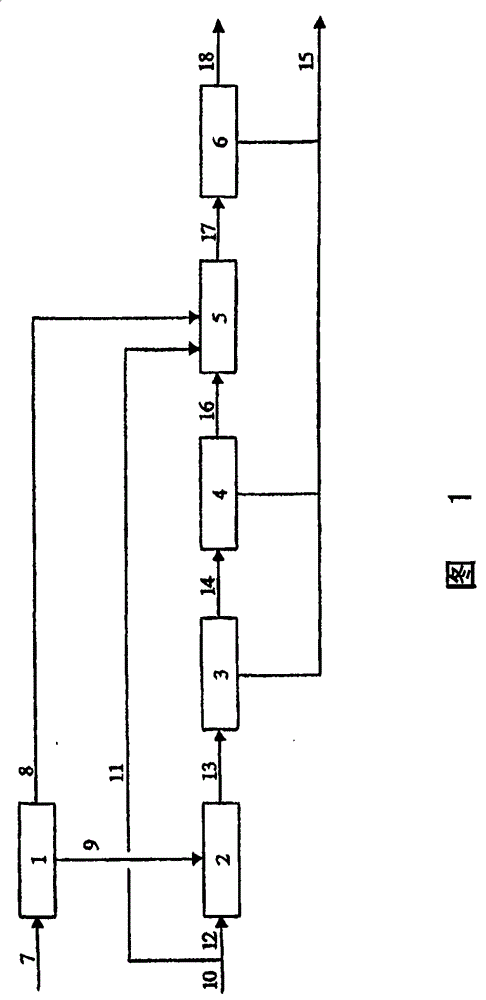
含尿素和硫酸铵的肥料生产方法本发明涉及含尿素和硫酸铵(AS)的肥料生产方法。采用管式反应器(PR)技术在尿素溶液中直接合成AS。
背景技术:尿素是最常用的含氮肥料,其全球消耗量已从七十年代早期的约2千万吨显著增长到二十一世纪初期的约1亿吨。氮是任何活体系(蛋白质)的基础组分。由于集约农作和由工业向空气中排放并随后通过雨水供应到土地的硫的减少,现代农业除了需要氮之外,还需要硫。良好的农业实践通常需要N和S之比为10/1至5/1,以符合作物需求,例如150kgN/公顷/年的N和30kgS/公顷/年。硫的缺乏导致作物数量较低且质量较低,并且缺乏硫通常在蛋白质含量和类型中得以体现。硫的确是进入生物细胞化学过程的主要元素,以例如氨基酸(胱氨酸、蛋氨酸等)的分子形式。其也是光合成的催化剂,在一些情况下,可改进大气氮的固定。硫酸根离子对于植物而言是容易获得的,而元素硫首先必须由土地细菌氧化。出于所有这些原因,看来通过混合尿素和硫酸铵获得的尿素硫酸铵(UAS)是非常令人关注的化合物肥料,其同时一方面包括氮,另一方面包括作物易得的硫酸盐形式的硫。可额外加入一些百分比的元素硫,以具有一些在整个农业季节中硫缓释的效果。AS可在固化(造粒、颗粒化......)之前作为细磨晶体被加入尿素溶液,或可在尿素溶液中或者在本专利所述的循环流内直接合成。硫可以熔融盐形式加入到尿素溶液中或者在造粒机中与UAS共同喷雾。商品等级的UAS应有利地含有5%-15%的硫和31-40%的氮,这代表2∶3至4∶1的尿素和硫酸铵之比。可以根据作物需求或市场需要以此方式定制该N/S比。尿素合成工艺的说明所有的尿素商业生产均来自二氧化碳和氨。反应以两步进行,第一步为氨基甲酸盐的形成,第二步为氨基甲酸盐脱水成为尿素和水。尿素是由作为原料的CO2和NH3合成的。由于操作条件(温度和压力),CO2和NH3容易结合成为氨基甲酸盐,同时脱水得到尿素和水。反应为两步:2HN3+CO2NH2COONH4[氨基甲酸盐]CO(NH2)2[尿素]+H2O两个反应均发生在液相中,而原料氨和二氧化碳处于气相。该反应并非完全的,而是达到平衡。由此,以超过化学计量比引入氨,以增加转化为尿素的收率。在典型尿素生产方法(例如,Stamicarbon,记载于例如“fertilizermanual”,第IX章,IFDC在1998年的印刷版)中获得的每道次(perpass)的转化收率是约80%的尿素,其可能被潜在地合成(即,全部CO2转化为尿素,过量氨剩余下来)。原料的转化并非在一个道次中完成,因此该工艺可以是:一次通过工艺,部分循环工艺,全部循环工艺。一次通过和部分循环工艺指未转化的原料在另一生产中被采用,例如氨将用于共同生产硫酸铵或硝酸铵。在该情况中,二氧化碳,其不过是氨合成的低价值副产物,通常被排放到大气。在一次通过工艺(例如MitsuiToastu)中,将原料泵送到约200℃和200巴的尿素反应器。反应器中的过量尿素可以是100-110%和N/C比是约3.5。约35%的氨被转化为尿素。未反应的氨在高压下被分离且循环。在汽提氨基甲酸盐之后,反应器流出物含有约80%尿素溶液。在一些其它工艺中必须使用大量氨(如“fertilizermanual”,第IX章,IFDC在1998年的印刷版中所述)。任何共同-生产均意味着灵活性较少,所以大多数新设施都是基于全部循环工艺;所有未转化的原料被循环到尿素反应器。这些工艺的基本原理如下:首先,尿素在高压(通常130-220巴)高温(通常150-210℃)反应器中合成,允许原料转化成氨基甲酸盐和尿素,其次,来自反应器的流随后被送到压力降低和氨基甲酸盐分解的连续阶段。因此氨和二氧化碳与一些水从溶液中汽提出,溶液中的过量物主要是尿素和水,第三,该尿素溶液可以进一步结晶或浓缩,直到获得充分的浓度用于最后工艺(颗粒化或造粒)。随后,尿素-未转化的反应物由于前述压力降低、闪蒸(flash)和汽提而被循环。随后这些气流冷凝为氨基甲酸盐溶液且泵送回尿素合成反应器。例如在Stamicarbon尿素合成工艺中(全部循环工艺),CO2和NH3在约140巴的压力和180-185℃的温度经由氨基甲酸铵转化为尿素。在反应器中的NH3/CO2摩尔比约3。这导致60%的CO2转化率和41%的NH3转化率。采用CO2作为汽提剂在反应器压力汽提含有未转化NH3和CO2的反应器流出物。热效应和汽提效应导致大约85%的残余氨基甲酸盐发生分解,且约80%的二氧化碳转化成在从汽提器排出的液流中的尿素。汽提器流出物中过量NH3和CO2在4巴的分解阶段中蒸发且随后冷凝形成氨基甲酸盐溶液,其被循环到合成区。在蒸发区产生尿素溶液的进一步浓缩,在此例如96%熔体得以产生以在造粒机中喷雾或者颗粒化。取决于工艺条件(压力和温度),未转化的氨可以是氨基甲酸盐、碳酸盐(NH3和CO2的不同组合)或氨的形式。此后所用的氨基甲酸盐含义应理解为尿素中未转化的原料,并不对应于特定化学化合物而是对应于产物族,其包括碳酸铵、氨基甲酸盐、倍半碳酸盐等,具体取决于摩尔比、温度和压力。在一些其它工艺(Snamprogetti,MitsuiToatsu)中,在反应器中运行更高的N/C比,约3.5。高压分离且循环过剩的氨。在这些工艺中,对纯且无水的过量氨进行冷凝和循环以避免水循环。在这些工艺中,氨的冷凝容量限制了尿素反应器收率增加。原位UAS生产该未转化的氨可由硫酸中和以产生UAS。由于两个氨分子和一个硫酸分子的结合产生AS合成反应。AS和水均由该反应产生。然而反应热可用作蒸发水的能源,用于浓缩所得尿素硫酸铵(UAS)溶液。AS合成反应为显著放热反应。为了由尿素水溶液生产UAS,已经确定且需要两个主要的技术步骤:尿素中的AS合成和UAS溶液浓缩。一方面,AS合成由硫酸和氨(游离的或者作为氨基甲酸盐结合的)之间的反应进行。另一方面,UAS溶液由于反应器中合成反应期间释放的反应热和通过蒸发器(若需要的话)进行浓缩。成功且经济的AS合成反应与UAS生产同操作条件和工艺设计密切相关。本发明考虑了新工艺(3条途径)来生产UAS。该工艺将在下文描述。本发明涉及基于管式反应器技术的互补单元操作,借此执行合成反应。现有技术目前的UAS商业生产由物理混合两种化合物来实现,通过在造粒步骤例如鼓或盘中,添加粉碎的固体硫酸铵到熔融尿素的工艺,如US3785796所述。这可称为“固体途径”。这看上去是相当简单的工艺。然而其存在一些严重缺点:从经济角度和工艺角度。AS作为其它工业,例如己内酰胺工业的副产物是廉价易得的。然而,其含有一些变动杂质。因此,重要的是确保AS质量的不变和稳定以使最终成粒的UAS的情况得以保持,这是重要的市场问题。为获得均匀和匀称的产物,待用于该固体途径的AS晶体需要在与尿素混合之前被细密地压碎。AS的压碎产生很有腐蚀性的灰尘,恶化建筑内工作条件且增强对周围的腐蚀,不仅显著增加压碎机维修成本,还增加整个设施的维修成本。而且,很细的AS固体颗粒也容易结块。这种现象意味着在停工期间生产率的损失和为预防这种事故的特殊维护,即额外成本。“固体”途径的这些缺点可由“液体”途径避免,该液体途径即为采用氨和硫酸作为原料,而非AS晶体。尿素溶液中AS合成反应在US3928015中描述为两步反应。硫酸氢盐溶液和氨在尿素溶液中反应以产生基本上无水的AS,其与熔融尿素在简单且廉价的罐式或管式反应器内掺合。硫酸氢盐对应于将1摩尔硫酸和1摩尔氨反应生成的产物,而硫酸铵对应于将1摩尔硫酸和2摩尔氨反应所得产物。硫酸的第一次氨化(得到硫酸氢盐)比第二次氨化放热更多。硫酸与氨的反应是强烈放热的,且因此该原位进行的反应释放的热允许浓缩尿素溶液且借此节省了蒸汽设施。然而,由于酸与尿素迅速反应产生尿素损失,所以在尿素溶液中原位合成AS是困难的。如果损失太高,那么这就显著限制了对于UAS生产而言,任何液体途径相对于固体途径的优势。相比于硫酸,硫酸氢盐对尿素不那么活泼。根据US3928015,硫酸氢盐被单独合成以最小化尿素分解。由此,其没有充分利用第一次氨化释放的热。在该专利描述的工艺中,固体途径中所需的昂贵压碎步骤得以避免,但是他们仅利用了第二次氨化释放的热。WO01/51429涉及含硫酸铵和尿素的肥料生产方法。提供了尿素水溶液,其相对于溶液总重量含有0.1-50wt%的游离氨和/或以氨基甲酸铵形式结合的氨。所述尿素水溶液与硫酸,并任选地与氨在25-250℃温度以及0.1-250巴压力下反应。尿素硫酸铵溶液或悬浮液的形成量使得硫酸铵与尿素在该尿素硫酸铵溶液或悬浮液中的重量比为10∶90至65∶35。在这些条件下排出的二氧化碳和氨返回尿素合成。此后,该尿素-硫酸铵溶液或悬浮液进行后续加工以生产固体或液体肥料。已描述原位反应的原则,没有详细描述在无高尿素损失的情况下获得该结果的技术。该专利充分利用了硫酸铵合成原位释放的热,但是在尿素全部产量方面没有贡献。本发明的目的在于在尿素合成反应器中在尿素转化率增加的情况下生产尿素硫酸铵。另一目的在于自由变化UAS中AS含量。进一步目的在于在尿素和硫酸之间基本没有反应的情况下进行该工艺。本发明的这些和其它目的由下述方法获得,且该发明由所附专利权利要求进一步限定和特征化。由此,本发明涉及从硫酸、氨和尿素生产固体尿素硫酸铵(UAS)肥料的方法,其中游离氨和/或作为来自尿素生产的待分解的氨基甲酸盐与硫酸反应,基本上不分解工艺流中的尿素。尿素和硫酸铵被进一步混合并微粒化。尿素生产工艺中硫酸铵生产的整合点根据所需产物组成而选择。反应优选在管式反应器中进行,其中反应器头部增强了硫酸和氨之间的化学反应...