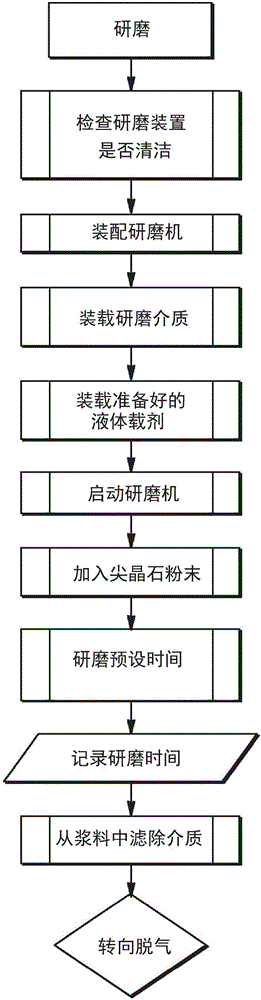
上述专利文献的所有公开内容都通过引用纳入本文。背景本发明总体上涉及用于制造薄的透明尖晶石和层压透明尖晶石的带材铸塑(tapecasting)方法。发明概述在一些实施方式中,本发明提供以下各项中的一项或多项:一种用于制造透明尖晶石板的带材铸塑方法;一种基于水性粘合剂体系的用于制造透明尖晶石板的带材铸塑方法;一种使经过铸塑的带材在整个厚度上都具有均匀的生坯微观结构的带材铸塑方法;一种在不具有或不存在烧结助剂的条件下制造透明尖晶石板的带材铸塑方法;一种用于制造透明尖晶石板的带材铸塑方法,所述方法提供具有例如35~85体积%的固体负载量的均匀的生坯带;一种用于制造透明尖晶石板的带材铸塑方法,所述方法通过进行带材铸塑来提供例如10微米~1毫米的很薄的带材,其适合被层压成若干厘米或更厚的所需厚度;以及一种用于制造透明尖晶石板的带材铸塑方法,所述方法可使用水性带材铸塑或非水性带材铸塑来完成。附图的简要说明在一些实施方式中:图1A~1I显示了在实验室规模下完成的本文所公开的带材铸塑方法的示例性的流程图。图2显示了使用三种具有不同性质的粉末所制造的带材的实验结果以及对该带材中的体积百分比尖晶石的影响。图3显示了刚制得的粉末(上方)和所制备的生坯带(下方)的SEM图像。图4显示了粘合剂体系的TGA分析,以确定用于带材的最佳粘合剂烧除程序。图5显示了用于除去粘合剂以及对尖晶石部件进行空气烧结的长(三角)、短(圆点)烧结曲线。图6显示了具有本文所定义的条件的HIP烧结循环。图7显示了后续的O2HIP工艺的结果,所述O2HIP工艺除去了颜色中心,并且使透射率数值移动至接近最大值。图8显示了所测得的通过带材烧制、层压和抛光制得的厚度约为325微米的部件的透射率曲线。图9是显示层压压力对生坯带中固体负载量的影响,所述压力通过压缩除去了带材的孔隙率。图10是未经抛光的部件(左侧点)和经过抛光的部件(右侧点)的韦布尔图,证明了抛光能够增加平均部件强度。发明详述下面参考附图(如果有的话)对本发明的各种实施方式进行详细描述。参考各种实施方式不限制本发明的范围,本发明的范围仅受所附权利要求书的范围限制。此外,在本说明书中列出的任何实施例都不是限制性的,且仅列出要求保护的本发明的诸多可能的实施方式中的一些实施方式。定义“体积百分比固体负载量”、“体积%固体负载量”等表述是指经过铸塑的带材中的无机固体。体积%固体负载量只考虑无机组分(即,尖晶石)。典型的体积%固体负载量可以是例如45~65体积%、50~65体积%、55~65体积%、60~65体积%,包括中间数值和范围。“带材的生坯密度”是指以g/cm3为单位的带材中尖晶石粉末(无机组分)与粘合剂体系(有机组分)的总和。生坯密度代表了带材中孔隙率的量,其将有机和无机组分都纳入考虑。典型的带材生坯密度可以是例如75~95%,其取决于例如起始粉末和有机组分。表8提供了本文所公开的示例性配方的带材组成(体积%)与带材生坯密度(g/cm3)的比较。“透射率”是指在特定波长下,入射光穿过样品的比例。“透明度”是指尖晶石允许光线在不被散射的条件下穿过的性质。“包括”、“包含”或类似术语意为包括但不限于,即内含而非排他。用来描述本发明实施方式的修饰例如组合物中成分的量、浓度、体积、处理温度、处理时间、产量、流速、压力、粘度等数值及它们的范围或者组件尺寸等数值及它们的范围的“约”是指数量的变化,可发生在例如:制备材料、组合物、复合物、浓缩物、组件零件、制品制造或应用制剂的典型测定和处理步骤中;这些步骤中的无意误差;制造、来源或用来实施所述方法的原料或成分的纯度方面的差异中;以及类似的考虑因素中。术语“约”还包括由于组合物或制剂的老化而与特定的初始浓度或混合物不同的量,以及由于混合或处理组合物或制剂而与特定的初始浓度或混合物不同的量。“可选的”或“可选地”表示随后描述的事件或情形可能发生,也可能不发生,而且该描述包括事件或情形发生的实例和所述事件或情形不发生的实例。除非另有说明,否则,本文所用的不定冠词“一个”或“一种”及其相应的定冠词“该”表示至少一(个/种),或者一(个/种)或多(个/种)。可采用本领域普通技术人员熟知的缩写(例如,表示小时的“h”或“hrs”,表示克的“g”或“gm”,表示毫升的“mL”,表示室温的“rt”,表示纳米的“nm”以及类似缩写)。在组分、成分、添加剂、尺度、条件、时间和类似方面公开的具体和优选的数值及其范围仅用于说明,它们不排除其他限定数值或限定范围内的其他数值。本发明的组合物和方法可包括本文所描述的任何数值或数值、具体数值、更具体的数值和优选数值的任何组合,包括显义或隐义的中间值和中间范围。在一些实施方式中,本发明提供了用于制造透明尖晶石薄板的带材铸塑方法。尖晶石是在可见光谱内以及在部分紫外和红外波长区域内具有优异透射性质的陶瓷。已对透明尖晶石研究了超过四十年。然而,由于有关水解的问题,还未出现有关用尖晶石制造的可用于商业的水基浆料工艺的报道。因此,所有以往的成形工作都是聚焦于用于尖晶石粉末的使用例如单轴、冷等静压制或热等静压制的干压法。干压法的主要问题是生坯体的不均匀性,这会导致最终产品性质不佳。干压法还在所能够制造的部件的总厚度上具有局限性。通常能够实现1mm的厚度。然而,高纵横比的部件需要比该厚度厚得多,例如为1cm或更厚。在一些实施方式中,本发明所提供的板材厚度范围从例如具有10~15微米厚度的薄板至具有40~100微米厚度的较厚板,可对薄板、中等厚度的板、厚板以及它们的组合进行层压以实现厚达若干厘米或更厚的所需厚度。现有的工艺还在同时获得透明度和强度目标上遇到了很大的困难。在现有的工艺中,部件必须(典型地通过使用氟化锂(LiF)烧结助剂)被完全致密化,以实现光学透明度。这种烧结助剂会导致晶粒的过度生长,且会导致烧结后的典型的晶粒尺寸大于100微米。这会导致强度大大降低。本文所公开的带材铸塑方法得到了极高的生坯密度,例如理论带材密度的75~95%,这能够排除对烧结助剂的需要。这允许保持较小的晶粒尺寸,例如小于5微米,导致相比于使用烧结助剂制备的尖晶石部件优异得多的烧结后强度。降低了的晶粒尺寸导致烧结后的部件具有更高的强度。使用烧结助剂制得的部件通常具有例如100~200MPa的强度,对应于100~200微米的晶粒尺寸。相比之下,不使用烧结助剂制得的本文所公开的部件具有更小的晶粒尺寸,且具有例如300~500MPa的烧结后强度,对应于小于10微米的晶粒尺寸。一种工业实践是使用热压来形成透明尖晶石。由于部件尺寸和生产能力的限制,这是一种昂贵的工艺。所以,潜在的产品应用被局限在不关心成本的市场,例如军事和防御系统或定制化产品。在诸如消费电子产品这样的更广阔的市场中的实际用途被排除在外。本文所公开的方法的另一个优势在于能够大大降低透明尖晶石产品的成本,产生巨大的商业潜力。在一些实施方式中,本文提供了基于水性和非水性的带材铸塑方法,并且提供了证明能够生产具有所需高性能的透明尖晶石的数据。在一些实施方式中,本文提供了透明的经过带材铸塑的尖晶石制品,其包含:以下各项中的至少一项:10~300微米的单层厚度;或包含多个经过层压的单层的层压件,所述层压件具有50微米~10毫米或更厚的厚度;所述尖晶石制品具有:基于87%的最大理论透明度的80%~87%,例如84%~87%的透明度;以及例如1~7微米、2~7微米、3~6微米、4~5微米的烧结后晶粒尺寸,包括中间数值和范围。相比之下,现有技术提到了使用诸如氟化锂这样的烧结助剂制得的透明的经过带材铸塑的尖晶石,其具有100~200微米烧结后晶粒尺寸,参见例如armorline.com/pdf/ArmorLine%20Corp-Transparent%20Spinel%20Brochure.pdf。在一些实施方式中,尖晶石制品包含在烧制前具有80~500纳米的窄中值粒径以及5~30m2/g的相对较低的BET表面积(SA)的尖晶石粉末。在一些实施方式中,尖晶石包含在烧制前具有100~300纳米的窄中值粒径以及6~15m2/g的相对较低的BET表面积的尖晶石粉末。在一些实施方式中,使用200g负荷测得的尖晶石制品的努氏硬度数可为10~16GPa、11~15GPa、12~15GPa、例如为14.1GPa,包括中间数值和范围。得到三种使用下示的不同热等静压制(HIP)条件由S15CR尖晶石制品制得的透明尖晶石样品的烧结后晶粒尺寸的测量结果:在1550℃下经过4小时HIP得到的结果是4.6微米;在1500℃下经过4小时HIP得到的结果是3.6微米;以及在1475℃下经过4小时HIP得到的结果是2.8微米。在一些实施方式中,尖晶石制品具有99.5重量%~99.9重量%的纯度,且具有0.01重量%~0.001重量%或更低的低含硫量。在一些实施方式中,本发明提供用于制造经过带材铸塑的透明尖晶石的方法,该方法包括:对包含中值粒径为75~500纳米、优选为100~500微米、更优选为200~400微米的尖晶石粉末、粘合剂、分散剂、增塑剂、消泡剂和水性溶剂的批料进行10分钟~10小时、优选30分钟~6小时、更优选1~3小时的碾磨以形成浆料;在真空下对所得到的经过分离的浆料进行脱气;对经过脱气的浆料进行带材铸塑,使其具有20~2000微米、优选为50~1000微米、更优选为100~500微米的湿厚度;使用床下加热器和经过加热的流动空气在经过带材铸塑的浆料处于20~100℃、优选40~80℃、更优选60~70℃的温度下对经过带材铸塑的浆料进行受控干燥,以形成具有5~1000微米、优选20~500微米、更优选40~200微米的干燥厚度的生坯带;在足够的温度下对生坯带进行足够时间的烧制,以提供经过烧结的透明尖晶石。在一些实施方式中,本发明的方法还可包括将生坯带层压成多个生坯带层,其为两层或多层,例如2~约28层,其中,所述层压可通过例如压缩方法来完成。在一些实施方式中,尖晶石粉末在被引入浆料之前的BET表面积为2~30m2/g,更优选为5~20m2/g,甚至更优选为6~15m2/g,最优选为6~8m2/g。在一些实施方式中,一种优选的尖晶石粉末的表面积为15m2/g,且具有50~1000nm、优选100~600nm、甚至更优选200~400nm的中值粒径分布。关于PSD测量方法的一个需要注意的地方是其测量的是团聚尺寸,对于纳米粉末并不特别可靠。在一些实施方式中,尖晶石粉末在浆料中的陶瓷固体负载量为例如5~60体积%,优选为10~40体积%,更优选为15~25体积%,且生坯带的陶瓷固体负载量为例如35~85体积%,优选为45~75体积%,更优选为55~75体积%,所述固体负载量水平允许对陶瓷进行烧结以使其具有高透明度。在一些实施方式中,一种优选的生坯带具有45~55体积%的固体负载量。在一些实施方式中,对生坯带的烧结可包括例如:在1500~1600℃下对生坯带进行2~8小时烧结,完成粘合剂的烧除(BBO),从而得到经过烧结的透明尖晶石;在例如1500~1600℃下,在例如5~60kpsi、优选10~40kpsi、更优选20~30kpsi的压力下,在例如在氩气惰性气氛中对经过烧结的透明尖晶石进行热等静压制(“HIP”)。在一些实施方式中,在约29kpsi或约200MPa下完成一种成功的热等静压制,以降低尖晶石中的残余孔隙率,其中,经过烧结的尖晶石在热等静压制之后的总孔隙率小于约500ppm,优选小于约200ppm,更优选小于约100ppm,甚至更优选小于约50ppm,包括中间数值和范围;在例如1000~1200℃下,在0.2~30kpsi、优选1~20kpsi、更优选5~10kpsi(包括这些范围的中间数值)的压力下对经过HIP烧结的透明尖晶石进行2~8小时的氧热等静压制(“O2HIP”)。在一些实施方式中,在8~10kpsi下完成一种成功的氧热等静压制以减小所得到的经过氧热等静压制和烧结的透明尖晶石中令人厌恶的颜色中心。热等静压制(HIP)是一种用于降低许多陶瓷材料的孔隙率以及增加它们的密度的制造方法。这改善了材料的机械性能和可加工性。HIP方法使组件处于高压储存容器中的升高了的温度和等静气体压力下。最常用的增压气体是氩气。可使用惰性气体,从而使材料不会发生化学反应。加热HIP腔室,这导致该容器内的压力升高。许多系统会压入相关气体以实现必要的压力水平。因为压力是从各个方向相材料施加的,因而该压制是“等静”的。在一些实施方式中,所述烧制可通过一步或两步完成,以提供经过烧结的带材铸塑透明尖晶石。在单步烧制处理中,BBO和烧结是在相同的炉子中完成的,然后是H2气氛或HIP。在两步烧制处理中,BBO和烧结是在分开的炉子中完成的,然后是H2气氛或HIP。在一些实施方式中,烧制可在不存在烧结助剂的条件下完成。在一些实施方式中,水性溶剂可以是去离子水。在一些实施方式中,本发明的方法的至少一个步骤是在微粒受控环境下完成的,所述微粒受控环境例如等级为100的无尘室、等级为1000的无尘室或类似的微粒污染少或没有微粒污染的受控的环境。另外,可对所述微粒受控环境进行化学清洁和生物除菌。在一些实施方式中,生坯带的孔隙率为例如约0.01~约25体积%,优选为1~20体积%,更优选为2~10体积%,包括这些范围的中间数值。在一些实施方式中,一种成功的生坯带在层压处理之前具有7~17体积%的孔隙率。在一些实施方式中,本发明的方法还可包括将生坯带成形(即,生坯成形)成所需的形状或物体,例如除了板材以外的可卷绕带材。在一些实施方式中,本发明的方法还可包括对经过脱气的浆料进行过滤以除去污染物,这些污染物是大微粒或大尺寸的污染物,例如研磨介质等,或者是比主要颗粒更大的团聚物。在一些实施方式中,本发明的方法还包括对所述经过烧结的透明尖晶石进行表面精整,以使其具有所需的厚度和表面质地。在一些实施方式中,如果生坯带陶瓷固体负载量大于45体积%,则对带材或带材层压件的烧结对带材铸塑浆料中粘合剂的量、或生坯带的孔隙率不敏感,即,有利的是,粘合剂含量或生坯带孔隙率的微小变化不会明显改变经过烧结的带材或经过烧结的层压产品的品质。在一些实施方式中,当利用SEM图像进行观察时,发现优选的生坯带的微观结构是均匀的。例如,观察到优异的颗粒去团聚化。这些颗粒大致均匀间隔,且在颗粒之间具有粘合剂和孔隙,参见例如图3(下方中间的S15CR生坯带图像),其具有优异的微观结构,以及图3(下方右侧的S8CR生坯带图像),其具有相对较差的微观结构(S8带材)。由不同尺寸的颗粒所制得的带材之间均匀性的差异十分明显。在一些实施方式中,可利用本文所公开的制备方法来制备经过带材铸塑的透明尖晶石制品。在一些实施方式中,可利用本文所公开的制备方法来制备经过带材铸塑和层压的透明尖晶石制品。在一些实施方式中,本发明提供了一种用于制造透明尖晶石板的带材铸塑方法。在一些实施方式中,本发明提供了一种用于制造具有包括分散剂在内的水性粘合剂体系的透明尖晶石板的带材铸塑方法。所述包括分散剂的粘合剂体系具有相对较高的碱性pH(例如8.5~13、9~12、9.5~11、9.5~10.5,包括中间数值和范围),所述碱性pH可通过例如氨水来实现,且所述粘合剂体系能够防止尖晶石粉末在浆料制备和铸塑过程中发生水解和凝胶化。在一些实施方式中,本发明提供了一种用于制造透明尖晶石板的带材铸塑方法,该方法能够使经过铸塑的带材在整个厚度上具有均匀的生坯微观结构。所述均匀的生坯微观结构可通过例如使用具有例如2~30m2/g、更优选5~20m2/g、甚至更优选6~8m2/g的边界明确的比表面积、以及例如50~1000nm、更优选100~600nm、甚至更优选200~400nm的很窄的粒径分布的起始的尖晶石粉末来实现。通过大量实验,发现如果起始的尖晶石粉末具有与上述的相对应的表面积和粒径分布的粉末性质,则能够使用带材铸塑方法制造本文所公开的透明陶瓷,例如透明尖晶石。在一些实施方式中,本发明提供了一种用于制造具有均匀的生坯带的透明尖晶石板的带材铸塑方法,所述均匀的生坯带的固体负载量为35~85体积%,更优选为45~65体积%,甚至更优选为55~65体积%,所述固体负载量允许烧结成透明。如果不具有利用本文所公开的方法所得到的足够高的生坯密度,则不可能得到透明尖晶石。通过大量实验,还发现如果生坯带的固体负载量以及所得到的生坯密度并非上述数值,则不可能使用带材铸塑方法制造本文所公开的透明陶瓷,例如透明尖晶石。在一些实施方式中,本发明提供了一种用于制造透明尖晶石板的带材铸塑方法,所述方法通过进行带材铸塑来提供例如10微米~1毫米的很薄的带材,然后将所述很薄的带材层压成若干厘米或更厚的厚度。虽然无意受限于理论,但使用本文所公开的方法所能够得到的透明层压件的厚度只受能够得到的层压装置的尺寸所限。在一些实施方式中,本发明提供了一种用于制造透明尖晶石板的带材铸塑方法,该方法可使用水性带材铸塑(例如只使用水或组合使用诸如醇类这样的可混溶溶剂)或在需要的情况下使用非水性带材铸塑(例如使用诸如乙醇、甲苯或MEK这样的溶剂,以及使用PVB或碳酸盐粘合剂体系)来完成。本文所公开的组合物、制品和方法由于提供了例如以下各项中的至少一项而具有优势:一种形成高密度生坯带的带材铸塑方法,所述高密度生坯带允许在不使用烧结助剂的条件下对透明尖晶石进行烧结。不使用烧结助剂能够限制晶粒在烧结处理过程中的生长。相比于使用LiF烧结助剂和热压制方法时大于100微米的晶粒尺寸,不使用烧结助剂会导致约1~5微米的最终晶粒尺寸。较小的晶粒尺寸能够使所得到的尖晶石具有与其它市售可得的尖晶石(例如Surmet或Armorline)相比显著增加的强度。可放大至大规模且相比于其它商业上可行的工艺具有低成本的带材铸塑和层压方法。例如,本文所公开的带材铸塑方法可以合成蓝宝石的一部分成本(例如50%或更低)生产出一种具有与其相似的性质的透明板材料。一种能够灵活制造具有不同厚度的部件的带材铸塑和层压方法。一种能够制造用于消费电子应用的大型、薄且平坦的板材的带材铸塑和层压方法。一种能够使用现有工艺装置的带材铸塑和层压方法。参照附图,图1A~1I显示了本文所公开的带材铸塑方法的流程图。图2显示了使用三种具有不同性质的粉末所制造的带材的实验结果以及对该带材中的体积百分比尖晶石的影响。每一种粉末都具有不同的表面积(SA)(30、15或10.5m2/g)。利用三个数据点来表示生坯带固体负载量的差异。粉末SA的减小允许带材固体负载量增加。较高的固体负载量允许烧结成透明。被测试的三种不同粉末的BET表面积(SA)性质的详细细节列于表1中。使用尽可能少量的粘合剂可制造优选的带材,该用量不会导致带材开裂。表面积(SA)较低且具有相对较大的平均粒径的粉末能够使用较少的粘合剂,并且能够在不发生开裂的条件下实现较高的带材密度。表1.尖晶石粉末的性质。粉末名称S30CRS15CRS8CRBETSA(m2/g)30.415.410.5表2总结了三种被选中的尖晶石粉末样品的元素分析,并且列出了它们的杂质水平。表2.尖晶石粉末的元素分析(杂质,单位:ppm)。杂质S30CRS15CRS8CRNa40348.8K100未测量19Fe275.6Si332643Ca1266S<80<80<80图3显示了刚制得的粉末(上方)和所制备的生坯带(下方)的SEM图像。两组图像都具有两(2)微米的比例尺。在所测试的粉末中,S15CR粉末具有优异的结果。S30CR粉末具有极高的SA,该带材需要大量粘合剂,例如批料浆料中约为15~20体积%,经过干燥和铸塑的带材中大于约50体积%的粘合剂来防止该带材在干燥过程中发生开裂。虽然无意受限于理论,但各固体颗粒应当被有机粘合剂材料包围以防止发生开裂。在高粘合剂含量下,带材中的最大固体负载量只有36~37体积%,该负载量太低以至于无法对透明尖晶石进行烧结。从图3中上方的SEM图像中可以看出,S8CR具有较高的SA,但具有不均匀的粒径分布(PSD)。这种PSD是双峰的,具有不超过1微米的强烈团聚的大颗粒。该PSD不允许进行均匀的烧结。S15CR粉末提供了比由S30CR或S8CR粉末制得的带材更优异的带材。S15CR粉末具有窄的PSD和相对较低的SA,这些特征允许进行优异的带材成形和烧结。同样地,虽然无意受限于理论,所能够得到的结果暗示,除了具有略微更大的粒径(例如约300微米)和较小的SA(例如约7m2/g)外,能够得到甚至更加优选的与S15CR相似的粉末。图4显示了粘合剂体系的TGA分析,以确定用于材料的最佳粘合剂烧除现象。值得注意的温度被确认为180、350和600℃,在这些温度下的质量损失被确认为粘合剂的除去。基于该分析的烧结曲线示于图5。图5显示了用于除去粘合剂以及对尖晶石部件进行烧结的长(三角;慢速)、短(圆点,快速)烧结曲线。值得注意的是,为了除去粘合剂并使部件的翘曲/隆起降到最低,在180、350和600℃下进行保温。然后将样品烧结至1550℃,为了进行氩气HIP而使该部件致密化。长烧结曲线可被用于较厚或较大的部件,以确保粘合剂被完全除去。对于薄、小的部件,已证明短烧结周期足以胜任。表3和表4分别列出了慢速和快速粘合剂烧除(BBO)程序以及烧结程序的更多细节。取决于部件的尺寸,可根据需要在值得注意的温度使用更长的停留时间。或者,还可对BBO(粘合剂烧除)使用更慢的升温速率。BBO并不仅限于该加热程序。表3.基于TGA的慢速粘合剂烧除(BBO)以及烧结的细节。表4.基于TGA的快速粘合剂烧除(BBO)以及烧结的细节。在初始的空气烧结处理之后,对这些部件进行氩气HIP以烧结成透明。该处理步骤的一种替代性路径包括增加这些部件的生坯密度、使用粘合剂烧除处理、并随后进行氢气烧结,这比进行HIP成本更低。氢气烧结是一种已知的用于其它诸如照明工业中的氧化铝和其它先进陶瓷应用中的YAG这样的透明或半透明氧化物材料的工艺。图6显示了HIP烧结循环,表5提供了这些条件的列表。在氩气HIP(ArHIP)之后,对这些部件进行氧气HIP(O2HIP)以除去氧空位,这些空位会使部件颜色变深。表5HIP烧结循环。烧结之后,按照需要对经过烧结的部件进行抛光。在这些部件中观察到的大部分缺陷(尽管相对较少)都是由于处理过程中的表面污染所致。当选择合适的无尘室处理环境时,这些缺陷可被显著减少,例如减少约75%或更多。对经过ArHIP的部件(具有颜色中心)和经过ArHIP并随后进行O2HIP以除去颜色中心的部件进行透射率测量。图7显示了后续的O2HIP的结果,所述O2HIP工艺除去了许多颜色中心,并且使透射率数值(%T)移动至接近理论最大值。图8显示了所测得的具有约325微米厚度的经过层压和抛光的部件的透射率曲线。受到折射率的限制,透射率(%T)能够达到87%的理论最大值。实际透射率与理论透射率的偏差在实验误差范围内。图9是显示了层压压力对生坯带中固体负载量的影响。使用了实施例1的批料组合物组合物。利用铸塑带材(单层,层压压力=0)和五个经过层压的样品的尖晶石体积%(菱形;左侧坐标)、有机物体积%(正方形;左侧坐标)和孔隙率(三角形;右侧坐标)绘图,五个经过层压的样品中的每一个都具有二十八(28)个层压层,且在3000~30000psi的不同的层压压力下形成。观察到随着层压压力在3000~30000psi的范围内上升,孔隙率减小。这导致生坯带的固体负载量从原始铸塑带材的约47%增加到在30000psi下层压的样品的约54%。生坯态下的增加的尖晶石固体负载量实现了:改善的烧结;较低的温度;以及可选的氢气烧结。所有带材都在70℃下层压,在1000psi下保持15分钟,然后压至3000~30000psi的目标压力,随后再额外保持15分钟。表6中所列的结果被图形化地示于图9。表6.带材铸塑浆料的示例性批料组合物配方。尖晶石粉末。WB4101是一种在溶液中具有添加剂的专有的丙烯酸类粘合剂。DF002是一种不含有机硅的消泡剂。DS001是一种聚合物分散剂。PL005是一种高pH增塑剂。聚合物创新有限公司(PolymerInnovations,Inc.,维斯塔,加利福尼亚州)对这些组分进行配制以用于水性陶瓷带材铸塑。S15CR尖晶石颗粒批料组合物的带材铸塑浆料配方中的组分列于表7A。各组分的量都足以用来形成本文所公开的带材,所述带材不会开裂,具有高生坯密度,且可被层压成一个或多个层,即若干个层,包括其自身或其它材料。该浆料由于更高的含水量而比例如表7B的浆料具有更低的粘度,且当试图对具有大于约50微米干燥厚度的较厚的带材进行铸塑时,该带材发生开裂。S15CR尖晶石颗粒批料组合物的另一种带材铸塑浆料配方中的组分列于表7B。该配方相比于表7A的配方具有进步。表7B的浆料具有更低的含水量和更高的粉末含量。这会导致带材铸塑处理过程中的干燥应力降低,允许形成具有最少开裂的厚度厚至约100微米的更厚的带材。表7C列出了用于制备S15CR尖晶石颗粒批料组合物的带材铸塑浆料的各组分的量。表7A.带材铸塑浆料的批料组合物组合物。表7B.带材铸塑浆料的批料组合物。表7C.带材铸塑浆料的批料组合物。带材铸塑方法的概述JamesS.Reed在《陶瓷加工原理》(PrinciplesofCeramicProcessing,1995年,第二版,ISBN-13:978-0471597216)中公开和说明了一种常规的带材铸塑方法和装置。以下描述介绍了所公开的制造方法,并且确定了其与常规带材铸塑方法的区别。下文还讨论了示于图1A~1I的所公开的制造方法的具有代表性的实验室规模带材铸塑方法。配制批料(图1A):尖晶石粉末与包含粘合剂、分散剂、增塑剂和消泡剂的水基带材铸塑体系相混合。研磨(图1B):利用例如球磨、高速剪切混合、碾磨、振动磨、辊磨等方法在研磨机中对批料材料进行研磨和混合。脱气(图1C):完成研磨之后,从浆料中滤除研磨介质,然后使用真空对浆料进行除空气/脱气。该处理从经过研磨的产品中除去了被截留的空气,否则这些空气会最终成为混合物中的气泡。过滤:可选地对浆料进行过滤,以从混合物中除去任何大尺寸的污染物,否则这些污染物会使烧结后的材料具有不利的光学性能。可通过例如由例如尼龙、纤维或其它合适材料制得的50微米、25微米、10微米或1微米的过滤器来完成过滤。带材铸塑(图1D):然后,在所需厚度下,在刮刀下对浆料进行带材铸塑,以形成陶瓷浆料的湿、薄板材。在受控条件下对湿带材进行干燥以形成可被成形为所需形状的薄的陶瓷/聚合物复合带材(被称为“生坯态”下的带材、或者“生坯带”)。压力裁断(图1E):从在带材铸塑方法中得到的带材卷上压力裁断(即,冲压切割)出所需的部件几何形状。压力裁断形成了近净形状(nearnetshape)。然后,可通过例如各种精整方法,例如切割、抛光等精整操作,形成生坯态的最终部件,或在后烧结处理中形成最终部件。堆叠(图1F):对经过压力裁断的层进行堆叠以实现所需的烧结后部件厚度。在进行层压的同时,可根据层压多个部件的需要,在相同的层压处理条件下将插页材料插入堆叠部件之间。层压(图1G):可使用单轴或等静压制对所需的多个陶瓷带材层进行堆叠和层压以形成更厚的带材。这是一个可选的步骤,并且仅当无法在原始铸塑状态下实现所需带材厚度时才有必要进行。生坯成形:可选地使用任何合适的陶瓷成形技术使生坯带成形为所需的形状,所述合适的陶瓷形成技术例如:激光切割、热刀切割、穿孔、冲压、压制等方法,或这些方法的组合。替代地或附加地,可对带材进行烧制,随后使用例如激光切割或切断使其在经过烧结的状态下成形。烧制/烧结(图1H):可在单步或两步处理中对带材进行烧制。单步处理能够在单次烧制中除去粘合剂并且烧结带材。在两步处理中,在一个炉子中除去粘合剂,然后在第二个炉子中将该部件烧结成最终密度。可使用氢气炉、真空炉、热等静压制(HIP)、N2或Ar炉、或空气炉来实现最终烧结。典型的烧制温度可以是例如1400~1800℃。抛光(图1I):烧制以后,可将这些部件研磨、精研和抛光成最终的所需厚度和表面光洁度。例如,可使用例如碳化硅或金刚石、砂纸或浆料对部件进行粗研磨以得到上表面和下表面的同面性。氧化钇和氧化铝也是常用的抛光剂,它们可作为替代抛光剂使用。实现同面性以后,可随后使用更细的金刚石浆料或金刚石带(例如9、6、3和1微米是典型的尺寸)对这些表面进行抛光,最终抛光可使用1微米的金刚石浆料。可为光学应用选用更细的抛光剂。抛光程序可进行1~24小时,更优选为2~12小时,最优选为4~8小时,包括中间数值和范围。参照图10,未经抛光的部件(左侧点)和经过抛光的部件(右侧点)的韦布尔概率图显示抛光能够将平均环叠环(ROR)部件强度从137MPa增加至373MPa,或者说提供约3倍(经计算为2.72倍)的增量,或者说平均部件强度增加了约172%。该方法的几个关键方面研磨(图1B):该研磨处理是一个重要步骤,其必须提供完全去团聚化的颗粒并且生成均匀(即,分散良好)的浆料。购自联合工艺有限公司(UnionProcess)的碾磨机(aka.:搅动球磨机)是一种用于实现去团聚化,即打碎尖晶石粉末的团聚体或纳米团聚体(所述去团聚化难以利用替代性的方法高效且经济地实现)的优选的研磨机。这种碾磨机由于能够在研磨处理过程中向材料输入高能量而优于其它研磨工艺和装置。相比于其它技术,其允许在较短时间(例如相比于使用球磨的50~100小时为1~3小时)内将批料研磨至较小的粒径。所使用的一种碾磨机具有750mL的总容积和250mL的加工容积(加工能力)。罐体中装载有130mL浆料和740克购自联合工艺有限公司的1mm纯度为99.9%的Al2O3介质(即,研磨介质)。在研磨处理过程中用水将罐体冷却至15℃,以避免过热和减少溶剂蒸发。初始在500rpm下对浆料进行5分钟的研磨以打碎大的团聚物,然后将速度升至1300rpm并研磨1小时。在研磨结束时使罐体减速至170rpm,加入消泡剂以除去被截留的空气。然后,将浆料倾倒在80~120目的筛网上以在除气之前从该浆料中除去研磨介质。除气(脱气)处理(图1C):在从浆料中滤除研磨介质之后,对浆料进行除气。使用干燥器腔室并随后使用Mazerustar真空行星式混合器来完成除气。将浆料装入干燥器腔室并进行不超过10分钟的除气。在初始的除气之后,将浆料装入行星式混合器中,在真空下运行5分钟。一种能够不使用Mazerustar混合器的替代性的除气程序是在干燥器腔室中使用更高的真空。粘合剂体系:有机粘合剂组合物对于本文所公开的优异的尖晶石带材铸塑方法而言是重要的。使用购自聚合物创新有限公司的粘合剂体系,其包含可溶于高pH(例如pH约为9~12)的水中的基于丙烯酸类树脂的粘合剂。该粘合剂体系允许得到一种稳定的尖晶石浆料系统,所述系统不会在带材铸塑前絮凝和凝胶化。带材铸塑:在标准的实验室环境中进行初始的带材铸塑。在实验室中制得的样品具有大量会严重降低材料光学品质的污染物。因此将本方法的铸塑部分移至等级为1000的无尘室中进行。这消除了75%的在材料中观察到的缺陷。在无尘室中完成研磨、除气和层压步骤能够进一步降低污染物水平。在厚度约为50~100微米的涂覆有有机硅的膜上对样品进行带材铸塑。有机硅涂层使得带材料在干燥后易于揭下。用于带材的其它合适的膜可以是例如玻璃、金属带等替代性的材料。使浆料在间隙约为4~20密尔(即,100~500微米)的刮刀下(通常使用4密尔(100微米)的刮刀高度)通过,以形成陶瓷带的薄板。带材干燥后的厚度为40~60微米,烧结后的厚度约为20~40微米。铸塑用刮刀以例如10毫米/秒的速度移动经过可根据需要改变该速度,以加快处理速度,以及改变带材的厚度。层压处理:对生坯带的卷料(其尺寸可例如从一张纸的大小至数米宽、数百米长)进行压力裁断(冲压/切割),形成所需的大致形状,例如1、2或3平方英寸的直径为1或3英寸的圆。对带材的取向进行标记,以在之后的取向中知晓铸塑的方向、以及带材的顶部和底部表面。如果陶瓷颗粒的形态是各向异性的,则它们会优先沿着铸塑方向对齐,这会导致在x-y方向上发生不同的收缩,从而导致在烧结后发生局部隆起。另外,粘合剂体系的聚合物链可能会优先沿着铸塑方向对齐,这也会促进非均匀的收缩。带材的顶部和底部表面可由于干燥动力学而具有不同量或浓度的粘合剂和孔隙率。这会导致在z-方向上(平面外)发生不均匀的收缩,这是局部隆起的另一个可能的缘由。在铸塑方向已知的前提下,对空白带材进行堆叠。为了减轻铸塑过程中颗粒优先取向所产生的影响,使带材每层相互旋转90度(另外,也可以不进行旋转或者旋转180度)。带材通常在不翻转的情况下堆叠在彼此的顶部。第一层的底面被置于下一层的顶面上,按序重复以得到所需的层数。由于干燥动力学,带材的底面通常会含有更高浓度的粘合剂,而顶面则更加多孔。通过将层置于彼此的顶部,在层压处理中,高粘合剂表面被压缩至多孔表面上。可将两个高粘合剂表面层压在一起,然而,如果对两个多孔表面进行层压,则通常会观察到脱层,除非带材中的粘合剂浓度高到甚至能够填充入带材顶面的孔中。有必要使生坯带具有一定量的孔隙率以允许在层压步骤中进行压缩。典型地,以5~10%作为目标,但更低或更高的孔隙率也能够使人满意。通过使用所需的旋转和堆叠技术,带材被置于彼此的顶部并被堆叠成所需的层数。例如,4~28层的每层厚度约为40微米的生坯带提供了厚度为160~1120微米的生坯带层压件。然而,如果需要较厚的部件,则也可以制造具有数百层的堆叠件。在各种层压例中,以顶对底的方式堆叠了4~28层的带材,且通过旋转90度对所添加的每一件带材进行取向。将带材的堆叠件置于两片涂覆有有机硅的(“书挡”)上以允许在层压后揭下。可将一片压力试纸置于的顶部以使处理完成后的压力分布可视化。随着所施加的压力的增加,压力纸片从白色变为红色,再变为暗红色。将具有“书挡”的堆叠件置于两块金属板之间,真空密封在袋中,进行等静压层压(或者也可采用单轴压制)。在60~80℃的温度下,所使用的典型的压力为3000~5000psi。然而,也可使用60~100℃的温度、1000~10000psi的压力,更优选为在70℃下使用4000~5000psi。将堆叠件样品置于预热至70℃的层压机中,在无压力或低压(例如150psi)下预热15分钟。然后将样品升高至所需压力(例如3000psi)并保持15分钟。完成循环之后,释放压力,将这些样品从腔室中取出。使这些样品冷却至室温,并从层压板和Mylar载膜上取下。然后将样品“部件”移至脱粘/烧结步骤,或者可使用冲压或切割方法使部件在生坯态成形。烧制处理:层压后,如图1H所示,使这些生坯体经历粘合剂烧除(BBO)和烧结处理。烧结后,经过烧制的尖晶石体具有超过94%的密度,表明基本上所有的孔都已关闭。为了消除任何残余的孔隙率,使用热等静压(HIP)。用于慢速和快速BBO的HIP程序分别列于表3和表4中。使用高功率石墨炉来进行HIP(“空气HIP”)处理以实现高温(例如1500℃或更高)。在进行氩气HIP之后,这些部件呈深色,例如显示出颜色中心。虽然无意受限于理论,但认为这些颜色中心与这些部件中的氧空位有关,所述氧空位充当了颜色吸收中心。为了增加透射率,优选从这些部件中除去颜色中心。使用“O2HIP”来除去这些颜色中心。在“O2HIP”处理过程中,在80体积%的Ar和20体积%的O2的混合气体中,在约1000psi或更高(例如10kpsi或5500psi)的压力下,在高于600℃(例如1100℃)的温度下对这些部件进行若干小时的HIP。由于高压力的O2,颜色中心通过氧空位的除去而被消除。表8列出了由基于颗粒性质与粘合剂的不同比例且与生坯带密度具有关联性的不同尖晶石粉末起始材料制得的带材铸塑组合物。使用S15CR粉末成功地制得了具有一定范围的粉末与粘合剂的比例的带材。粘合剂含量较高的带材导致了较低的开裂倾向,但这些带材受限于低生坯带厚度以防止开裂。使用S15CR粉末制备的样品在烧制过程中需要在顶部放置重物以保持带材的平整,使翘曲最小化。所有的组合物无论带材的组成如何都产生了良好的烧结后部件的透明度。优选制得的带材具有50:50或55:45的尖晶石:有机物的比例,因为它们能够对带材品质、透明度和平整度做出最好的折中。相比之下,使用S30CR粉末制得的带材只能在很高的粘合剂含量下铸塑,并且具有受限的带材品质、透明度和平整度。由于防止开裂所需的薄厚度,处理基于S30CR的带材的能力不佳。由于极薄的层厚度,搬运过程中经常发生带材撕裂。可得到半透明的经过烧结的带材,但高表面积和小粒径带来的限制使得S30CR粉末不太适合进行带材铸塑处理。S8CR粉末以牺牲透明度为代价能够得到更好的带材品质(即,厚度)和烧结后的部件平整度。由于S8CR起始粉末的硬团聚物和双峰粒径分布,不可能在烧结后生成透明的部件。然而,改善了的带材的生坯密度允许生产更厚的带材而不会发生开裂,并且允许进行平坦的烧结而无需在样品顶部放置重物。所有在早先实验工作中制备的部件都显示出一定水平的缺陷,所述缺陷可归因于概念验证实验室规模处理,这向经过层压的层中引入了缺陷。表9列出了所观察到的性能,其为表8中所列组合物的烧结后的带材铸塑部件的性能。表8.带材铸塑组合物。表9.经过烧结的带材铸塑部件的性能。1.带材品质N/A=带材开裂而无法使用;无法确定性能。-=只有极薄(即,小于40微米)的带材是可铸塑的,其避免了带材开裂;可能存在少量的带材开裂。o=能够制造具有40~60微米厚度且不开裂的可接受的带材。+=能够制造厚度大于60微米且不开裂的带材。2.透明度N/A=带材开裂而无法使用;无法确定性能。-=部件在烧结之后是不透明的。o=部件在烧结之后是半透明的。+=部件在烧结之后是透明的。3.平整度N/A=带材开裂而无法使用;无法确定性能。-=部件在烧结之后具有翘曲之处。o=部件可通过在顶部放置重物来平整地烧结。+=部件在没有重物的条件下平整。4.缺陷N/A=带材开裂而无法使用;无法确定性能。-=由于原材料污染以及颗粒的团聚而具有大量缺陷。o=由于处理过程中的污染而具有一些小缺陷。+=部件没有缺陷。粒径数值全都来源于BET表面积分析。难以测量个别纳米尺度的颗粒。使用以下公式来计算个别颗粒的平均粒径:d=6×103/(ρ×SBET)其中,d表示直径或平均粒径(单位:nm),ρ表示尖晶石的密度(3.58g/cm3),SBET表示由BET测得的表面积(单位:m2/g)。表10列出了由商业粉末S30、S15和S8的BET表面积分析得到的计算的平均粒径(d)。虽然无意受限于理论,但基于预测性模型,预计“TARGETS”颗粒的性质能够提供比本文所公开的实际带材铸塑部件具有更好的性能的带材铸塑部件(另请参见预测性实施例2)。表10.尖晶石粉末颗粒的性质。非水性带材铸塑还展示了一种与本文所公开的水性处理有关的用于制造透明尖晶石的非水性带材铸塑方法。可使用基于乙醇的溶剂体系和聚乙烯醇缩丁醛粘合剂来制造尖晶石带。使用直径为1mm的3YSZ研磨介质对商业尖晶石粉末(BaikowskiS30CR)进行1小时的碾磨以打碎团聚物。研磨批料(MB)的组成列于表11。表11.非水性研磨批料(MB)的组成。Dyspersbyk-118是一种购自毕克化学有限公司(BYK-Chemie)的商业分散剂。在研磨批料中混合聚乙烯醇缩丁醛粘合剂(ButvarB98)、邻苯二甲酸二丁酯增塑剂和额外的溶剂以制造组分如表12所示的粉浆铸料。表12.非水性带材铸塑。1.“D-118”是指Dyspersbyk-118。2.“DBT”是指邻苯二甲酸二丁酯。3.“PVB-98”是指ButvarB98聚乙烯醇缩丁醛粘合剂。使用14密耳的刮刀在涂覆有的载膜上对该粉浆进行铸塑。干燥后小心揭下带材,将其切割成形状,并在1500℃下烧结4小时。经过烧制的层的厚度约为30微米,并且是透明的。可对铸塑的尖晶石带施用其它非水性体系。例如,聚丙烯碳酸酯(PPC)粘合剂能够溶于诸如碳酸二甲酯或碳酸二乙酯这样的碳酸酯溶剂中,并能够使粘合剂在低温下被干净地除去而无残留碳。消除残留碳对于实现经过烧制的带材中小于0.1%的孔隙率而言可能是特别重要的,需要低孔隙率来实现高透明度。另外,PPC粘合剂因热解而分解,并且可在惰性气氛中被干净地除去。这可在进一步降低低温孔隙率,进而降低需要通过传统烧结来除去的孔隙率水平方面提供额外的优势。丙烯酸类粘合剂(其发生“解压”或解聚而非燃烧)对于制造孔隙率非常低的经过烧制的带材而言是有益的。实施例以下实施例展示了根据上述一般程序的本文所公开的尖晶石制品的制造、用途和分析。实施例1一种经过带材铸塑和层压的透明尖晶石的制造方法——S15粉末;高透明度。使用拜科斯基(Baikowski)提供的S15CR粉末来实施一种优异的用于制造透明尖晶石部件的方法。这导致了良好的带材品质和高透明度部件。通过混合126.49克的去离子水、7.66克的30%水性氢氧化铵(赛默飞世尔科技公司(FisherScientific))、62.43克的WB4101粘合剂(聚合物创新有限公司)、1.99克的PL005增塑剂(聚合物创新有限公司)、0.64克的DF002消泡剂(聚合物创新有限公司)和4.60克的DS001分散剂(聚合物创新有限公司)(参见表7A、7B和7C中的批料组合物)在250mL的乐基因(Nalgene)瓶中制备粘合剂体系。封闭该瓶子并对其进行震荡以充分混合粘合剂溶液的成分。使用配备有1400cc涂覆有Tefzel的研磨腔、Lub-R塑料搅拌碟和纯度为99.9%的1mmAl2O3研磨介质的01-HDDM联合工艺碾磨机来制备浆料。将研磨介质和粘合剂溶液加入碾磨机中,启动碾磨机并将速度调至500rpm。在碾磨机运行时添加144.84克的S15CR尖晶石粉末(拜科斯基)。添加粉末后,将研磨速度提升至1300rpm,允许对浆料进行60分钟的研磨。研磨完成后,利用80目的尼龙滤网进行过滤以使浆料与研磨介质分离。使用干燥器腔室和Mazerustar行星式混合器/脱气机对浆料进行脱气。脱气后,将浆料装入一支60mL的注射器中,在该注射器的末端附有11微米的尼龙过滤器,用来在铸塑过程中进行过滤。使用下拉设备在间隙为100微米的铸塑用刮刀下以10毫米/秒的速度将浆料铸塑在涂覆有有机硅的Mylar载膜上。在环境条件下(约70℃,35%的相对湿度)将带材干燥成约50微米的最终厚度。将带材切割成1×1平方英寸的块件,然后堆叠成28层的厚度。将堆叠的层装在两个金属板之间,在空气密封袋中真空密封以用于层压。将这些部件装入已预热至70℃的等静层压机中,以1000psi的压力压制15分钟,然后在4000psi下压制15分钟。将样品从层压机中取出并准备进行烧结。将样品装在耐火架上,在该耐火架的顶部放置有高纯度的氧化铝重物以保持平整度。然后在标准箱式炉中在空气中对样品进行烧制;以120℃/小时的速率加热至180℃并保温2小时,以120℃/小时的速率加热至350℃并保温2小时,以120℃/小时的速率加热至600℃并保温4小时,以120℃/小时的速率加热至1550℃并保温4小时,然后以480℃/小时的速率冷却。然后将样品转移至HIP以进行后续的烧结以除去最终孔隙并实现透明度。在29000psi的氩气下将样品加热至1550℃并保温8小时。在进行氩气HIP后,在Ar/O2混合气中对样品进行烧结以除去氧气空位并且恢复透明度。在80体积%的Ar和20体积%的O2的气氛所形成的混合气中,在5500psi下对样品进行4小时的HIP,然后使其冷却。在完成烧结处理之后,使用1微米的金刚石膜对样品的每个面分别进行4小时的抛光,以除去表面层,实现最终所需的透明度。实施例2(预测性)一种经过带材铸塑的透明尖晶石的制造方法。除了选用不同的尖晶石起始粉末(例如具有6m2/g的估算BET表面积、3.58g/cm3的密度和279nm的估算粒径的TARGETS粉末(参见表10))以外,重复实施例1的方法。带材铸塑得到的产物具有高透明度。通过上述层压处理,制得了4~约28层带材铸塑产物的层压件。比较例2一种经过带材铸塑的透明尖晶石的不成功的制造方法——S30CR粉末;不具有透明度;有裂纹。除了使用不同的尖晶石起始粉末S30CR来代替S15CR、以及对粘合剂含量进行些许改变并且降低含水量以对抗形成裂纹的趋势以外,重复实施例1的方法。使用105.35克的去离子水、5.58克的30%水性氢氧化铵(赛默飞世尔科技公司)、39.86克的WB4101粘合剂(聚合物创新有限公司)、1.22克的PL005增塑剂(聚合物创新有限公司)、1.21克的DF002消泡剂(聚合物创新有限公司)、2.95克的DS001分散剂(聚合物创新有限公司)和92.12克的S30CR尖晶石粉末(拜科斯基)在125mL的乐基因瓶中制备粘合剂体系。所制备的批料是实施例1中所使用的量的一半。按照实施例1中的方法对样品进行研磨、滤除、脱气、过滤、铸塑、层压和烧结。其组成与用于实施例1中的S15粉末的组成相似。比较例2的批料列于表13中。增加粘合剂含量并且降低含水量以试图降低在初始铸塑过程中观察到的会导致开裂的干燥应力。确定需要高粘合剂含量来防止带材开裂。高粘合剂含量使带材中尖晶石的固体负载量降低至无法烧结成具有透明度的数值。表13.比较性的带材铸塑尖晶石。比较例3一种经过带材铸塑的透明尖晶石的不成功的制造方法——S8粉末;不具有透明度;低粘合剂含量。除了选用S8粉末以外,重复实施例1的方法。所使用的与用于实施例1中的S15粉末的组成相似的批料组成列于表14中。所得到的铸塑带材不具有透明度。使用78.00g的去离子水、5.58g的30%水性氢氧化铵(赛默飞世尔科技公司)、26.00克的WB4101粘合剂(聚合物创新有限公司)、1.17克的PL005增塑剂(聚合物创新有限公司)、0.39克的DF002消泡剂(聚合物创新有限公司)、2.98克的DS001分散剂(聚合物创新有限公司)和92.89克的S30CR尖晶石粉末(拜科斯基)在125mL的乐基因瓶中制备粘合剂体系。所制备的批料是实施例1中所使用的量的一半。按照实施例1中所述的方法对样品进行研磨、滤除、脱气、过滤、铸塑、层压和烧结。表14.比较性的带材铸塑尖晶石。以参照各种特定的实施方式和技术对本发明进行了描述。然而,在保持在本发明的范围内还可进行许多修改和变动。当前第1页1 2 3