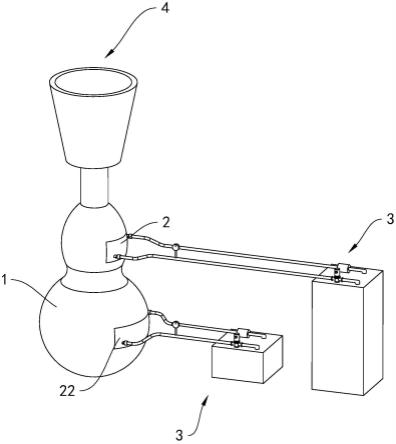
1.本技术涉及熔模铸造技术领域,特别涉及一种熔模铸造模具。
背景技术:2.在熔模铸造过程中,铸件壁厚处金属液散热较慢,形成的热节部位,热节部位因补缩不足会形成缩孔。
3.熔模铸造的过程主要包括熔蜡、浇铸金属液及后处理等工序,外冷铁是解决极端件内部缩孔缺陷的一个重要结构,外冷铁布置于蜡模的指定区域集成一个壳体,此时再浇铸金属液,覆盖有外冷铁位置的金属液冷却速度将更快,由此形成差异化的冷却速度,缓解热节部位的缩孔情况。
4.目前,常见的采用外冷铁局部冷却的熔模铸件包括铸件型壳和外冷铁,外冷铁安装在型壳上。浇筑时采用吹气或者水冷的方式对裸露在模具之外的冷铁部分进行强制冷却,达到加快铸件热节部位金属液凝固的目的。
5.针对上述技术方案,发明人发现由于铸件不同热节部位厚度不同,对于外冷铁所要求的温度也不相同。上述方案在浇注时,通过吹风或者水冷的方式对外冷铁进行集中降温,不同部位的外冷铁降温速度相同,依然容易存在缩孔情况。
技术实现要素:6.为了解决铸件不同热节部位外冷铁温度相同的问题,本技术提供了一种熔模铸造模具。
7.本技术提供的一种熔模铸造模具,采用如下的技术方案:
8.一种熔模铸造模具,包括型壳,所述型壳上设有冷铁,所述冷铁上可拆卸连接有冷却系统,所述冷却系统包括用于输送冷却介质进行循环的循环系统、用于控制循环系统运行的温控系统。
9.通过采用上述技术方案,在冷铁上能够额外快速组装冷却系统,冷铁与冷却系统连接,其中循环系统形成整体的冷媒循环,促使冷铁能够通过冷媒带走热量,提升降温速度,另外,通过温控系统调节不同热节部位的冷铁温度,使得不同部位的冷铁温度不一致,达到差异化降温的效果,间接提高不同位置的热节部位的凝固速度,使金属液在型壳内尽量均匀凝固,减少缩孔现象,提高铸件质量。
10.在一个具体的可实施方案中:所述冷铁内盘旋设有冷媒通道,所述冷铁上设有进口接头与出口接头,所述进口接头与所述出口接头均与冷媒通道连通。
11.通过采用上述技术方案,在冷铁内部设置冷媒通道,冷却介质通过进口接头进入冷铁内部,对冷铁进行降温,然后由出口接头流出冷铁。该过程中,冷却介质在冷铁内部流动,使冷铁温度更均匀;而冷媒通道盘旋设置在冷铁内部,延长了冷却介质在冷铁内部流动时滞留的时间,冷铁内的冷却体积较大,覆盖度较广,提高冷铁整体的冷却效果。
12.在一个具体的可实施方案中:所述循环系统包括循环泵、冷却器和冷却介质容器,
所述循环泵的出口与进口接头连通,所述冷却器的进口与出口接头连通,所述循环泵的进口与冷却器的出口均与冷却介质容器连通。
13.通过采用上述技术方案,冷却介质盛放在冷却介质容器中,在循环泵的作用下在冷铁与冷却器之间循环流动,实现对冷铁的降温效果,由于循环泵的持续作业,相比传统的吹气,冷却效果更好,且能够借助循环泵实现冷却介质不同的流速,达到差异化降温的效果。
14.在一个具体的可实施方案中:所述进口接头与所述出口接头设有外螺纹,所述循环泵的出口设有第一连接头,所述冷却器的进口设有第二连接头,所述第一连接头与进口接头螺纹连接,所述第二连接头与出口接头螺纹连接。
15.通过采用上述技术方案,采用螺纹连接的方式将冷铁接入冷却系统中,便于冷铁的安装与拆卸。
16.在一个具体的可实施方案中:所述循环泵与所述第一连接头之间设有流量阀。
17.通过采用上述技术方案,通过流量阀调节不同部位冷铁内冷却介质流速,实现调节不同部位冷铁温度的效果
18.在一个具体的可实施方案中:所述温控系统与循环泵电连接,所述温控系统为plc或单片机。
19.通过采用上述技术方案,温控系统控制循环泵的功率,即能够控制冷却介质的流速,在流速变化的情况下,实现冷铁差异化的降温。
20.在一个具体的可实施方案中:所述型壳上开有安装口,所述冷铁嵌装在所述安装口内。
21.通过采用上述技术方案,在型壳上设置安装口,将冷铁嵌装在安装孔内,能够尽量避免冷铁在型壳上的移动,提高铸件质量。
22.在一个具体的可实施方案中:所述冷铁上设有凸台,所述安装口内设有与凸台相配合的定位台,所述凸台与所述定位台卡合,所述凸台高度与所述定位台厚度相同。
23.通过采用上述技术方案,由于冷铁是通过安装口嵌入型壳内,通过定位台与凸台卡合,在将冷铁嵌入安装口时,能够尽量避免冷铁插入型壳深度过大,所以定位台与凸台具有限位效果。
24.在一个具体的可实施方案中:所述冷铁与所述安装口之间通过密封胶密封。
25.通过采用上述技术方案,由于浇筑铸件时需要对型壳内的型腔内注入金属液,通过密封胶对冷铁与型壳之间的缝隙进行密封,能够尽量避免金属液渗出。
26.综上所述,本技术至少包含一种有益技术效果:
27.1、通过冷却系统调节不同热节部位的冷铁温度,间接控制热节部位的凝固速度,使金属液在型壳内尽量均匀凝固,减少缩孔现象,提高铸件质量。
28.2、采用螺纹连接的方式将冷铁接入冷却系统中,便于冷铁安装与拆卸。
附图说明
29.图1为本技术实施例的整体结构示意图;
30.图2为本技术实施例用于体现型壳的结构示意图;
31.图3为本技术实施例用于体现冷铁的剖视图;
32.图4为本技术实施例用于体现冷却系统的结构图。
33.附图标记说明:
34.1、型壳;11安装口;12、定位台;2、冷铁;21、冷媒通道;22、进口接头;23、出口接头;24、凸台;3、冷却系统;31、循环泵;32、冷却器;33、第一连接头;34、流量阀;35、冷却介质容器;36、第二连接头;4、浇注口。
具体实施方式
35.以下结合附图对本技术作进一步详细说明。
36.本技术公开了一种熔模铸造模具,参考图1,熔模铸造模具包括型壳1、连接于型壳1上方的浇注口4,金属液通过浇注口4进入型壳1。型壳1上嵌装有冷铁2,冷铁2与型壳1内腔相通,冷铁2上连接有冷却系统3。冷却系统3包括循环系统和温控系统,通过循环系统能够带走热节部位的冷铁2的温度,通过温控系统能够控制循环系统内冷却介质的流速,即将冷铁2的温度差异化,降温速度达到差异化的效果。
37.冷铁2与型壳1之间通过工业密封胶密封,密封胶可选用耐火泥等耐高温材料,提高型壳1与冷铁2连接处的相对密封性。
38.参考图2,型壳1上开有安装口11,安装口11内固定连接有定位台12,定位台12相对安装口11形成阶梯面,冷铁2上固定连接有与定位台12相卡合的凸台24。当冷铁2嵌装在型壳1上时,定位台12与凸台24相互卡合,能够尽量避免冷铁2过分插入型壳1内,实现冷铁2的位置定位。
39.参考图2和图3,冷铁2裸露在型壳1外部的表面上固定连接有进口接头22和出口接头23,冷铁2内部留有冷媒通道21,冷媒通道21整体在冷铁2内部往复盘旋,覆盖于冷铁2的各个位置,且冷媒通道21的入口与进口接头22相通,冷媒通道21的出口与出口接头23相通。冷却介质通过进口接头22进入冷铁2内部,在给冷铁2降温后由出口接头23流出冷铁2。
40.参考图2和图4,冷却系统3包括冷却介质容器35、循环泵31和冷却器32,循环泵31与冷却器32固定安装在冷却介质容器35上方,循环泵31的进口与冷却器32的出口均与冷却介质容器35连通。循环泵31的出口固定连接有第一连接头33,第一连接头33与进口接头22螺纹连接(结合图1);冷却器的进口固定连接有第二连接头36,第二连接头36与出口接头23螺纹连接(结合图1)。在循环泵31的作用下,冷却介质从冷却介质容器35流出,然后进入冷铁2,在给冷铁2降温后经过冷却器32降温,最后流入冷却介质容器35。在循环泵31与第一连接头33之间串联有流量阀34,通过流量阀34获取当前的介质流速并进行适应性调整,达到控制冷铁2 温度的效果。
41.其中,温控系统与循环泵31电连接,温控系统采用下位机中的plc或单片机,通过温控系统可控制循环泵31的功率,在循环泵31的功率调节后,即相当于调节了冷却介质的流速,对冷铁2的降温也能实现差异化调整。
42.本实施例的工作原理为:金属液通过浇筑孔4进入在型壳1内,冷铁2嵌装在型壳1的不同热节部位,金属液在型壳1内凝固时,通过冷却系统3控制不同部位的冷铁2的温度,从而控制型壳1内金属液的凝固速度,使型壳1内的金属液尽量均匀凝固,减少缩孔缺陷,提高铸件质量。
43.以上所述仅是本技术的优选实施方式,本技术的保护范围并不仅局限于上述实施
例,凡属于本实用新型思路下的技术方案均属于本技术的保护范围。应当指出,对于本技术领域的普通技术人员来说,在不脱离本实用新型原理前提下的若干改进和润饰,这些改进和润饰也应视为本技术的保护范围。