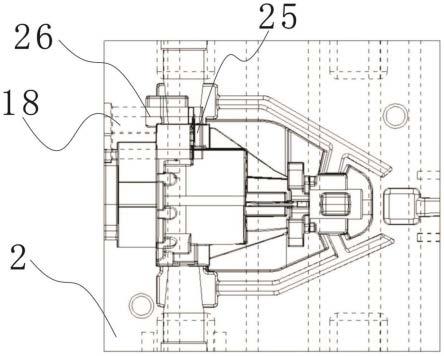
1.本实用新型属于铸造领域,具体涉及一种前桥主减速器壳体铸造模具。
背景技术:2.主减速器壳体是驱动桥的重要部件之一。主减速器壳体装配于汽车前桥。
3.前桥主减速器壳体为大型薄壁铸件(如图3、4),其前端有前端管口a,后部有两对称的轴承孔b,靠近一轴承孔处的前桥主减速器壳体有一向外凸出的悬置臂c,悬置臂端部悬置孔,悬置臂前后侧面有内凹结构c1,结构复杂。因悬置臂结构、位置特殊,目前,前桥主减速器壳体采用分体式铸件,悬置臂单独铸造后再与前桥主减速器壳体的主体结构焊接。
4.加工步骤多,焊接处焊接质量的高低也会影响产品的品质。
技术实现要素:5.本实用新型的目的是克服现有技术的上述不足,而提供一种前桥主减速器壳体铸造模具,不采用焊接加工,通过模具成型一体式结构的前桥主减速器壳体,保证产品品质的稳定。
6.本实用新型的技术方案是:
7.一种前桥主减速器壳体铸造模具,包括由上模、下模组成的模具本体,装于模具本体上两用于成型两轴承孔的圆柱侧抽芯,置于模具本体内的用于成型前桥主减速器壳体内壁的砂芯;下模上设有用于成型悬置臂的活动模组,活动模组包括侧抽块和活块一,活块一与侧抽块相对设置,下模上还设有用于让位悬置臂脱模的活块二。
8.下模侧面有与侧抽块相配合安装的抽块孔,活块二置于悬置臂c上方,下模上有与活块二配合的安装凹部。
9.侧抽块外端经支撑杆连接震击锤。
10.侧抽块前端外形有用于成型悬置臂后侧面内凹结构的成型面,活块二上有用于成型悬置臂前侧面内凹结构的成型面。
11.一轴承孔内端面的凸台侧壁d对应处的砂芯表面设有冷铁一,另一轴承孔内端面的凸台侧壁对应处的砂芯表面设有冷铁四,前端管口内壁e对应处的砂芯表面设有冷铁三、冷铁二。冷铁二、冷铁三两块冷铁对扣,成为一个半圆形,粘接在砂芯上,由于冷铁的激冷作用,铸件内腔管壁的厚大部位在凝固过程中,较快冷却,从而保证该部位的内部组织密度。另两块冷铁安放于两侧轴承孔的砂芯表面,同样地,对该部位的铝水凝固起到加速作用,保证该部位不出现疏松、缩孔等质量问题。
12.所述模具还包括顶料机构;所述顶料机构包括顶料板、与顶料板连接的顶料固定板、顶料杆,复位杆和顶料杆一起都安装固定在顶料板和顶料固定板之间,顶料板和顶料固定板压着复位杆和顶料杆的端头,不让其前后窜动;顶料杆的长度与模具型腔内不同形状的表面平齐,各根顶料杆的长度不一致,各复位杆前端面和模具的分型面平齐,各复位杆长度相同。
13.所述模具还包括浇注系统,排气杆;所述浇注系统包括浇口杯、浇道、冒口,浇口杯设置于位置模具侧面,安装在下模上,浇口补贴安装于上模浇口部位顶面,其前侧面与浇口杯斜面部位紧密贴合,冒口对应于主减速器壳体的前端管口部位及两侧的轴承孔部位。
14.本实用新型通过合理的模具设计,避免了焊接悬置臂,使得前桥主减速器壳体铸件为成型一体式结构。
15.发明人经过研究发现主减速器壳体三个口处因壁厚较壳体其他部位厚,主减速器壳体铸件在凝固过程中,对于厚壁处组织致密度不够,易产生缩松缺陷,成品率低。本实用新型通过在主减速器壳体铸件的三个口处对应砂芯表面采用粘芯胶粘接冷铁,冷铁比砂芯冷却的快,冷铁加快主减速器壳体铸件局部冷却速度,提高主减速器壳体铸件致密度,从而降低产品的缩松缺陷。
附图说明
16.图1是本实用新型的铸造模具的结构示意图;
17.图2是图1的俯视图;
18.图3是主减速器壳体的结构示意图之一;
19.图4是主减速器壳体的结构示意图之二;
20.图5是下模的主视图;
21.图6是下模的仰视图;
22.图7是下模的侧视图;
23.图8是侧抽块的结构示意图;
24.图9是图8的侧视图;
25.图10是活块二的结构示意图;
26.图11是活动二的俯视图;
27.图12是活块一的结构示意图;
28.图13是活块二的侧视图。
具体实施方式
29.本实用新型的前桥主减速器壳体铸造方法,包括以下步骤:
30.a模具合模
31.如图1-13中,模具包括由上模3、下模2组成的模具本体,置于模具本体内的用于成型前桥主减速器壳体内壁的砂芯,顶料机构,浇注系统,排气杆7;
32.下模2上设有用于成型悬置臂的活动模组,所述活动模组包括侧抽块18、与侧抽块18相配合的活块一25,置于下模2上用于让位悬置臂脱模的活块二26;
33.一轴承孔内端面的凸台侧壁d对应处的砂芯表面设有冷铁一27,对应另一轴承孔内端面的凸台侧壁处的砂芯表面设有冷铁四30,前端管口内壁e对应处的砂芯表面设有冷铁三29、冷铁二28;冷铁三29、冷铁二28两块冷铁对扣,成为一个半圆形,粘接在砂芯上,由于冷铁的激冷作用,铸件内腔管壁的厚大部位在凝固过程中,较快冷却,从而保证该部位的内部组织密度。另两块冷铁安放于两侧轴承孔的砂芯表面,同样地,对该部位的铝水凝固起到加速作用,保证该部位不出现疏松、缩孔等质量问题。
34.顶料机构包括顶料板9、与顶料板9连接的顶料固定板10、顶料杆15,复位杆14和顶料杆15一起都安装固定在顶料板和顶料固定板之间,顶料板9和顶料固定板10压着复位杆14和顶料杆15的端头,不让其前后窜动;顶料杆15的长度与模具型腔内不同形状的表面平齐,各根顶料杆15的长度不一致,各复位杆14前端面和模具的分型面平齐,各复位杆14长度相同;复位杆14起作用就是把顶料板顶回去;复位杆14将模具的顶料板及顶料固定板顶回,固定于顶料板上的顶料杆前段与模具型腔高度平齐。
35.模具还包括两用于成型两轴承孔的圆柱侧抽芯17;下模2侧面有与侧抽块18相配合的抽块孔,侧抽块18外端经支撑杆20连接震击锤19;侧抽块18前端外形有用于成型悬置臂后侧面内凹结构的成型面,活块一25上有用于成型悬置臂前侧面内凹结构的成型面,侧抽块18、活块二26、活块一25的设计使铸件顺利从侧面脱出模腔。活块二26的弧形面261与圆柱侧抽芯17配合。
36.浇注系统包括浇口杯1、浇道、冒口,浇口杯1设置于位置模具侧面,安装在下模上,浇口补贴4作用是防止浇注时铝水瞬时流量过大,从上模顶面溢出,浇口补贴4安装于上模浇口部位顶面,其前侧面与浇口杯斜面部位紧密贴合,冒口对应于主减速器壳体的前端管口部位及两侧的轴承孔部位,给该部位的厚大热节提供了充足的铝水补缩来源。上模3经上模连接杆5与上模连接板6连接。顶料机构还包括导向组件,导向组件包括导向杆12、导向套13,导向杆12插装于导向套内,导向套固定于安装孔中,顶料板9上有上安装孔,顶料固定板10上有下安装孔,上下安装孔形成一安整的安装孔,上安装孔的上安装孔下端面有与导向套中部法兰部相配合的凹部。排气杆7下端与上模3上的排气杆孔相配合,置于顶料板9上端的排气杆7头部有提拉孔,顶料板9、顶料固定板10上有与排气杆7配合的让位孔。
37.b上模合于下模上之后,把复位杆14压下,复位杆14前端面与分型面平齐,固定于顶料板上的顶料杆前段与模具型腔高度平齐;
38.c浇注成型铸件;
39.d上下模开模,铸件出模时,顶料杆15、复位杆14被顶起;
40.e铸件出模后,重复步骤a-d进行下一铸件铸造。
41.制芯方法为:
42.芯盒加热:接好各电热管电源接线,接通电源,对模具加热,模具温度: 静模200
°
c-240
°
c,动模:210
°
c-250
°
c,且动模温度高于静模温度10℃以上;用手动制芯二至三次,待动作无误且制出砂芯合格后,采用kw957壳芯机使用半自动或全自动制芯,在型腔表面喷上脱模剂,调节射砂压力,射砂时间及加热时间,射砂压力:0.4-0.6mpa,射砂时间:4-7s,结壳时间:1.5-2min,加热时间5-6min;用锯条将砂芯分型批缝锉平,将顶杆痕迹及凹陷部位抹平,用粘芯胶将冷铁在砂芯上粘接好;
43.浇注方法为:
44.预热模具,使之表面达到150-250
°
c;喷涂料,先喷底料,再喷面料,底料厚度控制在0.1mm,面料层厚度约为0.05-0.1mm左右,浇冒口处应喷保温涂料,厚度在1.5-2mm左右;继续将模具预热到250-450
°
c,使之达到浇注需要;
45.浇注:刮去分型面上的涂料,将模具吹净,启动开模机,将模具合平;将砂芯准确放入下模型腔内;舀取适量铝液,稳流快速连续浇注,浇注时间8-12s,浇注的浇注铝液温度:700-720℃,自检,将表面缺陷严重的铸件标记;
46.铸件出模后的加工步骤为:
47.a对用冲床冲掉直浇道及横浇道;
48.b去冒口:将铸件放在带锯机上,定位铸件,启动锯床,锯掉浇冒口,残余高度不超过3-5mm;
49.c清砂:用铁锤去掉披缝,用榔头敲击铸件厚实部位及加工表面,用震动清砂机震掉芯砂及活块;
50.d去毛刺:用錾子去除铸件内外表面的飞边、毛刺、凸瘤,用风铲或打磨机将批缝、凸瘤铲除、修磨平整,非加工面分型毛刺高度要求在1mm以内,加工面分型毛刺高度要求不超过3mm;
51.e热处理:铸件采用t6热处理,t6热处理分为两个阶段即时效处理和固溶处理;
52.f抛丸:将铸件放入滚筒抛丸机内,每次放不超地5件,抛丸时间5-10分钟;内外表面外观一致;检查产品内外表面是否有孔洞,有孔洞的做好标记,铲开、焊补并抛丸;作用是抛丸的作用和功能就较多:不但除锈,除表面氧化皮,还提高表面粗糙度,去除零件机加工毛刺,消除零件内应力,减少热处理后零件变形,提高零件表面耐磨,受压能力等。
53.g机械性能检验:硬度≥80hbs,抗拉强度≥270mpa,延伸率≥7%;
54.h铸件检验:检查铸件表面是否有气孔、冷隔、裂纹穿透性的缺陷存在,非加工面直径小于2mm的气孔,进行修补处理待加工面能加工掉的缺陷允许残留;铸件非加工面的分型痕迹凸起或凹下深度不得超过1mm。
55.铝合金熔炼的步骤主要如下:
56.①
装料。在预热后的坩埚中装入预制合金锭、优质回炉料,再加中fol合金,较后加合金元素。
57.②
温度控制。严格控制铝合金熔炼的温度,只有合适的温度才能获得高质量的合金液,避免过热。若温度过高,会加大合金中各种元素的氧化烧损,引起合金中化学成分的变化。温度过低,会使合金的化学成分不均匀,合金中的氧化夹杂物、气体等不易排出,合金的理化性能下降,影响铸造性能。
58.③
时间控制。严格控制熔炼时间,操作要迅速,减少合金吸气和氧化夹杂,增加合金元素的烧损,影响合金化学成分。
59.④
精炼操作。铝合金精炼的主要目的是清除熔液内的气体和非金属夹杂物、均匀合金成分。精炼是熔炼中极为重要的一个工艺过程。应正确选用精炼剂、控制好加入量份般加入合金质量的0.5%-0.7%及把握好精炼温度,精炼温度一般控制在700-7200c。在精炼的过程中,用钟罩将精炼剂分批压入熔液面下约2/3处,均匀缓慢做顺时针转动,速度要缓、动作要平稳,避免金属液大幅度搅动,以防增加氢含量和卷入夹杂。
60.⑤
变质处理。
61.合金变质的目的是细化晶粒,提高铸件性能。变质剂应先预热,控制要点是:
①
变质温度,一般不超过7400c;
②
变质时间,一般为10min ;
③
变质剂的加入量,使用双色变质剂的用量一般为合金液质量的1.0%-1.2%;
④
操作方法要到位。合金精炼后要尽快浇注完毕,砂型铸造一般应控制在40min内,金属型铸造应控制在2h内,否则,要重新进行精炼、变质,再次精炼时加入的精炼剂为合金质量的0.2%左右。
62.装炉熔炼成浇注铝液的具体方法为:
63.将回炉料砸成小块装入炉底,再将部分新料中的铝锭、结晶硅混合排于炉中,炉料要大小块掺杂,力求提高致密度,排满工频炉为止。
64.送电熔化,注意随化随添新炉料,直至全部炉料(钛添加剂、镁、锑除外)加完为止;待全部炉料熔化后,升温至730℃断电,先加钛添加剂、锑后再加镁,用钟罩压入炉中心并轻轻移动,使镁向四周扩散。
65.送电升温,利用磁力搅拌使ti、sb元素均匀化,待熔炼温度升致730-760℃时断电;
66.取光谱分析试块进行光谱分析,并根据分析结果调整化学成分至合格;
67.待成分合格后送电升温至760~770℃,断电将铝液转入保温炉,30分钟内转完。转运前转包温度预热至400~450℃,保温坩埚炉预先升温至730-750℃。
68.精炼及变质处理
69.向在保温炉中的铝液表面撒入适量的铝打渣剂,用扒渣工具对浮渣“炒”式搓揉,待渣铝明显分离时,捞净液面浮渣。将铝水调温至720~740℃,将铝液新料重量0.8-1%的锶盐变质剂洒向液面。
70.将精炼机氩气瓶开关打开,调节流量表使其读数为5-10l,用行车将精炼转子头放入保温炉,深度不低于炉体深度一半,根据空气湿度设置精炼机的精炼时间(湿度<50%时,精炼时间设定为5分钟;50%≤湿度≤75%时,设定为6分钟;湿度>75%时,设定为8分钟)。
71.启动精炼机精炼,精炼结束后,用扒渣工具对锶盐变质剂“炒”式搓揉后打渣,用扒渣瓢捞净液面浮渣。
72.精炼及变质处理后,应立即取样检查铝液的精炼效果(测氢含量),测氢结果要求,试块密度达到2.59g/cm3以上的为合格,否则需重新精炼除气,直到符合要求。同时应进行断口检查;浇注试棒试块1组/1炉;试样的浇注温度720~740℃;每炉铝水取3个试块,并依次在合金熔化后、合金变质后及浇注中期各取一块;试棒取3根,在变质完15分钟后进行。并在试棒试块上按要求做好清晰的标识(日期、炉次号、代号)。
73.变质至浇注完毕时间不得超过3小时,防止变质失效,否则,需要重新进行精炼变质,并补充一定量的镁,镁的补充量应占剩余铝水重量的0.04~0.05%。
74.t6热处理中时效处理:(设备:铝合金时效炉)
75.时效处理是将固溶处理后的铝合金铸件加热到某一温度,保温一定时间后出炉,在空气中缓慢冷却到室温的工艺称为时效。如果时效强化是在室温下进行的称为自然时效,如果时效强化是在高于室温并保温一段时间后进行称为人工时效。时效处理进行着过饱和固溶体分解的自发过程,从而使合金基体的点阵恢复到比较稳定的状态。
76.时效温度和时间的选择取决于对合金性能的要求、合金的特性、固溶体的过饱和程度以及铸造方法等。人工时效可分为三类:不完全人工时效,完全人工时效和过时效。不完全人工时效是采用比较低的时效温度或较短的保温时间,获得优良的综合力学性能,即获得比较高的强度,良好的塑性和韧性,但耐腐蚀性能可能比较低。完全人工时效是采用较高的时效温度和较长的保温时间,获得最大的硬度和最高的抗拉强度,但伸长率较低。过时效是在更高的温度下进行,这时合金保持较高的强度,同时塑性有所提高,主要是为了得到好的抗应力腐蚀性能。为了得到稳定的组织和几何尺寸,时效应该在更高的温度下进行。过时效根据使用要求通常也分为稳定化处理和软化处理。
77.固溶处理:(设备:铝合金固溶淬火炉)
78.固溶处理是把铸件加热到尽可能高的温度,接近于共晶体的熔点,温度越高,强化元素溶解速度越快,强化效果越好。一般加热温度的上限低于合金开始过烧温度,下限应使强化组元尽可能多地溶入固溶体中。在该温度下保持足够长的时间,使强化组元最大限度的溶解,这种高温状态被固定保存到室温,保温时间是由强化元素的溶解速度来决定,这取决于合金的种类、成分、组织、铸造方法和铸件的形状及壁厚。
79.淬火时快速冷却,给予铸件的冷却速度越大,使固溶体自高温状态保存下来的过饱溫度也越高,从而使铸件获得高的力学性能,但同时所形成的内应力也越大,使铸件变形的可能性也越大,所以对冷却介质温度关系很大。该过程称为固溶处理。固溶处理可以提高铸件的强度和塑性,改善合金的耐腐蚀性能。固溶热处理的淬火转移时间应尽可能地短,一般应不大于15s,以免合金元素的扩散析出而降低合金的性能。