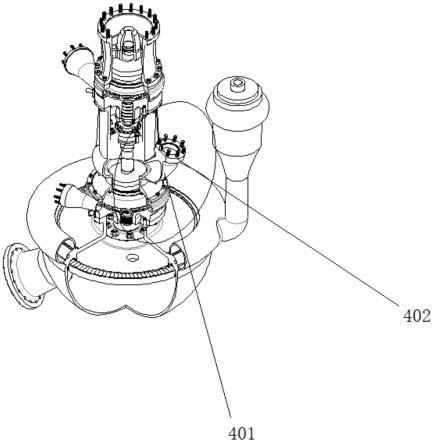
1.本实用新型涉及退火炉领域,具体而言,涉及一种退火炉自吸式燃烧结构。
背景技术:2.退火是一种金属热处理工艺,指的是将金属缓慢加热到一定温度,保持足够时间,然后以适宜速度冷却。目的是降低硬度,改善切削加工性;降低残余应力,稳定尺寸,减少变形与裂纹倾向;细化晶粒,调整组织,消除组织缺陷。准确的说,退火是一种对材料的热处理工艺,包括金属材料、非金属材料。而且新材料的退火目的也与传统金属退火存在异同。
3.当前退火炉燃烧方式是通过管道进气燃烧的方式进行燃烧,这种火焰燃烧时会产生温差,所以生产时会应力消除不好的现象,还会造成产品的应力不均匀等情况,根据目前存在的这些问题,因此我们对此做出改进,提出一种退火炉自吸式燃烧结构。
技术实现要素:4.本实用新型的目的在于:针对目前存在的背景技术提出的问题,为了实现上述实用新型目的,本实用新型提供了以下技术方案:一种退火炉自吸式燃烧结构,包括所述主连接板的上方设有燃烧机构,所述燃烧机构包括燃气灯杆、燃气输气管、燃气火花塞、燃气喷火孔、燃气氧气通气管,所述燃气灯杆的内表面设置有所述燃气输气管,所述燃气输气管的底端连接着所述燃气火花塞,所述燃气输气管的顶端嵌套着所述燃气喷火孔,所述燃气灯杆外侧的顶端镶嵌连接所述燃气氧气通气管,所述主连接板的底端设有燃料进气机构,所述燃烧机构的表面设有自吸进气机构。
5.作为本实用新型优选的技术方案,所述燃气灯杆设在所述主连接板的上表面。
6.作为本实用新型优选的技术方案,所述燃气输气管穿过所述燃气火花塞贯穿所述主连接板。
7.作为本实用新型优选的技术方案,所述燃料进气机构包括燃烧气体缓存腔、退火炉燃烧进气管、进气管法兰盘、紧固螺栓孔,所述燃烧气体缓存腔的左表面镶嵌连接所述退火炉燃烧进气管,所述退火炉燃烧进气管的前端焊接连接所述进气管法兰盘,所述进气管法兰盘的外表面环型阵列着所述紧固螺栓孔。
8.作为本实用新型优选的技术方案,所述燃烧气体缓存腔设在所述主连接板的底端,而所述主连接板可作为密封盖使用。
9.作为本实用新型优选的技术方案,所述燃气输气管贯穿着所述主连接板底端则处于所述燃烧气体缓存腔内。
10.作为本实用新型优选的技术方案,所述自吸进气机构包括负压自吸进气管、进气管法兰连接盘,所述燃气灯杆外侧的底端镶嵌连接所述负压自吸进气管,所述负压自吸进气管的前端焊接连接所述进气管法兰连接盘。
11.与现有技术相比,本实用新型的有益效果:
12.在本实用新型的方案中:通过燃气输气管进行燃气输气,并通过燃气火花塞将燃
气打火,并通过燃气喷火孔进行喷火,燃气氧气通气管在燃气喷火孔燃烧的过程中提供氧气,同时通过燃烧气体缓存腔可对燃气输气管输出的燃气进行缓存,在燃烧的过程中,当燃烧气体缓存腔中的气体在消耗的过程中,燃烧气体缓存腔内会产生负压,进而通过负压使得负压自吸进气管吸入氧气使得燃烧更加的均匀,进而减少燃烧不均匀而使得退火炉中的温度产生温差,进而更加有效的在退火的过程中消除应力,来达到产品的稳定性,通过在生产成型过程中高效运行,改善生产条件,从而提高了其产品强度和稳定性。
附图说明:
13.图1为本实用新型提供的结构示意图;
14.图2为本实用新型提供的结构示意图;
15.图3为本实用新型提供的剖视结构示意图;
16.图4为本实用新型提供的主视图;
17.图5为本实用新型提供的侧视图;
18.图6为本实用新型提供的俯视图。
19.图中标示:
20.1、主连接板;
21.2、燃烧机构;201、燃气灯杆;202、燃气输气管;203、燃气火花塞;204、燃气喷火孔;205、燃气氧气通气管;
22.3、燃料进气机构;301、燃烧气体缓存腔;302、退火炉燃烧进气管;303、进气管法兰盘;3031、紧固螺栓孔;
23.4、自吸进气机构;401、负压自吸进气管;402、进气管法兰连接盘。
具体实施方式
24.为使本实用新型实施例的目的、技术方案和优点更加清楚,下面将结合附图,对本实用新型实施例中的技术方案进行清楚、完整的描述。显然,所描述的实施例是本实用新型的一部分实施例,而不是全部的实施例。
25.因此,以下对本实用新型的实施例的详细描述并非旨在限制要求保护的本实用新型的范围,而是仅仅表示本实用新型的部分实施例。基于本实用新型中的实施例,本领域普通技术人员在没有作出创造性劳动前提下所获得的所有其他实施例,都属于本实用新型保护的范围,需要说明的是,在不冲突的情况下,本实用新型中的实施例及实施例中的特征和技术方案可以相互组合,应注意到:相似的标号和字母在下面的附图中表示类似项,因此,一旦某一项在一个附图中被定义,则在随后的附图中不需要对其进行进一步定义和解释。
26.实施例1:请参阅图1-6,一种退火炉自吸式燃烧结构,包括主连接板1的上方设有燃烧机构2,燃烧机构2包括燃气灯杆201、燃气输气管202、燃气火花塞203、燃气喷火孔204、燃气氧气通气管205,燃气灯杆201的内表面设置有燃气输气管202,燃气输气管202的底端连接着燃气火花塞203,燃气输气管202的顶端嵌套着燃气喷火孔204,燃气灯杆201外侧的顶端镶嵌连接燃气氧气通气管205,主连接板1的底端设有燃料进气机构3,燃烧机构2的表面设有自吸进气机构4。燃气灯杆201设在主连接板1的上表面。燃气输气管202穿过燃气火花塞203贯穿主连接板1。
27.燃料进气机构3包括燃烧气体缓存腔301、退火炉燃烧进气管302、进气管法兰盘303、紧固螺栓孔3031,燃烧气体缓存腔301的左表面镶嵌连接退火炉燃烧进气管302,退火炉燃烧进气管302的前端焊接连接进气管法兰盘303,进气管法兰盘303的外表面环型阵列着紧固螺栓孔3031。燃烧气体缓存腔301设在主连接板1的底端,而主连接板1可作为密封盖使用。燃气输气管202贯穿着主连接板1底端则处于燃烧气体缓存腔301内。
28.自吸进气机构4包括负压自吸进气管401、进气管法兰连接盘402,燃气灯杆201外侧的底端镶嵌连接负压自吸进气管401,负压自吸进气管401的前端焊接连接进气管法兰连接盘402。
29.实施例2:请参阅图1-6,一种退火炉自吸式燃烧结构,燃烧气体缓存腔301的左表面镶嵌连接退火炉燃烧进气管302,退火炉燃烧进气管302的前端焊接连接进气管法兰盘303,进气管法兰盘303的外表面环型阵列着紧固螺栓孔3031。燃烧气体缓存腔301设在主连接板1的底端,而主连接板1可作为密封盖使用。燃气输气管202贯穿着主连接板1底端则处于燃烧气体缓存腔301内
30.主连接板1的上方设有燃烧机构2,燃气灯杆201的内表面设置有燃气输气管202,燃气输气管202的底端连接着燃气火花塞203,燃气输气管202的顶端嵌套着燃气喷火孔204,燃气灯杆201外侧的顶端镶嵌连接燃气氧气通气管205,燃气灯杆201外侧的底端镶嵌连接负压自吸进气管401,负压自吸进气管401的前端焊接连接进气管法兰连接盘402,主连接板1的底端设有燃料进气机构3,燃烧机构2的表面设有自吸进气机构4。燃气灯杆201设在主连接板1的上表面。燃气输气管202穿过燃气火花塞203贯穿主连接板1。
31.工作原理:本实用新型在使用的过程中,首先通过燃气输气管202进行燃气输气,并通过燃气火花塞203将燃气打火,并通过燃气喷火孔204进行喷火,燃气氧气通气管205在燃气喷火孔204燃烧的过程中提供氧气,同时通过燃烧气体缓存腔301可对燃气输气管202输出的燃气进行缓存,在燃烧的过程中,当燃烧气体缓存腔301中的气体在消耗的过程中,燃烧气体缓存腔301内会产生负压,进而通过负压使得负压自吸进气管401吸入氧气使得燃烧更加的均匀,进而减少燃烧不均匀而使得退火炉中的温度产生温差,进而更加有效的在退火的过程中消除应力。
32.以上实施例仅用以说明本实用新型而并非限制本实用新型所描述的技术方案,尽管本说明书参照上述的各个实施例对本实用新型已进行了详细的说明,但本实用新型不局限于上述具体实施方式,因此任何对本实用新型进行修改或等同替换;而一切不脱离实用新型的精神和范围的技术方案及其改进,其均涵盖在本实用新型的权利要求范围当中。