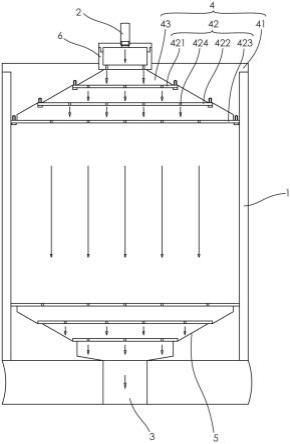
1.本实用新型涉及化学气相沉积炉技术领域,具体涉及一种化学气相沉积炉。
背景技术:2.近年来石墨材料在半导体等领域的应用越来越广泛,然而目前在半导体领域的诸多制造工艺涉及高温和使用腐蚀性气体的恶劣环境,在此环境条件下石墨材料损耗加快,寿命变短,甚至功能失效,严重影响安全生产及工艺稳定。
3.利用化学气相沉积技术制备的碳化物涂层,能够是石墨材料具有抗氧化、耐高温和耐酸碱腐蚀等优异性能且物理化学性能稳定,能够对石墨器件起到良好的保护作用,延长石墨器件的工作寿命,提高产品的质量。
4.现有的化学气相炉反应室内会发生气体湍流和紊流,化学气相沉积存在涂层表面质量差,厚度不均匀等问题。
技术实现要素:5.本实用新型要解决的技术问题是克服现有技术存在的不足,提供一种化学气相沉积炉,其反应室内气体呈现层流状态,避免气体湍流和紊流的发生,解决涂层表面质量差,涂层厚度不均匀的问题。
6.为解决上述技术问题,本实用新型采用以下技术方案:
7.一种化学气相沉积炉,包括反应室,所述反应室的两个相对的端部分别连接有与反应室内部连通的进气管和出气管,所述反应室内设有相对设置并使反应室内的气体以层流的形式流动的进气装置和出气装置,所述进气装置与进气管连接,所述出气装置与出气管连接。
8.进一步的,所述进气装置和出气装置均包括分气筒,两个所述分气筒分别与进气管和出气管连通,各所述分气筒内设有多级分气机构,所述多级分气机构与分气筒的内壁连接形成多个相连通并使分气筒内的气体逐渐扩散或汇聚的分气腔室。
9.进一步的,所述多级分气机构包括由反应室的端部向反应室的内部依次布置的一级分气板、二级分气板和三级分气板,所述一级分气板、二级分气板和三级分气板上均设有多个贯通的通气孔,所述一级分气板、二级分气板和三级分气板上的通气孔数量依次增多。
10.进一步的,所述进气管、出气管、一级分气板、二级分气板和三级分气板的轴线均与反应室的轴线重合。
11.进一步的,所述一级分气板、二级分气板和三级分气板沿反应室的轴线均匀间隔分布。
12.进一步的,所述一级分气板和三级分气板的中心均设有通气孔,所述一级分气板上以中心为圆心、直径为a的圆上均匀分布有多个通气孔,所述二级分气板上以中心为圆心、直径为b和c的圆上分别均匀分布有多个通气孔,所述三级分气板上以中心为圆心、直径为d和e的圆上分别均匀分布有多个通气孔,所述反应室的内径为f,a/2=b=c/3=d/2=e/
4=f/6。
13.进一步的,所述多级分气机构沿反应室轴线的宽度不大于反应室沿反应室轴线的宽度的五分之一。
14.进一步的,所述分气筒的内径由反应室的端部向反应室的内部逐渐变大。
15.进一步的,所述进气管与分气筒的进气口之间连通有混气室,所述混气室通过通气孔与分气腔室连通。
16.进一步的,所述混气室上以中心为圆心的圆上均匀分布有多个通气孔。
17.与现有技术相比,本实用新型的优点在于:
18.本实用新型通过进气装置和出气装置能控制反应室内气体的流动,由于进气管和出气管相对设置,与进气管连通的进气装置和出气管连通的出气装置也是相对设置,从而能对气体直接进行分气控制,使气体在反应室内的流动呈现层流状态,从而避免气体湍流和紊流的发生,进而解决了涂层表面质量差,涂层厚度不均匀的问题。
附图说明
19.图1为化学气相沉积炉的剖视结构示意图。
20.图2为进气装置的剖视结构示意图。
21.图3为一级分气板的俯视结构示意图。
22.图4为二级分气板的俯视结构示意图。
23.图5为三级分气板的俯视结构示意图。
24.图6为混气室的剖视结构示意图。
25.图7为混气室的俯视结构示意图。
26.图例说明:
27.1、反应室;2、进气管;3、出气管;4、进气装置;41、分气筒;42、多级分气机构;421、一级分气板;422、二级分气板;423、三级分气板;424、通气孔;43、分气腔室;5、出气装置;6、混气室。
具体实施方式
28.以下结合附图和具体实施例对本实用新型作进一步详细说明。
29.如图1-图7所示,本实施例的化学气相沉积炉,包括反应室1,反应室1的两个相对的端部分别连接有与反应室1内部连通的进气管2和出气管3,反应室1内设有相对设置并使反应室1内的气体以层流的形式流动的进气装置4和出气装置5,进气装置4与进气管2连接,出气装置5与出气管3连接。通过进气装置4和出气装置5能控制反应室1内气体的流动,由于进气管2和出气管3相对设置,与进气管2连通的进气装置4和与出气管3连通的出气装置5也是相对设置,从而能对气体直接进行分气控制,使气体在反应室1内的流动呈现层流状态,从而避免气体湍流和紊流的发生,进而解决了涂层表面质量差,涂层厚度不均匀的问题。
30.本实施例中,进气装置4和出气装置5均包括分气筒41,两个分气筒41分别与进气管2和出气管3连通,各分气筒41内设有多级分气机构42,多级分气机构42与分气筒41的内壁连接形成多个相连通并使分气筒41内的气体逐渐扩散或汇聚的分气腔室43。进气管2通过进气装置4的分气筒41与反应室1的端部连通,出气管3通过出气装置5的分气筒41与反应
室1的端部连通,进气装置4中的分气筒41与多级分气机构42形成的分气腔室43,能使气体从进气管2逐渐扩散至反应室1,出气装置5中的分气腔室43,能使气体从反应室1逐渐汇聚至出气管3,从而实现了气体在反应室1内的流动呈现层流状态。
31.本实施例中,多级分气机构42包括由反应室1的端部向反应室1的内部依次布置的一级分气板421、二级分气板422和三级分气板423,一级分气板421、二级分气板422和三级分气板423上均设有多个贯通的通气孔424,一级分气板421、二级分气板422和三级分气板423上的通气孔424数量依次增多。通过设置一级分气板421、二级分气板422和三级分气板423及其数量依次增多的通气孔424,从而实现了进气装置4中的分气腔室43内的气体能从进气管2逐级扩散至反应室1,以及出气装置5中的分气腔室43内的气体从反应室1逐级汇聚至出气管3,进而实现了气体在反应室1内的流动呈现层流状态。一级分气板421、二级分气板422和三级分气板423均为c/c复合材料,板材厚度为3mm,c/c复合材料具有耐高温,变形量小的优点,且在厚度较薄时依然具有较高强度,能够保证各级分气板具有较长的使用寿命。
32.本实施例中,进气管2、出气管3、一级分气板421、二级分气板422和三级分气板423的轴线均与反应室1的轴线重合。各部件轴线重合,便于加工制作,也便于气体的流动。
33.本实施例中,一级分气板421、二级分气板422和三级分气板423沿反应室1的轴线均匀间隔分布。一级分气板421、二级分气板422和三级分气板423之间的间距一致,能使气体的流动有足够的空间。
34.本实施例中,一级分气板421和三级分气板423的中心均设有通气孔424,一级分气板421上以中心为圆心、直径为a的圆上均匀分布有多个通气孔424,二级分气板422上以中心为圆心、直径为b和c的圆上分别均匀分布有多个通气孔424,三级分气板423上以中心为圆心、直径为d和e的圆上分别均匀分布有多个通气孔424,反应室1的内径为f,a/2=b=c/3=d/2=e/4=f/6。一级分气板421上以中心为圆心、直径为a的圆上均匀分布有8个通气孔424,二级分气板422上以中心为圆心、直径为b的圆上分别均匀分布有6个通气孔424,直径为c的圆上分别均匀分布有12个通气孔424,三级分气板423上以中心为圆心、直径为d的圆上分别均匀分布有8个通气孔424,直径为e的圆上分别均匀分布有16个通气孔424。通气孔424和通气孔424的直径大小一致、且直径为8-12mm。各级分气板上的多个特定位置上的通气孔424,能实现气体在反应室1内的流动呈现层流状态。
35.本实施例中,多级分气机构42沿反应室1轴线的宽度不大于反应室1沿反应室1轴线的宽度的五分之一。能够保证反应室1内气体流动的空间得到更加合理的利用。
36.本实施例中,分气筒41的内径由反应室1的端部向反应室1的内部逐渐变大。分气筒41为大开口朝向反应室1内部的喇叭,从而更利于气体的逐渐扩散或汇聚。
37.本实施例中,进气管2与分气筒41的进气口之间连通有混气室6,混气室6通过通气孔424与分气腔室43连通。混气室6的顶部设有盖体,进气管2插装在盖体的中心。
38.本实施例中,混气室6上以中心为圆心的圆上均匀分布有多个通气孔424。混气室6能使进入的各种气体进一步混合,混气室6的底面上以中心为圆心、直径为b的圆上均匀布置4个圆形的通气孔424。
39.本实施例中,进气装置4中的一级分气板421、二级分气板422和三级分气板423均通过螺栓固定在分气筒41上,出气装置5中的一级分气板421、二级分气板422和三级分气板
423水平放置在分气筒41中,以便于尾气残渣的清理。
40.以上所述仅是本实用新型的优选实施方式,本实用新型的保护范围并不仅局限于上述实施例。对于本技术领域的技术人员来说,在不脱离本实用新型技术构思前提下所得到的改进和变换也应视为本实用新型的保护范围。