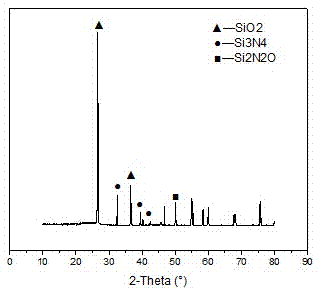
本发明涉及熔融石英陶瓷制备
技术领域:
,更具体地,涉及一种制备注凝成型熔融石英陶瓷的工艺方法。
背景技术:
:熔融石英陶瓷,具有热膨胀系数小、热稳定性好、电绝缘性好、耐化学侵蚀性好等众多优良的特性已广泛应用到各个领域,但形状复杂、尺寸要求精确的产品,其生产成本高、可靠性和生产重现性差、商业化生产的主要因素。研究表明,理想的解决办法是采用净尺寸成型工艺生产,而注凝成型就是这样一种接近净尺寸成型技术。注凝成型技术将传统的陶瓷工艺和有机聚合物化学结合,将高分子单体聚合的方法灵活的引入到陶瓷成型工艺,由于其工艺简单无需贵重设备、含脂量低,所制备的生柸可加工性能好,能真正实现近尺寸成型,但与其它结构陶瓷相比,注凝成型所得熔融石英陶瓷存在体积密度低和力学性能差的缺陷,这是由于烧结过程中有机单体的缺失,造成成型坯体体积密度低,气孔大所致,现有工艺研究表明,引入烧结助剂可以有效改进熔融石英陶瓷坯体致密度低的问题,其中最常用的烧结助剂为氮化硅,当前引入烧结助剂氮化硅的方式主要为机械添加氮化硅粉末,但是机械添加氮化硅在大工业生产中存在混合不均匀、以及烧结温度高易导致熔融石英晶化。因此,研究能在保证熔融石英陶致密度以及强度的情况下,同时防止熔融石英烧结成型过程析晶一直是本领域研究人员关注的重点。授权公告号为cn103342547b的发明专利,公开了一种制备高致密度熔融石英陶瓷的方法,先用盐酸作为正硅酸乙酯水解催化剂产生硅溶胶,然后加入超分散好的熔融石英粉末,通过搅拌实现表面同质溶胶的均匀包覆,包覆好的熔融石英陶瓷粉末经压制烧结后得到了致密度提高的熔融石英陶瓷,但是包覆过程中使用的催化剂盐酸,会引入难以清除的微量杂质氯,且通过搅拌实现溶胶对粉末均匀包覆,存在一定的局限性,难以适应工业化大生产要求。技术实现要素:本发明要解决的技术问题是针对现有制备熔融石英陶瓷技术不足,提供一种制备注凝成型熔融石英陶瓷的工艺方法。本发明的目的通过以下技术方案予以实现:提供一种制备注凝成型熔融石英陶瓷的工艺方法,包括以下步骤:s1.制备功能化熔融石英粉末:s2.料浆制备:取s1所得功能化熔融石英粉末,再将有机单体、交联剂、分散剂柠檬酸铵、引发剂和去离子水在搅拌下超声震荡制得料浆;s3.注凝固化:常温下将s2所得料浆注入模具,进行固化,脱模得到熔融石英陶瓷生柸;s4.烧结成型:将s3所得熔融石英陶瓷生柸,放入微波反应炉进行程序升温烧结成型;其中,s1所述功能化熔融石英粉末的制备包括以下步骤:s1-1.将熔融石英颗粒球磨成粉末得熔融石英粉;s1-2.配制一定浓度的糖溶液做为碳源,与步骤s1-1所得熔融石英粉以一定物质的量配比混合均匀,烘干;s1-3.将步骤s1-2所得混合物置于高温气氛炉中,在氮气保护下,进行糖热分解;s1-4.将步骤s1-3糖热分解所得粉末在真空条件下,通入氮气,进行碳热氮化还原反应;s1-5.将步骤s1-4碳热氮化还原反应所得粉末加热处理,得到所述功能化熔融石英粉。优选地,s1-2所述糖溶液可以为蔗糖溶液或者果糖溶液;所述糖溶液的浓度为0.35mol/l,素数糖溶液与熔融石英粉的摩尔配比为1:3,所述烘干温度为70~100℃,烘干时间为20~36h。更优选地,s1-2所述温度为80℃,烘干时间为36h。优选地,s1-2所述真空干燥箱温度控制程序设置为,以10℃/min的升温速率至600~900℃,后保温0.5~1h。更优选地,所述真空干燥箱温度控制程序设置为10℃/min的升温速率至700℃,后保温1h。优选地,s1-4所述烘氮气流速为不小于5l/min,所述碳热氮化还原反应采用微波炉作为反应容器,所述微波反应炉温度控制程序设置为,以10℃/min的升温速率至900~1100℃,后保温0.5~1.5h。更优选地,所s1-4所述烘氮气述流速为5l/min,,所述微波反应炉温度控制程序设置为,以10℃/min的升温速率至1050℃,后保温1.5h。优选地,s1-5所述高温处理温度为600℃,时间为2h。优选地,s2所述有机单体为n-羟甲基丙烯酰胺;交联剂为n,n’-亚甲基丙烯酰胺;分散剂为柠檬酸铵;引发剂为过硫酸铵;其中,n-羟甲基丙烯酰胺、n,n’-亚甲基丙烯酰胺、柠檬酸铵、过硫酸铵、四甲基乙二胺的用量分别为所述功能化熔融石英粉末质量的5%、0.05%、1.2%、0.5%、0.2%。优选地,s2所述几种组分的加入方式为:首先将交联剂与有机单体制备凝胶体系预混液,再加入分散剂、步骤s1所得熔融石英粉末,然后在进行超声搅拌的过程中,依次加入引发剂,搅拌150s,最后加入催化剂。优选地,s3所述固化条件为100℃下保温6h。优选地,所述微波反应炉加热程序设置600℃以下加热速率为2~5℃/min,至所需温度后保温3h。本发明同时提供所述制备注凝成型熔融石英陶瓷的工艺方法,制备得到的致密度提高以及力学性能增强的熔融石英陶瓷。本发明的有益效果:本发明创造性地利用热分解后的糖作为碳源,在氮气的氛围中,通过碳热氮化还原反应以熔融石英粉制备得到一种新的烧结助剂—功能化熔融石英粉。本发明以所述功能化熔融石英粉作为原料应用于熔融陶瓷制备成型,与机械加入氮化硅或者其它助剂相比,其可在基体中分布更加均匀,能获得致密度更好的熔融石英陶瓷,由于在功能化处理的过程中消耗粉末中的微量氧元素,可以在一定程度上抑制方石英的产生,同时运用蔗糖热分解后的碳做为碳源降低了氮还原反应温度,不仅获得了意想不到的技术效果,而且实现了低能耗和经济环保。应用所得功能化的熔融石英粉末经过料浆制备、注凝脱模、烧结成型步骤所得的熔融石英陶瓷致密度得到了显著提高,并且机械强度也得到了提升,所得陶瓷的致密度和室温抗弯折强度得到了提高,所得到的熔融石英陶瓷体积密度为1.96g/cm3、抗折强度达到了43.5mpa。本发明工艺方法操作简单稳定、节能高效且所用原料廉价易得环境友好,适合工业化生产。附图说明图1sio2-c-n体系反应自由焓△g随温度变化曲线图。图2sio2-c-n体系反应产物x射线衍射分析。图3蔗糖tg-dsc分析图。图4本发明蔗糖热分解后得到的sio2/c复合粉末的电镜扫描图。图5经hf处理后蔗糖热分解后得到的sio2/c复合粉末的电镜扫描图。图6本发明氮化反应后所得粉末的x射线衍射分析结果。图7本发明氮化反应后所得粉末的傅里叶红外光谱仪图。图8本发明产物的能谱分析图。具体实施方式下面结合附图和具体实施例进一步详细说明本发明。除非特别说明,本发明实施例使用的各种原料均可以通过常规市购得到,或根据本领域的常规方法制备得到,所用设备为实验常用设备。除非另有定义或说明,本文中所使用的所有专业与科学用语与本领域技术熟练人员所熟悉的意义相同。实施例1在石英陶瓷成型中机械加入一定量的氮化硅粉末能有效改进熔融石英陶瓷致密性,其基本原理主要是氮化硅在烧结过程中,会被氧气氧化,生成液相的二氧化硅从而填充基体的孔隙,达到致密化,同时由于氮元素可以降低熔融石英粉末的氧含量,从而可以在一定程度下抑制熔融石英粉末析晶。基于以上理论基础,本发明创造性地改变机械加入的方式,以熔融石英粉末为主要原料,让其原位自生预处理引进氮元素,其存在的化合物形式可能是氮化硅或者氧氮硅,采用热力学计算软件hsc5.0可计算可得,sio2-c-n体系的碳热氮化反应中,可能存在以下化学反应:3sio2(s)+3c(s)+2n2(g)=si3n4(s)+3co2(g)(1)3sio2(s)+6c(s)+2n2(g)=si3n4(s)+6co(g)(2)sio2(s)+2c(s)=sic(s)+co2(g)(3)sio2(s)+3c(s)=sic(s)+2co(g)(4)2sio2(s)+3c(s)+n2(g)=si2n2o(s)+3co(g)(5)采用热力学计算软件hsc5.0可计算出反应方程式(1)-(5)的温度-自由焓,结果如附图1所示:从温度-反应自由焓的曲线图可以知道,反应(1)、反应(3)吉布斯自由能都大于0,说明不发生反应,其中反应(2)、反应(4)、反应(5)均随着温度的升高反应驱动力增大,其中反应(2)、反应(4)、反应(5)在1400~1600之间吉布斯自由能小于0,意味着此温度区间反应开始进行。碳热还原氮化反应影响因素主要是温度和氮气分压,这些反应的进行不仅要满足热力学条件,还需要满足动力学条件。其反应可以看做sio2先被c还原:sio2(s)+c(s)=sio(g)+co(g)。本发明的主要目的是引进氮元素,所以一定要避免sic的产生,相关文献研究结果表明,sic的生成要求sio的气体分压大于一定数值(约0.1~1kpa)。而在氮气气氛中,因为sio气体一般与氮气优先发生如下反应:3sio(g)+3c(s)+2n2(g)=si3n4(s)+3co(g),所以在保证氮气充足的情况下,sic在1400~1600℃也很难产生。在上述理论原理的基础上进行实际实验总结和分析:采用石墨粉作为碳源,与二氧化硅一起装入石墨坩埚,以sic片作为辅热,放入微波反应炉,然后抽真空,以5l/min动态流量通氮气、保证反应具有充足的氮气,以10℃/min的升温速率升至1200℃,保温90min,对所得产物进行x射线衍射分析,结果如图2所示,可知:有一定量的氮化硅和氧氮硅生成,并且未能检测到碳化硅的存在,说本发明制备方法理论原理成立。为了方便说明,本发明以蔗糖溶液进行说明。为了确定蔗糖热分解的温度,采用tg-dsc分析对蔗糖在碳化的过程中质量的变化和吸热放热的的情况蔗糖进行了分析,结果如图3所示,可以看出:(1)从室温到225℃,质量有少量的减少,同时伴随着一个较宽的吸热峰,说明在这个温度范围内,有少量的自由水蒸发;(2)从225℃到395℃,质量有非常明显地减少,失重率约49%,同时对应有一个较尖锐的吸热峰,说明在这个温度范围内蔗糖已经开始发生化学反应,释放出大量结合水而使得质量减少,即已经开始碳化;(3)从395℃到600℃的温度范围内,失重的比较缓慢,说明热解反应基本完成,其中失重率约10%,当温度高于600℃以后,质量几乎保持不变,说明碳化已基本完成,因此,蔗糖热分解温度须高于600℃。本实施例提供一种用于石英陶瓷制备的功能化熔融石英粉的制备方法,包括以下步骤:s1.用球磨机将熔融石英球磨成粉末,取能过200目筛的粉末备用;s2.取蔗糖342g溶于200ml去离子水中,然后在搅拌的情况下向蔗糖溶液中缓慢加入步骤s1所得熔融石英粉180g,混合均匀,置于干燥箱中,80℃下进行烘干36h,冷却,放入坩埚中;s3.将坩埚置于高温气氛炉中,在氮气的保护下,以10℃/min的升温速率加热至700℃,后保温1h,进行蔗糖热分解,将所得粉末冷却备用;s4.将s3所得熔融石英粉末,置于微波反应炉中,先抽真空后,以5l/min的速度通氮气,一段时间后,以10℃/min的升温速率加热至1050℃进行碳热还原反应,1.5h后冷却取出;s5.将s4所得熔融石英粉末,放入马弗炉中进行加热处理,炉门不完全封闭,在600℃处理2h,去除反应剩余的碳,得到功能化熔融石英粉。实施例2用球磨机将熔融石英球磨成粉末,取能过200目筛的粉末备用,取蔗糖342g溶于200ml去离子水中,然后在搅拌的情况下向蔗糖溶液中缓慢加入熔融石英粉,其它条件和实施例1相同,不同的是碳热还原以10℃/min的升温速率加热至900℃进行碳热还原反应。实施例3用球磨机将熔融石英球磨成粉末,取能过200目筛的粉末备用,取蔗糖342g溶于200ml去离子水中,然后在搅拌的情况下向蔗糖溶液中缓慢加入熔融石英粉,其它条件和实施例1相同,不同的是碳热还原以10℃/min的升温速率加热至950℃进行碳热还原反应。实施例4用球磨机将熔融石英球磨成粉末,取能过200目筛的粉末备用,取蔗糖342g溶于200ml去离子水中,然后在搅拌的情况下向蔗糖溶液中缓慢加入熔融石英粉,其它条件和实施例1相同,不同的是碳热还原以10℃/min的升温速率加热至1000℃进行碳热还原反应。实施例5用球磨机将熔融石英球磨成粉末,取能过200目筛的粉末备用,取蔗糖342g溶于200ml去离子水中,然后在搅拌的情况下向蔗糖溶液中缓慢加入180g熔融石英粉,其它条件和实施例1相同,不同的是碳热还原以10℃/min的升温速率加热至1100℃进行碳热还原反应。实施例6功能化熔融石英粉的分析(1)蔗糖热分解反应产物分析采用型号为日本电子jsm-6510的扫描电镜对实施例1~5任一实施例蔗糖热分解所得熔融石英粉及其经hf酸洗后熔融粉末进行电镜扫描,图4、5分别为hf酸洗前、后熔融石英粉电镜扫描图,可以看出粉末非常均匀与致密,基本完全接触,经过hf酸洗后的电镜扫描图中,可以看出出现了均匀的孔隙,其孔隙应该就是为被hf洗掉的二氧化硅,从图4、图5均可以看出,得到的sio2/c复合粉末非常均匀,蔗糖碳化后得到的碳粉与二氧化硅接触的很彻底。(2)氮化反应产物分析采用日本rigaku,uitima-iv型号x射线衍射仪对实施例1~5氮化反应后的x射线衍射分析,结果如图6所示,从图6可以看出在实施例1、实施例3、实施例4均未检测到新物质的晶相,这种结果一般有两种情况,一种就是在此工艺条件下,并没有新的晶相产生,另一种情况就是,有新的物质产生但是由于其含量太低用x射线衍射未能检测出来。在实施例5二氧化硅有点微量的转化成方石英,且有一定量的氮化硅晶相产生。图7为傅里叶变换红外光谱仪,nicolet380,美国赛默飞科技公司,对不同温度下产物的傅里叶红外光谱分析图,其中红外光谱检测采用kbr压片。从图7可以看出,在实施例3、实施例4中并未检测到新的化学键,实施例1产物的红外光谱图可以明显在波长800~1100cm-1之间有一尖锐的峰,由氮化硅红外光谱文献可知,在800cm-1100cm-1中一强锐的吸收峰为si-n键的骨架振动。说明在实施例1的工艺条件下,熔融石英并未转化成方石英,同时微量引入了氮元素。氮元素可能以氮化硅的形式存在,也可能以氧氮硅的形式存在,不管其以哪种方式存在,其均能在成型过程中提高成型坯体的致密性。采用型号为日本电子jsm-6510的电镜扫描对实施例1的产物进行的能谱分析图,从图8可以看出经过预处理后的粉末含有氮元素,且多余的碳元素已经基本去除。实施例7提供一种制备注凝成型熔融石英陶瓷致密度的工艺方法,包括以下步骤:s1.准备好实施例1~5任一例所制备得到的功能化熔融石英粉末;s2.料浆制备:首先将交联剂剂n,n’-亚甲基丙烯酰胺0.9g与有机单体n-羟甲基丙烯酰胺9g溶于适量去离子水中制备凝胶体系预混液,再加入分散剂柠檬酸铵2.16g、步骤s1所得熔融石英粉末180g,得到固相含量为65%的料浆料浆,然后在进行超声搅拌的过程中,依次加入引发剂过硫酸铵0.9g,搅拌150s后,最后加入催化剂适量,超声震荡0.5h;s3.注凝固化:常温下将所得料浆注入模具,放入干燥箱在100℃下保温6h进行固化,脱模,得熔融石英陶瓷生柸;s4.烧结成型:将所得熔融石英陶瓷生柸,放入微波反应炉进行程序升温烧结成型,加热程序设置600℃以下加热速率为5℃/min,至1050℃后保温3h,冷却取出即得注凝成型熔融石英陶瓷。将所得成型样进行体积密度和抗折强度测试,所得熔融石英陶瓷体积密度为1.96g/cm3,抗折强度为43.5mpa。实施例8~实施例18其它工艺操作与实施例7相同,不同的工艺参数如表1所示,以及所得注凝成型熔融石英陶瓷的性能检测结果,如表2所示。表1不同工艺条件n-羟甲基丙烯酰胺/g柠檬酸铵/g过硫酸铵/g实施例87.21.800.54实施例97.22.160.72实施例107.22.250.90实施例119.01.800.72实施例129.02.161.08实施例139.02.250.54实施例1410.81.800.90实施例1510.82.160.54实施例1610.82.250.72实施例1710.81.801.08实施例187.22.161.081表2不同工艺条件所得注凝成型熔融石英陶瓷的性能检测结果体积致密/(g/cm3)抗折强度/mpa实施例81.8037.9实施例91.8538.2实施例101.8738.6实施例111.8939.7实施例121.9240.2实施例131.9340.6实施例141.9442.5实施例151.9543.0实施例161.9342.7实施例171.9241.2实施例181.8338.1当前第1页12