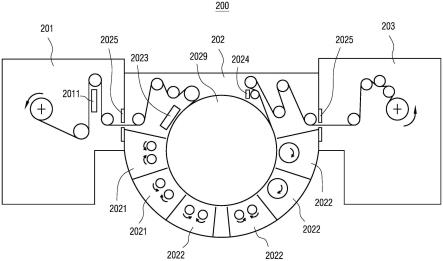
1.本实用新型涉及一种用于复合铜箔膜的预镀膜处理设备。
背景技术:2.锂离子电池中的集流体由用于导电的金属箔膜组成,主要作用是承载正负极的电极材料,同时收集电流和传导电子。常见的正极集流体采用的是铝箔,常见的负极集流体采用的是铜箔。用做集流体的铝箔和铜箔主要用于导电,并不参与活性反应,因而在提高电池的能量密度的需求下,其厚度已经减小到了强度极限,已经没有继续减薄的空间。
3.现有技术的金属箔膜需要在高温下将靶材蒸发成气体然后附着在高分子薄膜层的表面,靶材的蒸发温度越高,高分子薄膜层越容易出现熔断或烫破之类的缺陷。因而,现有技术通过磁控溅射或蒸镀的方式生产的一般是复合铝箔,很少有制备负极集流体的复合铜箔的情形,因为铜的蒸发温度更高。靶材的蒸发温度越高,就需要高分子薄膜层的运转速度越快,因而形成的金属层也会越薄,金属箔膜的导电性能也会相应的变差,因而现有的复合金属箔及其制备工艺难以适用于生产制备可用做集流体的复合铜箔膜。
4.另外现有技术也缺少适用于可用做锂离子电池的负极集流体的复合铜箔膜的制造系统,也缺少对复合铜箔膜进行预镀膜处理的设备。
技术实现要素:5.本实用新型要解决的技术问题是提供一种用于复合铜箔膜的预镀膜处理设备,以减少或避免前面所提到的问题。
6.为解决上述技术问题,本实用新型提出了一种用于复合铜箔膜的预镀膜处理设备,用于对聚酯薄膜进行预处理并在其两侧形成金属铜溅射层;其中,所述预镀膜处理设备包括对制膜设备制备获得的聚酯薄膜的表面进行电晕处理以获得电晕层的电晕腔、环形真空溅射腔以及收料腔;经过电晕处理的聚酯薄膜由电晕腔输入环形真空溅射腔,通过环形真空溅射腔,在电晕层的外侧溅射形成阻隔层,在阻隔层的外侧溅射形成金属铜溅射层;形成金属铜溅射层的聚酯薄膜由环形真空溅射腔输入收料腔中将聚酯薄膜收料成卷。
7.优选的,所述环形真空溅射腔至少包括一个设置于上游的阻隔料溅射腔,阻隔料溅射腔的下游至少包括一个铜料溅射腔。
8.优选的,所述环形真空溅射腔的进料口一侧设置有至少一个对输入的聚脂薄膜进行去水汽烘烤的第一红外加热单元。
9.优选的,所述环形真空溅射腔的出料口一侧设置有至少一个对输料滚轴进行加热的第二红外加热单元,输料滚轴进而对输出的聚脂薄膜进一步加热。
10.优选的,所述环形真空溅射腔的进料口和出料口均设置有换料闸门。
11.优选的,电晕腔内设置有多组张紧辊;电晕腔内部设置有用于在聚酯薄膜的至少一侧形成电晕层的电晕电极。
12.优选的,电晕腔、环形真空溅射腔和收料腔形成为一个整体结构。
13.本实用新型的预镀膜处理设备通过对聚脂薄膜进行表面电晕处理,提高了阻隔层的附着力,阻隔层形成对聚脂薄膜的包覆隔绝,并在聚脂薄膜的表面形成疏水结构,避免形成导电层时的水分吸收和释放问题。
附图说明
14.以下附图仅旨在于对本技术做示意性说明和解释,并不限定本技术的范围。
15.图1显示的是根据本技术的一个具体实施例的复合铜箔膜的结构示意图。
16.图2显示的是根据本技术的另一个具体实施例的复合铜箔膜的结构示意图。
17.图3显示的是根据本技术的一个具体实施例的用于复合铜箔膜的制造系统的结构示意图。
18.图4显示的是根据本技术的一个具体实施例的一种用于复合铜箔膜的预镀膜处理设备的结构示意图。
具体实施方式
19.为了对本技术的技术特征、目的和效果有更加清楚的理解,现对照附图说明本技术的具体实施方式。其中,相同的部件采用相同的标号。
20.如图1-2所示,本实用新型提出了一种可用做锂离子电池的负极集流体的复合铜箔膜,该复合铜箔膜由基材层1和附着在基材层1的两侧的导电层2构成,该导电层2主要由金属铜构成。如前所述,由于金属铜的蒸发温度较高,如果通过蒸镀的方式附着在高分子材料构成的基材层1的表面会破坏基材层1的表面结构的均匀性,而且难以获得足够的电气性能所需的厚度,并且堆叠的厚度越大越容易脱落掉粉,不适于用做负极集流体。
21.有鉴于此,本技术提出了一种复合铜箔膜,其中的导电层2采用了多层导电结构,在图示具体实施例中,导电层2从内向外依次包括金属铜溅射层21、金属铜电镀层22以及保护层23。其中,金属铜溅射层21是采用真空溅射工艺形成在基材层1的两侧表面的一层厚度为5-15nm的金属铜,金属铜电镀层22是采用水电镀工艺在金属铜溅射层21的外表面上生长形成的一层100-500nm的金属铜,保护层23是通过电镀或化学腐蚀工艺对金属铜电镀层22的外表面进行钝化处理后形成的致密保护层,优选的,所述保护层23是通过电镀工艺形成的一层5-15nm的金属铬保护层。
22.本技术的复合铜箔膜中,真空溅射形成的金属铜溅射层的致密性和附着力远优于蒸镀工艺,而且由于所需厚度很薄,基材层的运转速度可以很快,基本杜绝了基材层出现熔断或烫破之类的缺陷的可能性。金属铜溅射层的厚度虽然很薄,但是可以提供基本的导电性能,因而可以进一步通过水电镀的方式在其表面生长得到较厚的金属铜层。通过真空溅射工艺和水电镀工艺的结合,本技术可以在不破坏基材层表面结构的前提下获得优异的电气性能和附着力,后面将对此进一步说明。
23.另外,为了避免由于基材层的表面结构不均匀所导致的金属铜层附着力不够的问题,本技术还提出了一种改进的基材层1,在本技术的一个具体实施例中,本技术的基材层1是由添加了聚酯功能母料的聚酯薄膜制成的,所述基材层1可以是表层和底层添加了所述聚酯功能母料的包含表层a、芯层b、底层c的三层结构的聚酯薄膜(图1),或者是添加了聚酯功能母料的单层结构的聚酯薄膜(图2)。
24.本实用新型中所称的聚酯是指由选自包含二元酸的多元羧酸以及它们的成酯性衍生物中的一种或二种以上、与选自包含二元醇的多元醇中的一种或二种以上形成的聚酯;或由羟基羧酸以及它们的成酯性衍生物形成的聚酯;或由环状酯形成的聚酯。聚酯的制造可以按照现有公知的方法进行。例如,以pet的制备为例,其可以通过如下方法获得:对苯二甲酸与乙二醇的酯化后进行缩聚的方法;或者以对苯二甲酸二甲酯之类的对苯二甲酸的烷基酯与乙二醇进行酯交换反应后进行缩聚的方法。本实用新型的聚酯优选为pet。
25.在一个具体实施例中,构成所述基材层1的所述聚酯薄膜为含有5~20wt%的聚酯功能母料的单层聚酯薄膜,或者为表层a和底层c含有5~20wt%的聚酯功能母料的包含表层a、芯层b、底层c的三层结构的聚酯薄膜,所述聚酯功能母料由包括如下重量份的原料制备而成:聚间苯二亚甲基二酰胺30-50重量份、新癸酸钴1-3重量份、二丁基羟基甲苯3-5重量份、1,4-二碘苯5~10重量份、二氧化硅20~30重量份、pet 50-100重量份。
26.本实用新型的聚酯功能母料可以制备成颗粒或者切片形式,在生产聚酯薄膜的过程中添加到普通聚酯中,以制备获得本实用新型的基材层1。例如,可以将80~95wt%的不含其它成分的聚酯与5~20wt%的本实用新型的聚酯功能母料进行熔融共混,然后通过拉伸等工艺生产获得单层结构的基材层1,或者通过多层共挤工艺获得本实用新型的基材层1的表层结构等。
27.本实用新型的聚酯功能母料的各原料组分,均可以以颗粒料的形式均匀混合之后,利用诸如挤出机之类的设备挤出、造粒获得本实用新型的聚酯功能母料。
28.在一个具体实施例中,可以在常温下,将50-100重量份的粉状pet、20~30重量份的纳米二氧化硅、30-50重量份的粉状聚间苯二亚甲基二酰胺、1-3重量份的粉状新癸酸钴、3-5重量份的粉状二丁基羟基甲苯以及5~10重量份的粉状1,4-二碘苯加入混料机中预分散混合,转速在1500~2000rpm,混合30~60分钟,形成混合料。然后通过双螺杆挤出机进行熔融挤出,之后水冷造粒或切片,获得所述聚酯功能母料。
29.在另一个具体实施例中,例如,可以在制备获得聚酯功能母料的切片之后,取5~20wt%的聚酯功能母料,添加到80~95wt%的pet颗粒中均匀混合,二者熔融共混,最后通过拉伸等工艺生产获得单层结构的基材层1,或者通过多层共挤工艺获得三层结构的基材层1的表层a和底层b。
30.下面以单层聚酯薄膜为例,进一步说明本实用新型的用于复合铜箔膜的聚酯薄膜的制备方法。本实用新型的用于复合铜箔膜的聚酯薄膜的制备方法包括如下步骤:
31.将以下重量比的组分:80~95wt%的pet树脂,5~20wt%的聚酯功能母料分别经过电子秤计量,进入混合料仓中进行混合制成混合料。
32.之后混合料进入排气式双螺杆挤出机,调整双螺杆挤出机的温度为270℃~280℃。
33.物料在挤出机中熔融后,经过过滤,挤出制成厚片。厚片的厚度、轮廓可以通过挤出机挤出量、铸片辊转速、模头开度进行调整。
34.将上述厚片在50℃~90℃温度下预热,进入300℃~500℃的红外加热区,用40~150m/min的线速度进行纵向拉伸,纵向拉伸倍率是4.0,得到拉伸片。
35.将拉伸片在90℃~120℃温度下预热,在100℃~160℃温度下进行横向拉伸,横向拉伸倍率是3.8。之后在160℃~240℃温度下定型,再经过100℃~50℃温度冷却,制得用于
复合铜箔膜的聚酯薄膜。
36.制得的聚酯薄膜的厚度为6-10μm。
37.下面以三层聚酯薄膜为例,进一步说明本实用新型的用于复合铜箔膜的聚酯薄膜的制备方法。本实用新型的用于复合铜箔膜的聚酯薄膜的制备方法包括如下步骤:
38.将以下重量比的组分:80~95wt%的pet树脂,5~20wt%的聚酯功能母料分别经过电子秤计量,进入混合料仓中进行混合制成混合料。
39.之后混合料进入排气式双螺杆挤出机e。
40.将100%的pet树脂,投入预结晶器中,以160℃温度预结晶15分钟,之后pet料进入干燥塔中,在160℃温度下干燥6小时,之后进入单螺杆挤出机f。
41.调整双螺杆挤出机e和f的温度为270℃~280℃。
42.物料在两台挤出机中熔融后,经过过滤,以双螺杆挤出机e挤出的物料作为表层a和底层c,单螺杆挤出机f挤出的物料作为芯层b,经过多层共挤工艺制成三层复合的厚片。厚片的厚度、轮廓可以通过挤出机挤出量、铸片辊转速、模头开度进行调整。
43.将上述厚片在50℃~90℃温度下预热,进入300℃~500℃的红外加热区,用40~150m/min的线速度进行纵向拉伸,纵向拉伸倍率是4.0,得到拉伸片。
44.将拉伸片在90℃~120℃温度下预热,在100℃~160℃温度下进行横向拉伸,横向拉伸倍率是3.8。之后在160℃~240℃温度下定型,再经过100℃~50℃温度冷却,制得所述三层结构的聚酯薄膜。
45.制得的聚酯薄膜的厚度为6-10μm,其中a层的厚度为1-2μm,b层的厚度为2-8μm,c层的厚度为1-2μm。
46.实施例1-5
47.按照下表的原料重量份比例,分别制备获得聚酯功能母料切片,然后投入普通pet树脂制备获得单层结构的用于复合铜箔膜的聚酯薄膜。
[0048] 实施例1实施例2实施例3实施例4实施例5聚间苯二亚甲基二酰胺3035404550新癸酸钴11.522.53二丁基羟基甲苯33.544.551,4-二碘苯577.5810二氧化硅2022252730pet50657585100制备单层基材层的切片量5wt%10wt%13wt%15wt%20wt%基材层厚度μm678910
[0049]
对比例6-10
[0050]
按照上述实施例同样的方法,按下表的原料重量份比例制备作为对比的聚酯薄膜。
[0051]
[0052][0053]
分别测试制备获得各聚脂薄膜的性能参数,同时将未添加任何功能母料的纯pet制备的8μm厚的薄膜进行对比,各性能参数如下表所示。
[0054][0055]
分别通过真空溅射工艺在上表所述聚脂薄膜的两侧表面形成金属铜溅射层,控制真空溅射的两侧金属铜层的厚度均为5nm,测试制备形成的薄膜的表面裂纹参数。
[0056]
[0057][0058]
通过上述膜层的性能参数和金属镀层的裂纹情况可见,通过添加本技术的聚酯功能母料制备的聚酯薄膜,其孔隙率、吸水率、氧气透过率等性能均有大幅提升,而且形成金属铜导电层之后未见明显裂纹的扩展。
[0059]
进一步地,测试上表所示聚酯薄膜的两侧的金属铜溅射层的电阻率差异,如下表所示。
[0060][0061][0062]
通过添加本技术的聚酯功能母料制备的聚酯薄膜,其上形成的金属铜溅射层的电阻率差异明显小于未添加功能母料的薄膜,表明其两侧结构具有更加优异的一致性。
[0063]
进一步地,由于本技术需要首先在基材层1的表面形成金属铜溅射层21,因而溅射
时基材层1需要控制在较低的温度下运转。虽然改进后的基材层1的聚脂薄膜具有优异的孔隙率、吸水率、氧气透过率等性能,但是仍然需要防范低温下聚脂薄膜表面吸水然后溅射时释放水分对真空度的干扰问题。
[0064]
因此,在一个具体实施例中,如图2所示,为了避免溅射时基材层1的水分吸收和释放问题,导电层2和基材层1之间的基材层1的外侧还溅射形成有一层阻隔层11,以提高导电层2的性能。具体地,可以通过双旋转阴极、中频反应磁控溅射的方式在基材层1的两侧表面分别沉积一层2-3nm的二氧化硅构成的阻隔层11,以对基材层1的表面形成包覆隔绝,并在基材层1的表面形成疏水结构。
[0065]
再进一步地,由于阻隔层11的厚度很小,为了提高阻隔层11在基材层1的表面的附着力,在溅射形成阻隔层11之前,优选对基材层1的表面进行电晕处理,以在基材层1的表面形成一层1-2nm厚的电晕层10,阻隔层11形成在电晕层10的外侧。电晕处理是一种现有技术,其基本原理是利用高频率高电压在被处理的塑料表面电晕放电,使基材层1的表面变粗糙,以增加基材层1的表面对阻隔层11的附着能力。
[0066]
当然,本领域技术人员应当理解,所述电晕层10和阻隔层11同样也可以形成在图1所示的三层结构的聚酯薄膜构成的基材层1的表面。
[0067]
下面参照图3-4进一步说明本技术的用于复合铜箔膜的制造系统。
[0068]
如图所示,本技术的一种复合铜箔膜制造系统包括用于制备构成基材层1的聚脂薄膜的制膜设备100、用于对聚酯薄膜进行预处理并在其两侧形成金属铜溅射层21的预镀膜处理设备200、以及在金属铜溅射层21的外侧形成金属层电镀层22和保护层23的水电镀设备300。
[0069]
其中,所述制膜设备100包括用于制备聚酯功能母料的混料机101和第一挤出机102。如前所述,可以在常温下在混料机101中添加如下重量份的原料:聚间苯二亚甲基二酰胺30-50重量份、新癸酸钴1-3重量份、二丁基羟基甲苯3-5重量份、1,4-二碘苯5~10重量份、二氧化硅20~30重量份、pet 50-100重量份。更具体地,可以将50-100重量份的粉状pet、20~30重量份的纳米二氧化硅、30-50重量份的粉状聚间苯二亚甲基二酰胺、1-3重量份的粉状新癸酸钴、3-5重量份的粉状二丁基羟基甲苯以及5~10重量份的粉状1,4-二碘苯加入混料机101中预分散混合,转速在1500~2000rpm,混合30~60分钟,形成混合料。然后通过第一挤出机102(例如,双螺杆挤出机)进行熔融挤出,之后水冷造粒或切片,获得所述聚酯功能母料。
[0070]
从第一挤出机102输出的聚酯功能母料与普通pet树脂进料管103输入的普通pet树脂通过管道输入混合料仓104中均匀混合并进一步输入第二挤出机105。如前所述,例如,可以将第一挤出机102获得的5~20wt%的聚酯功能母料与普通pet树脂进料管103输入的80~95wt%的普通pet树脂,输入到混合料仓104中进行混合制成混合料,然后进入第二挤出机105(例如,排气式双螺杆挤出机e)。
[0071]
通过第二挤出机105熔融的聚酯功能母料分别通过表层管道和底层管道输入薄膜制备机构108制备获得聚酯薄膜的表层a以及底层c,普通pet树脂通过第三挤出机109(例如,单螺杆挤出机f)以及芯层管道输入薄膜制备机构108制备获得聚脂薄膜的芯层b。如前所述,例如,以双螺杆挤出机e挤出的物料作为表层a和底层c,单螺杆挤出机f挤出的物料作为芯层b,经过薄膜制备机构108的多层共挤工艺制成三层复合的厚片;将上述厚片在50℃
~90℃温度下预热,进入300℃~500℃的红外加热区,用40~150m/min的线速度进行纵向拉伸,纵向拉伸倍率是4.0,得到拉伸片;将拉伸片在90℃~120℃温度下预热,在100℃~160℃温度下进行横向拉伸,横向拉伸倍率是3.8;之后在160℃~240℃温度下定型,再经过100℃~50℃温度冷却,制得三层结构的聚酯薄膜。
[0072]
当然,所述制膜设备100也可以是任何一种现有的可用于制备单层结构或者三层结构的聚酯薄膜的设备。例如,所述制膜设备100可以是采用前述单层结构的聚酯薄膜的制备工艺的设备。
[0073]
进一步地,如图4所示,预镀膜处理设备200包括对制膜设备100制备获得的聚酯薄膜的表面进行电晕处理以获得电晕层10的电晕腔201、环形真空溅射腔202以及收料腔203;经过电晕处理的聚酯薄膜由电晕腔201输入环形真空溅射腔202,通过环形真空溅射腔202,在电晕层10的外侧溅射形成阻隔层11,在阻隔层11的外侧溅射形成金属铜溅射层21;形成金属铜溅射层21的聚酯薄膜由环形真空溅射腔202输入收料腔203中将聚酯薄膜收料成卷。
[0074]
电晕腔201、环形真空溅射腔202和收料腔203形成为一个整体结构,为了在换料时保持环形真空溅射腔202的真空度,在环形真空溅射腔202的进料口和出料口均设置有换料闸门2025,用于换料时将环形真空溅射腔202与电晕腔201和收料腔203隔绝,如图所示。换料闸门2025成对设置在环形真空溅射腔202的进料口和出料口的外侧,换料闸门2025之间留有供聚酯薄膜通过的狭缝,闸门闭合时将聚脂薄膜夹持在中间,伸出环形真空溅射腔202的聚酯薄膜可以分别与新的供料卷和收料卷的端部粘贴而后完成接续换料。
[0075]
电晕腔201内设置有多组张紧辊,以维持聚酯薄膜运转过程中的张紧度。电晕腔201内部设置有电晕电极2011,用于在聚酯薄膜的至少一侧形成电晕层10。
[0076]
图中结构可以看出,预镀膜处理设备200经过一次运转,仅可在聚酯薄膜的一侧形成阻隔层11和金属铜溅射层21,因此为了在聚酯薄膜两侧均形成阻隔层11和金属铜溅射层21,需要在一卷聚酯薄膜完成溅射之后,将收料卷重新装载到电晕腔201中在聚酯薄膜的另一侧再溅射一次。因此,电晕腔201中的电晕电极2011只需要设置一组结构,只需要在需要溅射的一侧形成电晕层10,而后方便在电晕层10上形成阻隔层11。
[0077]
环形真空溅射腔202的中部设置有一个中空的冷却辊2029,工作时冷却辊2029中通有冷却介质,聚脂薄膜紧贴在冷却辊2029的外侧运转,通过冷却辊2029将聚酯薄膜冷却到零下20-30摄氏度左右,以防止溅射时将聚酯薄膜烫破。
[0078]
围绕冷却辊2029,在环形真空溅射腔202中设置有多个溅射腔,在图中总共显示有七个腔室,其中中间的腔室没有设置溅射物料,两侧各有三个腔室可以作为溅射腔使用。
[0079]
其中,环形真空溅射腔202至少包括一个设置于上游的阻隔料溅射腔2021,阻隔料溅射腔2021的下游至少包括一个铜料溅射腔2022。例如,在聚酯薄膜运转的上游的头两个溅射腔可以设置为阻隔料溅射腔2021,其中可以设置例如形成二氧化硅阻隔层的两个对向旋转的棒材物料。溅射时棒材物料作为原料供给源,在高压作用下将二氧化硅之类的阻隔材料溅射到聚酯薄膜上。对向旋转的棒材物料可以形成更均匀的溅射层结构。在阻隔料溅射腔2021的下游的另外四个溅射腔可以设置为铜料溅射腔2022,其中前两个溅射腔中设置的是对向旋转的铜棒材物料。根据实际需要,可以仅将上游的第一个溅射腔作为阻隔料溅射腔2021,后续的三个溅射腔作为铜料溅射腔2022,最后的两个溅射腔可以设置单根铜棒材物料,以在最外侧形成同一方向分布的金属铜溅射层21,以便于后续水电镀时的铜层的
生产速度保持一致。
[0080]
为了避免聚酯薄膜表面的水汽对溅射的干扰,环形真空溅射腔202的进料口一侧设置有至少一个对输入的聚脂薄膜进行去水汽烘烤的第一红外加热单元2023。
[0081]
进一步地,由于溅射时聚酯薄膜保持在极低的温度下运转,低温聚酯薄膜进入收料腔203将会很容易在其上形成冷凝水,因此,在环形真空溅射腔202的出料口一侧设置有至少一个对输料滚轴进行加热的第二红外加热单元2024,输料滚轴进而对输出的聚脂薄膜进一步加热。采用对输料滚轴进行间接加热,是因为聚酯薄膜温度很低,直接加热温度场不均匀,容易烫破或者加热温度不一致,因而通过间接加热的方式的加热更均匀,提高聚酯薄膜的温度的效率也更高。
[0082]
回到图3,水电镀设备300包括铜电镀槽301和保护电镀槽302,形成有金属铜溅射层21的聚酯薄膜从预镀膜处理设备200输入铜电镀槽301,在金属铜溅射层21的外侧采用电镀工艺形成金属铜电镀层22;形成金属铜电镀层22的聚脂薄膜从铜电镀槽301输入保护电镀槽302,在金属铜电镀层22的外侧通过电镀工艺形成保护层23。
[0083]
如前所述,金属铜溅射层的厚度虽然很薄,但是可以提供基本的导电性能,因而通过预镀膜处理设备200处理之后的聚酯薄膜,其表面形成有一层金属铜溅射层21,之后采用传统已知的水电镀工艺,可以在铜电镀槽301和保护电镀槽302中分别形成金属铜电镀层22和保护层23。例如,可以在铜电镀槽301中添加硫酸铜为主的电解液,在保护电镀槽302中添加铬酐和硫酸为主的电解液,通过控制聚酯薄膜的运转速度和电镀槽的长度控制镀层的厚度。
[0084]
以实施例1-5制备的聚脂薄膜作为基材层,分别经过电晕处理、溅射阻隔层、溅射金属铜溅射层、电镀金属铜电镀层、电镀保护层,制备获得如下参数的复合铜箔膜。
[0085][0086]
通过测量参数可见,本技术的复合铜箔膜具备优异的电气性能,而且导电层附着力极强,常规使用几乎不会出现导电层剥离的情况。
[0087]
以上所述仅为本技术示意性的具体实施方式,并非用以限定本技术的范围。任何本领域的技术人员,在不脱离本技术的构思和原则的前提下所作的等同变化、修改与结合,
均应属于本技术保护的范围。