镍钴合金的基础上,重新设计c含量以及主要合金元素cr、mo、v的含量,从成分的角度提高合金的导电率、降低热膨胀系数;通过控制c元素与cr、mo、v的配比关系,可保障合金基体在形成固溶强化的同时,有合适比例的合金元素通过后续固溶和时效强化处理后,形成稳定、细小弥散分布的第二相,以提高合金强度。
14.在本发明中通过在合金里添加c和cr、mo、v元素,在使合金产生固溶强化的同时,结合本发明所述的加工方法,使其析出细小弥散分布的第二相,从而提高合金的强度。
15.cr和v元素的加入虽然会提高合金的强度,但对合金的导电率有一定的影响。因此,为了保障合金的高导电率,可添加v、cr元素的1~2种,且v:0.1~0.25%,cr:0.5~0.7%。
16.为了保证合金中析出相的尺寸和分布状态,同时避免因析出相的导致合金热膨胀
系数的变化,对c 的加入量必须进行规定,碳的加入量应满足c=0.6~1.1(0.045mo+0.2v+0.2cr),在此条件下,可以保障cr、mo、v的碳化物的稳定、可控析出,同时避免过多的碳产生游离,能在合金保障高强度的同时,保持一定的韧性,并稳定合金的热膨胀系系数。
17.其中,各元素的作用及配比依据如下:c:碳元素是合金中的碳化物析出相的必要元素,与其他析出相元素共同决定了析出相的种类、大小和分布状态等。因此,碳元素必须保障一定的下限,以此来保障合金的析出;同时,过多的碳元素会造成碳化物析出相的过大、同时产生游离态的碳,恶化合金的强度、韧性及热膨胀性能。本发明c 含量设计为0.09~0.32%。
18.ni:ni是保证合金具备低膨胀性能的必需元素。本发明中由于在cr、mo、v元素的加入及后续碳化物的析出,会一定程度提高合金的热膨胀系数,因此必须适当提高ni的含量,本发明规定ni含量为36.5~38.7%。
19.mo:mo为碳化物析出元素,通过本发明中的加工工艺,可形成moc、mo2c等细小弥散析出相,提高合金的强度。但mo的加入量会导致成本上升和膨胀系数增大,将其上限规定为2.3%。
20.v、cr:v为0.1~0.25%,cr为0.5~0.7%。v和cr为碳化物析出元素,能提高合金强度,但过量添加则会生成粗大的碳化物;同时,v会降低合金的导电率,cr会增大膨胀系数,因此本发明规定可添加v、cr中的一种或者两种,且含量进行严格控制。
21.b:b元素能提高合金的热加工性能。
22.mn:mn虽然能提高合金的热加工性能,但影响合金的热膨胀性能和导电率,因此上限规定为0.1%。
23.ti:ti元素与c形成的碳化物在合金中难以回溶,影响合金的韧性,同时会影响合金的导电率,因此规定上限为0.01%。
24.si:si会增大合金的膨胀系数,将上限规定为0.2%。
25.p≤0.02%,s≤0.01%:p、s作为有害杂质元素,对其含量需严格控制,并且含量越低越好。
26.2、真空冶炼保证了合金的纯净度;保护气氛电渣重熔二次精炼后,钢中的s含量会处于较低的水平,同时电渣锭的铸态组织较中频锭的铸态组织要细小、致密,大大有利于后续加工。采用两段式补缩工艺,极大地提高了电渣锭上部整体的凝固质量,保证钢锭末端的凝固组织无明显疏松、气孔、夹渣等缺陷,补缩端几乎不需要切除。因此,利用真空冶熔炼+保护气氛电渣重熔二次精炼的制备方法在控制成分的同时,得到铸态组织细小、致密的电渣锭,保障了后续热加工的成材率。
27.3、本发明合金成分体系下,通过在加热过程中快速加热至800~900℃保温,可以有效避免合金在600~700℃的温区内孕育生成第二相组织,从而提高合金的变形抗力。同时,由于铸态组织中存在较大的枝晶、组织偏析,以及大尺寸的一次析出相。通过1180~1220℃下的高温扩散退火,可以促使一次析出相的回溶,改善枝晶组织以及组织偏析,提高合金的高温热塑性,降低合金的高温脆性区间;同时,本发明锻造方法中的压下量、锻造送进量、端部锻造送进量等要求,可大幅降低大尺寸的铸锭在开坯及精锻过程中的锻造开裂现象,减少锻坯面裂、角裂、折叠等表面缺陷的形成,且有助于铸锭内孔隙、疏松和气孔的焊合,提高锻坯的组织质量。
28.4、采用本发明所述的轧制方法,可在保障合金热加工性能的同时,提高轧制成材率;采用氮气保护方式,可大幅降低盘条在固溶处理中的氧化现象;采用盘条及加热炉的热装,可大幅提高生产效率,降低能耗及加热时间;两段式加热方式可保证合金在加热炉内能均匀升温,且在固溶温度下进行充分的固溶、降低盘条的抗拉强度,确保后续拉拔及时效热处理工艺的顺利进行。
29.5、采用车刀剥皮+双砂带打磨,可去除难以用酸洗方法去除的合金氧化皮;采用冷拔+时效退火工艺,区别于常规的冷拔+热处理+二次冷拔工艺,丝材最后的工艺为退火工艺,使用氢氮还原气氛,可对丝材表面起到光亮退火的作用,进一步降低表面的残留,得到高表面质量的合金丝材。
30.本发明适用于生产直径2~6mm的铁镍钼合金丝材,所生产的丝材抗拉强度≥1150mpa,20℃导电率≥2%iacs,15~230℃热膨胀系数≤2.4
×
10-6
/℃,具有高强度、低膨胀、高导电率等综合性能,且采用无co成分设计,能大幅降低合金原料成本。
具体实施方式
31.本发明高强高导电率低膨胀铁镍钼合金丝材的生产方法适用于生产直径2~6mm的丝材,包括真空熔炼、保护气氛电渣重熔二次精炼、锻造、轧制、固溶处理、冷拔、时效热处理工序;具体工艺步骤如下所述:(1)真空熔炼工序:包括原料准备、烘烤干燥、布料、冶炼、出钢浇注、脱模步骤。
32.①
原料准备:准备好真空冶炼炉熔炼需要合金料,具体包括:工业纯铁、电解镍板,金属铬、钼铁、钒铁、硼铁,低氮增碳剂;
②
烘烤干燥:锭模在100~120℃下烘烤≥12h;
③
布料:底层铺放镍板,加入铬、钼铁、钒铁,再放置铁棒和镍板;
④
冶炼:当炉内真空度达到15pa时,逐级提升加热功率,直至炉料完全熔清;炉料完全熔清后,充入氩气,开始加碳粉和硼铁,待熔清后,取样分析化学成分,补加各类合金料,直至成分符合要求;
⑤
出钢浇铸:出钢浇铸温度控制在1460~1480℃,浇铸模规格为φ180~200mm;
⑥
脱模:浇铸12h后进行脱模。
33.(2)保护气氛电渣重熔二次精炼工序:包括电渣前准备、电渣冶炼、电渣锭脱模工序。
34.①
电渣前准备:需要准备电极、引锭板、渣料;电极:将铸锭头尾利用锯床锯切平直,然后将锭身打磨至表面无氧化铁皮,利用焊条将铸锭头部与假电极焊接在一起;引锭板:选用30mm厚度,端面磨平、无锈的本合金切片,作为引锭板;渣料:选用成分(重量百分比)为55~65%caf2、15~25%cao、15~25%al2o3的预熔渣作为渣料,使用前在600~700℃下烘烤≥24h。
35.②
电渣冶炼自熔电极棒与结晶器的直径比值为填充比,所述填充比为0.6~0.7;电渣精炼前20~30min向电渣炉内通入高纯氩气作为保护气;电渣精炼过程中通过调节电流、电压,控制稳态熔速在4.3
±
0.3kg/min;
补缩期分两段补缩,电压在45~40v、电流在6k~4ka内递减,每段时间控制在2~4min。
36.③
电渣锭脱模:电渣冶炼完成2h后进行脱膜,然后空冷。
37.(3)锻造工序:包括加热、锻造、冷却步骤;所述加热步骤,采用三段式加热,第一段为以100~150℃/h的速率升温至800~900℃,保温2~3h;第二段为以150~180℃/h的速率升温至1180~1220℃,保温4~6h;第三段为随炉冷却至1150~1170℃,保温0.5~1h;所述锻造步骤,采用单向拔长的方式,锻造温度900~1100℃,锻造过程的送进量l=0.5~0.8h,单次压下量δh<18%h,端部锻造送进量a>0.4h;其中,h为锻造过程中锻件的厚度,mm;δh为单次压下量,mm;a为端部锻造送进量,即开锻时端部的送进量,mm;l、δh、a、均与h值(锻件厚度)有关,此处的锻件厚度并非固定值,因为每次锻造捶打下,锻件的厚度h均会发生改变,即对应的l、δh和a也会随时变化,需要在锻造过程中即时调整;最后锻造得到截面尺寸为135mm
×
135mm~150mm
×
150mm的方坯;所述冷却步骤,采用缓冷坑缓冷或砂冷的方式,冷却至方坯表面温度≤300℃。
38.(4)轧制工序:锻造后的坯料进行表面打磨,使用砂轮打磨机将锻坯表面及角部进行打磨,打去角裂、表面发纹等,最后将有裂纹的头部切去。之后连轧机进行轧制,工艺为:方坯在1130~1180℃保温2~3h,之后进行粗轧,出钢温度≥900℃;中间补温至950℃后进行精轧,轧制为φ8~12mm的盘条,吐丝温度800~850℃。
39.(5)固溶处理工序:采用井式加热炉进行,在加热炉内通入氮气进行保护,根据加热炉的容量,每立方米氮气的通气量为4~6.5l/min;盘条装炉前,加热炉先进行预热,升温至800~850℃保温1h以上,在盘条完全冷却前装炉;装炉后,采用两段式加热,第一段为以150~180℃/h的速率升温至1050~1110℃,保温0.5h;第二段为以100~120℃/h的速率升温至1190~1220℃进行保温,保温时间t1=1.5+0.1 d1,之后出炉水冷;t1为保温时间,h;d1为轧制后盘条的直径,mm。
40.(6)冷拔工序:包括剥皮、拉拔步骤;剥皮前先使用1~1.5mm沙粒进行喷丸处理,去除表面松散氧化皮,之后采用车刀剥皮+双砂带打磨方式进行剥皮;车刀剥皮总去除量≤0.4mm;双砂带打磨过程中,单边打磨去除总量h与砂带机前、后砂带的规格满足:当h<0.1mm时,前、后砂带分别为240目、320目;当0.1≤h≤0.2mm时,前、后砂带分别为180目、320目;当h>0.20mm时,前、后砂带分别为80目、240目;拉拔过程,除最后一道次拉拔无减面率要求外,其他道次的减面率按如下控制:当d2>6mm时,单道次减面率为25~30%;当d2≤6mm时,单道次减面率为20~25%;d2为拉拔过程中丝材的直径,mm;总减面率≥70%,拉拔为φ2~6mm丝材。
41.(7)时效热处理工序:在氢气气氛保护下,在550~630℃进行热处理,热处理时间t2=0.25d,t2为热处理时间,h;d为铁镍钼合金丝材的直径,mm。
42.上述工序所得到的铁镍钼合金丝材抗拉强度≥1150mpa,20℃导电率≥2%iacs,室温~230℃热膨胀系数≤2.4
×
10-6
/℃。
43.本发明实施例1-10铁镍钼合金丝材的化学成分及质量含量见表1,各生产工序的参数设置见表2-表5,生产的铁镍钼合金丝材的力学性能见表6。
44.表1.各实施例中铁镍钼合金丝材的化学成分(质量分数,%)表2.各实施例真空熔炼及电渣重熔工艺参数设置
表3.各实施例锻造工艺参数设置
表4.各实施例轧制及固溶处理工艺参数设置表5.各实施例冷拔、时效热处理工艺参数设置
表6.各实施例中铁镍钼合金丝材的性能。