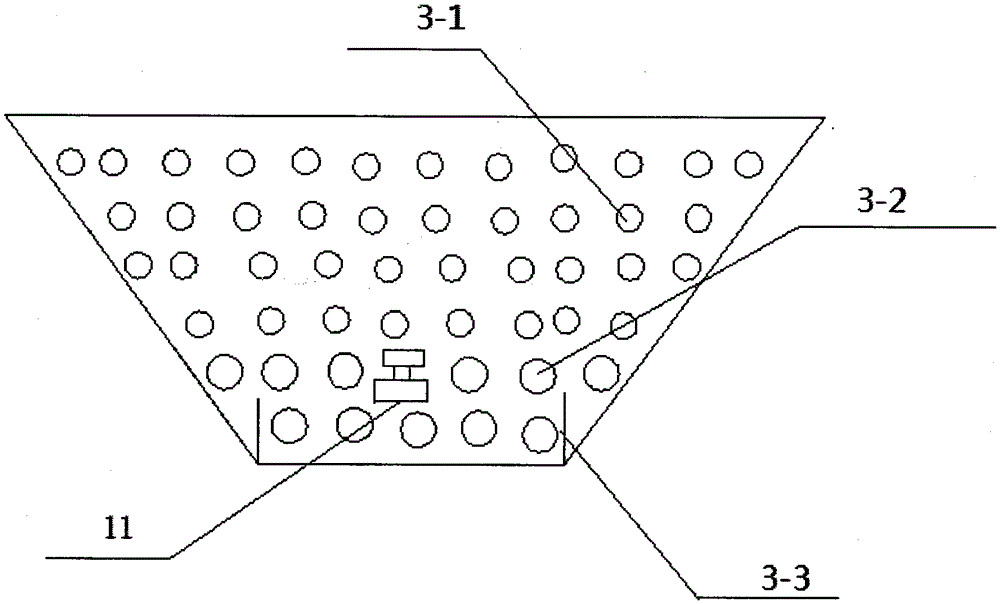
本发明属于四氯化钛制备技术领域,具体涉及制备四氯化钛的装置及方法。
背景技术:四氯化钛是制造钛白(二氧化钛)、金属钛的一个重要中间体。钛白被认为是目前世界上性能最好的一种白色颜料,广泛应用于涂料、塑料、造纸、印刷油墨、化纤、橡胶、化妆品等工业。中国目前已经是继美国后第二大的钛白粉消耗国,而且增长势头迅猛,潜力也非常大。目前钛的用途发展也很快,已被广泛应用于飞机、火箭、人造卫星、宇宙飞船、舰艇、轻工、化工、纺织、医疗以及石油化工等领域。中国是钛资源大国,我国的钛资源主要集中在攀枝花地区,其二氧化钛(TiO2)的储量达8.7亿吨左右,占国内钛储量的90%以上。现有四氯化钛的制备是通过精钛矿或富钛料与氯气在高温下反应获得,其生产工艺主要有两种:(1)熔盐氯化法,是将含钛原料和焦炭混合物置入由KCl,NaCl,MgCl2熔盐中,通入氯气进行反应,该工艺的缺点是设备产能低、反应体积大,特别是废液废渣多,对环境污染大,已不满足现代制造业的要求,正逐步被淘汰。(2)沸腾氯化法,沸腾氯化是将含钛原料制备成一定分布的颗粒,并随焦炭颗粒一起放入反应器中,通人氯气使颗粒悬浮起来进行反应,该方法反应器效率高,没有废液产生,废渣也很少,对环境的影响也较小,因而沸腾氯化是目前制备四氯化钛的主要方法。该工艺的缺点是对原料品质要求很高,特别是钙镁氧化物含量要小于1%,这是由于沸腾氯化反应温度通常在800~1000℃之间,当钛渣中含有较多的钙镁氧化物时,将产生大量的氯化钙、氯化镁,而氯化钙的熔点为714℃,氯化镁的熔点为772℃,在800-1000℃的氯化反应器内氯化钙和氯化镁都呈液态,粘结周围的颗粒形成较大的聚团,破坏沸腾床的稳定操作。但攀枝花钛矿的品位较低,钙镁氧化物含量高,以攀枝花钛精矿冶炼的高钛渣CaO、MgO含量在7~11%,现有的沸腾氯化工艺还不能将低品位(钙镁含量高)的钛原料直接用作沸腾氯化的原料。如何充分利用攀枝花地区的低品位钛矿制备四氯化钛,是急待解决的难题。现有用低品位高钛渣制备四氯化钛的装置及方法,如2003年11月12日公开的,公开号为CN1454849A的“用于含钛矿物氯化制备四氯化钛的装置和方法”专利,公开是一种多级快速流化床和湍动流化床串联的方式处理低品位高钛渣工艺,即以含钛矿物和石油焦为固体原料、以氯气和氧气为气体原料,采用多级(3-10级)快速反应流化床和湍流流化床作为反应器,先进行高温氯化反应,后经冷却,再进行一次固气分离而制得成品。该专利主要有以下缺点:1)反应器结构复杂,需要的反应器数量较多,而且两类反应器之间结构差异较大,设 备投资大,生产成本高。2)为了避免密度很小的焦炭颗粒被气体携带出反应器,须采用颗粒直径很大的焦炭颗粒,或者采用较小的操作气速,这两种情况都会降低反应的速率,影响反应器的效率,生产效率不高。3)湍动流化床与快速流化床的直径相差较大,进出口之间有较大的倾角,固体颗粒,特别是对于由于表面有氯化镁、氯化钙而粘性较大的高钛渣颗粒,容易在进出口粘结,造成系统操作的而不正常,影响产品的产量和质量;又如专利号为ZL200910103049.9的“一种半循环流化制备四氯化钛的方法”,公开的方法是以低品位的高钛渣和焦炭为固体原料,以氯气和氮气为气体原料,采用循环流化床装置,经过高温氯化反应,冷却及气固分离而将四氯化钛产品。该方法的主要缺点是:1)循环流化床装置较为复杂,所包含的流化床反应器包含了加热段,高温反应段以及顶部的冷却分离段,结构复杂,操作不方便,设备投资大;2)为了促使聚团破碎,需要较高的气速,为提高单程转化率低需要很高的反应器;3)由于反应器在不同高度存在升温和降温,能量效率低。
技术实现要素:本发明的目的是:针对现有用低品位高钛渣制备四氯化钛的装置及方法的不足,提供一种振动式内循环流化制备四氯化钛的装置及方法,本发明装置具有结构紧凑,热量利用高,生产效率高,产品质量好,操作方便且能有效处理钙镁含量高,粘性大的低品位钛渣等特点,本发明方法是将物料加热和高温氯化反应耦合在一起,采用外循环流化床加热,内流化床反应器反应的方法,具有反应温度分布均匀,控制方便,钛转化率高等特点。本发明的机理:本发明采用振动式内循环流化氯化制备四氯化钛的方法,反应物氯气和钛渣颗粒以及焦炭颗粒在流化床内部进行流化氯化反应,由于该反应属于缩核反应:随着反应的进行,气固混合物在上行过程中,固体反应物颗粒的粒径逐渐减小。反应物从内流化床反应器顶部出口流出进入自由空域,由于自由空域直径增大,气体的表观速度减小,携带的细颗粒被抛撒在振动分布板上,在振动器的振动下细颗粒穿过振动分布板上的细孔进入外循环流化床,与新加入的焦炭颗粒一起下流,从内流化床反应器壁上的回料口进入内流化床反应器,从而形成内循环流化氯化过程。从自由空域顶部出料管流出的气体将携带极细小的粉尘通过直管进入高效旋风分离器,粉尘从旋风分离器下部固体颗粒出料口排出。设备底部设置有氧气和氮气混合气体进料管,输入的氧气和焦炭颗粒进行烧炭反应,放出大量的热量,可以为整个反应系统提供充分的热量,输入的氮气维持外循环床内颗粒处于初始流化状态,便于颗粒向下流动。在内流化床反应器底部有氯气进料管,携带钛渣颗粒进入内流化床反应器,进行高温氯化反应,制得四氯化钛产品。实现本发明目的的技术方案是:一种振动式内循环流化制备四氯化钛的装置,主要包括外循环流化床、内流化床反应器、振动分布板和振动器、旋风分离器、气体缓冲罐和气体分 布板等。其特征是:所述外循环流化床、内流化床反应器、振动分布板、气体缓冲罐、挡板、出料管、直管、进料管的材料均为不锈钢材质或钛合金材质。所述外循环流化床的形状为顶端封闭的圆柱形壳体,所述圆柱形壳体的内径为500~3000mm、长度为1000~5000mm、厚度为3~8mm。在所述圆柱形壳体内的上部高度为400~3000mm的空间为自由空域,设置自由空域用以焦炭固体原料的进料及从所述内流化床反应器流出的固体颗粒的沉降。在所述自由空域的圆周壁上,对称地设置两个孔径为50~150mm的通孔(即焦炭固体原料入口),在所述焦炭固体原料入口外分别焊接一根长度为500~1500mm、与所述外循环流化床的壳体的夹角呈30°~70°、内径与所述焦炭固体原料入口相匹配的焦炭颗粒进料管,以便焦炭固体原料能顺利地输入所述的外循环流化床内,并通过所述的振动分布板进入所述的内循环流化床反应器内。在所述圆柱形壳体的顶端面的圆心处(即位于所述自由空域的顶端圆心处)设置一孔径为50~200mm的通孔(即出料口),在所述的出料口处焊接一根长度为1500~2000mm、内径与所述出料口相匹配的出料管,并在所述出料管的另一端焊接一根长度为1000~5000mm、外径为50~200mm、与所述出料管相垂直的直管,所述直管的另一端与所述旋风分离器的入口固接连通,以便所述外循环流化床输出的经过氯化反应后的混合气体顺利输入所述的旋风分离器进行气固分离。所述外循环流化床底端通过法兰固接气体分布板1,所述的气体分布板1为厚度为1~10mm、外径与所述的外循环流化床壳体的内径相匹配、内径与所述内循环流化床反应器壳体的内径相匹配的圆环形陶瓷板,在所述的气体分布板1上均匀设置开孔率为1%~10%、孔径为0.5~2.5mm的通孔,以便所述的氮气和氧气的混合气体均匀地输入所述的外循环流化床的壳体内,所述气体分布板1用于氧气和氮气混合气体均匀分布。在所述外循环流化床的圆柱形壳体内的自由空域的下端处,焊接一振动分布板,以便焦炭固体颗粒通过所述振动分布板进入所述的外循环流化床内和所述的内流化床反应器内。所述内流化床反应器的形状为两端开口的圆柱形壳体,所述内流化床反应器壳体的顶端焊接在所述的振动分布板下部的外表面上。所述圆柱形壳体内径为250~2500mm、长度为800~2000mm、厚度为3~8mm。在所述圆柱形壳体的下部的圆周壁上还均匀设置2~8个、孔径为10~50mm的通孔(即颗粒回料口),以便经所述振动分布板的焦炭固体原料顺利进入所述的内流化床反应器内进行氯化反应。在所述圆柱形内流化床反应器壳体下部一侧的壁上设置一孔径为50~150mm的通孔(即钛渣固体原料入口),在所述的通孔处焊接一根长度为200~800mm、与所述圆柱形内流化床反应器壳体的夹角呈30°~70°、内径与所述钛渣固体原料入口相匹配的钛渣颗粒进料管,以便钛渣固体原料顺利进入所述的内循环流化床反应器内。 所述圆柱形内流化床反应器壳体底端通过法兰固接气体分布板2,所述的气体分布板2为厚度为1~10mm、外径与所述内流化床反应器壳体的内径相匹配的圆盘形陶瓷板,在所述的气体分布板2上均匀设置开孔率为1%~10%、孔径为0.5~2.5mm的通孔,以便所述的氯气气体原料均匀地输入所述圆柱形内流化床反应器壳体内。所述的振动分布板的形状为两端敞开的截锥形壳体,所述截锥形壳体的上顶面的内径与所述外循环流化床壳体的内径相匹配、下底面的内径为100~1000mm、高度为300~1200mm、厚度为100~400mm。所述截锥形壳体分为上部和下部,在所述截锥形壳体的上部(即占整个振动分布板长度的2/3)均匀设置孔径为0.5~2mm、孔间距为2~6mm的小孔(即振动分布板上部小孔),以便较小的焦炭固体颗粒经过所述小孔进入所述外循环流化床中进行物料循环;在所述截锥形壳体下部(即占整个振动分布板长度的1/3)均匀设置孔径为1~3mm、孔间距为3~10mm的大孔(即振动分布板下部大孔),以便较大的焦炭固体颗粒经过所述大孔进入所述内流化床反应器内进行氯化反应。在所述截锥形壳体内的底端面上设置一两端面均敞开的圆柱形壳体的挡板,所述挡板的高度为20~50mm、厚度为5~8mm、内径与所述截锥形壳体的底面内径相匹配,用以阻挡所述振动分布板中下滑的焦炭固体颗粒,防止过多焦炭固体颗粒直接进入所述内流化床反应器内。在所述的振动分布板内放置一振动器,所述振动器为市购的、振动压力为0.1~0.35MPa的仓壁式振动器,通过调整振动频率和功率,赋予所述振动分布板上颗粒更高的能量,促使焦炭固体颗粒通过所述振动分布板的细孔进入所述外循环流化床内和所述内流化床反应器中。所述的气体缓冲罐为厚度为3~10mm的、一小一大的两个开口顶面和封闭底面的截锥形壳体。两个所述的截锥形壳体组装成一个同轴心的容器,所述的小的截锥形壳体(即气体缓冲罐2)的长度为200~1500mm、开口顶面的内径与所述内流化床反应器壳体的内径相匹配、封闭底面的内径为150~1200mm,所述的气体缓冲罐2与所述的圆盘形气体分布板2通过法兰固接所述内流化床反应器底端,在所述的气体缓冲罐2的封闭底面的轴心处,设置一孔径为50~120mm的通孔(即氯气原料进料口),在所述通孔处焊接一管径与所述的氯气原料进料口相匹配、总长度为400~2100mm的直角形气体进料管2,以便顺利地将氯气气体原料输入所述的气体缓冲罐2内,保证氯气气体原料持续稳定地输入所述的内流化床反应器内,所述气体缓冲罐2用于氯气气体的缓冲。所述的大的截锥形壳体(即气体缓冲罐1)的长度为500~2000mm、顶面开口的内径与所述外循环流化床壳体的内径相匹配、封面底面的内径为300~2000mm,所述气体缓冲罐1与所述的圆环形气体分布板1通过法兰固接所述外循环流化床底端,并在所述的气体缓冲罐1的截锥形壳体的外壁上的同一高度均匀焊接4~6个鞍型支架或支撑式支架或掩护式支架固定在地面上。在所述气体缓冲罐1的封闭底面的轴心处,设 置一孔径为50~150mm的通孔(即氯气和氮气的混合气体的进料口),在所述混合气体进料口处焊接一根长度为100~500mm、管径与所述混合气体进料口相匹配的气体进料管1,以便将所述的混合气体持续稳定地输入所述的气体缓冲罐1内,所述气体缓冲罐1用于氧气和氮气混合气体的缓冲;并在所述气体缓冲罐1的侧壁上并对应于所述气体进料管2的出口处,设置一孔径与所述进料管2的外径相匹配的通孔,以便所述的气体进料管2伸出所述的气体缓冲罐1外,保证让氯气气体原料顺利输入到所述的气体缓冲罐2内。所述的旋风分离器为市售的常规产品,从所述的外循环流化床的自由空域顶部流出的携带极细小的粉尘的气体通过所述的直管进入所述的旋风分离器,进行气固分离,收集从所述旋风分离器下部的固体颗粒出料口排出的粉尘,经分离后再循环利用,收集从所述旋风分离器上部的气体出口排出的气体,经冷却后得到四氯化钛产品,并收集滤出的剩余气体,经处理后可再利用,以免污染大气。一种振动式内循环流化制备四氯化钛的方法,以低品位的钙镁含量高的高钛渣和焦炭为固体原料,以氧气,氮气及氯气为气体原料,利用本发明装置,经过氯化反应和冷却及气固分离而制得成品。所述的具体步骤如下:(1)原料处理以低品位的钙镁含量高的高钛渣(简称高钛渣)和焦炭为固体原料,以氧气和氮气及氯气为气体原料,先对所述的固体原料分别通过0.7~21目的分离筛进行分筛,并按高钛渣颗粒的平均粒径∶焦炭颗粒的平均粒径之比1∶0.8~1.2,和按高钛渣颗粒的质量∶焦炭颗粒的质量比为1∶0.3~3的比例备料,然后分别对高钛渣颗粒和焦炭颗粒进行加热,加热至固体颗粒温度为400~600℃,备用。对所述气体原料中的氯气进行加热至300~500℃,备用;对氧气和氮气先按氧气∶氮气的体积比为1∶0.1~0.5的比例进行混合,再对混合气体进行加热至100~300℃,备用。(2)氯化反应第(1)步完成后,将第(1)步处理后的原料,分别输入到本发明的装置中,即焦炭颗粒以1.8~540kg/h的速度从所述装置的焦炭颗粒进料管输入,通过所述装置振动分布板进入所述装置的外循环流化床内和内流化床反应器中;高钛渣颗粒以36~180kg/h的速度从所述装置的钛渣颗粒进料管输入到所述的内流化床反应器中;氯气以0.5~3.5m/s的速度从所述装置的气体缓冲罐2底面的气体进料管2输入到所述的内流化床反应器中,氧气和氮气的混合气体以0.2~1.5m/s的速度从所述装置的气体缓冲罐1底面的气体进料管1输入到所述的外循环流化床中。使所述的焦炭颗粒在所述外循环流化床下行中与所述的氧气和氮气混合气体逆流接触反应,利用反应放出的热量加热焦炭颗粒,使焦炭颗粒达到1000~1300℃,所得到的高温 焦炭颗粒从所述内流化床反应器壁上的颗粒回料口进入所述的内流化床反应器内,用以保持所述内流化床反应器内部温度为800~1100℃;从所述的气体进料管2输入的氯气和从所述钛渣颗粒进料管进入的钛渣颗粒在所述的内流化床反应器内进行高温氯化反应;随反应的进行,气固混合物在上行过程中,固体反应物颗粒粒径逐渐减小,进入所述外循环流化床内上部的自由空域,气体表观速度减小,携带的细颗粒被抛洒在所述振动分布板上,在所述振动器振动下较小颗粒穿过所述振动分布板上部小孔进入所述外循环流化床内,与新进料的焦炭颗粒一起下流,经过所述的颗粒回料口进入所述内流化床反应器内,从而形成内循环流化氯化过程;所述氯化反应后产生的并携带有少量粉尘的气体通过所述的外循环流化床上部的自由空域和出料管及直管输入所述装置的旋风分离器中。所述的装置在运行中的压力为0.1~0.35MPa。(3)气固分离第(2)步完成后,在所述装置的旋风分离器中,对第(2)步氯化反应产生的带有少量粉尘的气体,进行气固分离,收集在所述旋风分离器上部的气体出口滤出的气体,自然冷却后得到四氯化钛产品,并收集滤出的剩余气体,经处理后可再利用以免污染大气;收集从所述旋风分离器下部的固体颗粒出料口滤出的粉尘,经分离后再利用。本发明采用上述技术方案,主要有以下效果1本发明装置采用的振动式内循环流化床,进料的焦炭颗粒通过颗粒回料口在外循环流化床和内流化床反应器内进行物料循环并和进料的气体接触反应,使得几种物料良性接触且得到充分的利用,避免了过多物料的损失,节约成本,生产效率进一步提高,气固两相处于流化状态,避免了颗粒间相互粘结形成的较大的聚团,破坏振动式内循环流化床的稳定操作;其次,本发明装置利用振动可以将附着在振动分布板上的颗粒松动,而倾斜的出口板有利于粘性颗粒流动,防止颗粒黏附在振动分布板上。2本发明装置中振动分布板上开有不同大小的细孔,可以通过振动将颗粒分级,细颗粒先从振动分布板上部小孔流出,从外循环流化床以初始流化状态缓慢流下,而较大的颗粒从振动分布板下部大孔流出,沿内流化床反应器壁向下流动,这样可以阻止粘性颗粒黏附在内流化床反应器内壁,起到阻粘作用。3本发明装置采用旋风分离器出口排渣不影响反应系统的操作,因而系统可以连续、稳定、长期工作,且产品质量高,适用于大规模的工业生产。4本发明装置的反应器结构紧凑,易于操作、检修,降低了生产成本。5本发明方法采用部分焦炭氧化产生热量满足反应所需热量,这样供热体系与反应体系耦合在一个装置内,并采用热容量大的固体焦炭颗粒为热介质,提高料热量的使用效率。6本发明方法操作方便且能充分利用低品位钙镁含量高粘性大钛渣,将物料加热和高温氯化反应耦合在一起,采用外循环流化床加热,内流化床反应器反应的方法,反应温度分布均匀,控制方便,钛转化率高。本发明可广泛应用于利用钛矿制备四氯化钛,特别适用于利用低品位的钙镁含量高的高钛渣制备四氯化钛。附图说明图1为本发明装置的结构示意图;图2为图1中放大的振动分布板的结构示意图。图中:1外循环流化床,1-1外循环流化床壁,1-2焦炭颗粒进料管,1-3钛渣颗粒进料管,2内循环流化床反应器,2-1内流化床反应器壁,2-2颗粒回料口,3振动分布板,3-1振动分布板上部小孔,3-2振动分布板下部大孔,3-3挡板,4出料管,5直管,6旋风分离器,6-1气体出口,6-2阀门,6-3固体颗粒出料口,7钛渣颗粒,8-1气体分布板2,8-2气体分布板1,9-1气体缓冲罐2,9-2气体进料管2,9-3气体进料罐1,9-4气体进料管1,10焦炭颗粒,11振动器。具体实施方式下面结合具体实施方式,进一步说明本发明。实施例1如图1、2所示,一种振动式内循环流化制备四氯化钛的装置。主要包括外循环流化床、内流化床反应器、振动分布板和振动器、旋风分离器、气体缓冲罐和气体分布板等。其特征是:所述外循环流化床、内流化床反应器、振动分布板、气体缓冲罐、挡板、出料管、直管、进料管的材料均为不锈钢材质。所述外循环流化床1的形状为顶端封闭的圆柱形壳体,所述圆柱形壳体设置的内径为1800mm、长度为3000mm、厚度为5mm。在所述圆柱形壳体内的上部高度1700mm的空间为自由空域,设置自由空域用以焦炭固体原料的进料及从所述内流化床反应器2流出的固体颗粒的沉降。在所述自由空域的圆周壁上,对称地设置两个孔径为100mm的通孔(即焦炭固体原料入口),在所述焦炭固体原料入口外分别焊接一根长度为1000mm、与所述外循环流化床1的壳体的夹角呈50°、内径与所述焦炭固体原料入口相匹配的焦炭颗粒进料管1-2,以便焦炭固体原料能顺利地输入所述的外循环流化床1内,并通过所述的振动分布板3进入所述的内循环流化床反应器2内。在所述圆柱形壳体的顶端面的圆心处,即位于所述自由空域的顶端圆心处,设置一孔径为120mm的通孔(即出料口),在所述的出料口处焊接一根长度为 1000mm、内径与所述出料口相匹配的出料管4,并在所述出料管4的另一端焊接一根长度为3000mm、外径为120mm、与所述出料管4相垂直的直管5。所述直管5的另一端与所述旋风分离器6的入口固接连通,以便所述外循环流化床1输出的经过氯化反应后的混合气体顺利输入所述的旋风分离器6进行气固分离。所述外循环流化床1底端通过法兰固接气体分布板18-2,所述的气体分布板18-2为厚度为5.5mm、外径与所述的外循环流化床1壳体的内径相匹配、内径与所述内循环流化床反应器2壳体的内径相匹配的圆环形陶瓷板。在所述的气体分布板18-2上均匀设置开孔率为0.05、孔径为1.5mm的通孔,以便所述的氮气和氧气的混合气体均匀地输入所述的外循环流化床1的壳体内,所述气体分布板18-2用于氧气和氮气混合气体均匀分布。在所述外循环流化床1的圆柱形壳体内的自由空域的下端处,焊接一振动分布板3,以便焦炭固体颗粒通过所述振动分布板3进入所述的外循环流化床1内和所述的内流化床反应器2内。所述内流化床反应器2的形状为两端开口的圆柱形壳体,所述内流化床反应器2壳体的顶端焊接在所述的振动分布板3下部的外表面上,所述圆柱形壳体内径为1350mm,长度为1400mm,厚度为5mm。在所述圆柱形壳体的下部的圆周壁上还均匀设置5个,孔径为30mm的通孔(即颗粒回料口2-2),以便经所述振动分布板3的焦炭固体原料顺利进入所述的内流化床反应器2内进行氯化反应。在所述圆柱形内流化床反应器2壳体下部一侧的壁上设置一孔径为100mm的通孔(即钛渣固体原料入口),在所述的通孔处焊接一根长度为500mm、与所述圆柱形内流化床反应器2壳体的夹角呈50°、内径与所述钛渣固体原料入口相匹配的钛渣颗粒进料管1-3,以便钛渣固体原料顺利进入所述的内循环流化床反应器2内。所述圆柱形内流化床反应器2壳体底端通过法兰固接气体分布板28-1,所述的气体分布板28-1为长度为厚度为5.5mm、外径与所述内流化床反应器2壳体的内径相匹配的圆盘形陶瓷板,在所述的气体分布板28-1上均匀设置开孔率为0.05、孔径为1.5mm的通孔,以便所述的氯气气体原料均匀地输入所述圆柱形内流化床反应器2壳体内。所述的振动分布板3的形状为两端敞开的截锥形壳体,所述截锥形壳体的上顶面的内径与所述外循环流化床1壳体的内径相匹配、下底面的内径为550mm、高度为750mm、厚度为250mm,所述截锥形壳体分为上部和下部,在所述截锥形壳体的上部(即占整个振动分布板3长度的2/3),均匀设置孔径为1.2mm、孔间距为4mm的小孔(即振动分布板上部小孔3-1),以便较小的焦炭固体颗粒经过所述小孔进入所述外循环流化床1中进行物料循环。在所述截锥形壳体下部(即占整个振动分布板3长度的1/3),均匀设置孔径为2mm、孔间距为6.5mm的大孔(即振动分布板下部大孔3-2),以便较大的焦炭固体颗粒经过所述大孔进入所述内流化床反应器2内进行氯化反应。在所述截锥形壳体内的底端面上设置一两端面均敞开的圆柱 形壳体的挡板3-3,所述挡板3-3的高度为35mm、厚度为6.5mm、内径与所述截锥形壳体的底面内径相匹配,用以阻挡所述振动分布板3中下滑的焦炭固体颗粒,防止过多焦炭固体颗粒直接进入所述内流化床反应器2内。在所述的振动分布板3内放置一振动器11,所述振动器11为市购的、振动压力为0.22MPa的仓壁式振动器,通过调整振动频率和功率,赋予所述振动分布板上颗粒更高的能量,促使焦炭固体颗粒通过所述振动分布板3的细孔进入所述外循环流化床1内和所述内流化床反应器2中。所述的气体缓冲罐为厚度为6.5mm的、一小一大的两个开口顶面、封闭底面的截锥形壳体,两个所述的截锥形壳体组装成一个同轴心的容器,所述的小的截锥形壳体(即气体缓冲罐29-1)的长度为900mm、开口顶面的内径与所述内流化床反应器2壳体的内径相匹配、封闭底面的内径为700mm,所述的气体缓冲罐29-1与所述的圆盘形气体分布板28-1通过法兰固接在所述内流化床反应器2底端,在所述的气体缓冲罐29-1的封闭底面的轴心处,设置一孔径为80mm的通孔(即氯气原料进料口),在所述通孔处焊接一管径与所述的氯气原料进料口相匹配、总长度为1250mm的直角形气体进料管29-2,以便顺利地将氯气气体原料输入所述的气体缓冲罐29-1内,保证氯气气体原料持续稳定地输入所述的内流化床反应器2内,所述气体缓冲罐29-1用于氯气气体的缓冲。所述的大的截锥形壳体(即气体缓冲罐19-3)的长度为1250mm,顶面开口的内径与所述外循环流化床1壳体的内径相匹配,封面底面的内径为1200mm,所述气体缓冲罐19-3与所述的圆环形气体分布板18-2通过法兰固接在所述外循环流化床1底端,并在所述的气体缓冲罐19-3的截锥形壳体的外壁上的同一高度均匀焊接5个支撑式支架固定在地面上。在所述气体缓冲罐19-3的封闭底面的轴心处,设置一孔径为100mm的通孔(即氯气原料进料口),在所述混合气体进料口处焊接一根长度为300mm、管径与所述混合气体进料口相匹配的气体进料管19-4,以便将所述的混合气体持续稳定地输入所述的气体缓冲罐19-3内,所述气体缓冲罐19-3用于氧气和氮气混合气体的缓冲;并在所述气体缓冲罐19-3的侧壁上并对应于所述气体进料管29-2的出口处,设置一孔径与所述进料管29-2的外径相匹配的通孔,以便所述的气体进料管29-2伸出所述的气体缓冲罐19-3外,让氯气气体原料顺利输入。所述的旋风分离器6为市售的常规产品,从所述的外循环流化床1的自由空域顶部流出的携带极细小的粉尘的气体通过所述的直管5进入所述的旋风分离器6,进行气固分离,收集从所述旋风分离器6下部的固体颗粒出料口6-3排出的粉尘,经分离后再循环利用,收集从所述旋风分离器上部的气体出口6-1排出的气体,经冷却后得到四氯化钛产品,并收集滤出的剩余气体,经处理后可再利用,以免污染大气。实施例2一种振动式内循环流化制备四氯化钛的装置,同实施例1,其中:所述外循环流化床1的内径为500mm、长度为1000mm、厚度为3mm,在所述圆柱形壳体内的自由空域上部高度为400mm,所述自由空域的圆周壁上的两个通孔(即焦炭固体原料入口)的孔径为50mm。在所述焦炭固体原料入口外分别焊接一根长度为500mm、与所述外循环流化床1的壳体的夹角呈30°、内径与所述焦炭固体原料入口相匹配的焦炭颗粒进料管1-2。在所述圆柱形壳体的顶端面的圆心处的通孔(即出料口)的孔径为50mm,在所述的出料口处焊接一根长度为1500mm、内径与所述出料口相匹配的出料管4,并在所述出料管4的另一端焊接一根长度为1000mm、外径为50mm、与所述出料管4相垂直的直管5。所述的气体分布板18-2为厚度为1mm。在所述的气体分布板18-2上均匀设置开孔率为0.01、孔径为0.5mm的通孔。所述内流化床反应器2圆柱形壳体的内径为250mm、长度为800mm、厚度为3mm,所述圆柱形壳体的下部的圆周壁上还均匀设置2个、孔径为10mm的通孔(即颗粒回料口2-2)。在所述圆柱形内流化床反应器2壳体下部一侧的壁上设置一孔径为50mm的通孔(即钛渣固体原料入口),在所述的通孔处焊接一根长度为200mm、与所述圆柱形内流化床反应器2壳体的夹角呈30°、内径与所述钛渣固体原料入口相匹配的钛渣颗粒进料管1-3。述圆柱形内流化床反应器2壳体底端通过法兰固接在气体分布板28-1上,所述的气体分布板28-1为厚度为1mm、外径与所述内流化床反应器2壳体的内径相匹配的圆盘形陶瓷板。所述的气体分布板28-1上均匀设置开孔率为0.01、孔径为0.5mm的通孔。所述的振动分布板3的下底面的内径为100mm、高度为300mm、厚度为100mm。在所述振动分布板的上部均匀设置孔径为0.5mm、孔间距为2mm的小孔(即振动分布板上部小孔3-1)。在所述振动分布板的下部均匀设置孔径为1mm、孔间距为3mm的大孔(即振动分布板下部大孔3-2)。所述挡板3-3的高度为20mm、厚度为5mm。所述振动器11为振动压力为0.1MPa的仓壁式振动器。所述的气体缓冲罐为厚度为3mm的一小一大的两个截锥形壳体,气体缓冲罐29-1的长度为200mm、封闭底面的内径为150mm。在所述的气体缓冲罐29-1的封闭底面的轴心处,设置一孔径为50mm的通孔(即氯气原料进料口),在所述通孔处焊接一管径与所述的氯气原料进料口相匹配、总长度为400mm的直角形气体进料管29-2。气体缓冲罐19-3的长度为500mm、封面底面的内径为300mm。在所述的气体缓冲罐19-3的截锥形壳体的外壁上的同一高度均匀焊接4个鞍型支架固定在地面上,在所述气体缓冲罐19-3的封闭底面的轴心处,设置一孔径为50mm的通孔(即氯气和氮气的混合气体的进料口),在所述混合气体进料口处焊接一根长度为100mm的气体进料管19-4。实施例3一种振动式内循环流化制备四氯化钛的装置,同实施例1,其中:所述外循环流化床、内流化床反应器、振动分布板、气体缓冲罐、挡板、出料管、直管、进料管的材料均为钛合金材质。所述外循环流化床1的内径为3000mm、长度为5000mm、厚度为8mm,所述圆柱形壳体内的上部自由空域的高度为3000mm,所述自由空域的圆周壁上的通孔(即焦炭固体原料入口)的孔径为150mm,在所述焦炭固体原料入口外分别焊接一根长度为1500mm、与所述外循环流化床1的壳体的夹角呈70°的焦炭颗粒进料管1-2。在所述圆柱形壳体的顶端面的圆心处,设置一孔径为200mm的通孔(即出料口),在所述的出料口处焊接一根长度为2000mm的出料管4,并在所述出料管4的另一端焊接一根长度为5000mm、外径为200mm、与所述出料管4相垂直的直管5。所述的气体分布板18-2为厚度为10mm的圆环形陶瓷板,在所述的气体分布板18-2上均匀设置开孔率为0.1、孔径为2.5mm的通孔。所述内流化床反应器2的内径为2500mm、长度为2000mm、厚度为8mm,在所述圆柱形壳体的下部的圆周壁上均匀设置8个、孔径为50mm的通孔(即颗粒回料口2-2),在所述内流化床反应器2壳体下部一侧的壁上设置一孔径为150mm的通孔(即钛渣固体原料入口),在所述的通孔处焊接一根长度为800mm、与所述圆柱形内流化床反应器2壳体的夹角呈70°的钛渣颗粒进料管1-3。所述的气体分布板28-1为长度为厚度为10mm的圆盘形陶瓷板,在所述的气体分布板28-1上均匀设置开孔率为0.1,孔径为2.5mm的通孔。所述振动分布板3的下底面的内径为1000mm、高度为1200mm、厚度为400mm。所述振动分布板3的上部均匀设置孔径为2mm、孔间距为6mm的小孔(即振动分布板上部小孔3-1),在所述振动分布板3下部(即占整个振动分布板3长度的1/3),均匀设置孔径为3mm、孔间距为10mm的大孔(即振动分布板下部大孔3-2),所述挡板3-3的高度为50mm、厚度为8mm。所述振动器11为振动压力为0.35MPa的仓壁式振动器。所述的气体缓冲罐为厚度为10mm的一小一大的两个截锥形壳体。气体缓冲罐29-1的长度为1500mm,封闭底面的内径为1200mm,在所述的气体缓冲罐29-1的封闭底面的轴心处,设置一孔径为120mm的通孔(即氯气原料进料口),在所述通孔处焊接一管径与所述的氯气原料进料口相匹配、总长度为2100mm的直角形气体进料管29-2。气体缓冲罐19-3的长度为2000mm,封面底面的内径为2000mm。在所述的气体缓冲罐19-3的截锥形壳体的外壁上的同一高度均匀焊接6掩护式支架固定在地面上,在所述气体缓冲罐19-3的封闭底面的轴心处,设置一孔径为150mm的通孔(即氯气和氮气的混合气体的进料口),在所述混合气体进料口处焊接一根长度为500mm的气体进料管19-4。实施例4一种振动式内循环流化制备四氯化钛的方法,以低品位的钙镁含量高的高钛渣和焦炭为固体原料,以氧气,氮气及氯气为气体原料,利用本发明装置,经过氯化反应和冷却及气固分离而制得成品。所述的具体步骤如下:(1)原料处理以低品位的钙镁含量高的高钛渣(简称高钛渣)和焦炭为固体原料,以氧气和氮气及氯气为气体原料,先对所述的固体原料分别通过11目的分离筛进行分筛,并按高钛渣颗粒的平均粒径∶焦炭颗粒的平均粒径之比1∶1,和按高钛渣颗粒的质量∶焦炭颗粒的质量比为1∶1.65的比例备料,然后分别对高钛渣颗粒和焦炭颗粒进行加热,加热至固体颗粒温度都为500℃,备用,对所述气体原料中的氯气进行加热至400℃,备用,对氧气和氮气先按氧气∶氮气的体积比为1∶0.3的比例进行混合,再对混合气体进行加热至200℃,备用。(2)氯化反应第(1)步完成后,将第(1)步处理后的原料,分别输入到本发明的装置中,即焦炭颗粒以271kg/h的速度从所述装置的焦炭颗粒进料管1-2输入,通过所述装置的振动分布板3进入所述装置的外循环流化床1内和所述装置的内流化床反应器2中,高钛渣颗粒以110kg/h的速度从所述装置的钛渣颗粒进料管1-3输入到所述的内流化床反应器2中,氯气以2m/s的速度从所述装置的气体缓冲罐29-1底面的气体进料管29-2输入到所述的内流化床反应器2中,氧气和氮气的混合气体以0.8m/s的速度从所述装置的气体缓冲罐19-3底面的气体进料管19-4输入到所述的外循环流化床1中。使所述的焦炭颗粒在所述外循环流化床1下行中与所述的氧气和氮气混合气体逆流接触反应,利用反应放出的热量加热焦炭颗粒,使焦炭颗粒达到1200℃,所得到的高温焦炭颗粒从所述内流化床反应器壁2-1上的颗粒回料口2-2进入所述的内流化床反应器2内,用以保持所述内流化床反应器2内部温度为950℃,从所述的气体进料管29-2输入的氯气和从所述钛渣颗粒进料管1-3进入的钛渣颗粒在所述的内流化床反应器2内进行高温氯化反应,随反应的进行,气固混合物在上行过程中,固体反应物颗粒粒径逐渐减小,进入所述外循环流化床1内上部的自由空域,气体表观速度减小,携带的细颗粒被抛洒在所述振动分布板3上,在所述振动器11振动下较小颗粒穿过所述振动分布板上部小孔3-1进入所述外循环流化床1内,与新进料的焦炭颗粒一起下流,经过所述颗粒回料口2-2进入所述内流化床反应器2内,从而形成内循环流化氯化过程,所述氯化反应后产生的并携带有少量粉尘的气体通过所述的外循环流化床1上部的自由空域和出料管4及直管5输入所述装置的旋风分离器6中,所述装置在运行中的压力为0.22MPa。(3)气固分离第(2)步完成后,在所述装置的旋风分离器6中,对第(2)步氯化反应产生的带有少量粉尘的气体,进行气固分离,收集在所述旋风分离器6上部的气体出口6-1滤出的气体,自然冷却后得到四氯化钛产品,并收集滤出的剩余气体,经处理后可再利用以免污染大气;收集从所述旋风分离器6下部的固体颗粒出料口6-3滤出的粉尘,经分离后再利用。最后经测定,含钛矿物的氯化率达到99%,经精制工序后,得到纯度为99%(质量分数)的四氯化钛。实施例5一种振动式内循环流化制备四氯化钛的方法,同实施例4,其中:第(1)步中,对所述的固体原料分别通过0.7目的分离筛进行分筛,高钛渣颗粒的平均粒径∶焦炭颗粒的平均粒径之比1∶0.8,高钛渣颗粒的质量∶焦炭颗粒的质量比为1∶0.3的比例备料,分别加热高钛渣颗粒和焦炭颗粒至温度都为400℃,对所述气体原料中的氯气进行加热至300℃,对氧气和氮气先按氧气∶氮气的体积比为1∶0.1的比例进行混合,再对混合气体进行加热至100℃。第(2)步中,焦炭颗粒以1.8kg/h的速度从所述装置的焦炭颗粒进料管1-2输入,高钛渣颗粒以36kg/h的速度从所述装置的钛渣颗粒进料管1-3输入到内流化床反应器2中,氯气以0.5m/s的速度从所述装置的气体缓冲罐29-1底面的气体进料管29-2输入到内流化床反应器2中,氧气和氮气的混合气体以0.2m/s的速度从所述装置的气体缓冲罐19-3底面的气体进料管19-4输入到外循环流化床1中。利用焦炭颗粒与所述的氧气和氮气混合气体反应放出的热量加热焦炭颗粒达到1000℃,用以保持所述内流化床反应器2内部温度为800℃,本发明装置在运行中的压力为0.1MPa。第(3)步中,收集在所述旋风分离器6上部的气体出口6-1滤出的气体,自然冷却后得到四氯化钛产品;收集从所述旋风分离器6下部的固体颗粒出料口6-3滤出的粉尘,经分离后再利用。最后经测定,含钛矿物的氯化率达到96%,经精制工序后,得到纯度为97%(质量分数)的四氯化钛。实施例6一种振动式内循环流化制备四氯化钛的方法,同实施例4,其中:第(1)步中,先对所述的固体原料分别通过21目的分离筛进行分筛,并按高钛渣颗粒的平均粒径∶焦炭颗粒的平均粒径之比1∶1.2,和按高钛渣颗粒的质量∶焦炭颗粒的质量比为1∶3的比例备料,分别加热高钛渣颗粒和焦炭颗粒至温度都为600℃。对所述气体原料中的氯气进行加热至500℃,对氧气和氮气先按氧气∶氮气的体积比为1∶0.5的比例进行混合,再 对混合气体进行加热至300℃。第(2)步中,焦炭颗粒以540kg/h的速度从所述装置的焦炭颗粒进料管1-2输入,高钛渣颗粒以180kg/h的速度从所述装置的钛渣颗粒进料管1-3输入到所述装置的内流化床反应器2中,氯气以3.5m/s的速度从所述装置的气体缓冲罐29-1底面的气体进料管29-2输入到所述的内流化床反应器2中,氧气和氮气的混合气体以1.5m/s的速度从所述装置的气体缓冲罐19-3底面的气体进料管19-4输入到所述的外循环流化床1中。利用焦炭颗粒与所述的氧气和氮气混合气体反应放出的热量加热焦炭颗粒达到1300℃,保持所述内流化床反应器2内部温度为1100℃,所述装置在运行中的压力为0.35MPa。第(3)步中,收集在所述旋风分离器6上部的气体出口6-1滤出的气体,自然冷却后得到四氯化钛产品;收集从所述旋风分离器6下部的固体颗粒出料口6-3滤出的粉尘,经分离后再利用。最后经测定,含钛矿物的氯化率达到97%,经精制工序后,得到纯度为98%(质量分数)的四氯化钛。