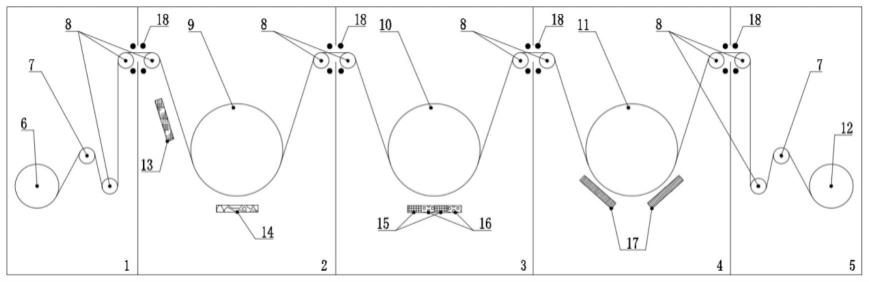
1.本实用新型属极薄铜箔技术领域,特别是涉及一种附载体极薄铜箔的生产装置。
背景技术:2.近年来电子产品行业发展迅速,在功能越来越齐全的基础上,产品整体也变得越来越轻薄,其中集成电路板制造技术正在进行快速的更新迭代。传统的集成电路板制备方法已经越来越难以适应更小线宽线距的电路制造需求,因此改良型半加成法(msap)应运而生。msap过程中需要用到极薄铜箔(厚度小于5μm的铜箔),以达到线路闪蚀的目的,但是极薄铜箔的制备方法复杂,产品质量稳定性较低,因此是当前集成电路行业发展过程中的一大挑战。
3.极薄铜箔由于其极薄的厚度和自身抗拉强度,使其难以通过现有表面处理设备进行表面处理,因此附载体极薄铜箔成为当前的研究热点。附载体极薄铜箔主要包括起物理支撑作用的载体层、防止各功能层相互扩散的阻挡层、实现膜层分离功能的剥离层和极薄铜层,其中剥离层是整个附载体极薄铜箔制造过程中的关键。目前常用作剥离层的材料分金属和非金属两大类:金属类剥离层材料包括ni/mo/co/cr/fe/ti/w/zn的单质或合金,制备方法包括电镀、化学镀、磁控溅射以及物理蒸镀;非金属类剥离层材料包括碳类、羧酸类小分子、咪唑类小分子及其混合物,制备方法包括浸渍、喷雾、涂布等方式。但是利用现有的工艺方法都存在一些问题,造成产品量产可控性较低,产品质量参差不齐,合格率低等一系列问题。比如电镀金属或者合金作为剥离层时,剥离力的大小受金属组分和界面状态的影响非常大,且可行性窗口区间较小,因此必须配套及其严苛的工艺控制体系才能实现连续稳定生产。利用真空镀膜的方法制备金属剥离层能够在膜层连续性和均一性方面得到提升,但是溅射的金属往往具有较强的结合力,尤其是极薄铜箔经过高温压板后,剥离层的结合力较大,在载体基材表面粗糙度较大时易出现局部粘连,因此对载体箔材的表面轮廓要求较高,生产难度增大。采用浸渍、涂布等方法制备非金属类材料作为剥离层时,剥离效果较好,但常出现剥离层不连续、不均匀或者电镀加厚时出现局部无法电镀等问题,因此较易出现局部粘连和极薄铜箔中存在大量针孔的问题。
4.一方面,真空镀膜的方法具有膜层连续、厚度均匀等特点,尤其是在剥离层表面溅射铜种子层,会极大地降低后续电镀加厚中的针孔问题。另一方面,一些有机小分子能够提供较为可控的剥离强度,但是其成膜均匀性较差,大大降低了生产的连续性和产品质量稳定性。因此如何开发出一种新的剥离层,使其兼具稳定的剥离能力和较好的连续性是目前载体铜箔制造中的最大挑战。
技术实现要素:5.本实用新型所要解决的技术问题是提供一种附载体极薄铜箔的生产装置,解决目前附载体极薄铜箔生产较难、工艺稳定性差、合格率低的问题。
6.本实用新型解决其技术问题所采用的技术方案是:提供一种附载体极薄铜箔的生
产装置,包括设于真空仓室内的溅射蒸镀模块及外置的电镀加厚模块,所述真空仓室内还设有用于持续转运载体箔材的卷绕系统,其特征在于,所述溅射蒸镀模块包括依次布置且互相连通的放卷仓、第一金属层真空溅射仓、第二金属层真空蒸镀仓、第三金属层真空溅射仓及收卷仓,所述卷绕系统使载体箔材自所述放卷仓开始放卷,随后依次通过所述第一金属层真空溅射仓、第二金属层真空蒸镀仓、第三金属层真空溅射仓,最后进入所述收卷仓内完成收卷,
7.所述第一金属层真空溅射仓内设有正对所述载体箔材正面的离子源处理模块及第一金属层真空溅射模块;
8.所述第二金属层真空蒸镀仓内设有正对所述载体箔材正面的第二金属层真空蒸镀模块,所述第二金属层真空蒸镀模块包括交错布置的金属源以及配体分子源;
9.所述第三金属层真空溅射仓内设有正对所述载体箔材正面的第三金属层真空溅射模块。
10.进一步地,所述电镀加厚模块包括卷绕系统以及依次排列的碱镀池、水洗池一、酸镀池、水洗池二、粗化池、固化池、水洗池、黑化池、水洗池三、灰化池、水洗池四、钝化池、水洗池五、偶联剂涂覆池及烘箱。
11.进一步地,所述放卷仓、第一金属层真空溅射仓、第二金属层真空蒸镀仓、第三金属层真空溅射仓及收卷仓中,相邻两仓的连接处设有辅助抽气组件。
12.进一步地,所述卷绕系统包括设于放卷仓内的放卷辊、张力辊、第一金属层真空溅射仓内的第一金属层控温辊、第二金属层真空蒸镀仓内的第二金属层控温辊、第三金属层真空溅射仓内的第三金属层控温辊以及所述收卷仓内的收卷辊,所述张力辊、第一金属层控温辊、第二金属层控温辊、第三金属层控温辊之间设有过渡辊。
13.进一步地,所述张力辊内设有用于控制载体箔材卷张力锥度的压力传感器、伺服电机及plc控制柜。
14.进一步地,所述第一金属层真空溅射模块靶阴极为平面靶或圆柱靶,所述靶阴极分布于所述第一金属层控温辊的一侧。
15.进一步地,所述离子源处理模块中的离子源设于所述第一金属层真空溅射仓的入口处。
16.进一步地,所述金属源以及配体分子源交替布置于所述第二金属层控温辊的一侧。
17.进一步地,所述第三金属层真空溅射模块靶阴极为平面靶或圆柱靶,所述靶阴极分布于所述第三金属层控温辊的一侧。
18.进一步地,所述金属源可蒸镀cu、ni、co、zr、zn、fe或其合金,所述配体分子源可蒸镀对苯二甲酸、2-氨基-对苯二甲酸、均苯三甲酸、二甲基咪唑或其混合物。。
19.有益效果
20.本实用新型采用溅射与蒸镀结合的方式,在剥离力稳定的同时保有较好的膜层连续性,少有粘连和针孔产生,能够维持较高的产品合格率和生产连续性,极大地提高产能和效益。
21.本实用新型在蒸镀仓的金属蒸镀源附近交替设置配体分子源,使通过本实用新型制作铜箔的剥离层时,可同时蒸镀金属和作为配体的有机小分子,如此原位形成组分稳定
的金属络合物膜层,使产品能够维持稳定一致的载体剥离能力。
22.采用本实用新型生产的附载体极薄铜箔具有工艺控制稳定、各功能层连续均匀和载体层分离力一致等优点,而且该方法能够满足大批量连续生产的质量稳定性。在真空镀膜工段,首先利用离子源等处理载体层表面,使其表面清洁均一;然后通过磁控溅射技术在载体层表面镀一层致密且稳定的镍、钼等金属作为阻挡层。接下来利用蒸镀技术,在阻挡层金属表面制备一层金属络合物作为载体剥离层。之后在剥离层表面溅射一层铜作为后续电镀的种子层。该方法通过磁控溅射和蒸镀结合的方式实现了载体层的稳定分离,同时真空镀膜的工艺方法保证了各功能层的厚度均一性、膜层连续性和质量稳定性,因此该工艺方法能够较易实现产品的量产和质量的稳定性,对超微细线路板的发展具有重大的推动作用。
附图说明
23.图1为一种附载体极薄铜箔生产装置溅射蒸镀模块的结构示意图。
24.图2为一种附载体极薄铜箔生产装置电镀加厚模块的流程示意图。
25.其中,1-放卷仓;2-第一金属层真空溅射仓;3-第二金属层真空蒸镀仓;4-第三金属层真空溅射仓;5-收卷仓;6-放卷辊;7-张力辊;8-过渡辊;9-第一金属层控温辊;10-第二金属层控温辊;11-第三金属层控温辊;12-收卷辊;13-离子源处理模块;14-第一金属层真空溅射模块;15-金属源;16-配体分子源;17-第三金属层真空溅射模块;18-辅助抽气组件;19-电镀加厚模块
26.各图中相同标记代表同一部件。
具体实施方式
27.下面结合具体实施例,进一步阐述本实用新型。应理解,这些实施例仅用于说明本实用新型而不用于限制本实用新型的范围。此外应理解,在阅读了本实用新型讲授的内容之后,本领域技术人员可以对本实用新型作各种改动或修改,这些等价形式同样落于本技术所附权利要求书所限定的范围。
28.如图1、2所示,一种附载体极薄铜箔的生产装置,包括设于真空仓室内的溅射蒸镀模块及外置的电镀加厚模块19,所述真空仓室内还设有用于持续转运载体箔材的卷绕系统。所述溅射蒸镀模块包括依次布置且互相连通的放卷仓1、第一金属层真空溅射仓2、第二金属层真空蒸镀仓3、第三金属层真空溅射仓4及收卷仓5。所述卷绕系统使载体箔材自所述放卷仓1开始放卷,随后依次通过所述第一金属层真空溅射仓2、第二金属层真空蒸镀仓3、第三金属层真空溅射仓4,最后进入所述收卷仓5内完成收卷。所述载体箔材主要指铜箔,也可以根据情况更换为铝箔等金属箔或pi薄膜等聚合物类薄膜。
29.所述第一金属层真空溅射仓2内设有正对所述载体箔材正面的离子源处理模块13及第一金属层真空溅射模块14。通过所述第一金属层真空溅射模块14在所述载体箔材表面溅射镀金属阻挡层。
30.所述离子源处理模块13中的离子源设于所述第一金属层真空溅射仓2的入口处,所述离子源包括但不限于霍尔离子源、阳极层离子源、电弧预处理、考夫曼离子源、icp离子源、电晕、电浆轰击等。所用气体包括但不仅限于氩气、氮气、氧气、一氧化二氮、二氧化碳、
一氧化碳和氢气等。其主要作用是通过高能量的离子轰击,清理基底表面的杂质异物,同时较高能量的离子也会将表层有机分子的化学键打破,形成气态的小分子挥发而离开表面,从而暴露出新的活性表层。所述第一金属层真空溅射模块14靶阴极为平面靶或圆柱靶,所述靶阴极分布于所述第一金属层控温辊9的一侧,所述阴极靶的数量可以根据开发的工艺情况进行适当调整。
31.所述第二金属层真空蒸镀仓3内设有正对所述载体箔材正面的第二金属层真空蒸镀模块,所述第二金属层真空蒸镀模块包括交错布置的金属源15以及配体分子源16。通过真空蒸镀技术在所述金属阻挡层表面继续蒸镀剥离层。
32.所述金属源15以及配体分子源16交替布置于所述第二金属层控温辊10的一侧。所述金属源15可蒸镀cu、ni、co、zr、zn、fe或其合金,所述配体分子源16可蒸镀对苯二甲酸、2-氨基-对苯二甲酸、均苯三甲酸、二甲基咪唑或其混合物。通过采用溅射与蒸镀结合的方式,在剥离力稳定的同时保有较好的膜层连续性,少有粘连和针孔产生,能够维持较高的产品合格率和生产连续性,极大地提高产能和效益。
33.所述第三金属层真空溅射仓4内设有正对所述载体箔材正面的第三金属层真空溅射模块17。通过第三金属层真空溅射模块17在所述剥离层表面溅射镀铜种子层。
34.所述第三金属层真空溅射模块17靶阴极为平面靶或圆柱靶,所述靶阴极分布于所述第三金属层控温辊11的一侧,所述阴极靶的数量可以根据开发的工艺情况进行适当调整。
35.所述放卷仓1、第一金属层真空溅射仓2、第二金属层真空蒸镀仓3、第三金属层真空溅射仓4及收卷仓5中,相邻两仓的连接处设有辅助抽气组件18。真空仓室在靠机械泵、分子泵或维持泵等泵组抽真空以外,通过所述辅助抽气组件18(外接泵)及时将溅射或蒸镀出来的残余原子或分子抽走,实现各仓之间无污染的高质量连续镀膜。所述辅助抽气组件18的抽气口数量可根据实际情况进行适当调整,在本实施例中所述抽气口的具体设置为:在两相邻仓室之间、所述载体箔材两面各设一个抽气口。
36.采用本实用新型生产的附载体极薄铜箔具有工艺控制稳定、各功能层连续均匀和载体层分离力一致等优点,而且该方法能够满足大批量连续生产的质量稳定性。在真空镀膜工段,首先利用离子源等处理载体层表面,使其表面清洁均一;然后通过磁控溅射技术在载体层表面镀一层致密且稳定的镍、钼等金属作为阻挡层。接下来利用蒸镀技术,在阻挡层金属表面制备一层金属络合物作为载体剥离层。之后在剥离层表面溅射一层铜作为后续电镀的种子层。该方法通过磁控溅射和蒸镀结合的方式实现了载体层的稳定分离,同时真空镀膜的工艺方法保证了各功能层的厚度均一性、膜层连续性和质量稳定性,因此该工艺方法能够较易实现产品的量产和质量的稳定性,对超微细线路板的发展具有重大的推动作用。
37.当一卷载体箔材在所述溅射蒸镀模块中完成真空溅射及真空蒸镀加工后,通过人工取出并转运至所述真空仓室外电镀加厚模块19的卷绕系统中并进行电镀加厚,以在所述铜种子层表面电镀加厚铜层至目标厚度。随后在镀膜上采用与电子电路箔类似的表面处理技术对超薄载体箔材表面进行表面处理。如图2所示,所述电镀加厚模块19包括卷绕系统以及依次排列的碱镀池、水洗池一、酸镀池、水洗池二、粗化池、固化池、水洗池、黑化池、水洗池三、灰化池、水洗池四、钝化池、水洗池五、偶联剂涂覆池及烘箱。根据实际情况,用于碱
法-酸法电镀加厚的碱镀池及酸镀池也可以变更为只采用碱镀池的单一碱法电镀加厚或是只采用酸镀池的单一酸法电镀加厚。
38.所述真空仓室内的卷绕系统包括设于放卷仓1内的放卷辊6、张力辊7、第一金属层真空溅射仓2内的第一金属层控温辊9、第二金属层真空蒸镀仓3内的第二金属层控温辊10、第三金属层真空溅射仓4内的第三金属层控温辊11以及所述收卷仓5内的收卷辊12,所述张力辊7、第一金属层控温辊9、第二金属层控温辊10、第三金属层控温辊11之间设有过渡辊8。所述溅射蒸镀模块中的卷绕系统同样包括放卷辊、张力辊、过渡辊及收卷辊。所述张力辊7内设有用于控制载体箔材卷张力锥度的压力传感器、伺服电机及plc控制柜。
39.所述张力辊7为所述卷绕系统中张力系统的主要部件,其作用为在传动过程中,随着放卷卷径不断减小,收卷卷径不断增大,通过控制张力锥度,使整个系统维持在一个恒张力的状态,从而避免收卷窜卷、卷松或者收卷不圆等异常状况的发生。
40.以下通过具体实施例来详述本实用新型的工作流程:
41.实施例1
42.将宽幅为600mm的整卷18μm厚的铜箔固定于放卷仓1中的放卷辊6上,打开辅助抽气组件18,通过张力辊7和过渡辊8调整后,铜箔光面依次通过第一金属层真空溅射仓2中的离子源处理模块13、第一金属层真空溅射模块14;第二金属层真空蒸镀仓3中的第二金属层真空蒸镀模块,其中分布有金属源15和配体分子源16;第三金属层真空溅射仓4中的第三金属层真空溅射模块17。其中,离子源为阳极层离子源,设定功率为4kw,处理时间为6min;溅射阻挡层金属为ni,阻挡层厚度为25nm;剥离层蒸镀厚度为20nm,金属蒸发源为co,小分子蒸发源为二甲基咪唑;溅射种子铜层厚度为70nm。溅射完成后铜箔固定于收卷辊12,封装保存待用。
43.将整卷经过真空镀膜处理的铜箔置于电镀处理线上,在种子层表面进行电镀加厚和表面处理,依次经过碱镀槽、水洗槽、酸镀槽、水洗槽、粗化槽、固化槽、水洗槽、黑化槽、水洗槽、灰化槽、水洗槽、钝化槽、水洗槽、硅烷涂布槽和烘箱,然后铜箔在经过张力调整后进行收卷封装。其中碱镀槽为焦磷酸铜/焦磷酸钾电镀液,酸镀槽为硫酸铜/硫酸电镀液,电镀加厚至金属层厚度为3μm,其他表面处理具体工艺与常规电子电路用铜箔的表处工艺相同。
44.实施例2
45.将宽幅为600mm的整卷18μm厚的铜箔固定于放卷仓1中的放卷辊6上,打开辅助抽气组件18,通过张力辊7和过渡辊8调整后,铜箔光面依次通过第一金属层真空溅射仓2中的离子源处理模块13、第一金属层真空溅射模块14;第二金属层真空蒸镀仓3中的第二金属层真空蒸镀模块,其中分布有金属源15和配体分子源16;第三金属层真空溅射仓4中的第三金属层真空溅射模块17。其中,离子源为阳极层离子源,设定功率为4kw,处理时间为6min;溅射阻挡层金属为ni,阻挡层厚度为25nm;剥离层蒸镀厚度为20nm,金属蒸发源为ni,小分子蒸发源为2-氨基-对苯二甲酸;溅射种子铜层厚度为70nm。溅射完成后铜箔固定于收卷辊12,封装保存待用。
46.将整卷经过真空镀膜处理的铜箔置于电镀处理线上,在种子层表面进行电镀加厚和表面处理,依次经过碱镀槽、水洗槽、酸镀槽、水洗槽、粗化槽、固化槽、水洗槽、黑化槽、水洗槽、灰化槽、水洗槽、钝化槽、水洗槽、硅烷涂布槽和烘箱,然后铜箔在经过张力调整后进行收卷封装。其中碱镀槽为焦磷酸铜/焦磷酸钾电镀液,酸镀槽为硫酸铜/硫酸电镀液,电镀
加厚至金属层厚度为3μm,其他表面处理具体工艺与常规电子电路用铜箔的表处工艺相同。
47.实施例3
48.将宽幅为600mm的整卷18μm厚的铜箔固定于放卷仓1中的放卷辊6上,打开辅助抽气组件18,通过张力辊7和过渡辊8调整后,铜箔光面依次通过第一金属层真空溅射仓2中的离子源处理模块13、第一金属层真空溅射模块14;第二金属层真空蒸镀仓3中的第二金属层真空蒸镀模块,其中分布有金属源15和配体分子源16;第三金属层真空溅射仓4中的第三金属层真空溅射模块17。其中,离子源为阳极层离子源,设定功率为4kw,处理时间为6min;溅射阻挡层金属为ni,阻挡层厚度为25nm;剥离层蒸镀厚度为20nm,金属蒸发源为zr,小分子蒸发源为对苯二甲酸;溅射种子铜层厚度为70nm。溅射完成后铜箔固定于收卷辊12,封装保存待用。
49.将整卷经过真空镀膜处理的铜箔置于电镀处理线上,在种子层表面进行电镀加厚和表面处理,依次经过碱镀槽、水洗槽、酸镀槽、水洗槽、粗化槽、固化槽、水洗槽、黑化槽、水洗槽、灰化槽、水洗槽、钝化槽、水洗槽、硅烷涂布槽和烘箱,然后铜箔在经过张力调整后进行收卷封装。其中碱镀槽为焦磷酸铜/焦磷酸钾电镀液,酸镀槽为硫酸铜/硫酸电镀液,电镀加厚至金属层厚度为3μm,其他表面处理具体工艺与常规电子电路用铜箔的表处工艺相同。
50.以下通过对照例的剥离后铜箔表面情况与实施例进行效果对比:
51.对照例1
52.对照例1与实施例1工艺完全相同,其唯一区别是蒸镀剥离层时只蒸镀金属co,无小分子蒸发源。
53.对照例2
54.对照例2与实施例1工艺完全相同,其唯一区别是蒸镀剥离层时只蒸镀小分子二甲基咪唑,无金属蒸发源。
55.对照例3
56.对照例3与实施例1工艺完全相同,其唯一区别是无溅射铜种子层的过程,直接电镀加厚和表面处理过程。
57.样品评估方法
58.样品收卷后在100米长度内随机取样10片,与半固化片叠合进行高温真空热压板。热压结束降温后逐片剥离载体,记录剥离过程中的问题并统计肉眼所见针孔等缺陷。
59.结果分析
60.no.剥离过程剥离后极薄铜箔表面情况实施例1易剥离表面铜箔颜色均一,无渗胶斑点实施例2易剥离表面铜箔颜色均一,无渗胶斑点实施例3易剥离表面铜箔颜色均一,无渗胶斑点对照例1较难剥离,局部粘连表面颜色不一致,局部有灰色斑和因粘连造成的孔对照例2极易剥离表面颜色均一,但局部稍有粘连和因粘连造成的孔对照例3较难剥离,局部粘连表面颜色不均一,有较多渗胶斑点和粘连孔
61.从实验结果可见,利用本发明方法制备剥离层,能够实现较好的载体层剥离,极薄铜箔致密连续无针孔。对照例1中没有蒸镀有机小分子,剥离层为金属钴,钴与阻挡层金属镍以及种子铜层结合力比较强,因此较难剥离。对照例2中只蒸镀小分子二甲基咪唑,没有
形成更加稳定的络合物,所以在电镀加厚和表面处理过程中就比较容易褶皱脱落破裂,而且由于其不稳定性,溅射种子铜层后薄膜连续性较差,造成局部粘连。对照例3没有溅射种子铜层,在电镀加厚过程中,作为剥离层的二甲基咪唑钴在溶液中比较容易被破坏,因此造成剥离力不均匀,局部粘连,同时,电镀加厚的铜层不致密,存在较多针孔。
62.综上:本方法通过同时蒸镀金属和易络合小分子,制备了较为稳定的剥离层,再通过溅射制备种子铜层,保障了后续电镀的稳定性和铜层致密性,实现了附载体极薄铜箔的稳定量产,因此本方法具有广泛的应用价值和重大的经济效益。