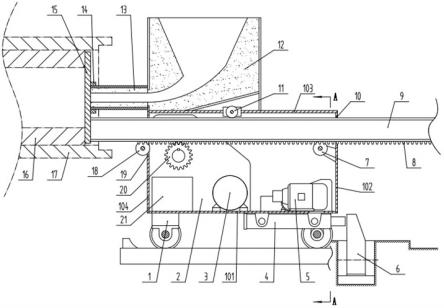
1.本实用新型应用于离心铸造行业,涉及铸钢管推管机构,具体是将铸钢管浇注车和推管机构合二为一的推管车。
背景技术:2.离心铸造铸钢管多采用卧式离心机和管模,钢水离心浇铸时,需要水平进入管模内,浇注中间包是必备机构,为保证中间包流嘴与管模浇注挡板对正,中间包常常固定在浇注车上,如公告号为cn212495288u、cn212495284u和公布号为cn101804451b、cn111531145a的专利申请,均是如此。铸钢管浇注冷却后,需要从管模内拔出或推出,推管机或拔管机也是离心机的必备装备。通常情况下,受到位置限制,浇注中间包位于管模的浇注端,推管机只能位于管模的非浇注端。如公布号cn111531145a和公告号cn212495288u、cn212495284u专利文献中的公开的推管机构位置所示。铸钢管自非浇注端推出到浇注端,需要采用吊车将铸钢管吊运到精整线。受到浇注端浇注操作空间限制,无法在浇注端设计接管臂使铸钢管自动进入精整线。
3.为减小车间天车的工作压力,将铸钢管的推管装置设计在浇注端,这样,铸钢管自非浇注端推出,可以不使用天车,直接由机械臂送入精整线。前期在实验室采用了新设计的推管中间包,将推管机构和中间包一起安装在小车上,推管液压缸设置在轨道中部,液压缸推动小车,小车的流嘴推管。其不足在于液压管道和液压缸在地面上放置,需设置保护措施,否则易产生安全隐患或液压设备故障,而且造成地面不平,影响车辆和人员通行。本实用新型将液压缸安装在小车上,解决安全隐患和通行不方便的问题。
技术实现要素:4.本实用新型解决的技术问题是:提供一种铸钢管浇注推管车,将浇注与推管合一,设计在离心机的浇注端,无凸出地面的设施,消除安全隐患,为人员和车辆通行提供方便。
5.本实用新型所采用的技术方案是:铸钢管浇注推管车包括小车和其顶面的中间包。所述小车安装有组成箱体的底板、后板、顶板、前板和侧板,所述箱体内安装有行走机构、推管机构和液压机构。所述液压机构的液压缸设置在底板下、小车的后部,安装在小车中间,或小车两侧。该液压缸与后座配合推管,所述后座放置在后背的沟槽内。
6.进一步,所述推管机构包括推管电机、推管变速箱、齿轮、齿条和推杆。所述齿条固定在推杆底面中部,与齿条啮合。推管电机通过推管变速箱带动齿轮转动。所述推杆穿过后板上的后口和前板上的前口,可前后移动。
7.进一步,所述中间包前端安装有流嘴,所述推杆位于该流嘴的正下方;所述流嘴和推杆与推板配合推管,所述推板中心固定支撑环,该支撑环与流嘴配合相应。
8.进一步,推杆的截面为工字梁或方管,由固定在前板上的前支撑轮和固定在后板上的后支撑轮支撑,前后支撑轮设计有与推杆配合的限位挡边,限制其左右移动。在推杆的顶面,与固定安装在顶板的限位轮配合,限位轮限制其向上移动。
9.进一步,所述后座包括通过小轴转动连接的支架和后座板,所述后座板侧面安装有方便后座板旋升的螺钉,所述支架上固定定位块,该定位块可限定后座板旋升的位置,所述后座的顶部安装有便于吊运的内六方螺栓。
10.进一步,所述行走机构包括行走电机、行走变速箱、链条;所述行走电机的输出轴与行走变速箱的输入轴连接,行走变速箱的输出轴通过链条与小车车轴连接,行走电机转动时,可带动小车前后行走。
11.本实用新型的有益效果是:本实用新型将钢水浇注和推管操作集中在一台小车上,节约设备占地面积。液压机构全部安装在小车上,地面平整,消除了安全隐患,行人或车辆通行方便。推管机构设计在浇注端,向非浇注端推管,满足车间向后道工序转运的物流要求。
附图说明
12.图1为实施例1的主视结构示意图;
13.图2为图1的a-a结构示意图;
14.图3为后座主视结构示意图;
15.图4为图3的左向视图;
16.图5为图3的俯视图;
17.图6为实施例2结构示意图;
18.图7为实施例3结构示意图;
19.附图标记:1-小车、 2-推管变速箱、 3-推管电机、 4-液压缸、5-液压泵、 6-后座、7-后支撑轮、8-齿条、9-推杆、10-后口、11-限位轮、12-中间包、13-流嘴、14-支撑环、15-推板、16-铸钢管、17-管模、18-前支撑轮、19-前口、20-齿轮、21-油箱、22-行走电机、23-行走变速箱、24-链条;
20.61-小轴、62-内六方螺栓、63-后座板、64-螺钉、65-支架、66-定位块;
21.101-底板、102-后板、103-顶板、104-前板、105-侧板。
具体实施方式
22.下述前后是相对于附图1中的流嘴位置而言,流嘴所在小车的位置为前,背对流嘴的位置为后。下述上下是指本实用新型使用的状态而言,即附图的上下相对位置。下述安装、设置、连接除特殊说明外,均指固定连接,可以是焊接、或紧固件连接、或其他固定连接的方式。下述底板、后板、顶板、前板和侧板包括与之连接、起到固定、增强、保护作用的型钢结构件。
23.实施例1。
24.本实施例浇注推管车结构如附图1和附图2所示,附图2为附图1的a-a结构示意图。浇注推管车包括小车1和在小车顶面安装的中间包12。小车1上安装有底板101、后板102、顶板103、前板104和侧板105,成为箱体结构,箱体内安装有行走机构、推管机构和液压机构。在前板104和后板102上设计有相应的前口19和后口10,前口19和后口10方便推管时推杆9前后通过。顶板103上安装可拆卸的中间包12,中间包12上安装有浇注用流嘴13,该流嘴13与管模17的旋转轴线一致。侧板105、后板102和前板104用于保护箱体内的机构,侧板105可
拆卸,便于行机构的维修和部件更换,为方便电机的维修,箱体内的电机均安装在侧板附近。箱体内行走机构、推管机构和液压机构的部件位置设计要考虑小车行走的平稳性,以及底板101受力的均匀性,避免偏重。
25.所述行走机构包括行走电机22、行走变速箱23、链条24等。行走电机22的输出轴与行走变速箱23的输入轴连接,行走变速箱23的输出轴通过链条24与小车车轴连接。行走电机22启动,通过行走变速箱23和链条24可带动小车1在轨道上前后移动。小车行走轨道与车间地面齐平。
26.所述推管机构包括推管电机3、推管变速箱2、齿轮20、齿条8和推杆9等。推管电机3的输出轴与推管变速箱2的输入轴连接,推管变速箱2的输出轴上安装齿轮20,齿轮20与推杆9上的齿条8啮合配合。所述推杆9为水平方向,与管模17的旋转轴线方向一致,位于流嘴13的正下方。推管电机3启动,通过推管变速箱2带动齿轮20旋转,齿轮20带动齿条8移动,从而带动推杆9的前后移动,实现推管操作和推杆9的收回。
27.所述推杆9的结构如附图2所示,为工字梁结构,穿过小车的前口19和后口10,在推杆9底面中部,固定连接齿条8,齿条8与齿轮20啮合配合良好。齿条8两侧的底面平面与固定在小车上的前支撑轮18和后支撑轮7配合,前支撑轮18安装在小车前板104上,后支撑轮7安装在小车后板102上。为防止推管时推杆9上移,在推杆9的顶部,设置有与推杆9顶面配合的限位轮11,所述限位轮11位于中间包12的下方,固定在小车顶板103中部的开口处,如附图1和附图2所示。前后支撑轮和限位轮11的转轴构成三角形,限定了推杆9只能前后移动,从而保证推管的顺利进行。
28.所述液压机构包括液压缸4、液压泵5、油箱21和连通油管等,液压缸4安装在底板101后部下表面,小车的中心。在小车1行走的轨道中间,采用混凝土浇筑推管后背,该后背的标高稍低于小车车轴,方便小车通行,尽可能减小与液压缸的高度距离,便于推管时提供更安全的反作用力。该后背与液压缸推管相配的位置设计有沟槽,在沟槽内放置后座6,该后座6与液压缸4配合实现推管操作。后座6的结构见附图3-5所示,附图3为后座6的主视结构示意图,附图4为图3的左向视图,附图5为图3的俯视图。后座6包括支架65和后座板63,两者通过小轴61转动连接。小车1前后移动时,后座板63放倒,防止磕碰小车底部的车轴。推管操作时,后座板63旋起,与液压缸4配合推管。为方便后座板63的旋转操作,在后座板63的侧面安装螺钉64。为方便后座板63旋起定位,在支架65上固定定位块66。为方便后座6自沟槽中取出或安放,在后座的顶部安装有内六方螺栓62,平时内六方螺栓62的高度不高于后座6最高点,需要将后座6吊出时,旋升内六方螺栓62,挂吊绳用天车吊出即可。通常情况下,该沟槽用钢板覆盖,防止垃圾掉入,由于后背标高高于车间地面,沟槽内不会积水,方便了现场清洁。
29.离心浇铸铸钢管时,移动小车,流嘴13通过浇注端挡板的浇注孔伸入管模17内,浇注钢水后,小车1退回,钢水凝固冷却成铸钢管16,拆掉浇注端挡板。如附图1所示,将推板15挂在流嘴13上。推板15的中心位置焊接支撑环14,支撑环14与流嘴13配合,一限定推板15的位置,保证与管模17无磕碰;二防止推板15脱落。当推板15接触铸钢管16的端部时,小车停止,启动推管电机3,齿轮20带动推杆9前移,使推杆9接触推板15。然后旋升后座板63,启动液压泵5,液压缸的缸杆向后伸出作用在后座板63上,后座板63由混凝土后背支撑,给液压缸4反作用力,使得小车前移,流嘴13推动推板15,推板15推动铸钢管16前移。当液压缸4推
管时,齿轮20带动推杆9同时推管。当液压缸4的缸杆全部伸出时,流嘴13停止前移,此时,推杆9推动推板15前移,将铸钢管16逐渐推出管模17。由于铸钢管16在管模17内的初始移动静摩擦力最大,所以采用液压缸推管,一旦铸钢管16在管模17内移动后,其摩擦力减小,可采用推杆9推管。铸钢管16全部推出管模17后,推管电机3反转,推杆9后移收回,推板15自动落下。液压缸4的缸杆回缩复位。此时可拆卸中间包12进行维修更换,也可以在推杆推管的过程中拆卸,但吊起浇注包时,注意防止流嘴与管模的磕碰。
30.附图1所示前支撑轮18位于小车箱体的外侧,后支撑轮7位于小车箱体的内侧,也可以将前支撑轮18位于小车箱体的内侧,后支撑轮7位于小车箱体的外侧,由前后板或钢结构件固定即可。附图1所示限位轮11为一个,位于前后支撑轮中部,也可以设计两个或多个,也可以安装在顶板103的底面,只要安装在与推杆9顶面配合的位置,限制推杆9上移均可。
31.本实施例指给出了后座6的一种结构形式,不代表只有该结构形式可以满足推管要求,只是该结构使用更为便捷。其他插入式、翻转式也可以提供液压缸的反作用力,实现推管操作,不做详细阐述。
32.实施例2。
33.上述实施例1中,液压缸推管依赖小车传力,如果液压缸推力方向与推管力的方向有偏差,则会造成小车承受扭矩,小车易产生扭曲变形。而且混凝土后背单点受力,局部应力集中。本实施例是在实施例1的基础上的改进,将一个液压缸改为对称的两个,如附图6所示。这样,消除了小车可能的扭曲受力,增加了一个后座6,后背的单点受力改变为两点受力,改善后背的受力状况,减轻了后背压力。
34.实施例3。
35.本实施例与实施例1的区别在于推杆9的截面结构不同。实施例1中的推杆截面为工字型,虽然推杆强度和刚度能够满足推管的需要,但其抗扭能力稍差,如果在推管时,误操作使得管模旋转,有可能造成推杆9的扭曲变形。
36.如附图7所示,本实施例将推杆9改进为方管结构,大大增加了推杆的抗扭能力。同时,前支撑轮18和后支撑轮7的挡边与推杆配合,限制了推杆的左右侧向移动,与限位轮11一起,既保证了推杆只能水平前后移动,也保证即使管模误操作旋转,推杆端部与推板15产生滑动摩擦,推杆9不会变形。
37.本实用新型将钢水浇注和推管操作集中在一台小车上,节约设备占地面积。将液压机构安装在小车上,是对实验室推管中间包的改进,液压系统部件集中,轨道附近无液压部件,地面平整,消除了安全隐患,行人或车辆通行方便。推管机构设计在浇注端,向非浇注端推管,满足车间向后道工序转运的物流要求。尤其对于不锈钢和镍基合金的铸钢管而言,在非浇注端放置水箱,推出管模后的高温铸钢管可实现立即淬火固溶处理,大大方便了离心机和固溶处理的操作。如果浇注端必须通过车辆,可以将长度较长的推杆从小车上卸掉,然后再安装上即可。