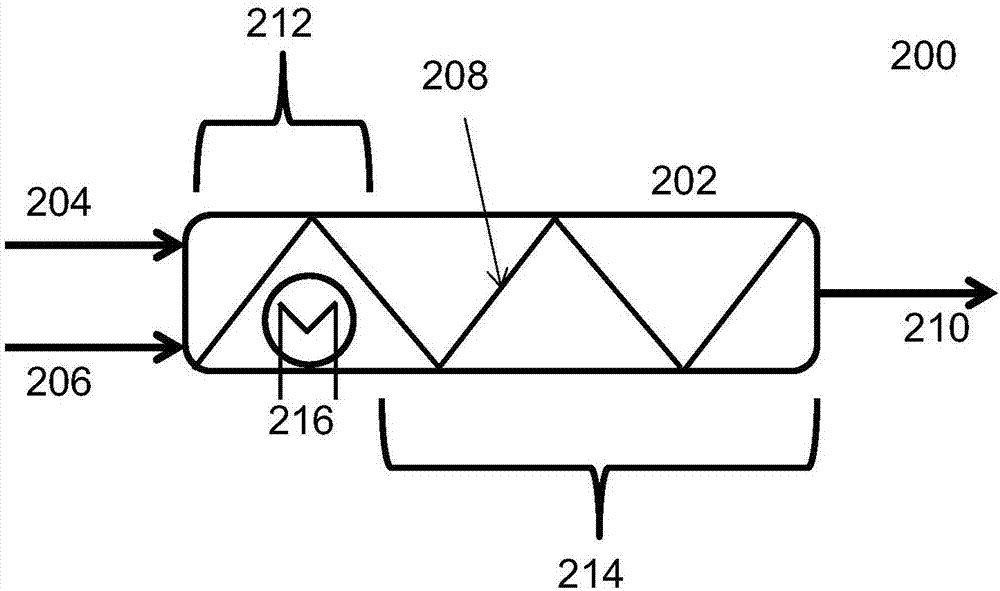
发明领域本发明涉及到含钛材料的选矿,该含钛材料含有大量的锐钛矿和/或金红石和/或假金红石结构成分。这些材料包括锐钛矿矿石和矿物以及其他来源的锐钛矿,以及包括常规来源的钛和二氧化钛的掺合物或混合物,如钛铁矿和钛渣。本发明特别但非排他地对锐钛矿材料对颜料质量的二氧化钛加工感兴趣。该工艺对加工含有大量锐钛矿或金红石成分的材料,如白钛石,也有效。发明背景从含钛矿石和其他材料(如钛渣)得到颜料级二氧化钛的两个常规工艺之一是20世纪初发明的所谓硫酸盐法。在此工艺中,钛铁矿或钛渣在浓硫酸中处理,产生含硫酸钛物质和硫酸亚铁和硫酸铁(特别是如果钛铁矿为原料)的块状物。将块状物溶解于水或弱酸中,分离出其它固体,得到被称为“黑液”的含硫酸钛物质的液体,尤其是硫酸氧钛tioso4。在钛铁矿作为原料的情况下,使用铁屑来还原三价铁,通过降低溶液温度,铁随后以被称为绿矾的硫酸亚铁形式结晶出来。通过加热(通常在80℃以上)溶液硫酸钛物质发生水解得到水合二氧化钛沉淀物。由于硫酸铁具有与钛共沉淀的倾向,所以早期还原三价铁是必要的。然后将水解步骤的湿的浆状产品置于内燃式倾斜回转窑中煅烧,其中浆状物被干燥并强烈吸水,so2和so3被释放,根据所使用的条件无定形tio(oh)2转化成锐钛矿或金红石颜料。例如,在水解步骤中使用晶种以获得下游金红石产物,否则会产生锐钛矿。目前溶解阶段的工艺包括:研磨矿石为反应提供表面部位。将经研磨的矿石与比化学计量所需量多加10%的98%的硫酸混合,从现有的金属元素(如ti、fe、mn、v、al、mg、ca等)形成硫酸盐物质。在工厂里通常使用压缩空气和/或蒸汽进行混合。对钛铁矿,典型酸对二氧化钛(a:t)的比率为1.7-2.0,对矿渣,比率为1.6-1.75。加入水(被称为引发),将酸的浓度从98%稀释到85%至95%(酸攻击强度)之间,这取决于使用的矿物,通过加热溶液使混合物的热增加,通常达到80-130℃。这通常辅以蒸汽直接加入。较低的温度用于高铁进料如钛铁矿,因为feo溶解反应是高度放热的,而tio2溶解反应是弱放热的。较低的feo矿渣需要较高的起始温度(约130℃),通过放热反应实现>200℃的反应温度。反应然后产生放热,使温度升至200-220℃,这取决于反应的矿石,通常形成一种具有从糖浆到固体的稠度的块状物。在此阶段继续进行压缩空气和/或蒸汽混合。一旦温度达到峰值,对于钛铁矿,将反应混合物“烘烤”约45分钟,对于矿渣,则“烘烤”5-6小时。由于反应器内衬耐火材料因此工业规模上的热损失是最低的且反应器的外表面积与反应物的体积相比较低。因此,在烘烤阶段,200-220℃的峰值温度大部分被保留。烘烤完成后,块状物用水或稀释(通常是回收的)硫酸溶解,因此,ti和其它硫酸盐被包括在溶液相中,控制回收的酸的量以确保酸与钛的比例(a:t)保持在1.75-1.85(其中比例为h2so4比tio2,其中所有tioso4转化为tio2和h2so4),因为较高的酸比对水解步骤造成不利影响。剩余的残留物通常被过滤并洗涤以收集任何剩余的液体,然后处理掉。残余物含有不溶性矿物相(例如二氧化硅和硅铝酸盐)和任何不溶性的ti相,如金红石和假金红石,不溶形式的fe,如磁铁矿,和不溶性硫酸盐物质,其中可包括ba、sr、ca的硫酸盐和不溶性α-tioso4。通常发现常规的硫酸盐法不能成功地和商业化地应用于锐钛矿矿石和含有锐钛矿的矿石,主要是因为在常规的硫酸溶解步骤的条件下锐钛矿不够充分溶解。通常还认为金红石和假金红石在浓硫酸中基本上不溶,因此不能用硫酸盐法处理。国际专利公开wo92/08816和巴西专利申请pi9005841a公开了一种类硫酸盐法,其中可以成功地处理某些锐钛矿矿石的提炼浓缩物,以生产颜料级二氧化钛。根据wo92/08816的公开内容,将提炼的锐钛矿浓缩物溶解于硫酸,控制条件,使得溶解结束后产生硫酸钛结晶块状物。将块状物用水或可循环液体溶解获得主要含有硫酸钛物质的“黑液”,通过硫酸盐法的进一步步骤处理,获得颜料级二氧化钛。wo92/08816工艺中的溶解阶段与常规硫酸盐法的不同之处在于,类似于细砂的浓硫酸、矿石和结晶的硫酸钛的混合物保持在悬浮液中,且在液相中有大量过量的酸,即a:o从2:1到10:1。将悬浮液在沸腾条件下保持平衡,这引起硫酸钛结晶。由该工艺产生的液体不能用于标准硫酸盐法“后端”,因为酸与钛(a:t)的比例太高,这使得水解失效。此外,由于过量酸的成本较高,且需要中和(用石灰)和处理掉过量的酸,使用大量过量的酸不经济,因此,该工艺将需要重新设计的(和新的)工厂从过滤液中产生最终的tio2颜料。欧洲专利公开ep0475104公开了一种处理通过硫酸盐法生产二氧化钛后残留的溶解残余物的方法。在去除硫酸盐法产生的可溶性硫酸盐后,溶解残余物主要是固体。ep0475104公开了溶解残余物可以包含20至60%的钛(为tio2)。ti存在于不溶相中,包括:金红石,假金红石,钛磁铁矿,白钛石和不溶性α-tioso4。溶解残余物通常还含有高比例的ca、mg、mn、al、si和fe氧化物(如磁铁矿)和ba和sr硫酸盐。ep0475104还公开了溶解残余物中的tio2不能在硫酸盐法的常用条件下被提取出来,因此通常将其排出或再循环到制浆过程中进一步提取,尽管低产率。ep0475104提出了一种从溶解残余物中回收tio2的方法。ep0475104描述了一种用于提高tio2回收率的两步骤方法,包括使用常规硫酸盐法处理矿石的第一步骤,以及从所得溶解残余物中提取另外的tio2的第二步骤。在该第二步骤中,ep0475104公开了以tio2:h2so4比为1:1至1:3.5将溶解残余物与硫酸混合,然后提供热能将该混合物加热至120℃至300℃,加热15分钟至20小时。ep0475104公开了通过向混合物中加入水来提供能量。硫酸在水中稀释是放热过程,其产生足够的放热将混合物的温度提高到上述的120℃至300℃范围内。在溶解步骤之后,ep0475104公开了可以根据硫酸盐法的常用条件回收tio2。本发明的一个目的是提供一种硫酸盐法在含有大量锐钛矿和/或金红石和/或假金红石结构成分的含钛矿石和其它材料的加工中的实际应用,以生产颜料级金红石或锐钛矿。对本说明书中的任何现有技术的引用不是承认或暗示该现有技术构成任何司法管辖区的常识的一部分,或者该现有技术可以合理地被本领域技术人员理解,认为是相关的,和/或与其他现有技术组合。发明概述在本发明的第一方面,提供了一种用于含有大量锐钛矿结构成分的含钛材料的选矿工艺,包括:将含钛材料溶于94至98%硫酸或发烟硫酸中,添加足以将温度升高至220℃以上的非放热热量,形成所得混合物;在220°-300℃范围内的烘烤温度下烘烤所得混合物至少4小时,形成烘烤混合物;和将烘烤混合物用水或稀酸溶解,分离主要含有硫酸钛物质的液体。在一个实施方式中,该方法还包括水解硫酸钛物质以获得水合二氧化钛沉淀物的步骤。在一个实施方式中,所述含钛材料选自下组:锐钛矿矿石,含锐钛矿矿石,比精制前含有更高比例锐钛矿的精矿,锐钛矿精矿或含锐钛矿精矿。在一个实施方式中,在含钛材料中的锐钛矿结构的锐钛矿提取率至少为90%(以氧化物表示)。也就是说,在含钛材料中至少90%的锐钛矿结构被分离在液体中。在本发明的第二方面,提供了一种用于含有大量金红石或假金红石结构成分的含钛材料的选矿工艺,包括:将含钛材料溶于94至98%硫酸或发烟硫酸中,添加足以将温度升高至220℃或以上的非放热热量,形成所得混合物;在220°-300℃范围内的烘烤温度下烘烤所得混合物至少4小时,形成烘烤混合物;和将烘烤混合物用水或稀酸溶解,分离主要含有硫酸钛物质的液体。在一个实施方式中,该方法还包括水解硫酸钛物质以获得水合二氧化钛沉淀物的步骤。在一个实施方式中,所述含钛材料选自下组:金红石或假金红石矿石,含金红石或假金红石矿石,比精制前含有更高比例的金红石或假金红石的精矿,金红石或假金红石精矿或含金红石或假金红石精矿。在一个实施方式中,在含钛材料中的金红石或假金红石结构的金红石或假金红石提取率至少为65%(以氧化物表示)。也就是说,在含钛材料中至少65%的金红石或假金红石结构被分离在液体中。发明人已经发现,与常规的硫酸盐法使用的放热热能比,非放热热能的使用具有许多优点。术语“非放热热”是指热从外源加入到系统而不是由系统内组分之间的反应产生的热量。这样的热量可以通过加热元件,热交换器,或在含钛材料和/或带有加热的或过热气体(包括蒸汽)的94至98%硫酸或发烟硫酸之间的直接接触提供。使用过热气体是有利的,因为它还有助于搅拌含钛材料和硫酸的混合物。如前面在
背景技术:
:部分所讨论的,在钛铁矿溶解的标准工艺中,将硫酸与钛铁矿混合,然后稀释。硫酸的稀释是高度放热反应,其产生足够的放热热能来驱动硫酸盐法溶解和烘烤步骤。通过这种放热溶解反应获得的热能通常被认为比硫酸盐法有利,因为它降低了能量成本,即不需要外部施加的热量。虽然该方法对于最终从钛铁矿中提取tio2是有用的,但该方法对于从含有大量的锐钛矿、金红石或假金红石组分的含钛材料中除去tio2是无效的。发明人已经发现,本发明工艺为溶解和烘烤步骤提供的非放热热量对于含有大量锐钛矿,金红石或假金红石组分的含钛材料具有许多优点。特别地,含钛材料和硫酸或发烟硫酸可以加热到高于硫酸盐法(如220℃或更高)中通常采用的温度,硫酸或发烟硫酸可以保持高浓度。本发明人相信,这可以从含有大量的锐钛矿、金红石或假金红石组分的含钛材料中有效地回收tio2。在第一和第二方面的一个实施方式中,溶解含钛材料的步骤包括用94至98%的硫酸或发烟硫酸搅拌该材料。优选地,压缩空气和/或蒸汽(例如过热蒸汽)被用于用94至98%的硫酸或发烟硫酸搅拌该材料。尽管含钛材料上(无论是来自上游处理或是因为来自搅拌的蒸汽冷凝)可能存在一些残留水分,这种水分存在的量非常小,以至于其不足以充分稀释94至98%的硫酸或发烟硫酸,因此在没有非放热热存在的情况下产生的任何放热不足以将混合物的温度升高至220℃或以上以进行溶解和烘烤。在第一和第二方面的一个实施方式中,基本上不添加引发水来稀释94至98%的硫酸或发烟硫酸,从而不在溶解和烘烤步骤中提供稀释的放热热。优选地,不添加引发水。如上所述,由于残留水分的存在,可能会产生放热。然而,热量主要作为非放热热添加。因此,将温度从基础温度(例如从室温)升高到220℃或以上所加入的热能主要是非放热热。在这种情况下,非放热热占温度升高至220℃或以上需的总能量的50%以上,优选为60%,更优选为70%,进一步优选为90%,最优选为95%。然而,在第一和第二方面的优选实施方式中,所述非放热热基本上不用来自硫酸或发烟硫酸溶解反应的放热来补充。应当理解,这种非放热热可以由不同的机制提供。在一个实施方式中,含钛材料和任选的硫酸或发烟硫酸用非放热热预热,例如在溶解步骤之前达到220℃或更高的温度。在另一个实施方式中,将非放热热和硫酸进料一起加入,在这种情况下,硫酸或发烟硫酸进料被预热,使得在溶解步骤中,温度升至220℃或更高。在第一和第二方面的实施方式中,烘烤温度在220至275℃的范围内。在第一和第二方面的实施方式中,在水解硫酸钛物质步骤之前,处理液体除去铁。在第一和第二方面的实施方式中,在水解硫酸钛物质的步骤期间不存在三价铁。在第一和第二方面的实施方式中,在溶解含钛材料的步骤之前该方法还包括精制含钛材料以将含钛材料从脉石中分离的步骤。在第一和第二方面的实施方式中,该工艺是连续工艺。优选地,该连续工艺进一步限定为至少溶解含钛材料的步骤和烘烤所得混合物的步骤在连续反应器中进行。优选地,所述连续工艺进一步限定为连续反应器是螺杆式反应器。在第一或第二方面的一个实施方式中,该工艺还包括煅烧沉淀的水合二氧化钛以产生锐钛矿型tio2的步骤。在第一或第二方面的替代实施方式中,该工艺还包括煅烧沉淀的水合二氧化钛以产生金红石型tio2的步骤。附图简要说明图1是说明本发明工艺在混合罐反应器中进行的一个实施方式的工艺流程图。图2是说明本发明工艺在螺杆式反应器中进行的一个实施方式的工艺流程图。图3是说明本发明工艺使用混合罐和螺杆反应器进行的一个实施方式的工艺流程图。详细说明根据本发明,已经发现,通过对常规溶解和烘烤步骤的某些修改,硫酸盐法可以成功地处理锐钛矿矿石和其它含锐钛矿和含金红石或假金红石的含钛材料。具体地,通过提供足够的非放热热以达到220℃或更高的反应温度进行烘烤来改进常规的溶解步骤。还发现烘烤温度越高,所需的烘烤时间越短,低至4小时(这与矿渣的5-6小时的现有工艺不同)。进一步发现随后的溶解阶段时间越长,tio2至tioso4溶液的收率越高。因此,本发明在第一方面提供了一种用于大量含有锐钛矿结构成分的含钛材料的选矿工艺,包括:将含钛材料溶于94至98%硫酸或发烟硫酸中,添加足以将温度升高至220℃或以上的非放热热量;在220°-300℃范围内的烘烤温度下烘烤所得混合物至少4小时;将烘烤混合物用水或稀酸溶解,分离主要含有硫酸钛物质的液体;然后水解硫酸钛物质以获得水合二氧化钛的沉淀物。在第二方面,本发明提供了一种用于大量含有金红石或假金红石结构成分的含钛材料的选矿工艺,包括:将含钛材料溶于94至98%硫酸或发烟硫酸中,添加足以将温度升高至220℃以上的非放热热量;在220-300℃范围内的烘烤温度下烘烤所得混合物至少4小时,将烘烤混合物用水或稀酸溶解,分离主要含有硫酸钛物质的液体;然后水解硫酸钛物质以获得水合二氧化钛的沉淀物。当应用于含锐钛矿、金红石和假金红石中的两种或两种以上混合物的钛铁矿改进产品时,本发明特别有用,典型的这种产品是矿物混合物白钛石。在某些应用中,例如缺乏铁的矿物,其中没有潜在可用于溶解和烘烤步骤的放热热,所有所需的热量可以从外部提供,即非放热地。在其他情况下,例如某些混合矿物产品,在溶解和烘烤步骤中可能会有一些反应的放热热。通常,不添加水,即引发以稀释酸,从而增加放热热。应当理解,可能存在与含钛材料相关的一定量的水,特别是在含钛料材料已经进行某种形式的预处理或精制的情况下。例如,当含钛材料含有大量锐钛矿结构成分时,这种材料很可能是滤饼的形式。这个滤饼很可能包括残留的水分。然而,该残留水分存在量非常少,以至于不足以使94至98%的硫酸充分稀释,并且在没有非放热的情况下因此产生的任何放热热不足以将混合物的温度升高至220℃或更高来进行溶解和烘烤。本发明的第一方面特别适用于主要是锐钛矿结构的各种含钛材料。不限于此,它们包括以原生矿物出现的锐钛矿,和其它含钛矿物(如钛铁矿,螺晶,钙钛矿和潜在的含钛磁铁矿)的改性产品。这些发现可能与碱性侵入复合物的风化,水热变化或沉淀(沉积)沉积物,沉淀变性沉积物和铝土矿或红土矿物有关。优选地,烘烤温度在220至275℃的范围内,更优选至少230℃,最优选至少240℃,更优选最多260℃,最优选最多250℃。通常,溶解步骤提供的非放热热足以在烘烤期间将烘烤温度保持在所需范围内。然而,应当理解,在一些情况下,可能需要提供另外的非放热热量来保持所需的烘烤温度。通常,烘烤步骤将混合物转化成硫酸盐块状物,即硫酸盐的固体混合物。所提供的硫酸的比例通常足以满足酸消耗反应的化学计量要求且通常过量约10%。烘烤持续时间优选为2至18小时,更优选为4至12小时。烘烤优选例如与a:o比,温度和持续时间有关,使得锐钛矿提取率为至少90%,更优选至少95%(以氧化物表示)。烘烤优选例如与a:o比,温度和持续时间有关,使得金红石或假金红石提取率至少65%,更优选至少80%,最优选至少90%(以氧化物表示)。金红石提取率可以达到大于80%,更优选至少85%,最优选至少90%(以氧化物表示)的值,但可以根据所需的液体性质和烘烤条件进行调整。用于该工艺的含钛材料进料通常可以是锐钛矿,或含有锐钛矿的矿石,例如白钛石矿石,和/或通常可以是制备的精矿。根据形式和形态,可以在溶解步骤之前以多种不同的方式处理锐钛矿或含锐钛矿的矿石。一些情况,如澳大利亚墨累盆地存在的那些典型的锐钛矿,将需要一些精制。这种精制可能是通过常规的矿砂浓缩工艺。风化的碱性复合物将需要使用常规技术进行一些精制,例如轻度破碎,湿式磁力分离,磨耗和脱灰,而其他如水热变质岩沉积物则需要粉碎和研磨,也可能使用浓缩技术如浮选,以从硅胶基质中释放锐钛矿,或至少在溶解步骤中使锐钛矿受到腐蚀。在溶解步骤中,进料含钛材料在硫酸中的混合物优选搅拌,例如优选地通过压缩空气,蒸汽(通常是过热的)搅拌或通过物理手段,例如通过使用搅拌器搅拌。若需要,在液体水解之前,任何存在的铁都可以通过结晶成水合硫酸亚铁(绿矾)来去除,通常,水解步骤优选不存在三价铁,因为它具有与钛共沉淀的倾向并且在结晶之前会被还原成亚铁形式。水解步骤可以通过提高硫酸钛溶液的温度来有效引起水合二氧化钛的沉淀,例如至约80℃。可以通过引入锐钛矿或金红石形式的晶核来加速水合二氧化钛的沉淀。通常,水解步骤可以基本上根据常规的硫酸盐法。通常,一旦煅烧,沉淀的水合二氧化钛是锐钛矿形式,但根据条件和根据在水解阶段中加入的晶核的性质,煅烧(见下文)可能产生锐钛矿或金红石颜料。优选地,例如在内燃式倾斜回转窑内将沉淀的水合二氧化钛煅烧,二氧化钛浆通过重力转动。沉淀物可以在煅烧之前经处理,例如通过在还原条件下过滤、洗涤和/或浸出以除去任何残留的三价铁。煅烧可以基本上根据常规的硫酸盐法。在窑中,水合二氧化钛在强吸附水之前初步被干燥,释放so2和so3。控制窑中的条件以控制微晶生长,以便根据需要形成锐钛矿或金红石颜料。温度通常在1000℃左右。在水解步骤之前,根据需要,该工艺可以包括处理液体以选择性地从硫酸钛物质分离一种或多种杂质。选择性分离可适当地通过溶剂萃取和/或离子交换进行。在主要含有硫酸钛物质的液体的选择性分离处理中分离出的杂质通常可以包括至少一种或多种过渡金属,例如,铬、钒和铌,和/或源自原始矿石中的稀土矿物独居石,堇青石或纤磷钙铝石的元素。在一个实施方式中,选择性分离可以是过渡金属的选择性分离。这些预期作为可溶性硫酸盐存在。用于该目的的合适的溶剂萃取系统是三唑并喹唑啉酮或中性有机磷三正辛基氧化膦(topo)。在另一个实施方式中,选择性分离通过从保留杂质的液体中提取硫酸钛物质来实现。从酸性(硫酸盐和氯化物)溶液中提取tioso4的已知试剂如有机磷酸二(2-辛基己基)磷酸(d2ehpa)或中性有机磷三正辛基氧化膦(topo)。topo将提取一定范围的过渡金属,因此可能没有足够的选择性来防止过渡元素氧化物被共同提取,但已知cr(iii)不能从topo的酸性溶液中萃取出来。萃取后,通过将有机溶液母液与稀硫酸相接触,将硫酸钛物质从萃取试剂中提取进行随后的水解。通常,处理液体以选择性地从硫酸钛物质中分离一种或多种杂质的步骤将涉及许多步骤,这些步骤用于分别处理不同的杂质或元素,因为在大多数情况下,单一提取系统不会覆盖所有所需元素。应当理解,该方法可以是批工艺,例如在一个或多个间歇反应器中进行;半连续工艺;或连续工艺,例如在一个或多个连续搅拌釜式反应器和/或一个或多个活塞式流动反应器中进行的。或者,该工艺的一些部分可以是间歇操作,而其他部分是连续的。然而,优选该工艺是连续工艺。连续反应器的优选类型是螺杆式反应器。螺杆式反应器包括驱动混合物沿反应器的反应体积的一个螺旋旋转叶片或两个相互啮合的叶片。叶片有助于混合,且有利地将混合物保持为颗粒形式,这些颗粒的直径通常为20至50mm。图1是批处理工艺100的工艺流程图。含钛材料,如锐钛矿矿石或精矿、或含锐钛矿的矿石或精矿,经由第一入口104进料到反应器102中。将94至98%的硫酸或发烟硫酸通过第二入口106进料到反应器102中。在这种情况下,搅拌器108用于混合含钛材料和硫酸或发烟硫酸。然而,应当理解,可以使用不同的搅拌或混合系统。一旦形成混合物,在反应器102内进行溶解和烘烤。如前所述,在溶解步骤中,硫酸中的含钛材料进料的混合物优选通过压缩空气或蒸汽(未示出)进行搅拌。在溶解和烘烤之后,通过出口110将经烘烤的混合物从反应器102中排出,然后进行下游处理,包括水解硫酸钛物质以获得水合二氧化钛的沉淀物。含钛材料和硫酸或发烟硫酸可以在进料到反应器102之前被加热,或者可以在反应器102内加热。在该实施方式中,提供非放热热以提高含钛材料进料和硫酸或发烟硫酸进料的温度,使得混合时所得混合物的温度为220℃或更高。优选地,加热步骤分别将含钛材料进料和硫酸或发烟硫酸进料的温度升高至220℃或更高。非放热热通常由热交换器或加热元件提供(参见进料流104和106上的加热元件112和114)。在替代实施方式中,提供非放热热以提高反应器102中的混合物的温度。在这种情况下,反应器102包括热交换器或加热元件。图2是连续工艺200的工艺流程图。含钛物料,如锐钛矿矿石或精矿、或含锐钛矿的矿石或精矿,经由第一入口204进料到反应器202中。将94至98%的硫酸或发烟硫酸通过第二入口206进料到反应器202中。在这种情况下,连续反应器202是螺杆式反应器,其具有用于混合含钛材料和硫酸或发烟硫酸的中心螺纹孔208,并将该混合物从反应器内的入口204和206输送到出口210。在这种情况下,反应器包括第一区域212和第二区域214。在第一区域212中进行含钛材料和硫酸或发烟硫酸的混合,在第二区域214内进行所得混合物的溶解和烘烤。溶解和烘烤后,经由出口210将经烘烤的混合物从反应器202中排出,然后进行下游处理,包括水解硫酸钛物质以获得水合二氧化钛的沉淀物。应当理解,两个分开的串联的连续反应器可以替代使用具有第一混合区和第二溶解和烘烤区的单个连续反应器。与图1的实施方式一样,可以在进料到反应器202之前或在反应器202内使用非放热热加热含钛材料和硫酸或发烟硫酸。在该实施方式中,在溶解和烘烤步骤之前,反应器202包括在第一区域内的加热元件216,以将混合物加热到所需温度。在替代实施例中,进料可以在引入反应器202之前被预热,或者可以在反应器202的第二区域214中加热。图3是另一工艺300的工艺流程图。在这一例子中使用了两个单独的反应器。第一反应器302是经第一入口304接收含钛材料并经第二入口306接收94至98%硫酸或发烟硫酸的混合容器。该反应器302可以作为间歇式反应器或连续搅拌釜式反应器操作。混合后,所得混合物脱离反应器302,并通过管线310进料到螺杆反应器308中用于溶解和烘烤。在溶解和烘烤之后,经出口312将经烘烤的混合物从反应器308中排出,然后进行下游处理,包括水解硫酸钛物质以获得水合二氧化钛的沉淀物。如上所述,可以在该工艺的各个阶段提供非放热热,以提供温度为220℃或更高的含钛材料/硫酸或发烟硫酸的混合物。例如,对容器302的单个进料可以被预热;或者可以在容器302,管线310或容器308的第一区域中进行加热所得混合物。在该实施例中,反应器302包括加热元件314,以加热含钛材料和硫酸或发烟硫酸,在进料到反应器308中进行溶解和烘烤阶段之前,将其混合至所需温度。在所有上述方法中,应当理解,由于上游处理,将含钛材料进料到反应器中可能含有残留的水分。例如,在一些情况下,含钛材料将进行上游选矿过程,例如浮选,过滤,固液萃取等。在这些情况下,含钛材料可能包括一些夹带的水分。然而,当与硫酸结合时,夹带的水分量不足以充分稀释硫酸,因此不能产生将混合物的温度升高至220℃或更高的放热。具体实施方式实施例1将金红石和锐钛矿精矿研磨并与浓硫酸以1.5的酸比1的矿石的质量比混合。将所得混合物在250℃下烘烤8小时以产生硫酸盐块状物。将块状物用10%硫酸溶解以产生硫酸钛溶液。结果总共提取了98%的锐钛矿,92%的金红石和92.0%的总tio2,进料和溶解残留分析见表1。表1实施例1的进料和残留物分析实施例2将金红石和锐钛矿精矿研磨并与浓硫酸以1.5的酸比1的矿石的质量比混合,将所得混合物在250℃下烘烤4小时以产生硫酸盐块状物,将块状物用10%硫酸溶解以产生硫酸钛溶液,结果总共提取了98%的锐钛矿,84%的金红石和86.7%的总tio2。进料和溶解残留分析见表2。相对于实施例1,烘烤持续时间的明显降低对锐钛矿回收没有显著影响,但金红石回收率稍低。表2实施例2的进料和残留物分析实施例3将金红石和锐钛矿精矿研磨并与浓硫酸以1.2的酸比1的矿石的质量比混合,将所得混合物在220℃下烘烤12小时以产生硫酸块状物。将块状物溶解在水中以产生硫酸钛溶液,结果总共提取了98%的锐钛矿,85%的金红石和84.4%的总tio2。进料和溶解残留分析见表3。相对于实施例1,与实施例2类似,酸和温度的降低但持续时间的增加解决了金红石回收率,但是基本不影响锐钛矿回收率。表3实施例3的进料和残留物分析物质进料残留提取率质量(g)10030.669.4锐钛矿(%)36398金红石(%)331685tio2(%)76.237.784.4fe2o3(%)2.100.4593.5sio2(%)11.639.9<1zro2(%)5.3712.0730.6p2o5(%)0.1990.07588.4al2o3(%)2.011.5177.0nb2o5(%)0.2640.13684.2cr2o3(%)0.0720.3883.6实施例4将金红石和锐钛矿精矿研磨并与浓硫酸以1.5的酸比1的矿石的质量比混合,将所得混合物在180℃下烘烤12小时以产生硫酸盐块状物,将块状物用10%硫酸溶解以产生硫酸钛溶液。结果总共提取了38%的锐钛矿,18%的金红石和30.7%的总tio2,进料和溶解残留分析见表4。相对于实施例1至3,尽管持续时间为12小时,但将温度进一步降低到180℃导致锐钛矿和金红石两者的极低回收。表4实施例4的进料和残留物分析物质进料残留提取率质量(g)10072.327.7锐钛矿(%)363138金红石(%)333718tio2(%)76.273.130.7fe2o3(%)2.100.5880.1sio2(%)11.615.91.1zro2(%)5.376.7-8.9p2o5(%)0.1990.05082.0al2o3(%)2.011.2056.6nb2o5(%)0.2640.25729.6cr2o3(%)0.0720.05049.2实施例5将金红石和锐钛矿精矿研磨并与浓硫酸以1.0的酸比1的矿石的质量比混合,将所得混合物在250℃下烘烤8小时以产生硫酸盐块状物,将块状物用10%硫酸溶解以产生硫酸钛溶液。结果总共提取了93%的锐钛矿,74%的金红石和74.3%的总tio2。进料和溶解残留分析见表5。相对于实施例1,该实施例显示将相对于矿石的酸减少至仅化学计量比例如何显著影响锐钛矿和金红石溶解和回收。表5实施例5的进料和残留物分析物质进料残留提取率质量(g)10039.5560.4锐钛矿(%)36693金红石(%)332274tio2(%)76.249.574.3fe2o3(%)2.1092.292.2sio2(%)11.67.57.5zro2(%)5.3716.616.6p2o5(%)0.1990.0687.5al2o3(%)2.011.18476.7nb2o5(%)0.2640.18272.7cr2o3(%)0.0720.04575.5实施例6将金红石和锐钛矿精矿研磨并与浓硫酸以1.0的酸比1的矿石的质量比混合,将所得混合物在220℃下烘烤12小时以产生硫酸盐块状物,将块状物用10%硫酸溶解以产生硫酸钛溶液,结果总共提取了92%的锐钛矿,70%的金红石和72.0%的总tio2,进料和溶解残留分析见表6。相对于实施例5,该实施例突出较低的温度可以如何被较长的处理持续时间平衡。表6实施例6的进料和残留物分析实施例7将金红石浓缩物研磨并与浓硫酸以1.5的酸比1的矿石的质量比混合,将所得混合物在250℃下烘烤8小时以产生硫酸盐块状物,将块状物用10%硫酸溶解以产生硫酸钛溶液。结果总共提取了73%的金红石和70.9%的总tio2,进料和溶解残留分析见表8。该实施例表明,与实施例1的混合矿石比,无锐钛矿时,金红石的回收率较低。表7实施例7的进料和残留物分析应当理解,本说明书中公开和定义的发明延伸到文本或附图中提及的或明显获得的两个或更多个独立特征的所有替代组合。所有这些不同的组合构成了本发明的各种替代方式。当前第1页12