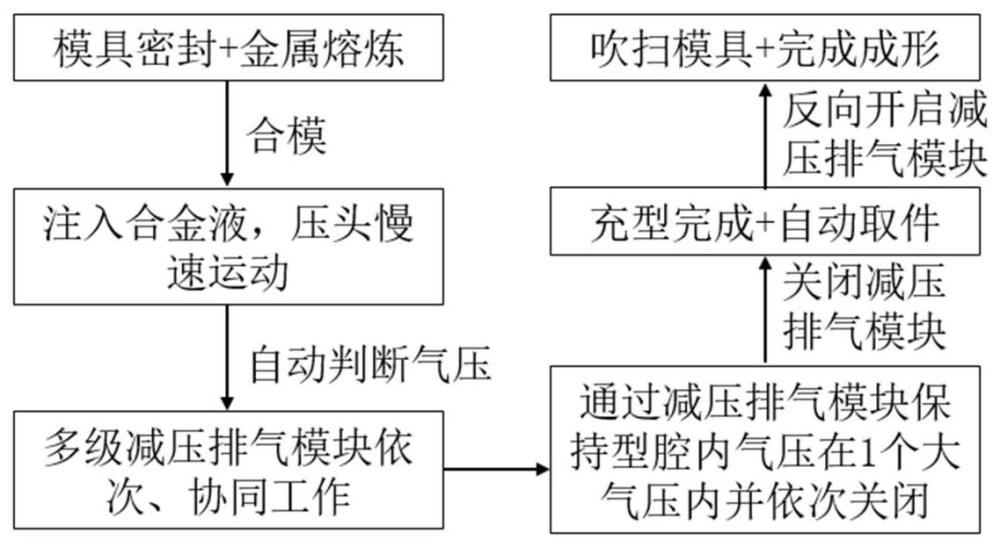
本发明属于合金材料加工,具体涉及一种减压铸造成形装置以及减压铸造方法。
背景技术:
1、进入21世纪,随着通讯、汽车、航空航天等领域高速发展,压力铸造作为一种近净成型技术,由于其极高的生产效率、较低的生产成本以及所生产铸件优秀的表面质量和尺寸稳定性而得到了广泛的应用。
2、高压压铸的两大特点即为高压和高速充型,常用的喷射压力从几千到几万kpa,甚至高达2×105kpa,其充填速度约为10-50m/s,有时甚至可达100m/s以上,且充填时间很短,一般在0.01~0.2s范围内。
3、普通的压铸件往往因为金属液在高速高压下完成充型、凝固,在压铸机的高速高压压射下,一方面,合金液强行填充模具型腔,导致模具型腔内的空气无法及时排出,从而瞬间产生巨大的压力,严重阻碍了压铸充型的过程;另一方面,模具内的气体在熔体的强力压缩下来不及排放,以致使铸件内部形成气孔,零件力学性能差,高压铸造零件延伸率一般不超过3%。
4、为了解决上述问题,半固态压铸技术、真空压铸技术应运而生,但采用半固态压铸技术的设备结构复杂、安装所需空间大、操作不方便,难以连续生产大尺寸薄壁长距离充型金属铸坯,且高速充型时模具型腔内的空气仍然无法及时排出,导致排气效果有所变差,金属铸坯质量有所下降。
5、而采用真空压铸技术在填充过程中主动抽离出模具型腔中的气体,有效减少零件在冷却过程中所产生的溶解气体和气泡,还可减少型腔的反压力,可使用较低的比压,有可能用小机器压铸较大的铸件,但真空压铸法目前制约于多个生产条件,例如需要使用大功率的真空泵设备来维持较好的真空度,在模具结构相对复杂的情况下,也需要进行长时间的排空或者多次排空的方式来进一步提高真空度(一般要达到50mbar)。
6、不论采用半固态压铸技术,还是采用真空压铸技术所使用的设备要求都较高,且生产效率降低,而高压压铸的压铸件内部有气孔,零件力学性能差。故急需要一种能够快速高效地释放型腔内压力的压铸成形方法,来减小模具型腔里形成阻碍充型的压力,从而使压铸过程实现无阻力充型。
7、为了解决这个问题,本技术提出一种减压铸造成形装置以及减压铸造方法,既能实现铸件形状完整、组织致密,还可进行热处理,进一步增加铸件的力学性能
技术实现思路
1、发明目的:提供一种减压铸造成形装置以及减压铸造方法,解决了现有技术存在的上述问题。
2、技术方案:一种减压铸造成形装置,包括挤压组件,所述挤压组件内形成一端敞口的压室,所述挤压组件的挤压端设有进料口,通过进料口往压室内填充金属液,所述挤压组件端部垂直连接有成型组件,所述成型组件内形成一端敞口的型腔,所述型腔的敞口端与压室的敞口端连通,所述成型组件的一侧壁安装有减压组件,所述减压组件操作性连通型腔,所述减压组件远离型腔的端部连接储气罐,所述减压组件通讯连接有控制器,所述控制器用于控制减压组件对型腔进行充气或排气。
3、优选的,还包括若干顶出件,所述顶出件滑动安装在所述成型组件的侧壁且与所述减压组件位于同侧,所述顶出件用于将型腔内的铸造完成的工件顶出脱离型腔。
4、优选的,所述挤压组件包括收容壳体,所述收容壳体为两端敞口的中空结构,所述收容壳体其中一敞口端安装有压杆,压杆的端部连接有压头,所述压头与压杆形成联动部件,所述收容壳体与联动部件配合形成压室,所述进料口开设在所述收容壳体的侧壁,所述进料口靠近所述联动部,通过进料口向中空结构内填充金属液,并在收容壳体的中空结构对联动部件的收容,完成压室的大小变化,将金属液挤压至型腔内。
5、优选的,所述成型组件包括定模和动模,所述顶出件由下至上线性阵列安装在动模上,所述动模向定模移动形成密封合模,所述动模远离所述定模形成开模,当形成合模时,所述定模与所述动模对立设置且其端部分别与挤压组件的端部垂直连接,所述定模与所述动模之间预留有间隙形成型腔,型腔的下端与压室连通,型腔的上端通过减压组件的局部对其封堵形成密封,用于金属液进入形成铸件,当铸件完成后,定模和动模远离形成分模,通过对顶出件施加外力,所述顶出件将动模内的铸件顶出。
6、优选的,所述成型组件还包括镶块,所述镶块安装在所述定模的侧壁,当所述定模与所述动模形成合模时,所述镶块位于所述定模与所述动模之间。
7、优选的,所述减压组件包括第一减压块、第二减压块和第三减压块,所述第一减压块、第二减压块由下至上嵌入动模内,所述第三减压块设于定模与动模的顶部,所述第三减压块与型腔接触的端面为w型结构,所述第一减压块、第二减压块和第三减压块均连通有气管,气管相互连通后形成一个进出口与储气罐连通,靠近第一减压块、第二减压块和第三减压块的气管端部均安装有电磁阀门,所述电磁阀门均与所述控制器控制连接,所述第一减压块、第二减压块和第三减压块连接的气管上分别安装有示压器,所述示压器分别与控制器通讯连接。
8、一种减压铸造成形装置的减压铸造方法,包括以下步骤:
9、s1、对定模和动模进行预热,在定模和动模完成预热后,动模向定模移动形成密封合模,通过将预定温度的金属液注入压室内;
10、s2、在预定温度下,对金属进行熔炼,熔炼完成后得到金属液,通过进料口向压室内注入金属液,当完成金属液注入完成后,挤压组件中的压头依据金属液与型腔之间的位置关系,分级压射速度对金属液挤压,将金属液挤压至型腔内;
11、s3、当对金属液进行挤压初期,通过减压组件获取型腔内的初始压力,当初始压力为1个大气压时,挤压组件以预定速度将金属液向型腔内推动,并在推动过程中,通过控制器与减压组件的相互配合下,对型腔内的压力进行实时获取,在对金属液推动的过程中,型腔内的压力超过1个大气压时,通过控制器对减压组件进行控制,对型腔内的压力进行分级排气释放,使型腔内的压力始终保持在1个大气压,直至将金属液完全推入型腔充型完成后,控制器控制减压组件完全闭合;
12、s4、当步骤s3完成铸件的充型后,对成型组件进行开模处理,并配合顶出件将铸件顶出,配合机械手将铸件移动至指定位置;
13、s5、在步骤s4中,完成铸件的移出后,在控制器的控制下,储气罐配合减压组件对型腔、压室进行吹扫处理,使型腔和压室保持洁净;
14、s6、重复步骤s1至s5所有步骤,直至完成预定铸件数量。
15、优选的,步骤s2压头分速对金属液挤压的具体过程为:
16、s21、当金属液全部位于压室内时,压头以第一级压射速度运动,对压室内的金属液进行挤压,使金属液向型腔内移动;
17、s22、当金属液部分填入型腔内完成铸件横浇道的填充后,压头以第二级压射速度运动,对金属液进行挤压,直至金属液全部充入型腔内,压头暂停移动,并在压头的封堵下,使金属液停留在型腔内;
18、优选的,步骤s3中的分级排气释放的具体过程为:
19、s31、当金属液进行初次挤压时,此时金属液的液位处于减压组件与压室之间,通过减压组件获取型腔内的压力,当型腔内的压力大于1个大气压时,减压组件中靠近压室的电磁阀门在控制器的控制下打开排气,当型腔内的压力小于等于1个大气压时,减压组件中的所有电磁阀门均处于闭合状态,压头将金属液挤压,使金属液向型腔内移动;
20、s32、在金属液向型腔内移动时,型腔内的压力增大,当型腔内的压力大于1个大气压时,获取金属液的液位;
21、当金属液的液位低于减压组件的第一减压块时,则此时控制器控制位于第一减压块气管端部的电磁阀门打开排气;
22、当金属液的位于处于第一减压块和第二减压块之间时,此时控制器控制位于第一减压块气管端的电磁阀门关闭,位于第二减压块气管端的电磁阀门打开排气,直至型腔内的压力小于等于1个大气压时,控制器控制电磁阀门关闭;
23、当金属液的液位于处于第二减压块和第三减压块之间时,此时控制器控制位于第一减压块、第二减压块气管端的电磁阀门均关闭,位于第三减压块气管端的电磁阀门打开排气,直至金属液对型腔充型完成后,控制器控制电磁阀门关闭,此时金属液与第三减压块(11)面接触或压射至第三减压块(11)的w型结构内;
24、有益效果:本发明涉及一种减压铸造成形装置以及减压铸造方法,在动模中嵌入三组减压块,并通过气管插入每组减压块内,配合电磁阀门、示压器和控制器对型腔内的压力进行调节,与现有高真空压铸工艺相比省去了繁杂的预先抽取真空的时间,显著降低了能耗,且同时具有短流程、低成本、工艺简单的特点,与常压铸造工艺相比,铸件内部气孔少,铸件密度增大,力学效果提升;
25、其次,在金属液进入型腔内时,在减压组件和控制器的相互配合下,将型腔内的被压缩气体及时排出,控制型腔内的大气压始终保持在1个大气压的环境下,实现了无阻力平稳充型,减少铸件内部的气孔,进而获得形状完整、组织致密的组件。