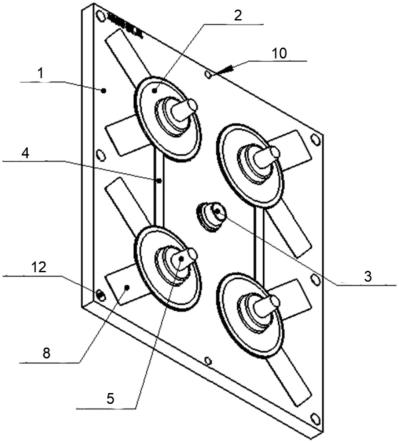
1.本实用新型涉及离心泵叶轮砂型铸造模具,尤其涉及一种防止离心泵叶轮打泡的自动线铸造模具。
背景技术:2.离心泵是利用叶轮旋转而使水发生离心运动来工作的一种电力排灌设备,叶轮是离心泵的“心脏”,属于关键零件,结构形式一般为闭式,包括有前盖板、后盖板和中间若干叶片,材质一般是灰铸铁件,为了节约生产成本和提升生产效率,通常是采用自动线粘土砂机器造型,泥芯采用覆膜砂制造。
3.生产时经常发现,在完成自动线机器造型后的浇注铁水过程中,铁水从浇注系统流入型腔,与型腔内的覆膜砂接触后,覆膜砂芯受到铁水的热作用及化学作用,树脂及其他发气物挥发、分解、燃烧产生的气体,不能及时有效地全部排出,因此,铁水在未来得及排出的气体周围逐渐凝固,产生打泡现象,使铸件毛坯盖板处空心破损,报废率非常高,对于低比转速离心泵叶轮,由于外圆直径与流道比值很大,甚至无法铸造出来,无法完成客户订单,严重影响了企业经营效益。
技术实现要素:4.本实用新型针对上述自动线机器造型后的浇注铁水过程中,不能及时有效地全部排出,铁水在未来得及排出的气体周围逐渐凝固,产生打泡现象使铸件毛坯空心破损的情况,摒弃传统的千方百计降低覆膜砂泥芯发气量的思路,运用了“大禹治水”的方法,从堵到排,从模具上增设排气通道,使高温铁水与覆膜砂作用产生的气体从排气通道排出,防止铸件毛坯空心破损;
5.为解决上述技术问题,本实用新型提供以下的技术方案:
6.本实用新型提供了一种防止离心泵叶轮打泡的自动线铸造模具,
7.包括型板,所述型板包括型板上表面、型板下表面,所述型板上表面的表面设置有上模样、直浇道,所述上模样设置为四组,四组所述上模样呈矩形分布在所述型板上表面的表面上,位于左侧的两组上模样之间通过内浇道连接,位于右侧的两组所述上模样之间通过内浇道连接,位于左侧的两组上模样与位于右侧的两组所述上模样位于所述直浇道竖直轴线对称设置,所述上模样上均设置有排气柱;
8.所述型板下表面的表面设置有下模样、横浇道,所述下模样设置为四组,四组所述下模样呈矩形分布在所述型板下表面的表面上,位于上侧的两组下模样之间通过内浇道连接,位于下侧的两组所述下模样之间通过内浇道连接,位于上侧的两组下模样与位于下侧的两组所述下模样位于所述横浇道水平轴线对称设置。
9.可选的,所述上模样上均设置有排气片,所述排气片至少设置为一组,位于左侧的两组所述上模样的排气片安装方向与位于右侧的两组所述上模样的排气片安装方向相反。
10.可选的,所述型板上表面的表面边沿开设有螺纹孔,所述螺纹孔至少设置为两组。
11.可选的,所述型板下表面的表面边沿开设有定位孔,所述定位孔至少设置为两组。
12.可选的,所述型板上表面与所述型板下表面的边沿均开设有锁紧孔,所述锁紧孔至少设置为六组。
13.可选的,所述螺纹孔、锁紧孔、定位孔的横截面均设置为圆形结构,或所述螺纹孔、锁紧孔、定位孔的横截面均设置为矩形结构。
14.本实用新型有益效果
15.本实用新型能防止自动线粘土砂机器造型,泥芯采用覆膜砂,浇注过程中产生的打泡现象,防止铸件毛坯空心破损,提升毛坯合格率,且便于自动化生产,提升了毛坯生产效率。
附图说明
16.图1为本实用新型型板上表面结构示意图。
17.图2为本实用新型型板下表面结构示意图。
18.附图标记说明:1-型板上表面,2-上模样,3-直浇道,4-内浇道,5-排气柱,6-型板下表面,7-下模样,8-横浇道,9-排气片,10-螺纹孔,11-定位孔,12-锁紧孔。
具体实施方式
19.下面将结合本实用新型的实施例中的附图,对本实用新型的实施例中的技术方案进行清楚、完整地描述,显然,所描述的实施例仅仅是本实用新型一部分实施例,而不是全部的实施例。基于本实用新型中的实施例,本领域普通技术人员在没有做出创造性劳动前提下所获得的所有其他实施例,都属于本实用新型保护的范围。
20.实施例
21.如图1-图2所示,本实用新型提供了一种防止离心泵叶轮打泡的自动线铸造模具,
22.包括型板,所述型板包括型板上表面1、型板下表面6,所述型板上表面1的表面设置有上模样2、直浇道3,所述上模样2设置为四组,四组所述上模样2呈矩形分布在所述型板上表面1的表面上,位于左侧的两组上模样2之间通过内浇道4连接,位于右侧的两组所述上模样2之间通过内浇道4连接,位于左侧的两组上模样2与位于右侧的两组所述上模样2位于所述直浇道3竖直轴线对称设置,所述上模样2上均设置有排气柱;
23.所述型板下表面6的表面设置有下模样7、横浇道8,所述下模样7设置为四组,四组所述下模样7呈矩形分布在所述型板下表面6的表面上,位于上侧的两组下模样7之间通过内浇道4连接,位于下侧的两组所述下模样7之间通过内浇道4连接,位于上侧的两组下模样7与位于下侧的两组所述下模样7位于所述横浇道8水平轴线对称设置,
24.通过上述设计,上模样2是形成毛坯的上模部分,造型时,该位置放置覆膜砂泥芯,直浇道3与自动造型机的浇口杯相连接,是浇注时铁水开始进入的通道,内浇道4分别与四组上模样2和个横浇道8相连接,来自横浇道8的铁水经内浇道4,分别进入上模样2和下模样7,凝固后形成毛坯,下模样7是形成毛坯的下模部分,造型时,该位置放置覆膜砂泥芯,横浇道8分别与直浇道3、内浇道4相连接,将来自直浇道3的铁水引入到个内浇道4;
25.所述上模样2上均设置有排气片9,所述排气片9至少设置为一组,位于左侧的两组所述上模样2的排气片9安装方向与位于右侧的两组所述上模样2的排气片9安装方向相反,
26.在本实施例中,所述排气片9共设置为八组,通过上述设计,八组排气片9厚度很薄,与上模样2相连接,作用是在造型和浇注铁水后,将覆膜砂泥芯与高温铁水产生化学作用形成的气体排出去;
27.所述型板上表面1的表面边沿开设有螺纹孔10,所述螺纹孔10至少设置为两组,两组螺纹孔10的作用是装模和卸模时,旋入两个吊环螺栓,方便铁链的吊钩插入,将模具吊运;
28.所述型板下表面6的表面边沿开设有定位孔11,所述定位孔11至少设置为两组,两组定位孔11的作用是装模时,将模具定位在模具架上的定位销上;
29.所述型板上表面1与所述型板下表面6的边沿均开设有锁紧孔12,所述锁紧孔12至少设置为六组,六组锁紧孔12的作用是装模定位后,放置六个螺栓,将模具锁紧;
30.为便于设备的安装,所述螺纹孔10、锁紧孔12、定位孔11的横截面均设置为圆形结构;
31.本实用新型具体通过以下步骤实现:
32.1、在模具放置处,用两个相应规格的吊环螺栓,分别旋紧到两组螺纹孔10内,将铁链的吊钩插入,并固定好,利用行车,将模具吊运到自动线造型处的模具架上,
33.2、将模具定位孔11对正模具架上的定位销上,将模具定位好。
34.3、用六个相应规格的螺栓,分别旋紧到六组锁紧孔12,将模具固定好。
35.4、启动自动线造型机,进行造型。
36.5、进行浇注前的准备工作,待造型数量足够一包时,将熔炼好的铁水运送一包来,并倒入到自动浇注机的浇包内。
37.6、再将浇包内将铁水缓慢倒入砂型的浇口杯内。
38.7、此时,铁水经浇口杯流入到直浇道3、横浇道8,并经内浇道4分别流入到下模样7和上模样2内,与型腔内的覆膜砂泥芯接触。
39.8、覆膜砂泥芯受到铁水的热作用及化学作用,树脂及其他发气物挥发、分解、燃烧产生大量气体。
40.9、在高温铁水逐层凝固的作用力下,下模样7和上模样2内的气体分别经个排气片9和个排气柱从侧面和上方排出到空气中,这样型腔内的气体顺利排出,可以防止凝固后的叶轮毛坯出现打泡现象。
41.本实用新型能防止自动线粘土砂机器造型,泥芯采用覆膜砂,浇注过程中产生的打泡现象,防止铸件毛坯空心破损,提升毛坯合格率,且便于自动化生产,提升了毛坯生产效率。
42.最后应说明的是:以上所述仅为本实用新型的优选实施例而已,并不用于限制本实用新型,尽管参照前述实施例对本实用新型进行了详细的说明,对于本领域的技术人员来说,其依然可以对前述各实施例所记载的技术方案进行修改,或者对其中部分技术特征进行等同替换,凡在本实用新型的精神和原则之内,所作的任何修改、等同替换、改进等,均应包含在本实用新型的保护范围之内。