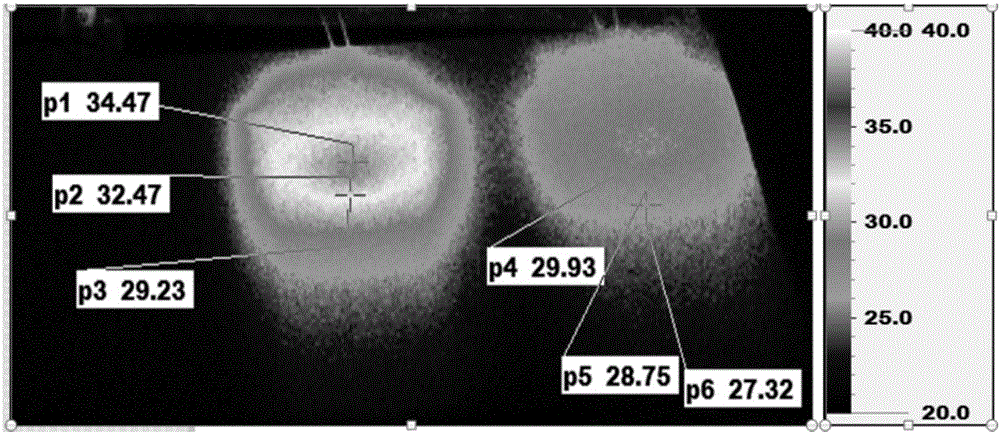
本发明是涉及一种氮掺杂石墨烯的制造方法及其复合式散热片的制造方法,尤其涉及一种利用固相含氮前驱物的氮掺杂石墨烯的制造方法及其复合式散热片的制造方法。
背景技术:
:石墨烯结构于2004年被具体观察发现并加以证实,已为近期碳相关研究中最具潜力和优势的新兴材料。石墨烯指具有一个碳原子至十个碳原子厚度以内的石墨层,为碳-碳共价键连接的六面型网状二维结构,具备良好热传导、电子传导、耐火、高电磁波吸收率及光穿透率等优良特性。此外,石墨烯可由进一步掺杂不同元素来调整材料内部电传导及热传导的性质,以往传统可由氮掺杂石墨烯来制备用于电子元件的复合材料,其氮掺杂步骤均使用液态氮源或氮气来完成,然使用液态氮源如中国专利公开号CN103818895A和CN104229789A内容所示,需于过程中额外添加溶剂,如此不仅可能造成不必要的污染,也会增加材料于制备上步骤程序繁琐的缺点;而使用氮气掺杂则需要较高能量方能使氮元素有效掺杂于石墨烯结构中,故本发明强调的固相制法,不仅具有氮源成本低廉且易于取得的优点,更具备运送及保存容易的优势,且本技术的固相制法在常压下进行即可,能有效降低量产时的困难及危险性,并减少对环境造成的污染。技术实现要素:本发明的主要目的在于提供一种氮掺杂石墨烯的制造方法及一种高导热的复合式散热片的制造方法,其适于工业化连续式生产,复合式散热片可为氮掺杂石墨烯与铜箔、氮掺杂石墨烯与铝基材或是氮掺杂石墨烯与其他相关金属基材的复合散热材。本发明主要针对石墨烯中含氧化官能基结构进行氮掺杂,其中石墨烯的结构组成并无含氮(N),石墨烯先驱物可为膨胀石墨、石墨层间化合物或石墨等的组合。本发明利用添加不同种类的固相氮源,并于 一还原气氛下进行高温烧结,以形成氮掺杂石墨烯,其中固相氮源包括有机及无机固相氮源,以掺杂方式(doping)将氮掺杂进石墨烯的结构中,固相氮源添加除了可对氧进行取代并进行掺杂外,透过本发明也能够使石墨烯增加晶格完整度并提高石墨烯的结晶性以及热传导效率。此外,由于氮掺杂过程在常压下即可进行,可避免石墨烯在氮掺杂过程中因高压而使其晶型结构改变或断裂而造成晶格缺陷,可适用于各种石墨烯材料。本发明可简单、有效地提高石墨烯中碳与碳间的结构完整性,且使用的有机或无机固相氮源具有成本低及易取得的优点,可有效降低制造成本。本发明的另一目的在于利用简单的固相制法,以氮掺杂方式修补石墨烯中的结构缺陷,并且使用工业中最常使用的涂布法,将氮掺杂石墨烯涂布于合适的金属基材上,以形成高导热的复合式散热片,藉此可达到工业化生产的需求。根据上述的目的,首先,本发明提供一种氮掺杂石墨烯的制造方法,包括:利用至少一种固相含氮前驱物与一石墨烯混合,以形成一混合物;以及将该混合物于一还原气氛下进行烧结,以形成一氮掺杂石墨烯。在此,于烧结后,可选择性进行研磨粉碎步骤,以形成氮掺杂石墨烯粉体或其他固相形态的氮掺杂石墨烯。根据上述的目的,接着,本发明提供一种复合式散热片的制造方法,包括:将上述方法所制得的氮掺杂石墨烯与一高分子粘结剂进行混合,以形成一浆料混合物;将该浆料混合物涂布于一金属基材的至少一表面上,以形成一复合材料;将该复合材料置入高温烘箱进行干燥;以及形成一具有一氮掺杂石墨烯薄膜的复合式散热片。在此,该浆料混合物涂布于一金属基材的涂布方式可为单面涂布或双面涂布,涂布膜厚可以是薄的或是厚的。于本发明中,该氮掺杂石墨烯具有以下键结方式:吡啶氮(PyridinicN)(398.1~399.3eV)和石墨氮(GraphiticN)(401.1~402.7eV)。在本发明中,复合式散热片的氮掺杂石墨烯薄膜可以为面向热源或面向远离热源的金属背盖或塑料背盖的方式,利用双面胶将具有氮掺杂石墨烯薄膜的复合式散热片贴在基材上面,以对准热源,可吸收CPU或是电池散发出的热量,将其热量以热传导或热辐射方式导离热源,避免热源残留于电子产品中导致电池效能降低或是电子零件损坏。此外,本发明所载的氮掺杂石墨烯的制备方法也可利用已合成或市售的有机及/或无机固相氮源材料,以氮掺 杂进入石墨烯结构的方式,使石墨烯增加晶格完整度并提高石墨烯的结晶性以及热传导效率,其中石墨烯包括可选自单层石墨烯、多层石墨烯、氧化石墨烯、氧化还原石墨烯及石墨烯衍生物中的至少一种。如前述的氮掺杂石墨烯的制造方法,其中该固相含氮前驱物与该石墨烯可以固相混合方式,以形成该混合物。如前述的氮掺杂石墨烯的制造方法,其中该固相含氮前驱物可为一有机固相氮源、一无机固相氮源或该有机固相氮源与该无机固相氮源的组合来与该石墨烯进行混合,其中该有机固相氮源可选自C6H12N4、C6H5COONH4、(NH4)2CO3、HOC(CO2NH4)(CH2CO2NH4)2、HCO2NH4、C3H3N6、C11H7N、C10H6(CN)2及C12H7NO2中的至少一种,而该无机固相氮源则可选自NH4NO3及其他无机硝酸盐类中的至少一种。如前述的氮掺杂石墨烯的制造方法,其中该石墨烯较佳选自单层石墨烯、多层石墨烯、氧化石墨烯、氧化还原石墨烯及石墨烯衍生物中的至少一种。如前述的氮掺杂石墨烯的制造方法,其中该氮掺杂石墨烯较佳具有吡啶氮(PyridinicN)(398.1~399.3eV)和石墨氮(GraphiticN)(401.1~402.7eV)的键结方式。如前述的氮掺杂石墨烯的制造方法,以该石墨烯与该固相含氮前驱物混合的总重量做为基准,该固相含氮前驱物与该石墨烯混合的重量比值较佳为1以上。如前述的氮掺杂石墨烯的制造方法,其中该石墨烯与该固相含氮前驱物混合的重量比例较佳为1:1至1:30。如前述的氮掺杂石墨烯的制造方法,其中该氮掺杂石墨烯的氮含量范围较佳为0.04-5wt%。如前述的氮掺杂石墨烯的制造方法,其中该混合物较佳于300℃至800℃的温度下进行烧结。如前述的氮掺杂石墨烯的制造方法,其中该混合物进行烧结的时间较佳为0.5~10小时。如前述的复合式散热片的制造方法,其中该高分子粘结剂较佳为羧甲基纤维素(CMC)。如前述的复合式散热片的制造方法,其中该浆料混合物更可包括添加一 导电剂、一胶粘剂或其组合,其中该导电剂的具体举例包括但不限于,KS-6(导电石墨)、Super-P(导电碳黑);该胶粘剂的具体举例包括但不限于SBR(丁苯橡胶)。如前述的复合式散热片的制造方法,其中该浆料混合物中的氮掺杂石墨烯含量较佳为50-93wt%,更佳为89-92wt%。如前述的复合式散热片的制造方法,该金属基材较佳为一铜箔。如前述的复合式散热片的制造方法,其中该氮掺杂石墨烯薄膜的厚度较佳为15-65μm。附图说明图1为根据本发明测试例1-5、7-9、12及实施例12-14所述的复合式散热片结构示意图;图2为根据本发明测试例1-5、7-9、12及实施例12-14所述的复合式散热片的散热测试装置示意图;图3A为根据本发明对照例所述的石墨烯材料的SEM图;图3B为根据本发明所述的氮掺杂石墨烯材料的XPS键结能量图;图3C为根据本发明实施例6所述的氮掺杂石墨烯材料的XPS键结能量图;图4为根据本发明测试例6、10-11及13所述的复合式散热片结构示意图;图5为根据本发明测试例5未氮掺杂的石墨烯涂布铜箔金像显微镜;图6为本发明实施例12所述的具有氮掺杂石墨烯薄膜的复合式散热片(左)与单纯铜箔(右)的整体区域观察的温度分布变化图。附图标记说明:100、200-复合式散热片101-氮掺杂石墨烯薄膜102-铜箔103-双面胶105-铜片106-基材107-加热芯片108-第一测试点109-第二测试点110-感温点111-锡箔纸具体实施方式以下以特定的具体实施例说明本发明的实施方式,本领域技术人员可由本说明书所公开的内容轻易地了解本发明的其他优点与功效。本发明也可以其他不同的具体实施例加以施行或应用,本说明书中的各项细节也可基于不同观点与应用,在不悖离本发明的精神下进行各种修饰与变更。下文中的说明,仅针对本发明的氮掺杂石墨烯、其制造方法及包括其的测试装置使用时的功能实现以及氮掺杂石墨烯、其制造方法及包括其的不同膜厚、单双面涂布与膜面方向所产生的功效进行详细说明。此外,于下述内文中的图式,也并未依据实际的相关尺寸完整绘制,其作用仅在表达与本发明特征有关的示意图。本发明提供一种氮掺杂石墨烯,具有以下化学键结方式:吡啶氮(PyridinicN)(398.1~399.3eV)和石墨氮(GraphiticN)(401.1~402.7eV)。其中固相氮源可包括有机及无机固相氮源,有机氮源包括C6H12N4(HMT)、C6H5COONH4、(NH4)2CO3、HOC(CO2NH4)(CH2CO2NH4)2、HCO2NH4、C3H3N6、C11H7N、C10H6(CN)2、C12H7NO2等;无机氮源包括NH4NO3等其他无机硝酸盐。此外,本发明所记载的氮掺杂石墨烯的制备方法可利用以机械剥离法或氧化还原法制备而得的石墨烯,与有机及/或无机固相氮源混合后,以氮掺杂方式进入石墨烯结构中,使石墨烯增加晶格完整度并提高石墨烯的结晶性以及热传导效率,其中石墨烯可选自单层石墨烯、多层石墨烯、氧化石墨烯、氧化还原石墨烯及石墨烯衍生物中的至少一种。请参阅图1及图2,为本发明测试例1-5、7-9、12及实施例12-14所述的复合式散热片的结构示意图及测试治具示意图,如图所示:复合式散热片100包括铜箔102以及氮掺杂石墨烯层101,其设置于铜箔102的一表面上。本发明提供一种温度差测试法,步骤如下:将复合式散热片100中的铜箔102的一表面贴上一层双面胶103或其他黏性材料,再将复合式散热片100与双面胶103贴附于基材106上,放置于测试治具中进行温度测试,测试治具可视为模拟3C产品中 的平板电脑,在测试治具中提供一个1*1cm2大小的加热芯片107并贴附于铜片105上,视为模拟CPU的运作,下方贴上锡箔纸111视为其他电子零件,此测试治具中含有三个测试温度的感测点,分别为加热芯片107上的感温点110、加热芯片107正上方的上方基材106上的第一测试点108、与第一测试点108相距0.5-5cm处的第二测试点109。本温度差测试法利用单纯铜箔102的第一测试点108与第二测试点109的温度差T1(℃)及复合式散热片100的第一测试点108与第二测试点109的温度差T2(℃)间的温度差T1-T2(℃)进行判断(在此,是以第一测试点108与第二测试点109间的水平距离0.5cm作实际测试,但本发明不以此为限。在图2中,感温点110的温度大于第一测试点108的温度,第一测试点108的温度大于第二测试点109的温度,当复合式散热片100具有良好散热效果时,代表其可有效将热导离加热芯片107,使第一测试点108和第二测试点109的温度较为接近,此时复合式散热片100的第一测试点108和第二测试点109的温度差T2(℃)相对较为小,单纯铜箔102的第一测试点108与第二测试点109的温度差T1(℃)则相对较大,使得T1(℃)大于T2(℃)。因此,当T1-T2(℃)为正值时,代表复合式散热片100具有良好散热效果,正值越大代表散热效果越佳。首先,取1g石墨烯,以XPS(X-射线光电子光谱)进行内部氮含量百分比、氧含量百分比与碳含量百分比的数值界定(请参见下表1中对照例所列的数值),以作为下述实施例1-7成分分析的比对基准;此外,该石墨烯(对照例)的SEM图(扫描式电子显微镜)请见图3A。石墨烯可为粉体或其他固态形式,本发明不以此为限。本发明实施例1提供一种氮掺杂石墨烯的结构及其制备方法,步骤如下:取1g石墨烯与1g固相HMT(Hexamethylenetetramine,C6H12N4)均匀混合之后研磨后放入坩锅(也可于均匀混合后直接放入坩锅,不经过研磨,本发明不以此为限),置入高温炉,于H2/N2的还原气氛下在800℃烧结8hr,从高温炉中取出后即可得氮掺杂石墨烯。氮掺杂石墨烯可为粉体或其他固态形式,本发明不以此为限。接着以XPS来分析实施例1的氮掺杂石墨烯,判断经过氮掺杂后得到氮含量百分比、氧含量百分比与碳含量百分比的数值,结果如下表1所示。本发明实施例2-7提供一种氮掺杂石墨烯的结构及其制备方法,其中,制备方法的步骤、条件及固相含氮前驱物种类均与实施例1相同,差异在于实施 例2-7分别加入不同重量比的固相HMT,加入的重量比为石墨烯:固相HMT分别为1:3、1:5、1:7、1:10、1:20或1:30,接着以XPS来分析实施例2-7的氮掺杂石墨烯中的氮含量百分比、氧含量百分比与碳含量百分比的数值,结果如下表1所示,键结能量请参见图3B与图3C。实施例6是对照例额外添加20wt%固相HMT后所得到的结果,相较于对照例,其相对氮含量百分比增加了3.92%(如下表1所示)。请继续参见图3C,图3C根据本发明实施例6所述的氮掺杂石墨烯的XPS键结能量图,从图3C得知,实施例6的氮掺杂石墨烯的键结方式包括吡啶氮(PyridinicN)(398.1~399.3eV)与石墨氮(GraphiticN)(401.1~402.7eV),相较于键结方式主要以C与O的方式键结的对照例,实施例6的氮掺杂石墨烯的键结方式多了C与N的键结方式,由于C与N的键结存在可降低石墨烯结构中的缺陷比例,因此实施例6可获得更好的热传导效果(良好散热效果),以此类推,实施例1、2-5、7的氮掺杂石墨烯同样均可达到较佳的热传导效果(良好散热效果)。在本发明中,该氮掺杂石墨烯的氮含量范围为0.04-5wt%,较佳氮含量范围为2-5wt%,最佳氮含量范围为4wt%。本发明实施例8-11提供一种氮掺杂石墨烯的结构及其制备方法,其中,制备方法的步骤、条件及石墨烯与固相含氮前驱物混合的重量比例均与实施例1相同,差别在于实施例8-11分别加入不同的有机及/或无机固相氮源,加入的有机及/或无机固相氮源分别为(NH4)2CO3、NH4NO3、HCO2NH4、C3H3N6,如下表2所述。接着以XPS来分析实施例8-11的氮掺杂石墨烯,以得到氮掺杂石墨烯中的氮含量百分比、氧含量百分比与碳含量百分比的数值,结果如下表2所示。表1:对照例和实施例1-7的氮掺杂石墨烯成分表表2:实施例8-11的氮掺杂石墨烯成分表实施例固相氮源Cwt.%Owt.%Nwt.%8(NH4)2CO390.578.211.149NH4NO391.788.220.0410HCO2NH492.376.251.311C3H3N689.177.473.36本发明测试例1-13提供一种未氮掺杂石墨烯薄膜的复合式散热片结构,结构示意图请参见图1,与实施例1-11的差异在于图1中的氮掺杂石墨烯薄膜101为未氮掺杂石墨烯薄膜。如图1及下表3所示,先针对未氮掺杂石墨烯浆料混合物(其使用对照例的未氮掺杂石墨烯,且另外包括KS-6、Super-P、CMC、SBR等非必要成份)测试在不同石墨烯重量含量、石墨烯浆料混合物厚度及石墨烯浆料混合物为单或双面涂布于铜箔102的散热性效果,找出最佳条件后,再进行氮掺杂石墨烯的散热性测试,由于氮掺杂石墨烯的键结方式多了C与N的键结方式,可降低石墨烯结构中的缺陷比例,故氮掺杂石墨烯可得到相较未氮掺杂石墨烯更佳的散热效果,其中测试例1-13的制备步骤均大致相同,差异仅在于测试例1-13分别加入不同比例的石墨烯、高分子粘结剂(CMC)、导电剂(KS-6、Super-P)、胶粘剂(SBR),依照石墨烯相较整体浆料混合物重量的比例分别为50、60、70、80、89、92、93wt%来进行测试。如表3所示,根据不 同含量的石墨烯进而改变KS-6、Super-P、CMC与SBR的添加量,为避免重复叙述相似内容,以下仅以测试例5作具体说明,而测试例1-4及6-13则可根据测试例5所述的内容及下表3所示的条件而制成。本发明测试例5提供一种未氮掺杂石墨烯薄膜的复合式散热片结构及其制备方法,步骤如下:取1.5g石墨烯、0.1011gCMC、0.0506gSuper-P与0.0337gSBR,利用水当作溶剂将上方四种材料依序加入均质搅拌机中均匀混合,将混合后的浆料混合物倒在铜箔102上,利用涂布机将浆料混合物涂布在铜箔102上方,将涂布后的复合材料置入高温烘箱中,以40~100℃烘烤去除浆料混合物中的水分,再将复合材料进行厚度的测试,并以适当的辗压率辗压至50μm,即可形成具有未氮掺杂石墨烯薄膜101的复合式散热片100。接着,请参见图2,将测试例1-5、7-9及12以单面涂布所获得具有未氮掺杂石墨烯薄膜101的复合式散热片100(如图1所示)贴上一层双面胶103或其他黏性材料,再将具有未氮掺杂石墨烯薄膜101的复合式散热片100与双面胶103贴附于基材106上,放置于如图2所示的测试治具中,并提供3W能量的加热芯片107进行加温,以进行单纯铜箔102的第一测试点108和第二测试点109的温度差T1(℃)与具有未氮掺杂石墨烯薄膜101的复合式散热片100的第一测试点108和第二测试点109的温度差T2(℃)间的温度差T1-T2(℃)判断;测试例6、10-11及13则是以双面涂布制得如图4所示的具有未氮掺杂石墨烯薄膜101的复合式散热片200(于铜箔102两相对表面上分别均涂布一未氮掺杂石墨烯薄膜101),其同样是以图2所示的测试治具进行温度差T1-T2(℃)测试(测试例6、10-11及13仅是将图2的具有未氮掺杂石墨烯薄膜101的复合式散热片100置换成图4所示的具有未氮掺杂石墨烯薄膜的复合式散热片200,其他条件均如上所述),结果如下表3所示。如下表3所示,测试例5是测试例1中的石墨烯添加量增加约40wt.%后得到的结果,相较于测试例1,在涂布厚度减少10μm的情况下,其散热效果能力反而提升1.27℃,请继续参见图5,图5根据本发明测试例5所述具有未氮掺杂石墨烯薄膜101单面涂布铜箔102的金像显微镜照片,可以发现在高含量的石墨烯的添加量下,石墨烯与其他添加物的分散均匀性也相对提高,因此相对于低含量石墨烯添加的结果其散热能力也随之提升。本发明测试例10及13控制石墨烯含量比例为60wt.%且KS-6、Super-P、 CMC与SBR的含量比例与涂布方式(双面)均为相同条件,但以不同涂布厚度的散热效果比较。测试例13相较于测试例10,其散热效果能力上升0.7℃,可以发现未氮掺杂石墨烯薄膜增厚相对地石墨烯含量也随的增加,因此相应于双面涂布下涂布较薄的未氮掺杂石墨烯薄膜结果,其散热能力也随之提升。本发明测试例12及13控制石墨烯含量比例为60wt%且KS-6、Super-P、CMC与SBR的含量比例与未氮掺杂石墨烯涂布厚度均为相同条件,但以不同涂布方式的散热效果比较。测试例13相较于测试例12,其散热效果能力上升0.8℃。由此可发现在双面涂布下,其中一面未氮掺杂石墨烯薄膜101作为吸热面,而另一面未氮掺杂石墨烯薄膜101作为散热面,因此相应于单面涂布的散热结果其散热能力也随之提升。表3:测试例1至13的具有未氮掺杂石墨烯薄膜的复合式散热片的散热效果测试表本发明实施例12提供一种具有氮掺杂石墨烯薄膜的复合式散热片结构及其制备方法,其中,制备方法的步骤及条件与测试例5相同,差异在于实施例12采用实施例6所制得的氮掺杂石墨烯,其添加含量为89wt%且KS-6、Super-P、CMC与SBR的含量比例、涂布厚度与涂布方式均为相同条件,如下表4所示根据有无氮掺杂后的散热结果进行比较。接着,请参见图2,将实施例12所获得的具有氮掺杂石墨烯薄膜101的复合式散热片100(如图1所示)贴上一层双面胶103或其他黏性材料,再将具有氮掺杂石墨烯薄膜101的复合式散热片100与双面胶103贴附于基材106上,放置于如图2所示的测试治具中,并提供3W能量的加热芯片107进行加温,以进行单纯铜箔102的第一测试点108和第二测试109的温度差T1(℃)与具有氮掺杂石墨烯薄膜101的复合式散热片100的第一测试点108和第二测试点109的温度差T2(℃)间的温度差T1-T2(℃)判断,较佳结果如表4所示。实施例12是测试例5在单面涂布下将石墨烯改为氮掺杂石墨烯后得到的结果,实施例12相较于测试例5,其散热效果能力上升1.4℃,因此相应于未氮掺杂石墨烯的结果其散热能力也随之提升。本发明实施例13-14提供一种具有氮掺杂石墨烯薄膜的复合式散热片结构及其制备方法,其中,制备方法的步骤及条件均与测试例5相同,差异在于实施例13-14采用实施例6所制得的氮掺杂石墨烯,其中实施例13-14的氮掺杂石墨烯添加量分别为89wt%与92wt%,实施例13的Super-P、CMC与SBR的含量比例分别为3wt.%、6wt.%与2wt.%,实施例14的Super-P、CMC与SBR的含量比例分别为0wt.%、8wt.%与0wt.%,实施例13-14的涂布厚度均为15μm,涂布方式均为单面涂布,如表4根据氮掺杂石墨烯的含量比例不同的散热结果进行比较。接着,请参见图2,将实施例13-14所获得的具有氮掺杂石墨烯薄膜101的复合式散热片100(如图1所示)贴上一层双面胶103或其他黏性材料,再将具有氮掺杂石墨烯薄膜101的复合式散热片100与双面胶103贴附于基材106上,放 置于如图2所示的测试治具中,并提供3W能量的加热芯片107进行加温,在此将加热芯片107的温度提高15℃,以进行铜箔102的第一测试点108和第二测试点109的温度差T1(℃)与具有氮掺杂石墨烯薄膜101的复合式散热片100的第一测试点108和第二测试点109的温度差T2(℃)间的温度差T1-T2(℃)判断,较佳结果如表4所示。实施例13相较于实施例14,其散热效果能力上升0.2℃,其原因在于添加Super-P有助于填补氮掺杂石墨烯堆迭过程中的空隙,因此相应于未添加Super-P的氮掺杂石墨烯的结果其散热能力也随的提升。另于表4中测试例5和实施例12-14的结果可发现,当将加热芯片107温度增加至90℃时,氮掺杂石墨烯会因高温导致内部分子振动频率增加,造成涂布的氮掺杂石墨烯薄膜101与铜箔102间的接触面积减少,使散热效果降低,但就算加热芯片107的温度提高至90℃,如实施例13-14所示,本发明实施例13-14的温度差T1-T2(℃)为正值,仍优于单纯使用铜箔102的散热效果,可有效提升散热效果能力约0.2-0.4℃。表4:测试例5和实施例12-14的具有未氮掺杂或氮掺杂石墨烯薄膜的复合式散热片的散热效果测试表本发明图6提供一种具有氮掺杂石墨烯薄膜的复合式散热片结构及其测试方法,为一种区域温度分布变化的整体观察结果,同样以图2所示的温度差 测试治具,提供3W能量的加热芯片107进行加温,并利用热成像仪观察在5分钟加热后的整体区域温度分布变化。P1及P4为加热芯片107正上方的感测点,P2及P3为P1分别向外延伸1及2公分的感测点,P5及P6为P4分别向外延伸1及2公分的感测点,温度越高者代表可有效将热以垂直及水平方式传导至远离热源位置。图6中的左图及右图分别为以实施例12制得的具有氮掺杂石墨烯薄膜101的复合式散热片100与铜箔102的散热效果比较。由热成像仪观察结果可看出,具有氮掺杂石墨烯薄膜101的复合式散热片100,可以提升热辐射吸收与热传导效率。在图6中,经5分钟加热后,具有氮掺杂石墨烯薄膜101的复合式散热片100的P1-P3的温度均高于铜箔102的P4-P6的温度,表示本发明的具有氮掺杂石墨烯薄膜101的复合式散热片100的垂直(P1高于P4的温度)与平面(P3高于P6温度)的热辐射吸收及热传导效率增加,相较右图的铜箔102具有较佳散热效果。当前第1页1 2 3