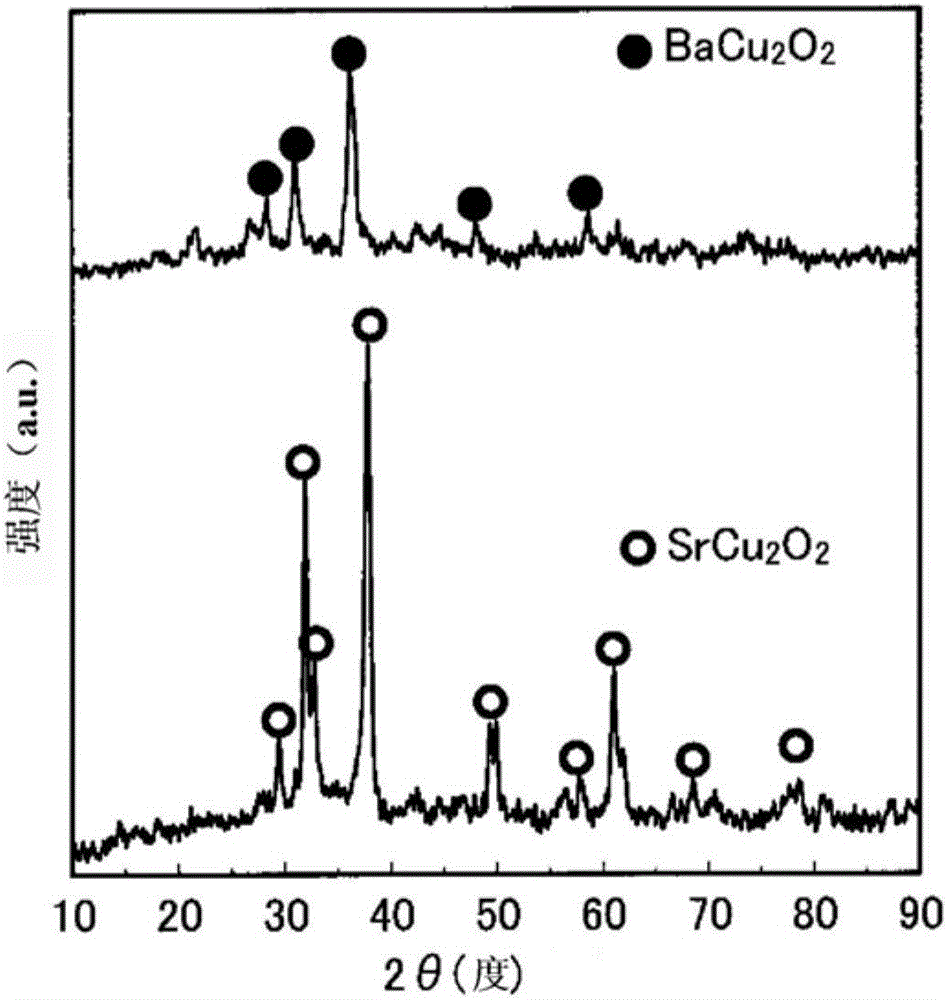
本发明涉及一种使用热电浆焰的以一般式MCu2O2表示的(M为Sr、Ba中的至少1种)且包含铜的金属复合氧化物微粒子及其制造方法。特别涉及可容易且确实地制造具有透明性的粒状的金属复合氧化物微粒子的金属复合氧化物微粒子的制造方法。
背景技术:
现在,各种微粒子使用于各种用途中。例如,金属微粒子、氧化物微粒子、氮化物微粒子、碳化物微粒子等微粒子用于半导体基板、印刷基板、各种电绝缘零件等电绝缘材料、切削工具、铸模、轴承等高硬度高精度的机械工作材料、晶界电容器、湿度感测器等功能性材料、精密烧结成形材料等烧结体的制造、发动机阀等要求高温耐磨耗性的材料等熔射零件制造、燃料电池的电极、电解质材料及各种触媒等领域,进而在半导体的领域中使用。
作为使用上述的微粒子,例如,专利文献1中记载一种氧化物半导体电极,其粒径为0.1nm~1000nm,由包含Cu、Al、Ag、Ni、Co、In、Fe、Zn、Rh、Ga、Sr、Li、N中的任一种的p型无机氧化物半导体构成,且p型无机氧化物半导体的一部分具有纤维结构。专利文献1的p型无机氧化物半导体电极是以沉淀法或溶胶-凝胶法制作的。
现有技术文献
专利文献
专利文献1:日本特开2006-66215号公报
技术实现要素:
发明要解决的问题
在专利文献1中记载了p型无机氧化物半导体电极是以沉淀法或溶胶-凝胶法制作的,其中一部分具有纤维结构。然而,专利文献1中没有公开任何关于可分散状态的p型无机氧化物半导体的粒子,也没有揭示可分散状态的p型无机氧化物半导体的粒子的具体的制造方法。并且,在专利文献1中,作为p型无机氧化物半导体可列举:CuO、Cu2O、CuGaO2、ZnRh2O4、NiO、CoO、CuAlO2、SrCu2O2、NiO:Li、CuO:Li、Cu2O:Li、CuO:Li、ZnO:In:N、ZnO:Be:N。在这些p型无机氧化物半导体中也可以包含如CuO、NiO、CoO等无透明性的物质。目前并无具有透明性且粒状的p型无机氧化物半导体的粒子。
本发明的目的是,消除基于前述现有技术的问题,而提供一种金属复合氧化物微粒子,该金属复合氧化物微粒子具有透明性,且其粒度分布宽度窄,具有均一的粒径,是几乎无1μm以上的粗大粒子的混入的粒状的p型无机氧化物半导体的微粒子;并提供可容易且确实地制造该金属复合氧化物微粒子的金属复合氧化物微粒子的制造方法。
用于解决问题的手段
为了达成上述目的,本发明提供一种金属复合氧化物微粒子,其是以一般式MCu2O2表示的包含铜的金属复合氧化物微粒子,其特征为,M为Sr及Ba中的至少1种碱土金属,粒径为1~100nm,且具有透明性。在此,M也可以进一步包含Mg及Ca中的至少1种第2族元素。
本发明提供一种金属复合氧化物微粒子的制造方法,其特征为,具有以下步骤:将铜化合物的粉末与包含Sr及Ba中的至少1种碱土金属的碱土金属化合物的粉末进行前处理的前处理步骤、以及使用热电浆焰使经前处理的铜化合物的粉末及碱土金属化合物的粉末生成具有透明性的粒状的金属复合氧化物微粒子的生成步骤,热电浆焰来自于惰性气体。
在此,优选地,前处理步骤包含使用载体气体使铜化合物的粉末与碱土金属化合物的粉末分散的步骤;生成步骤具有将经分散的铜化合物的粉末及碱土金属化合物的粉末供给至热电浆焰中的步骤。
另外,优选地,前处理步骤包含使铜化合物的粉末与碱土金属化合物的粉末分散在水中而成为浆体的步骤;生成步骤具有使浆体液滴化而供给至热电浆焰中的步骤。
例如,惰性气体为氦气、氩气及氮气中的至少1种。
另外,碱土金属化合物的粉末可进一步含有:包含Mg及Ca中的至少1种第2族元素的化合物。
发明的效果
依据本发明,可以提供一种金属复合氧化物微粒子,其具有透明性,且其粒度分布宽度窄,具有均一的粒径,是几乎无1μm以上的粗大粒子的混入的粒状的p型无机氧化物半导体的微粒子。
并且,依据本发明,可以容易且确实地制造具有透明性的粒状的金属复合氧化物微粒子。
附图说明
图1为显示本发明的实施形态的金属复合氧化物微粒子的制造方法中所使用的微粒子制造装置的示意图。
图2为显示金属复合氧化物微粒子通过X射线衍射法所得到的解析结果的图表。
图3为显示金属复合氧化物微粒子的图面代用照片。
图4为显示金属复合氧化物微粒子通过X射线衍射法所得到的解析结果的图表。
图5为显示金属复合氧化物微粒子通过X射线衍射法所得到的解析结果的图表。
图6为显示组成的比率不同的金属复合氧化物微粒子通过X射线衍射法所得到的解析结果的图表。
图7为显示组成的比率不同的金属复合氧化物微粒子通过X射线衍射法所得到的解析结果的图表。
图8为图7的重要部分放大图。
图9为显示金属复合氧化物微粒子的光学特性的图表。
附图标记
10微粒子制造装置 12电浆炬 14材料供给装置 15 1次微粒子 16腔室
18微粒子(2次微粒子) 19旋风器 20回收部 22电浆气体供给装置
24热电浆焰 28气体供给装置
具体实施方式
以下,根据附图所示的较佳实施形态,来详细地说明本发明的金属复合氧化物微粒子及其制造方法。
图1为显示本发明的实施形态的金属复合氧化物微粒子的制造方法中所使用的微粒子制造装置的示意图。
图1所示的微粒子制造装置(以下,简称为制造装置)10为金属复合氧化物微粒子的制造所使用的装置。
制造装置10具有:电浆炬12、材料供给装置14、腔室16、旋风器19、以及回收部20,该电浆炬12用来产生热电浆;该材料供给装置14将金属复合氧化物微粒子的制造用材料供给至电浆炬12内;该腔室16具有作为用以生成氧化亚铜的1次微粒子15的冷却槽的功能;该旋风器19将具有任意规定的粒径以上的粒径的粗大粒子从所生成的金属复合氧化物微粒子的1次微粒子15去除;该回收部20将经旋风器19分级后的具有所期望的粒径的金属复合氧化物微粒子的2次微粒子18进行回收。关于材料供给装置14、腔室16、旋风器19、回收部20可使用例如日本特开2007-138287号公报中所记载的各种装置。
在本实施形态中,金属复合氧化物微粒子的制造可使用铜化合物的粉末与包含Sr及Ba中的至少1种碱土金属的碱土金属化合物的粉末。
为了使铜化合物的粉末在热电浆焰中容易蒸发,可适当设定其平均粒径,但平均粒径为例如100μm以下,优选为10μm以下,更优选为3μm以下。作为该铜化合物的粉末可使用例如:氧化铜(CuO)、氢氧化铜(Cu(OH)2)、)硫酸铜(CuSO4)、硝酸铜(Cu(NO3)2)及过氧化铜(Cu2O3、CuO2、CuO3)的粉末。
作为包含Sr及Ba中的至少1种碱土金属的碱土金属化合物的粉末可使用例如:碳酸锶(SrCO3)、碳酸钡(BaCO3)。
碱土金属化合物的粉末可进一步含有:包含Mg及Ca中的至少1种第2族元素的化合物。具体而言为碳酸镁(MgCO3)、碳酸钙(CaCO3)。
以下,碱土金属化合物是指包含Sr及Ba中的至少1种碱土金属的化合物,或者包含该等碱土金属的化合物,除此之外,进一步包含Mg及Ca中的至少1种第2族元素的化合物。
并且,这种碱土金属化合物的粉末的平均粒径为例如100μm以下,优选为10μm以下,更优选为3μm以下。上述的碱土金属化合物的粉末的平均粒径可以BET法进行测定。
电浆炬12由石英管12a与围绕其外侧的高频振荡用线圈12b构成。在电浆炬12的上部在其中央部设有供给管14a,该供给管14a用以将铜化合物的粉末及上述碱土金属化合物的粉末以粉末或者浆体的形态供给至电浆炬12内。电浆气体供给口12c形成于供给管14a的周边部(同一圆周上),电浆气体供给口12c为环状。
电浆气体供给装置22是将电浆气体供给至电浆炬12内的装置。该电浆气体供给装置22具有气体供给部(未图示),气体供给部经由配管22a连接于电浆气体供给口12c。在气体供给部设有用以调整各供给量的阀等供给量调整部(未图示)。
电浆气体从电浆气体供给装置22经过电浆气体供给口12c供给至电浆炬12内。电浆气体可使用惰性气体。作为惰性气体可使用例如氦气、氩气及氮气中的至少1种气体。
例如,在气体供给部中储存例如氦气、氩气及氮气中的至少1种气体。从电浆气体供给装置22的气体供给部,将作为电浆气体的氦气、氩气及氮气中的至少1种气体经由配管22a,并经过环状的电浆气体供给口12c,从箭头P指示的方向供给至电浆炬12内。接着,对高频振荡用线圈12b施加高频电压,而在电浆炬12内产生热电浆焰24。
另外,电浆气体为氦气、氩气及氮气中的至少1种气体即可,并不限定于单质,也可以将该等组合使用。作为电浆气体,例如,可将氩气与氮气组合使用。
热电浆焰24的温度必须高于铜化合物的粉末及上述碱土金属化合物的粉末的沸点。另一方面,虽然热电浆焰24的温度越高则越容易使铜化合物的粉末及碱土金属化合物的粉末成为气相状态,因而为佳,但温度并无特别限定。例如,可以将热电浆焰24的温度设为6000℃,理论上认为可达到10000℃左右。
并且,电浆炬12内的压力环境优选为大气压以下。在此,关于大气压以下的环境无特别限定,例如为0.5-100kPa。
另外,石英管12a的外侧被形成为同心圆状的管(未图示)所包围,使冷却水在此管与石英管12a之间循环来将石英管12a进行水冷却,而防止由于电浆炬12内所产生的热电浆焰24使石英管12a变得过于高温。
材料供给装置14经由供给管14a连接在电浆炬12的上部。作为材料供给装置14,例如,可使用将铜化合物的粉末及碱土金属化合物的粉末以粉末的形态进行供给、和以含有铜化合物的粉末及碱土金属化合物的粉末的浆体的形态进行供给的2种方式。
作为将铜化合物的粉末及碱土金属化合物的粉末以粉末的形态进行供给的材料供给装置14,例如,可使用日本特开2007-138287号公报所公开的装置。在该情况下,材料供给装置14,例如,具有:储存槽(未图示)、螺旋进料机(未图示)、分散部(未图示)、以及载体气体供给源(未图示),该储存槽用来储存铜化合物的粉末及碱土金属化合物的粉末;该螺旋进料机用来定量搬运铜化合物的粉末及碱土金属化合物的粉末;该分散部在由螺旋进料机所搬运的铜化合物粉末及碱土金属化合物的粉末被最后散布之前,使其分散为一次粒子的状态。
铜化合物的粉末及碱土金属化合物的粉末与从载体气体供给源被施加挤压压力的载体气体一起经由供给管14a被供给至电浆炬12内的热电浆焰24中。
材料供给装置14只要能够防止铜化合物的粉末及碱土金属化合物的粉末的凝聚,并在维持分散状态下,将铜化合物的粉末及碱土金属化合物的粉末散布于电浆炬12内,则其构造并无特别限定。载体气体,例如,可与上述电浆气体相同地使用惰性气体。载体气体流量可使用浮子式流量计来进行控制。并且,载体气体的流量值为流量计的刻度值。
将铜化合物的粉末以浆体的形态进行供给的材料供给装置14,例如,可使用日本特开2011-213524号公报所公开的装置。在该情况下,材料供给装置14具有:容器(未图示)、搅拌机(未图示)、泵(未图示)、以及喷雾气体供给源(未图示),该容器用来装浆体(未图示);该搅拌机用来搅拌容器中的浆体;该泵(未图示)用以经由供给管14a来对浆体施加高压而供给至电浆炬12内;该喷雾气体供给源用来供给用以使浆体液滴化而供给至电浆炬12内的喷雾气体。喷雾气体供给源相当于载体气体供给源。喷雾气体电称为载体气体。
在本实施形态中,在将铜化合物的粉末及碱土金属化合物的粉末以浆体的形态进行供给的情况中,使铜化合物的粉末及碱土金属化合物的粉末分散于水中制成浆体,并使用该浆体来制造金属复合氧化物微粒子。
另外,浆体中的铜化合物的粉末及碱土金属化合物的粉末与水的混合比并无特别限定,例如,以质量比计为5∶5(50%:50%)。
在使用将铜化合物的粉末及碱土金属化合物的粉末以浆体的形态进行供给的材料供给装置14的情况中,将从喷雾气体供给源施加挤压压力的喷雾气体与浆体一起经由供给管14a供给至电浆炬12内的热电浆焰24中。供给管14a具有用以将浆体喷雾至电浆炬内的热电浆焰24中并予以液滴化的双流体喷嘴机构,藉此,能够将浆体喷雾至电浆炬12内的热电浆焰24中,即,使浆体液滴化。与载体气体相同地,例如,喷雾气体可与上述的电浆气体相同地使用惰性气体。
因此,双流体喷嘴机构可以对浆体施加高压,并通过作为气体的喷雾气体(载体气体)将浆体进行喷雾,并用作使浆体液滴化的方法之一。
另外,并不限定于上述的双流体喷嘴机构,也可以使用单流体喷嘴机构。进而,作为其他方法,可列举例如:使浆体以一定速度落下至旋转中的圆板上,并通过离心力予以液滴化(形成液滴)的方法、对浆体表面施加高的电压予以液滴化(产生液滴)的方法等。
腔室16邻接设置于电浆炬12的下方。被供给至电浆炬12内的热电浆焰24中的铜化合物的粉末及碱土金属化合物的粉末蒸发而成为气相状态,铜化合物与碱土金属化合物反应而成为金属复合氧化物微粒子。然后,通过冷却气体在腔室16内急速冷却而生成1次微粒子15(金属复合氧化物微粒子)。腔室16也具有作为冷却槽的功能。
气体供给装置28经由配管28a连接到腔室16上。气体供给装置28具有:气体供给部(未图示)及压缩机、鼓风机等的压力赋予手段(未图示),该气体供给部用来储存供给至腔室16内的冷却气体;该压力赋予手段用来对来自气体供给部的冷却气体施加挤压压力。并且,在气体供给装置28上设有用来控制来自气体供给部的气体供给量的压力控制阀28b。
作为冷却气体,例如,可与上述的电浆气体相同地使用惰性气体。例如,在气体供给部中储存氮气。
气体供给装置28朝向热电浆焰24的尾部,即与电浆气体供给口12c相反侧的热电浆焰24的一端(热电浆焰24的终端部),以特定的角度,例如,沿箭头Q的方向,供给例如氮气作为冷却气体,并且沿着腔室16的侧壁从上方朝向下方,即沿图1所示的箭头R的方向供给冷却气体。该冷却气体的流量,例如,可以使用浮子式流量计来进行控制。冷却气体的流量值为该流量计的刻度值。
另外,从气体供给装置28所供给的冷却气体除了具有将在上述的腔室16内所生成的金属复合氧化物微粒子急速冷却而成为1次微粒子15的作用以外,也具有有益于旋风器19中的1次微粒子15的分级等附加作用。
在材料供给装置14为粉末的形态进行供给的情况下,从材料供给装置14与载体气体一起被供给至电浆炬12内的铜化合物的粉末及碱土金属化合物的粉末在热电浆焰24中成为气相状态。通过从气体供给装置28朝向热电浆焰24沿箭头Q的方向供给的氮气进行急速冷却,生成金属复合氧化物微粒子的1次微粒子15。此时,通过沿箭头R的方向供给的氮气可以防止1次微粒子15附着于腔室16内壁。藉此,生成的1次微粒子15的产率提高。
基于上述内容,关于冷却气体,在生成金属复合氧化物微粒子的1次微粒子15的过程中,必须有将所得到的金属复合氧化物微粒子急速冷却的充分的供给量,同时,得到能够将1次微粒子15在下游的旋风器19中以任意分级点分级的流速,且不妨碍热电浆焰24的稳定的程度的量为佳。并且,只要不妨碍热电浆焰24的稳定,冷却气体的供给方法及供给位置等并无特别限定。在本实施形态的微粒子制造装置10中,虽然在顶板17上形成圆周状的缝隙来供给冷却气体,但只要是在从热电浆焰24至旋风器19的路径上,能够确实地供给气体的方法或位置,即使为其他的方法、位置也无妨。
沿箭头Q的方向供给的氮气及沿箭头R的方向供给的氮气的合计的量以设为供给至上述热电浆焰24中的气体的200体积%-5000体积%为佳。在此,供给至上述热电浆焰24中的气体是指形成热电浆焰24的电浆气体和用来形成电浆流的中央气体及喷雾气体混合而成的气体。
在材料供给装置14以浆体的形态进行供给的情况下,从材料供给装置14使用特定流量的喷雾气体供给至电浆炬12内的含有铜化合物的粉末及碱土金属化合物的粉末的液滴化后的浆体,通过热电浆焰24而成为气相状态,铜化合物与碱土金属化合物会进行反应而生成金属复合氧化物微粒子。接着,由铜化合物的粉末及碱土金属化合物的粉末所形成的金属复合氧化物微粒子,通过朝向热电浆焰24并沿箭头Q的方向供给的冷却气体,该金属复合氧化物微粒子在腔室16内急速冷却而生成金属复合氧化物微粒子的1次微粒子15。此时,通过沿箭头R的方向供给的氩气可以防止1次微粒子15附着于腔室16的内壁。在该情况中,通过沿箭头R的方向供给的氩气而使生成的1次微粒子15的产率提高。
如图1所示,在腔室16的侧方下部设有用于将所生成的1次微粒子15以所期望的粒径进行分级的旋风器19。该旋风器19具备有:入口管19a、圆筒形状的外筒19b、圆锥台部19c、粗大粒子回收腔室19d、以及内管19e;入口管19a从腔室16供给1次微粒子15;圆筒形状的外筒19b与该入口管19a连接,且位于旋风器19的上部;该圆锥台部19c从该外筒19b下部朝向下侧连续且直径渐渐缩减;该粗大粒子回收腔室19d连接在该圆锥台部19c下侧,且用来将具有上述的所期望的粒径以上的粒径的粗大粒子进行回收;该内管19e连接在之后详述的回收部20,且突出设置于外筒19b。
在腔室16内所生成的1次微粒子15从旋风器19的入口管19a进入,包含有在腔室16内所生成的1次微粒子15的气流会沿着外筒19b内周壁被吹入,藉此,该气流会如图1中的箭头T所示从外筒19b的内周壁朝向圆锥台部19c方向流动,藉此而形成下降的旋流。
接着,当使上述下降的旋流反转,成为上升流时,由于离心力与阻力的平衡,粗大粒子无法跟着上升流,而沿着圆锥台部19c侧面下降,被粗大粒子回收腔室19d所回收。并且,相较于离心力更会受到阻力的影响的微粒子会随着在圆锥台部19c内壁的上升流一起从内管19e被排出系统外。
并且,通过内管19e而从之后详述的回收部20产生负压(吸引力)。接着,从上述的回旋的气流分离后的金属复合氧化物微粒子会如符号U所示地被该负压(吸引力)吸引,并通过内管19e被送至回收部20。
在旋风器19内的气流的出口即内管19e的延长上设有回收部20,该回收部20用于回收具有所期望的纳米等级的粒径的金属复合氧化物微粒子的2次微粒子18。该回收部20具备:回收室20a、设置在回收室20a内的过滤器20b、以及经由设置于回收室20a内下方的管连接的真空泵(未图示)。从旋风器19送出的微粒子会被真空泵(未图示)所吸引,藉此而被引入回收室20a内,并成为停留在过滤器20b的表面的状态而被回收。
以下,针对使用上述制造装置10的金属复合氧化物微粒子的制造方法,以及通过该制造方法所生成的金属复合氧化物微粒子进行说明。
在本实施形态中,材料供给例如可使用将铜化合物的粉末及碱土金属化合物的粉末以粉末的形态进行供给、以及将铜化合物的粉末及碱土金属化合物的粉末以浆体的形态进行供给的2种方式。针对以各材料供给方式所进行的金属复合氧化物微粒子的制造方法进行说明。
首先,在以粉末的形态进行供给的情况中,将作为铜化合物的粉末例如平均粒径为5μm以下的铜化合物的粉末与碱土金属化合物的粉末以例如质量比计为5∶5投入材料供给装置14。
电浆气体使用例如氩气与氮气,对高频振荡用线圈12b施加高频电压,使电浆炬12内产生热电浆焰24。
并且,从气体供给装置28将氮气沿箭头Q的方向供给至热电浆焰24的尾部即热电浆焰24的终端部。此时,沿箭头R的方向也供给氮气。
接着,将使用例如氩气作为载体气体对铜化合物的粉末及碱土金属化合物的粉末进行气体搬运,并经由供给管14a供给至电浆炬12内的热电浆焰24中。以热电浆焰24使铜化合物的粉末与碱土金属化合物的粉末蒸发而成为气相状态,铜化合物与碱土金属化合物反应而成为金属氧化物微粒子。此时,在腔室16内金属复合氧化物微粒子被冷却气体急速冷却而生成金属复合物微粒子的1次微粒子15。
在腔室16内所生成的金属复合氧化物微粒子的1次微粒子15从旋风器19的入口管19a,与气流一起沿着外筒19b的内周壁被吹人,藉此,该气流如图1的箭头T所示沿着外筒19b的内周壁流动,藉此而形成旋流下降。接着,当上述下降的旋流反转成为上升流时,通过离心力与阻力的平衡,粗大粒子并无法跟着上升流,而沿着圆锥台部19c侧面下降,被粗大粒子回收腔室19d所回收。并且,相较于离心力更会受到阻力的影响的微粒子会随着在圆锥台部19c内壁的上升流一起从内管19e被排出至系统外。
被排出的金属复合氧化物微粒子的2次微粒子18被来自回收部20的负压(吸引力)朝向图1中符号U所示的方向吸引,通过内管19e送至回收部20,而被回收部20的过滤器20b所回收。此时的旋风器19内的内压较佳为大气压以下。并且,金属复合氧化物微粒子的2次微粒子18的粒径根据需要可规定为纳米等级的任意的粒径。
如此一来,在本实施形态中,仅将铜化合物的粉末及碱土金属化合物的粉末进行电浆处理即可容易且确实地得到纳米等级的具有透明性的粒状的金属复合氧化物微粒子。
另外,作为金属复合氧化物微粒子,例如,可制作SrCu2O2粒子、BaCu2O2粒子。这些均是p型半导体,且透过率高,具有透明性,即所谓的p型的透明氧化物半导体。如此一来,能够得到具有透明性的粒状的p型的透明氧化物半导体粒子。
在本发明中,具有透明性是指波长350-700nm的可见光区域的平均透过率比波长超过300nm且未达350nm的紫外线区域的平均透过率更高。在上述的专利文献1中记载的CuO、NiO、CoO的p型无机氧化物半导体中,可见光区域的平均透过率与紫外线区域的平均透过率相同程度,并不高于紫外线区域的平均透过率。
通过本实施形态的金属复合氧化物微粒子的制造方法所制造的金属复合氧化物微粒子,其粒度分布宽度窄,即具有均一的粒径,且几乎无μm以上的粗大粒子的混入,具体而言,其平均粒径为1-100nm左右的纳米等级的金属复合氧化物微粒子。
接着,针对以浆体的形态进行供给的情况进行说明。
在该情况下,例如,使用平均粒径为5μm以下的铜化合物的粉末,使用碱土金属化合物的粉末,使用例如水作为分散介质。将铜化合物的粉末与碱土金属化合物的粉末的合计与水的混合比设为以质量比计为5∶5(50%:50%),而制作浆体。
将浆体装入图1所示的材料供给装置14的容器(未图示)内,并以搅拌机(未图示)进行搅拌。藉此,防止水中的铜化合物的粉末与碱土金属化合物的粉末沉淀,并维持水中的铜化合物的粉末与碱土金属化合物的粉末为被分散的状态的浆体。另外,也可以向材料供给装置14供给铜化合物的粉末、碱土金属化合物的粉末和水而连续地调制浆体。
接着,使用前述的双流体喷嘴机构(未图示)使浆体液滴化,并使用特定的流量的喷雾气体来将液滴化后的浆体供给至在电浆炬12内所产生的热电浆焰24中。含有铜化合物的粉末及碱土金属化合物的粉末的液滴化后的浆体通过热电浆焰24而成为气相状态,铜化合物与碱土金属化合物发生反应而生成金属复合氧化物微粒子。此时,由铜化合物的粉末及碱土金属化合物的粉末所形成的金属复合氧化物微粒子,会被沿箭头Q的方向供给的氮气急速冷却,并通过在腔室16内被急速冷却而得到1次微粒子15。
另外,在电浆炬12内的压力环境较佳为大气压以下。在此,虽然对大气压以下的环境无特别限定,但可以设为例如660Pa~100kPa。
最终,在腔室16内所生成的金属复合氧化物微粒子的1次微粒子15经过与以上述的粉末的形态所制作的相同的过程。
接着,与以上述的粉末的形态所制作的相同,被排出的金属复合氧化物微粒子的2次微粒子18被来自回收部20的负压(吸引力)朝向符号U所示的方向吸引,通过内管19e送至回收部20,而被回收部20的过滤器20b所回收。此时的旋风器19内的内压较佳为大气压以下。并且,金属复合氧化物微粒子的2次微粒子18的粒径,根据需要可规定为纳米等级的任意的粒径。
浆体的形态也与粉末的形态相同,仅通过进行电浆处理即可容易且确实地得到纳米等级的粒状且具有透明性的金属复合氧化物微粒子,即粒状的p型的透明氧化物半导体粒子。
另外,在本发明的金属复合氧化物微粒子的制造方法中,所使用的旋风器19的个数并不限定于1个,也可以为2个以上。
若因刚生成的微粒子彼此发生冲突,并形成凝聚物而产生粒径的不均一,则会成为质量降低的要因。然而,朝向热电浆焰24的尾部(终端部)并沿箭头Q的方向供给的冷却气体会将1次微粒子15稀释,藉此可以防止微粒子彼此发生冲突而凝聚。
在此,本发明使用氧化铜(CuO)的粉末作为铜化合物的粉末,使用碳酸锶(SrCO3)的粉末作为化合物的粉末,电浆气体使用氩气与氨气。通过将氧化铜(CuO)的粉末与碳酸锶(SrCO3)的粉末供给至热电浆焰,而制成具有透明性的金属复合氧化物微粒子,如图2所示,确认可得到SrCu2O2单相。此外,通过将氧化铜(CuO)的粉末与碳酸钡(BaCO3)的粉末供给至使用氩气与氮气的热电浆焰24,而制成金属复合氧化物微粒子,如图2所示,确认可得到BaCu2O2单相。在该情况下,作为组织可得到图3所示的粒状的组织。
另一方面,在将氧化铜(CuO)的粉末与碳酸钙(CaCO3)的粉末供给至使用氩气与氦气作为电浆气体的热电浆焰的情况下,如图4所示,确认形成了Cu2O(氧化亚铜)与CaO(氧化钙)的混合相,而无法得到金属复合氧化物微粒子。因此,如果不是本发明的铜化合物与包含Sr及Ba中的至少1种碱土金属的碱土金属化合物的组合,则无法得到本发明的金属复合氧化物微粒子。
进而,本发明人通过将氧化铜(CuO)的粉末、碳酸锶(SrCO3)的粉末、碳酸钙(CaCO3)的粉末供给至使用氩气与氮气作为电浆气体的热电浆焰,而制成具有透明性的金属复合氧化物微粒子,如图5所示,确认可得到(Sr,Ca)Cu2O2相。另外,为了比较而将SrCu2O2的通过X射线衍射法所得到的解析结果一并显示于图5中。
如图5所示,即使在氧化铜(CuO)的粉末、碳酸锟(SrCO3)的粉末中,进一步添加碳酸钙(CaCO3)的粉末,也可以得到SrCu2O2相。
并且,本发明人通过将氧化铜(CuO)的粉末、碳酸锶(SrCO3)的粉末、碳酸钡(BaCO3)的粉末供给至使用氩气与氮气作为电浆气体的热电浆焰,而制成金属复合氧化物微粒子,如图6所示,确认可得到(Sr,Ca)Cu2O2相。另外,为了比较而将BaCu2O2的通过X射线衍射法所得到的解析结果与SrCu2O2的通过X射线衍射法所得到的解析结果一并显示在图6中。
如图6所示,可以形成锶与钡混合组成的金属复合氧化物微粒子。
并且,本发明人通过将氧化铜(CuO)的粉末、碳酸锶(SrCO3)的粉末、碳酸钙(CaCO3)的粉末供给至使用氩气与氮气作为电浆气体的热电浆焰,而制成金属复合氧化物微粒子,如图7所示,确认可得到(Sr,Ca)Cu2O2相。在图7中,虽然显示了多个(Sr,Ca)Cu2O2相的结果,但这些结果是锶与钡的比率不同的结果。另外,为了比较而将SrCu2O2的通过X射线衍射法所到的解析结果一并显示在图7中。
如图7所示,可以形成锶与钡混合组成的金属复合氧化物微粒子,并且即使改变锶与钡的比率也可以形成金属复合氧化物微粒子。
另外,图8为图7的重要部分的放大。在图8中,C1显示SrCu2O2的峰值位置,C2显示Sr与Ca中Sr较多的(Sr,Ca)Cu2O2的峰值位置,C3显示Sr与Ca中Sr较多且与C2相比Ca的比率较高的(Sr, Ca)Cu2O2的峰值位置。如图8所示,可知若钙的比率提高则峰值位置会往高角侧位移。
使用超声波将SrCu2O2的组成的金属复合氧化物微粒子以及Sr∶Ca以摩尔比计为7∶3的(Sr,Ca)Cu2O2的组成的金属复合氧化物微粒子分别分散在乙醇溶剂中,测定透过率作为光学特性。将该结果显示于图9。另外,在透过率的测定中使用分光光度计。
如图9所示,锶和铜氧化物的金属复合氧化物微粒子以及Sr∶Ca以摩尔比计为7∶3的锶、钙与铜氧化物的金属复合氧化物微粒子中的任一者均能够进行透过率的测定。其显示为粒子分散在乙醇溶剂中。
并且,通过在锶中添加钙来提升透过率,即透明性增加。因此,可以通过改变金属复合氧化物微粒子的组成来改变光学特性。
即使是图9所示的例子,(Sr,Ca)Cu2O2的组成的金属复合氧化物微粒子及SrCu2O2的组成的金属复合氧化物微粒子,任一者的可见光区域的平均透过率均比紫外线区域的平均透过率更高。基于此,可知(Sr,Ca)Cu2O2的组成的金属复合氧化物微粒子及SrCu2O2的组成的金属复合氧化物微粒子具有透明性。
本发明基本上是如上所述而构成的。虽然以上针对本发明的金属复合氧化物微粒子及其制造方法进行了详细地说明,但本发明并不限定于上述实施形态,在不脱离本发明的主旨的范围内,当然可进行各种的改良或者变更。