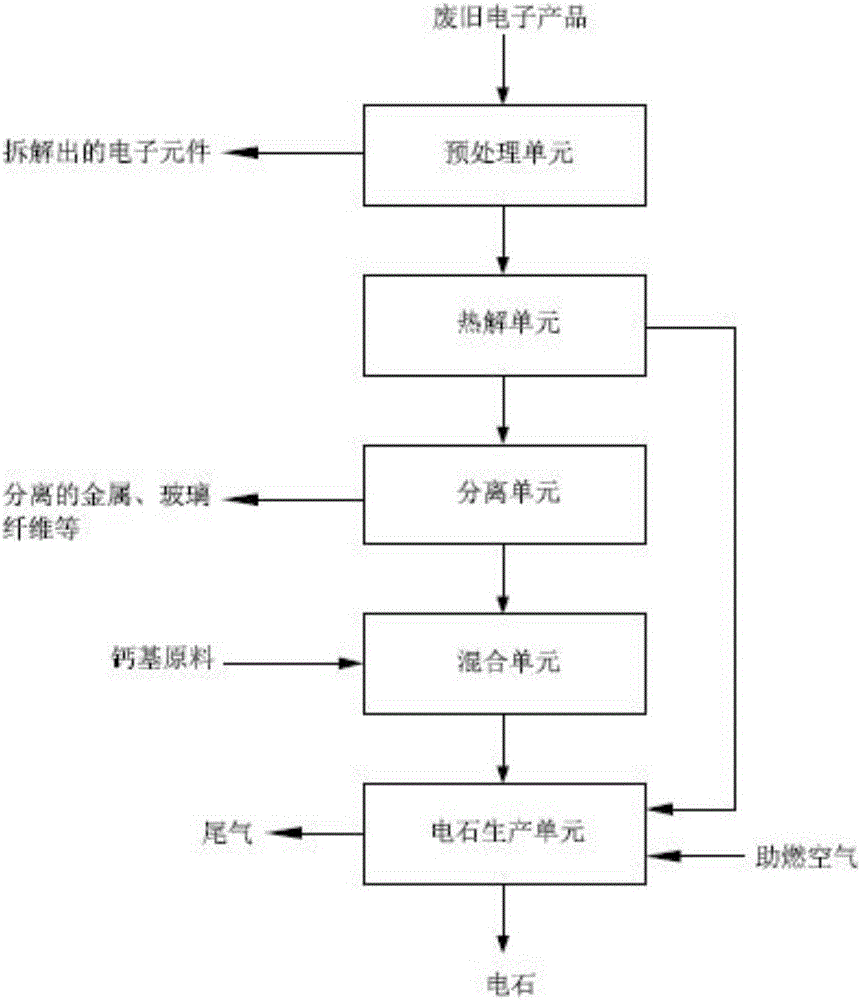
本发明属于固体废弃物资源化处理领域,尤其涉及一种处理废旧电子产品的系统和方法。
背景技术:
:随着科技的高速发展,废弃电子产品及电子产品加工过程中形成的边角料也与日俱增。在发达国家如日本、美国、欧盟电子垃圾年产量分别占城市垃圾的1%,2-5%和4%,并且以每5年16%-28%的速度增长,是城市垃圾增长速度的3-5倍。这种情况在我国尤为严重,我国不但人口众多,同时还是发达国家倾销电子垃圾的主要场所,资料显示美国80%的电子垃圾出口到亚洲,其中90%进入我国。国内外关于废电路板回收处理的技术主要包括机械物理分离法、湿法冶金技术、生物冶金技术和热解技术,这些技术除热解外大部分都关注于回收废旧印刷线路板中的金属。其中机械物理分离法易规模化,且对环境的污染相对较小,但各种金属无法彻底分离,剩余有机物或者填埋或者焚烧,不仅浪费资源而且环境污染严重;湿法冶金的金属回收率高,但是化学试剂消耗较大,工艺复杂,线路板中的高分子有机化合物同样没有得到回收利用;生物冶金技术目前还处于研究阶段,适合的细菌非常少而且很难培养;相比较而言,通过热解技术高温分解及物理分离方法的结合,不仅能有效回收废旧电子产品中的金属还能利用其中的高分子有机材料,将其分解为燃油、燃气和炭化物,同时由于电子产品中的非金属多为环氧树脂等高分子塑料,热解产品的碳化物含碳量高,适合作为化工原料使用。电石学名碳化钙,无色晶体,主要用于生产乙炔气,曾被称为“有机合成工业之母”。乙炔是重要的化工原料,主要用于生产聚氯乙烯基和醋酸乙烯基产品,我国PVC产品70%的生产原料乙炔来自于电石,电石对我国的经济发展具有十分重要的作用,近十余年来的产量不断增长,2013年产量达2200万吨以上。电石生产工艺主要有电热法和氧热法。无论是电热法还是氧热法,均需要兰炭或无烟煤或焦炭等优质的含碳原料作为电石生产的碳基原料,导致电石生产原料成本居高不下,另外,由于单位含碳燃料不完全燃烧的放热量较小,故需要燃烧大量含碳燃料供给热量,产生较多灰分富集到电石产物中,极大影响电石产物品质。如何降低电石生产成本,增加电石企业收益,成为我国电石行业发展难题之一。目前处理废旧电子产品通常采用简单热解方法,并给出热解后金属的回收方法,但此法忽视了热解过程中热解气、热解炭等产品的利用,并未达到资源利用的最大化,同时真空热解对设备要求较高,很难实现工业化。如上可见,现有技术中存在如下问题:废旧电子产品处理对非金属物质的回收资源化水平不够;废旧电子产品热解处理多作为预处理手段,热解产品后续利用技术缺乏;电石生产需要大量焦炭和热能/电能,原料成本高,能耗高;采用氧热法燃烧后的灰分富集到电石产物中,影响电石产物品质。技术实现要素:为解决上述问题,本发明旨在将废旧电子产品的资源化回收处理和电石生产工艺耦合在一起,并利用热解废旧电子产品产生的高温油气为电石生产提供热量,同时实现对废旧电子产品的资源化回收利用和降低电石生产成本并降低电石灰分含量的目的。为实现上述目的,本发明提出了一种处理废旧电子产品的系统,该系统包括:预处理单元、热解单元、分离单元、混合单元和电石生产单元,其中,所述预处理单元包括拆解单元和破碎单元,所述拆解单元包括废旧电子产品入口和拆解产物出口,所述破碎单元包括拆解产物入口和预处理产物出口,所述拆解产物入口和所述拆解产物出口相连;所述热解单元包括预处理产物入口、固体含碳物出口和高温油气出口,所述预处理产物入口和所述预处理产物出口相连;所述分离单元包括固体含碳物入口和热解炭出口,所述固体含碳物入口和所述固体含碳物出口相连;所述混合单元包括热解炭入口、钙基原料入口和混合产物出口,所述热解炭入口和所述热解炭出口相连;所述电石生产单元包括高温油气入口、混合产物入口和电石产物出口,所述高温油气入口和所述高温油气出口相连,所述混合产物入口和所述混合产物出口相连。具体的,所述分离单元为风选单元、磁选单元或静电分选单元的一种或者其组合;所述固体含碳物出口设有密封出料装置。进一步的,所述电石生产单元包括电石尾气出口;所述系统还包括气体净化和除尘单元,所述气体净化和除尘单元包括电石尾气入口,所述电石尾气入口和所述电石尾气出口相连。更进一步的,所述电石生产单元还包括助燃气入口,通过所述助燃气入口将助燃气引入辅助燃烧。本发明还提供一种处理废旧电子产品的方法,包括如下步骤:A预处理:在所述预处理单元通过将废旧电子产品拆解和破碎,得到预处理产物;B热解:将所述预处理产物给入所述热解单元内进行热解反应,生成高温油气和固体含碳物,所述高温油气通过在热解炉设置的油气管道收集,所述固体含碳物经出口出料;C分离:将所述固体含碳物经过细破碎、分选分离,获得热解炭;D混合:将所述热解炭与钙基原料混合,得到混合后产物;E电石生产:将所述混合后产物送入电石炉内进行反应,反应结束后得到电石。具体的,在所述步骤E中,以所述步骤B中的所述高温油气作为燃料,以多个电极和多个燃烧器组合作为电石炉的热源,进行所述电石炉内的反应;还向所述高温油气中另加入助燃气辅助燃烧。作为优选的实施方案,将所述步骤A中所述预处理产物的粒度控制为20-100mm。具体的,所述步骤D中所述钙基原料为选自石灰、石灰石、熟石灰或电石渣中的一种或几种。作为优选的实施方案,所述步骤B中所述热解反应的温度为450-850℃,热解时间为0.5-3h。进一步的,所述步骤E中所述混合后产物热送至电石炉的温度为400-800℃。利用本发明的上述系统和方法,通过将废旧电子产品的资源化回收处理和电石生产工艺耦合在一起,并利用废旧电子产品高温油气为电石生产提供热量,本发明取得了以下效果:(1)实现了废旧电子产品的清洁高效资源化处理;(2)有利于废旧电子产品中金属、非金属、玻璃纤维的分离回收;(3)实现了废旧电子产品热解产品的高值化利用;(4)能够使用价格低廉的原料,降低电石生产原料成本;(5)热解高温油气燃烧作为电石生成补充热源,降低电耗。本发明的附加方面和优点将在下面的描述中部分给出,部分将从下面的描述中变得明显,或通过本发明的实践了解到。附图说明图1是本发明的处理废旧电子产品的系统结构示意图。图2是本发明的处理废旧电子产品的工艺流程图。具体实施方式以下结合附图和实施例,对本发明的具体实施方式进行更加详细的说明,以便能够更好地理解本发明的方案及其各个方面的优点。然而,以下描述的具体实施方式和实施例仅是说明的目的,而不是对本发明的限制。在本发明的一个方面,本发明提出了一种处理废旧电子产品的系统,该系统包括预处理单元、热解单元、分离单元、混合单元和电石生产单元:A预处理单元:包括拆解、破碎,根据废旧电子产品原料的不同,废旧电子产品可回收元件拆解回收,粗破碎,破碎粒度为20-100mm。B热解单元:将经过预处理的废旧电子产品原料均匀给入热解炉内进行热解反应,热解温度为450-850℃,热解时间为0.5-3h,热解反应完全后生成高温油气和固体含碳物,高温油气通过在热解炉设置的油气管道收集送入电石生产单元,高温油气温度为400-800℃,固体含碳物经密封出料装置出料。C分离单元:包括细破碎、风选、磁选、静电分选的一种或几种。由于废旧电子产品经过热解反应,其中非金属有机物热解为热解炭,金属及玻璃纤维不发生反应,热解后的固体含碳物比原始电子产品更易实现分离,固体含碳物产率为5%-20%,来自热解单元的固体含碳物经过分离单元分离为金属、玻璃纤维和热解炭。D混合单元:由于废旧电子产品中的非金属多为环氧树脂等高分子有机材料,热解后分出的热解炭灰分低,固定碳含量高,适于作为电石生产的碳基原料,将来自热解单元的热解炭与钙基原料(石灰、石灰石、熟石灰或电石渣之一或几种混合物)混合。E电石生产单元:将混合后产物送入电石炉内,热送温度400-800℃,电石炉采用多个电极和多个燃烧器组合,为电石原料提供热源,其中燃烧器作为电极的补充热源,燃料为来自热解单元的高温油气,补充助燃气燃烧,燃烧产物无灰分,不会降低电石产品品质,电石炉温度为1700-2200℃,反应时间5~50min,电石尾气进入气体净化、除尘单元,电石产物出料口出料。下面参考具体实施例,对本发明进行描述,需要说明的是,这些实施例仅仅是描述性的,而不以任何方式限制本发明。实施例1本实施例提出了一种处理废旧电子产品的系统,该系统包括预处理单元、热解单元、分离单元、混合单元和电石生产单元:A预处理:对废旧电子产品可回收元件进行拆解回收,粗破碎,破碎粒度为100mm。B热解:将经过破碎的废旧电路板原料均匀给入热解炉内进行热解反应,热解温度为850℃,热解时间为0.5h,热解反应完全后生成高温油气和固体含碳物,高温油气通过在热解炉设置的油气管道收集送入电石生产单元,高温油气温度为600℃,固体含碳物经出口出料。C分离:来自热解单元的固体含碳物经过细破碎、风选、磁选分离为金属、玻璃纤维和热解炭。其中热解炭含量为原始废旧电子产品的10%。热解炭性质如下:表1热解炭主要性质项目单位数值备注水分wt%1.13收到基固定碳wt%83.77收到基挥发分wt%9.5收到基灰分wt%5.6收到基D混合:将来自分离单元的热解炭与石灰混合均匀。E电石生产:将混合后产物送入电石炉内,热送温度为700℃,电石炉采用多个电极和多个燃烧器组合,为电石原料提供热源。其中燃烧器作为电极的补充热源,燃料为来自热解单元的高温油气,补充助燃气燃烧,电石炉温度为2200℃,反应时间20min,电石尾气进入气体净化、除尘单元,电石产物出料口出料,产品电石中碳化钙含量78.43%,发气量287L/kg。实施例2本实施例与上述实施例1所用系统一样,但工艺条件不同,如下所述:A预处理:对废旧电子产品可回收元件进行拆解回收,粗破碎,破碎粒度为20mm。B热解:将经过破碎的废旧电路板原料均匀给入热解炉内进行热解反应,热解温度为650℃,热解时间为2h,热解反应完全后生成高温油气和固体含碳物,高温油气通过在热解炉设置的油气管道收集送入电石生产单元,高温油气温度为550℃,固体含碳物经出口出料。C分离:来自热解单元的固体含碳物经过细破碎、风选、磁选分离为金属、玻璃纤维和热解炭,其中热解炭含量为原始废旧电子产品的14%。热解炭性质如下:表2热解炭主要性质项目单位数值备注水分wt%1.27收到基固定碳wt%83.54收到基挥发分wt%10.2收到基灰分wt%4.99收到基D混合:将来自分离单元的热解炭与熟石灰混合均匀。E电石生产:将混合后产物送入电石炉内,热送温度为580℃,电石炉采用多个电极和多个燃烧器组合,为电石原料提供热源。其中燃烧器作为电极的补充热源,燃料为来自热解单元的高温油气,补充助燃气燃烧,电石炉温度为1700℃,反应时间30min,电石尾气进入气体净化、除尘单元,电石产物出料口出料。产品电石中碳化钙含量77.09%,发气量285L/kg。实施例3本实施例与上述实施例1所用系统一样,但工艺条件不同,如下所述:A预处理:对废旧电子产品可回收元件进行拆解回收,粗破碎,破碎粒度为60mm。B热解:将经过破碎的废旧电路板原料均匀给入热解炉内进行热解反应,热解温度为450℃,热解时间为3h,热解反应完全后生成高温油气和固体含碳物,高温油气通过在热解炉设置的油气管道收集送入电石生产单元,高温油气温度为400℃,固体含碳物经出口出料。C分离:来自热解单元的固体含碳物经过细破碎、风选、磁选分离为金属、玻璃纤维和热解炭。其中热解炭含量为原始废旧电子产品的18%。热解炭性质如下:表3热解炭主要性质项目单位数值备注水分wt%1.16收到基固定碳wt%80.07收到基挥发分wt%13.1收到基灰分wt%5.67收到基D混合:将来自分离单元的热解炭与电石渣混合均匀。E电石生产:将混合后产物送入电石炉内,热送温度为800℃,电石炉采用多个电极和多个燃烧器组合,为电石原料提供热源。其中燃烧器作为电极的补充热源,燃料为来自热解单元的高温油气,补充助燃气燃烧,电石炉温度为1900℃,反应时间50min,电石尾气进入气体净化、除尘单元,电石产物出料口出料。产品电石中碳化钙含量77.11%,发气量281L/kg。实施例4本实施例与上述实施例1所用系统一样,但工艺条件不同,如下所述:A预处理:对废旧电子产品可回收元件进行拆解回收,粗破碎,破碎粒度为70mm。B热解:将经过破碎的废旧电路板原料均匀给入热解炉内进行热解反应,热解温度为750℃,热解时间为1h,热解反应完全后生成高温油气和固体含碳物,高温油气通过在热解炉设置的油气管道收集送入电石生产单元,高温油气温度为600℃,固体含碳物经出口出料。C分离:来自热解单元的固体含碳物经过细破碎、风选、磁选分离为金属、玻璃纤维和热解炭。其中热解炭含量为原始废旧电子产品的12%。热解炭性质如下:表4热解炭主要性质项目单位数值备注水分wt%1.16收到基固定碳wt%83.61收到基挥发分wt%9.8收到基灰分wt%5.43收到基D混合:将来自分离单元的热解炭与石灰石混合均匀。E电石生产:将混合后产物送入电石炉内,热送温度为400℃,电石炉采用多个电极和多个燃烧器组合,为电石原料提供热源。其中燃烧器作为电极的补充热源,燃料为来自热解单元的高温油气,补充助燃气燃烧,电石炉温度为1800℃,反应时间5min,电石尾气进入气体净化、除尘单元,电石产物出料口出料。产品电石中碳化钙含量78.11%,发气量284L/kg。从上述实施例可见,本发明实现了废旧电子产品的清洁高效资源化处理;有利于废旧电子产品中金属、非金属、玻璃纤维的分离回收;实现了废旧电子产品热解产品的高值化利用;能够使用价格低廉的原料,降低电石生产原料成本;利用高温油气燃烧作为电石生成补充热源,降低电耗。尽管上面已经示出和描述了本发明的实施例,可以理解的是,上述实施例是示例性的,不能理解为对本发明的限制,本领域的普通技术人员在本发明的范围内可以对上述实施例进行变化、修改、替换和变型。本发明公开的内容论及的是示例性实施例,在不脱离权利要求书界定的保护范围的情况下,可以对本申请的各个实施例进行各种改变和修改。因此,所描述的实施例旨在涵盖落在所附权利要求书的保护范围内的所有此类改变、修改和变形。此外,除上下文另有所指外,以单数形式出现的词包括复数形式,反之亦然。另外,除非特别说明,那么任何实施例的全部或一部分可结合任何其它实施例的全部或一部分使用。当前第1页1 2 3